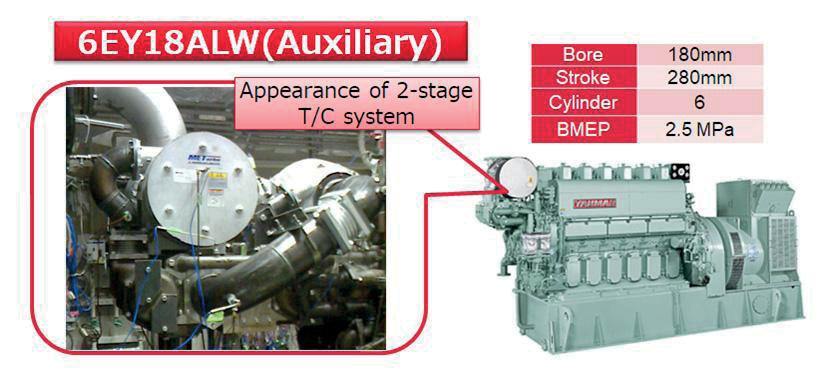
11 minute read
Auxiliary TC retrofi ts
YANMAR TESTS RETROFITTING ENGINES WITH TWO-STAGE TCS
Tests have shown retrofi tting four-stroke auxiliaries with two-stage turbocharging is practical and eff ective, off ering increased effi ciency and output possibilities, according to Yanmar
In a paper published in March, Yoshinori Fukui of its Speciality Machinery Engine Development Department said that the experiments had been prompted by two things: the success of its four-stroke 6EY26W propulsion engine - which was launched in 2014 and has two-stage turbocharging - and the rising electrical power demands caused by a growing amount of equipment installed onboard ships.
In particular, he singled out scrubbers that are being retrofitted as an alternative to using low-sulphur fuel to meet IMO’s 2020 sulphur cap. Their power demands are typically supplied either by installing additional auxiliary generator sets or uprating the existing installation. Instead, “it was thought that the ability to increase output without increasing the amount of space taken up by the engines would be a more desirable option,” his paper notes, which would make better use of the limited space available.
To check whether that could be done, Yanmar set out to test the same combination of two-stage turbocharging and a ‘strong’ Miller cycle (which has an earlier inlet valve close timing than the conventional Miller cycle) that is used on the 6EY26W and apply it to a 6EY18ALW test engine.
Its results were impressive: a 10 % increase in brake mean effective pressure (BMEP) and a reduction in fuel consumption of 5-10g/kWh across the entire load range. Although the paper does not express that as a percentage, a data sheet for the 6EY18ALW engine on Yanmar’s website indicates a typical fuel consumption of around 190g/kWh, which suggests the new set-up provides a saving of up to 5%.
To achieve this required an additional piece of technology, however: a new waste gate valve (WGV), which Yanmar developed as part of the project. It was produced by repurposing a commercially-available valve as a WGV and using electronic control to provide linear valve opening characteristics.
In fact, because there are two turbochargers, two separate
Image: Yanmar
8 Yanmar’s
6EY18ALW test engine fi tted with two-stage turbocharging
WGVs were fitted and the researchers found contrasting results between the high-pressure WGV (HP-WPV) and lowpressure WGV (LP-WPV). In an engine with single-stage turbocharging, reductions in pressure ratio due to the WGV reduce the combustion pressure, ultimately leading to a deterioration in brake-specific fuel consumption (BSFC), their report comments. But “while the LP-WGV demonstrates this characteristic, in the case of the HP-WGV, the BSFC remains largely unaffected by changes in the pressure ratio caused by valve opening or closing,” it records.
In addition, “when the results of the gas exchange work in the HP-WGV are considered, the amount of work tends to increase the greater the reduction in pressure ratio, indicating an improvement in pumping losses in the air intake and exhaust,” which compensates for the reduced combustion pressure. Overall, “the testing demonstrated a reduction in NOx emissions due to the lower pressure ratio.”
It also showed that the combination of two-stage turbocharging and the new HP-WGV increases engine output but does not lead to higher maximum combustion pressure, so “the system keeps the load on pistons, cranks, and other key engine components at a similar level to that of previous engines.”
There is still more work to be done, however. When fitted with two-stage turbocharging, the engines meet IMO’s Tier II NOx limits, but would need an SCR unit to meet Tier III. Future research could include investigating high-pressure SCR systems and low-NOx combustion techniques by adding water to fuel; both techniques “are already in commercial use on two-stroke engines but remain rare on four-strokes,” the paper notes.
So “issues remain,” the paper concludes, but it promises that “Yanmar intends to keep working toward commercialisation of the technology in recognition of its ability to deliver added value to customers.”
GAS-SHIELDED BERGEN ENGINES SPECIFIED FOR BMVI SHIP
Two 95m multi-purpose emergency-response vessels under construction at German shipyard Abeking & Rasmussen will each be powered by four Bergen B36:45L6AG engines rated at 3,600kW.
Each engine will be shielded by a gas protection arrangement that will allow them to remain operational even if the ambient air has been contaminated with explosive gases.
Bergen Diesels are built by Rolls-Royce Power Systems (RRPS) and Rolls-Royce has developed a protection system that will protect the engines when the ship is responding to, for example, a gas tanker accident. Although the four-stroke medium-speed engines are gas-fuelled, if it were to get into the combustion chamber in an uncontrolled way via the intake air, “the engine will become unmanageable,” explained Rolls-Royce project manager Christian Prinz in a statement.
Instead of preventing gas-laden air entering the engine, the system adjusts the amount of gas fuel supplied to the engine to take account of the amount being ingested via the intake air. As a last resort, “if the gas volume is too high, special quick-acting flaps shut off the intake of gas and air and the engine comes to a stop,” the statement explained.
It also quoted Knut Müller, vice president for marine at Rolls-Royce, said that Rolls-Royce is the only manufacturer worldwide able to supply such powerful engines with gas protection and the relevant certification. “We’ve combined the decades of experience ... in the field of medium-speed gas engines ... with our highly-specialised gas protection expertise to create an effective solution,” Mr Müller said.
Supporting the system’s development for this application has been Bergen Engines’ RRPS stablemate MTU Friedrichshafen. The pairing brought together Bergen Engines’ experience of building LNG-fuelled engines with MTU’s involvement since 1986 in developing engines for use in emergency-response missions.
MTU also has a historic connection to the order, which was placed by the German Federal Waterway and Shipping
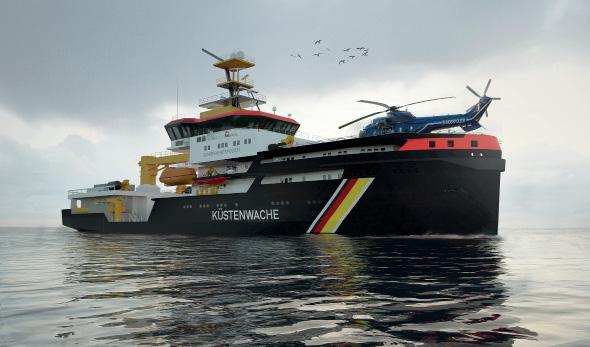
Administration to replace two smaller MTU-powered predecessors, Scharhörn and Mellum, after 46 and 36 years of service respectively.
In a December 2019 statement, the yard highlighted another aspect of the gas shielding arrangement by pointing out that it is important to prevent any leakage from the LNG fuel system during firefighting operations. The yard said that, working with its engine partners, it had further developed the technology so that “the entire LNG and piping systems are double-coated and encased” so that “in the unlikely instance of gas leakage, methane stays trapped in the protective casing.”
They are due to go into service in 2023 and 2024 and a third identical vessel may follow; a decision is due to be made by the end of this year.
Type-approval brings new HiMSEN engine to market
8 A Rolls-Royce
protection system will shield the Bergen engines on two new emergencyresponse vessels
Hyundai Heavy Industries’ (HHI) latest HiMSEN engine model is now being off ered as a propulsion option for small and medium-sized vessels, such as MR tankers.
Its H21M engine is a development from its established H21/32 engine, which dates back to 2002, but this new version is about 30% smaller, with a corresponding weight reduction, and is being marketed as a second-generation ‘Compact Powerful Engine’. Type-approval tests were carried out on a six-cylinder 6H21M engine on 25-26 March for DNV GL and the Korean Register. DNV GL’s certificate is dated 21 April, which is in line with HHI’s plan at the time the tests were carried out that it should be available that month; The Motorship has not been able to confirm when KR issued its certificate.
Rated speed, rpm 720 900 720 900
Mean eff ective pressure, bar 24.1 24.1 26.3 26.5
Max. fi ring pressure, bar 165 165 173 173
Rated power, kW/cyl 160 200 175 220
Max power (9 cylinders), kW 1,440 1,800 1,575 1,980
Among the design changes incorporated into the new version are adjustments to key parts such as its fuel injection pump, bearings and pistons so as to make it suitable for its new application. It has also been given a modular assembly concept, which particularly affects its lubricant coolers, filters, and supercharged air coolers.
8 HiMSEN H21M engine option
The engine is available in two speed options - 720rpm or 900rpm - and two firing pressures are available for each speed, giving four power ratings, with a maximum of 220kW/cyl and a maximum engine size of nine cylinders.
FOUR-STROKES SHARE DIGITALISATION BENEFIT
MAN Energy Solutions is applying digitalisation solutions to improve the reliability and performance of existing solutions, including monitoring four-stroke auxiliary gen sets
Per Hansson, head of digital and strategy at the engine builder, said that the term ‘digitalisation’ is often used “to sell more or less specialised software to shipowners” but he believes that its real value is much more than that.
In exclusive extracts from a Q&A transcript for The Motorship, Mr Hansson said that digitalisation “is about making life easier and business more effective and transparent for our customers, translating into bottom-line improvement.” It achieves that by being “based on measurable and manageable performance”, he added.ance , he added.
In his interview, Mr Hansson highlighted its PrimeServ ighted its PrimeServ Assist service, which was launched during the 2018 SMM uring the 2018 SMM exhibition and has been expanded since, including trials that e, including trials that started in December 2019 to add smart glasses. These art glasses. These provide its technical specialists in remote operations mote operations centres with the customer’s own view, which n view, which supplements the service’s data monitoring. ring.
He also referred to its digital platform MAN CEON, orm MAN CEON, which was launched last year (The Motorship, 5 March otorship, 5 March 2019) to collect and evaluate operating and sensor data to and sensor data to enable real-time monitoring of its marine, industrial and ne, industrial and power plant installations.
A year on, and this platform “now forms orms the backbone of our developing digitalalservice business,” Mr Hansson said, d,
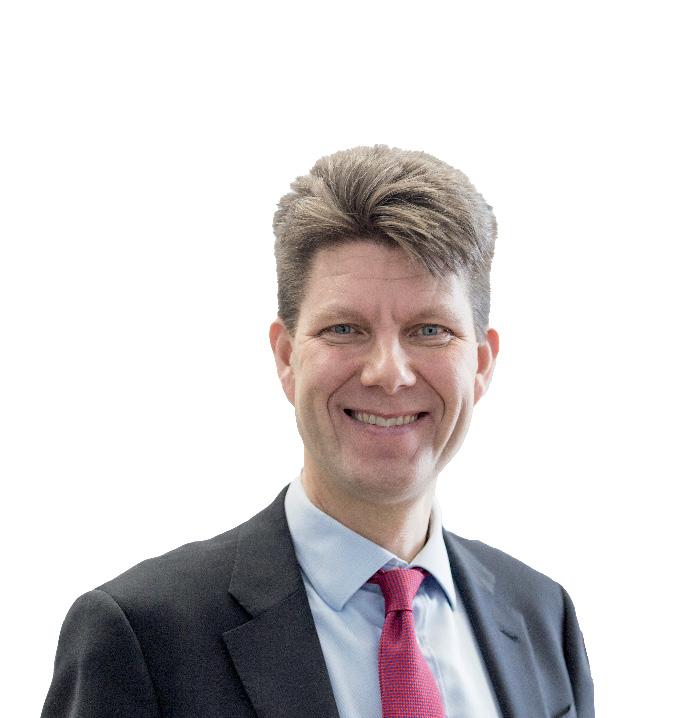
because it “integrates data and information from MAN machinery and its operational environment and applies intelligent analytics to evaluate the current condition [and] predict upcoming issues.”
He said that this marked the start of its exploration of “the potential of new digital solutions for our business” but it is a start that is founded on a number of initiatives taken since 2016, when the company started to build a dedicated digital team consisting of IoT experts, software engineers and data scientists. “They are closely working together with customer scientists. They are service representatives and domain experts to expand our service representati digital value-creation chain,” he said, which covers a digital value-creatio spectrum from digital hardware development to cloudspectrum from d based platforms and front-end applications. based platfo In future, through PrimeServ Assist and MAN In future, CEON “we will use this data to improve the reliability CEON “we w and performance of our existing solutions as well as and perform new, innovative service offerings,” he added. new, innova But digitalisation is more than a technical But digit consideration, he said. “It is above all a cultural issue; consideratio a mindset.” He explained that thinking digitally “means a mindset.” He being able to quickly adapt your own business being able model to make use of new technologies and model developments, and the exploding availability develo of data.” of dat
Caterpillar engines power landmark hybrid tug
When it entered service earlier this year, the hydraulic hybrid tug Boğaçay XXXVIII became the fi rst vessel in the world to be completely fi tted with Caterpillar Marine’s Advanced Variable Drive (AVD).
It also marks a commercial landmark, bringing to 200 the number Robert Allan designed tugs constructed by the Turkish tug builder and operator.
This vessel is based on the RAmparts 2400SX design and the AVD coordinates a Caterpillar propulsion system, consisting of two Caterpillar 3512 main engines rated at 1,765kW each, a C32 auxiliary engine of 1,081kW and two 2.7m diameter MTA 627 fixed pitch thrusters, linking them together and to the bridge controls.
The AVD system consists of a pair of dual input, continuously variable transmissions, located in the shaftlines between the main engines and the Z-drive propellers. It provides “a true variable speed marine transmission which will provide serious operational savings in fuel and maintenance,” according to Caterpillar Marine’s tug & dredge segment manager, Michael Braun. It achieves this by optimising engine and system operation independently of propeller speed while supplementing power hydraulically in one of three propulsion modes.
In its transit mode, the main engines are not powered off and are, with propulsion provided from the auxiliary engine via two 435kW hydraulic motors, giving a maximum speed of about 9 knots. In its work mode, propulsion is provided hydro-mechanically, using the most efficient combination of engines and hydraulic systems. This delivers a bollard pull of up to 60 tonnes.
In its boost mode, the auxiliary engine either provides additional hydraulic power to give a bollard pull of up to 70 tonnes or a maximum speed of more than 13 knots.
A further Fi-Fi mode is also available, in which the auxiliary engine is coupled to a firefighting pump while the main engines are dedicated to providing propulsion power.
In an online article posted on its website in May, Sanmar said that the AVD makes it possible for the engines to be smaller than would normally be the case in a tug of this power, which would normally be fitted with more powerful Caterpillar 3516 engines. The reduction has been made possible by using the C32 auxiliary engine both to drives the Fi-Fi pump and be available for propulsion support when required.
The installation’s flexible couplings, resilient mounts and composite shafts have all been supplied by Vulkan. Each main engine is resiliently mounted on its T60 mounts and the auxiliary engine sits on T35 mounts. The gearbox is rigidly mounted on Rotachocks. The engine is connected to the gearbox by Vulkan’s new Vulkardan F 57 shaft while a VULKAN floating composite shaft links the gearbox to the Caterpillar thrusters.
Its auxiliary drive line uses a torsional Vulkardan F 54 coupling from the engine to the gearbox and a Vulkan Metaflex shaft onward to the firefighting pump. Both gearbox and pump are mounted on Rotochocks, an arrangement that Vulkan reports reduced installation and alignment time, resulting in project cost savings.