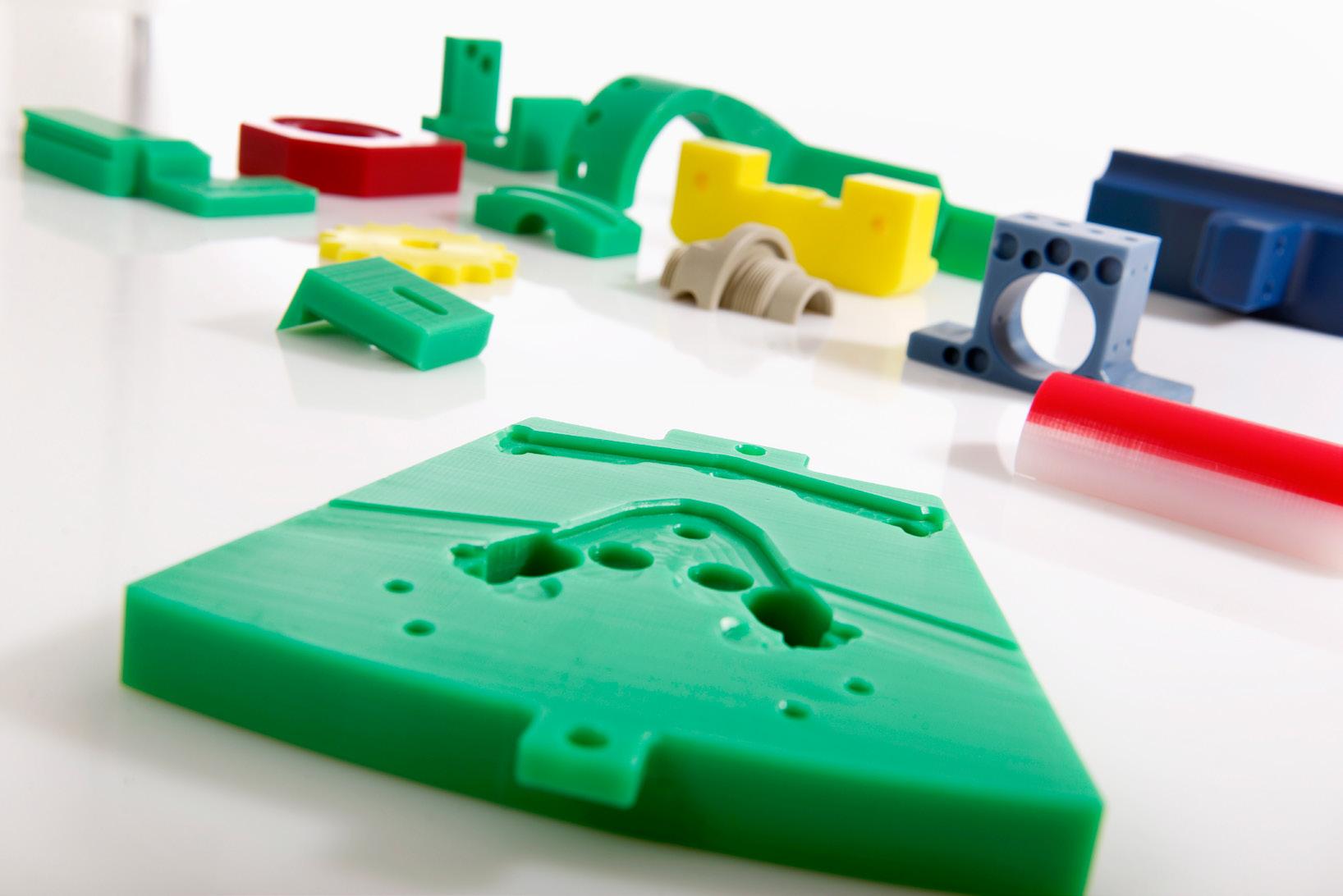
3 minute read
Plastic alternatives should not be written off
August - September 2020 Why we shouldn't dismiss plastic alternatives
Hero plastics’ performance during Covid-19 pandemic points to expanding industrial safety and hygiene uses
Advertisement
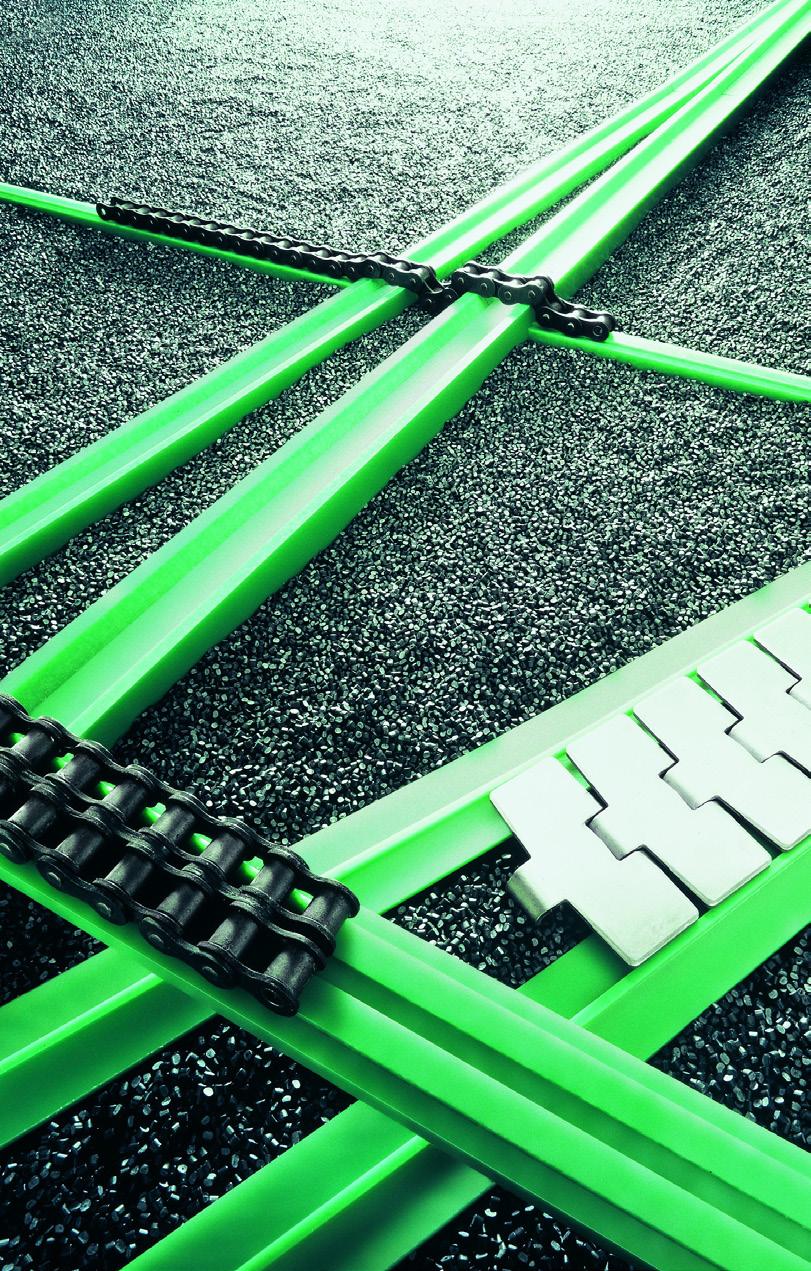
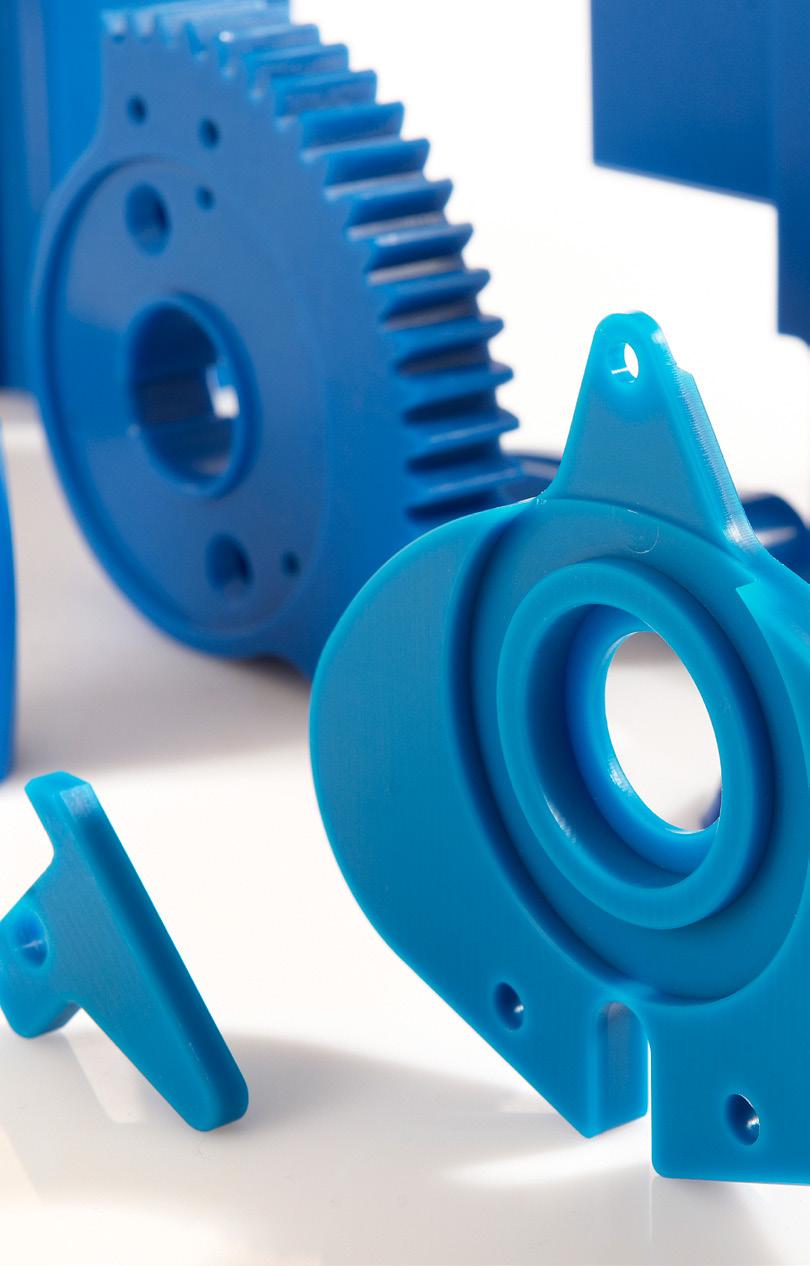
One of the major groups of materials protecting medical and front-line workers during the Covid-19 pandemic, engineering plastics, is also making headway as an alternative to metals in hygiene and safety-conscious industrial markets, including machinery componentry, safety, automation and industry 4.0 and process applications.
Most of the PPE equipment used in the masks, goggles, gloves, gowns and coveralls involved in the Covid-19 pandemic are made of non-woven polymer polypropylene, while other translucent shields between customers and retail staff, for example, are made from polycarbonates such as Wearguard™, which are not only very tough, but also very easy to wash down and resistant to chemicals involved.
“It is in fact quite possible to introduce anti-viral and anti-bacterial qualities into the formulation used to manufacture different engineering thermoplastics families – while other plastics groups are suitable in their natural or food grade state to substitute hygienically and cost efficiently for metals used in production process and Industry 4.0 higher speed automation,” says engineering plastics authority Mr Laurie Green.
Custom manufactured plastics – sometimes with added hygienic, mechanical and lubrication qualities – can include Wearlon™ PTFE (Polytetrafluorethylene) and Wearex™ UHMWPE (ultra-high molecular weight polyethylene). Standard product groups, including Wearlon™ Nylon, Wearace™ Acetal and Wearthane™ polyeurethane can not only be modified, but are often suitable in their
natural state as light but tough high-performance alternatives to metals in applications demanding excellent impact resistance, high mechanical strength, high physical protective qualities, strong washdown and chemical performance and outstanding sliding and machinability qualities.
“In addition to being used as machinery components – such as shields, rollers, bearings, guards, sprockets, guides and sheaves – some of these versatile materials can be used to fabricate entire large machinery components, such as plummer blocks,” says Mr Green, who is Managing Director of national and international plastics supplier Cut To Size Plastics. Cut To Size Plastics engineering materials comply with some of the world’s toughest food contact and process standards. The company is also registered on the NSW Government’s Covid-19 Emergency Suppliers portal as a company that can supply raw material for manufacturing processes and products, as well as adapting its processes to manufacture components for urgently needed medical equipment, such as ventilators.
Mr Green, who has more than 40 years’ experience in specifying and supplying engineering plastics, says the Covid-19 pandemic will give manufacturers a renewed focus on the hygiene and washdown qualities of materials to be selected for use in processes and machinery, particularly those involved in the preparation and export of food, beverage, medical and agricultural products.
“We are not saying for a moment that engineering plastics are better in every instance than metal alternatives, because you have to consider each application on its particular engineering merits. But we do say that, for an expanding variety of applications, engineering plastics may be ideal and cost-efficient for applications for which they have not previously been considered – until now.”
“Australian manufacturing has for a long time been metals-focussed, because that is the way it has always been done here. European and other purity-focused manufacturers have been much more open to change, and they are the ones who have been leaders in purity and hygiene standards. In a very hygiene-conscious post-covid world, our local attitudes may begin to
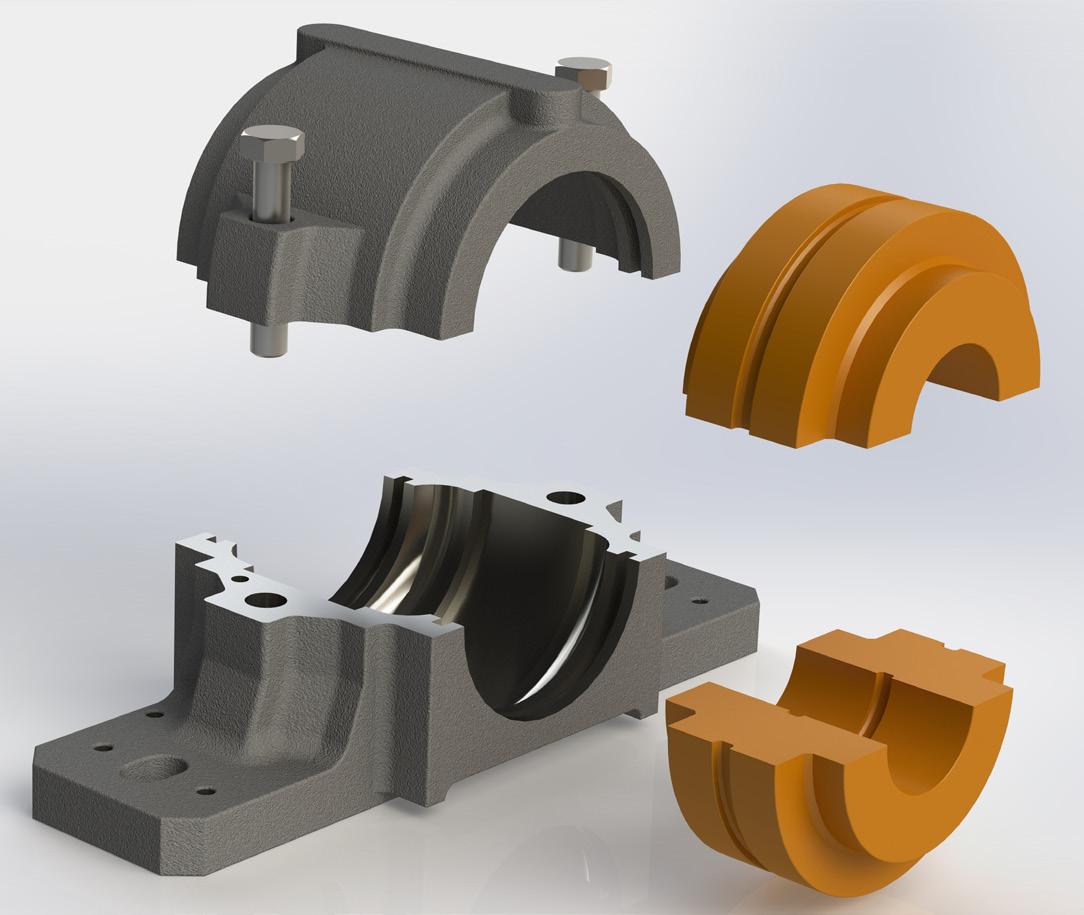
change,” says Mr Green, whose company has recently published guides to materials suitable for particular purposes in food and beverage processes and which also provides individual guidance to particular inquiries.
To cope with expanding demand for engineering plastics componentry, Cut To Size Plastics recently expanded its precision engineering capabilities with the introduction of a Morbidelli Author M100F heavy duty CNC router and machining centre. The performance and flexibility offered by the new machine provides a 60% time saving in machining cycles compared with older technology.
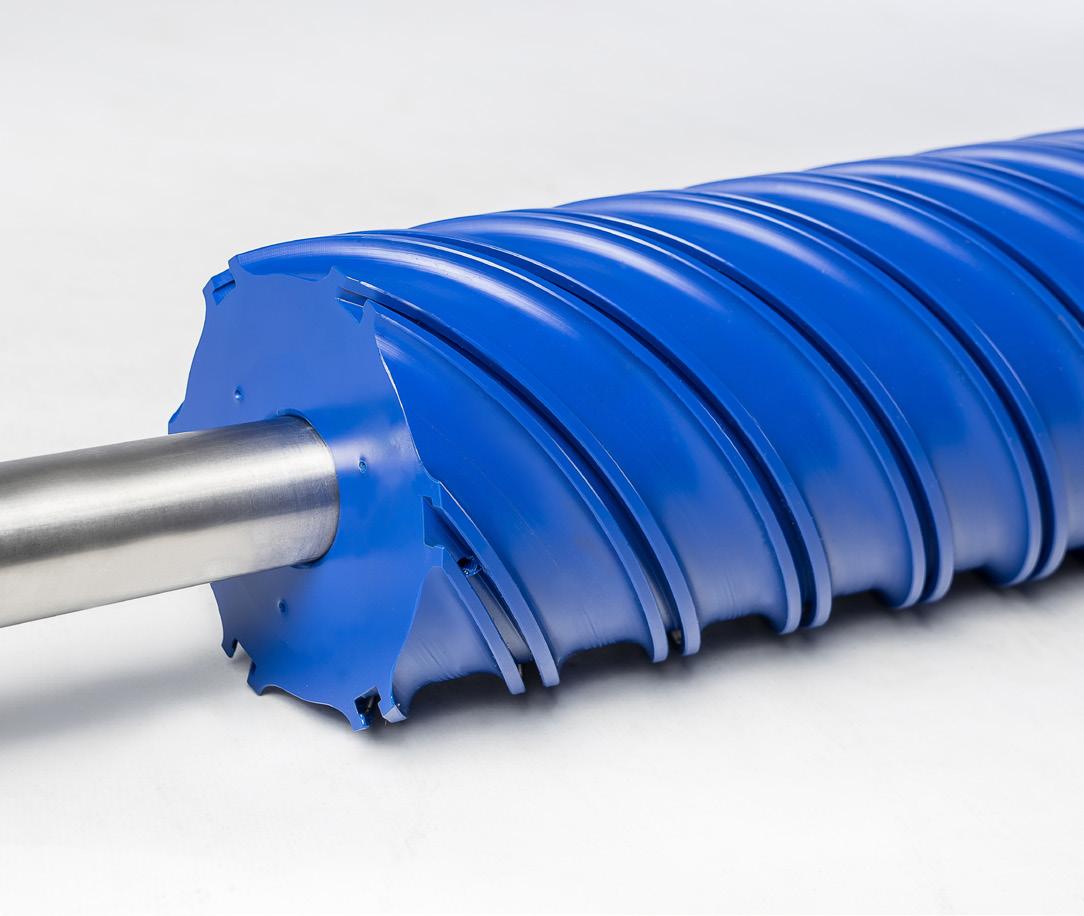
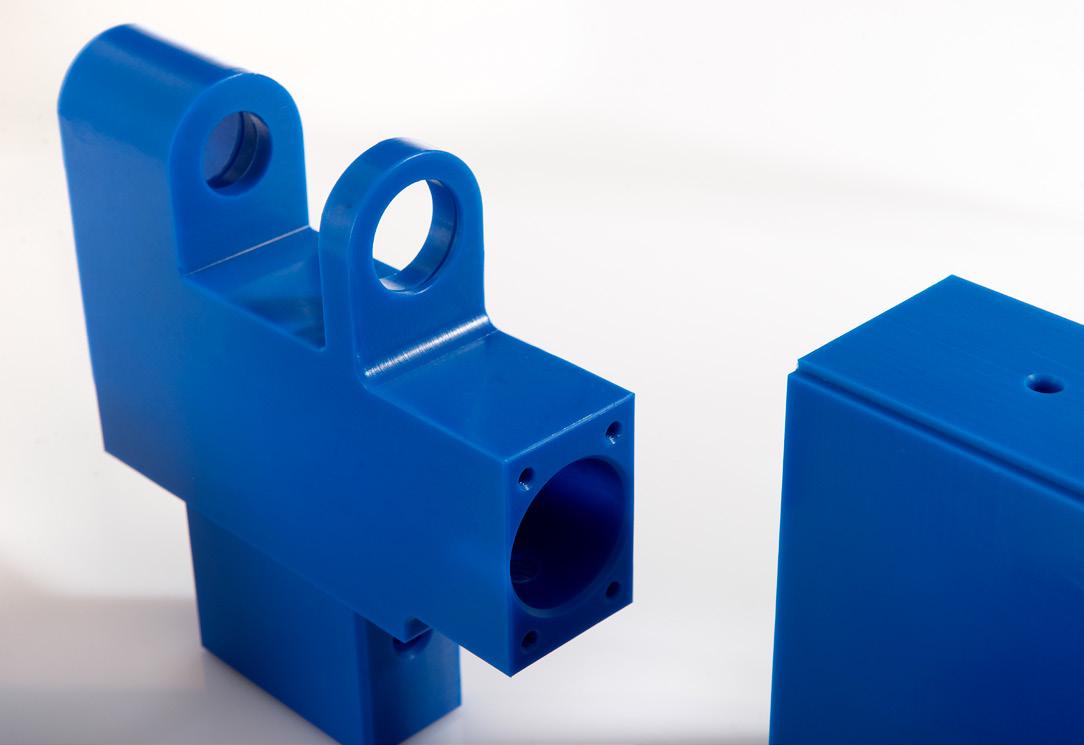
