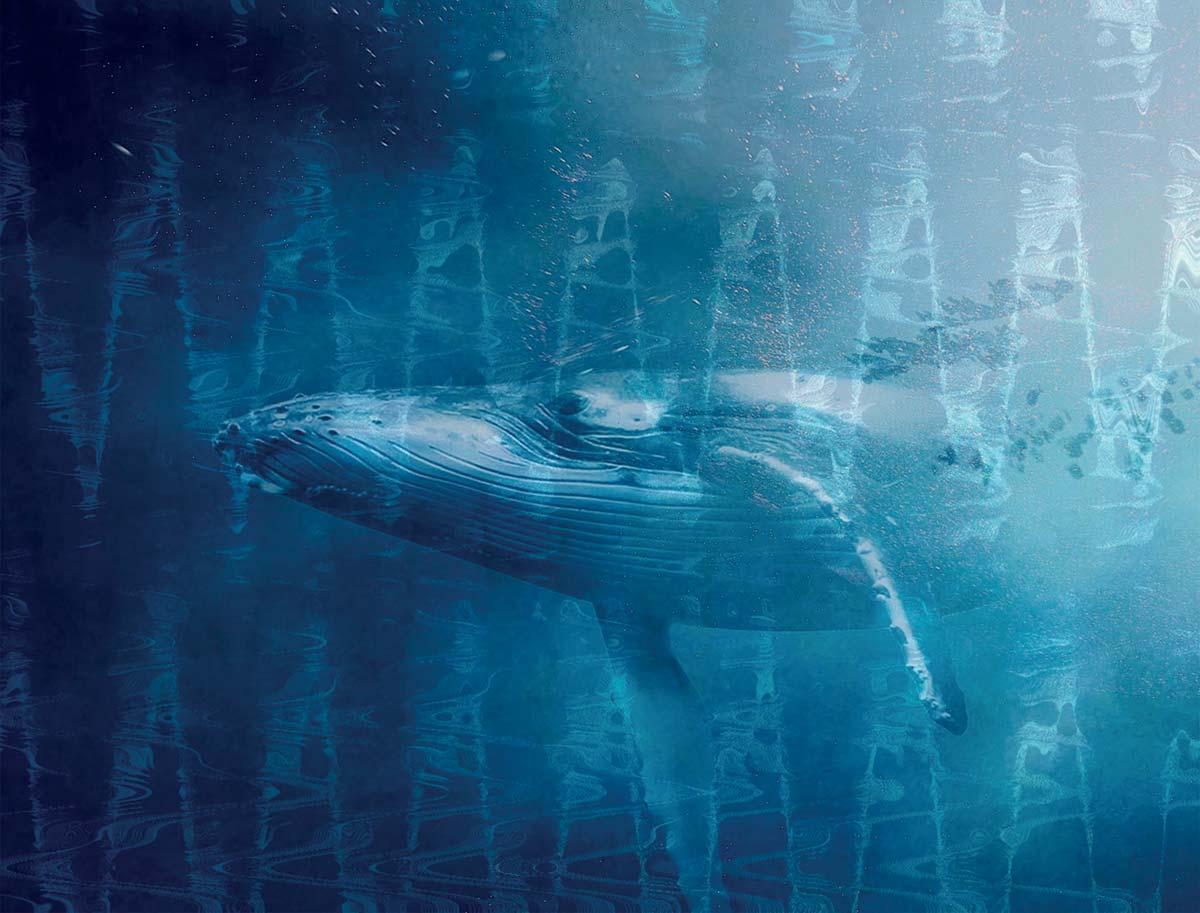
5 minute read
MEPC 80 TO CONSIDER DRAFT URN GUIDELINES UPDATE
The next meeting of the IMO’s Marine Environment Protection Committee (MEPC 80) will consider draft revised guidelines covering the reduction of underwater radiated noise (URN) agreed by the IMO Sub-Committee on Ship Design and Construction (SDC 9) in late January
8 Draft revised guidelines relating to the reduction of underwater noise from commercial shipping will be considered at MEPC 80 in June 2023
The review aims to make new recommendations based on the latest developments in ship design and technology and to address any barriers that could prevent the wider take up of noise reduction measures. This includes potential solutions relating to the retrofit of existing propeller and shaft technology that could contribute to a more peaceful marine environment.
Initial findings from research carried out by Thordon Bearings indicates a seawater-lubricated propeller shaft could have an important role to play in reducing propeller noise given it is significantly quieter than one lubricated by oil.
While comparative studies have yet to be completed, the Canadian polymer bearings specialist says the low URN of a ship operating seawater-lubricated propeller shaft bearings is, more than any other aspect, the primary reason why the arrangement is favoured by naval forces and the fisheries sector.
“For fishing vessels, we are told: ‘seawater-lubricated propeller shafts don’t scare the fish away’. And for naval ships, a low signature means they can avoid a submarine’s passive sonar system,” says Tony Hamilton, Technical Director,
Thordon Bearings. “But we are now seeing more sectors –cruise, expedition, and research ships, for example – adopt a seawater-lubricated arrangement for noise abatement reasons alone.”
Hamilton furthers that noise emissions should be considered as serious as marine exhaust gas emissions or any other source of ship-to-air and ship-to-sea pollution; but there is currently no legislation in place to prevent or reduce this source of environmental damage.
“Research shows the increase in ships and ship traffic globally is resulting in a steady rise in ambient noise across the frequency spectrum but current guidelines on URN are simply that: guidelines. More meaningful mandatory measures are required if the wider commercial maritime industry is serious about having a zero environmental impact or achieving UN Sustainable Development Goal #14, protecting life below water,” he says.
Typically, a rotating propeller and the vortex cavitation phenomena it creates can generate more than 180dB of underwater radiated noise – a din louder than a jet engine –and can be heard by marine fauna up to a hundred miles away.
Indeed, research carried out last year by the University of Victoria, one of Canada’s leading research academies, found that the noise from increased ship traffic in the Arctic is resulting in “ship-avoidance reactions by beluga whales at extremely far distances – much farther than the whales could be seen from a ship.”
The propeller is responsible for about 85% of a ship’s URN, with anything above 155db an existential threat to marine life, including whales, seals, porpoises, and dolphins, as it severely impairs their ability to navigate, communicate, source food, find a mate, avoid danger, and survive. Anthropogenic ocean noise negatively affects ecosystems, impacts biodiversity, and can alter the aquatic food chain.
“Unlike ships operating a metal bearing, an elastomeric polymer bearing is a noise dampener,” says naval architect Jeff Butt, Thordon’s Business Development Manager, Navy and Coast Guard. “There is a significant amount of empirical data and testimony indicating its noise abatement capability.”
Butt says that while the navies of the world will not release data specific to their vessels’ acoustics for obvious reasons, “we are told we win naval contracts because our COMPAC material exceeds the noise signature requirement. We have customers stating the material is substantially less noisy, and fishing vessel operators cite much larger catches after they have converted to a Thordon bearing.”
While it is completely logical that a seawater-lubricated polymer bearing is less noisy than the metal variety, the Thordon material is also reportedly quieter than rubber bearings and staves.
Gary Ren, Thordon’s Chief Research Engineer, says a common problem with conventional rubber bearings is the squeaking and squealing that can occur when trawling at low speeds.
“This high-pitched noise will reverberate for miles under water. But the friction associated with conventional bearings is removed with our system, meaning shafts turn more easily. Noise is absorbed by the bearing in the 20 to 200rpm range,” he says.
Propeller noise and cavitation on a seawater lubricated propeller shaft could apparently be reduced even further by “degasifying” the water around the screw, by injecting water filtered through a 5μm membrane around the propeller blades.
According to the authors of the paper Prevention of Cavitation in Propellers, published in in 2020 by Firenze University Press, “this boundary layer at least partially increases the negative pressure required to initiate cavitation at the surface, reducing the occurrence of cavitation during the relative movement”.
During trials on a test rig in Australia, measurements pointed to 10db noise reduction after releasing the degassed water behind the propeller.
There is also the Prairie Air System, which some navies have been using to reduce propeller cavitation and, to a lesser extent, hull noise, for years. This method involves channelling air along the leading edge of the blade.
Similar systems are being developed for commercial ships. And in 2019, for instance, Kongsberg Maritime announced it had adapted its Blade Air Emission system for commercial use. The company said the system, applicable to conventional fixed pitched and controllable pitched propellers, “minimises substantially underwater radiated noise” and, is “a real game-changer” in propeller design.
Similarly, the PressurePores concept unveiled this year by the University of Strathclyde and a UK-based start-up reduces propeller tip vortex cavitation by applying a small number of strategically placed holes in the propeller blades.
Meanwhile, researchers at the University of British Columbia, Canada, are studying how fluid injections could help control propeller movement and if the introduction of wavy, serrated blade edges can “break up” the water flow patterns that result in cavitation noise.
Dr. Rajeev Jaiman, an associate professor at the University’s Department of Mechanical Engineering, and his team are also developing an AI-based solution capable of analysing the fluid interactions and dynamics behind the noise. The intention is to develop software to aid the design and manufacture of quieter propellers.
The researchers are working closely with Seaspan Shipyards, Robert Allan Limited, and Vard Marine in the fiveyear project that has funding support from Natural Sciences and Engineering Research Council of Canada (NSERC).
“The good news for us, as researchers,” says Jelovica, “is that the marine industry is receptive to these innovations. It recognises the need to change and to become more sustainable and environmentally friendly.”
Draft URN guidelines agreed
Shortly before going to press, the International Maritime Organization announced that draft revised guidelines related to the reduction of URN from the shipping industry had been agreed by the IMO Sub-Committee on Ship Design and Construction (SDC 9), which met in late January 2023.
The draft guidelines revise the previous guidelines (issued in 2014), and include updated technical knowledge, including reference to international measurement standards, recommendations and classification society rules. They also provide sample templates to assist shipowners with the development of an underwater radiated noise management plan.
The guidelines assess the different approaches that are available to designers, shipbuilders and ship operators to reduce the underwater radiated noise of a vessel. They are intended to assist relevant stakeholders in establishing mechanisms and programmes through which noise reduction efforts can be realised.
The draft guidelines will now be submitted to the Marine Environment Protection Committee (MEPC 80), which meets from 3-7 July 2023, for approval.
The draft guidelines were developed by a correspondence group with further work completed by a working group which met during the Sub-Committee session.
Experts in marine engineering equipment
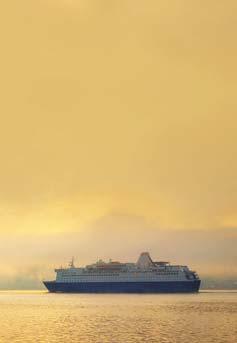
•Bilge water monitors & filtration
•Seals and bearings
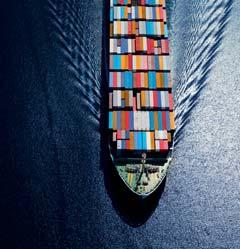
•Dry dock services atzmartec.com
Maintaining the highest possible standards for our customers. Service, upgrades and retrofits.
● Governors / Actuators
● Support for all Viking based products and our new simple to install Viking352G upgrade pack (below)
● Spare parts & Service
● OEM quality overhauls and service exchange units
● Propulsion Controls
● Generator Controls
● Power Management
● Turbocharger Condition Monitoring systems

