
6 minute read
3D-printed housing
Printing our way out of the housing crisis
3D printing a range of housing from emergency to luxury residential and high-rise apartments meets New Zealand building standards and stringent European and US standards, says Property& Build publisher Mike Bishara
Advertisement
Development is held back here by our own inability to adapt, retrain and deal with the major changes that will be wrought in the construction sector. The situation is aided and abetted by a Resource Management Act that has not been fit for purpose for years.
In the US, Europe and China off-site factory construction of walls, trusses and roofs has turned residential new building into largely producing a solid foundation and provision for the storm, waste and drinking water plus hooking up the electricity.
Here that privilege (with a lack of the need for double and triple consenting nightmares) is largely reserved to a few major players with a band of would-be competitors struggling in a maze of bureaucracy to compete. Legislation to create a more even playing field is wending its way tortuously through parliament
We are well behind the mark in even getting off site consented manufacturing universally approved while offshore, off site construction has moved forward and is now being increasingly augmented with onsite 3D printing.
The disruption of the construction sector worldwide is happening all around us while we remain passive observers in the midst of our own housing crisis.
Rush Digital chief executive Danu Abeysuriya says 3D printed homes could help to solve New Zealand's housing crisis but hundreds of jobs would be lost in the process.
Abeysuriya says for example California needs two million new homes to overcome its housing crisis and has introduced progressive rules around new technology and have developed a standard for 3D homes, which companies have taken into their designs. "There's a reason it's called disruptive technology. The reality is - if we do things the same way that we are doing them right now, we are never going to fill that backlog," Abeysuriya says
As well as the speed of the development of 3D houses, they also cost significantly less.
CNN reported the three-bedroom, two-bathroom homes to be built in
Rancho Mirage California, which come with a deck and a swimming pool, will have a starting price of US$595,000 compared with the average owner-occupied value of US$825,738.
Prices are low because the owners don't have to pay for labour to build the homes. US based 3D builder Mighty Buildings told the Guardian up to 80 percent of the construction can be automated, with 95 percent fewer labour hours and 10 times less waste than conventional construction.
On terms of emergency or special housing needs 3D printing is clearly the way to go. Another US innovator Icon has so far delivered more than two dozen 3-D-printed homes across the US and Mexico.
Coming projects run the gamut from social housing to disaster relief housing to market-rate real estate.
A project is also in the works with NASA to develop space-based construction systems that it hopes will eventually serve as habitats on both the moon and Mars.
When Icon was founded, its biggest hurdle was convincing sceptics, Jason Ballard, Icon’s chief executive told the New York Times.
“I had builders and developers explaining to me how it’s not possible to get concrete to do that, even as I walked them up to our 3-D printed house,” he says.
“Now our biggest challenge is we’ve just got to make more printers.”
An Icon partnership in Nacajuca, Mexico is building a village for residents living in poverty in shanties with dirt floors, and prone to flooding in the rainy season.
Building a home with Icon’s Vulcan II printer looks much like a massive softserve ice cream cone:
Layers of lavacrete, the company’s proprietary concrete mix, are poured one after another in long swirls. The printer is controlled by a tablet or smartphone, requires as few as three workers and can complete a home in less than 24 hours.
Up to 500 new homes being built by New Story, a San Francisco non profit organisation focused on providing housing solutions to communities in extreme poverty.
They can also be constructed to tolerate natural disasters: Nacajuca sits in a seismic zone.
New Story has partnered

Plopping a 3-D printer from an American tech company into the heart of a rural village in Mexico was a big shift
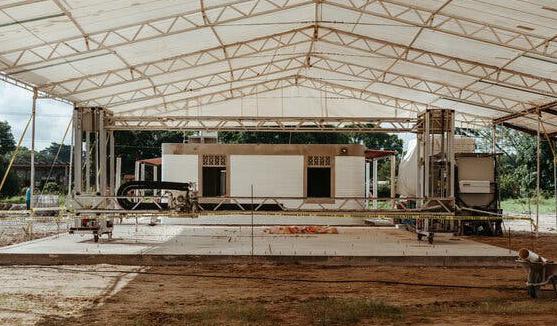
with Échale, a social housing production company in Mexico, and Icon,
Échale, which has been operating in Mexico for 24 years, helped New Story select residents for the new homes based on need. It decided to sign the titles of each home not to a whole family but to the woman of the house.
“It’s to protect the family,” said Francesco Piazzesi, Échale’s chief executive. “A man will sell a house if they need to. A woman will do whatever she needs to do to save the house for her children and her family.”
Échale hires local workers to build their own communities, so plopping a 3-D printer from an American tech company into the heart of a rural village was a shift, the New York Times reported.
“If you came to Nacajuca when the 3-D printer was there, you would see machinery that looked like a RoboCop movie,” Piazzesi says.
“It’s creating opportunities for the people because something gets into the community and it lasts.”
“We know that being able to build more quickly, without sacrificing quality, is something that we have to make huge leaps on if we’re going to even make a dent on the issue of housing in our lifetime,” says Brett Hagler, New Story’s chief executive.
Speed is only one factor in bringing a village to completion — New Story has teamed up with local officials in Tabasco to bring sewage services, electricity and water to the community.
The 3-D printing market grew 21 percent in the US last year last year, and Hubs, a manufacturing platform, projects that it will double in size over the next five years.
A manufacturing process that builds objects layer by layer from a digital file, 3-D printing is set for explosive growth.
After a pandemic-related boom from printing objects like test swabs, protective gear and respirator parts, the 3-D printing market is forecast to be worth $55.8 billion by 2027, according to Smithers, a technology consulting firm.
Single-family homes are a good testing ground for the durability of 3-D printed construction because they are small and offer a repetitive design process without much height, says Henry D’Esposito, who leads construction research at JLL.
“It really is a very effective and efficient way to build a small segment of properties, but it’s not something that applies across the broader commercial real estate ecosystem,” D’Esposito says.
“We don’t know exactly how these buildings will perform over decades or what the long-term value retention will be for them. So if you’re talking to an investor or lender, that’s a big yellow flag.”
The future and a warning
Layers of lavacrete, are poured one after another in long swirls. The printer is controlled by a tablet or smartphone, requires as few as three workers and can complete a home in less than 24 hours
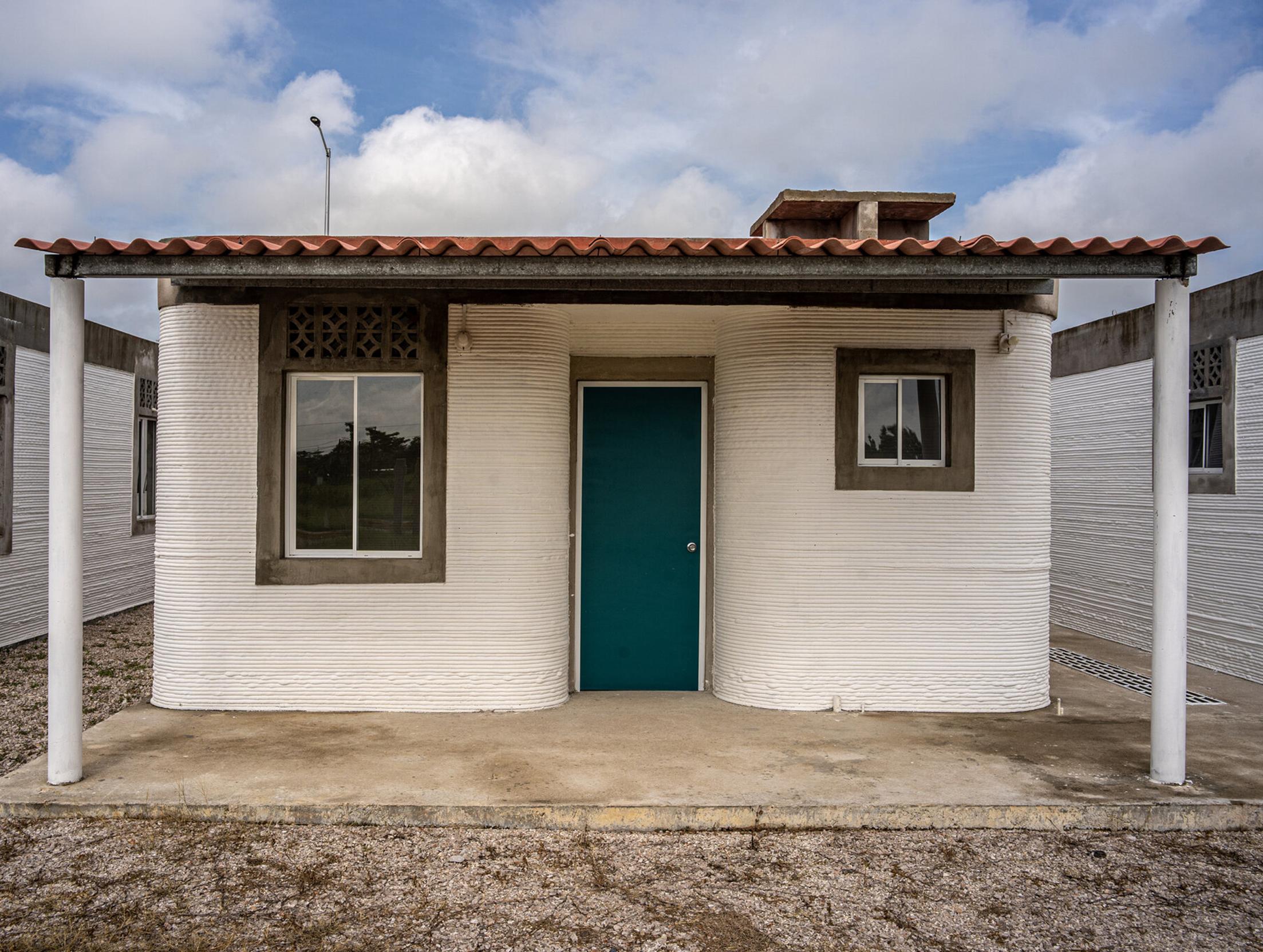