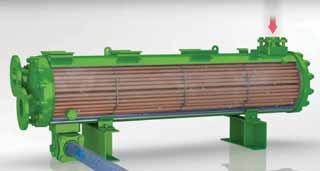
6 minute read
REFRIGERATION Shell and tube water-cooled condensers
Shell and Tube WaterCooled Condensers
There are a number of different types of condensers that can be used to reject the heat from a refrigeration system, and these can reject the heat to the ambient air, water or any other type of fluid that is available e at a low enough temperature.
For the current discussion, let’s focus on shell shell and tube condensers that reject their heat to at to water, or another form of aqueous solution. on.
Water-cooled condensers are typically designed and connected into the system in a counterflow arrangement. This means that the fluid flows in one direction and the refrigerant travels in the opposite direction.
With this method, the coldest water supply is used to provide refrigerant subcooling. This would not be possible if the condenser was piped for a parallel flow. Also, it makes less sense to use the coldest water to cool the incoming discharge gas. Air-cooled condensers are also designed using a counterflow arrangement.
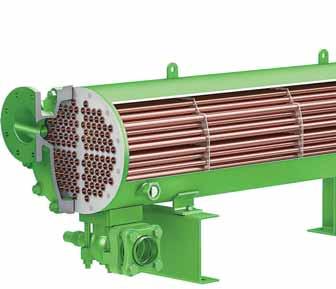
Inside a shell and tube condenser, the refrigerant flows in the shell from top to bottom. This makes sense because liquid is denser than vapour and will drop to the bottom of the shell where it can then be further cooled by the incoming water.
The tubes carry the fluid that is used as the cooling medium. Since the refrigerant flows within the shell, the shell side is relatively warm. Therefore, condensation is not likely to take place. This provides the added
WORKING WITH WATER, AND OTHER FLUIDS
Appropriate aqueous solutions include mixtures of propylene glycol, ethylene glycol or calcium chloride with water. And there are many other types of glycols that may be used for applications where the condenser water temperature can drop below the freezing point of water. Of course, if it is known that the temperature of the condensing medium will not fall below 33°F, then 100 per cent water can be used to carry the heat away from the system. In addition to being less expensive than a glycol or other chemical-based fluid, water also provides better heat-transfer characteristics than aqueous solutions.
Phil Boudreau Phil is the Ontario sales manager for Bitzer Canada Inc. and provides training and technical support for Bitzer’s clientele. He can be contacted at pboudreau@bitzer.ca.
Gobi II
Condensate pump

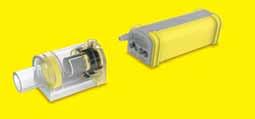
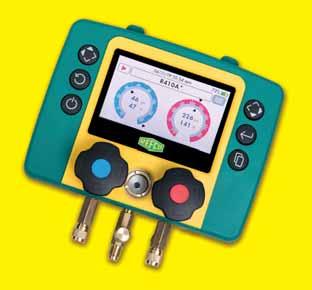
ENVIRO-DUO
Recovery machine for all popular refrigerants benefit of eliminating any corrosion to the outside of the shell or objectionable condensate from dripping off the condenser shell.
With a shell and tube condenser, the heads that are located at either end of the condenser are typically removable. This way, the tubes can be cleaned. If a leak is suspected at some point during the service life of the condenser, the heads can also be removed to facilitate Eddy-current testing of the tubing. This type of testing will reveal any weaknesses in the tube due to erosion and/or any corrosion that has taken place.
LOSING THE HEAT
32525
Valve core replacing tool
REFMATE
Digital manifold
A-38010 A-38410
Access control valves
HY-EX
Hydraulic expander tool kit
ECO-5
Two-stage rotary vane vacuum pump
OCTA-WIRELESS
Electronic charging scale
Distributed in Canada by Ontor Limited
12 Leswyn Road, Toronto, Ontario M6A 1K3 Tel.: (416) 781-5286 Email: info@ontor.com www.ontor.com Solution Focused, Support Driven
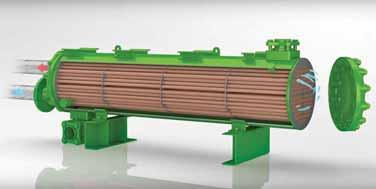
In a vapour compression system, the purpose of a condenser is to reject heat – all the heat that the circulating refrigerant absorbs. As such, it must reject the heat added by the evaporator, the suction line, the motor (hermetic/semi-hermetic compressors only), mechanical friction inside the compressor, along with the heat of compression. With more sophisticated system designs, there may also be other sources of heat. For example, a subcooler used with an economized compressor and in some cases, a compressor oil cooler can add heat to the circulating refrigerant. All these sources of heat combined, form the total heat of rejection or THR.
For the system to reject all heat efficiently, the THR must be removed by the condenser at a condensing temperature that is as low as possible. This is achieved by sizing the condenser so that it can remove all heat at a temperature difference that is as low as possible, but higher than the maximum expected temperature of the cooling medium supply. Additionally, the condenser should be able to supply enough subcooling to offset any liquid line pressure drop that may be present. Sources of liquid line pressure drop can include piping or fitting losses, liquid lift in risers, along with pressure losses through liquid line accessories such as the filter-drier and solenoid.
Approach Temperature
This is the difference between the cooling medium and liquid temperatures leaving the condenser. Lower approach temperatures increase efficiency but also require a larger condenser to do the job.
Condensing Temperature
This is the temperature at which the refrigerant condenses. For R400-series refrigerants, it is very important to determine whether the dewpoint or average temperature of the refrigerant will be used. It is generally recommended to use the average temperature when selecting a condenser. The same is true for selecting evaporators. It is even more important that all components sized within the system are based on the same reference temperature.
Fluid Flow Rate
As the term suggests, the fluid flow rate is the flow rate of the cooling medium in gallons per minute.
Fouling Factor
The fouling factor is used to de-rate the capacity of the condenser to compensate for a small amount of mineral deposits and other such impurities on the outside of the tubes. The unit of measure for fouling factor is ft 2 -°F-hr/ Btu. The fouling factor is typically a very small value, such as 0.000244 ft 2 -°Fhr/Btu, or so.
Temperature Range
This represents the difference of the entering and leaving cooling medium temperatures.
PICKING A CONDENSER
If the temperature range is used to select a watercooled condenser, the water flow rate is a function of the THR and the temperature range of the water. However, if the supply water temperature and fluid flow rate are used to select the condenser, the temperature of the cooling medium leaving the condenser is a function of the THR and the water flow rate.
When selecting a condenser, the specific heat and specific gravity of the cooling medium must also be taken into consideration if an aqueous solution cooling medium is used. Using water, the formula for calculating the required flow rate is THR divided by (500 x Temp Range). Using an aqueous solution, the formula becomes THR divided by (500 x Temperature Range x Specific Heat of Solution x Specific Gravity of Solution). The number 500 is a constant that approximately equals the number of pounds of water per (US) gallon, multiplied by the number of minutes in an hour (8.33 x 60).
Where Design & (IÀFLHQF\ Meat
Oxford Energy Solutions pairs its leading-edge control platform with low-pressure refrigerants and scroll technology to transform a traditional mid-sized deli operation into an expansion UHDG\ZRUOGFODVVHQHUJ\HIÀFLHQW showcase.

The result? Refrigerated space increased by 460%, while total facility electricity costs lowered by 30%.

Find out what Oxford can do for you on your next project. Oxford Energy Solutions Inc. 519-532-6373 oxfordenergy.ca