
13 minute read
DEVELOPMENTS
Is automotive ready for hydrogen?
With global sustainability legislations shifting the automotive market away from combustion engines, you’ve probably heard somebody utter “my next car will be electric”. If you haven’t, it’s likely you will soon. However, one fuel source doesn’t fit all. Making the green shift in the automotive market will require other sustainable fuel sources.
Advertisement
The move away from petrol, diesel and hybrid cars can seem like a shifting target. Despite deadlines for the ban on such vehicles varying by country, we can be sure that global change is happening — and soon. Automakers and drivers alike will need to adjust to a more sustainable future, but how can you decide which resource will power your vehicle?
BEVs versus FCEVs
The automotive sector typically views battery electric vehicles (BEVs) and fuel cell electric vehicles (FCEVs) as competing technologies. While BEVs use electricity stored in a battery that powers the vehicle’s electric motor, FCEVs are powered by fuel cells. A fuel cell converts energy stored in molecules into electrical energy. Only oxygen and hydrogen are required to power the fuel cell — the former is readily available in the atmosphere, and the latter can be generated through electrolysis. FCEVs can offer better weight economy, effectively powering larger vehicles such as haulage that need to limit unnecessary weight gain. Vehicles that travel long distances or that need to refuel quickly are also more suited to hydrogen. Hydrogen is also a good choice for longer-term storage, since it is a gas that can be stored in tanks and containers, while battery lifetime can suffer if the batteries are not charged and discharged correctly. However, hydrogen’s sustainable future relies on the production of green hydrogen — produced through electrolysis powered by renewable resources. Currently, around 96 per cent of hydrogen is generated from fossil fuels, so developments must still be made if FCEVs are going to match the feasibility of BEVs. Despite green hydrogen’s slow development, across Europe many projects are already underway to test and deploy hydrogen buses, taxis and other large vehicles, spurring on investment in refuelling stations and other infrastructure that will be critical to the roll-out of FCEVs. For instance, the Joint Initiative for Hydrogen Vehicles across Europe (JIVE) project seeks to deploy 139 new zero emission fuel cell buses and associated refuelling infrastructure across five European countries. JIVE is co-funded by a 32 million euro grant from the Fuel Cells and Hydrogen Joint Undertaking under the European Union Horizon 2020 framework programme for research and innovation. Planned operating sites include the UK, Belgium, Germany, Italy and Denmark. Elsewhere, British carmaker Jaguar Land Rover is working on a government-sponsored initiative, Project Zeus, that will develop fuel cell technologies for its larger vehicles. While the project remains in early development and the focus is on developing hydrogen powertrain technology, the first concept developed as a result of Project Zeus is likely to be an Evoque-sized SUV.
Getting prepared
As sustainable and viable hydrogen solutions begin to take off, hydrogen infrastructure will also be key to delivering the fuel source to the automotive industry. Infrastructure doesn’t only involve producing the fuel itself, but also the pipework to transport it, and the development of the fuel cells. A key component in this infrastructure is steel. High quality steel tubes will be an important requirement for gas companies, who will require flexible solutions to set up refuelling stations. Sandvik is already working with leading gas and engineering company, Linde, and is supplying its portable Solution in a Container to help the company build refuelling stations across Europe. The stainless steel alloy tubes transport hydrogen from a storage tank to a dispenser. Linde’s hydrogen gas is transported under both low and high pressures of up to 900 bars, so Sandvik’s tubes meet strict safety guidelines. The long tubes eliminate the need for conventional fittings, such as cone and thread connections or welding, which normally connect shorter tubes. Removing these connections helps reduce the risk of leakage and station shutdowns. In addition to hydrogen transport infrastructure, materials technology is also central to fuel cell development. The Sandvik Sanergy product platform consists of a coated strip for a critical fuel cell stack component. The strip is ready to be pressed to bipolar fuel cell plates, eliminating the costly need for individual plate coating. Today Sandvik has a unique, large-scale production facility in Sandviken, Sweden, and is ready for fuel cell technology to take off. As we move away from petrol and diesel, many automakers are entering new territory. While BEV technology is well underway, it’s important to recognise that other sustainable options may better suit certain automotive requirements. Hydrogen fuel cells remain a working progress, but ongoing investment and their clear potential make hydrogen a strong contender for the industry’s greener future.
continued from Page 1
Get your carbon diet on track: 5 steps to carbon reporting
carbon footprint. This is the same with embodied carbon, which is included in Scope 3 emissions and can be trickier to track than more direct emissions. Your supply chain likely includes a number of ready-made products, so you need to be aware of the emissions of these products before you use them. To prepare for external reporting and the higher stakes involved, seek out any hidden elements for carbon reporting and be ready to answer detailed questions in advance.
4. Set an ambitious reduction target
The crown jewel for external reporting is publicly committing to a reduction target by setting an ambitious emission reduction goal. GHG emission reduction targets set by companies are only considered ‘science-based’ if they are in line with the latest climate science on what is required “to limit global warming to well below 2°C above pre-industrial levels and pursue efforts to limit warming to 1.5°C.” As with any diet, surrounding yourself with the right groups can be beneficial for receiving support, resources, and opportunities for fruitful collaboration. The Science Based Targets initiative (SBTi) and the Climate Leaders Coalition are two support groups that can help on your carbon
reduction path. SBTi ensures that companies keep their carbon diet in check by helping them set science-based targets. This will help to further impress future or potential clients and other key stakeholders by giving companies a competitive edge in the race to a low-carbon economy. As of 31 December 2020, 556 companies have approved Science Based Targets (SBTs). In New Zealand, the Climate Leaders Coalition has grown rapidly and is now the largest business collective tackling climate change in the country. Both Climate Leaders Coalition and the SBTi have set their targets in accordance with the 2015 Paris agreement. thinkstep-anz is one of 10 companies in Oceania to have approved Science Based Targets and is also one of 103 signatories of the Climate Leaders Coalition. 5. Balance your carbon reductions with offsetting Offsetting can be the final step to achieving a well-rounded carbon reduction plan. While it is generally not practical to offset the majority of your carbon footprint, carbon offsets are a way to lower the impact of unavoidable, specific activities such as work-related flights. Balance is key for any diet; the carbon diet is no exception. The only way to achieve your carbon reduction goals is to set an ambitious yet realistic target. View it as a long-term investment and conscious lifestyle change, rather than a fad.
Figure 1: This image shows the different activities that make up Scope 3 emissions. Note that these include both upstream and downstream emissions.


EVOK3D Trans Tasman distributor for 3DGence INDUSTRY 3D range
EVOK3D have extended their portfolio of 3D printers to include the 3DGence INDUSTRY range. This professional extrusion-based FDM printer is designed for the manufacture of end-to-end use parts, functional prototypes and jigs and fixtures.
With prices starting around $50K AUD, the machine features a high-temp chamber for a stable print environment and quick-change printing modules for compatibility with a wide range of materials, including ULTEM and PEEK. 3DGence 3D printers are renowned for their reliability and repeatable performance. With the flagship F420 machine boasting a large build volume of 380 x 380 x 420mm, the key advantage this printer brings is undoubtable its ability to use a wide range of extreme polymers such as ULTEM, PEEK, or PEKK as well as commodity polymer such as ABS, ASA and PP etc. Other features include autocalibration to minimise setup times, 4 material bays for uninterrupted automatic spool change, very fast print speeds, soluble supports and open sourced consumables, to name a few. EVOK3D has been delivering quality 3D printing/additive manufacturing solutions for over eight years, adopting leading edge technologies backed with locally based support service. The team at EVOK3D believe the 3DGence range will help customers address their most demanding industry challenges that can’t be economically solved with conventional technologies and ultimately contribute to the rollout of Industry 4.0. EVOK3D is Australian owned and operating 3D printing specialist. Supplying and supporting professional and production digital manufacturing solutions, including machinery, consumables and software. Part of the Currie Group company, EVOK3D has offices in all capital cities across ANZ
Taking on 3D printer distributorship of the 3DGence INDUSTRY range is timely for the Australian and New Zealand markets, as local manufacturers are looking to evolve their design and manufacturing capabilities.

Mint Innovation raises $20m to build gold biorefineries
HRS highlights steam injection for food sterilisation
Precious metals refiner Mint Innovation will start mining in Sydney next year. Then the New Zealand cleantech company has its sights on building a second biorefinery in North West England. Mint Innovation has raised NZ$20 million to help build those plants, which are based on its proprietary biometallurgical process and scalable platform. During successful trials at its first biorefinery in Auckland, Mint Innovation recovered significant amounts of gold and copper from crushed and powdered electronic waste. Dr Will Barker, Mint Innovation’s CEO, says the Series B capital raise was led by New Zealand technology investor Movac, with strong support from around the globe, including Blackbird Ventures and major long term investor Icehouse Ventures. “This raise gives us the capital we need to deploy our technology, starting with the Greater Sydney biorefinery in early 2021,” Dr Barker says. “Once commissioned, the plant will be able to process up to 3,500 tonnes of electronic waste each year. “That’s enough capacity to turn all the waste circuit boards in New South Wales into precious metals, including gold and copper. Ideally those metals will be sold back to local businesses, such as jewellers and manufacturers, creating a truly circular economy.” Movac partner David Beard says the future for Mint Innovation lies in its plant design and technology being licensed for biorefineries to be built in cities around the world. “With the disposal of e-waste a growing issue, as countries like Mainland China close their doors to importing waste, a disruptive cleantech company like Mint Innovation has the potential to establish a global footprint quite quickly,” he says. Dr Barker says the second plant is expected to start being built later next year. The North West of England has a heritage in chemical process innovation and
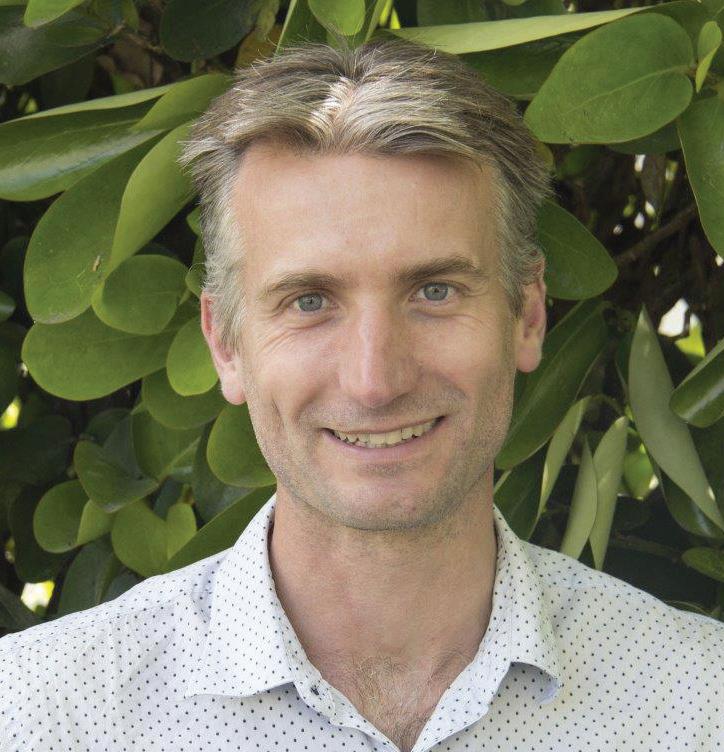
Dr. Will Barker Mint Innovation wants to bring clean tech to an area with which Dr Barker is familiar, having grown up in the UK. “There is a lot of recycling of e-waste by governments and cities, but our technology provides a new dimension to creating a circular economy,” he says. “Imagine the gold in your old laptop might end up as a ring on a person’s finger – or being re-used in new devices.”
HRS Process Solutions, Stand 3164, Foodtech Packtech 2021
After an exceptional year, HRS Process Solutions is delighted to be returning to the Foodtech Packtech event in Auckland in April and will be showcasing its DSI Series of direct steam injection pasteurisers and sterilisers which are ideal for food products such as plant-based milk drinks. The benefit of sterilising using direct steam injection is the speed of the process, with sterilisation temperatures of 100 to 145 deg. C. being reached in around a second; much quicker than the fastest heat exchanger systems. For products such as plant milks, this rapid heating prevents cooking of the product and formation of caramel-type compounds which can darken the product or produce unwanted flavours. Some products, such as oat milk, also benefit from the additional dilution with water which the steam injection provides. Chris Little, Managing Director at HRS Process Solutions, comments: “At HRS, we are always looking to provide full system solutions for the thermal treatment processes required by our clients. As part of this we have introduced the DSI Series of steam injection modules for the pasteurisation and sterilisation of products such as increasingly popular plant milks. “The first DSI Series unit has been running successfully for a number of months now and we are pleased to be able to offer another solution to our customers.” More information on the HRS DSI Series will be available on Stand 3164, at Foodtech Packtech in Auckland from 13-15 April 2021.
WelTec graduate gets dream engineering job
Philip Moore has long loved learning the mechanics of how things work, and as a child was always taking things apart and putting them back together. When he completed his engineering degree at WelTec in 2019 he was offered his dream role doing just that - as his first job after study. Philip grew up in Picton. His drive to learn about engineering was so strong that when he was in Year 11 he moved schools so he could take a class focused on this subject area. “I always knew that I wanted to study engineering, so when I finished college I enrolled in an engineering course at a university,” explains Philip. “I think, like a lot of teenagers, I had it drilled into me that I had to go to university to be successful, but I soon realised that it wasn’t for me.” “I found the course was too theoretical and it was honestly a bit boring. I asked around and heard good things about WelTec so I decided to drop my university course and enrol there.” The change in course did the trick and Philip hasn’t looked back. “The hands-on approach of the WelTec course was definitely more what I wanted out of my degree. I found the course work challenging and engaging and there was a good balance of theory to go alongside the practical work. I think what I found so useful about the course was the fact that the tutors were very good at showing us the practical implications of what we were learning for later in our careers. It made it feel relevant and worthwhile.” After completing his degree Philip applied for a position at Omeo Technology on the Kāpiti Coast. He impressed the Omeo team and was quickly offered the role. Omeo Technology is an innovative company based in taki, that creates electric, self-balancing mobility devices which can be driven completely hands free. The two-wheeled devices have all-terrain capabilities, meaning beaches, forests, tracks and unsealed pathways are now accessible for those restricted to a mobility device, and occupants can travel at speeds of up to 20km per hour. Omeo Technology is a team of 10 so each member has to pull their own weight which sometimes means doing jobs that are outside of your job description. “Being in a small team has been a huge blessing, I have gotten to understand the company structure in a way that I wouldn’t usually as an engineer in a bigger company, and I have been given opportunities such as completing a CPR course and becoming the company health and safety representative.”
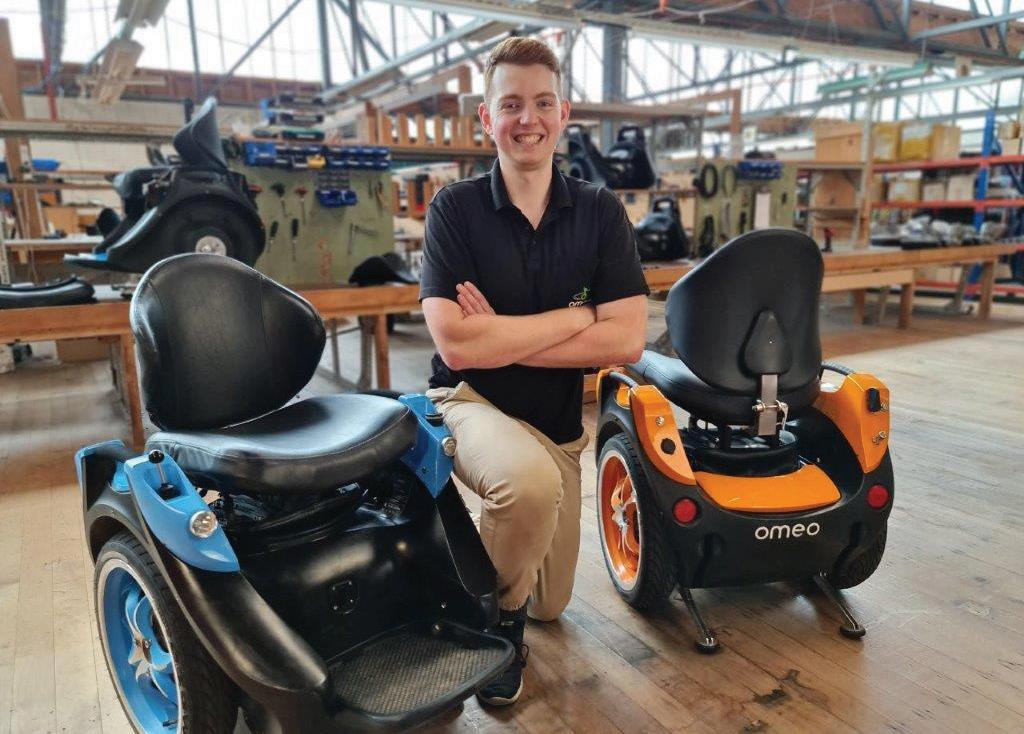