Expanding Horizons
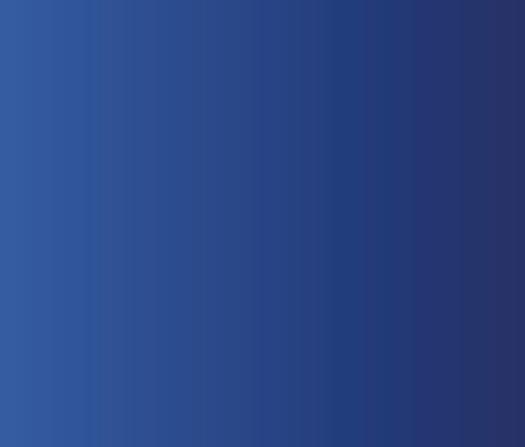
Martin Coles, Group CEO, Matrix Polymers
Introducing Expanding Horizons, a Rotoplas mini edition of the Matrix Polymers magazine. Over the past year, Matrix Polymers has proven our commitment to supply chain security. With reliable logistics solutions and local manufacturing, we offer a comprehensive range of raw materials, protecting our customers and allowing them to concentrate on their primary business goals. This magazine aims to help educate and inform designers, rotomoulders and OEMs about the endless possibilities that the rotational moulding process has to offer.
Many people are unaware of the very wide range of products that are manufactured, and our goal is to inspire and encourage the development of new applications. With its flexibility, durability, and relatively low production costs rotomoulding offers many advantages over more well-known plastics processes. Hopefully, the magazine will provide valuable insights and encourage you to explore and push the boundaries of what is possible with this technology.
I trust that you will find this mini edition to be a source of inspiration and that it will ignite your creativity as you nurture your ideas.
Enjoy the read!
A global leading supplier of row materials to the rotational moulding industry
Over 30 years of innovative raw material solutions
6 manufacturing sites across 3 continents
Co-founded in 1992, Matrix Polymers has grown into a global leader in supplying raw materials to the rotational moulding industry. Our remarkable growth is driven by our unwavering commitment to product excellence, technical expertise, and commercial integrity—all made possible by our dedicated and long-serving team.
The company’s vision is clear: “To become the global experts in rotomoulding materials through innovation and strong local partnerships.”
We are more than just suppliers—we are industry experts dedicated to helping our customers succeed. Through our extensive experience, innovative solutions, and reliable service, we add value at every step.
Our commitment lies in building lasting relationships and delivering the highest quality materials to the industry.
Reach out to us to discuss your next raw material solution.
Six Manufacturing Sites Across Three Continents
Global Footprint
Six Manufacturing Sites Across Three Continents
Key
Production / Manufacturing
Technical Services
Warehousing
Head Office
APAC R&D
European R&D
Key
Production / Manufacturing
Technical Services
Warehousing
Head Office
APAC R&D
European R&D
General Purpose Grades
Tank Grades
High Performance Grades
Super-Linear Grades
Speciality
Flame Retardant Grades
- LLDP - Others
+ Additives + Colours
< Grinding Natural >
Our products find utility in a diverse array of sectors including automotive, industrial, indoor and outdoor furniture, leisure marine, and gardening products. We are passionate about the unique features of the rotomoulding process and constantly push the boundary of our knowledge to develop cutting-edge technical solutions. Our technical customer service can be tailor-made to match any moulder’s demand.
We offer a range of cutting-edge material technologies including thermoplastics and thermosetting materials such as polyethylene, polyamides, polypropylene, and more. We offer one of the widest raw material selections and have developed several of our key grades under our ‘Designed for Roto®’ concept. Our mission is to introduce fresh ideas and exciting new materials to the market and expand the range of products that can be rotomoulded.
Moonlight Lumieres was founded in 1997 with a vision of creating a unique light diffusion and ambient lighting. Inventing the first PE globe lights on the market, this product won numerous design awards, such as Design Plus, Form, Good Design Award, IF Design Award. In addition to being able to be used indoors and outdoors, Moonlight lights can be seamlessly integrated into any environment, including gardens, architecture, or even wet areas. Moonlight has been the epitome of atmospheric light, innovative design, and maximum robustness and durability for more than 20 years. To ensure quality and robustness, all globe lights are manufactured at the company’s headquarters in Schwörstadt, Southern Germany.
A fundamental value of everyday life is the quality of light: Moonlight and Matrix Polymers collaborated on this basis to create high-quality, high-design lamps.
> Moonlight Battery Light
Human feelings are greatly influenced by light, whether it is in living rooms, gardens, architecture, or at social events. A harsh light is created by many light sources that does not exist in nature. Moonlight aims to mimic natural light as closely as possible, both in terms of design and visual effect. It was not possible to achieve the softness and indirect nature of a Moonlight, as well as its robustness, using glass.
An excellent design outlasts the spirit of the times, which is why Moonlight luminaires are still manufactured today in the same form and quality as they were in 1997. Their lighting characteristics create a nuanced and atmospheric environment that is appreciated by architects worldwide. From its inception until today, Moonlight has strived to create lamps that are timeless, capable of remaining current over time, and innovative in terms of light output.
> Ground-Anchored Moonlight Lamp
In addition to light intensity and color temperature, light distribution and diffusion has a decisive influence on mood, space reception, and ambience. With its soft, even light characteristics, every environment is filled with an unparalleled feeling of calm and tranquility. Moonlight is the emblem of atmospheric indoor and outdoor lighting for designing with light. The Moonlight lights are available in a variety of sizes, colors, and mounting systems to meet every design requirement. Viewers are almost invisible to all types of base mounts.
Moonlight’s 5 mm thickness of rotomoulded PE creates a new experience in light diffusion and durability. A Moonlight environment provides a base level of illumination for all elements within it, without blending humans into it. Shadows cast by ambient light are generally soft and less defined since there is no strong directional light source. By cutting the globe and recessing the socket, it can be fixed on the ground seamlessly and without any visible base at all.
It is by design that Moonlight lights are very well protected against moisture and dust up to IP68. The tread that connects the globe and the socket is integrated into the shape and mold. Due to the use of PE in the socket, a Moonlight can also be used in seawater environments, such as yachts, without corroding or oxidizing. Two times a year, the mold’s surface is restored, resulting in a shiny, completely even light surface.
With the exception of the lamp socket and wiring, all Moonlight parts are roto-moulded PE and PC. As a result, the company is able to control the thickness, which results in both outstanding light quality and UV stability. Furthermore, Moonlight lamps are extremely stable and robust against stresses and impacts. Rotomoulded lamps are particularly resistant to UV rays and temperatures from -40 to +80 degrees Celsius.
Over the years, Moonlight and Matrix Polymers have collaborated not only in supplying high quality raw materials but also in finding the best production solutions to produce high performance rotomoulded lamps. To continually improve the production process and the final quality of the lamp object, Matrix Polymers deploys its expertise in the rotational moulding.
> Moonlight with screw-on base
> Moonlight lights stone look
Moonlight lamps are highly versatile products that can be used for a wide range of applications. They are actually luminous globes that can be placed on the ground or suspended from a power cable. Furthermore, they can be used inside homes as well as for furnishing public spaces such as stations, airports, event spaces, exhibition halls, etc.
Floteks was founded in 1978 to apply flocking to plastic parts. In 1983, Floteks became the first company in Turkey to manufacture plastic parts using rotational molding. In today’s marketplace, Floteks is a pioneer in rotational molding and has international recognition. Through license agreements, Floteks exports technology to foreign companies.
Floteks is competent in product design, product development, engineering analysis, material and product testing for commercial vehicles, tractors and construction machines. As a fully integrated plant, Floteks designs and manufactures products, manufactures molds, prepares powder, manufactures rotational molded parts, assembles, tests, and controls quality. Floteks offers a wide range of products for the automotive industry. Amongst our main product groups are diesel fuel tanks, AdBlue (Urea) tanks, expansion tanks, fenders, bus cabinets, air ducts, tractor ceilings, interior trim parts, wiper water tanks, and hydraulic oil tanks. Under the Subterra brand, Floteks produces innovative products for the agriculture, livestock, and food sectors.
The case of Floteks exemplifies our approach: from large companies to small ones. In order to create innovation, every customer is important and becomes a strategic partner. Regardless of size, production capacity, or turnover.
An emblematic case that distinguishes the research and innovation developed by Floteks is related to Daimler buses. The German company was looking for an alternative technology for their storage boxes for their buses. Daimler was interested in making these products lighter and cheaper and for this reason rotational molding appeared as an interesting solution for which, however, the company had limited experience having produced, until then, only a rotomolded waste container.
> Detail of the opening mechanism
> Daimler Bus - Storage Box
When Daimler contacted Floteks, the project was still at a very general level and initially focused on the use of other production technologies. By using a single wall design for the main body and a double wall design for the lid, Floteks was able to meet most of their requirements, reducing the number of parts, assembly time, part weight, and overall cost. It was determined that rotational molding was the most appropriate technology to meet the client’s performance requirements for the entire project.
Rotomoulded parts had to integrate with the designers’ aesthetic vision. As a result, several suggestions to reduce waste and simplify production have not been accepted. In addition, even from a chromatic perspective, the rotomoulded pieces had to be coordinated with the interior of the bus. The process proved to be more challenging as different components produced using different technologies had to coexist. Furthermore, the lid hinges had to withstand thousands of openings and closings.
> Rotomoulded parts for MAN
> Rotomolded parts for MAN
A long process of research led to the development of the rotomolded container. Many details also contributed to the visual appearance of the final product: the seams were positioned so as not to be directly visible to people, while the final colors had to coordinate with those inside the vehicle. In this work, Matrix Polymers played a key role both in selecting the most appropriate material and in determining the additive polymer’s flammability and colorability.
Since 1997, Clark Tanks has been manufacturing rainwater storage tanks, agricultural products, and custom-moulded items designed to withstand Australia’s tough conditions. As the country’s premier brand of polymer rainwater tanks, Clark Tanks is committed to providing durable water tanks that cater to the needs of rural, commercial, and residential areas across Australia.
With branches in Victoria, New South Wales, and Queensland, Clark Tanks possesses the specialized knowledge and versatility needed to supply polymer rainwater tanks that can meet various industry requirements and applications. Their industrial tanks range from 1,000L to 50,050L and are designed to hold liquids with specific gravities from SG1 to SG2, ensuring compliance with AS-4766 and 9001 standards. These tanks are ideal for applications such as industrial water storage, water treatment plants, chemical treatment, and liquid transportation.
The large territories of the Australian continent require reliable and high-performance solutions for water collection. Clark Tanks has been engaged in this great challenge for years, providing durable and efficient products to meet the diverse water storage needs across the country.
Thanks to the close collaboration between Clark Tanks Dalby and Matrix Polymers, the best polymers for enhancing tank performance have been identified. Revolve® 6329U, a rotational moulding linear low-density polyethylene (LLDPE) hexene grade, is one such polymer. Due to its hexene comonomer, which contains a higher number of carbon atoms, this material is tougher, more resistant to creep and fatigue, and has greater impact resistance compared to butene grades.
Clark Tanks’ main mission is to provide efficient solutions for those living in rural and industrial areas of Australia characterized by persistent water scarcity. From this perspective, investing in a rainwater tank can offer financial savings and environmental benefits, making it a practical choice for many families and businesses located far from reservoirs or large metropolitan areas. The challenge lies in supplying large rotomolded tanks capable of withstanding atmospheric agents, shocks, and stresses over time.
The partnership between Matrix Polymers and Clark Tanks Dalby has flourished into a beacon of reliability and innovation over the last 20 years. What began as a simple collaboration to supply rural Queensland with highquality, UV-resistant water tanks has evolved into a dynamic synergy, where each entity complements the other in the pursuit of excellence. Matrix Polymers, with its wealth of expertise in polymer solutions, provides Clark Tanks Dalby with a reliable supply of top-grade materials, ensuring that each tank produced meets the highest standards of durability and performance for Australia’s harsh weather conditions.
The collaboration between Matrix Polymers and Clark Tanks is based on the idea of creating innovation and experimenting with new, unprecedented solutions. Together, they continually explore new technologies and techniques to improve their products and processes. Whether developing cutting-edge materials or perfecting manufacturing methods, both parties are committed to pushing the limits of what is possible in the industry. This spirit of innovation not only drives their individual success but also propels the entire industry forward.
Matrix Polymers plays a crucial role in the material selection process, providing Clark Tanks with Revolve HellCat, a hexene co-monomer-based material renowned for its excellent stress crack and chemical resistance properties. This material, coupled with UV15 protection for extended product life, ensures that tanks withstand the rigors of high load and temperature environments over their operational lifespan.
Through collaborative consultations and technical support, Matrix Polymers assists Clark Tanks Dalby in selecting the optimal material for each project, ensuring that every tank produced upholds the highest standards of performance, reliability, and longevity. By leveraging Matrix Polymers’ industry-leading products and expertise, Clark Tanks Dalby can confidently deliver superior water storage solutions that exceed customer expectations and withstand the test of time.
APEX Group, founded in 2000 in Rostock/Laage, Germany, has been one of the pioneers in the hydrogen industry since 2012. It is the company’s primary objective to become an internationally recognized developer and operator of hydrogen plants.
APEX’s core business is developing, constructing, selling, or operating green hydrogen electrolysis plants with a capacity of up to 1 GW. The development of these cuttingedge facilities is vital to the decarbonization of industrial value chains as well as to the production of green hydrogen and hydrogen derivatives like chemical hydrogen carriers and e-fuels. The solutions are applied to energy-intensive industries such as steel, chemicals, and cement, contributing significantly to their sustainability efforts.
In addition, APEX provides hydrogen infrastructure and logistics solutions, particularly in international industrial settings such as warehouses, ports, and production facilities.
To create a more efficient and sustainable society, renewable energy storage represents a crucial challenge. In order to address this important issue, APEX has developed an innovative industrial approach.
Renewable energy’s inherent nature is unpredictable. It fluctuates based on environmental conditions and may not align with peak demand on the electrical grid. Innovative technologies like electrolysers have emerged, allowing us to store energy in the form of Hydrogen gas for later use. Recognizing this potential, APEX has identified storage solutions as a pivotal product group that will play a crucial role in shaping renewable energy’s future. To this end, they have established a dedicated subsidiary, HydroExceed, specialising in the production of hydrogen pressure storage vessels.
> New 100 MW Electrolysis Plant, Rostock/Laage > CO2 Neutral Industrial Park, Rostock/Laage
Through the provision of efficient and reliable storage solutions, APEX strives to bridge the gap between renewable energy generation and its demand, ensuring a reliable and sustainable supply of power for a variety of applications.
A focus on storage technologies positions them as a key player in driving the clean energy transition, and fostering a greener future, for future generations as the adoption of renewable energy sources continues to grow.
APEX Group is a pioneer in the green energy transition. On behalf of their customers, they develop solutions for a CO 2 -neutral energy supply on an industrial scale. Their business model is based on project development and storage solutions. APEX assumes the role of an EPC partner for their clients, overseeing everything from approvals and detailed planning to the installation and commissioning of turnkey H2 projects. Beyond this, APEX has their own H2 production facility and operates a H2 power plant, complemented by an H2 refuelling station and an H2 trailer filling station.
APEX / HydroExceed utilizes crosslinked polyethylene for the rotomoulding of their liners, a material that has consistently demonstrated an exceptional balance between ease of processing and permeation performance. This material choice ensures that their customers receive top-notch liners that fulfil their requirements while also offering a costeffi cient solution. Rotomoulding allows HydroExceed to achieve exceptionally stable liner geometry, completely free from the surface defects often encountered in other productions.
> Type IV Pressure Vessel: Single Tank, Up To 500 bar
APEX has a long standing partnership with Matrix Polymers that began while developing their inaugural product - the TYPE IV vessel for stationary hydrogen storage. As APEX sought the optimal materials to align with their objectives, the collaboration with Matrix Polymers proved invaluable. Through a series of rigorous tests and design refibements, Matrix Polymers’ expertise and profound knowledge were crucial. Their contributions culminated in a certified product that APEX was able to proudly present to the market.
One of the most significant benefits is the ability of rotational moulding to create liners with seamless construction. Unlike other technologies that rely on joining pieces, this technology forms a single, homogeneous liner. It eliminates weak points that seams and welds can introduce, especially under fluctuating loads introduced by repetitive filling and emptying of hydrogen storage used in transport. By adopting rotational moulding, HydroExceed ensures that their liners possess a level of structural integrity and reliability that surpasses other manufacturing methods.
> Type IV Pressure Vessel
As APEX / HydroExceed ventured into new product territories, the need arose for a seasoned partner skilled in a vast array of polymer products, processing, and technologies. The objective was to develop a reliable hydrogen storage product to meet market demands. Matrix Polymers’ continuous support has been invaluable, particularly in determining the optimal processing parameters for liner production and ensuring the best synergy between various polymer and non-polymer materials.
> Type IV Pressure Vessel: Single Tank, Up To 500 bar
> Rotational Moulding Process
With the expertise of Matrix Polymers’ specialists playing a pivotal role in the development of APEX’s new products, a superior quality was achieved. Furthermore, through this continuous exchange of information and knowledge, APEX has obtained the possibility of creating products that optimize their manufacturability on an industrial level.
The following are all registered trademarks of Matrix Polymers.
Super-Linear® Designed for Roto®
Revolve®
The information contained in this magazine is given in good faith. The suitability for the application and performance of goods manufactured with materials processed and/or sold by Matrix Polymers is the sole responsibility of the end user. Product design, the production process and parameters of end use are factors that may affect the performance of the finished product and these and other factors are outside of Matrix Polymers’ area of control.
Matrix Polymers Ltd. Registered in England and Wales company number 02626784.
Registered office: Unit 2, Compass Industrial Park, Spindus Road, Speke, Liverpool, L24 1YA, UK
> Photo credits
Samuel Pavel Cover
Matrix Polymers Pg 01-08, 28
Euro3Plast Pg 07
Moonlight Pg 09-14
Floteks Pg 15-18
Clark Tanks Pg 19-22
APEX Group Pg 23-27
> Editorial contributions
Ranbir Kooner, Group Brand Marketing Manager
> Concept and Graphic design Studio Giovanetti
> All rights reserved by Matrix Polymers. Partial or total reproduction of the contents is prohibited without the prior authorization of the company
Get in touch
Registered Office
Matrix Polymers Liverpool
Unit 2, Compass Industrial Park, Spindus Rd, Speke, Liverpool, L24 1YA, UK
Tel: +44 (0) 151 448 7000
Email: sales@matrixpolymers.com
Matrix Polymers Polska Sp. z o.o.
Ul. Torunska 239/241
62 600, Kolo, Poland
Tel: +48 63 888 1069
Matrix Polymers Thai Co.,Ltd. No. 13, Highway No. 3191 Road, Tambol Huai Pong, Amphur Mueang Rayong, Rayong Province 21150 Thailand
Tel: +66 3368 3393-4
Email: sales.th@matrixpolymers.com
Revolve Matrix Polymers Malaysia Blok A, Lot 766, Persiaran Selangor, Seksyen 16, 40200 Shah Alam,
Matrix Polymers Australia Pty Ltd
37 Antimony St, Carole Park, QLD 4300 Australia
Tel: +61 (0) 7 3718 5400
Email: sales.aus@matrixpolymers.com
Matrix Polymers New Zealand
39 Railway Road, PO Box 5078, Terrace End, Palmerston North 4441, New Zealand
Tel: +64 (0) 6 357 8498
Email: sales.nz@matrixpolymers.com
Six Manufacturing Sites Across Three Continents