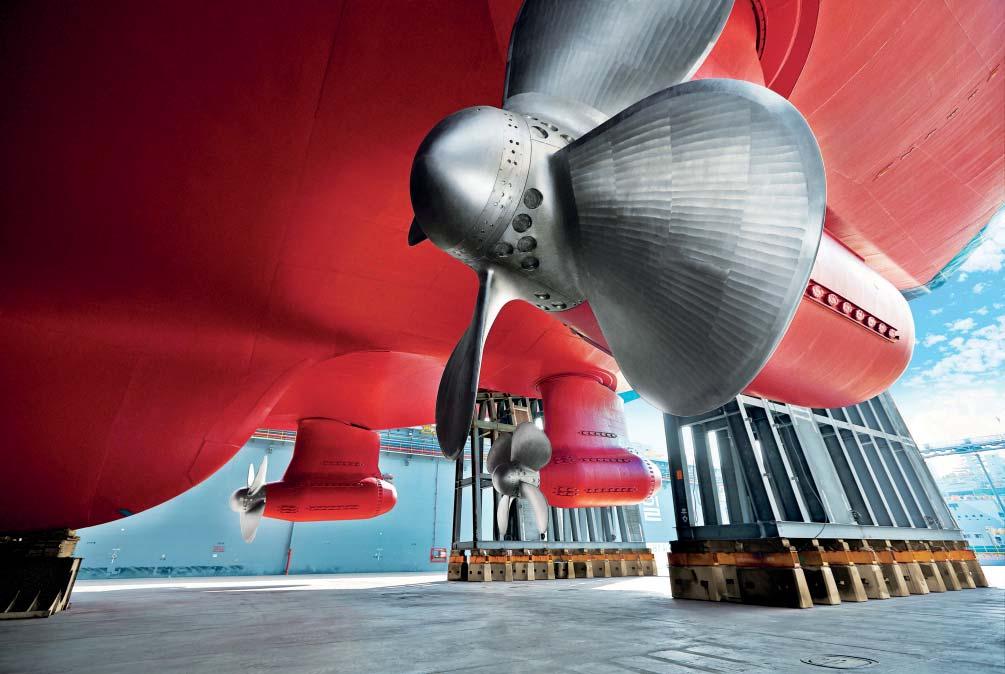
8 minute read
PODS AND PROPULSORS: THE PRIME MOVERS OF TOMORROW
In many ways, it is a surprise that shipping’s “bigger is better” philosophy did not start to feel the strain sooner. But the pandemic certainly brought forward the schedule, with the few vessels then-deployed on the spot market suddenly raking in cartoonish earnings. In one example, X-Press Mekong, a 2,743 TEU Singaporean feeder built in 2020, fixed a charter of 55 days at $175,000 per day
If one was lucky enough to get in early, a secondhand ship purchase would be earning profit within weeks. But what was impossible to ignore about this handful of vessels was just how old they were. According to Alphaliner data, the average container vessel in the up-to-999 TEU size range is over the hill at 17.4 years old. Unlike X-Press Mekong, most small vessels are not even designed to be feeders, particularly: rather, they are the flagships of yesteryear, from a time when 4,000TEU was still ‘big’.
In an article, the UN council on trade and development (UNCTAD) warned that Europe is facing “a chronic shortage of vessels in short sea shipping.”
“Can we then expect new capacity to come on-line over the next two to three years? Not so soon. Shipping supply can only be increased with a lag: it takes about two years to build a vessel,” the report read.
The maritime industry is already starved for small vessels, then. But other post-pandemic trends are likely to compound the situation. Many manufacturers and retailers are seeking to spread their supply chains across several countries in order to prevent the risk of another covid-like situation bringing their sales to a halt. This will mean that shipping will have to change, as well – from a situation where China’s onestop-shop enables economies of scale, and produces many of the arguments for 20,000 TEU giants, to a fragmented one where many countries feed into the whole.
The smaller the required vessels become, the worse the economics of the traditional prime-mover and propeller combo become, and the more attractive battery-electric propulsion begins to look. Feeders are bad performers under the IMO’s new CII measure, as they spend a lot of time in port, and sail at higher average speeds. The case is being made by several new small vessel designs including Yara Birkeland, Japan’s Project e5, and an as-yet unnamed DB Schenker feeder ship.
Converging with this is an explosion in another sector, offshore wind, now finally reaching US shores. As well as wind-turbine installation vessels (WTIVs) a generation of new service and operation vessels (SOVs) will be needed to support this segment, not only at the building stage, but also over the course of maintaining the turbines. With their extraordinary requirement for manoeuvrability coupled with the growing possibility of being charged by turbine power at sea, these vessels will create additional demand for electric propulsion.
An ABB installation aboard double-acting ferry P&O Pioneer, and its upcoming sister vessel P&O Liberte, point the way for how this will come about. Making its way from Guangzhou Shipyard, China (passing Greece at time of writing), the vessel is fitted with four ABB Azipod thrusters. These are powered in part by an 8.8MWH battery pack supplied by XALT Energy.
Although the ferry is ultimately fossil-fuelled, using four Wärtsilä diesel engines, the addition of a battery performing load-levelling duties allows the vessel to boast a 40% reduction in fuel consumption compared with a conventional diesel-electric vessel, and “…the most sustainable ferries ever to sail on the English Channel,” on P&O’s social media.
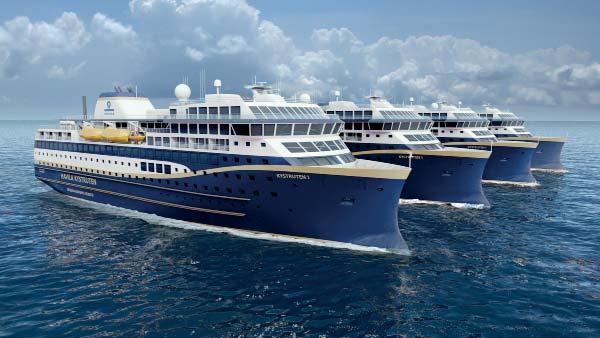
Meanwhile the ABB Azipods add to the vessel’s operational flexibility, enabling it to turn on the spot and approach the dock from any direction.
Electrified propulsion is almost completely efficient, and it is inevitable that vessel electrification will grow as more effort is made to curtail emissions. Podded propulsion therefore, still relatively recent, will likely experience a similar trajectory of improvements and optimisations as the more mature technologies such as four-stroke engines.
Wärtsilä is taking a digital approach, through its OPTI-DP programme. Using advanced computational fluid dynamics (CFD), Wärtsilä made the determination that tilting its thruster’s driveshaft and propeller downward by 8 degrees
The big push
Podded propulsion manufacturers have been squaring up to a new challenge recently – ice. Ice-class pods are markedly different in appearance from their openwater brethren, with a bulbous motor housing. The reasons for this are several, but crucially, ice-going ships must generate a massive amount of torque, as it is presumed that they must proceed against continuous resistance from ice. This is not unlike the operating condition of a tug during a towage operation.
For this reason, thruster manufacturers do not want to situate their electric motors inboard of the vessel, which would risk raw power being lost to shaft lines and gearings. Instead, the motors are situated in the water, with as direct a linkage to the propeller as possible. This has the added benefit of reducing noise, because the noisiest parts of the propulsor, the gears, are unnecessary. It also cuts down on the need for lube oils, nearly eliminates the problem of the ship’s hull geometry interfering with the thruster’s aft-flow, bringing its ‘thrust deduction factor’ down from 0.14 to 0.02.
This has informed Wärtsilä’s thruster design since. “There is minimal friction with the hull and power losses from the thruster,” said Wärtsilä product performance manager for thrusters Petra Stoltenkamp, at a conference in January. “The optimal tilt was 8 with the flow from the thruster not hindered by the vessel hull or other thrusters. We have shown that less power is needed, by optimising propulsion, reducing design costs and lead times.”
There may be many more exciting changes on the way. With electrification of ship propulsion on the rise, podded propulsion, tunnel and bow thrusters, will fit into this new paradigm in a way that the conventional combination of prime mover, driveshaft, propeller and rudder will not. For their manufacturers, there has probably never been a more exciting time to be in the business.
A permanent change
A recent trend in the design of thrusters has been concerned with reducing their footprint. Typically, a good way of minimising the environmental risks from an emission of oil to sea.
A large motor housing bats away ice chunks before they can reach the propeller; and if the propulsor takes a knock, there are no shafts to bend or be knocked out of alignment.
ABB thrusters are popular in Arctic and Ice applications, with many of the vessels operating in Russia’s Yamal peninsula, including LNG tankers Christophe de Margerie and Yakov Gakkel, fitted with ABB Azipod propulsors. The former made history in 2017, crossing the Northern Sea Route (NSR) in icy conditions without icebreaker assistance, using its ABB Azipods.
More recently, ABB Azipods have been installed on a Van Oord jack-up turbine installation vessel Boreas, under construction at Yantai CIMC Raffles shipyard in China. The installation has an enormous combined power of 16MW, providing extreme power for transportation of heavy turbine bodies, as well as acute precision when positioning pre-jack-up phase. narrowing the profile of a thruster underwater is relocating its motor and hydraulic systems inboard of the vessel, and connecting to its propellers using a driveline. This has had various benefits; it makes the thruster’s systems easier to inspect and repair by the crew. It has also led to marked improvements in thruster hydrodynamics.
“The ease of installing the Azipod system was another key factor in our decision to contract ABB; it is a matter of plugging the ready-made units into the vessel hull, saving considerable time and effort in the construction process,” explained Shiyan Sun, Director, Supply Chain Management Centre, Yantai CIMC Raffles Shipyard.
But it has not all been plain-sailing. After a protracted legal case, ABB paid out more than $150m in compensation after several Norwegian Cruise Line vessels fitted with ABB propulsors experienced failures. In one case, Norwegian Star, an ABB propulsion failure left the vessel stranded at sea, “… imperilling the safety of passengers and crew, and causing substantial harm to NCL’s reputation and business," according to an attorney representing NCL.
Modern thrusters tend to be sleeker and thinner, with fewer bulbous shapes beneath the waterline, and a better swept area for the propeller, allowing smaller propellers to provide the same propulsive power as a larger thruster with a motor situated inside the hub. Locating the motor inside the vessel’s hull also has the benefit of putting a noise barrier between it and the ocean, meaning less noise is emitted underwater – known as ‘underwater radiated noise’ (URN).
However, there are compromises. For one, increasing the inboard footprint of a thrusters means there is less space. It also increases the noise inside the vessel, and for various new vessel types including SOVs, which have large accommodation blocks for turbine engineers, this is unhelpful.
But recently, thruster manufacturers have been able to improve on these principles further, with the application of permanent magnet technologies. This has changed the design of the thruster once again. Kongsberg’s AZ-PM azimuthing propulsors seem at first glance to be fitted with Mewis Ducts, but in fact, they are ‘rim drive’ thrusters, with a stator inside the rim which manipulates a circular magnetic field. A set of permanent magnets inside the rotor causes the propeller to spin.
There are many advantages for this configuration. The thruster is the motor, requiring no motor inside the hull, saving space and reducing noise internally, and having no need for a driveshaft improves the propeller’s efficiency by 10%. This is compounded by the lack of a need for inboard hydraulics and cooling systems.
Another aspect is that by implementing rim drive thrusters, Kongsberg has stumbled upon another benefit – designed this way, the rotors have no tips. This prevents the vortices normally created at the tip of propeller blades, known as cavitation, better optimising the propeller inflow, and eliminating a major source of URN.
Kongsberg is not the only company to have developed a rim-drive thruster; Norway’s Brunvoll and Germany’s Schottel both have their own versions. But the Kongsberg design differs somewhat, featuring a prominent central hub, where the others have none.
Asked whether the hub added hydrodynamic resistance, Kongsberg Technical Product Manager Permanent Magnet Thrusters, Agatha Kalvatn explained that it was “the opposite” – the hub further improves hydrodynamics by preventing cavitation in the centre of the thruster.
In fact, this principle has only just been discovered by the MIT Lincoln Laboratory, in drones, which have recently been fitted with ‘toroidal’ figure-8 propellers with no tips. This redesign has reduced the noise output of drone propellers dramatically.
“Most of the noise in a thruster comes from the blade tip cavitation, there are no blade tips in this design,” explained Kalvatn, discussing her company’s range of permanent magnet thrusters. “This thruster was able to get a Silent E notation, because there are no gearings, and we have optimised hydrodynamics with no cavitation.”
Kongsberg has also optimised the geometry of propellers in its TT-PM tunnel thrusters, leading to a simplified design. Conventionally, Kongsberg tunnel thrusters were driveshaftdriven with inboard motors, leading to an asymmetrical layout which provided slightly more thrust in one direction than another. But with a rim drive thruster necessitating no driveshaft, Kongsberg has been able to optimise the propeller blades on its tunnel thrusters, to provide equal thrust in both directions.
The PM thrusters’ growing reference list includes Hurtigruten polar cruise vessels Roald Amundsen and Fridtjof Nansen, which each feature two TT-PM thrusters of 2m diameter, which each develop 243kN of thrust. The Havila Kystruten coastal cruiseferry quartet Capella, Castor, Polaris and Pollux are also so equipped, as well as Allseas Oceanic, a subsea vessel.
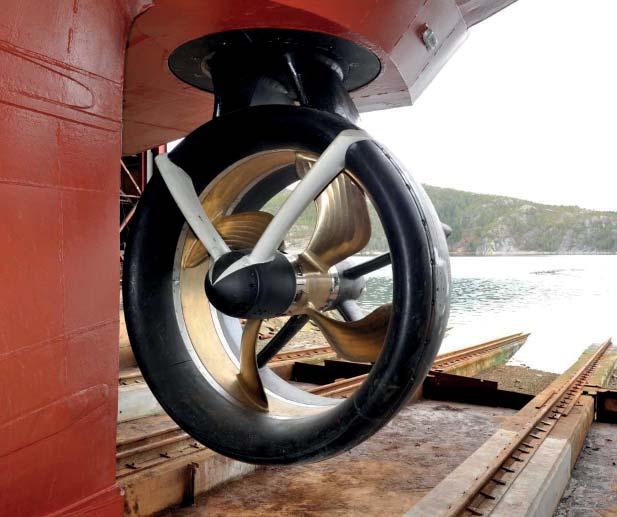

“By the end of 2024 we will have 60 units installed,” Kalvatn said. “There are rare Earth metals used, as with any permanent magnet design – future designs will consider how to reduce these in construction.”
Kongsberg has shown that it still wants to compete in the non- rim-drive segments however, with a new retractable thruster design, the ULE-PM, in January, featuring a prominent driveshaft and central hub.
JUNE 202 Southampton United Kingdom 14
The all-new 2023 Seawork Conferences will deliver bitesize in-person sessions to help commercial marine and workboat operators face the challenge of reducing operational expenditure at the same time as meeting
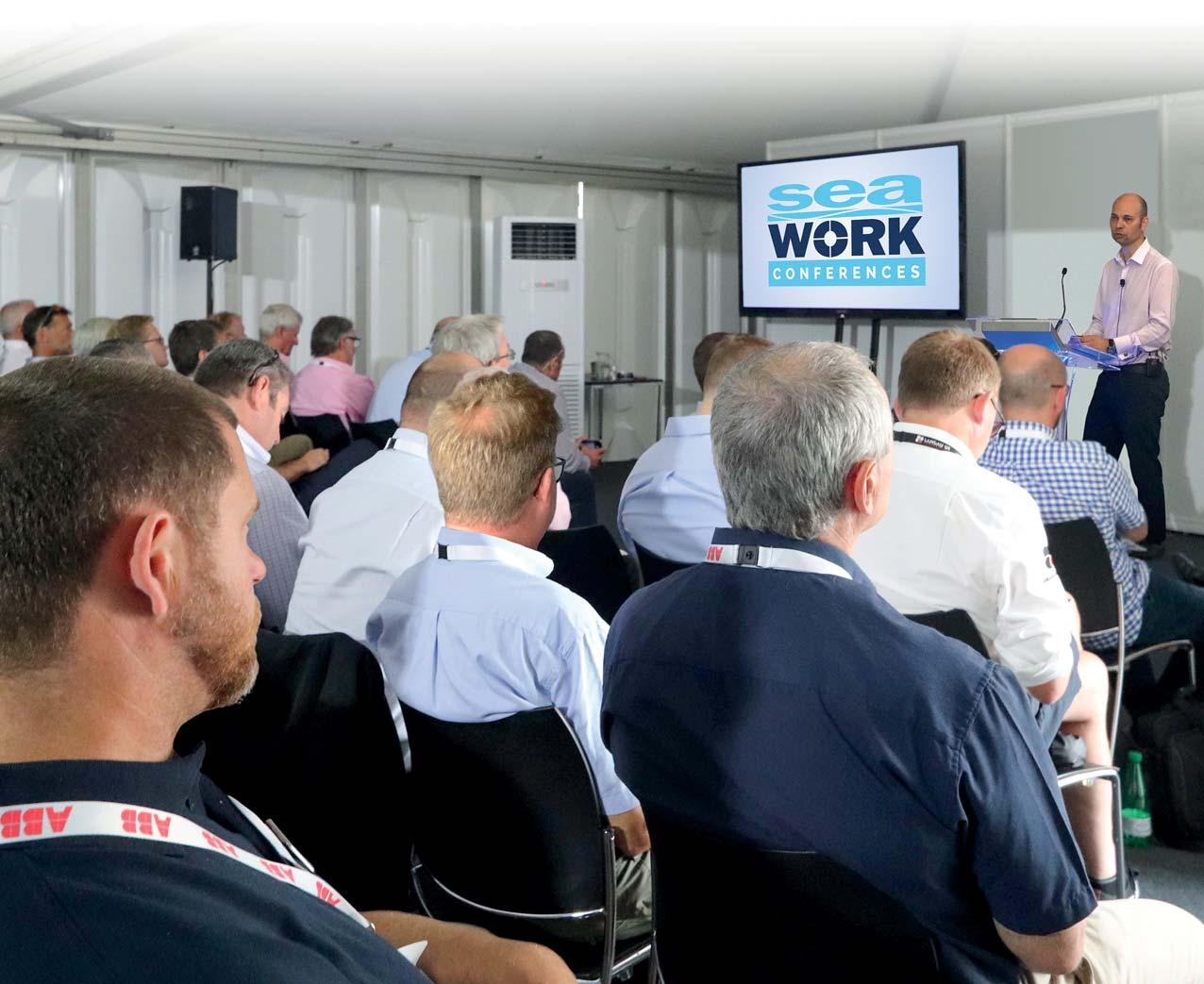
Learn how your business can create cost savings in alternative fuels, hybrid propulsion, technology, and design.
Conference Sessions
Alternative fuels – how operators can make operator costs
Vessel Design – Optimising
If you are interested in speaking, attending, or sponsoring these sessions please contact the events team on conferences@seawork.com or +44 1329 825335
Book to attend: seawork.com/our-conferences
Media partners: