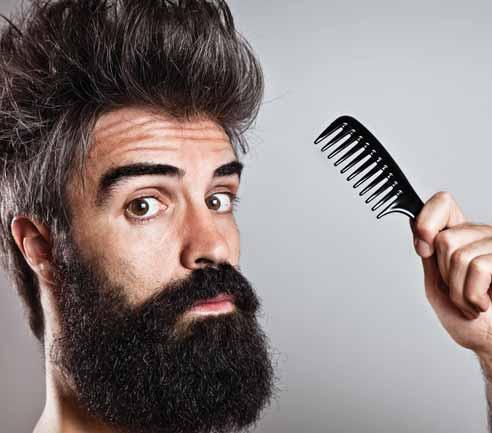
14 minute read
PLUMBING Hair, hair, everywhere
By Fred Bretzke
PLUMBING
Fred Bretzke is a full-time pipe trades instructor with SAIT Polytechnic in Calgary and the general manager of A&B Plumbing & Heating. He can be reached at fred.bretzke@sait.ca.
HAIR, HAIR, EVERYWHERE!


COVID-19 has certainly given us many challenges. On the lighter side, it seems that before the salons started opening again, a lot of people were suffering from bad hair, which got me thinking about hair and some of the horrors that I’ve seen.
TRYING TO KEEP MY COOL
Once a month, usually on a Monday night at dinner time in the Bretzke family, we would be sitting at the table and my almost-bald dad would claim that the family men needed a haircut. Now, remember, this was the ’70s, a time of bell-bottom jeans and long hair, and besides, my dad didn’t need a haircut, he was bald.
I think the German in him relished to see me suffer as he talked about giving me a brush cut. Anxiety would take over my whole body. All my friends had long hair. I couldn’t show up to school with a brush cut. My brother, Carl, would succumb to Dad’s wishes and have his hair blazed off, and hence be called “bristle hound” for the rest of the school year. My cousin Glen had just trained me to look cool by growing my hair longer and parting it down the centre, like all the cool rock bands: The Doors, The
AN UNEXPECTED TWIST
Sometime in the ’80s, when mall culture was at its height, I got a call proving that long hair isn’t always cool. In my service days, it wasn’t unusual to get a call for a plugged drain in a shopping mall, so I started this one like any other, working through the most obvious causes first. I investigated the restaurants, since more often than not, it would be a greasy drain problem. A lot of restaurateurs would try to save money by not getting their grease traps cleaned often enough, and grease would often pile up in the main building drain and back up in the washroom floor drains – or somewhere further downstream.
After checking the main restaurants in this mall, I realized that they all were cleaning their grease traps regularly, so I turned to my drum drain-cleaning machine and let it rip down the main drain to see what I came up against. My trusty drum drain cleaner had heavyduty power; it even came with a clutch. These machines can be powerful and dangerous, and while accidents will teach you a lesson, these machines can really hurt you if you are not careful. I once had the thick cable from one wrap
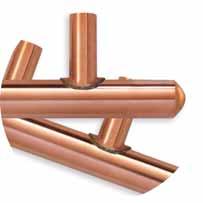

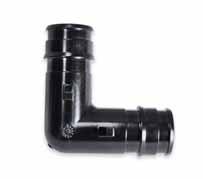
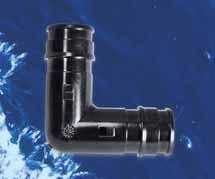
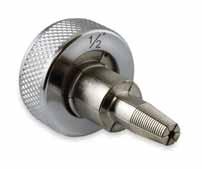

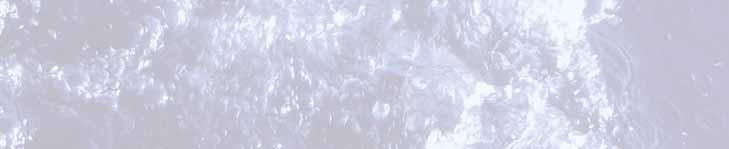
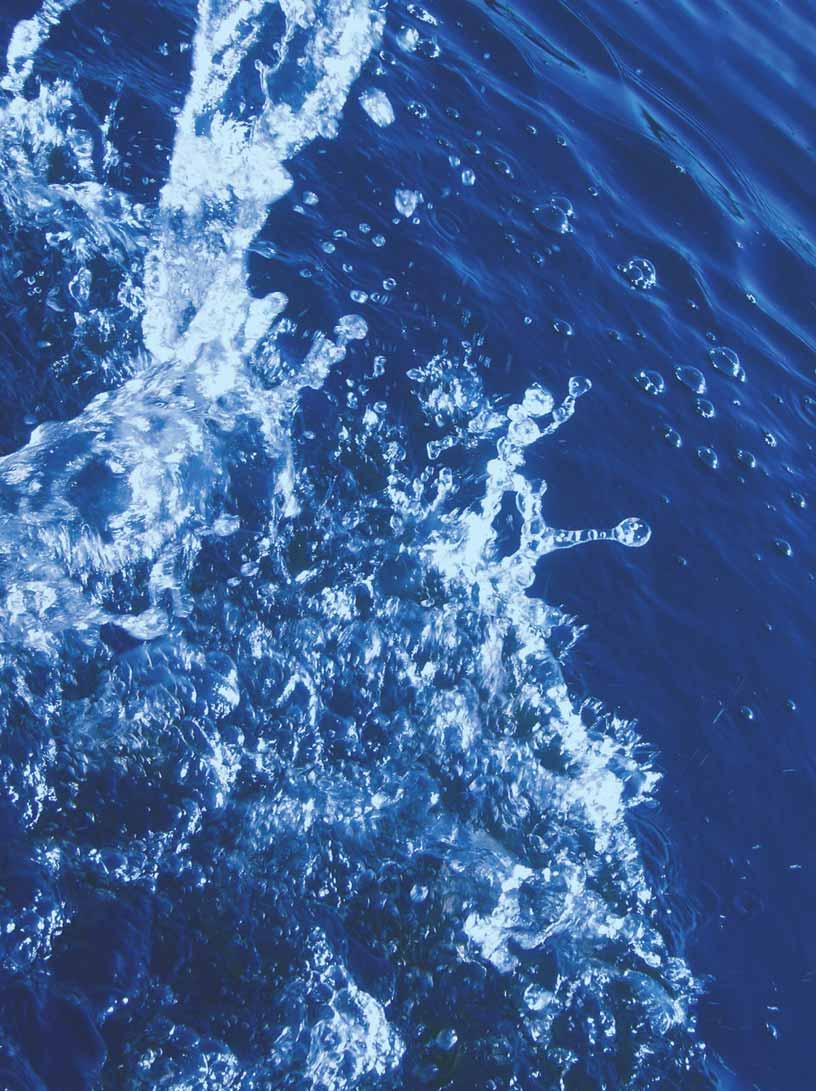
TRYING TO KEEP MY COOL,
continued from page 20
Eagles, etc. There was no way my locks were getting cut. I was way too vain for that. I had to come up with a plan, and it didn’t need to be elaborate, just effective. So, I quietly waited and let Carl get his buzz cut first, and I slid out the side door and headed for freedom when he did.
When someone finally did manage to cut my hair, some years later, it was a traumatic event. I still remember the razor vibrating and buzzing all over my scalp; my blonde locks of hair falling to the wayside. I’m sure there was a tear slowly trickling down my cheek as they robbed me of my cool side. As time would pass, I guess my mom thought she was experienced enough with cutting hair that she started her own hairstyling place. And later, my oldest sister Arlene would start a hair replacement business. So, I guess I’ve had a little bit of experience with hair, and of course as a plumber I’ve had many experiences with hair in all the wrong places, but none quite so memorable as a service call to a mall. around me as the unit was running in the on/forward position.

You would think that drain cleaning would be easy, however, it’s all about the feel for your equipment and getting a sense for when the cable comes up against an obstruction.
This time, as the cable started feeling like it was winding up, it almost felt like it had hit tree roots, but there were no trees in the mall, so I knew it had to be something else. You never know what you will find in a drain; a rope or clothing could have been flushed down a toilet.
Usually all I would have to do is push it forward and pull it backwards several times to clear the drain or free my auger, but not this time. I had caught the big one! I was thinking, “Could this be the Moby Dick of drain cleaning stories?” I had 200 feet of 3/4” auger cable down this line and, after struggling with it for a good hour, I finally pulled the line back to discover a full-bore blockage of the pipe. I had pulled out a 4” thick snake from the pipe – or at least it looked like a snake.
After pulling out at least 30 feet of an Anaconda-looking, rotten-smelling object, I realized it was hair. How could this much hair get lodged into the main drain? There were two hair salons in the mall, so off I went to investigate.
IGNORANCE IS BLISS
Before I got into plumbing, and once I got used to getting my hair professionally cut, it wasn’t unusual for me to lean back on a salon chair and relax as the hair stylist would wash, shampoo, and massage my scalp. I could see that some of my hair will shed and drain down the sink, but I never thought about what would happen next, or where [OH[OHPYNVLZ0Q\Z[ÄN\YLKP[ was supposed to go down the drain and into the sewer. I now know better.
DID YOU KNOW?
In the 2020 NPC, section 2.2.3.1.5, it states that a drum trap shall not be used as a fixture trap unless required to serve as an interceptor and access for servicing is provided.
The first one had weird looking traps under the salon sinks. These, I would find out, were drum traps. Made of ABS plastic, they had a removable nut on them that held a screen in place. These are hair interceptors. As I investigated the other hair salon, I saw that none of its eight sinks had drum traps on them. Apparently, the salon owner didn’t want to pay for the extra parts. After he was held responsible for the mall’s plumbing bill, he decided to invest in drum traps. Hair is a big problem in drains, just like grease. If you don’t realize this, try and pull out the rotting hair out of your bathtub or shower drains. You would wish you got your hair cut by my dad.
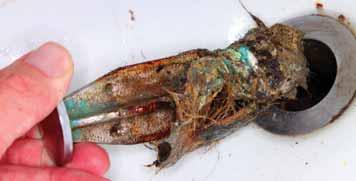
Vanessa Meats:
Growing while reducing the energy footprint
One of the goals, in addition to increasing refrigeration capacity, was to reduce hydro consumption.
FINDING EFFICIENCY WITH LOW PRESSURE
“Nobody would believe that you can expand refrigeration space by 4.5 and cut the power usage down by one-third…but we did,” says Kungl.
“There are no thermal expansion valves, no solenoid valves, no pressure operated valves of any type in the system architecture at all,” he says. “Because it’s electronically driven, you don’t need a lot of pressure differential in the system to make it work. That’s why it runs on such a small amount of power.”
And the refrigerant charge has been minimized as well.
“By splitting the facility in half, we were able to limit how much pipe we needed to put through the buildings,” he explains. “It made more sense for system redundancy since the two sides can run together but separately without using miles of pipe.”
The Vanessa Meats system is almost entirely hermetically sealed and uses a minimum of mechanical connections. Eliminating gasketed surface valve connections and fittings also reduced the risk of leaks and any associated maintenance costs, Kungl notes. W hen the new owners of Vanessa Meats were looking to expand, they wanted to increase the company’s refrigeration capacity, and to update the system to meet growing needs. Of course, this was no small bump in size, or minor retrofit; the new system will outpace the capacity of their original system by a factor of about 4.5 to one, despite costing 30 per cent less to run than the original facility size.
A long-standing company in Vanessa, Ont., the butcher and deli operation has grown to become a leading processor of custom meat offerings. Its refrigeration system services their smoking, dry aging, curing, and fermenting raw cooler, freezers, process cutting rooms and retail storefront.
Once fully completed, the refrigeration project will give the company the capacity to process
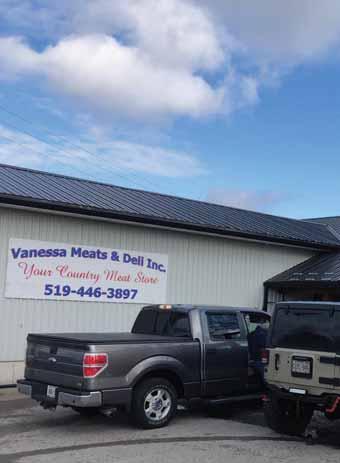

up to 15,000 pounds of meat a day, all while consuming less energy than their old system.
And, with early results looking good, system designer Ben Kungl of Oxford Energy Solutions thinks they can bring those operating costs even lower. The next step for this customer is going off grid, he says.
THE PLAN: • Update and replace existing R22/R-290 refrigeration system (approx. 7 TR) with low- pressure differential HFO refrigeration system (approx. 34 TR). • Maintain lowest possible pressure differentials throughout the system to achieve a long-term platform target of zero refrigerant leakage and reduce electrical operating costs. • Total facility refrigerant reduction plan for 21 loads: Approx. 25%.
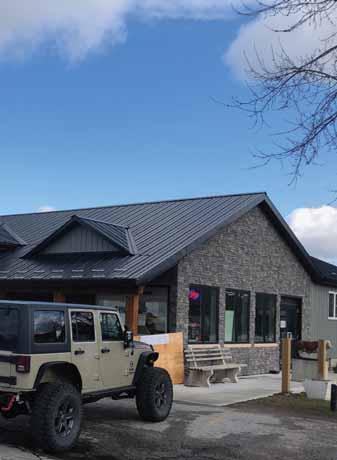
A FLEXIBLE FUTURE
Future proofing was a major consideration, so they decided to use a new low-pressure, low-GWP hydrofluoroolefin (HFO) refrigerant, says Kungl.
“It’s completely compliant, and the Oxford Equipment Platform allows the owner to be set up for any future changes to refrigerant trends such as an A2L type.”
It wasn’t about presenting a short-term plan, he adds. “Given that the new owner is young and eager to invest in his own future, why would you design and install a system that already has a potential end date attached to it?”
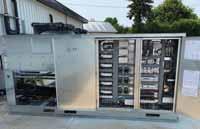
The design called for a fully automated system that can accommodate any future switchover of refrigerant.
“It made more sense to get into something that was adaptable and fully automated, including trending, graphing and alarming. This design allows you to change the settings on your computer or phone and the system will automatically change its operating characteristics for the refrigerant of choice.” When asked if there are any pressure-level concerns in the system, since it uses low-pressure differentials, Kungl explained that there are none with the control architecture being used. “The important thing to keep in mind is, the lower the pressure differential, the more efficient the pump is, and the less secondary heat it generates,” he explains. “Every type of compression has a bypass leak rate, and that increases as the pressure differential increases.” At lower differentials, the system has less stress on it, generates less secondary heat, consumes less wattage, there’s less vibration, and so forth. “With a low-pressure differential,” he adds, “it’s not a linear curve, but a proportional one. When you lower the differential, everything else magnifies in efficiency. Most systems can’t do that because they are designed conventionally and therefore have more limitations as to how low a compression ratio and system design pressure they can achieve.” Oxford used scroll compressors for this project, because of their operating pressure differential margins. “By taking full advantage of our ambient conditions, the ability for the system to operate down to and below a 30 psig differential, free subcooling that is, on average, over 20°F, it all sums up to a system that uses incredibly less power to do the same work,” says Kungl. “The savings are astronomical. The system really just exploits the massive energy gain in heavily subcooled liquid and low wattage inputs to move that fluid to the loads.”
REDUCING REFRIGERANT USAGE
A major consideration for the system, potential to leak. In this installation, given its size, was reducing refrigerant the Oxford Platform system can run charge and system piping, says Kungl. the facility’s north wing of 14 different “Those are the biggest things in circuits with a total system charge of refrigeration, or any equipment prone 50 lb. to leaks.” Any refrigerant in a system that is not doing work is a waste, he says, explaining that this can be seen in “systems that require large winter charges due to condenser flooding, or the use of EPRs on every evaporator which, in turn, increases the overall evaporator charge along with other negative system effects.” A properly designed system that can match load based on mass flow requires less valving and has less
A DIFFERENT PERSPECTIVE ON A SYSTEM
For Kungl, one of the reasons the system works is because they were able to minimize the number of moving parts in the system. “People think of refrigeration systems in components as individual sections, and then size or design those parts individually,” he says. “A lot of times, refrigeration systems are even purchased as separate components and then they apply controls and hope it all works. “The reality is, for a system to work this well, it has to be thought of as one working unit in which every part affects the entire system. The key is keeping things basic and letting the refrigerant do the work without unnecessary restrictions”
HVAC/R Products
Water detection Refco’s Aquaswitch is designed for applications where a reliable switch is needed to control or indicate the presence of water. It can be fixed to the wall of a drain pan by screws through the fixing slots or to the bottom of the tray using waterproof double-sided tape. The unit has a temperature range of 32°F to 167°F. The water level for the switching relay is 3/8”. www. ontor.com
Heat pumps Goodman’s GSXC18 split system heat pumps are available with cooling capacities of 23,000 to 56,500 BTUH and heating capacities of 22,000 to 59,500 BTUH. The units offer efficiencies up to 19 SEER and 10 HSPF. Standard features include a two-stage scroll compressor; highdensity foam compressor sound blanket; and app-based commissioning and diagnostic reporting via Bluetooth. www. goodmanmfg.com
Grease duct products
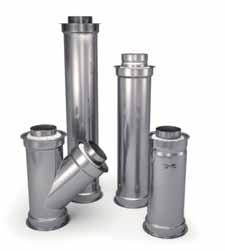
Cheminee Lining’s line of grease duct products are built to manage appliance exhaust of combustion gases under positive, negative or neutral pressure in industrial, institutional and commercial applications. They are laser welded and UL/ULc listed. They feature a male/female, slip-type jointing system. www. chemineelining.com
Piping packages
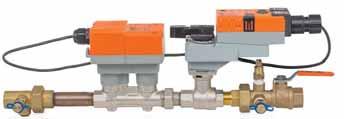
Belimo Piping Packages are designed to be a streamlined method of piping HVAC terminal units. They are custom factory assemblies that include isolation for the control valve and coil, pressure/temperature test ports for balancing, ncing, manual air vents, and strainers with integral drain options. options. Configurations are available with ePIV and Energy Valves, y Valves, as well as standard zone valve assemblies. www. belimo.usrefco.ch Ductless mini split The NextGen Arctic ductless mini split from Haier offers efficiency ratings up to 30 SEER and 15.2 HSPF. It is available in single-zone sizes of 9,000, 12,000, and 18,000 BTUH. The units are capable of delivering 100 per cent of the rated heating capacity at outdoor temperatures of 5°F and warm air at outdoor temperatures as low as -31°F. www. haierappliances.com
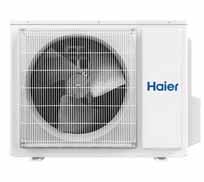
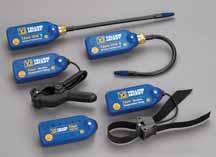
Bluetooth sensors
The YJACK Series of low energy Bluetooth (BLE) sensors from Yellow Jacket are designed to measure system pressures and temperatures, while monitoring the temperature, relative humidity, wet bulb, and dew point at the supply and return registers. The lineup includes a temperature clamp, temperature strap, psychrometer (YJACK DEW) and repeater/range extender (YJACK PATH). www. yellowjacket.comrefco.ch