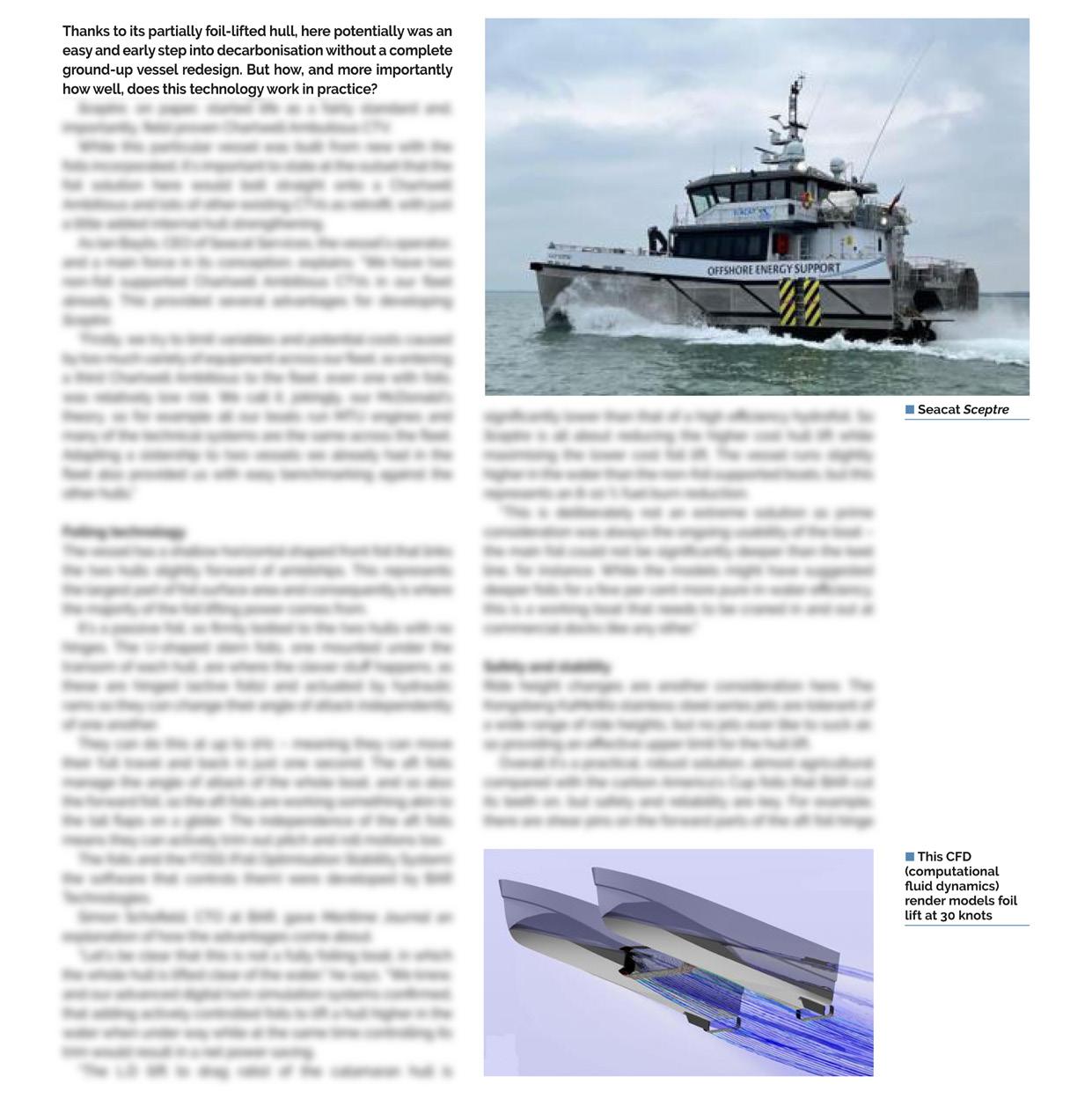
20 minute read
Semi-foiling
CHARTWELL & BARTECH SEACAT SCEPTRE FOILS UNDER SCRUTINY
When Seacat Sceptre hit the water in March 2022, Crew Transfer Vessel operators the world over took notice, reports Jake Frith
Thanks to its partially foil-lifted hull, here potentially was an easy and early step into decarbonisation without a complete ground-up vessel redesign. But how, and more importantly how well, does this technology work in practice?
Sceptre, on paper, started life as a fairly standard and, importantly, field proven Chartwell Ambutious CTV.
While this particular vessel was built from new with the foils incorporated, it’s important to state at the outset that the foil solution here would bolt straight onto a Chartwell Ambitious and lots of other existing CTVs as retrofit, with just a little added internal hull strengthening.
As Ian Baylis, CEO of Seacat Services, the vessel’s operator, and a main force in its conception, explains: “We have two non-foil supported Chartwell Ambitious CTVs in our fleet already. This provided several advantages for developing Sceptre.
“Firstly, we try to limit variables and potential costs caused by too much variety of equipment across our fleet, so entering a third Chartwell Ambitious to the fleet, even one with foils, was relatively low risk. We call it, jokingly, our McDonald’s theory, so for example all our boats run MTU engines and many of the technical systems are the same across the fleet. Adapting a sistership to two vessels we already had in the fleet also provided us with easy benchmarking against the other hulls.”
Foiling technology
The vessel has a shallow horizontal shaped front foil that links the two hulls slightly forward of amidships. This represents the largest part of foil surface area and consequently is where the majority of the foil lifting power comes from.
It’s a passive foil, so firmly bolted to the two hulls with no hinges. The U-shaped stern foils, one mounted under the transom of each hull, are where the clever stuff happens, as these are hinged (active foils) and actuated by hydraulic rams so they can change their angle of attack independently of one another.
They can do this at up to 1Hz – meaning they can move their full travel and back in just one second. The aft foils manage the angle of attack of the whole boat, and so also the forward foil, so the aft foils are working something akin to the tail flaps on a glider. The independence of the aft foils means they can actively trim out pitch and roll motions too.
The foils and the FOSS (Foil Optimisation Stability System) the software that controls them) were developed by BAR Technologies.
Simon Schofield, CTO at BAR, gave Maritime Journal an explanation of how the advantages come about.
“Let’s be clear that this is not a fully foiling boat, in which the whole hull is lifted clear of the water,” he says. “We knew, and our advanced digital twin simulation systems confirmed, that adding actively controlled foils to lift a hull higher in the water when under way while at the same time controlling its trim would result in a net power saving.
“The L:D (lift to drag ratio) of the catamaran hull is significantly lower than that of a high efficiency hydrofoil. So Sceptre is all about reducing the higher cost hull lift while maximising the lower cost foil lift. The vessel runs slightly higher in the water than the non-foil supported boats, but this represents an 8-10 % fuel burn reduction.
“This is deliberately not an extreme solution as prime consideration was always the ongoing usability of the boat – the main foil could not be significantly deeper than the keel line, for instance. While the models might have suggested deeper foils for a few per cent more pure in-water efficiency, this is a working boat that needs to be craned in and out at commercial docks like any other.”
Safety and stability
Ride height changes are another consideration here. The Kongsberg KaMeWa stainless steel series jets are tolerant of a wide range of ride heights, but no jets ever like to suck air, so providing an effective upper limit for the hull lift.
Overall it’s a practical, robust solution, almost agricultural compared with the carbon America’s Cup foils that BAR cut its teeth on, but safety and reliability are key. For example, there are shear pins on the forward parts of the aft foil hinge
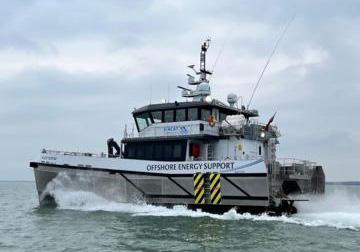
8 Seacat Sceptre
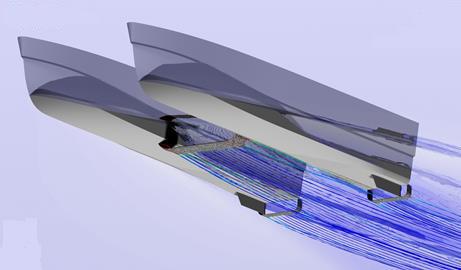
8 This CFD
(computational fluid dynamics) render models foil lift at 30 knots
Waves at sea are inherently unpredictable, and while we can predict trends, we can ‘‘ never accurately predict what the next wave will be. With that in mind, FOSS derives much of its benefit from the IMUs (inertial measurement units) communicating with the active aft foil rams, which react fast enough to make a big difference in the vessel’s efficiency
systems so an impact with anything large, such as a floating container, will not tear the transoms or jets out of the boat.
The FOSS control system’s underlying technologies fall somewhere under the wide and ever widening definitions of AI (Artificial Intelligence) and machine learning.
As Simon Scofield explains: “The foils are not entirely preprogrammed, nor are the foils solely reacting to the vessel’s accelerations at only that moment. The system has to also have a degree of prediction built into it but there are limits to how much of this it can do.
“Waves at sea are inherently unpredictable, and while we can predict trends, we can never accurately predict what the next wave will be. With that in mind, FOSS derives much of its benefit from the IMUs (inertial measurement units) communicating with the active aft foil rams, which react fast enough to make a big difference in the vessel’s efficiency.”
The 8-10 % fuel reduction number is only part of the story, which is fortunate as Seacat Sceptre cost approximately 10% more than a non-foiled version of the same boat. That number was recorded in flat water, and findings from Sceptre’s first season at Seagreen – a £3 billion (€3.4 billion), 114-turbine Scottish wind farm development venture between SSE Renewables and TotalEnergies in the North Sea Firth are much more encouraging.
“Vertical accelerations are also markedly reduced and average transit times reduced,” says Ian Baylis. “We run Reygar’s BareFleet monitoring system and can see at any time how our boats are working out on the wind farms. This outputs data on everything from fuel use, to speed, to motion sickness reports and vomiting events, which are down 15% on Sceptre compared with the foil-less boats.
“The FOSS system will support up to 35% displacement through vertical lift to the boat – when you put so much less hull in the water the motions of that hull are dramatically reduced. The rougher it gets, the bigger the cost savings that come from FOSS as the skipper need not reduce speeds as much. At slow speeds when manoeuvring in port and at the towers, skippers report that Sceptre is indistinguishable from her foil-less sisterships.”

Decarbonisation
The drive to decarbonisation of our energy sector is gathering pace, and without providing the exact and rather business confidential numbers, Ian Baylis does indicate that customers are starting to understand that there is a cost to green.
“Day rates boil down to the cost of the boat, but when you factor in the wind farm operators’ decarbonisation commitments, Seacat’s own decarbonisation commitments, the fact that the boat uses less fuel, transits faster and looks after its passengers and crews so much better, the overall package is environmentally, financially and morally attractive,” he says.
“We are looking at retrofit FOSS – equipping further boats in our range, but doing so while looking at other areas too, such as engine upgrades, future fuels and hybridisation.
“FOSS is simply something that works and we were able to do now. It will be some years before we see dockside green hydrogen, or in many parts of the world even dockside AdBlue pumps for our Tier III diesels.
“Getting decarbonisation gains from hull efficiency pays back now, but will also pay later when we re-engine such a boat with a more efficient, greener propulsion technology as it becomes more viable.
“It’s not a ‘white elephant’ technology, unlike investing too early in a future fuel propulsion system that may or may not ever obtain the critical mass of infrastructure to become viable.”
This CFD (computational fluid dynamics) render models foil lift at 30 knots.
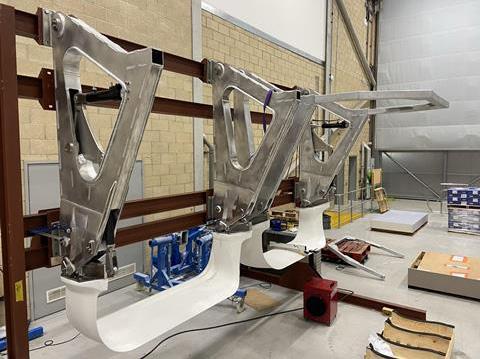
8 The rear
U-Shaped foils are hydraulically actuated at up to 1Hz
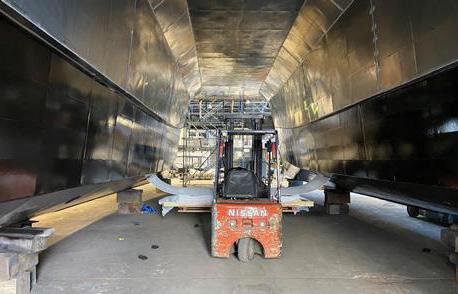
8 The main
horizontal foil is bolted between the two hulls just forward of amidships
CIVILS CONTRACTOR IN PROJECT FIRST WITH TENSIONER
Maritime Developments (MDL) has carried out transpooling and installation of mooring wire rope off the coast of India using a flex-lay spread
Consisting of a TTS-4/140 series tensioner, an adjustable radius controller, a reel drive system and an overboarding chute, the spread was mobilised onboard a locallyavailable construction support vessel (CSV).
“Another fantastic project for MDL where our fresh approach to overcoming project challenges delivered a successful campaign,” said Chris Reid, vice president-sales at MDL.
“The application of MDL’s lay spread, with our marketleading tensioner as the master item, delivered a safe and lean mooring solution, allowing for the wire rope to be installed in a single offshore trip, using a vessel of opportunity – that is, one that was readily available in the region.”
Eliminating risk
During the project, more than 6.4km of the 149mm OD sheathed Spiral Strand Wire Rope (SSWR) was transpooled at the mobilisation port in Singapore from storage reels onto five transportation reels. The SSWR was then deployed to moor in an FPSO in 310-500m water depths.
This was the first time an MDL tensioner was used for the installation of a wire rope off a CSV, allowing the project team to maintain consistent line tension and squeeze on the product while benefitting from MDL’s failsafe grip technology preventing unexpected loss of product.
Eliminating the risk associated with hose or other griprelated failure, this unique system removes the single point failure risk associated with other standard tensioners on the market. It provides a directly mounted manifold and accumulator on each individual active grip cylinder, ensuring that the required grip force is maintained in the event of any unforeseen system failure or black out.
Also used on the project was MDL’s adjustable radius controller, which optimised the handling of the wire rope as it was deployed from the double-drum transportation reels, by hydraulically moving in and out to maintain the product in the firing line.
The project followed other mooring projects in the Gulf of Mexico and offshore Brazil, where a similarly innovative approach was taken using an RDS-based spread mobilised onboard a heavy load carrier.
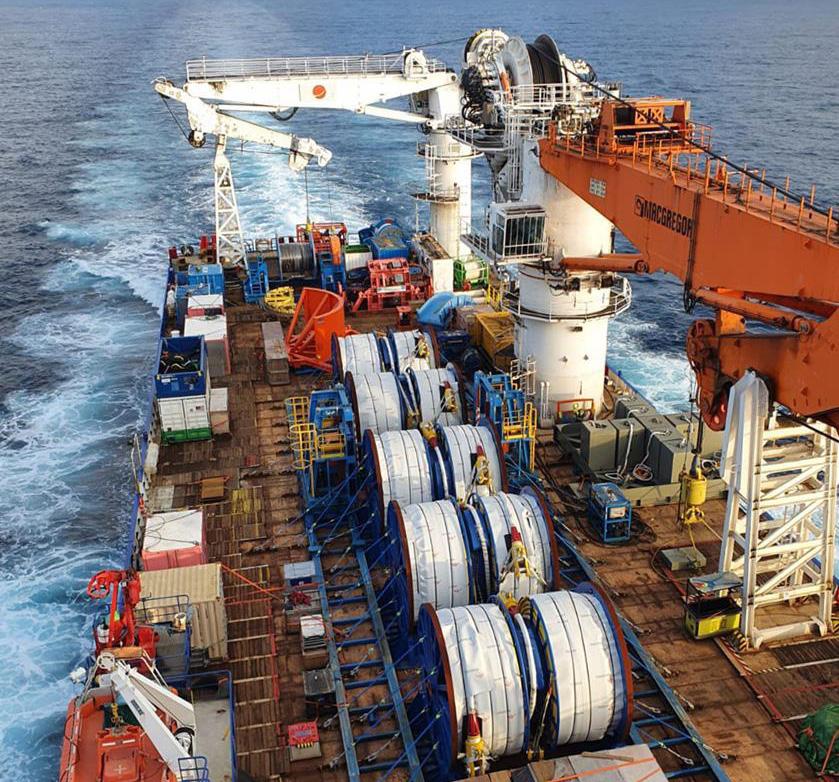
8 This was the
first time an MDL tensioner was used for the installation of a wire rope off a CSV
France could be sinking - models predict
Climate change models are predicting that France will have to spend €8 billion to protect the country’s buildings - and that doesn’t include roads and railways - as sea levels rise.
Presenting at the recent SeaTech 2022 event in Brest, France, Marissa Yates, a researcher with the government environment institution CEREMA - Centre d’études et d’expertise sur les risques, l’environnement, la mobilité et l’aménagement - (Centre for Studies on Risks, the Environment, Mobility and Urban Planning) said their models offered predictions, but that more data were needed.
Yates’s modelling predicts that 1.5 million people are exposed to the risk of marine flooding; 30km2 of land could be lost to coastal erosion within 50 years; and up to 30,000 buildings could be flooded in the 2100s at the cost of €8 billion.
“We have taken estimates of global climate change and applied it to local scenarios,” she said, adding that France had borders in five oceans and demographics were changing which necessitated action.
However there was still a desperate need for data in order to more accurately make predictions. Despite some records showing that there had been a 16cm sea level rise between 1902 and 2010, just two photographs showing the changing coastline meant seasonal variability and other factors could have played a part, she said. ”Data is sometimes inadequate or contradictory,” she said. ”So we need to take action now without having all the answers. We need to take no-regrets decisions, and assess nature-based solutions for coastal protection.”
Specific measures were not named, but there was a need for observation that hadn’t been accomplished yet, Yates said.
Quoting IPCC (Intergovernment Panel on Climate Change) models, sea levels were predicted to rise by 70cm within a century, Yates told attendees.
PORT PROJECT BRINGS NEW JOBS TO THE UK
Work has begun to build a fourth berth at DP World’s London Gateway hub, which will increase cargo capacity by a third
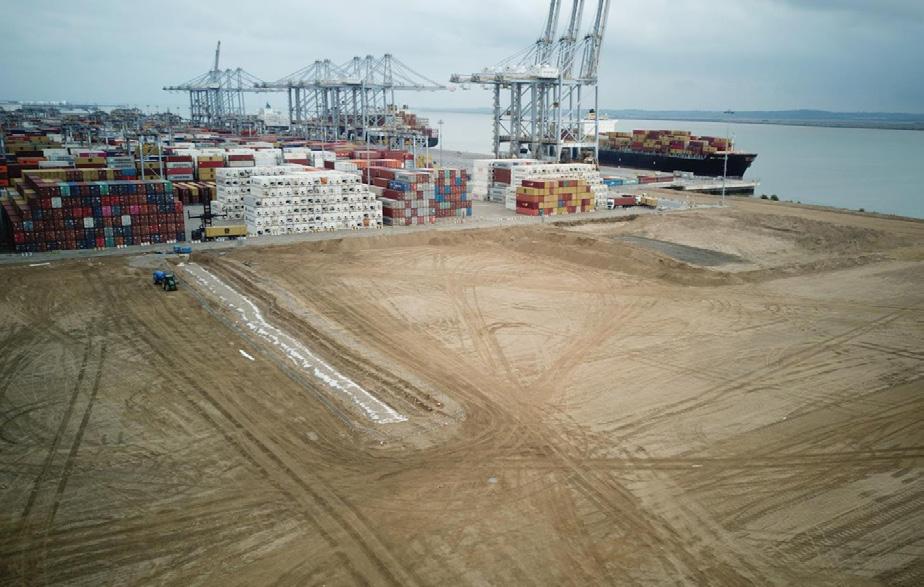
It’s hoped that the resilience of the UK supply chain will be strengthened by the £350 million (€398 million) project, which builds on DP World’s £2 billion (€2.3 billion) investment in Britain over the last decade.
“I am delighted that we have taken the next step in delivery of the new fourth berth and made clear our commitment to investing in and regenerating the areas where we operate,” said Ernst Schulze, UK chief executive of DP World.
“Over the next 10 years we have earmarked a further £1 billion of investment in this country.”
Big ambitions
The construction work will create 1,000 new jobs with the growing logistics park eventually home to 12,000 employees once it completes in five years’ time.
Civil engineering company McLaughlin & Harvey, is working with the port operator to build the new terminal.
“We are delighted to have been awarded the contract with DP World and to begin delivering this vital piece of national infrastructure. We bring with us extensive experience in the marine sector and look forward to engaging with our local supply chain and creating jobs locally,” said Seamus Devlin, covil engineering director, McLaughlin & Harvey Civil.
DP World operates two deep water ports at London Gateway and Southampton in the UK with access to freight rail terminals and a rapidly expanding logistics park on the doorstep of the capital.
By offering a choice of deep-water entry and exit points to and from the country, the port operator said it is giving greater flexibility to shipping lines, cargo owners and exporters.
Back in July, DP World announced that London Gateway handled more than one million TEU in six months between January and June - a record for the port.
Together with throughput at the Port of Southampton, the performance contributed to a record volume of cargo in the first half of the year for DP World’s UK port operation of 1,937,000 TEU.
8 Work has begun
at London Gateway’s fourth berth
13 15 TO JUNE 2023
Southampton United Kingdom
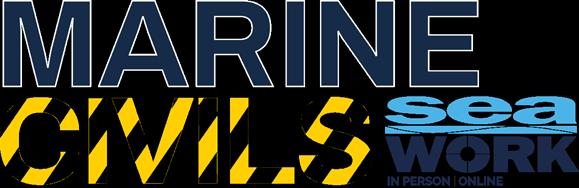
Marine Civils is co-located with Seawork
Marine Civils in association with Seawork - Europe’s leading event dedicated to showcasing the latest equipment and solutions for marine, coastal and other challenging civil engineering projects with unique landscape features.
Reach a larger audience than ever before
Reserve now for 2023 and make the most of marketing support from Marine
Civils, Seawork and our leading commercial marine magazines, in print, online, eNews and via social media channels.
Marine Civils attracts representatives from: • Civil engineering • UK port authorities, • Energy companies • Conservation organisations, amongst others With a big overlap in content and business for companies involved in marine construction, the event is uniquely positioned to provide invaluable opportunities to access wider relevant audiences via Seawork and Maritime Journal.
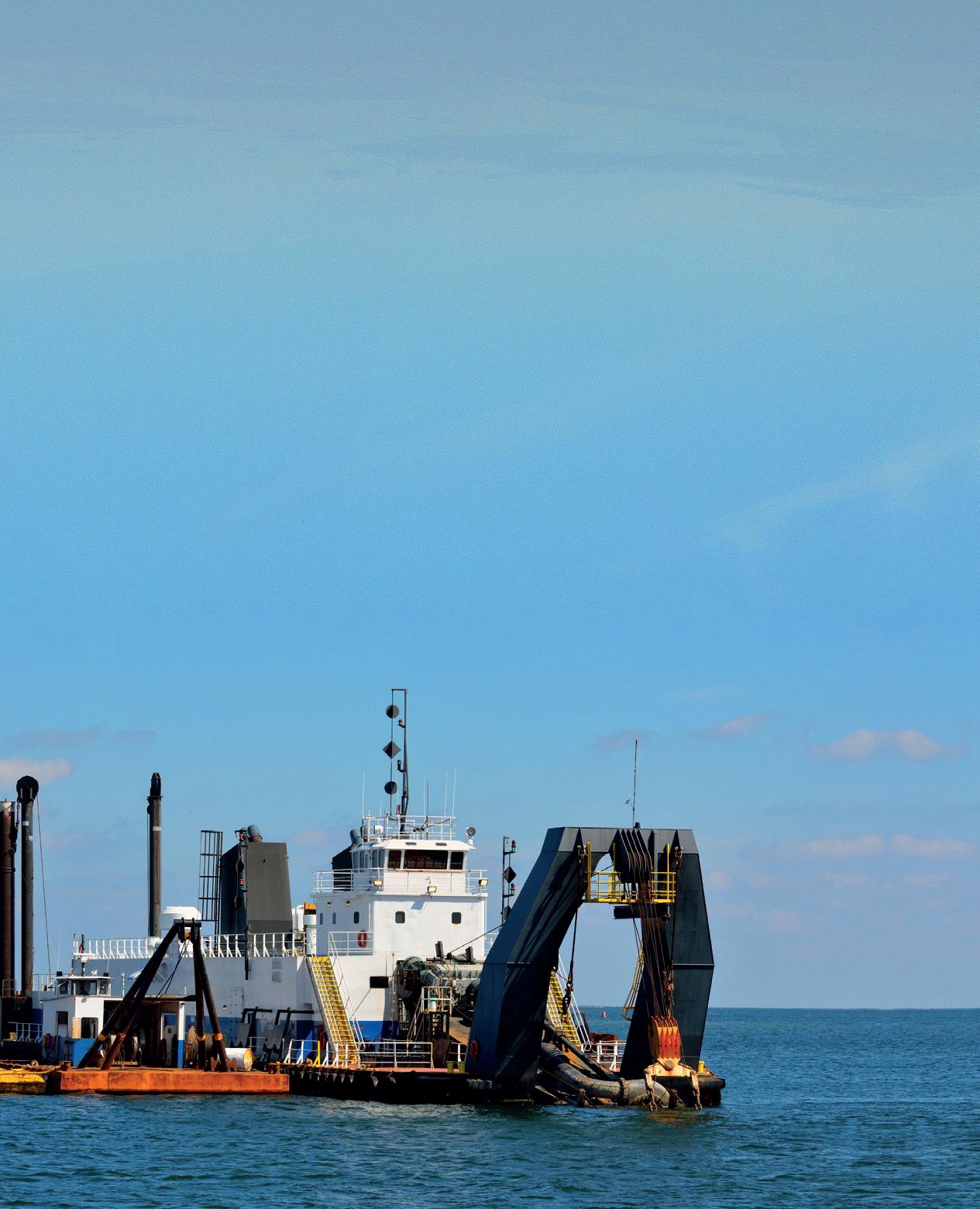
For more information visit: marinecivils.com contact: +44 1329 825335 or email: info@marinecivils.com
Organised by:
Media partners: MARITIMEJOURNAL
QUAYSIDE AND TERMINAL RENEWAL GIVEN GREEN LIGHT
The Port of Antwerp-Bruges and operator PSA Antwerp have agreed to renew the Europa Terminal so that today’s bigger container ships can continue to call at Antwerp
The €335 million renewal work, which will be carried out in three stages over a total of nine years, has been handed to four contractors after a tender process that concluded on October 6.
It will include electrification and wind turbine installation to reduce CO2 emissions, and the quayside will be given a new orientation to ensure there is enough distance between passing ships and the terminal.
An underwater dam will also be built in the final phase to provide additional protection for a nearby nature reserve, the contract provides.
The four winning tender companies were Artes-Roegiers, Artes-Depret, Herbosch Kiere and Boskalis - which ’all have extensive engineering experience in large-scale hydraulic engineering’, according to spokeswoman Daniela Baicoianu, and will form a temporary company under which to operate.
The depth of vessels that will be able to moor at the 1,200m quayside will increase from 13.5 metres to 16, and because it is vital that ships can still moor during the works, it will be done in three stages.
“With the modernisation of the Europa Terminal we are underlining our ambitions as a container port,” said Jacques Vandermeiren, Antwerp-Bruges Port CEO. ”As a world-class port, it is essential that we continue to play at the highest level and are able to accommodate the biggest ships.
“We are, however, aware of the impact of our activities on the surrounding area and local residents. That is why we are committed to reducing mooring emissions, among other things. With a new efficient and sustainable terminal, we are building the port infrastructure of the future.”
Capacity, said PSA Belgium CEO Cameron Thorpe, would increase by more than 70,000 TEU a year. ”We are very happy to undertake this project,” said the four contractors in a joint comment. ”It is a strategic project for the future of the port. It is technically complex and will be carried out in phases without too much disruption to container traffic. It will be a technical and operational feat, but one that we can handle thanks to our extensive expertise.”
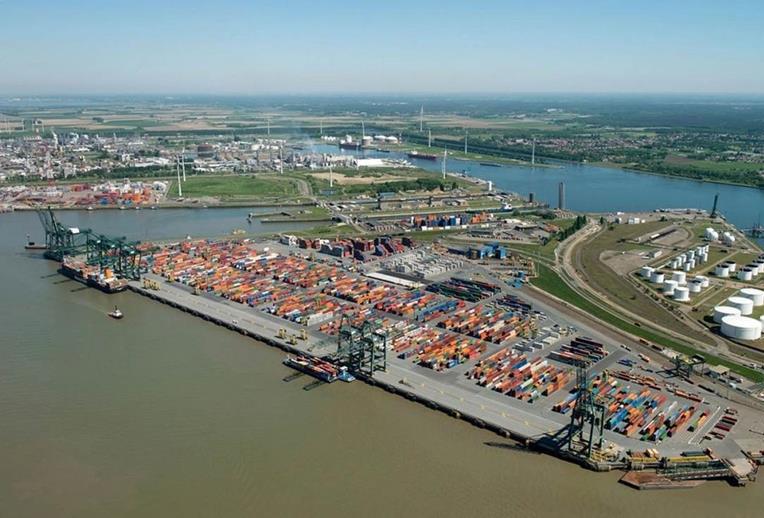
8 Europa Terminal,
Belgium
80 turbines installed at first French offshore wind farm
Jan de Nul’s offshore jack-up vessel has made neat work of an 80-turbine installation at France’s first commercial wind farm, the Saint Nazaire wind farm.
The Vole au vent was used to complete the installation of the turbines, each 6MW, bringing the total generating capacity 7of the wind farm to 480MW.
The electricity generated, says Jan de Nul, will make up 20% of the Loire-Atlantique’s annual consumption.
The turbines were loaded onto the Vole au vent in sets of four at the port of Saint-Nazaire, then transported the 12 miles
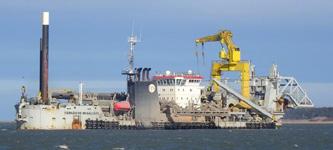
8 Jan de Nul’s cutter suction dredger Fernão de
Magalhães
to the northern part of the Bay of Biscay for installation.
It wasn’t just a case of sticking the monopiles in the seabed, however; because the seabed in the area is rocky and uneven, rock fragmenting operations had to be carried out first to give the jack-up barge a stable base from which to operate.
This was carried out by the company’s Cutter Section Dredger, Fernão de Magalhães, which fragmented the seabed with her rotating cutter head to smooth the ground.
The dredger is 138.5 metres long, with an installed power of 23,520kW.
France is on an energy drive, with plans to build 50 other wind farms of comparable size by 2050.
He also announced plans earlier this year to build another six nuclear reactors.
SUBSEA CABLE LAID FOR HiWave-5 PROJECT
CorPower Ocean and Maersk Supply have installed a subsea export cable off Portugal so that a wave energy converter can be connected to the grid
The 100-tonne cable was installed using Maersk’s Maersk Achiever vessel, and it will provide power and data connection from an on-land substation to the demo site 5.5km offshore.
CorPower’s Wave Energy Converter (WEC) will later form part of a larger four-system array, which will make it one of the world’s first grid-connected wave farms.
To install the cable, the Maersk Achiever was first positioned in a safe water depth within the cable corridor roughtly 1km offshore.
“A messenger line was passed from an onshore winch to the Maersk Achiever, and then connected to a pull-in head,” said Marine Operations manager Robert Argo. “As the cable was being deployed, buoyancy was attached to assist with the cable float into shore. Once onshore, the cable was pulled through a pre-installed cable conduit running under the beach and into the on-land substation, while the remaining cable was deployed using an onboard cable tensioner.
“During the lay operation, cable protection was added to provide additional mass where required for on-bottom stability. Various parameters were also monitored throughout including cable tension, cable departure angle and touch down monitoring. On completion a visual and positioning survey was carried out by a remotely operated vehicle.
“The cable lay process is a notoriously challenging aspect for marine energy projects, with much planning required and adaption to weather windows and ocean conditions. We are thankful to our highly diligent and professional partners, including Maersk Supply Service for their close support throughout the operation entire.”
CorPower is now gearing up for the arrival of the C4 PTO (Power Take Off) system, which has completed a rigorous one-year dry test programme in Sweden. Once transported the PTO will be integrated with a composite hull, which was custom built at CorPower Ocean’s Portuguese base, in Viana do Castelo.
The WEC will later be fused to the cable through a quickconnect interface located at the anchor-head. While providing power connection to feed electricity to shore through the 7.2kV cable it will also deliver high speed communication to the wave farm through fibre optic cores.
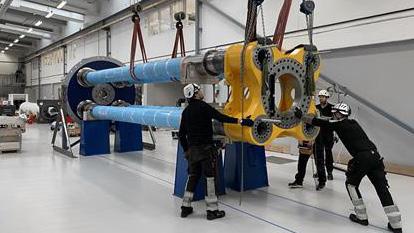
8 C4 PTO system
has been tested for a year
River Thames to be fully restored over three years
Britain’s River Thames is to be naturally restored in ongoing works that will include major engineering.
Wet civil engineering firm Land & Water has secured a contract for works along the entire length of the River Thames, which is the second longest river in the country at 215 miles.
The Thames Water River Restoration Project aims to improve fish passage, habitats and resilience in the river from its source in the Cotswolds, western England, to where it empties into the North Sea at the Thames Estuary.
Work will include weir removal or modification, channel bed re-profiling, riverbank re-profiling and replacement with softer, natural options.
“Barriers to fish passage will also be overcome, with pass channels and other solutions such as rock ramps and in-channel gravel to allow fish to lay their eggs,” says divisional business manager Fiona Moore. ”As custodians of the environment, it also ensures that we are safeguarding habitat for the flora and fauna for years to come.”
The project is being run by Thames Water, the UK’s largest water and waste water service provider, with a 15 million customer base.
Clodagh Pickavance, media relations manager for Thames Water, said a project to restore seven river stretches and four fish passages would run until March 2025, when further similar projects would be drawn up.
Land & Water is one of the first companies to be awarded a contract.
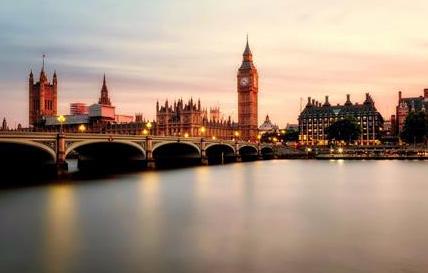
8 River Thames