
12 minute read
When the wind blows
RESEARCH PROJECTS DEEPENS WIND-ASSIST DESIGN INSIGHT
Researchers at MARIN are examining the regulatory framework and design maturity of wind-assist technologies
Over 20 companies participated in the WiSP1 project that evaluated the potential fuel savings of wind-assisted propulsion and fi nished in 2021. Emissions savings analyses from currently sailing ships range from roughly 5% up to 15% as a yearly average, but that is just the beginning, says Rogier Eggers, Senior Project Manager at MARIN. Now a follow-on project WiSP2, led by MARIN and ABS, is focused on evaluating the potential for greater savings as the technologies mature.
WiSP1 saw analysis mainly on the 5-15% wind-assisted scenario that was submitted to MEPC76 (June 2021) by Comoros and RINA. A follow-up informal working group led by Germany, also with other input, resulted in a revised guide line for the prediction of wind propulsion performance under EEDI and EEXI: MEPC.1/Circ.896. At that time, Eggers says a controversial change was also introduced: this guideline allows for the calculations to only consider the 50% best winds when determining EEDI and EEXI values. The impact of this is now also being investigating in WiSP2.
“This offers a big incentive. An incentive may be considered appropriate. Other energy saving devices (e.g. air lubrication) is only to be assessed at one speed and loading condition and in calm seas whereas wind propulsion was to be assessed using overall global wind conditions. Ships with wind propulsion are more likely to sail in better wind conditions. However, at the same time, the implemented incentive is very large. Also, some device types which are very selective with the wind conditions that they can work with may be favoured more than other devices that present a wider range of usable wind conditions. In short: we feel more work is needed, and we will do that in WiSP2”
For efficiency gains of 5% to 15%, there is not a lot of further discussion needed on ensuring ships’ operability in demanding conditions, says Eggers, who has been heavily involved in both projects. “Ships generally still behave the same way as a conventional ship, but as you go to more substantial proportions of wind power being used, more discussion is necessary. For instance, significant yaw moments are introduced that depend on the wind condition. In order to counteract these loads, steering systems will need to constantly keep the ship in balance. Enough reserve capacity needs to be ensured for manoeuvring and course keeping in wave, although it is mentioned that some wind propulsion systems may also in fact help steer the ship”
Current regulations were never intended for this scenario. In the updated circular for EEDI and EEXI there is a disclaimer that there would be a bias in the current regulations if they were applied to more substantially more wind power onboard, and correcting this is a focus area for WiSP2, along with other regulations, such as the IMO manoeuvring standards.
Ultimately, the aim of WiSP1 and now WiSP2 is to prove what kind of fuel savings shipowners can achieve, enabling them to make informed investment decisions. A study by CE Delft on the market potential for wind propulsion found that a major barrier to uptake is the shortage of transparent and independently verified information and methods to predict the performance of wind propulsors. Other barriers identified were a lack of sufficient practical examples and tailor-made work to demonstrate compliance with statutory and class rules and regulations.
“We have seen some really large savings being predicted by developers, followed by still larger claims by their
8 MV Ankie after installation of the extended VentiFoils
competitors, but there is a lot of uncertainty. The assumptions behind these predictions were often not published, so you couldn’t make apples-to-apples comparisons,” said Eggers.
WiSP2 aims to: 5 Improve methods for transparent performance prediction 5 Use the improved methods to provide ship owners/ operators with fast low-cost predictions for their fleet 5 Further review of the regulatory perspective, recommend improvements and clarifications, and provide examples to establish compliance 5 Develop a basic performance prediction tool to be used by participants 5 Propose in-service speed trials 5Assess the influence of seakeeping on performance.
The WiSP2 team is examining a range of vessels including coastal vessels of some 3,000 dwt up till 300,000dwt tankers and a range of wind technologies including Dynarig sails from Dykstra Naval Architects, VentoFoil suction wings from Econowind and wingsails and Flettner rotors from other participants.
The new findings from WiSP2 will be condensed into updated recommended methods for performance prediction and reported as submissions to MEPC, potentially other IMO committees and a new dedicated committee working on standards at the International Towing Tank Conference (ITTC). They are expected to be made public in March 2023.
Eggers believes that existing technologies can offer largescale wind power to a ship. In an update to industry at Posidonia, Eggers and his colleague Anton Kisjes discussed the case of a 300-metre Newcastlemax bulk carrier fitted with four Flettner rotors each 35 x 5 metres sailing. On common global routes for this type of ship, estimated fuel savings are about 10-15% annually in a business as usual scenario (fixed speed and course). Weather routing, more selective choice of routes and increasing number of wind propulsion units may push that up to 15% - 20% and further when the ship design and speed is also altered.
The determination of estimates such as this, they explained, particularly as more wind power is incorporated, involves verifying structural and seakeeping performance and evaluating the aerodynamics of how the propulsors interacted with each other and with the vessel.
Hydrodynamically, forces and moments need to be calculated as a function of drift and heel; propeller efficiency is calculated as well as ensuring there is sufficient steering capacity for course keeping in waves and during turning. Course keeping can improve or worsen depending on many factors, and other measures may be needed to ensure the safety and performance of the vessel. Relevant parameters include hull dimensions to create more draught, V-shaped sections or box keels, enlarge skegs, high-lift or multiple rudders or other appendages such as dagger boards.
MARIN’s research efforts go beyond WiSP. The research organisation announced the launch of the Optiwise HORIZON Project in 2022 which aims to holistically improve design and control of commercial ships with wind propulsion. The EU funded research project is targeting average energy savings between 30% and 50% when compared to equivalent conventional ships while ensuring operational feasibility in a realistic wind climate.
Eggers is one of the leaders of the project: “Fruitful and promising progress has been made with the introduction of new devices to the market, with some 15+ ships sailing commercially with wind propulsion in the world fleet. Wind propulsion is so far mostly applied without re-considering the overall ship design and operations. Whereas that fits within a business-as-usual scenario, it does limit the attainable savings.
“With Optiwise we are building on R&D already under development among the consortium partners in the last years and re-thinking the design process and energy management of ships with wind propulsion, while still making sure that these ships conform to common operational and regulatory requirements. We thereby expect to enable and showcase much higher savings than what can be seen in the present market applications.” The Optiwise project will pursue its objectives through three operational use cases: a bulk carrier with Flettner rotors, a tanker with wing sails and a passenger vessel with a AeroRig system involving rigid panels. These cases will provide a methodology that can be applied to the majority of the seagoing shipping fleet. While the wind propulsion type is preselected for each ship type, the exact implementation and change of the ship design and energy management is fully open to further performance enhancement. One option that Eggers envisages is the replacement of a single main engine with a number of generators that will provide more flexibility in power output and enable the engines to run more optimally than a single large engine would at low loads. He also envisages that DC distribution, when available at scale, may be suitable for gensets to run at optimal loading, and that controllable pitch propellers may be used to reduce drag and possibly to act as generators at the times when wind power is the dominant power source onboard. The project scope involves extensive simulations where disciplines such as aerodynamics, hydrodynamics and routing and energy management are holistically brought together. This will be complemented with basin tests to assess manoeuvring and seakeeping, bridge simulations to assess crew operation, and land-based wind propulsion tests to verify better control. The project will deliver open guidelines for integrated system optimisation with wind propulsion and smart measurement and control for best operation. The guidelines will be demonstrated in the aforementioned experimental model tests, bridge simulations and measurements on a full scale land based wind propulsion unit. The WiSP and Optiwise projects demonstrate a resurgence of research on wind assisted propulsion for ships, but this is not the first time it has occurred. Ever since the diesel engine and propeller have dominated ship propulsion, there has been research on wind propulsion, notably at the time of the oil crisis in the 1980s. Eggers is optimistic that this time the many research will lead to a major uptake of wind propulsion. e the eters aped ultiple earch
IZON n and e EU vings valent y in a l and on of ailing Wind g the thin a vings. research will lead to a major uptake of wind propulsion.
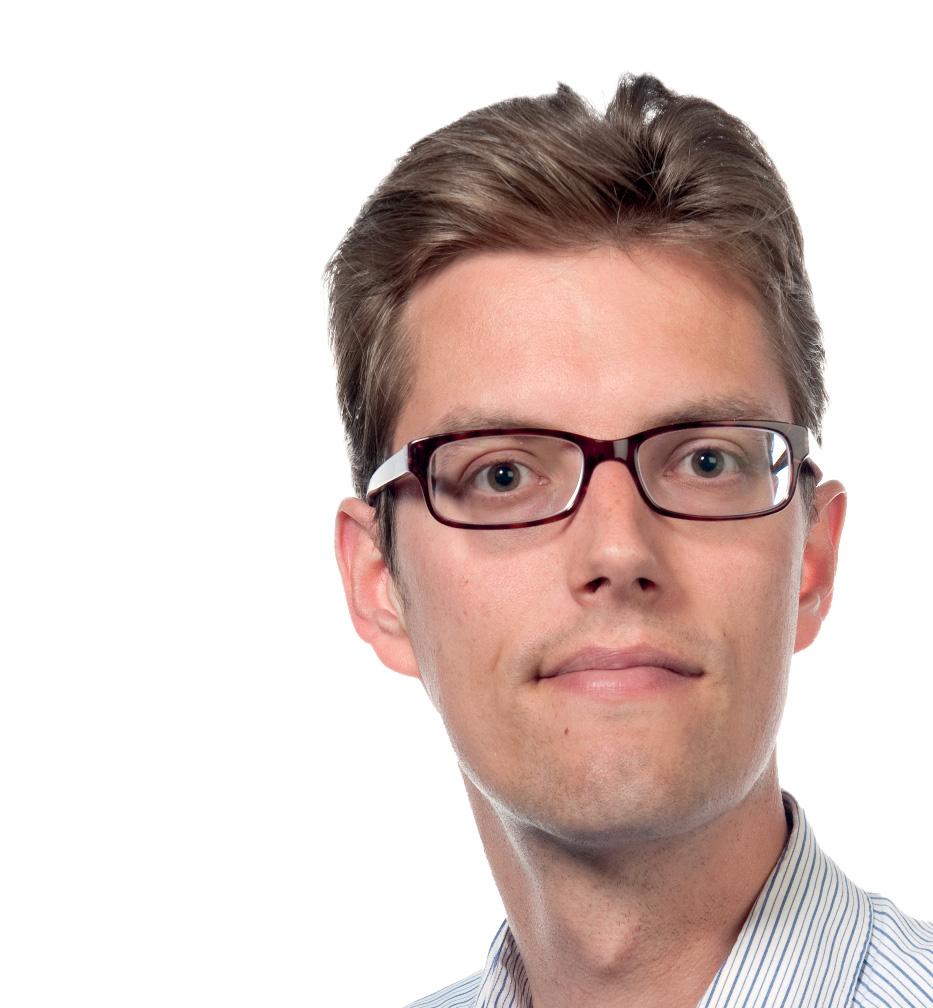
8 Rogier Eggers,
Senior Project Manager at MARIN

THE FUTURE OF WORLD SHIPBUILDING
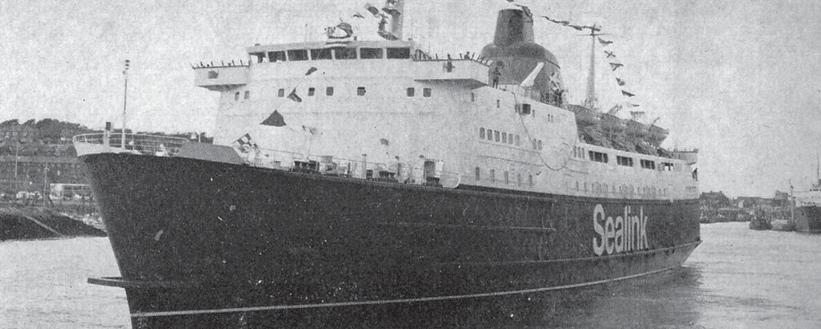
The July 1972 issue of The Motorship took a look forward, asking how ship design might develop in the following 30 years.
The first conclusion was that merchant ships would grow in sophistication, narrowing the technological dividing line between warships and commercial vessels. Propulsion was one instance of this: commercial vessels were expected more widely to adopt not only gas turbines, but also nuclear power. In fact, Japan was stated to be building 280 nuclearpowered ships in the 30-year period under investigation.
One prediction which certainly proved correct was the growth in containerisation, although at the time container vessels were mostly loss-making, because the industry had not found the right balance between over-large vessels which relied on only a few routes and passages to handle the trade, and smaller vessels, less able to absorb the stresses of rough seas. Unpredictability of the labour force at the docks, with an understandable resistance to change, was another problem. These, however, would all be overcome, with containerisation offering a viable interface between sea, rail and road transport systems. The LASH (lighter aboard ship) concept too showed promise, offering versatility and quick turnround in port, while the OBO (oil-bulk-ore) carrier was another example of a possible transport revolution, such vessels negating the need to travel in ballast, though the wide differential between cargo densities was acknowledges as presenting structural challenges.
Although ships were expected to grow, up to around 500,000 dwt, this would be accompanied by a boom in short-sea ro-ro traffic, able to carry large loaded lorries, doing away with the need for loading and unloading – but, in a prescient nod to future environmental concerns, use of such large vehicles could be restricted by government regulation. And despite expected growth in gas turbine and nuclear propulsion, the high-power diesel engine directly driving a propeller would reign supreme for large ocean-going ships.
Ship descriptions majored on the first of a trio of cross-Channel ro-paxes to be operated by British Rail, in conjunction with its French, Belgian and Dutch collaborators under the new ‘Sealink’ brand. The three were being built at Brest naval dockyard in France, and were said to offer new standards of comfort and facilities for the 1400 passengers. 130
8 The 5000gt cross-Channel ferry Hengist
cars or 38 trucks could be carried on the lower decks, loaded via a stern ramp and bow door, offering drive-on drive-off convenience. Main engines were a pair of Pielstick 16-cylinder PC2V engines, each rated 7,500 bhp, burning HFO.
The August issue offered a taste of things to come, with a scholarly study on the selection of propulsion machinery for LNG carrier ships. Boil-off gas, an intrinsic feature of these cargoes despite good tank insulation, was seen as offering potential ‘free’ fuel for propulsion. It was recognised that boil-off gas could be used ‘as is’ in the engines, or re-liquefied to return to the cargo tanks or for storage in fuel tanks for propulsion. Dual fuel engines seemed to be the answer, but the different characteristics of gas and oil fuels presented many challenges. Diesel, steam turbine and gas turbine options were all considered. Surprisingly, perhaps, the most viable solution was seen as a dual-fuel low-speed diesel. As we now know, achieving this ideal would take many more years.
Finally, another nod to today – the new HyundaiMipo shipyard in South Korea, due to be completed later that year, announced plans to build six supertankers, up to 700,000 dwt each, per year. A&P Appledore had helped set it up, staff were being trained at Scott Lithgow, with similar input from other European countries. Nobody in 1972 seemed to appreciate just how the Korean shipbuilding industry would grow.
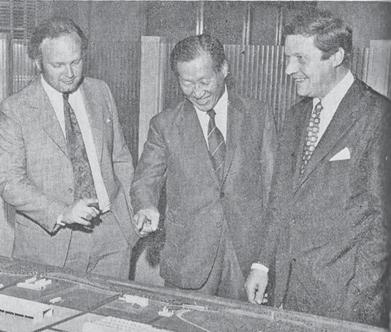
8 Management from Appledore, Maersk and Hyundai
examine a model of the new Korean shipyard
The international magazine for senior marine engineers
EDITORIAL & CONTENT
Editor: Nick Edstrom editor@mercatormedia.com
Correspondents
Please contact our correspondents at editor@motorship.com Bill Thomson, David Tinsley, Tom Todd, Stevie Knight, Wendy Laursen
Production
David Blake, Paul Dunnington production@mercatormedia.com
SALES & MARKETING t +44 1329 825335 f +44 1329 550192
Brand manager: Sue Stevens sstevens@mercatormedia.com
Marketing
marketing@mercatormedia.com
EXECUTIVE
Chief Executive: Andrew Webster awebster@mercatormedia.com
TMS magazine is published monthly by Mercator Media Limited Spinnaker House, Waterside Gardens, Fareham, Hampshire PO16 8SD, UK
t +44 1329 825335 f +44 1329 550192
info@mercatormedia.com www.mercatormedia.com
Subscriptions
Subscriptions@motorship.com or subscribe online at www.motorship.com Also, sign up to the weekly TMS E-Newsletter 1 year’s magazine subscription Digital Edition: £GBP177.00
© Mercator Media Limited 2022. ISSN 2633-4488 (online). Established 1920. The Motorship is a trade mark of Mercator Media Ltd. All rights reserved. No part of this magazine can be reproduced without the written consent of Mercator Media Ltd. Registered in England Company Number 2427909. Registered offi ce: Spinnaker House, Waterside Gardens, Fareham, Hampshire PO16 8SD, UK