
12 minute read
Expaning education
Expanding education environments
Education and training centers expand through modular construction written by Paul Jakse, Vice President Sales, Aerogo, Inc.
The demand for additional classrooms and training facilities in the education sector has skyrocketed. The COVID-19 pandemic has pushed academia to establish healthier and safer learning environments. These new spaces often need a bigger footprint to accommodate the same number of people, plus specific safety features like enhanced air flow and ventilation. Modular or prefabricated structures have emerged as a viable answer to the demand for expanding campus education and training centers quickly and cost-effectively.
Unfortunately, modular manufacturers are not always optimized for producing these factory-built learning environments. Traditional material handling systems that move massive 12-meter assemblies through the facility can create as many problems as they solve. To economically produce boxes at speed, manufacturing facilities have turned to a tool that capitalizes on the strengths of the prefab process: the air caster.
The science of air-prefabricated modular structures fill the gap between long-term building projects and short-term space requirements. Built in controlled factory environments where weather is not a mitigating factor, the structure can be produced faster, safer, and more economically than with traditional on-site construction. In fact, a report from industry advisory group McKinsey & Co. found that “modular construction can cut schedule by 20–50 percent and costs by 20 percent,” positioning it as an ideal method to meet the immediate demand for versatile training and education spaces.
The science of air
Air casters help to fast-track more modular structures through the production line and onto the campus by reducing friction. Air casters are donut-shaped bags that fill with standard compressed air. Once fully inflated, the air leaks between the bag and the floor until the structure is lifted on an ultrathin film of air no thicker than a business card. The friction coefficient is reduced to less than one percent, allowing the structure to glide like a puck on an air hockey table, with almost no resistance from the floor surface.
Once floating, even a structure 13 meters long weighing 30 metric tons can be moved from one station to another without need of a crane, forklift, chain – or even very many people. “Just grab a few more casters, put some air into them, and boom, move,” says John McElroy, process engineering manager at Plant Prefab. This U.S.-based manufacturer designs and builds bespoke, high-end modular buildings and uses air casters in its own production processes. A single operator exerting no more than 2 to 11 kg of force can move and position a load weighing as much as 2 metric tons. Moving heavier loads requires only a modest increase in the number of additional air caster modules and operators.
The economics of air
Air casters power a degree of plant design flexibility that is impossible with other material handling systems. This flexibility, in turn, can power operational, labor, and cost efficiencies that wouldn’t otherwise be possible. “Perhaps the fundamental benefit of air casters is the ability to design creative plants,” says Jason Carter, president of advisory firm The Mod Coach, which works with modular manufacturers to improve factory design.
Air casters benefit production processes in five specific ways:
1. Air casters make it easier to move heavy and lengthy structures. “One of the most difficult and costly challenges in prefab is moving large volumetric pieces,” says McElroy. Because modular assemblies are so cumbersome to move, they require larger and more expensive material handling systems like cranes, forklifts or chain systems. Worse, the cost of the material handling system increases at a disproportionate rate as the size and weight of the assembly grows. “As a crane needs to become bigger to pick up heavier boxes, the cost increase for the crane to handle more weight is not a linear scale relative to the weight,” McElroy explains. “The cost increases almost on an exponential scale.” An air caster system, by contrast, is based on a single principle: compressed air motion. Operators can move heavier items just by adding more air caster modules. Here, the cost progression is linear relative to weight increases. Once floating, a structure as much as 13 meters long weighing 30 metric tons can be moved from one station to another without need of a crane, forklift, chain, or even very many people. Air casters are so small, lightweight, and easy to manage, they require no operator certification and minimal training. 2. Air casters require less space, so facilities can fit more structures into the same footprint. Because air casters fit within the footprint of the structure being moved, little additional space is required for maneuvering. Other solutions must be included in planning the floor layout. Forklifts require space to maneuver. Cranes and chain systems have to be built into the facility itself and, once installed, are usually permanent and unchangeable. With less production space, production throughput falls. Air casters have no such impact. With air casters, manufacturers can maximize production capacity and reduce production waste and excess travel – key objectives when implementing lean manufacturing methodologies. 3. Air casters enable plant reconfiguration. With cranes or chains, manufacturing facilities are limited to a straight-line production layout for moving assemblies from station to station. The facility cannot introduce changes that improve efficiency or productivity. By contrast, air casters are mobile, so a facility can easily change, grow and adapt, switching to a more efficient U-shaped production line, for example. Adaptability is especially
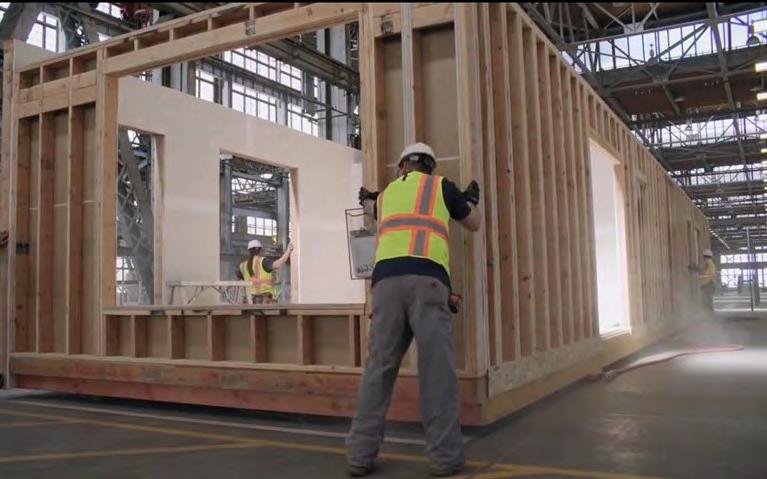
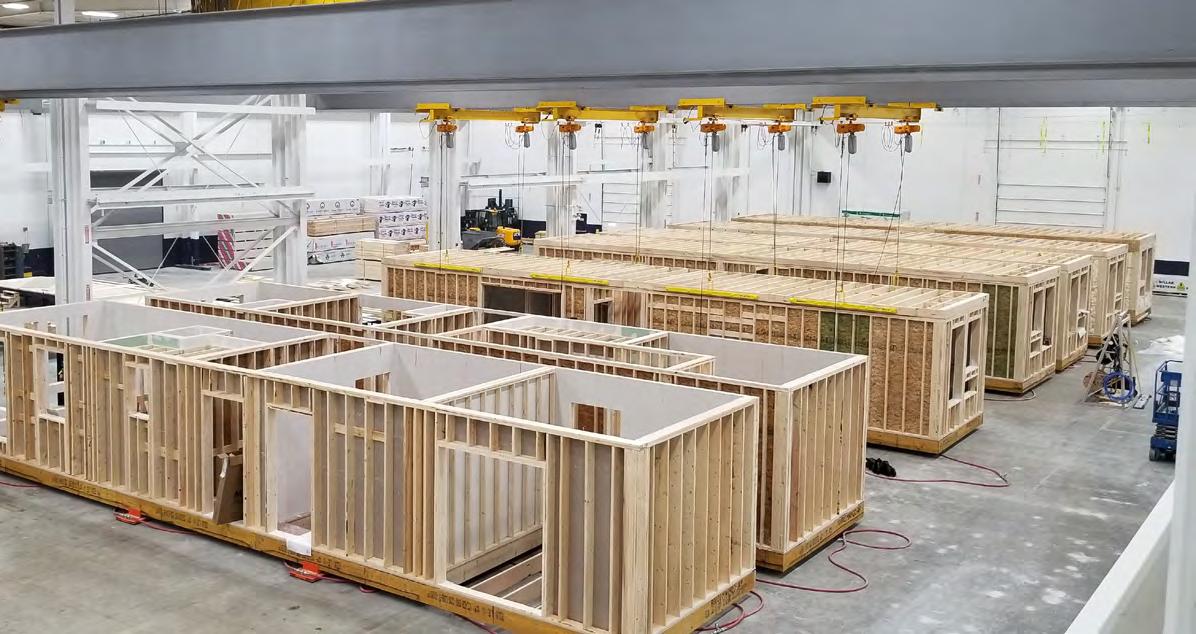
critical when manufacturing modular structures are intended for education because they often have unique structural or electrical requirements and can vary tremendously in form, function, and features. 4. Air casters reduce risk of injury. Cranes, forklifts, and chains all impose specific safety hazards. Chains in particular present a significant tripping hazard, as a massive chain may cross a number of workstations along a length stretching hundreds of feet. Due to their light weight and compact size, positioning air casters underneath the modular structure creates less risk of strain-related injuries. Since air casters raise loads no more than a few centimeters, the risk of injury due to falling loads is eliminated. 5. Air casters optimize labor and supplies. Efficiency gains can yield secondary benefits. For example, the flexibility of air casters can also be helpful in dealing with pandemic-induced supply shortages. A manufacturer who is unable to finish a structure due to supply chain issues can temporarily move an assembly out and then back to the line without line stoppage.
Outcome for educational environments
Ultimately, rising demand for additional training and education space is prompting the construction industry to rely on prefabricated structures. Manufacturers are under pressure to produce these structures swiftly, safely, and reliably. “The speed, safety, and reliability of the material handling system have to match the overall goal,” says McElroy. With air casters, modular manufacturers increase production speed and cost savings, making it possible to meet the demand for much-needed training and education facilities. “That's why we're incorporating an air caster methodology into our process. It's extremely versatile. It's extremely safe. And it's fast.”
Paul Jakse, Vice President Sales, Aerogo, Inc.
Kas Mohammed
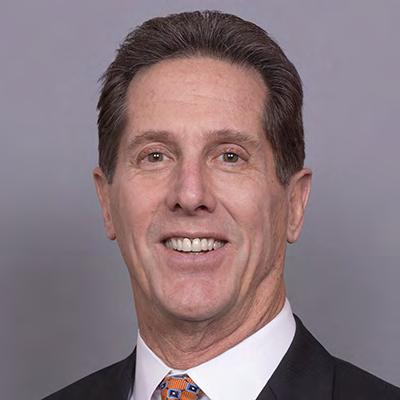
For further information please visit www.aerogo.com
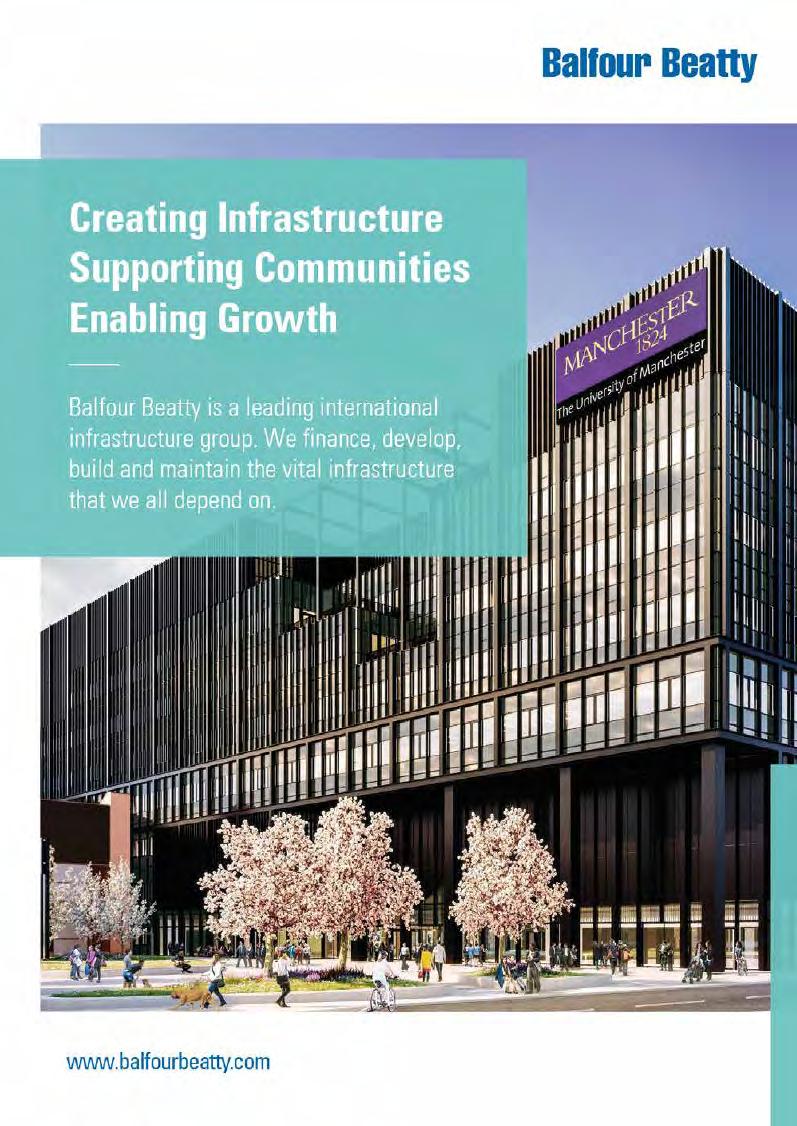
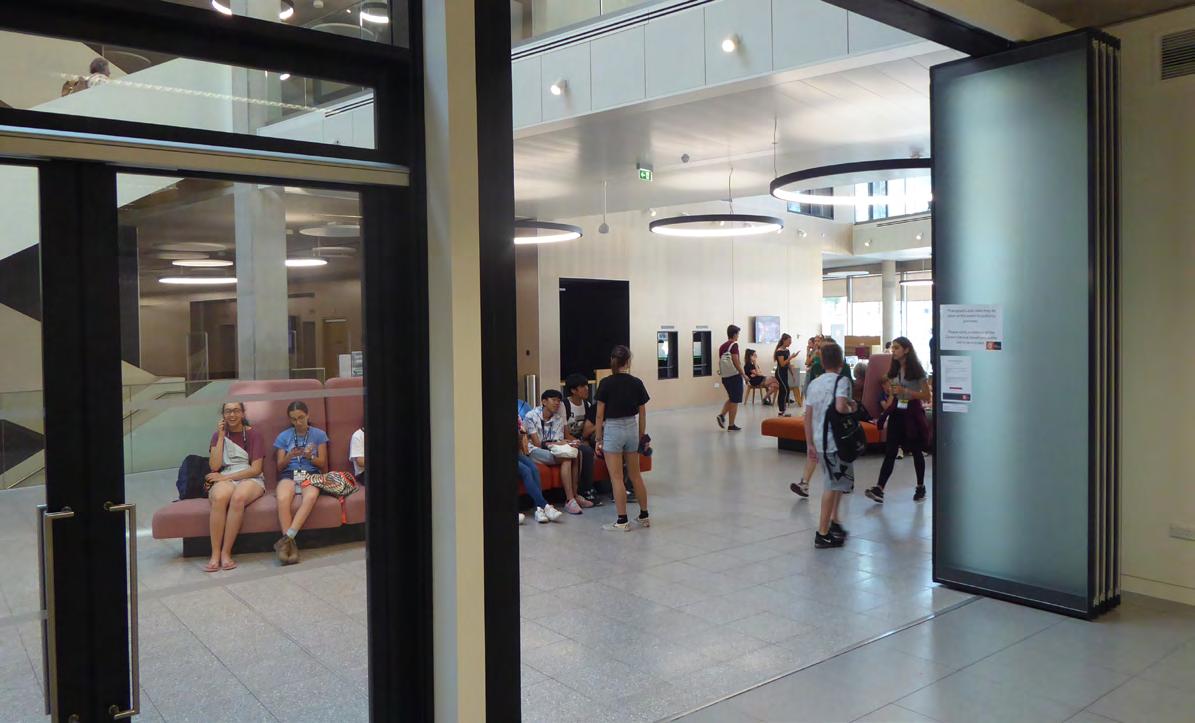
Adapting teaching space to meet the needs of the future
Julian Sargent, Group MD for partitioning experts Style, explains the applications for modern moveable wall systems
Education establishments have all been challenged during the pandemic and there is no doubt that temporary measures, such as deep cleaning, the use screens and the creative implementation of teaching bubbles, have all helped to keep pupils in school. However, the most forward- thinking schools, colleges and universities are already considering long-term options that will not only ensure a more effective response to any future pandemic but also add practical value to available teaching space. Allowing almost any teaching area to be used more effectively, modern movable walls can be used to quickly divide a classroom into two or more sections, depending on the demands of the teaching day. The space can then be rapidly opened out again as required, allowing a single teacher to work with a larger group of socially distanced pupils. Here we will outline the options for dividing space, as well as offer practical advice on choosing an appropriate system for your location, considering cost-effectiveness, longevity, acoustic performance, as well as sustainability.
Modern partitioning solutions – what’s new
Folding partitioning walls have been around for decades, but technology
has leapt forward, and current systems can deliver a truly solid divide between areas. Suitable for retrofitting into almost any location this is often the simplest option, offering rapid installation with minimum downtime.
Quick and easy to manually move into place, a folding wall can easily be opened and closed by a single teacher, as often as required throughout the day.
Sliding moveable walls consist of individual panels, or elements, that move along a ceiling track to form a more substantial partition. Rubber seals between the elements are expanded either manually, or through semi-automatic operation, which has the advantage of ensuring the optimum acoustic seal is achieved every time. A fully automatic version of this system moves the wall into place at the press of button. Pass doors can be accommodated to allow easy access between areas and to add even greater functionality to the space.
An extensive range of finishes can add functionality to a dividing wall including options for white board or magnetic elements, aesthetically impactful graphics, as well as fabric and laminate alternatives to enhance surrounding décor.
Elements can be neatly stacked to one side of the room when not in use, or in a purpose-built cavity.
At the premium end of the market is a vertical-rising partitioning wall that automatically unfolds from a space in the ceiling cavity. Apart from being incredibly impressive, this option has the obvious advantage of maximising floor space when not in use. It can also be used to divide a stepped room such as a lecture theatre or auditorium, greatly increasing the use of a prestigious facility in any school, college or university.
For a more personalised and innovative solution to divide an area, creative tracking options allow individual elements to spin and glide in multiple directions, creating small areas for collaborative learning.
Acoustics – reality check
The acoustics within any teaching facilities have been shown to have a dramatic impact on the quality of teaching and consequently, the ability of pupils to learn.
Dividing walls do not always need to offer an acoustic barrier though and it is important to consider how the areas are going to be used.
A better understanding of noise penetration, combined with the development of effective sound absorption materials, has greatly improve acoustic performance of modern moveable partitions, realistically allowing a lecture to take place alongside a noisy drama class, for example.
To make a meaningful comparison between different moveable wall systems you need to use the Rw dB rating. This is the acoustic performance achieved under strict laboratory conditions. Installed acoustic performance is given as the R’w and can be as much as 12-15% lower than the Rw dB, due to sound leakage, and will vary between different installations. Clearly, installation is key to maximising acoustic performance and it is essential to check the credentials of the team doing the work. It is worth noting that system manufacturers must approve any supplier to install their partitioning system, otherwise acoustic test certificates are understandably invalidated.
As a guideline, any system boasting 60Rw dB will deliver
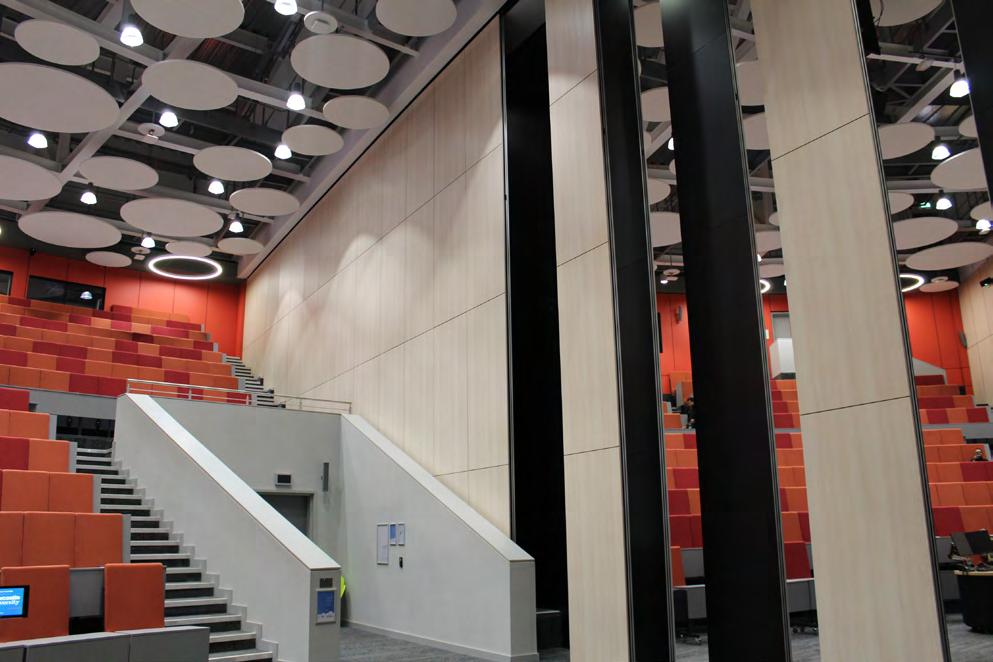
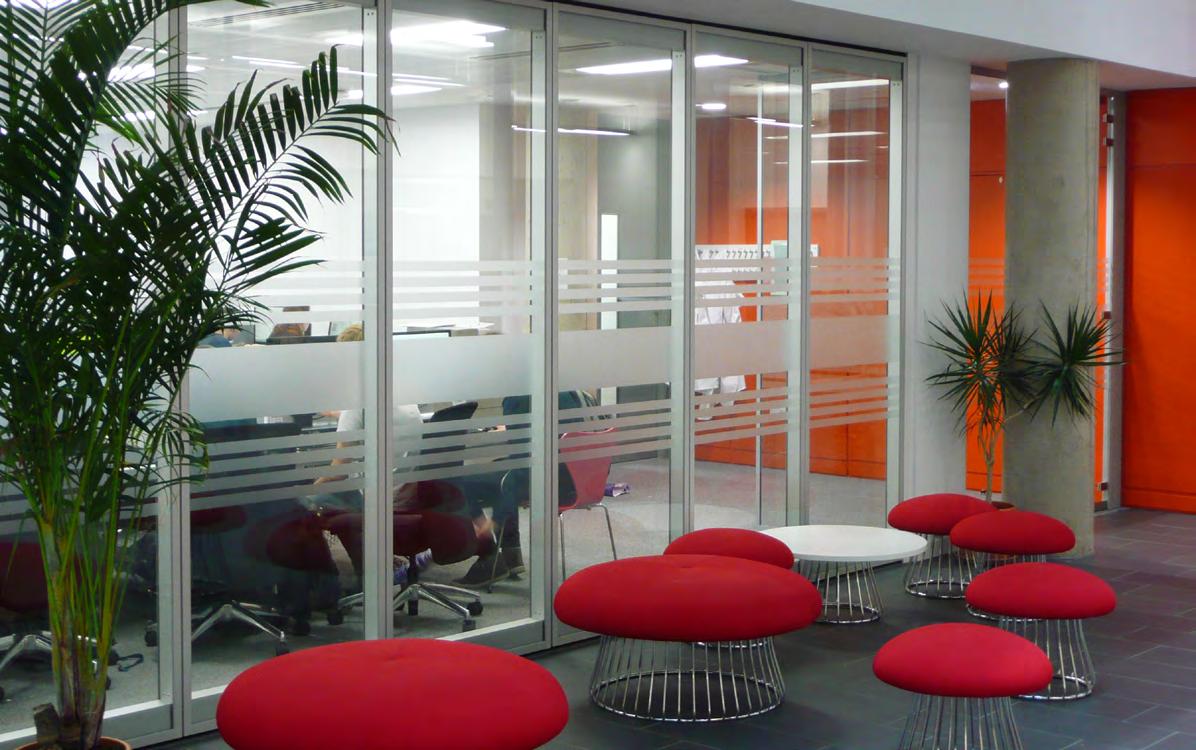
impeccable acoustic performance, giving privacy to both sides of the moveable wall. Anything above 50Rw dB should be a good quality solution that will allow the space to be used flexibly. Glass partitioning walls are popular and, with integral blinds, can deliver a good compromise between light and the need for privacy. Acoustics should still be in the region of 40-50Rw dB which is perfectly adequate for general teaching situations.
An independent verification scheme is run by the FIS (Finishes Interiors Sector) website, where you can check the authenticity of any acoustic test certificates - https:// www.thefis.org/knowledge-hub/ specifiers/acoustic-verificationscheme
Protect your investment – service contracts
Routine servicing and timely repairs can dramatically extend the lifespan of a moveable wall, helping deliver an excellent return on your investment. A risk-assessment will indicate the frequency and nature of your maintenance schedule but as a general guideline, we recommend that for a fully automated system, a trained engineer should visit the site bi-annually.
Helping reduce the risk of unscheduled downtime, a service contract provides regular testing and repair, ensuring the wall is always safe and legal. You do not have to use the manufacturer or installer responsible for the initial work. Take the time to compare quotes and check the small print to ensure any contract offers a full service rather than a ‘due diligence’ visual inspection which may not satisfy health and safety obligations.
The green divide – sustainable schools
Any building development within the education sector needs to consider the project’s carbon footprint. Any operable wall system that carries an Environmental Product Declaration ISO 14025 (EPD) offers verified and comparable information about its environmental performance and is the pinnacle of product sustainability for anyone seeking BREEAM, LEED and SKA rating certification.
If an EPD is not available, consider the recyclable content of the system, aiming for at least 97%. Creative use of rapidly renewable resources such as soy or eucalyptus is an obvious plus, as are fabric finishes.
For a long-life span, individual elements of the partitioning wall should be easily separated, allowing for easy replacement or system upgrades in the future.
It would be useful if the chosen installer has accreditation under the ISO 14001:2004 Environmental Management System, ensuring all operational processes will maximise sustainability goals whilst limiting wasted resources.
Adaptablity is key - beyond the pandemic
Improving the flexibility of available space in your education establishment is not just relevant to allow social distancing measure in the event of a pandemic. Adaptable teaching space ensures resources are maximised at all times, allowing greater creativity in the daily timetable and the ability to create a forward-thinking educational environment that is welcomed by both students and teachers.
For further information please visit www.style-partitions.co.uk