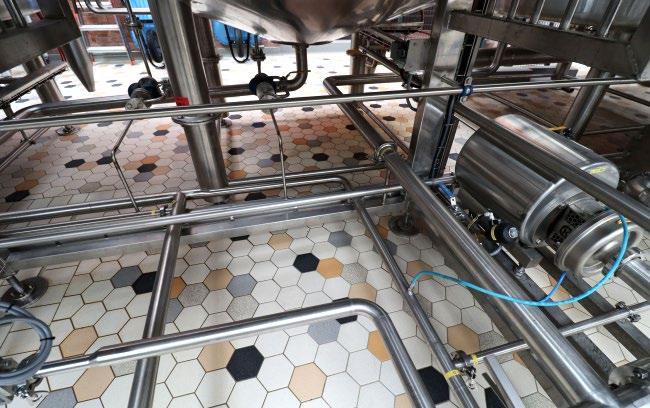
3 minute read
THE FLOORING CHALLENGE
It cannot be denied or underestimated that breweries have their specific flooring and drainage challenges. These can be related to hygiene, large liquid discharges, chemical resistance, health and safety (H&S), longevity and can even be determined by the lease of their brewery building.
Other factors include heavy traffic, impact from casks, beer, acid and caustic spillages; thermal cycling, aesthetics and humidity. These requirements influence floor design, drainage and materials selection.
Concrete, a highly robust flooring material that structurally supports any building, is widely used in breweries and has its own disadvantages. Concrete is porous and can absorb liquids, beer and caustic cleaning chemicals that can attack the cement matrix- resulting in the rapid breakdown of a concrete surface or worse. Concrete can dust when trafficked, which is far from ideal in a food & beverage environment. What’s more, the material can also deteriorate due to regular use from vehicular traffic, movement of heavy kegs, and pallet trucks.
A concrete floor is very important as it’s the structure that supports the building and the weight of any brew kit or fermentation vessels. A concrete floor is expensive to replace, so all efforts should be made to protect this very important part in a brewery.
Finding Your Fit
Hygiene should be a top priority and brewers must ensure that their flooring solution has a hygienic surface, and it meets strict hygiene standards set for the food and beverage (F&B) industry on avoiding microbial growth.
According to EU law, any floor in a F&B facility should be impervious and easy to clean, concrete on its own does provide this. Durability is next in importance, any flooring solution must be able to withstand rigorous cleaning that involves highly corrosive chemicals such as caustic and peracetic acid, thermal shock from hot water, high temperatures, thermal cycling and steam.
It’s also worth remembering that an appropriate drainage system, which is often-overlooked and under-specified, must also be installed to take away the waste liquids associated with beer production. It is recommended that either stainless steel, fully welded drainage channels or stainless-steel floor gullies are used.
These should be installed as near as possible to areas where the spillages or discharges take place - so that pipework can be directed straight into the drainage to avoid spillages running over the floor. In addition, an ideal drainage solution must include drainage “falls” which is another EU stipulation. Drainage “falls” also save clean down time as spillages don’t have to be squeezing away to drain. Flooring is a long-term investment, and brewers must conduct in-depth reviews of their facilities based on workload and their specific environment to identify key requirements before selecting a flooring solution.
Seeking external help from experts is a great way of getting relevant recommendations. For instance, Kemtile we advise breweries on all aspects of selecting appropriate flooring including tiling, drainage design, hygienic walling systems and much more that enable brewers to improve health and safety whilst leveraging longevity.
Health And Safety
It goes without saying that spillages from water, chemicals and beer are common occurrences in brewing environments. Constantly wet floors lead to slippery floor surfaces that can result in an increased risk of slips, trips and falls. In fact, statistics from HSE show that slips and trips are a major cause of injuries in the UK workplaces. Brewers must install flooring in compliance with H&S advice and compliance by specifying slipresistant floor surfaces to reduce the risk. Moreover, health and safety isn’t a one-time thing, rather, it is an ongoing process. Brewers need to follow best practices day to day to ensure the flooring solution is maintained by regular cleaning so it retains its properties in the long-term.
Periodic on-site inspections can also be a great way to ensure the flooring is continuing to do its job effectively and brewing businesses can set these up with flooring experts once the job is completed. Choosing a flooring partner who is familiar with the industry’s process is a help here - together with proven install expertise.
Flooring specialists should be able to identify what sort of flooring and drainage is required and it does save time and effort if you are buying a ‘single source’ solution - so product and installation are all from the same company. Some providers can even offer support on other aspects of work - such as civil works - in a total turnkey solution. What’s more, brewers must also be confident that the company can meet all the required health and safety standards for the food and drink sector.
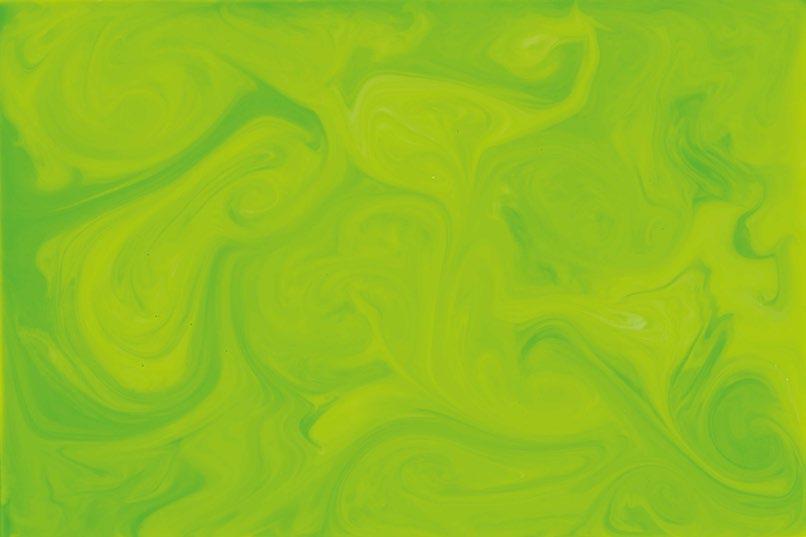
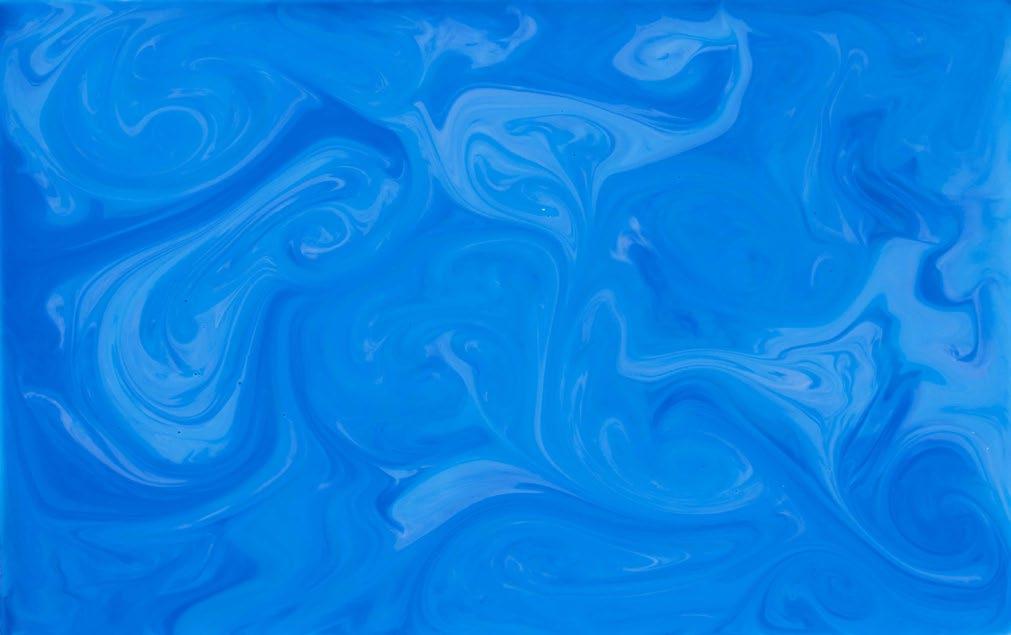
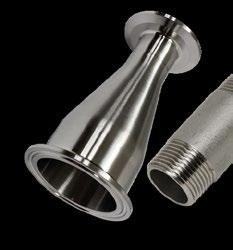
Look for providers who are certified by well-known accreditation schemes and members of respected trade bodies. Accreditations with HACCP (Hazard Analysis and Critical Control Point), CHAS (Contractors Health and Safety Assessment Scheme), EHEDG (European Hygienic Engineering & Design Group) plus membership of FeRFA (the Resin Flooring Association) and other trade organisations reassure on compliance, health and safety, quality and high performance.
