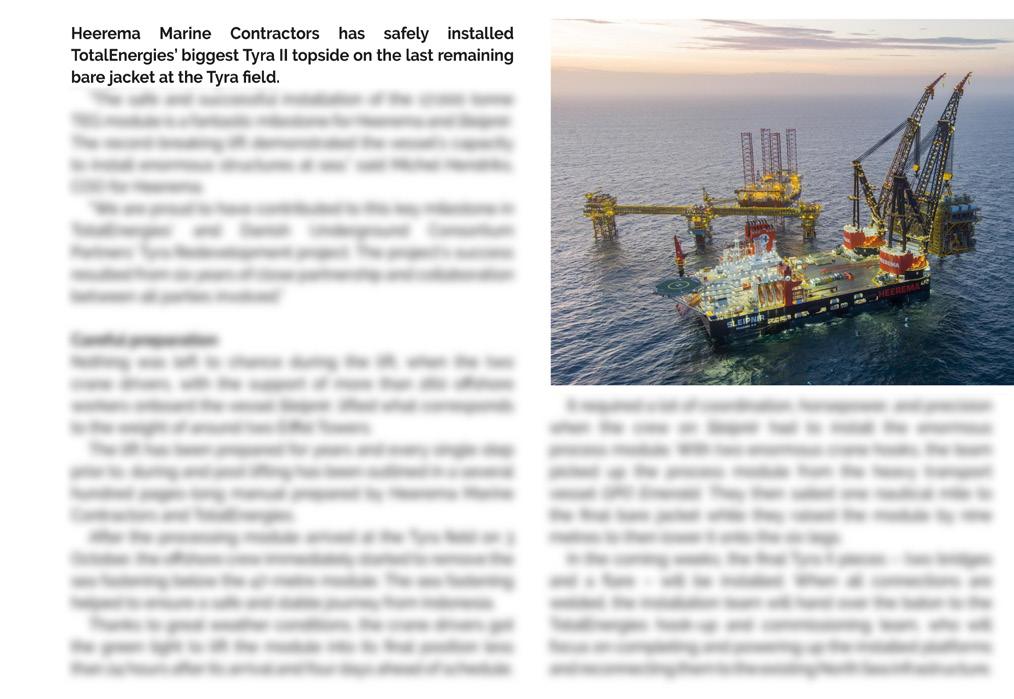
10 minute read
Heavy lifting
HEEREMA BREAKS HEAVY LIFT RECORD
A heavy lift contractor has broken a record with the lift of a 17,000 metric tonne heavy process module, which it says is the heaviest crane lift ever undertaken at sea
Heerema Marine Contractors has safely installed TotalEnergies’ biggest Tyra II topside on the last remaining bare jacket at the Tyra field.
”The safe and successful installation of the 17,000 tonne TEG module is a fantastic milestone for Heerema and Sleipnir. The record-breaking lift demonstrated the vessel’s capacity to install enormous structures at sea,” said Michel Hendriks, COO for Heerema. ”We are proud to have contributed to this key milestone in TotalEnergies’ and Danish Underground Consortium Partners’ Tyra Redevelopment project. The project’s success resulted from six years of close partnership and collaboration between all parties involved.”
Careful preparation
Nothing was left to chance during the lift, when the two crane drivers, with the support of more than 260 offshore workers onboard the vessel Sleipnir, lifted what corresponds to the weight of around two Eiffel Towers.
The lift has been prepared for years and every single step prior to, during and post lifting has been outlined in a several hundred pages-long manual prepared by Heerema Marine Contractors and TotalEnergies.
After the processing module arrived at the Tyra field on 3 October, the offshore crew immediately started to remove the sea fastening below the 47-metre module. The sea fastening helped to ensure a safe and stable journey from Indonesia.
Thanks to great weather conditions, the crane drivers got the green light to lift the module into its final position less than 24 hours after its arrival and four days ahead of schedule.
It required a lot of coordination, horsepower, and precision when the crew on Sleipnir had to install the enormous process module. With two enormous crane hooks, the team picked up the process module from the heavy transport vessel GPO Emerald. They then sailed one nautical mile to the final bare jacket while they raised the module by nine metres to then lower it onto the six legs.
In the coming weeks, the final Tyra II pieces – two bridges and a flare – will be installed. When all connections are welded, the installation team will hand over the baton to the TotalEnergies hook-up and commissioning team, who will focus on completing and powering up the installed platforms and reconnecting them to the existing North Sea infrastructure.
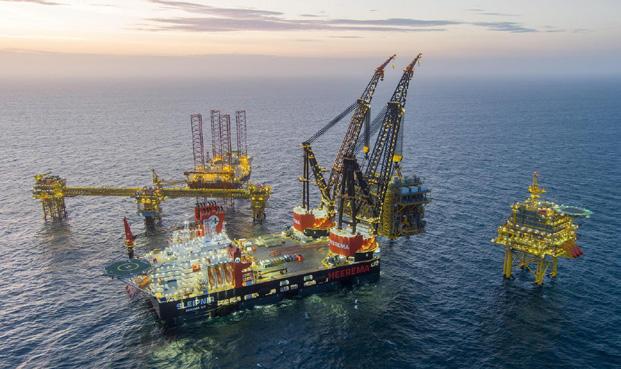
8 Heerema
has nstalled TotalEnergies’ biggest Tyra II topside on the last remaining bare jacket at the Tyra field
ScaffFloat adds knuckle boom crane to pontoons
Pontoon hiring firm ScaffFloat has added a 2.8t crane to its product - leading to some comparing it to a workboat.
Made entirely from scaffold components, the ScaffFloat system has now been fitted with a crane and used in a project on the River Thames for ladders, chains and wooden fendering installation.
The crane, which can lift 600kg and was fitted to a steel crane base, was designed according to the Lloyd’s Register Code for Lifting Appliances in a Marine Environment and assessed in line with IMO standards, founder and managing director Toby Budd says. The pontoon was licensed by the Port of London Authority as a commercial vessel before the work was carried out.
For the project on the Thames ScaffFloat mobilised an 8m x 6.4m ScaffFloat, fitted with two 60hp, high-thrust outboards giving 0.8t of bollard pull and a 5-knot service speed, said Budd. Thirty of the company’s small 0.5m3 patented plastic floats provided 15m3 of buoyancy, giving it a comfortable 5t payload on the large open 50m2 wood deck. ”We started off with simple pontoons that could be used for access. Then we added outboard pods to the pontoons turning them into workboats, suddenly they became much more useful to our customers and now 90% of our hires go out as a ‘vessel’. ”We then added spud legs, deck winches, and other bolt-ons to add further value. But there is no doubt that it is the addition of a knuckle boom crane that marks the biggest advance in the system from an engineering perspective. Lifting is a key component for most marine works and I am delighted we can now offer this to our customers.”
ScaffFloat won the Spirit of Innovation Award at Seawork in 2019. It is now developing a crane base for larger projects.
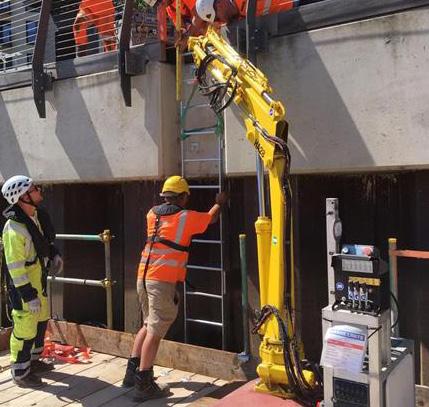
Credit: ScaffFloat
8 Work on the River Lea using the ScaffFloat
crane
Crane manufacturer Liebherr has confirmed the successful completion of two major installation projects using its largest offshore crane in Germany and France.
The HLC 295000 has a lifting capacity of 5,000 tonnes and a maximum lifting height of 175 metres above deck, and was used on Orion, which Liebherr says is ‘currently considered the world’s most innovative vessel in the offshore wind industry’.
In the first project, French offshore wind farm Fécamp, Orion and the crane set down a 1,300-tonne jacket foundation on prepared seabed in preparation for a 2,200-tonne transformer platform to be placed on top.
“It was particularly important not to lose sight of the tight schedule and the weather conditions in Normandy. which was achieved not least thanks to the good dynamic positional system of the Orion and the high precision in the control of the HLC 295000,” says LiebherrMCCtec Rostock.
For the German Arcadis Ost 1 wind farm in the Baltic Sea. the crane was used to install 28 monopile foundations with lengths of up to 110 metres and weighing up to 2,100 tonnes each.
“The innovation of the Orion is the ability to install the monopiles floating,” says Liebherr. “This means that no time-consuming jack-up process of the ship out of the water is necessary, as it has been the case up to now with jack-up units.”
Lieberr says the crane is often in use for 24 hours non stop. ”Our initial experience indicates that the installation times of previous vessels of about 3 to 3.5 days per monopile can be significantly reduced to about 0.9 to one day per monopile with the use of the Orion and our HLC,” said Robert Pitschmann, global application manager, Liebherr-MCCtec Rostock.
“The HLC series and the expansion of the heavy-duty crane range are firmly anchored in Liebherr’s strategy, not least because of the energy transition,” the company says. “In order to ensure a sustainable energy supply for present and future generations, significantly more and larger offshore wind turbines are being built.
“For the construction of these modern wind turbines, the lifting height of the HLC 295000 is a decisive factor. In addition, there is a trend towards decommissioning disused oil and gas platforms. This involves dismantling large and heavy parts on the open sea.”
LIEBHERR COMPLETES TWO OFFSHORE INSTALLATIONS
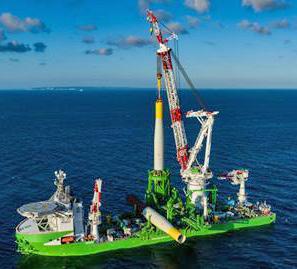
8 Liebherr’s installation vessel Orion transporting
the HLC 295000 heavy-lift crane
Contact us for more information:
CASE STUDY: THREE FAST FERRIES MOVED IN ONE
Specialist expertise in bespoke logistics was called upon in a recent single-ship transport of three 36m catamaran fast ferries
Peters & May received an enquiry from Golden Cargo in January 2022 concerning the transport of three aluminium, light construction carbon fibre ferries from their builder, Brodrene AA in Hyen, Norway to their new operator, Hellenic Seaways in Piraeus, Greece.
The vessels are broad of course (36m x 9.7m), but relatively light at just 82 tonnes each.
As Paul Elsom, Peters & May’s Global technical director, explained, there was an additional challenge of getting all three ferries onto one vessel.
“At Peters & May we take both decarbonisation of all our operations and providing the best value to our clients very seriously,” he said. “With this in mind, instead of fulfilling this transport with more than one trip, we decided to look at using the state-of-the art Rolldock Sky heavy cargo vessel with one of the ferries stowed below deck level and the other two above.
“It would take a bit of maths to get all three aboard securely, particularly as they all had to be tandem lifted, but this is what we do and successfully moving the three ferries in just one trip would save both carbon from the atmosphere and costs for our client.”
Rolldock Sky, launched in 2016, is a highly configurable 142m vessel with three different loading modes – Float-In / Float-Out, Roll-On / Roll-Off and Lift-On / Lift-Off.
During Flo-Flo operations, the vessel can submerge to 12.5 metres, creating a draught in hold of 6.6 metres. With a draught of 5.67 metres, the vessel is suitable for shallow draught waters, and each deck crane can lift up to 350mt, or 700mt in tandem lifting.
Change needed in submersible function
Peters & May was unable to use Rolldock Sky’s submersible functionalities on this occasion, as the fjord depth at the loading location meant local regulations deemed this too risky in the unlikely event of a vessel systems fault and subsequent salvage operation.
The vessel’s tandem lift capability would be key to this operation though, not due to the overall weight of the ferries, but to follow the lifting conditions stipulated by the shipbuilder.
“Loading operations started on July 11 and took two days because one ferry was stowed underdeck while the other two were on deck,” said Elsom. “Using two cranes in a tandem lift configuration meant that the ferries had to be loaded in a fore and aft configuration.”
The loading operation was conducted in a fjord in northern Norway, which brought its own positives and negatives.
“The steep valley sides made it glass calm - so perfect lifting conditions,” said Elsom. “The marine traffic there was very light, so we had plenty of time to get things set up well, but there was no berth available, leaving us to conduct the lifts at anchor.
“Finding a suitable anchorage in the very deep water there was a bit of a challenge in itself. We used tugs to deliver the ferries alongside the ship and all loading, cradling and lashing equipment had to be supplied to the vessel at its last port of call - in Finland!”
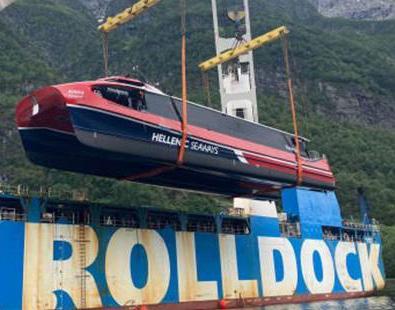
Planning at both ends
Thanks to meticulous planning by Elsom and the Technical Team and loadmaster attendance at both POL and POD (Port of loading and Port of discharge), the operation went without a hitch at either end.
Peters & May would like to thank maritime logistics company Golden Cargo SA, based in Piraeus, Greece, who kept in close contact with the ferries’ owner (Hellenic Seaways/ Attica Group) in Greece, ensuring they could remain confident in this special project shipment through every step from booking to delivery.
Peters & May has worked with major commercial vessel owners and operators for more than a decade, shipping vessels and their equipment across the globe.
8 Rolldock Sky 8
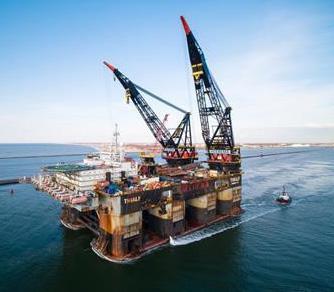
A third motion compensation pile gripper will be built by civil engineering equipment maker Huisman following an order from offshore energy firm Heerema.
The new gripper will allow installation of wind turbines 12.5 metres in diameter, 115 m in height and 3,200 tonnes in weight.
It has been designed specifically for Heerema’s semi-submersible crane vessel (SSCV) Thialf, on the side of which it will be positioned once completed.
Dubbed ’’Heerema’s workhorse’ by Heerema, Thialf has undertaken some impressive projects in her almost 30 years of life.
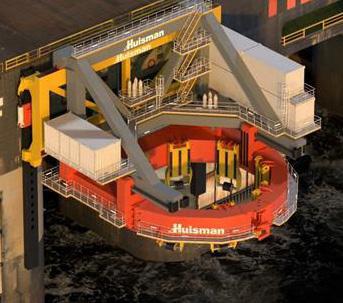
In 2020, eight months of work were completed when seven platform topsides, seven jackets and 22 conductors were removed by reverse installation for
HUISMAN ORDERED TO BUILD THIRD MCPG
8 Thialf
8 HEEREMA - MCPG
ExxonMobil Canada’s Sable offshore natural gas facility. The work involved the removal of 48,000 tonnes of infrastructure, and the company says 99% of that was recycled at the ABLE UK decommissioning yard.
This year, Thialf has been involved in projects in projects in the Baltic Sea, including the Arcadis Ost 1 offshore wind farm.
“Huisman is very honoured to receive this order, for Heerema’s first pile gripper,” said David Roodenburg, CEO of Huisman. ”This is a complex project, the execution of which will draw upon the knowledge and experience of both parties. We are looking forward to collaborating with Heerema to deliver this innovative gripper.”
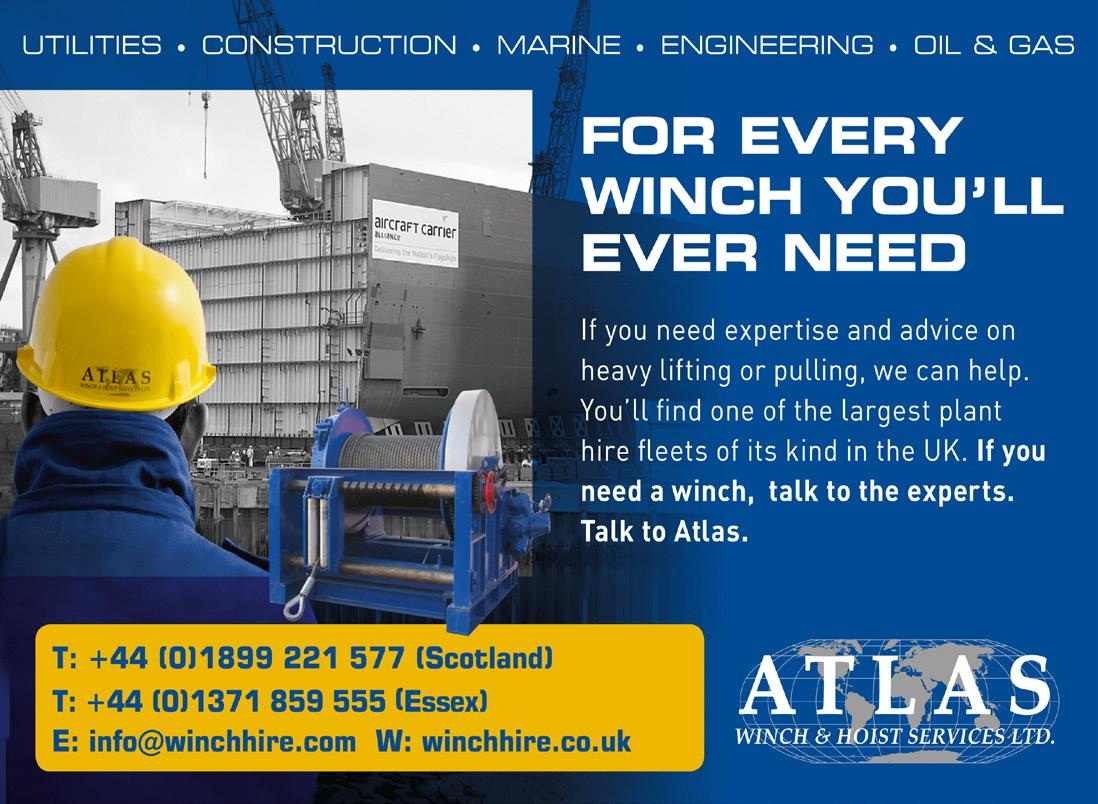