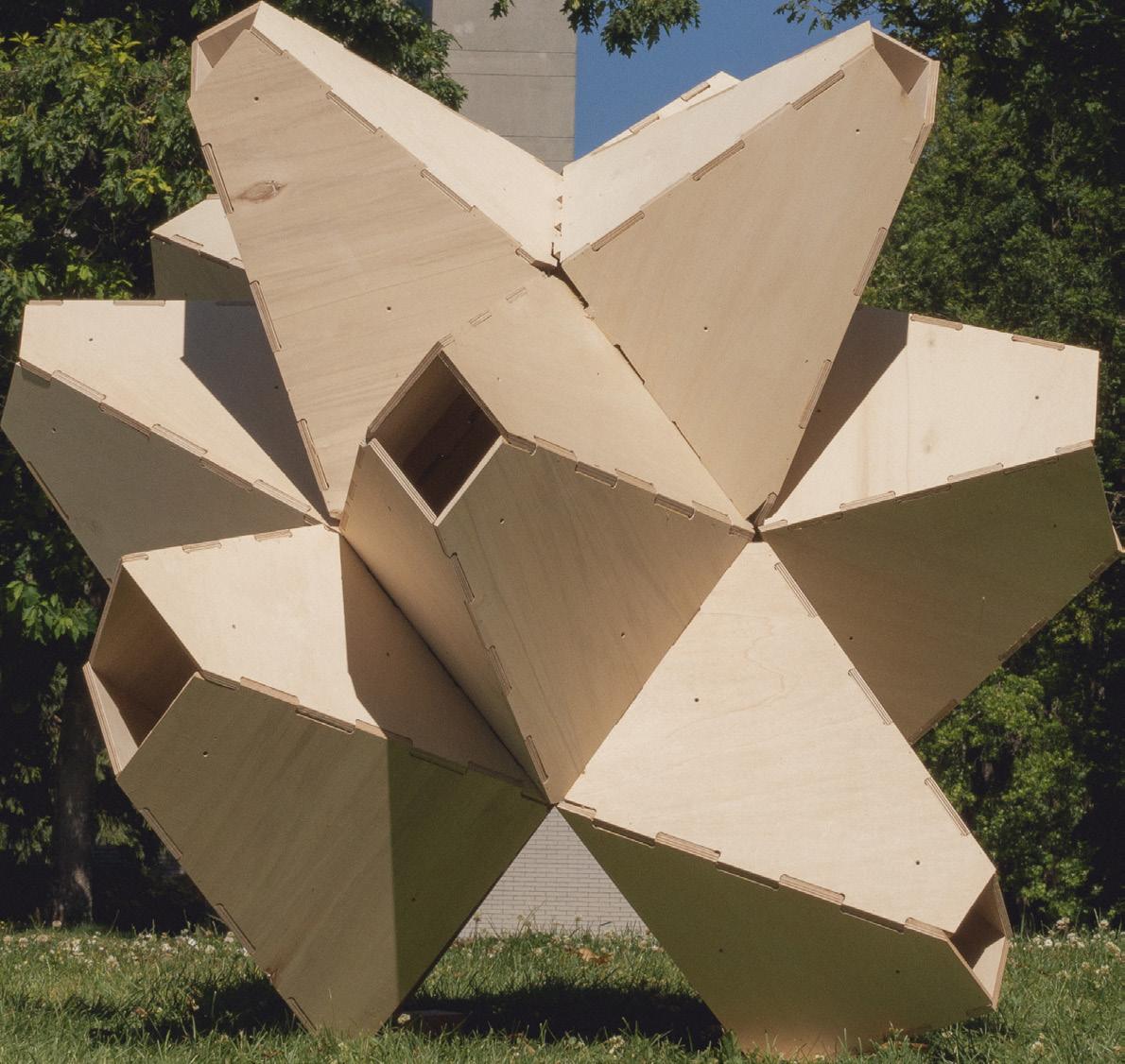
1 minute read
Geode
June 2022 - July 2022
UBC Performative Wood Seminar
Advertisement
Instructor: Annalisa Meyboom
Team: Julieta Alva, Nick Krahn, Richard Mohammed
Developing a fluency with parametric design and an understanding of the implications robotic fabrication has within the built environment was the goal of this seminar. Using Grasshopper 3D parametric modelling software and UBC’s 8-axis Kuka robotic area, we were challenged to design and build a wooden structure using a repeated structural component that could come together without the use of fasteners or glue.
Over two months, our team of four designed and constructed a 1 m tall geometric structure maded up of a repeated diamond extrusion joined by a box-joint. The primary challenge of the design and fabrication process was ensuring that the unique orientations of each interlocking panel was accurately accounted for in the parametric code and the specific angles in each box-joint connection could be machined by the robotic arm on a specified thickness of material.
The design began with the intention to create a human-sized lantern articulated with different aperature sizes extruded and skewed in different directions, similar to an amethyst gemstone. The inital massing began with a simple capsule form segmented using a diagrid. Aperatures were extruded using the centerpoints of each diagrid. Its size, extrusion length, and direction were parameterized and varied using a random generator.
Challenged to construct our structure without the use of glue or hardware, our group developed a box-joint connection that leverages the capabilities of both parametric design and robotic fabrication. The angles of each panel relative to adjacent panels were precisely captured by Grasshopper and used to machine the unique connection at each joint. Panels were cut out of 3/4” marine grade plywood using the robotic arm.
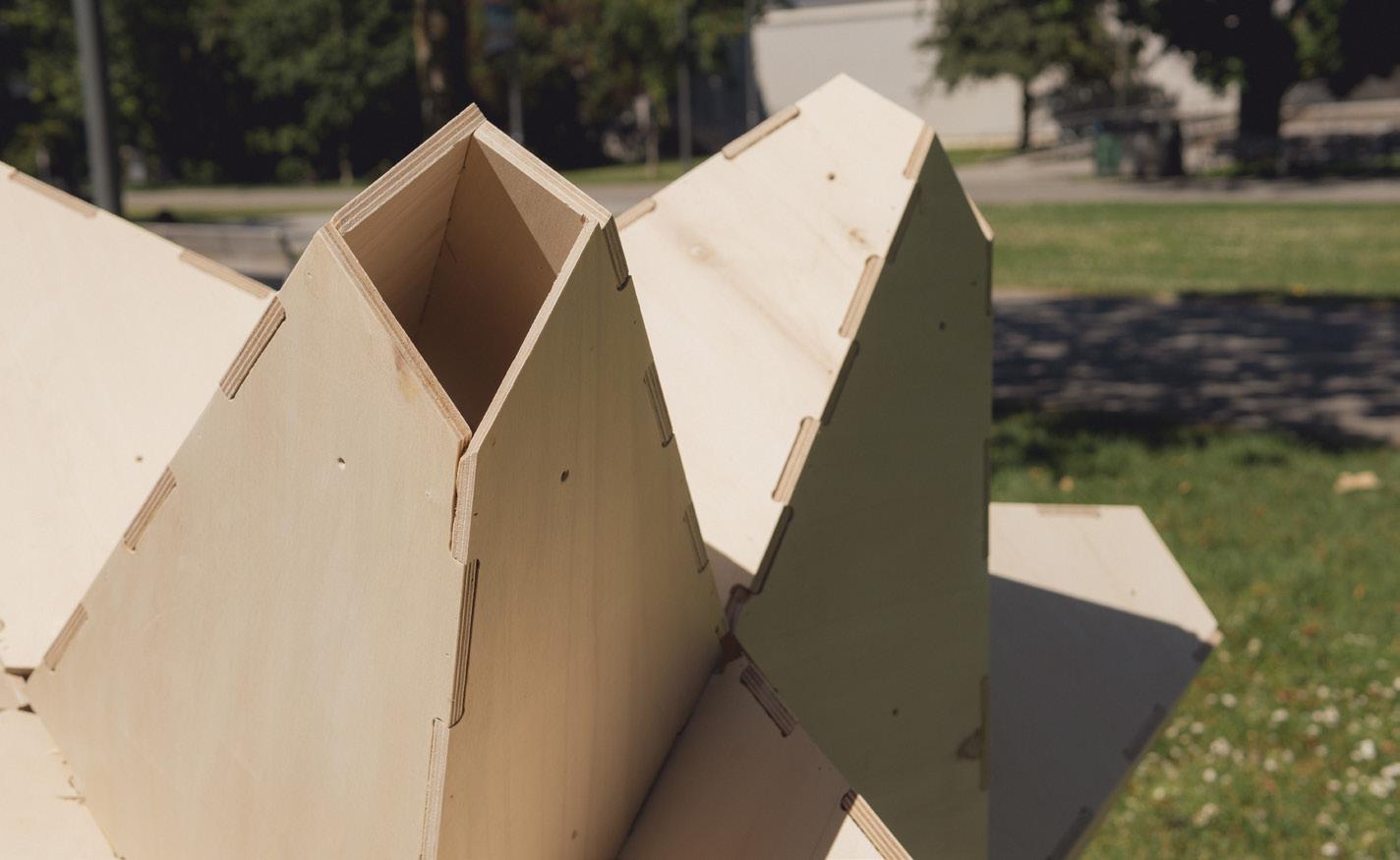
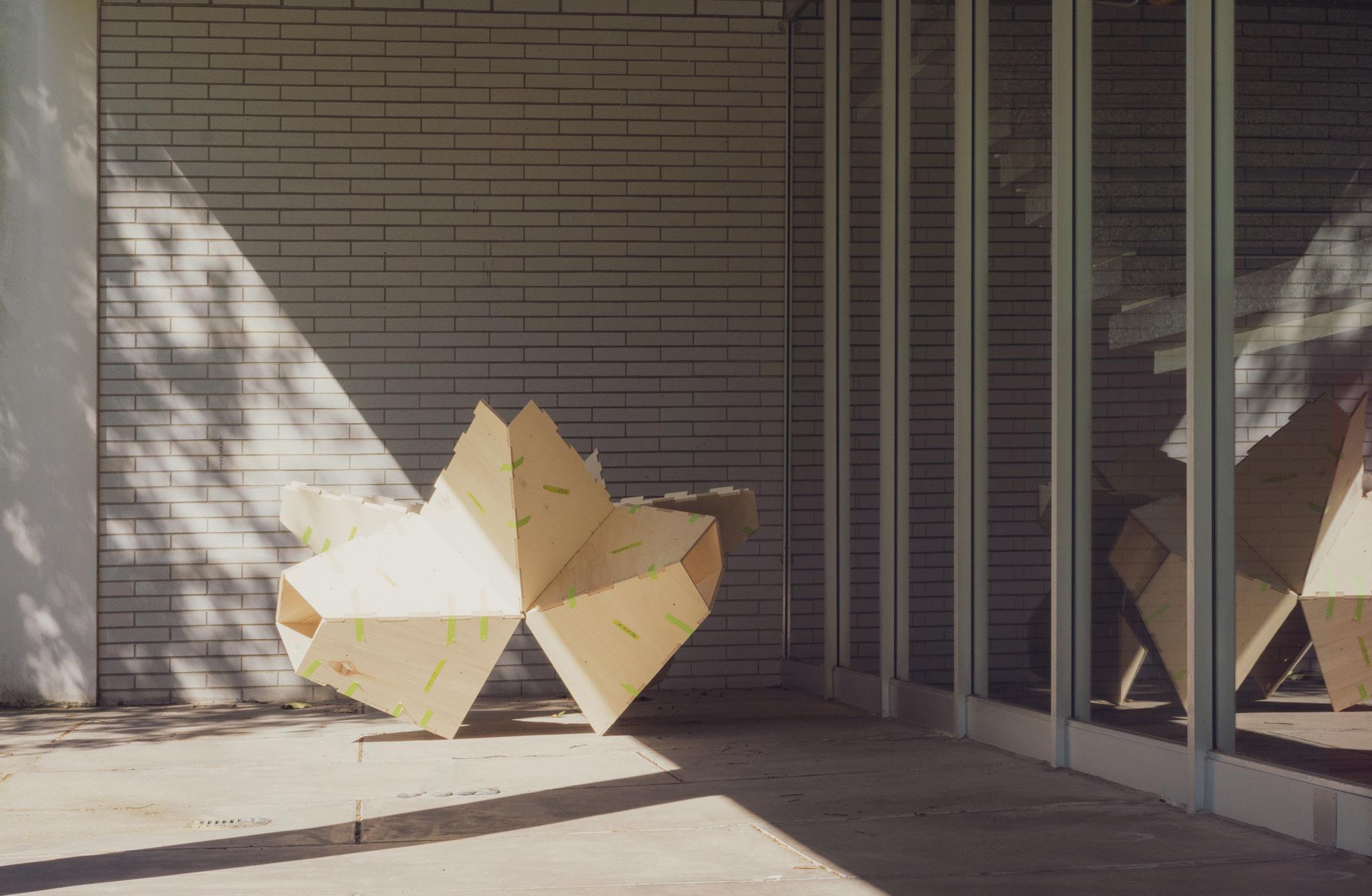