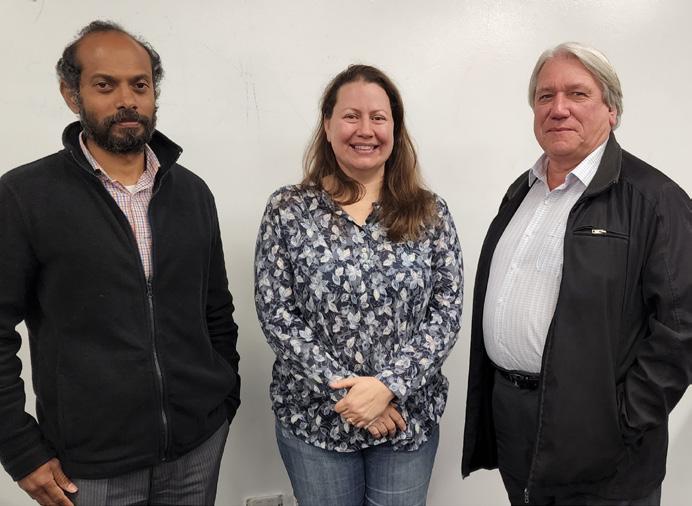
3 minute read
WA Branch Meeting Report - 8 August 2022
Joint meeting with Australian Foundry Institute
Source: Louise Petrick, Senior Welding Engineer, Materials & Welding Solutions
Louise Petrick recently presented a case study for the Western Australian Branch on Weld repair of 1960s low alloy cast turbine casing with microstructure replication. Louise is a Senior Materials and Welding Engineer with Materials and Welding Solutions. Prior to this, she provided materials and welding consulting support through Weld Australia, where she worked for six years. Her power generation experience started at Eskom in South Africa, where she spent eight years, and continued after her move to Australia with two years at Synergy, supporting Muja Power Station. Louise started her engineering career at Highveld Steel and Vanadium after completing a research masters on welding and corrosion of stainless steel (at the University of Pretoria) before moving to Mintek, working on corrosion research.
The case study concerned weld repairs to three steam turbine casings so that they could be de-mothballed and returned to service, with an expected additional service life of at least 15 years. The turbines had been in continuous use for around 20 years from the late 1960s and had been mothballed for nearly 20 years after that. They had been cast from a proprietary Cr-Mo-V low alloy steel, made at a time when there was limited capacity for control of tramp impurity elements.
They had been operating in the temper embrittlement, and creep, temperature range for around 150,000 hours (longer than their 100,000-hour design life), and had also been subjected to low cycle fatigue through around 150 cold starts over that time. Non-destructive testing revealed manufacturing defects, cracks, and a number of cosmetic carbon steel weld repairs. Louise became involved as a specialist welding engineer after the maintenance team attempted a weld repair with nickel, expecting that this relatively ductile metal would accommodate any stresses induced by welding. It did not. The result was nearly disastrous, with deep cracking occurring in the cast metal surrounding the filled area. The welding specialist team was brought in see if the situation could be remedied. Initial testing showed that the cast metal had a Charpy impact energy absorption of about 5J – tougher than a cracker biscuit, but so brittle as to require exceptional care as a candidate material for weld repair. The prescribed solution, developed jointly with the maintenance team and the OEM, was to excavate the cracked material and undertake a full weld repair with post-weld heat treatment to match microstructure. In a few areas, the excavation required machining away 90% of the 80mm casing thickness.
The process selected was manual metal arc welding with the smallest available electrode of similar composition, with minimal penetration and a prescribed pattern of overlapping beads so that each deposit normalised the underlying ones.
The practical challenge was how to achieve this. The solution was to bolt the two halves of the casing together, to avoid distortion. However, this meant that the welder had to work inside the casing, which was stood vertically, with steps to give the welder access. The additional complication was that the casing had to be heated to around 200°C (with ceramic bead heaters). This meant that the welder had to wear a full heat-reflective suit, and each member of the welding team could only lay one rod before exiting the casing. After each layer of deposit had been completed, the casing was allowed to cool to 100°C for magnetic particle inspection. After completion of the repair, the casing was heated to 700°C (with ceramic bead blankets), held for around four hours, cooled under control to 300°C and finally allowed to cool under the unheated blanket.
It all worked, and the passing of time has proved that desired life extension had been obtained.
Louise illustrated her presentation with photographs of casings, the welding being undertaken and photomicrographs of replicas showing the microstructures, including defects, cracks, grain boundary precipitates and creep voids. The very engaged audience had many questions for Louise, and one in particular drew a most emphatic response. This concerned excavation of the cracks prior to welding. Working with such a brittle metal, grinding was absolutely not an option; grinding simply propagated the cracks. Louise explained that when this work was done in 2006, Eskom had a fully integrated operational, maintenance, R&D and internal consultancy structure. Whether such an ambitious repair could (or would) be undertaken with outsourced repair capacity and outsourced consultancy remains an intriguing question.
L to R: Schree Chandran, Louise Petrick, John Wootton