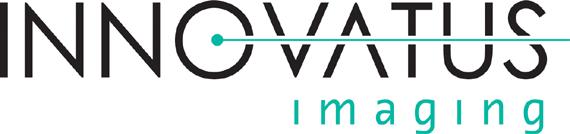
3 minute read
Sponsored Content: 20/20 Imaging Insights
20/20 IMAGING INSIGHTS
SafeTEE Process Analysis Program = Proven Cost Savings
BY MATT TOMORY
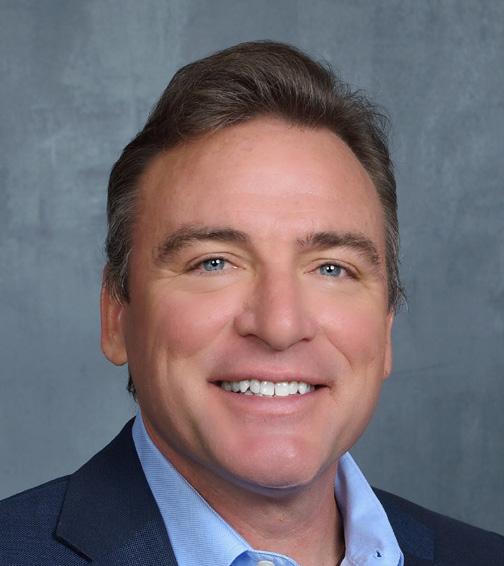
Matt Tomory
When it comes to imaging devices, little things go a long way. And not always in the right direction.
A little slip of the hands could cause trauma to a TEE probe, and according to years of data from first-hand experience and researching common failures, trauma is one of the leading reasons for costly repair services. In fact, many believe that “biting” is one of the primary causes of traumatic damage, yet research conducted by our Centers of Excellence show that poor transportation practices and poor set-up practices are a much higher cause.
Additionally, the process of disinfecting a transducer with traumatic damage, such as a hole in the bending rubber or crack in the distal tip, is one of the primary causes of irreparable catastrophic damage.
Research also shows that many of the little things that lead to big repairs are easily avoidable by training staff in key processes for handling, cleaning and storing. Repairs and replacements can add up fast. Consider the following typical costs you could incur: • Exchange through an OEM may range from $12,000 to $50,000 • Exchange through the third-party market may range from $5,000 to $40,000 • Cost of repair may range from less than $500 to about $10,000
By implementing the SafeTEE Process Analysis Program, facilities of all sizes can drastically reduce their cost of operations and ownership for TEE and other types of probes. For example, our clinical experts pioneered TEE care and handling assessments as a means to assist customers with failure prevention.
Our pilot customer “owned 10-TEE transducers, yet experienced 28 catastrophic failures stemming from trauma and gross fluid invasion in a single year.” By modifying key steps in cross-functional processes, this customer achieved the following results: • 50% failure rate reduction in year 1 • Additional 31% failure rate reduction in year 2 • Translated into a 44% cost reduction for a 3-year trend • Resulted in increased customer satisfaction Crushed Insertion Tube
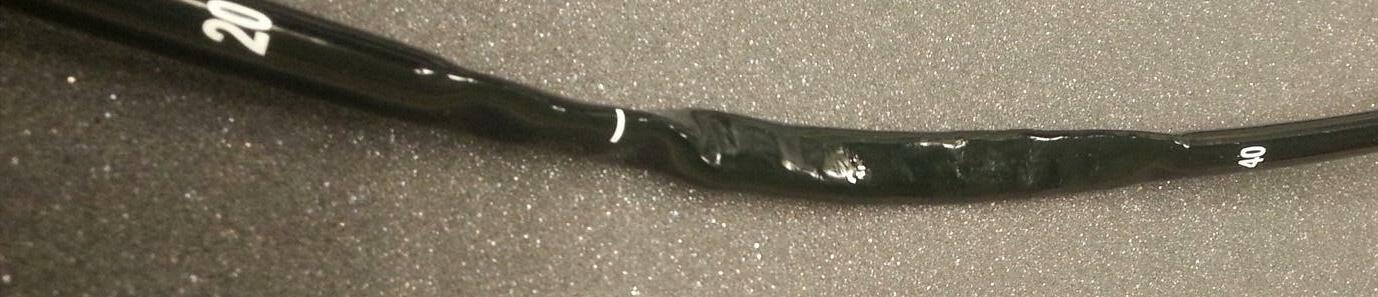
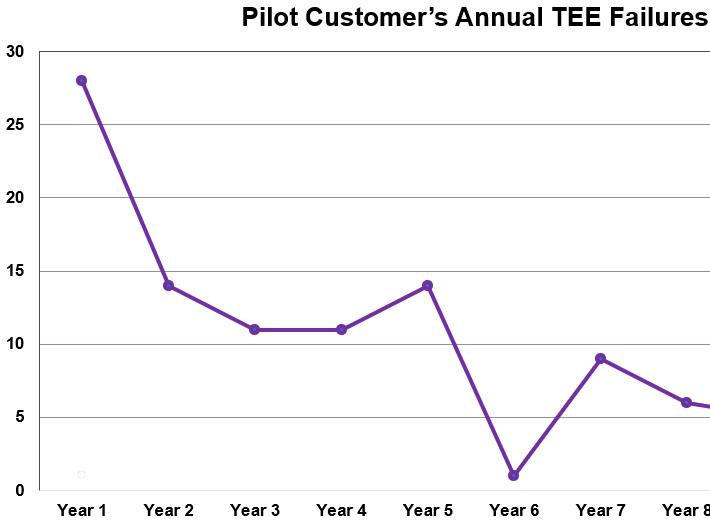
Annual TEE probe failure rate from Innovatus pilot customer.
Here are a few of the steps that have helped cut costs and failures in half. Determine a Benchmark and Starting Point: • Compare existing processes with industry best practices • Monitor and observe how staff behavior aligns with these best practices • Partner with Innovatus Imaging, the pioneer in TEE process analysis, to “observe” (as sometimes insiders don’t see what others see). • Review observations to determine weaknesses, strengths and resources needed to achieve goals Develop a Plan: • Define what processes should be modified and the managers able to implement change • Determine who is responsible for assuring staff compliance • Establish goals and how to measure team success Act, Monitor and Repeat: • Educate end-users regarding best practices • Integrate as many best practices as possible • Monitor compliance frequently • Perform preventative maintenance on all TEE probes Report and Analyze: • Use worksheets, controls and other tools to empower employees to self-report or suggest improvements • Capture photographic evidence • Highlight good practices and identify areas for improvement The money saved by eliminating several catastrophic failures with the above steps can often justify the expense of one employee to fully manage this process. With over 20 plus years, we’ve proven that following these tips can potentially save facilities 50% or more in TEE probe maintenance costs, regardless of size and patient volume.
The Process Analysis Program is just one of the segments in our comprehensive SafeTEE program. Our experts provide your teams with the tools and training needed to become the TEE experts in your facility.
To learn more about the SafeTEE Program, go to innovatusimaging.com/safetee or contact us at safetee@innovatusimaging.com.
Matt Tomory is the vice president of sales and marketing at Innovatus Imaging.
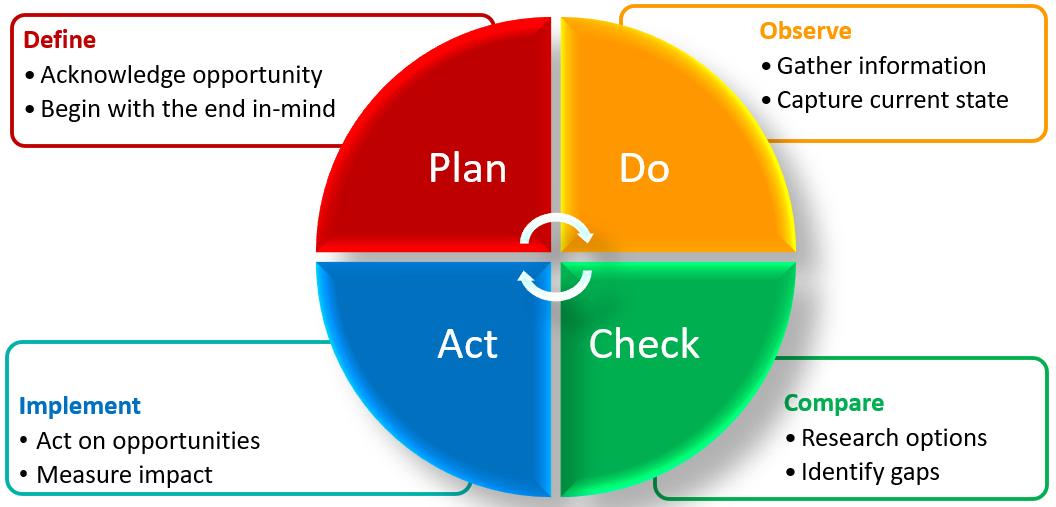