
7 minute read
OXYGEN MINIMISATION WITH CARBON DIOXIDE CONSUMPTION
TThe author was invited to present this work at the Brewers Congress in, London in December 2022. A ‘good place to be’ in terms of bulk beer dissolved oxygen in a Bright Beer Tank (BBT) would be 25 parts per billion (ppb) O2. Understanding real consumption of carbon dioxide in our production processes, and quantities available for harvesting, are the beginning of our picture of what is realistic and possible within our brewery walls…the first step in evaluating investment in carbon dioxide reclaim or enhanced reclaim processes. It is hoped that this paper will provide the toolkit for calculating what the Brewer needs to quantify. (Hint: it would be a fine project for a brewery engineering intern!) Table 1 presents data on how much CO2 is created in fermentation for an 11.2 deg Plato (SG 1.0448) wort, and the data represents the author’s past work in quantifying generation and recovery. Approximately 50% of the carbon dioxide created in fermentation is recoverable, but with use of a CO2 distillation set for gas purification into holding tank, the total recovery possible increases. A brewery distributes CO2 at a pressure about 1-2 Bar in process areas and a maximum of 6 Bar in packaging. A 100,000 hL/year CO2 consumption would be (approximately):
Processing: 553,550 kg
Packaging: 186,700 kg
Total: 740,250 kg
Therefore, 7.4 kg CO2 are required per hectoliter
The amount of carbon dioxide required to maintain the top pressure on the beer in the BBTs would be of the order of 50,000 kg when the plant is running at 100,000 hL a year. And all that gas could be recovered.
Harvesting Co2 At Lower Purities
For decades, the standard for gas purity was 99.5% and higher, yet add-on technology exists in the form of CO2 stills, where lower purity gas can be harvested. An enhanced recovery plant could be plumbed so that it it uses purge line gas from the existing plant as a feedstock.
When liquid CO2 from the bulk tank is vaporized its volume increases by 25 times, so the volumetric concentration of impurities in the gas phase is 1/25 that in the liquid. As these re-boiled gases rise through the liquid they absorb impurities
Co2 Generation And Recovery From Beer Fermentation
from the liquid. Purification efficiency can be improved by using gas from the bulk tank to absorb impurities from the liquid exiting the liquefier before it reaches the bulk tank. This process occurs in a packed tower/still. The purity of CO2 could be 90% and the upgrading would be fine.
Co2 Purity And Its Impact On Dissolved Oxygen In The Tank
Table 2 is work shared by Chaz Benedict, who did an impressive quantity and quality of focused work on Dissolved Oxygen (DO) during his employment with Hach. He illuminates that the greater the impurity (oxygen) in the bulk carbon dioxide, the direct and immediate impact on beer in BBT. As one expects, the greater carbonation required, the greater the dissolved oxygen in beer. It seems counter-intuitive to look at influence of entrapped, minute quantities of air (oxygen) in bulk purchased CO2, but it’s good to remind ourselves that there is a direct impact on dissolved oxygen in the beer.
Dissolved Oxygen In Gas Phase Of The Tank Prefilling With Beer
100 ppb DO at atmospheric pressure is equivalent to = 0.0076 mm (compared to 760 mm at sea level) - so the proportion dissolving in the beer is going to be minimal once you have a flat fill. BBTs always start filling with an agitated (sometimes it is described as ‘volcanic fill’!), but the desired fill state is quiescent so as to minimize gas absorption form the gas on top of the beer in the tank being filled.
Best Practice For Minimizing Bright Beer Tank Do Dissolved Oxygen
We can fill BBT with de-oxygenated water & then push it out with CO2, and deploy a gas-phase tolerant oxygen sensor to the outlet of a CO2-only purge, and we would see that the transition between DAW-filled tank and transition is a sharp cutoff. Compare that with purging of air by CO2 gas, and the same meter would present the change in composition of high-% air and 100% CO2 as a curve. Air and CO2 tend to mix, even with the quietest/slowest CO2 purge. Such common practices illuminates that the process requires more than just one tank-fill-equivalent of CO2. Filling the tank with de-aerated water (DAW) completely removes ALL air (so needs only a single tank-fill of CO2 to push out)
Common Standard Operating Procedures
Different breweries have differing opinions and best-practices that are applied in purging air from BBTs and other tanks: u Fill to 15 psi from bottom and purge slowly from the CIP arm twice (down to 1-5 psig) u Low and Slow: low pressure CO2 in the bottom of tank and an open blow off: Use about 4psi CO2 feed for approximately 150 minutes to on a 100 bbl BBT….15 min/10 hLs
- Reference point: to get the DO reading under 500 ppb (max)...that reads as 95% CO2 on the Zahm & Nagel tool, Figure 1 or Pentair’s device for measuring CO2 quality. u Purge properly transfer pipes / hoses / pumps etc. with DAW, and then blow out with CO2 (or nitrogen). Or purge first with CLT water, then blow out with CO2 (or nitrogen). u Purge with water from CLT then push it back to CLT with CO2
BBT Top Pressure Control
Too often we know we waste CO2 at this stage. Specifically at Step 4 described below:
1. Pressurize tank with CO2 from 0.5-1.2 barg
2. Fill with beer, displacing CO2
3. Empty tank, maintaining CO2 pressure at original top pressure
4. De-pressurize tank, venting excess CO2
5. If greater than 6 rinses have been carried out, perform caustic or acidphase cleaning.
6. If caustic-washed, purge air from tank by blowing in 1 tank volume of CO2. The following section explores quantification of how much carbon dioxide is consumed in some familiar processes: Gas required for BBT processing, Gas required for processing five Hoyer tankers each week, Gas required for processing two BBTs twice
CO2 Displacement – consumed carbon dioxide
A. Gas displaced by beer in a BBT
Assume top pressure is 0.7 barg
Density of CO2 at 1 barg =1.951 kg/m3
Mass of CO2 = (0.1)(1.7)(1.951) = 0.331 kg/hL
B. Gas released by de-pressurization
Mass of CO2 = (0.1)(0.7)(1.951) = 0.137 kg/hL
C. Gas required for purging (note that a common “purge volume” in a vertical tank is “1/7” of the tanks overall volume.
Mass of CO2 = (0.1)(1.951)(1/7) = 0.0.279 kg/hL
Total = A + B + C = 0.4959 kg/hL
Five Hoyer Tankers per week, 190 hL each
Each tanker is 19 m3 volume
Filling against top pressure of CO2 which is vented mCO2 = (1.5)(1.951)(19) = 54.58 kg… (assume top pressure is 0.5 bar g)
Each year: mCO2 = (50)(5)(54.58) = 13.6 T
Then purging usage...and assume Four tank volumes of CO2 used mCO2 = (4)(1.951)(19) = 145.5 kg
Annual mass = (5)(50)(145.5) = 36.38 T
Total consumption is 13.6+36.38 = 50 T/year
2 BBTs- each emptied twice daily, 100 hL each
Each BBT is 10 m3 volume; caustic-based CIP once/week (each tank)
Filling against top pressure of CO2 which is vented mCO2 = (2)(5)(1.7)(1.951)(10) = 331 kg… (top pressure is 0.7 bar g)
De-pressuring: Each week: mCO2 = (2)(0.7)(1.951)(10) = 27 kg
Then purging usage…assume 2 tank volumes of CO2 used in purging mCO2 = (2)(10)(1.951)(2) = 78 kg
Total weekly mass = 331 + 27 + 78 = 431kg
Annual mass = (50)(431) = 21,555 kg = 21.55 T (ie, typical for a 100,000 hL annual regional brewery)
Lagering tanks caustic-CIPd after every use: Each tank is purged by blowing CO2 through tank
Mass of pressurized CO2 displaced by beer: mCO2 = (0.1)(1.7)(1.951)= 0.326 kg/hL… (top pressure is 0.7 bar g)
Mass released by De-pressuring: mCO2 = (0.1)(0.7)(1.951)= 0.13 kg/hL mCO2 = (0.1)(1.951)= 0.195 kg/hL
Assume 1 vol CO2 used in purging air from tank after CIP...
Total Mass CO2 consumed = 0.326 + 0.13 + 0.195 = 0.65 kg/hL daily, and an Ageing tank/Lagering Tank that is CIP’d after every emptying. The calculations are all similar, and these examples form a calculation template that can be adopted and implemented for calculations in your brewery. The author hopes you find them useful examples.
Please note that decisions about how long to purge can vary widely, and there is no standard. In broad strokes, horizontal tanks would require more CO2 purging because ethe beer surface area is so greater than in a vertical tank. In the sample calculations below, the author applies different quantities of purge gas in the situations. He certainly knows that many breweries do not have gas meters to measure CO2 consumption at usage point, and that many breweries are satisfied in using a timed period of purging. Yet… a quality gas meter that displays totalized CO2 applied…is a good investment and allows a true picture of CO2 usage to present itself.
Conclusion
The brewer has several options available for recovering Carbon Dioxide, and more are coming. Not long ago, a brewery would need to approach 1 million hL a year to justify a comprehensive and robust carbon dioxide recovery system. The craft brewer today is facing unprecedented and rising costs for its CO2 purchases, and fortunately there are solutions available to them to harvest their carbon dioxide and greatly reduce outside purchases. We already see these new solution-providers display their technologies and trade studies and offer case studies. An exciting future for their right-sized engineering is on our horizon. The author, past-President of the Master Brewers Association of the Americas, is grateful for the opportunity he enjoyed in being invited to the memorable Brewers’ Congress in December, 2022 in Islington, organised by the Brewers Journal, especially as it allowed him a reason to travel from Pennsylvania and celebrate Derek Prentice being honoured. Across the author’s 39 years in brewing (which includes three years in distillation, flavoured malt beverages, natural/ botanical soft drinks and cannabis beverages), he has never encountered as inspirational and wonderful role model as Derek, whom he met when he joined as a Junior Engineer at the Truman, Hanbury & Buxton Brewery in 1984. Some years later, he had the privilege to return to the UK and work on optimisation projects at Courage Berkshire Brewery, and he was delighted to be inspired by its leaders Greg Stones and Paddy Johnson. In late 2022, he took up new employment in one of the world’s largest chocolate plants in Northeastern Pennsylvania where he appreciates wonderful and exciting processes with his (patient) Cargill colleagues who express such passion for quality chocolate… yet he knows it was his tenure in brewing beer where he found his place. He is fortunate in serving as Plant Superintendent at Cargill Cocoa & Chocolate, NA in Hazleton, Pennsylvania today.
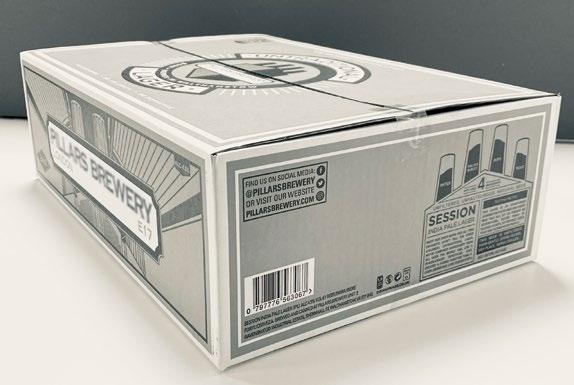
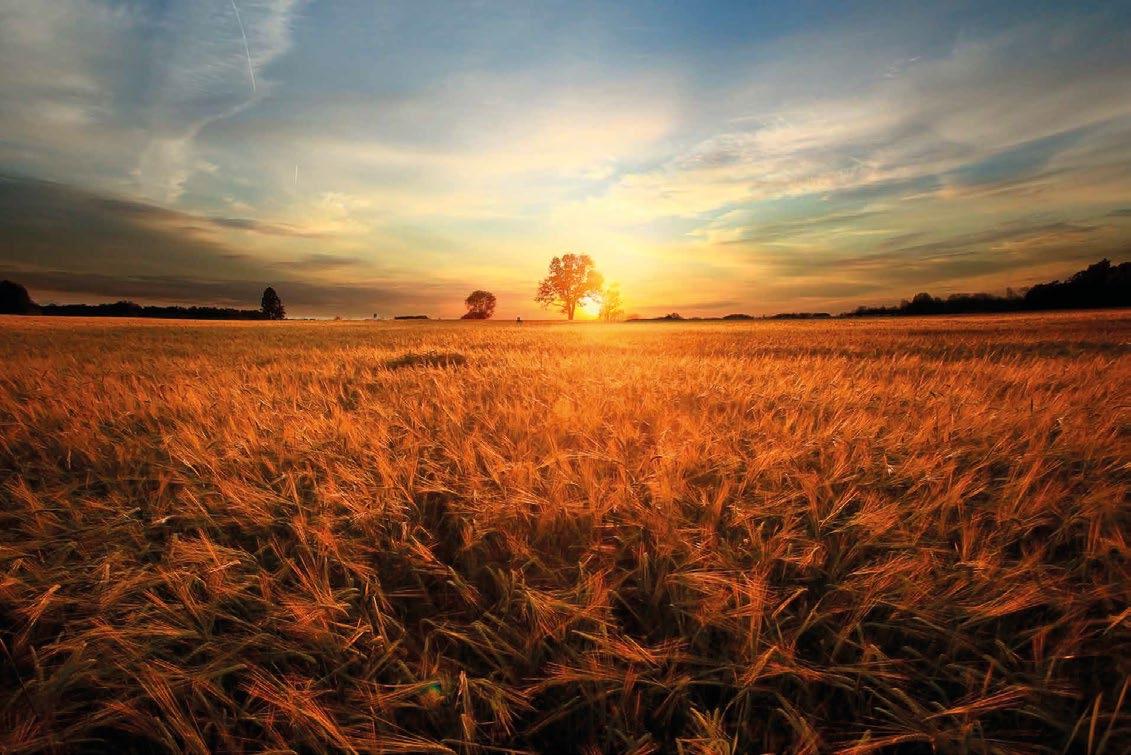