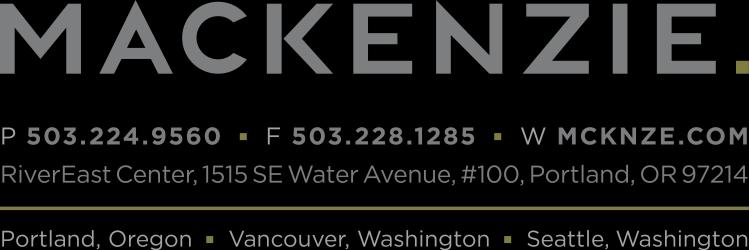
DATE: July 09, 2024
TO: All Staff
FROM: Design Leadership Team
STANDARD TYPE: Technical
SUBJECT: Quality Control
Expectations
Introduction
DATE: July 09, 2024
TO: All Staff
FROM: Design Leadership Team
STANDARD TYPE: Technical
SUBJECT: Quality Control
Expectations
Introduction
The purpose of this guideline is to outline the expected procedures to complete the Quality Control (QC) procedures for projects. As opposed to Quality Assurance (QA), which is the defined as how we design and carry out projects to assure quality, QC is focused on the process to validate that the design work has been completed to meet the standard of care and the Mackenzie Platform goals for projects. This requires that all team members, including our consultants, participate in the evaluation and verification of the design work. Construction Documents are never perfect, that is why the construction process has RFI’s, ASI’s, COR’s, and Change Orders. That is also why the Owner and Contractor often carry contingencies in their budgets. Nevertheless, we are always on a quest to strive for perfection. Following the QC process is certainly a part of that quest.
Depending on the project size and complexity, the frequency and specifics of this QC review will vary. The intent of the guideline for QC is to be general enough to be applicable to a majority if not all the projects at Mackenzie. This contrasts with the QA guidelines that are specific to each discipline; knowing that the process for how we complete the design for projects varies by discipline. Currently the QA guidelines for the disciplines are being developed and will be available soon. The Principal-in-Charge, Project Manager, Architect/Engineer of Record, and Design Lead will discuss the specific nature of the project at the beginning of the design effort and agree on the process to be used.
Things to consider in this discussion:
▪ Has this team (including Client, Consultants, and Contractor) recently successfully completed a similar project?
▪ Complexity of project (from speculative shell to intricate manufacturing Build to Suit).
▪ Fee, as an approximation of effort
▪ What unique conditions exist on this project (e.g., new Client, new building type, new location, new team members, unique design opportunities, etc.)?
▪ Have we worked with the jurisdiction before?
▪ What is the project schedule like? How will that impact the design and QC process?
▪ Will technical reviews be done by a single individual or split into areas of focus (e.g., envelope, code check, egress, etc.)?
Quality Control Standard
July, 09 2024
Page 2
▪ What review process is going to be most productive at each milestone/role (e.g., page turn at major milestones, Bluebeam Sessions for weekly reviews, etc.)?
It will be up to the project leaders (PIC/PM, AOR/EOR, Design Lead) to establish the required frequency of these reviews and work with the Project Manager at the start of the project to document this expectation for the team. The intent is that this guideline will be used as a tool to facilitate and be the basis of the QC plan from the initial concept plan all the way through completion of construction. The PM will develop a project schedule that conveys this review frequency and coordinate efforts with the team based on the QC matrix and the narrative.
At the start of each milestone QC review, the PM will circulate the QC Review Form (see template in the PM Dashboard) that the various parties engaged in reviews will date and sign. All the PIC/AOR/EOR’s should see the signed form before signing or issuing sets. These forms will be saved in with the Checkset Drawings on H:\ with the project for internal documentation that the QC process was completed.
It is expected that the QC reviews at each of the milestones is to be completed before drawings and specifications are submitted to the client, for pricing, permits, bidding, or final construction documents. For exceptions and nonstandard situations, see the discussion “Non-Standard QC Process.” In addition, the PIC will see to it that the design team implements the protocols appropriately on each project, for each phase, including construction. If these are not followed and issues arise – whether in project timelines, constructability, or financial performance – the responsibility is borne by the PIC. End of year discussions with PICs will specifically focus on engagement and success within this program.
The Design Leadership Team has outlined a recommended protocol to follow to complete a successful QC effort. It is understood that this recommended protocol may not be possible or practical on some projects. If this recommended protocol is not implemented, the PIC and the rest of the project leadership team will need to inform the project team what QC steps will be followed and document completion.
To help facilitate the QC process a matrix has been developed that outlines the expectations for different types of projects and the different reviewers. The matrix is intended to be an outline and a guide. As outlined in the introduction, for each project the team must decide and outline the QC process. Also included is a narrative that is a companion to the matrix that gives insight regarding the roles of the reviewers and the intent.
Quality Control Standard
July, 09 2024
Page 4
Quality Control starts with doing the work well and checking your work as you go. To complete this process effectively and efficiently, each member of the team has a role to play. There is a rhythm and flow to this process that each project should follow:
1. Production:
A. As staff work on a project, they should be sure that they know:
I. The Discipline Lead and Professional of Record’s expectations for the outcome of their efforts
II. The amount of time expected to complete a task
III. What “done” looks like
B. Ask questions and engage the rest of the team in the development of the design as you proceed.
C. Once a task is completed, staff should back check their own work before providing to next in line for QC review.
D. Complete a summary that discusses areas you would like focused review and areas where you are not complete yet.
E. Sign and date your completed review.
2. Discipline Lead
A. As Production Staff are working, the Discipline Lead shall provide oversight and direction. Ask questions of those working with you to gauge their understanding of what they are working on.
B. Together with the Professional of Record, identify what lessons learned from prior projects will be incorporated into this design effort and provide direction to the production staff.
C. Answer the production’s staff questions in a timely manner so they can keep on task.
D. Provide information on schedule and expectations of deliverable
E. Once a task is completed and back checked by production, complete your own review Look through the documents for:
I. Questions from previous review and provide answers where you are able
II. Areas that were not developed fully and provide input on next steps
III. Overall completeness and accuracy appropriate for stage of design
IV. Constructability issues
V. Construction budget
F. If your discipline completes calculations as part of their design effort, these should be reviewed similarly to other project documents.
G. Provide direct feedback to Production staff from your review. This is an essential part of their growth.
H. At appropriate stages of the design process (as determined by the project leadership at the start of the project – see below for more discussion), Discipline Leads shall review the drawings of other pertinent disciplines and provide feedback
I. Complete a summary that discusses areas you would like focused review and areas where the team is not complete yet.
J. Sign and date your completed review
3. Professional of Record (AOR/EOR)
A. As the team is working, the Professional of Record shall provide oversite and direction. Ask questions of those working with you to gauge their understanding of what they are working on, making special attention to the concept of the design
July, 09 2024
Page 5
B. Answer their questions in a timely manner so they can keep on task.
C. Provide information on expectations of deliverable
D. Once a task is completed and back checked by Production and Discipline Lead, complete your own review. Look through the documents for:
I. Questions from previous review and provide direction
II. Areas that were not developed fully and provide input on next steps
III. Overall completeness and accuracy appropriate for stage of design
IV. Constructability issues
V. Construction budget
E. Provide direct feedback to Discipline Lead and Production staff from your review. This is an essential part of their growth.
F. Sign and date your completed review. This should be completed prior to release of the documents
In addition to the review cycle outlined above, the following other reviews will need to be completed at appropriate intervals:
4.
A. Prior to release of milestone sets designated and requiring review by the matrix, the reviewer shall review a full set of all disciplines, including the consultants’ drawings to look for:
I. Completeness: verify the documents contain the information expected for the intended purpose (PIC - do the documents have all the big-ticket items depicted or noted so they can be priced; PM - do the drawings have the detailing needed for permit approval; Design Lead – does the documentation align with the design vision that was established by the project team with the client).
II. Design suitability: PIC - Has the team worked with the Design Lead and incorporated their input appropriately
III. Meet client goals: PIC to understand how the design solves the Client’s goals and objectives. This can be through review of drawings or discussions with Discipline Leads. It is recommended that the PIC contact the client during design, at the completion of design, and at the completion of construction to assess their opinion of the design effort meeting their goals. PM to understand how the design has addressed client’s specific requests of the design team expressed through the design process. This can be through review of drawings or discussions with Discipline Leads.
IV. Design/technical issues: AOR/EOR are responsible for technical issues. PIC/PM will direct the Discipline Leads to engage in this design review process and support resolution of technical issues with the Professionals of Record. Professionals or Record have ultimate control over all code/technical issues.
V. Coordination of disciplines: AOR/EOR and their staff to confirm that appropriate disciplines have understood and addressed design challenges. PM may be needed to the facilitation of discussions between individuals or disciplines.
VI. Barriers to meeting Platform Goals: Looking for “big picture” items that may impact the project. This is where experienced staff bring their knowledge to the project and look ahead of the team to identify areas that will need special attention.
July, 09 2024
Page 6
VII. Sign and date the completed review.
A. The purpose of the designated reviewer is to be an independent, knowledgeable, experienced reviewer that can provide a fresh perspective. So often, especially on larger projects, the team can get “tunnel vision” from being intimately involved in a project. A fresh perspective can be invaluable. The intent is that the reviewer has knowledge of the type of project being reviewed. Senior experience would be preferred that can identify common pitfalls and coordination items. The reviewer can be from any discipline or could be from the same team; the reviewer cannot have worked on the project except for independent review.
B. As outlined by the matrix, the designated reviewer shall review a full set of all discipline drawings looking for:
I. Completeness: Verify the documents contain the information expected for the intended purpose.
II. Design/technical issues: Identify significant design issues of the various disciplines. Work with the team to support resolution to the items identified.
III. Coordination of disciplines: Confirm that appropriate disciplines have understood and addressed design challenges.
IV. Barriers to meeting Platform Goals: Looking for “big picture” items that may impact the project.
V. Sign and date the completed review
It is important to note that QC efforts are not limited to a review of the drawings. Often, the PIC and PM will complete their QC review of the project by discussions with the team to understand how their direction has been executed. As part of their project engagement, the PIC and PM bring their experience to help steer the project towards success. This is communicated to the team for their use in executing the project.
As valuable members of our project design team, it is important that our consultants also participate in the QC review process. It is recommended that the PM:
▪ At the start of a project, discuss with consultants what their QC plan is for the project.
▪ Include consultant team members in discussions about schedule and timing of the QC reviews and be sure to include them in any calendar reminders of QC dates.
▪ Invite consultants to actively participate in Bluebeam Sessions for QC review so that they may see the entire set of project documents and provide comments.
▪ Encourage the entire team, including consultants, to complete their QC review of their documents in this same Bluebeam Session so that everyone has visibility into the set of drawings and the comments being raised.
If it becomes obvious that a consultant is not thoroughly checking their drawings and there are issues on the project, the PIC and PM should have a discussion with the consultant to encourage review of the documents and specifications.
Quality Control Standard
July, 09 2024
Page 7
There are certainly going to be times where the Client’s project goals dictate that a non-standard approach to QC reviews occurs (e.g., completing the QC reviews after permit submission to meet a financing or lease obligation date), but these should always be discussed with the entire team, including Client, Consultants, and Contractor, well in advance of these milestones and receive approval from the PIC, PM, AOR/EOR.
After a review is completed, it is imperative that the input is communicated to the right team members. Redlines, notes, or questions on the drawings are useful in advancing the project, but the most impactful exchange is when the reviewer and team discuss the outcome of the review and the outcome of that discussion can be incorporated into the set of the drawings.
At the start of each milestone QC review, the PM will circulate the QC Review Form (see template in the PM Dashboard) that the various parties engaged in reviews will date and sign. We are asking all the PIC/AOR/EOR’s to ask to see the signed form before signing or issuing sets. These forms will be saved in with the Checkset Drawings on H:\ with the project for internal documentation that the QC process was completed.
Each one of us has a role to play in the quality execution of our projects. As an issue comes up, ask questions and be sure everyone understand the expected result. As work is completed, be sure to scrutinize the product, and check your own work before passing it on. Ask yourself “did WE deliver on expectations”? Look at the results with a critical eye. This process is not intended to slow down the overall design process but taking the time to validate work as it is done at every level will yield intended results for the project and for your growth as a professional.
The Quality Control process as outlined above is a critical element of project execution. Your engagement in the process is crucial. If you have questions, do not hesitate to ask the project PIC or PM, your discipline Director, or someone from the Design Leadership Team.
FAQ
1. I am the PIC on a new project. This is the fifth project of this type my team has worked on for this client. Do I still need to follow the QC Policy? Yes. Every project should have some level of Quality Control, as we are all human and can still make mistakes, even after having already done something four times before. Suggest looking at the project and identifying what is unique or has potential for risk and then tailor the QC efforts for this project around those areas. The AOR and EOR should ensure that their drawings have been executed to meet the standard of care.
2. I am the PM on a project similar to ones I have done many times before. With my experience setting me up for success, what am I expected to do for the QC efforts for this job? As PM, one of your responsibilities is to ensure that the team is following the QC guideline. While you may have experience with this project type, it is likely that not everyone on the team will. Use your experience to help guide them towards success, but also manage the team to follow the QC guideline. Set up your schedule to allow the team time to conduct their reviews. Have discussions with the team about their progress and what you can do to support their successful design efforts. Get them to sign the QC Review Form. Have the Lessons Learned meeting and provide that feedback to the right parties.
3. I am PIC on a several projects all in design. How am I supposed to review all these drawings and specifications and provide feedback without holding up the project? QC is not just reviewing drawings. It is recognized that as PIC, weekly drawing reviews is not always possible. Be engaged in the project with
July, 09 2024
Page 8
the team. Asking questions, listening to the answers, and providing input is a form of Quality Control. Use this engagement to look ahead in the project and anticipate issues to help team successfully meet client goals. Ensure that others on the team who have more time are focusing on the appropriate level of drawing review. Spot check issues you note as critical in the drawings to achieve a level of comfort in the product. As the person who is ultimately responsible for QC, you don’t need to “do”, but rather ensure QC gets done.
4. I am working on stair sections and details for the first time in my career. How can I provide QC support on this work that I am not familiar with? Will I really know if what I did is right or wrong? Every design solution has something unique with it, so the fact that this is your first time doing this work doesn’t limit your ability to QC your work. Here are some things to think about:
A. Everyone should ask questions when assigned a task – make sure you understand the assignment fully.
B. Identify the critical elements of your task and as you are working on it, engage others (the Project Architect or Engineer in this case might be good resources) to be sure you are headed toward the correct solution.
C. As you complete a portion of the work, look back at your work and ask, “does this look right?” or “does this connect to the rest of the project the way I thought it should?” or “do I have enough information here so that someone can price it/permit it/build it?” (depending on phase).
D. Ask others for examples of projects that were successful and compare to your work
E. Back-check your work as you go.
F. Ask for input from other reviewers when you get redlines.
5. My project is in construction and our client asked us to change the entry canopy design. I am preparing drawings for a Proposal Request to issue to the contractor. Since we already completed the QC process for Permit/Bid documents and checked how the canopy integrates into the skin, drains, and meets local design requirements, do we need to QC this again? These drawings should have a QC review. With a new design, there is a need to check that the design is appropriate. This will likely be a fairly brief review as it is a fairly succinct scope. Just because the design is happening during construction, after the final set of documents doesn’t mean that Quality Control is done. QC happens at every step of design.