
3 minute read
Sponsored Content: Avante Health Solutions
Avoiding Helium Loss in MRI
BY MATT TALLEY
Matt Talley
Biomedical service technicians know that expectations for expertise across multiple forms of equipment can easily become overwhelming. Hospital staff expect you to have the answers to the problems they are experiencing. Whether you service general medical equipment, or specialize in some form of imaging modality, hospital staff are calling your department for help. In the case of MRI, round the clock coverage is required. If responses to certain MRI problems are not addressed immediately, it can result in extremely costly or extensive repairs. Imagine being on call and you get an urgent service request from the MRI department. You know that certain MRI failures require immediate attention, but you don’t really know MRI systems very well. What should you do? Who should you call? The first step in managing the situation is to familiarize yourself with some basics before there is an emergency, so let’s talk about it.
Safety: The most important consideration when dealing with MRI is … safety! I know we have all heard the safety mantra a million times so it’s easy for some of us to just tune out when we hear the word, but MRI is unlike any other machine you will be exposed to in a hospital. Don’t gloss over the very real danger of this machine. The scan room has a high-powered magnet that is always on. Do no enter the scan room without first having specialized training or unless you are under the supervision of an MRI technician/engineer.
A major concern for any hospital/MRI department is the loss of liquid helium. Many urgent calls for MRI will be the result of a failure in one of the components necessary for preventing the loss of liquid helium. Usually the service request will state, “coldhead is off” or “not chirping.” The coldhead should be running 24 hours a day, 7 days a week. If it is off – or “not chirping” – time is of the essence.
The components necessary for maintaining liquid helium levels are: 1. Coldhead 2. Coldhead compressor 3. Chilled water supply (Chiller)
Before you ever get a service call for an MRI, you should try to identify these components and any associated gauges and service indicators. There are many variations of coldhead compressors, chillers, plumbing line, etc. Therefore, it’s best practice to observe them when operating normally. In most equipment rooms you will find supply and return chilled water pressure gauges, and sometimes temperature sensors with visible readouts. Mark any pressure gauge or temperature reading with the system operating normally so you know what it should be. Most chillers will have run and fault indicator lights. The coldhead is located at the top of the magnet vessel inside the scan room (refer to previous safety note). It is not important to physically see this component, but it is important to hear it. It should not be necessary to enter the scan room to hear if the coldhead is running. The distinct coldhead “chirping” sound is typically audible from the control and equipment rooms. If the coldhead is off (no audible chirping sound) the problem will be one of the above components. Check the following: 1. Check pressure gauges for chilled water. If normal move to step 2.
Check the chiller, if no indicator lights are on, and the fans are not spinning, check if the main breaker for the chiller is on. Reset the main breaker. Try pressing the RUN or ON button at the chiller. If unresponsive and incoming power is available call a HVAC service company. If no incoming power, call facility electrician. 2. Check coldhead compressor
Error on compressor display? Try resetting compressor. Check incoming power. If incoming power and chilled water are OK, call MRI service engineer.
Avante has remote MRI monitoring available to help prevent these issues. Call us today.
Matthew Talley is an MRI support specialist.
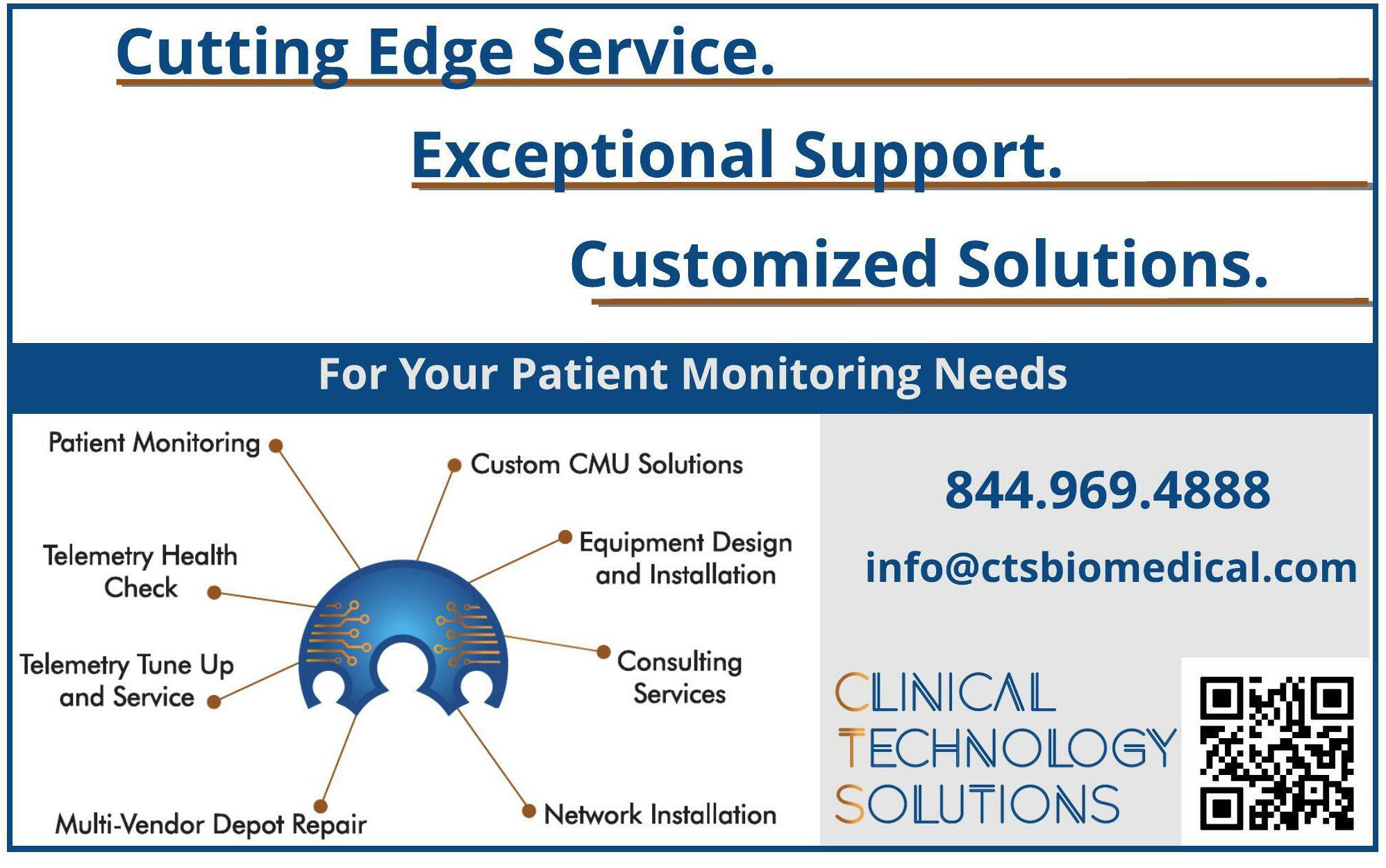
