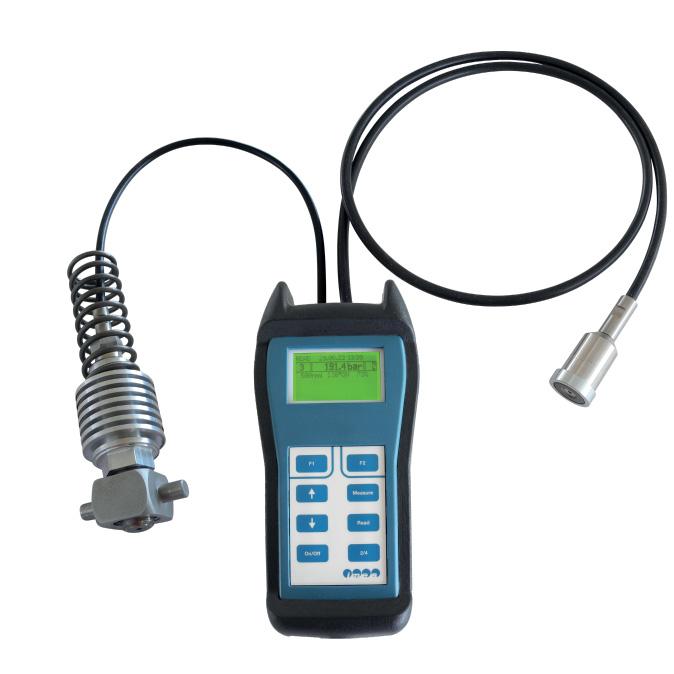
14 minute read
New EPM
EPM NEXT GENERATION
The German IMES GmbH, specialist in fi eld of cylinder pressure sensors and engine monitoring systems, will present the new generation of its successful electronic handheld devices type EPM on its booth A2 235 at SMM in Hamburg
Since 2008 the electronic indicator EPM-XP is in series production and up to now IMES off ers four diff erent EPM types: EPM-Peak, EPM-XP, EPM-XPplus and EPM-XPplus-vibro.
All EPM devices are battery powered, compact and lightweight handheld devices for 2- and 4-stroke diesel engines. They convince with their ease of use, robustness, and high accuracy. There is no need of factory calibration, neither after several years of operation.
More than 5,000 units have been sold up to now.
The measurements the user can perform are depending on the EPM type he is using. The digital peak pressure indicator EPM-Peak is designed to measure the maximum value of cylinder pressure while the engine analyser EPMXPplus-vibro enables advanced combustion pressure measurements including vibro-acoustic diagnostic on 2- and 4-stroke diesel engines.
The further development EPM Next Generation offers one common hardware for all EMP types, this enables a simple upgrade from peak pressure indicator EPM-Peak up to engine analyser EPM-XPplus-vibro. The user can download a higher version from the Internet and it is not necessary to send the device back to IMES.
The collected data of all EPM types can be displayed and evaluated from the EPM visualization software. Via USB port the device will be connected to a PC and the visualization software identifies the EPM type and activates the corresponding software functions. Depending on the instrument peak pressure, pressure- and combustion behavior, performance data as well as valve timing will be evaluated and analyzed. If the PC is connected to the internet it will be automatically checked if there are any hardware or visualization software updates. The user can install the updates and they are free of charge.
Furthermore, the optimized handheld devices of the EPM Next Generation offer 2 additional function keys for an easier handling and a larger and more comprehensive display.
All devices of EPM family are equipped with the very robust cylinder pressure sensor HTT-06 that offers a very good thermodynamic performance and they all have a battery capacity of more than 20 working hours.
Compact contender in high-speed stakes
8 IMES will present
the next generation of its EPM electronic handheld device at its booth at SMM in Hamburg in September
French high-speed engine maker Moteurs Baudouin has unveiled an especially compact new model targeted at small vessel and workboat propulsion applications, writes David Tinsley
The new engines was introduced at the Euromaritime Exhibition in Marseilles in June. Yhe 6F21 diesel covers a power band up to 735kW at 2,300rpm crankshaft speed and is characterised by a claimed ‘best in class’ power density.
As the latest outcome of the steady investment in Baudouin since its acquisition by the Weichai Group of China 13 years ago, the 127mm-bore addition to the portfolio incorporates a two-stage turbocharger system, two intercoolers and high-pressure common-rail fuel injection, operating at 2,200bar.
The engine structure is strengthened to withstand high torque and a cylinder pressure in excess of 200bar, although this has been achieved through the use of light materials, so as to keep overall weight down. Cast iron and steel have been employed only where stress and temperature criteria so demand. The flywheel housing, oil sump, covers, brackets, supports, and heat exchanger bodies have all been constructed from light alloys.
Conceived for the broad market spread encompassed by high-speed diesel power, the 6F21 is offered at three duty ratings, common to which is the 2,300rpm maximum rotational speed. Thus, the P3 intermittent duty model for pilot boats, small passenger vessels and workcraft, delivers 599kW, and the P4 light duty engine for military and fast rescue vessels, survey ships and other vessels turns out 662kW, while the P5 high-performance version, for the leisure market, yields 735kW.
With main dimensions of 1,470 x 1,100 x 1,075mm main dimensions, making for what Baudouin describes as “the most compact marine engine in our history”, the six-cylinder in-line 6F21 is suited to the smallest of machinery rooms.
Ease of maintenance has been an important tenet of the design project, as expressed in the adoption of individual cylinder heads, ease of access to key components without necessitating engine dismantling, and front mounting of fuel filters.
Weichai has ploughed more than EUR100m(US$105m) into Baudouin since taking over the 1918-founded company in 2009.
WHY SHIPS’ ‘REAL’ CARBON FOOTPRINT IS KEY TO INVESTMENT
Shipowners and operators should be well into planning ahead for the EEXI and CII regulations coming in from 2023, and what improvements they should make so their ships comply. The best future-proof path forward is to base investment decisions on analysis of a ship’s actual carbon footprint, says research manager Mia Elg of ship designer Deltamarin
Energy-effi ciency rules under EEXI and CII are being extended to cover practically all tonnage, old and new. Given that we will potentially move towards even tighter emission targets even faster than expected, I recommend that owners and operators fi rst perform a preliminary analysis of the status of their existing fl eet to give a basic understanding of the compliance challenge, then ensure their ships pass the EEXI requirements. Many will have already done this simply as a ticket to operate.
The first, and in my experience, most popular, option is to implement engine power limitation (EPL). Main engine EPL is fully possible for many typical bulkers and tankers because it seems the typical operative load is rather low, between 50% and 70%, mainly due to higher design speeds versus typical operating speeds today.
Saving energy
If EPL isn’t an option, you can move on to assessing technologies that improve engine and propulsion performance, and energy-saving devices (ESDs). Various individual ESDs can reduce EEXI value marginally, typically 2% to 5%. These include shaft generators, devices for improving hydrodynamic performance and waste-heat recovery. One interesting alternative that may alone reduce EEXI values considerably is wind-assisted propulsion; our research shows that even moderate wind-assisted propulsion combined with several other technologies could reduce EEXI values by 10%-15%.
Carbon capture is an additional measure in the future to reduce a ship’s footprint. Depending on a potential carbon tax introduced for fuels, we estimate a realistic payback time for carbon capture, with an emission reduction rate of between 25%-40%, of less than five years. However, we don’t yet know how it will be considered in the EEXI calculation or CII reporting.
For all ships it’s important to be aware that good performance in EEXI doesn’t guarantee an acceptable result in CII. In addition, EEXI is a ‘one-time’ check, whereas CII is the required level of ship ‘carbon performance’ that will be assessed continually.
Simple equation
Calculating CII rating is straightforward. All you need is the annual fuel consumption (converted to carbon emissions with a fuel-specific carbon factor), the distance the ship has travelled and its capacity. Any ship landing in the D band for three consecutive years or getting an E rating in a single year will need an improvement action plan.
I suggest optimization investment should focus more towards CII, but still keeping in mind the vessel’s ‘real’ carbon/environmental footprint. This is because the relationship between EEXI versus CII versus actual energy efficiency is not always linear. The rules are constantly developing and will be corrected towards real environmental impact in any case.
Energy modelling
What mix of improvements are optimal requires ‘energy modelling’ simulating the operational profile of the vessel and the different machinery and available fuel options. Our research shows energy modelling and related analysis can have a massive impact on CII performance and power consumption per mode.
Any energy-saving method applied on a typical cargo ship will bring similar savings in the CII context. This is not always the case with a typical passenger ship because the calculation punishes ships with large hotel load and that spend considerable time in port (although shore power is a good method to improve CII performance).
Since there is no guarantee that the CII correction factors under discussion, still after MEPC 78 on 6-10 June, will be introduced in final IMO rules, I recommend focusing on the ship’s actual carbon footprint as the basis for investment decisions as the most future-proof way forward. In addition, while the regulation involves no hard punishment and owners will have several years to improve scores, the real drivers for good CII performance will likely be commercial ratings where being a low performer will not be good PR, and high fuel prices where energy savings are good for business.
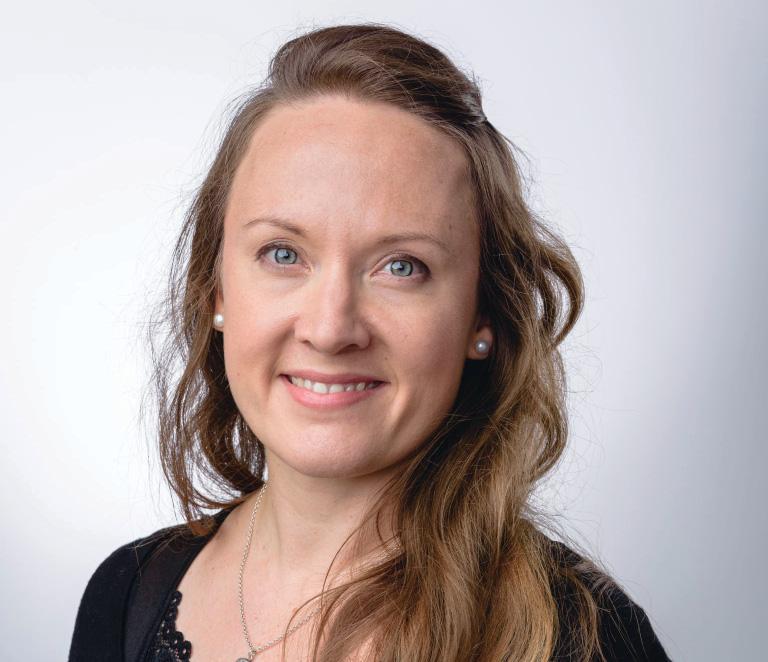
8 Mia Elg of
ship designer Deltamarin
CONSIDERATIONS WHEN SELECTING COMPRESSORS
Paul Clark, CTS Sales and Marketing of Atlas Copco Compressors provides a guide to marine compressors.
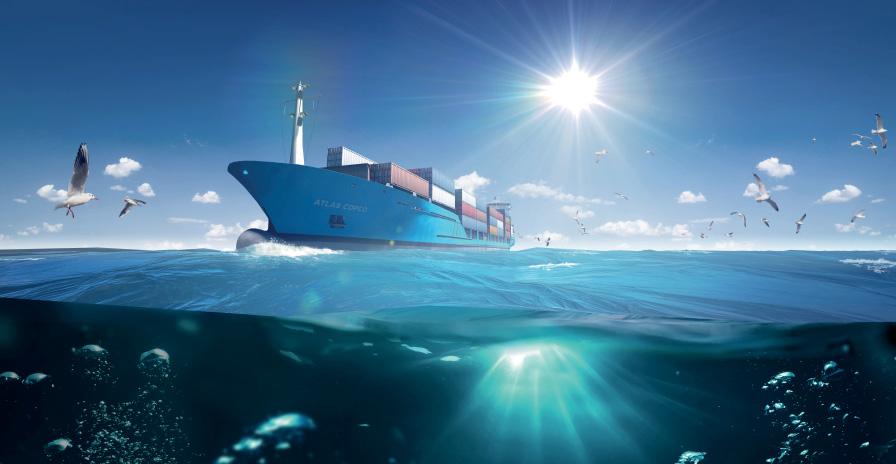
Marine compressor systems are vital elements that must be specifi cally designed for multiple duties as an integral part of shipboard operations. Whether they are located in the engine room or on deck, they have to be robust and reliable to withstand the environmental conditions experienced while operating in mid-ocean, often days or weeks away from landfall and servicing facilities.
As marine compressor solutions become ever more sophisticated, it is a wise precaution for ship owners and shipyards making equipment choices to examine the application roles, the equipment options, and the regulatory framework specific to maritime operations.
The starting point for these considerations has to be the principal duties of shipboard compressors.
Principal compressor duties
The first and foremost duty for the compressor is providing starting air for the main engines, normally at a pressure of 30 bar, followed by the supply of starting air for diesel generating sets. The latter can be at 10 or 30 bar pressure depending on the starting air method, either direct in the cylinder or by a starting air motor.
High quality, clean, dry, oil-free air at 7-8 bar is an equally essential requirement for consistently accurate performance of vital bridge instruments, such as monitoring and engine control systems. It is also required for cargo pumps turbine governors and LNG/LPG cargo instrument air applications. Also needing clean dry air, is a vessel’s main engine remote control pneumatic systems, tank gauging operations, together with temperature and pressure controls.
At the same time, an efficient supply of low-pressure working air is an essential requirement for a wide range of other important applications − for tools, air-operating lights, air-operated fans, dry bulk handling, nitrogen booster compressor operation, ballast water treatment, soot filtration, exhaust gas cleaning equipment, air for sewage systems − everything from regular maintenance to bulk handling needs a 7 bar-13.8 bar air supply on tap.
And finally, there are specialist applications such as medical air or high-pressure air for seismic operations, bubble curtains and for diving or air breathing apparatus bottle filling.
The equipment criteria
Within the practical shipboard constraints of minimum power consumption and restricted installation space, it is vital for shipyards and shipowners to ensure that the performance and build quality of a marine compressed air system can meet the operational criteria for reliability, energy efficiency, stability, safety, and regulatory compliance.
Reliability: That has to be the watchword for all essential shipboard systems. Marine compressors must be fully optimised for shipborne use and be designed and constructed for continuous operational capability within engine room environments of up to 50 degrees C ambient. That means robust, tried and tested components and ancillaries that combine the benefits of long service intervals and energy-efficient whole life performance.
Stability at sea: The compressors’ component configuration should be designed to provide a low centre of gravity that minimises equipment stress even in severe running conditions. It must comply with the Lloyd’s Register Rules and Regulations of operating conditions for main and auxiliary machinery that: ‘installed equipment can operate normally in rough seas at an angle of inclination athwartships of 15 degrees static/ 22.5 degrees dynamic and 5 degrees fore-and-aft static/7.5 degrees dynamic’.
8 Atlas Copco
off ers a remote data monitoring system that off ers continuously updated data on compressor operations
Electrical safety: Under the LR regulations concerning location and construction of electrical installations, all electrical equipment is to be constructed or selected and installed such that live parts cannot be inadvertently touched, do not cause injury when handled or touched in the normal manner; and are unaffected by any water, steam or oil and oil vapour to which it is likely to be exposed.
Accessibility and compact dimensions: This is a major issue in equipment siting. However large a vessel may be, the engine room space is always at a premium. That is why the best option is to match required performance to equipment designed with fully integrated components, such as air dryers, thereby offering the smallest footprint.
A compact compressor’s dimensions should allow installation access through standard ship-sized doors and thus avoid hot work necessary to accommodate the unit. For the same reason, air connections and ancillaries such as condensate drains should be located at one side of each unit to allow maximum proximity to bulkheads and provide easy access for routine maintenance procedures.
Compliance: It is importance to establish that the materials, construction, and environmental impact of shipboard compressor equipment conforms to the rules, inspections, and certification procedures of the major recognised classification organisations. LR, ABS, DNV, ClassNK and RINA are just some of the major companies in the classification society business whose focus is to ensure owners and shipyards conform to the safety, security and quality standards set by the shipping industry.
It is the equipment manufacturers and suppliers responsibility to comply with all major classifications and Environmental Protection notations such as EP, clean design; comfort notations; environmental performance monitoring; and Green Passports (Inventory of Hazardous Materials).
All ships also have to comply with the Annex IV of MARPOL 73/78 Regulations for the Prevention of Pollution by Sewage from Ships and have to be equipped with sewage plants. To keep them in proper working condition and good balance, the sewage plant needs air to stimulate the growth of the bacterial culture. This application requires low pressure, clean and guaranteed oil-free air, best delivered by the latest low-pressure compressor screw blowers whose energy requirement is on average 30% more energy-efficient than conventional Roots-type lobe blowers.
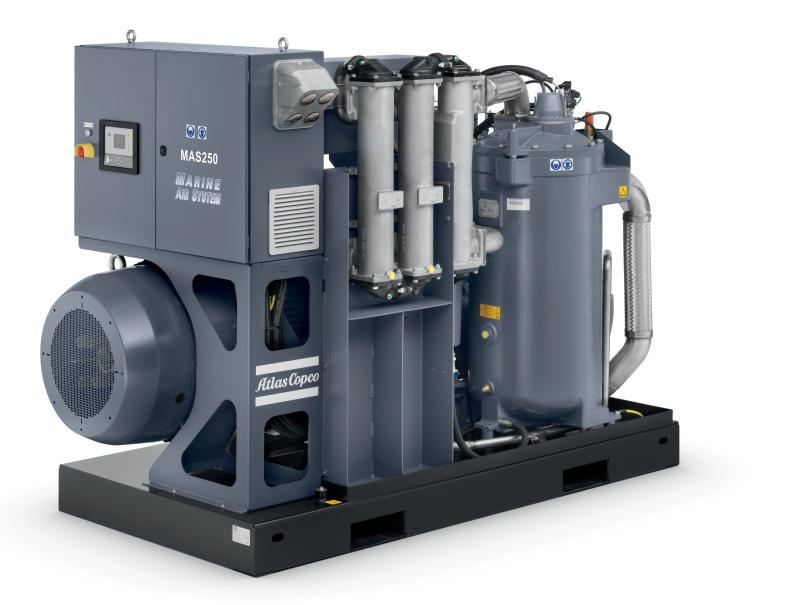
Energy effi ciency
Finally, the ultimate goal is for marine compressor equipment that demonstrates significant energy efficiency. Much has been achieved by the advanced design of key components, such as the non-contact intermeshing screw elements of an oil-free compressor, the sophisticated control algorithm of the electronic regulator used to control the speed of a compressor’s induction motor. But the most significant benefit of all is VSD technology that closely follows the air demand, automatically adjusting the motor speed, and results in achieving energy savings of up to 35% and even more.
Linked to this goal is the overriding requirement for marine compressor installations whose design and efficiency generates sustainable onboard productivity for the owners and operators yet presents no risk for the global environment.
Air power for RRS Sir David Attenborough
As a practical example of the need for custom solutions to marine air power needs, shipbuilders Cammell Laird Construction installed Atlas Copco marine-duty compressors aboard one of the most advanced polar research vessels in the world, RRS Sir David Attenborough.
8 Atlas Copco off ers a family of 5-90 kW oil-injected screw marine compressors
The vessel’s full spectrum of compressed air duties was met from Atlas Copco’s MAS range of marine compressors, technically advanced solutions fully optimised for shipborne use. The MAS family of 5-90 kW oil-injected screw marine compressors, derived from its premium GA range of stationary industrial units, sets the standard in marine compressed air production, combining low cost of ownership with reliable, energy-efficient performance.
However, even the most advanced compressors offering long maintenance intervals and service lives still need attention. That is why Atlas Copco offers parts and services packages which provide peace of mind while vessels are at sea. Atlas Copco's global presence means that servicing, spare parts supply, training, and technical support can be supplied locally wherever it was required.
Atlas Copco can supply original compressor parts, and OEM non-Atlas Copco parts, direct to freight forwarders or anywhere on the planet at short notice. Over 3600 Atlas Copco field service engineers in 180 countries are ready to attend onboard when assistance is needed for major services and overhauls.
The role of SmartLink
Knowing the status of marine compressed air equipment at all times is the surest way to spot any developing problems, uncover potential energy savings, and achieve maximum uptime of the compressed air systems. These insights can be realised through SmartLink, Atlas Copco’s remote data monitoring system that works via a vessel’s internet (satellite) network, and where compressor data will be continuously updated. Alternatively, SmartLink can rely on passing through network coverage areas and data can be uploaded from there.
Conclusion
When it comes to marine compressor applications it is evident that there is no one-size-fits-all solution. Each machine installation requires matching specification and performance to the shipborne equipment and the operational profile.
Equally, the hardware installation has to be supported by a worldwide onshore service and parts support network. In making equipment choices there is no doubt that shipyards and shipowners will give preference to suppliers who can offer a wide range of compressor options, a 24/7 global support network of marine experts, based in all major industrial ports, together with an immediate OEM parts supply backed by informed maintenance procedure guidance.