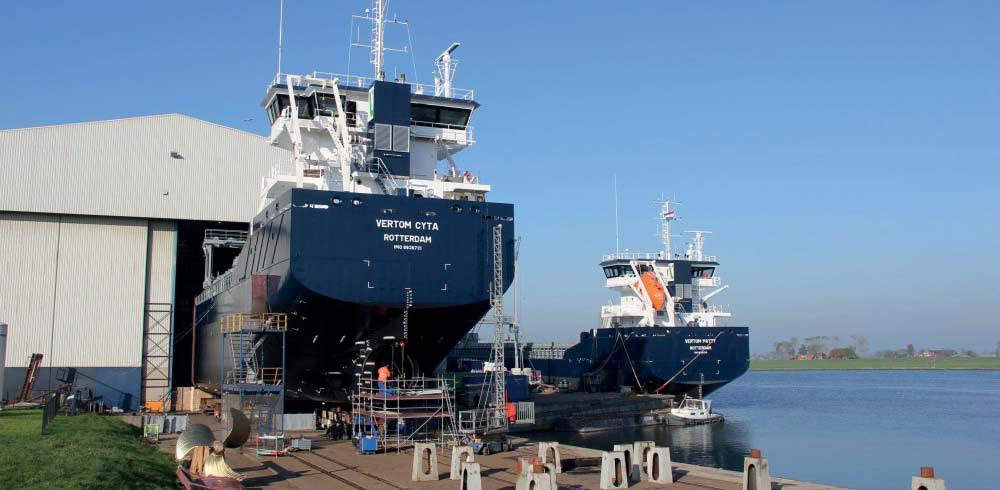
4 minute read
RESILIENT DUTCH BUILD BUSINESS PLATFORM
Although the much-vaunted scheme to realise at least 30 domestically-produced, zero-emission ships by 2030 under the Maritime Master Plan has yet to be endorsed by government, Dutch shipbuilders continue to show resilience and business verve, writes
8 New breed: diesel-electric coasters for Vertom at Thecla Bodewes’ Kampen yard
While Royal IHC is the subject of a further rescue plan due to a dearth of new contracts for larger, complex vessels in its target sectors, orderbooks among many of the industry’s key players have seen some strengthening over the past 12 months. Positive influences are an expansion-minded and innovative domestic shipowning and shipmanagement community, with recourse to an extensive supply chain and network of knowledge centres, underpinned by a Dutch propensity for cost-minded, technologically-pragmatic solutions.
Exemplifying the well-proven practice of many Dutch shipbuilders to assign the bulk of newbuild steel fabrication to yards in lower-cost countries, the Polish-built hull of a roro heavy-load carrier recently arrived at Urk, on the IJsselmeer, for completion by main contractor Hartman Marine. The latest project adheres to the production pattern adopted by the Hartman group for successive stages of its in-house fleet development programme.
The 108m Southern Rock is the third in a series of four vessels of the R3 Carrier-type ordered by Hartman Seatrade. With Partner Shipyard in Szczecin, Poland, having built the bare hull and superstructure, Hartman Marine has put in hand the high added-value phase entailing the fitting of the main engine, generators, compressors, separators, pumps, ballast system, navigation and electronic devices, hatch covers and hatch crane, together with interior outfitting, at its Urk premises.
The 3,500dwt R3 Carrier design is a lengthened version of the R2 Carrier type, a derivation of the M2 Runner multipurpose/project cargo vessel class. Shared key features of the ro-ro and general cargo designs include the proportionally large extent of deck space, provision for sailing in open-top condition, dangerous goods certification, and cost competitiveness. With full-width stern ramp access, the adoption of the ro-ro mode is considered a safer, more cost- effective and less time consuming cargo working method compared to conventional lo-lo, for the target business involved.
The R3 Carrier is 13m longer than its R2 antecedent, allowing an increase in hold length of some 5m to 74m. Both ro-ro versions can accept rolling loads up to 80t per axle, and the ship’s removable tweendecks can take 5t/m2 up to a total 350t per tweendeck.
The continuity and commonality expressed in the Hartman programme yield important benefits as regards production flow and equipment purchasing. While the seminal M2 Runner series made its debut in 2012 via the 93m Oceanic, the initial ro-ro variant first came into being by way of the R2 Carrier Baltic in 2017, followed in the consecutive years by the Western Rock and Eastern Rock.
The R3 Carrier iteration assumed first form in the December 2021-delivered Celtic, and second-of-class Adriatic was commissioned last October. With outfitting of Southern Rock now in hand at Urk, fabrication of the fourth vessel, Rock Carrier, is under way in Poland before transfer to the Netherlands and scheduled handover to the operator during December 2023.
Inland from the IJsselmeer, on the lower reaches of the River IJssel, the town of Kampen has received a boost to shipbuilding activity through what has become an eight-ship series entrusted to Thecla Bodewes by the Vertom Group.
The 7,000dwt dry cargo carrier generation, designated the LABRAX-type, has been developed in association with Groot Ship Design and features diesel-electric propulsion and CFD(computational fluid dynamics) optimisation of the hull form for efficiency across the power and speed profile. The two holds are completely box-shaped, maximising loading flexibility and cargo intake.
The modular propulsion concept employed is intended to allow the vessel to be readily adapted to future carbon emission-reducing solutions. The system distributes the energy load in efficient manner by using smaller engine prime movers for optimised combustion and fuel usage. The arrangements are also designed to facilitate any future switch to methanol-electric or hydrogen-electric propulsion.
Following sea trials conducted during December 2022, class leader Vertom Patty has been phased into trade, while the second ship in the series, Vertom Cyta, was side-launched at Kampen on February 23 this year with a view to April commissioning. Six more sisters are on order, Thecla Bodewes having been awarded the seventh and eighth units a couple of weeks before Vertom Cyta went down the ways, such that the production programme extends into the latter stages of 2025.
Vertom has also joined forces with Groot Ship Design in a project entailing a series of smaller vessels, of 5,600dwt, based on the same platform as the 7,000dwt type. A construction contract calling for six newbuilds to the 99m, diesel-electric design has been placed with Chowgule & Company in Goa, India.
Each of the 5,600dwt multi-purpose cargo ships has been specified with four main generators of approximately 400kW apiece, feeding two 650kW propulsion motors and a 400kW bow thruster. At ‘economical’ speed settings, achieving around 10 knots at design draught, operation will be on three generators.
The company has gone ahead with further investments in wind-assisted propulsion systems by specifying VentoFoil retrofit installations for two of its existing short-sea cargo vessel fleet, the 2009-built, 118m sisters Progress and Perfect.
VentoFoil is the latest version of the VentiFoil solution, and is a wing-shaped element harnessing innovation in aerodynamics to create a high propelling force relative to its size. Vertom had been studying the wind-assist technology in more detail since signing a contract for two VentiFoil units to be retrofitted to the 2008-built, 90m cargo ship Anna in June last year.
Conoship International’s current work on new designs for the short-sea sector shows a predilection towards dieselelectric main power. Electric motors favour the use of a larger-diameter propeller in combination with an optimised aftship form, as encapsulated by the ConoDuctTail arrangement. This allows for very high propulsive efficiency and comparatively modest power in the electric propulsion motors. The large, fixed-pitch propeller is capable of handling wide torque fluctuations.
Drawing on extensive market research, Conoship has formulated a new CIP series of diesel-electric general cargo vessels suited to operations into small ports and river terminals throughout north and west Europe. Contracts were awarded to Holland Shipyards at the end of December last, spanning a total of five singledeckers. Two 88m cargo vessels will be built for De Bock Maritiem of Alkmaar in accordance with Conoship’s CIP 3600 blueprints, while three examples of the CIP 3800-designated 89.4m version have been ordered by Hartel Shipping & Chartering.
In all cases, the frequency-controlled diesel-electric power train, based on a pair of 374kW electro motors, will regulate the speed of the screw according to variables such as load factor, water level and navigation route. Fuel savings as great as 30-35% are anticipated.
The three diesel generators are to be sited on the upper deck, facilitating access for future adaptation of the prime movers for alternative fuels and the requisite fuel storage. The electric propulsion train would remain unchanged in such a conversion. Moreover, the CIP series has been prepared to facilitate the adoption, either at the newbuild