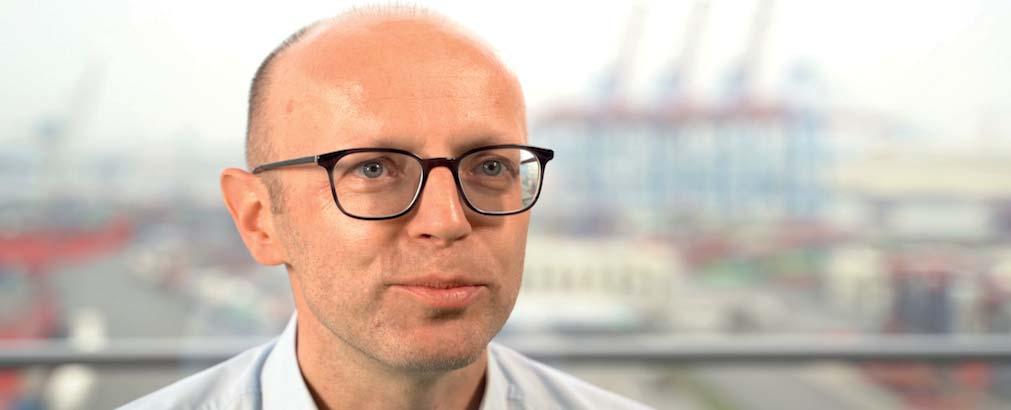
8 minute read
ELECTRIFICATION 10 YEARS ON
The shift from AC to DC grids has paved the way for increased onboard electrification, and 10 years on, the flexibility that it brings is enabling greater power optimisation
In March 2013, ABB delivered its first onboard DC grid system to the MPSV Dina Star, making it the first IMO vessel in the world powered by a modern, primary DC power system.
A DC-based power system enables simple, flexible integration of variable speed gensets and shaft generators, batteries and fuel cells, says ABB. For offshore vessels, it can bring better fault tolerance as well as the fuel saving benefits of variable speed generators and energy storage. For ferries, this enables hybrid or fully electric operation. For large cruise ships, the ability to distribute main power at 1000Vdc instead of 690 or 660Vac represents savings of up 40% or more on cabling.
The DC switchboard was a gamechanger for engine manufacturers, because it enabled variable speed operation and more optimal engine utilisation and therefor minimal fuel consumption, says Bernd Friedrich, Senior Manager and Head of Solutions Engineering at MAN.
The ability to run engines efficiently during mostly calm conditions but to also be able to increase the thrust applied to the propeller within 10 seconds for high current conditions was important for a recent MAN Energy Solutions system developed for Seaspan. For this solution, MAN together with its partner AKA configured a hybrid system with two generators, a DC switchboard, energy storage, and electric machines driving two azimuth thrusters with fixed pitch propellers. The energy storage provides the boost needed for high-current navigation much faster than the engines would have been able to, especially in gas mode on dualfuel engines.
Combinator curve
Energy storage also enables the propeller to be run closer to their combinator curve. Typically, the gap is around 20%, but with the availability of a power reserve if something unpredictable happens, this can be reduced to 10% or less. This means the propeller can typically be run at a lower RPM, maintaining hydrodynamic performance while reducing energy consumption.
Diesel mechanical systems are still best suited to the operating profile of many deepsea vessels, but MAN’s hybrid version (HyProp Eco) enables incorporation of a degree of electrification. It includes controllable pitch propeller, PTI/ PTO, electric machines and batteries, with single or dual main engines driving the shaft mechanically. “This enables a good trade off and split between the number of cylinders we install on the main engine and the auxiliaries,” says Friedrich. “Typically, we try to achieve a loading on our engines of 8590% where the engine is optimized but we still have some margin. This is strategic loading, and load fluctuations can be handled by energy storage, so we can often have one cylinder less on the main engine.”
Variable speed gensets
Torsten Büssow, Managing Director, Electrical & Power Systems Business at Wärtsilä, says a DC system makes sense in two situations: when the system has a big battery, because it will give DC electricity, or if variable speed gensets are desirable.
However, he says, DC is not needed for the incorporation of solar systems onboard. “Solar panels come with smart converters that will generate 200-500kW that can go directly to the switchboard. There's no advantage on the DC grid. Otherwise, you need to have a DC power module, and each connection to a converter drives up the costs,” says Büssow.
“A DC grid comes with electrical losses of around 5%, so it's adding a lot of cost to the whole propulsion system. You pay twice, basically, for the DC grid and for the battery. So, in many cases, it's not needed.” While a DC system will be used for the battery and for charging the battery from shore power, an AC system can still be used for the normal vessel gensets and main propulsion.
Some in the industry have indicated that the power capabilities of DC grids are limiting the uptake of hybrid solutions in large vessels, but John Olav Lindtjørn, Head of Product & Portfolio Management, Electric Solutions at ABB Marine & Ports, says there are other, more important factors. These include the cost and availability of marine grade batteries. Cost and availability are also issues for fuel cells, as is the viability of viable zero-emissions fuels.

“The upper limit depends on a number of things,” says Lindtjørn. “To start – the main factor is will often be limited by a combination of maximum power of individual power sources or loads. Today, this is around the 6MW mark for sources and 8MW for loads. If a system design stays within these parameters, the next limit would be the point at which power distribution becomes impractical using low voltage (690Vac or 1000Vdc). This depends on the application. If the main source of power is low voltage (e.g. batteries or fuel cells) and there is little need to distribute power over long distances, there would be a strong motivation to stay with a low voltage DC system. In such cases systems could approach (and possibly exceed) 30MW installed power. On the other hand, if the main source comes from internal combustion engines, it may be tempting to go for a medium voltage AC solution sooner.”
Time as a parameter
Unlike a direct engine-driven ship where typically power sources are separately dedicated either to mechanical propulsion or to electrical auxiliary power, in GE Power Conversion’s Ship’s Electric Grid any prime mover can feed any load or consumer on the vessel. This unlocks higher levels of flexibility, resilience and efficiency, particularly coupled with the growth in vessel power demands for complex operational systems that have transitioned to needing electrical rather than mechanical or hydraulic power.
The Ship’s Electric Grid inherent scalability means electric architectures and propulsion are just as suited to smaller and lower voltage vessel fleets as to the biggest, higher voltage ships. One of the biggest advantages is in ‘right-sizing’ the power system which comes from this ability to share power around the vessel. The vessel’s power system is more likely to be able to be configured without over-sizing one element (for example, propulsion or auxiliary power), helping to mitigate the occurrence of black-outs but also to reduce contingency or oversized power sources, which are often under-utilized on traditional mechanical drive ships.
The size of battery installations is a potentially limiting factor for electrification that is giving way to new technology.
Leclanché has been selected as the battery technology provider for two hybrid vessels being built for Stena Line and Brittany Ferries. Each battery system has a capacity of 11.3 MWh, so the RoPax ferries will be the world’s largest hybrid vessels.
Current limitations
GE Power Conversion’s Nick Smith says: “More customers are asking us how they can help to future-proof their ships for higher energy needs. Energy-efficient architectures, like GE’s SeaPulse™ Advanced AC and DC architectures, help to optimize the ship’s power network, providing the right levels of power and power quality across propulsion, on-board services and operations.”
Power network flexibility and configurability are also enhanced by the Ship’s Electric Grid incorporating increasingly intelligent and digitalized automation, control and energy management systems. “Electric ships function as microgrids, but they historically have functioned as power, not energy networks,” says Smith. “Ships’ power management and energy storage systems are adding ‘time’ as a parameter to become holistic energy management systems. It means we can shift to a more efficient and more automated way of getting power in the right place at the right time.”
Yaskawa Environmental Energy/The Switch has developed a battery short circuit prevention device that boosts the safety of large battery installations and expands the scope of onboard electrification possible. “The flip side of using very large batteries is the need for much greater protection for the rest of the power distribution system. Without fast, reliable protection, a sudden release of energy can result in major damage or, in the worst case, an electrical fire,” says Asbjørn Halsebakke, Manager Technical Solutions Marine Business.
The company’s Battery Short-circuit Current Limiter (BSCL) and the closely related Electric Current Limiter (ECL) enables energy storage systems in excess of 1 MWh, minimises the number of parallel systems required and thus reduces installation size. “In principle, implementing a BSCL means you only need two DC-Hubs for an ESS of up to 40 MWh,” says Halsebakke.
The standalone device is placed close to the batteries and between drives. The ECL supports the further development and use of DC power distribution. It maintains the integrity of
The Switch DC-Hub in any situation by disconnecting a critical fault in microseconds. Thus, DC loads can be safely connected to a DC-Hub.
Donato Agostinelli, Sales Manager at Steerprop, cites a progression in electrification that will eventually result in the complete overhaul of the engine and propulsion rooms. Long shaft lines have been replaced initially by dieselelectric propulsion systems and that is paving the way for fully battery and fuel cell powered systems. “This has enabled more efficient thruster systems by going from Z-Drive with two reduction gears, to L-Drive where only one reduction is needed and mechanical efficiency is further improved.”
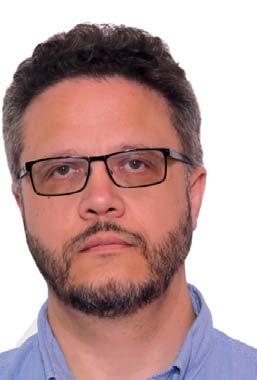
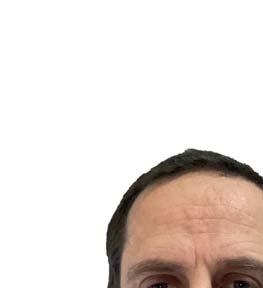
Alt fuel benefits
He says the benefit can be huge, with over 25% energy savings under 50% MCR, and it also provides energy efficiency for the most demanding operations. “In today's electric vessels, this means savings on the needed battery capacity requirements, for example, and less fuel consumption. When talking of future fuels with generators and fuel cells running with methanol, hydrogen, ammonia, etc., this also plays an important part, since the storage requirements will be three to 10 times higher than the storage volume requirements of today's vessels.”
A series of battery/new fuel combination vessels is already being developed by Damen Shipyards in cooperation with offshore personnel transfer company Windcat and CMB.
TECH. The power requirements of the “Elevation Series” hydrogen-powered Commissioning Service Operation Vessels (CSOVs) are driven by DP2 rules and notations and therefore need to account for worst case failures such as loss of an engine, switch board or propulsion unit, without impact on the vessel duty – in this case the use of the gangway to transfer technicians to an offshore structure.
Windcat says the power system design is that of a diesel electric vessel, hence no gearboxes. Subject to final configuration it will have approximately 5.6MW of installed main engine power, coming from three medium speed engines. Given the DP2 design, the engines are supported by a c800kW battery that acts as a peak shaving / spinning reserve alternative. This reduces fuel burn by removing the need to have an additional engine spinning without load in case of a worst-case failure. Similarly, when slightly more power is required than the loaded engines, the battery can be used. Finally, the battery can be used to support shore power needs and or offshore hotel load if for example
Onboard wind power is likely to have signi cant impact on power system designs. The EU’s CHEK project is anticipating that ships can achieve power savings of around 20% by combining wind assist technology with weather routing. In general, the savings can be considerable, varying between 10-30%, depending on the typical routes, operational speeds and weather profile. Savings of this magnitude could result in lower engine power requirements on newbuildings, says Mia Elg, R&D Manager at Deltamarin. “Today it’s typical that cargo ships operate at lower speeds than design so we see often engine loads of 50-70%. When adding the considerable energy savings possible with wind and voyage optimization, the engine loads get even smaller.”
DC system evolution
This will change ship design significantly. “It of course takes some courage to design new systems and specify things in a new way, but for instance the methodology that we have presented in the CHEK project, including simulations run in several “generations” including verifying the results always when possible, gives us the confidence to go forward.”
Meanwhile, ABB Marine & Ports continues to push the limits of its Onboard DC Grid™, also increasing its high-power capabilities, by expanding capabilities of the existing system, enabling better integration with medium voltage AC solutions and increasing the DC voltages.
Matti Lehti, Global Product Manager at ABB Marine & Ports, says the next big development in onboard power systems may be within higher-powered DC systems with a combination of medium and low DC voltages in the same system. He sees three key enablers: high-frequency, galvanically isolated DC/DC converters (DC voltage transformers) allowing the coupling of different DC voltage levels from low voltage to high voltage and simpler integration of large batteries and fuel cells into higher DC bus-voltages. Additionally, new medium voltage converter types that support larger medium voltage DC switchboards as well as medium voltage DC protection devices.