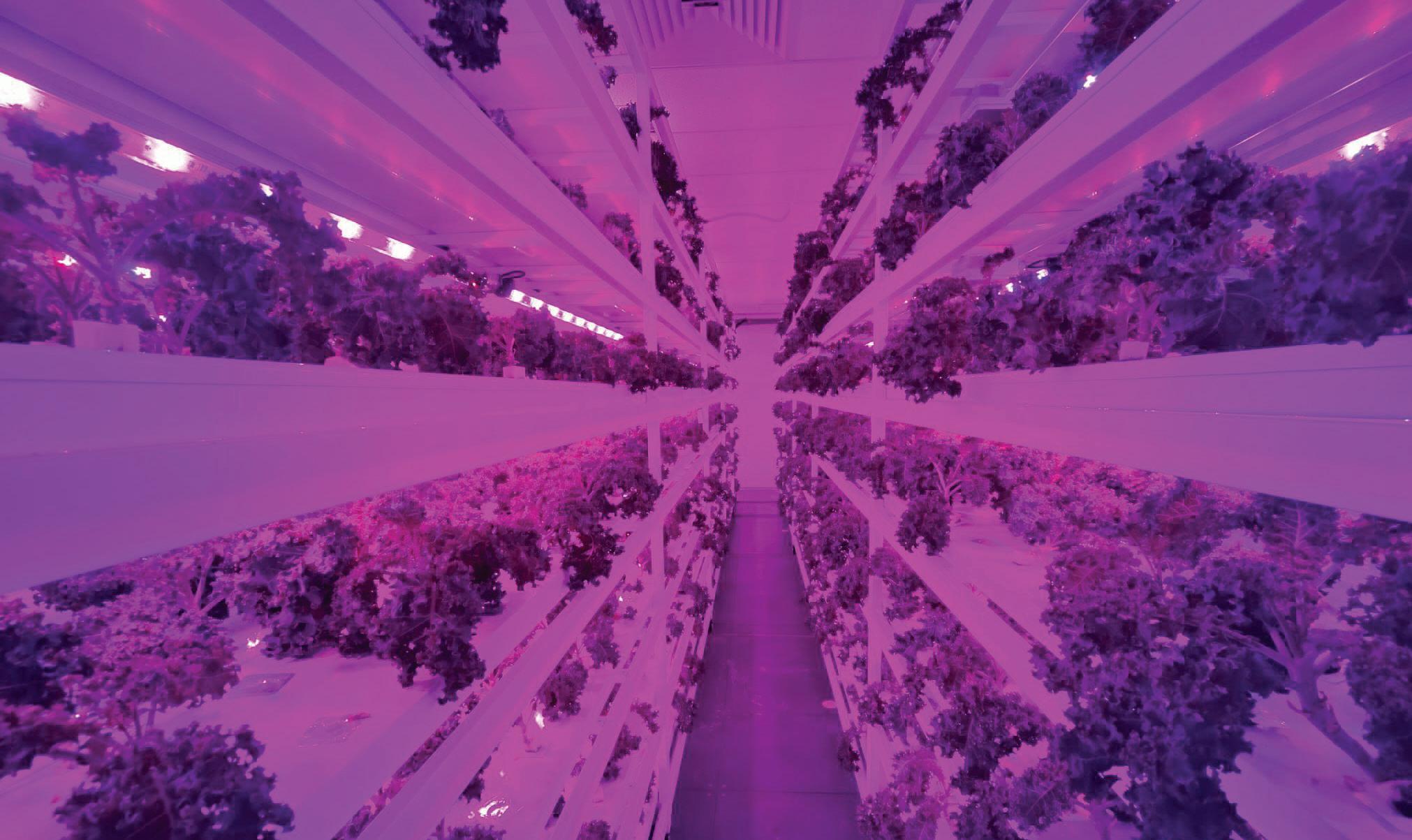
2 minute read
Indoor Farming
SAFEGUARDING THE FOOD SAFETY AND PRODUCT QUALITY OF BABY LEAF VEGETABLES AT AN INDOOR VERTICAL FARM
Although it is home to 5.6 million people, the citystate of Singapore is located on a small island that covers merely 715 square kilometers (276 square miles). As a consequence of crowding, it has been necessary to expand upwards, accommodating residents and businesses in high-rise buildings. Land is in such great demand in Singapore that only 1% is used for conventional farming, with local food production meeting less than 10% of residents' nutritional needs. But now agriculture, too, is reaching for the skies: investment is increasing in indoor vertical farming.
Advertisement
This trend is being encouraged by the Singapore Food Agency (SFA), the authority with the mission of ensuring that the nation has a resilient supply of food safety and food security from farm-to-fork. The SFA calculates that multi-story LED vegetable farms can produce 10 to 15 times more Vegetables, per square meter, than conventional farms.
One leader in the shift to vertical farming is Sustenir Agriculture, which runs indoor farms in Malaysia and Hong Kong and will open another in Jakarta by early 2023. Sustenir describes itself as specializing in growing "superfoods for supercities, farming at the heart of demand in urban populations to minimize carbon footprint whilst maximizing positive impact in local communities."
Sustenir harvests crops daily all-year-round, selling them as 100% clean, with no need for washing before eating. The company's indoor farm uses no pesticides, generates 92% less carbon emissions than imported produce, and consumes 95% less water than conventional farming on arable land. The company recently decided to take care of food safety and product quality by investing in its first optical sorting machine from TOMRA Food.
Indoor farming challenges
Sustenir's Singapore farm grows kale, curly kale, spinach, arugula (rocket), and lettuce. Even when grown in a precisely controlled indoor environment, these crops are vulnerable to a wide range of natural defects: chlorosis, black spot, crystallization, black rot, tip burn, light burn, discoloration, and purple leaf.
Another risk at indoor farms is foreign materials. Though it is true that indoor crops are grown in clean and dry conditions, even so, they face the threats of insect damage (from the tiny fungus gnat), foam, and fragments of plastic.
Sustenir initially removed defects and foreign materials manually, relying on the vision and concentration of 20 people. But human sorters are subjective, imperfect, and significantly less accurate when tired or bored. And because manual sorting is a relatively slow process (Sustenir found that each person could typically sort 24 kg per hour), it restricts throughput. An optical sorting machine, however, is accurate, consistent, and fast. What's more, optical sorters also reduce food waste by enhancing yields and recuperating some rejected product for sale at lower grades.
It was only logical, then, that Sustenir should transition from manual to mechanical sorting. Logical, too, that the business should consider acquiring a machine from TOMRA Food, the industry leader which combines world-class expertise with locallevel customer support. And when Sustenir's senior managers witnessed a live online demonstration of a TOMRA machine sorting baby leaf vegetables, with results precisely quantified, their minds were made up: this was a musthave.