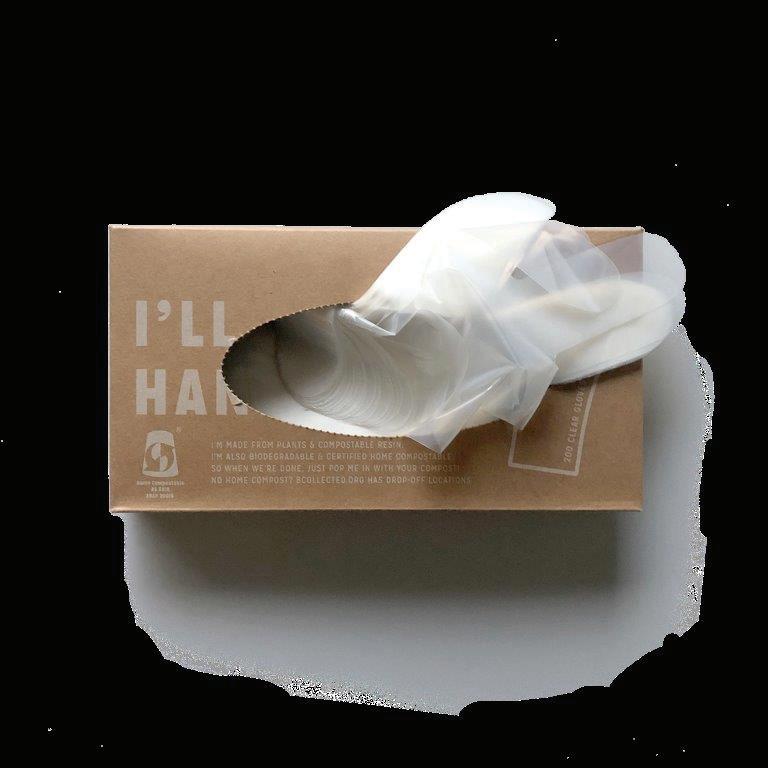
4 minute read
QUALITY CONTROL
Co-ordinated action on compostable packaging needed
NDC sensors control manufacturing at the front line
Advertisement
A recent survey of compostable packaging stakeholders by The Packaging Forum shows that between them they have completed over 100 compostable packaging projects in the last five years, with another 81 in progress and 85 more planned.
Yet there has been little progress made on developing a viable end-of-life solution for compostable packaging at the scale New Zealand requires. This according to Kim Renshaw of Beyond the Bin, who is project manager for The Packaging Forum’s Compostable Technical Advisory Group (CTAG). What’s needed for progress to happen, she says, is clear in the top six requirements identified by stakeholders:
• Nationally available collections infrastructure • A labelling system • Increased processing infrastructure • An official New Zealand standard for compostability of packaging • Funding • Networking (knowledge sharing) The CTAG is taking a collaborative approach in laying the groundwork for these to be developed and funded, she says. “The next step is to gain an understanding of the volume of compostable packaging in the New Zealand market, and to clarify what level of investment and infrastructure is needed.”
As there is no existing data on this, the CTAG’s next survey will be asking manufacturers and importers to supply data to inform that understanding. Data will be aggregated to protect commercial sensitivity, Kim says. “As public opinion has turned against plastics, many importers, manufacturers and brands have turned to compostable packaging as a promising solution. However, all packaging types need to end up in the right system at the end of their life to avoid causing unintended harm.”
“We’re working to overcome some complex problems such as the risk of contamination of compostable packaging with other materials, the ratios of compostable packaging that can be accepted by composters compared to other compostable material, what collection infrastructure could look like and how it could be funded,” she says. The Forum recognises how important it is to overcome challenges and get systems in place for an increasingly popular packaging choice and will be working with all stakeholders to achieve this. Ultimately the purpose of this work is to support Government in developing the right regulations for compostable packaging in New Zealand, ensuring the solution provides the best outcome for consumers and the environment, Kim says. The Forum is inviting the following stakeholders to register to participate in a work programme and receive information:
• Manufacturers and importer of compostable packaging • Brands and retailers who sell goods in compostable packaging • Composting collectors and processors • Brands considering switching to compostable packaging
-Simon Ganley Most customer food complaints relate to colour.
Too dark is considered to be over cooked or baked. Too light is perceived to be underdone. You wouldn’t believe just what people complain about. But businesses have to take complaints seriously and it costs to deal with them. So now a lot of food manufacturing companies are adding colour to the other parameters they measure and control, saving a lot of money by doing so. There is a good chance that a biscuit you buy in NZ will have had the manufacture controlled by colour rather than moisture. The measurement was developed in NZ with NDC and is being rolled out world-wide.
This saves a manufacturer a fortune in power consumption, scrap, waste, staff time and raw materials. And dealing with complaints. Next time you eat fries at top quality franchised restaurants, they will have had the manufacture controlled with moisture, oil, colour, bed depth and temperature - all on the one NDC sensor that sits above the fryer. Coffee is another application. The top brands of coffee have NDC sensors controlling the colour, moisture and caffeine. They also control tea. Sugar is another application that is being developed at the moment. NDC controls the manufacture of pretty much all the sugar made and sold in NZ. “Wet” sugar moisture can be controlled to 0.1% on-line and dry sugar to 0.006%. But customers are alert to shades of brown that creep into refined sugar. Strangely the colour we see in sugar isn’t brown. It is actually in the blue/green part of the spectrum. Lactose is another product that downgrades with shades of brown and manufacturers of quality products build NDC sensors into the fluid bed driers to maintain top yield prices. When we talk about product control with colour, we are not talking about colour sorters. These allocate products with different colours after they have been made.
What NDC sensors do is control the manufacture at the front line so only items of a selected colour range get made. The sensors can combine measurements of moisture, fat, oil, protein, caffeine etc to the colour and send each measurement result to the various PLCs and PCs that automate the manufacture.
They generally pay for themselves in weeks rather than months.
So, if you manufacture products that can have a variable colour, maybe we can help you. There is a good reason that NDC Technologies is the world’s largest supplier of on-line and at-line process control solutions.
If you run a fluid bed drier, oven, tunnel oven or blender, we may be able to make you a lot of money. Visit; www.ganleyengineering.co.nz and www.ndc. com