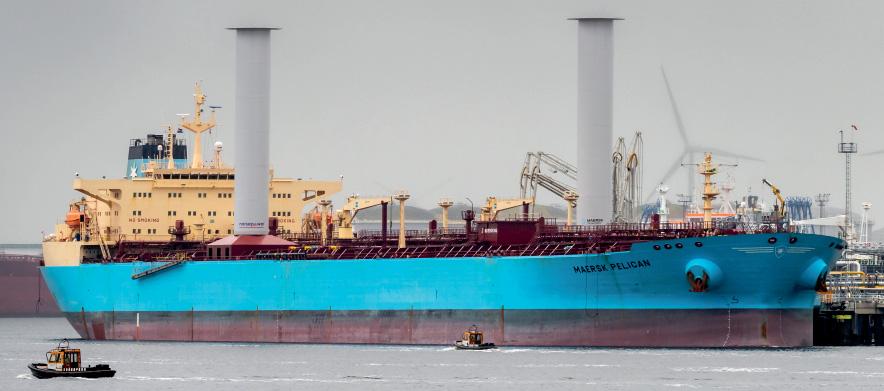
41 minute read
When the wind blows
WIND ABOVE: WHAT GOES ON BELOW?
Could wind’s promised effi ciency impact other systems? Stevie Knight asks the questions...
Currently, “Flettner rotors or kites are rather easy to integrate” says Philip Holt of MAN ES. That’s partly because the eff ective power provided by these systems has historically been quite low: “We have heard of fuel saving of around 3.5% to 5% and up to 10% in special cases on merchant vessels”, he explains. That puts it in the same ballpark “as sailing in small waves with a tail wind.... for the same rpm setting, the propeller simply requires a lower amount of torque”.
However, if the whispers of a near-future 20% and potential 40% vessel efficiency are to be believed, there are further considerations.
“As these mechanical sails push the ship forward through the hull, the amount of additional energy introduced could vary a lot, from zero to half the installed power,” says Tuomas Riski of Norsepower, adding that the onboard plant needs to be flexible enough to compensate for these reduced loads. However, given fairly steady conditions, this still falls within the efficiency range for long-haul ships’ two-stroke engines.
“If you’re operating on 50% engine load with the wind propulsion aid, and 90% without it, the specific fuel oil consumption (SFOC) will only deviate by a few grams,” says Holt, adding that MAN’s slow speed, two-stroke models tend to be efficient down to 10% MCR.
It’s plausible that these engines’ load response might be a little slow, but as Van der Kolk goes on to explain, while most studies look at retaining a fixed speed, in fact there is a wider operating envelope as in reality some wind variation will simply be taken up by a greater ship speed. MARIN’s Rogier Eggers adds that even if a conventional, two-stroke propulsion plant isn’t fully adjusted for WASP, “the savings are likely to still be significant, even if they could be higher”.
Riski remarks that experience bears this out: Maersk Pelican’s impressive 8.2%, savings resulted from installing a pair of large, 30m Rotor Sails without paying the engines any special attention. The 61,000gt tanker “has faced variable wind conditions on continuous basis, but” he stresses “it has not had any challenges in adapting to fluctuating loads”.
However, a greater degree of wind assistance may change the picture: “We will have to see what is really possible with adjusting two-stroke propulsion,” says Eggers, though Holt adds that while “it’s mostly speculative”, during high levels of wind assistance, the engine might benefit from alternative optimisation parameters - although “firm consideration” is still over the horizon, “actual numbers will be required to perform a study of the potential”.
Despite this, Holt underlines that even given sizeable WASP capacity, MAN ES “doesn’t recommend reducing the main engine power based on an installation of some sort of wind assistance... as it cannot be ensured to operate in heavy weather”.
Still, WASP installation could give rise to alternative power configurations. Installing a shaft-generator PTO along with the WASP on deck “could be beneficial” says Holt, as the main engine may be used to supply the electrical power rather than the auxiliaries. It would make for an interesting set up, says Sami Kanerva, ABB Marine and Ports: the gensets could take a break as the two-stroke engine picks up the load during periods of greater wind assistance.
NOT ONLY FOR THE BIG BOYS
Ship type does play a part says Eggers: higher speed results in “the effective wind direction above deck being mostly from ahead”, so don’t expect long-haul containerships to line up for WASP installation, even if they could arrange it without sacrificing capacity. However, more modest general cargo vessels and coasters “are interesting, because their lower speed translates to a more favourable wind angle”, he remarks.
And in this arena, four-stroke engines reach a broader audience.
As Kanerva explains “in contrast to the larger oceangoing cargo ships, diesel-electric propulsion is typically applied to smaller vessels with a wider operating profile”, given this, it is “usually more effective to have multiple medium-speed engines”. This, of course, applies doubly to those looking at low-carbon or coastal emission-mitigation strategies.
8 Maersk Pelican’s
engines absorbed the variable loads from the Flettner tow eff ect
“Wind assist is like another form of hybrid - with its own particular requirements... so you need to tie together and balance the various power inputs”, says MARIN’s Alex Grasman. He underlines, this demands high level power management, not just engine control. But for first movers, it’s a good idea to be able to track what’s really going on so Viking Grace has installed ABB’s Octopus system which can validate the collected data and a machine learning module which can carve up the various effects into their components: drag, wind, wave resistance as well as the push from the WASP.
The recent Flettner trial on Viking Grace uncovered a picture that underlines the subtleties: for example, threading through an archipelago or long fairway “where a vessel needs to move precisely but the wind can be inconsistent, it’s actually difficult for either Flettners or even the power plant to run that optimally”, says Kanerva. However, the picture changes if there’s a longer sea leg.
He remarks: “When we look into ro-ro and merchant vessels with steadier wind conditions and longer ocean passages where they can slightly optimise their heading, then it is really very viable as propulsion support.”
Eggers also believes that some vessels could gain an advantage, he cites ro-ro as presenting “little conflict” with loading or unloading patterns: further, ferries and cruise vessels “may operate in specific areas with favourable winds”.
Moreover, as Kanerva remarks, a four-stroke plant will likely be better able to follow the load curve, which may result in a closer match with the desired speed. Eggers comments that, “even without changing schedules and routes, large savings could be achieved, although it will still not be at its theoretical maximum”. He also points out that for cruise and longer-distance ferries especially “there is the additional incentive of good PR”.
“Of course you want to be confident in selecting the appropriate route and speed distribution” for each voyage, he adds: if the engines have limited response to the load curve, “speed variation may be wider over the duration of an individual trip”.
ROUTES
This brings us to route choice. Usefully, the rapid advance of artificial intelligence means that voyage optimisation services release WASP-installed vessels from traditional 19thC trades, enabling savings on a wide range of less windy routes.
It also allows realistic choices. For example, NAPA’s software uses AI to tailor the output for forecasted weather patterns, specific vessels and type of assistance, yielding a balance between time and fuel saving options.
However, while suitable routes can offer general consistency, that’s spread around a probability curve. So, while the wind conditions don’t usually change that fast, “fast changes can occur”, remarks Riski.
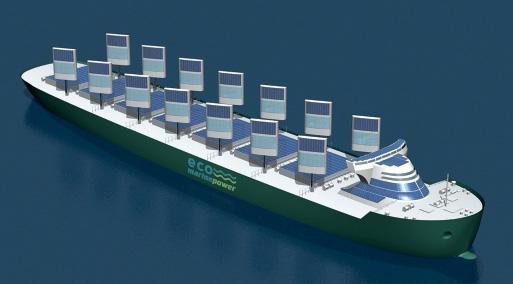
8 EMP’s Aquarius Eco Ship design “would most likely
incorporate an onboard DC grid to allow a range of power sources to be plugged in”
It will take careful handling: inadequate power management could result in “generators cutting in and out several times an hour, eating away at the savings” says Kanerva.
Even with a forgiving operational envelope, a number of four-stroke applications might usefully entrain an energy storage system. Kanerva explains that this would be for “strategic loading, not peak shaving”: the battery potentially supporting the propulsion for longer periods, “maybe even up to half an hour”, he adds.

ONBOARD GRID
This yields a synergy with other, potentially interesting power sources. As Riski points out, “whether that’s LNG-electric, hydrogen-electric or some other electric hybrid, everything gets routed through the motor”. He adds that typically, this leads to “a more responsive power plant”, making the integration of WASP systems somewhat easier.
Atkinson explains EMP’s Aquarius Eco Ship design “would most likely incorporate an onboard DC electrical grid and this would allow a range of power sources to plugged in” he says, from batteries and photovoltaics to fuel cells.
Importantly, the idea avoids penalising first movers. He adds: “As these technologies develop further, the existing equipment on the ship could be upgraded or even perhaps replaced.”
In fact, the sail rests on the company’s Aquarius MRE (Marine Renewable Energy) base, a control solution that’s developed to be adaptable, taking on new forms of energy as they reach fruition.
One more point to add from Holt: there might be a challenge in the resistance created by the WASP during adverse weathers and designers will have to take this into account when designing for compliance with the rule on the minimum propulsion power which is currently being set.
ECONOMICS
However, when it comes to the business case, the cargo industry simply has the “wrong model” concludes Gavin Allwright. He points out there’s still a disconnect between who pays for the investment and who gains, but adds the system could do with a complete overhaul. “If you are tweaking the existing paradigm you’ll get significant gains, but what’s really needed is a move from a time-charter to a slot-charter model with a fuel or carbon-based clause,” he explains. “If you are prioritizing decarbonisation, it could benefit the environment and bottom line.”
8 Voyage
optimisation will be part of the deal for any wind assisted propulsion
BY THE NUMBERS: DATA OFFERS OPERATIONAL INSIGHTS
Data led solutions, such as Hempel’s SHAPE, have a vital role to play in helping shipowners meet targets, notes Andreas Glud, Group Segment Manager, Dry Dock, Hempel A/S
To say that data matters when looking at operational effi ciency is an understatement. Against the backdrop of uncertainty, adopting solutions that allow data-driven decisions to be taken is vital. But why has this become more important now than ever before?
One of the most significant environmental regulations affecting the maritime industry came into force on the 1 January 2020. The International Maritime Organization’s (IMO) 0.5 per cent global sulphur cap changed everything. Simultaneously the IMO is pushing towards reducing greenhouse gas emissions by 50 per cent by 2050, compared to a 2008 baseline.
That’s not all. The IMO has sped up the phase three requirements of the Energy Efficiency Design Index (EEDI) and moved them forward from 2025 to 2022. This means that several new build ship types - including gas carriers, general cargo ships and LNG carriers - will need to become significantly more energy efficient.
In addition, shipping companies are also positively working towards adopting the United Nations Sustainable Development Goals (SDGs). In particular goal number 13 – Climate Action: To take urgent action to combat climate change and its impacts. The IMO and other international bodies are continuously working towards integrating climate change measures into national policies, strategies and planning.
Sustainability is key to our industry evolving for the better. And, by having accurate data to base your decisions on, businesses can unlock opportunities to maximise fuel efficiency. Hull performance monitoring and analysis is one solution on offer to shipowners and operators. This enables continuous efficiency improvements by reducing fuel consumption and associated CO2 emissions.
USING INNOVATIVE SOLUTIONS
Advanced hull coatings have long been applied to commercial vessels to reduce the impact of marine fouling and corrosion, as well as increasing efficiency. Biofouling remains a significant cause of operational losses for shipowners, operators and managers. Frictional resistance caused by fouling correlates directly with increased drag, reduced hydrodynamic performance and, in turn, increased fuel consumption. At its worst, fouling typically increases the engine power needed by close to 20 per cent over five years. The result is more environmental emissions and a significant upswing in costs.
But in order to understand a vessel’s performance - and for a hull coating to deliver tangible returns - here is where measuring operating results is key. Hempel, the worldwide coatings manufacturer, launched a hull performance system - SHAPE (Systems for Hull and Propeller Efficiency) to enable shipowners and operators to compare their hull solutions with simple and transparent data.
STEP BY STEP
SHAPE uses in-service performance KPIs to track long-term trends that generate important data for fact-based decisions. This information offers a whole new level of fuel-efficiency intelligence. Shipowners and operators can now make informed, sustainable and competitive decisions to put their business operations in the best position.
SHAPE is a structured process which can be applied to every vessel regardless of the age, size or operating pattern. As a first step, individual speed power reference curves are established based on the vessel’s operating patterns and its location. Once established, the relevant data is collected and reviewed to clean and retain key information. This means removing any data from extreme operating conditions and accounting for any environmental factors. This allows Hempel’s analysts to calculate the vessel’s precise speed loss and to establish four KPIs. The KPIs relate to all stages of the vessel’s operational life, its dry-docking performance, inservice performance, the maintenance triggers and the maintenance effects on vessel speed. The resulting detailed data can then be used to make changes that deliver fuel efficiency, tailored to each vessel’s specific needs. Using this methodology those savings can be refined and delivered year-on-year
Our industry is changing for the better with more focus on environmental and sustainable initiatives. By being able to effectively manage operational performance through the use of hard data, shipowners and operators can make intelligent decisions to play their part in this. Reducing fuel consumption by maximising a fleet’s productivity and efficiency is one part of the puzzle to a better future.
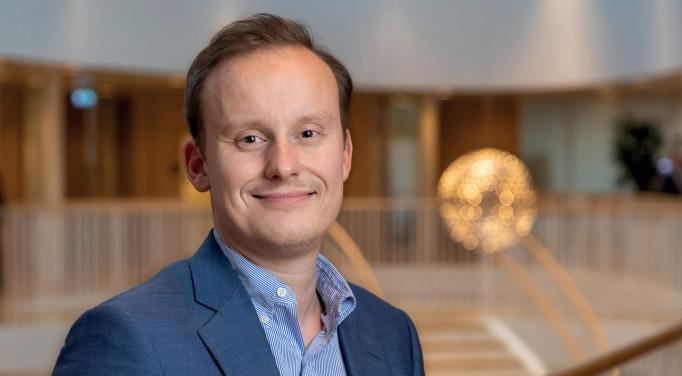
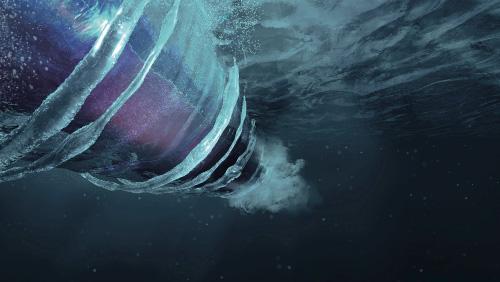
8 Andreas Glud,
Group Segment Manager, Dry Dock at Hempel stressed the importance of measuring results
8 SHAPE combines
elements of hull and propeller effi ciency optimisation, delivering expert advice and solutions to ship operators
HOW BOXES WRAPPED UP GLOBAL TRADE
Any history of containerisation should start with Malcom McClean. By inventing the container, he started a global business that has transformed the way we live
Some of the popular mythology is incorrect: McClean did not invent the concept of containerised shipping and it was not an instantaneous ‘eureka’ revelation. But what Malcom McLean did was to introduce standardisation, make it work on a grand scale and realise that shipping’s underlying priority was to move cargo. In the 1930s, when he was running a trucking company, shipping was very ineffi cient at that: ships could spend as long in port loading and unloading as they spent at sea.
In 1937 he spent nearly a whole day sitting in his truck’s cab in the port in Hoboken, New Jersey, as he waited to deliver some cotton bales. He later told the magazine American Shipper that “it struck me that I was looking at a lot of wasted time and money. ... The thought occurred to me ... that it would be easier to lift my trailer up and, without any of its contents being touched, put it on the ship.”
But it was not until 1955 that he and an engineer, Keith Tantlinger, developed the container that we know today, with its corrugated sides and twistlock. Although McLean patented it, Tantlinger persuaded him to make the design freely available, helping to ensure its adoption.
He was not the only one exploring the potential of containerising cargo. In November 1955 - independently of his activities - the first purpose-built container vessel, Clifford J. Rodgers, carried 600 containers between North Vancouver and Alaska for transhipment to rail. It was on 26 April the following year that McClean put 58 of his containers onto a converted tanker, Ideal X, which took them from Newark, New Jersey, to Houston in Texas, marking the start of the first container shipping company.
From such humble beginnings, the vessels and trade have evolved. The largest container ships in 2019, the MSC Gülsün class, were rated at 23,756TEU but have since been surpassed by the 24,000TEU HMM Algeciras class. These container ships embody the same factors that influenced McLean: size, speed and efficiency. Their development over the past 64 years has been underpinned by world trade, making them equally vulnerable to its variations. The current coronavirus pandemic has also left its mark on both production and demand, leading to many ‘blank’ sailings in container operators’ schedules.
Containership size has grown in distinct steps, with the Panama Canal as a limiter. Panamax box ships arrived in the mid-1980s, carrying around 4,000TEU, and little changed for about a decade until post-Panamax ships of around 6,600TEU appeared, relying on growing world trade to make them economical.
When the canal’s larger locks opened in 2016, a new reference benchmark was set and the largest ship so far through the canal is Costamare’s 14,424TEU Triton, in service with Evergreen on its Far East-US East Coast service, which made its first transit in May 2019.
Away from the canal, MOL became the first operator to put a 20,000+TEU vessel into service, in March 2017, with the delivery of its 20,150TEU MOL Triumph. It was trumped just two weeks later by Madrid Maersk, rated at 20,568TEU, a figure that has been surpassed several times in the three years since.
At this rate of growth, the Suez Canal’s capacity comes into view as the next constraint. If that were breached, a Malaccamax design of around 30,000TEU could follow, but ports might baulk at investing in suitable infrastructure.
Container ship speed and efficiency have been intertwined over the years, with high speeds being beneficial because of their high cargo values. But the years following the 2008 world economic crisis ended that upward curve, with many young and fast container ships being laid up for long periods while older ones went for scrap.
De-rated engines and slow steaming became the norm for existing ships and once newbuildings were specified for lower service speeds, the days of fast box ships was over. MSC’s online data sheet for MSC Gülsün, for example, lists its speed as “varies; capable of 21kts”; in 2010, that top speed would have been classed as ‘slow steaming’.
These lower speeds, however, play their part in making larger ships possible; if container ship speeds had not fallen, finding a suitable engine for today’s huge ships would be difficult. MSC Gülsün, for example, is powered by an MAN B&W 11G95ME-C9.5 engine, which has a top rating of 75,570kW, although it operates at 66,650kW in this installation, while HMM Algeciras is propelled by a MAN B&W G95ME-C10.5 engine.
Future containership evolution, then, will depend on a balance between size and speed, with an eye on emissions and efficiency. Perhaps we have now reached the largest practical size, but engine designers and naval architects have delighted in disproving predictions in the past.
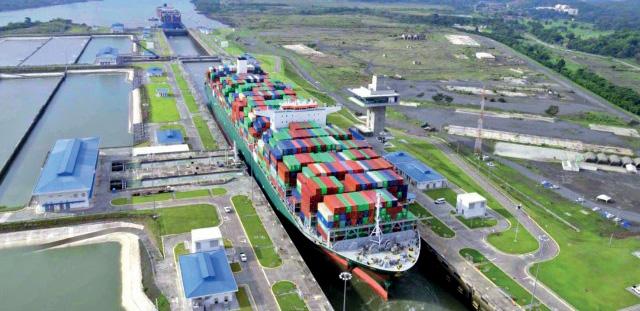

8 Triton is the
largest ship to have passed through the enlarged Panama Canal locks
8 Malcom McClean
understood the real purpose of shipping
Credit: Wikimedia
MAN R&D CHIEF PREPARES FOR MULTI-FUEL FUTURE
Brian Østergaard Sørensen, Vice President, Head of R&D 2-Stroke Business, at MAN Energy Solutions, looks forward and discusses the challenges of choosing between research priorities
QFrom an engine design and operation perspective, what do you think have been the most important
technological innovations during your career?
AAlthough the introduction of electronic controlled engines into the two-speed portfolio occurred relatively recently, it has been the foundation of many of the recent developments that have occurred in the industry, such as emissions control, advanced engine control and monitoring solutions and the new generations of gas-fuelled engines. Taking a wider view, electronic controlled engines also laid the foundations for the introduction of digitalisation solutions into the marine propulsion market. [The development of the ME-concept engine by MAN Diesel engineers in the early 2000s - as well as the launch of the 32/44CR all electronic four-stroke - represented advances in electronically controlled fuel injection].
Looking ahead, digitalisation is a rapidly developing area. It is a common thread running through all aspects of our business - it touches everything from how we sell spare parts to how we utilise data within R&D. It is inevitable that it will increase - and I expect it to alter our business model in the future, whether that is through subscriptions for higher value services, condition based monitoring or other solutions.
QAs a master mariner who subsequently qualifi ed in mechanical engineering, how do you see the future
role of the internal combustion engine? Will it remain the prime mover for marine transportation in the future?
ATwo-stroke engines offer unchallenged efficiency, and we expect to achieve further advances in the coming years using combined cycle technologies (such as Organic Rankine Cycle solutions), for example. I believe that two
Image courtesy of MAN Energy Solutions

stroke engine technology will remain the prime mover of deep-sea shipping. However, the range of fuels will change in the future as we leave a monofuel world - LNG, methanol and perhaps ammonia might play a larger role in the fuel mix. The fuels being consumed may also vary according to the route and operating profile, which will increase demand for fuel flexibility among ship operators.
Without a doubt, we expect to see an evolution in the integration of power systems aboard vessels. Staying abreast of developments in battery and fuel cell technology, for example, is paramount to the success of MAN as a company.
QYou mention combined cycle technologies as an interesting area for research. Looking at MAN engines
after a century of continuous research, are we approaching a limit for how much more effi cient the engines can become?
AIf you had asked engineers a decade ago, they would have told you current efficiencies were unachievable! We are working towards further improving the efficiency of our portfolio of diesel fuelled engines, and will be targeting improvements in engine management, via our new engine control system, as well as broader digitalisation improvements. This is a key area of focus for MAN.
We are continuing to pursue research into combined cycle technologies (such as power turbines, steam turbines or Organic Rankine Systems) to utilise waste heat recovery as a means of improving the efficiency of the engine. We are also looking at other ways of integrating our engines into other shipboard systems - such as using excess air to drive other systems. The growth in refrigerated alternative fuels, such as LNG, has also opened up the area of ‘waste cold recovery’ from fuel gas supply systems, for example.
8 MAN Energy
Solutions’ plans to launch its ME-GA low-pressure engine platform by Q1 2022 remain on track
QGiven the pace of technological development, how do you choose which areas to focus your research? A Compared with the world of 15 years ago, we have to choose from a wide range of different research areas including advanced combustion and spray injection modelling technology; improvements in digitalisation techniques; engine monitoring and control and emerging energy management issues.
It is important to prioritise and maintain focus when undertaking research projects. (The Motorship noted that MAN ES successfully developed its new low pressure ME-GA engine platform under a compressed development timetable. The engine remains on schedule for the early 2022 commercial launch deadline.)
Commercial considerations also need to be borne in mind: we need to develop engine platforms that are scalable. If we utilise common components on engine platforms as far as possible, this minimises the number of variants.
In addition, 10 or 15 years ago, we were dealing with a monofuel world. As a supplier to the industry, we have to prepare for the emergence of new fuels, so that we have the solutions on the shelf when the customer needs them. These new fuels, and combinations of fuels, all have different characteristics compared with diesel fuel, which has knockon implications for engine research. To give one example, methanol and ammonia are both low lubricity fuels that have poor combustion characteristics.
Luckily, we don’t have to do everything ourselves. There are areas where we benefit from collaborations with partners. We have established links with a number of technical universities in pre-commercial and ‘blue sky’ research areas. For commercial development work, we have long-standing relationships with several engine manufacturer licensees, while we also see increasing opportunities for research with industrial partners.
What are the next areas for improvements in effi ciency?
AHaving successfully lowered SFOC in our latest engine platforms by increasing combustion pressures, we are looking at finding the sweet spot between improved fuel efficiency and minimising emissions. Finding the correct balance is a challenge.
Sequential injection, an established technology on common rail engines, permits each injection valve to fire individually. The advantage from an engine designer’s perspective is that the fuel mix can be modified dynamically, permitting very rapid changes in fuel air ratios. The sequential injection technology ensures an additional tool in our toolbox for securing that we can hit the sweet spot between engine efficiency and engine emissions. We have recently added sequential injection to our portfolio on our largest engines.
As the development of new engines with increased combustion pressures are not only increasing mechanical stresses but are also increasing heat load of combustion chamber components, we are of course also focusing on development of new materials with improved resistance against mechanical and thermal loading to secure improved/ enhanced reliability of combustion chamber components
Further all the new control strategies including the new control strategies for engines operating as dual fuel or triple fuels are increasing the requirements for control hardware, we will begin rolling out a new engine control system, TRITON, across our electronically-controlled engine portfolio over the next few years. The TRITON engine control system will be introduced as a standard solution on new electronically controlled engines and will offer a number of benefits.
These benefits include enhanced control. This will be fundamental to two new efficiency solutions that MAN ES is launching: sequential injection and gas optimisation.
However, as I mentioned, we are also seeing the impact of digitalisation solutions on efficiency. Improved access to engine data will improve our insight into the performance of our engines. The latter will lead to improvements in longterm engine performance as we get improved access to operational data from our engines.
This focus on improved reliability is part of our mediumterm goal to eliminate unplanned maintenance between dry docks by 2030. In other words, we want to develop platforms that are more efficient, without an reduction in operational reliability.
There is another aspect to operational efficiency. Our customers will also be able to achieve greater efficiencies by using data. You can have a highly efficient car, but the fuel efficiency you achieve will vary depending on how you drive it. [Early in his career, Sørensen spent a period as deck officer at sea]. Improved monitoring of components and engine performance help us provide support to crew members and colleagues located ashore.

QFinally, how do you feel the recent Covid-19 situation has aff ected customer interest in alternative fuels? A It is perfectly true that the recent Covid-19 situation is likely to have an impact on customers’ appetite for investing in the short-term. But I don’t think that the recent interest in fuel efficiency measures has just been a function of high fuel prices. The drivers of the decarbonisation agenda are regulations, and social pressures - and ultimately a wider energy transition that is starting to occur. e receiving increasing enquiries from across the world - from both large and small owners, as well as brokers and financiers - who want to understand the technology. At MAN, we have an important role to play in making the technology available. We can show the way towards what is possible and can also support the transition.
8 Brian Østergaard
Sørensen is a master mariner who subsequently qualifi ed in mechanical engineering
HULL FORM OPTIMISATION DROVE SUPER-ECO ULTRAMAX GAINS
A hull form optimisation project using Computational Fluid Dynamics (CFD) helped a new class of Ultramax bulk carriers to achieve best in class fuel consumption
In the spring of 2017 Cyprus-based shipowning group Lemissoler launched a project to improve the effi ciency of an existing Ultramax bulk carrier design. The project involved close collaboration between Lemissoler, the Chinese shipbuilder New Times Shipbuilding, Shanghaibased naval architects SDARI and classifi cation society ABS. The project resulted in a new class of 65,000 dwt super-eco Ultramax bulk carriers, LEM65.
The initial discussions encompassed the vessel’s main particulars, including cargo intake which was agreed prior to commencing the optimisation of the vessel design, with work initially focussing around the initial hull form proposed by SDARI.
HULL FORM OPTIMISATION
The optimisation work involved the ABS Energy Efficiency team in Copenhagen and the Houston-based CFD team, which utilised a range of CFD models and a proprietary optimisation tool in the ABS Large CFD Cluster.
The optimisation of vessel hull form is a fine balance between minimising the power requirement without compromising either the cargo intake in terms of available deadweight nor the tons per centimetre (TPC) immersion for commercial reasons.
Christian Schack, who leads the ABS Energy Efficiency team, commented on the need for close dialogue between the project partners. “In order to optimise a vessel hull form and propulsion arrangement it is paramount to understand the intended operation and the intent of the owners. Thus we always seek to have as close a dialogue as possible to understand the ‘pain points’ for the owner, enabling us to optimise the vessel as far as possible.”
The work was carried out in multiple rounds to ensure that each element of the hull form was carefully evaluated and optimised. in total more than 5,000 CFD simulations were carried out. After each round of optimisation, the results were presented to the joint team and discussed to ensure that the data were consistent and did not breach any of the preagreed requirements.
As a part of the optimisation process, open-water data for the specified Kappel propeller design from MAN Energy Solutions was provided in the final optimisation of the aft of the ship, to ensure the propeller had the best operating conditions with an even inflow of water to the propeller disk.
The final optimised hull form was subsequently evaluated using the same procedures as were applied for the baseline hull design in order to quantify the performance gains. It was found that the required power - averaged over the operational profile - could be reduced by 4.4% and that at the same time, the required power at the design condition was reduced by 5.6%. The power savings corresponded to a saving in fuel oil consumption of about 4.3% over the operational profile, which in this case consisted of four speed and draft combinations and of about 6.2% at the design condition.
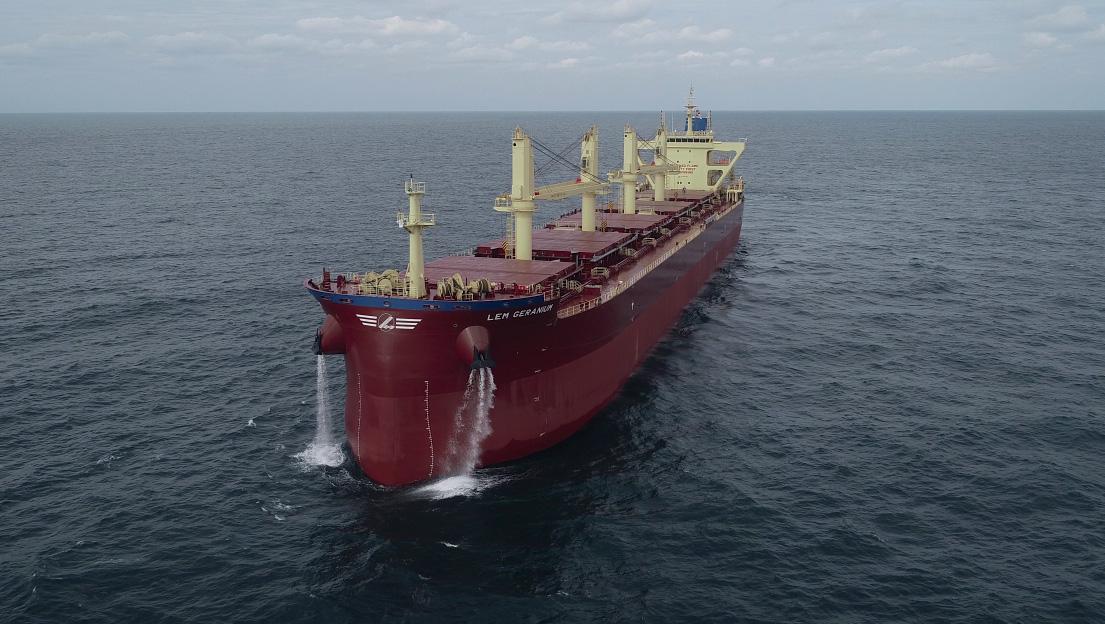
INNOVATIVE FEATURES
In addition to the process of rigorous hull form optimisation, the vessel design encompasses a series of other innovative features to reduce energy consumption, including: 5 Optimised propulsion system with well selected main engine and Kappel propeller delivered by MAN Energy Solutions to minimize fuel consumptions and eliminate vibrations;
8 The fi rst two
LEM65 class super-eco Ultramax bulk carriers have entered service
5 Propeller boss cap fin to reduce the hub swirl and improve propulsion performance; 5 Fan duct to improve flow into the propeller disk and in turn reduce the power requirements; 5 Optimized skeg to ensure course-keeping ability without adding additional resistance; 5 Aerodynamic accommodation design to minimize air resistance; 5 Super-eco electric cranes co-developed by Lemissoler and manufacturing partners; 5 Wide installation of LED fixtures to reduce the lighting power consumption 5 Optimized energy generation and consumption throughout the vessel.
The CFD simulations were verified by model tests performed at model basin China Ship Scientific Research Center (CSSRC) in Wuxi, China.
Several model tests were performed to evaluate the impact of multiple combinations of Energy Saving Devices (ESD), until the optimal results were obtained at the prevailing operational profile delivered by Lemissoler.
The rigorous tests confirmed that the optimisation had produced the expected results and provided a high level of confidence to the joint team about the final performance of the vessel series when built.
During the model tests the EEDI condition was also tested and this allowed the preliminary EEDI to be calculated.
The preliminary EEDI results showed that the unique design was able to meet proposed Phase 3 of the EEDI rules which define 30% lower emissions than the baseline.
PRINCIPAL PARTICULARS - MV Lem Geranium
Length, overall 199.90m Breadth, moulded 32.26m Depth, overall 18.50m Draught, scantling 13.50m Deadweight 64,900 Main engine 7G50ME-C9.6 Class ABS
8 Christian Schack noted that
the results of the optimisation process translated into SFOC savings of about 4.3% over the operational profi le
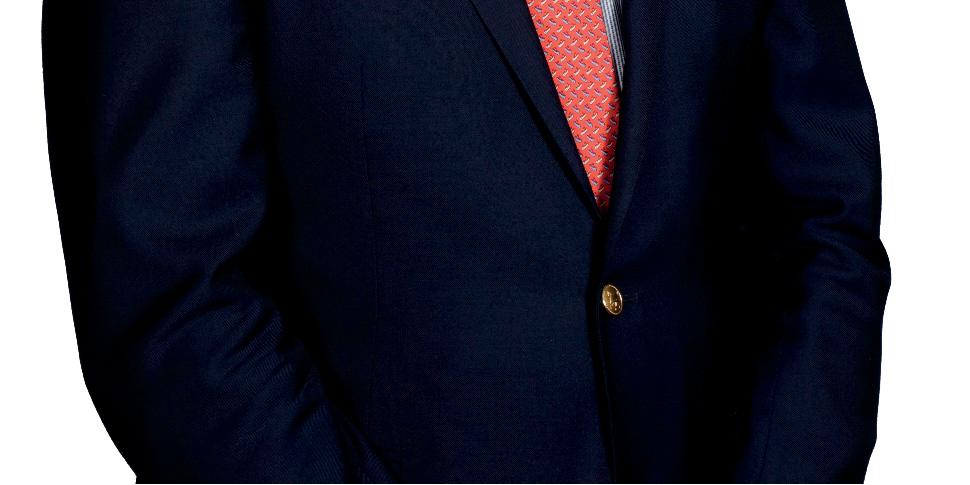
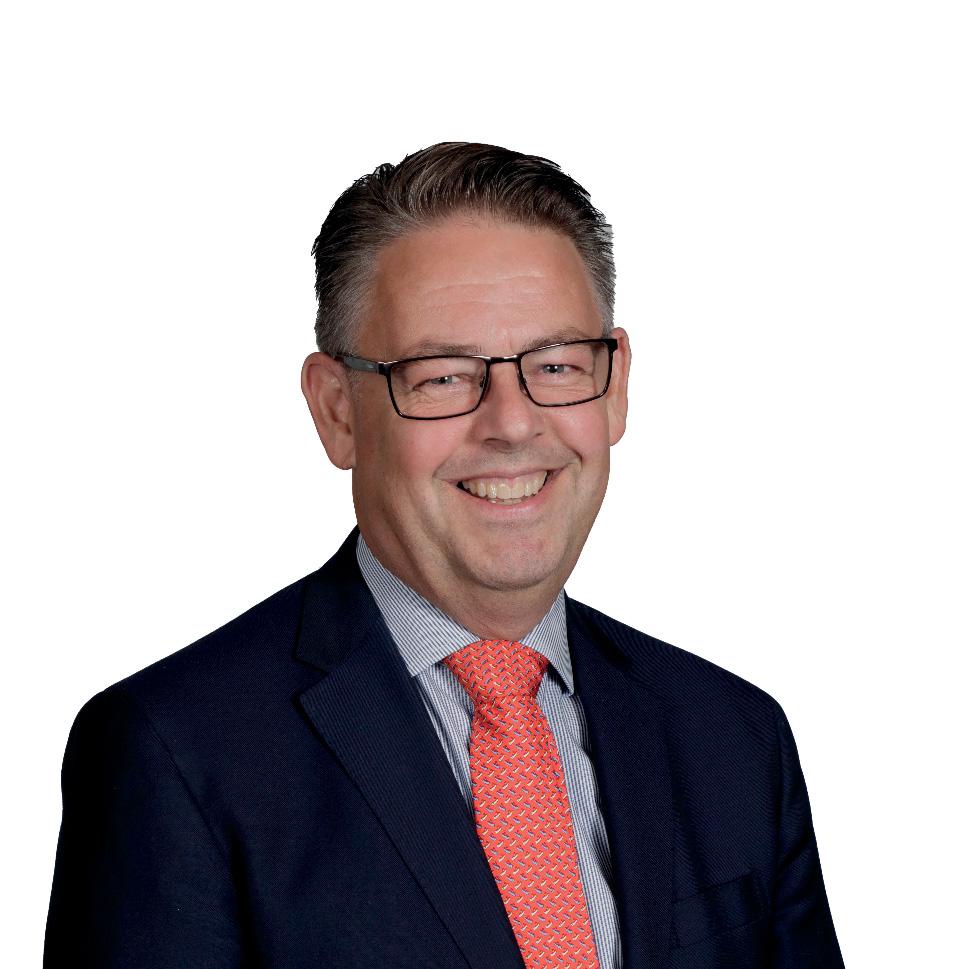
SEA TRIALS AND OPERATIONAL EXPERIENCEPERIENCE
The sea trials of the first vessel MV Lem GeraniumLem Geranium in late November 2019 confirmed that the vessel’s hat the vessel’s performance was in line with expectations from the ctations from the hull form optimisation and model tests. The sea sts. The sea trials allowed the calculation of the e final final EEDI for the vessel, confirming the he results from the model tests. All ll results have been further verified d following the deliveries of MV Lem m Geranium in early December 2019 9 and MV Lem Marigold in March 2020.
Lemissoler Technical Director Dimitris Solomonides said: “Our operational experience with our so far two deliveries MV Lem Geranium m and MV Lem Marigold has been n exceptionally good and could even n say exceeded our expectations when n we initially pitched the ‘LEM65’ 65’ concept to ABS and SDARI.”
www.navalia.es
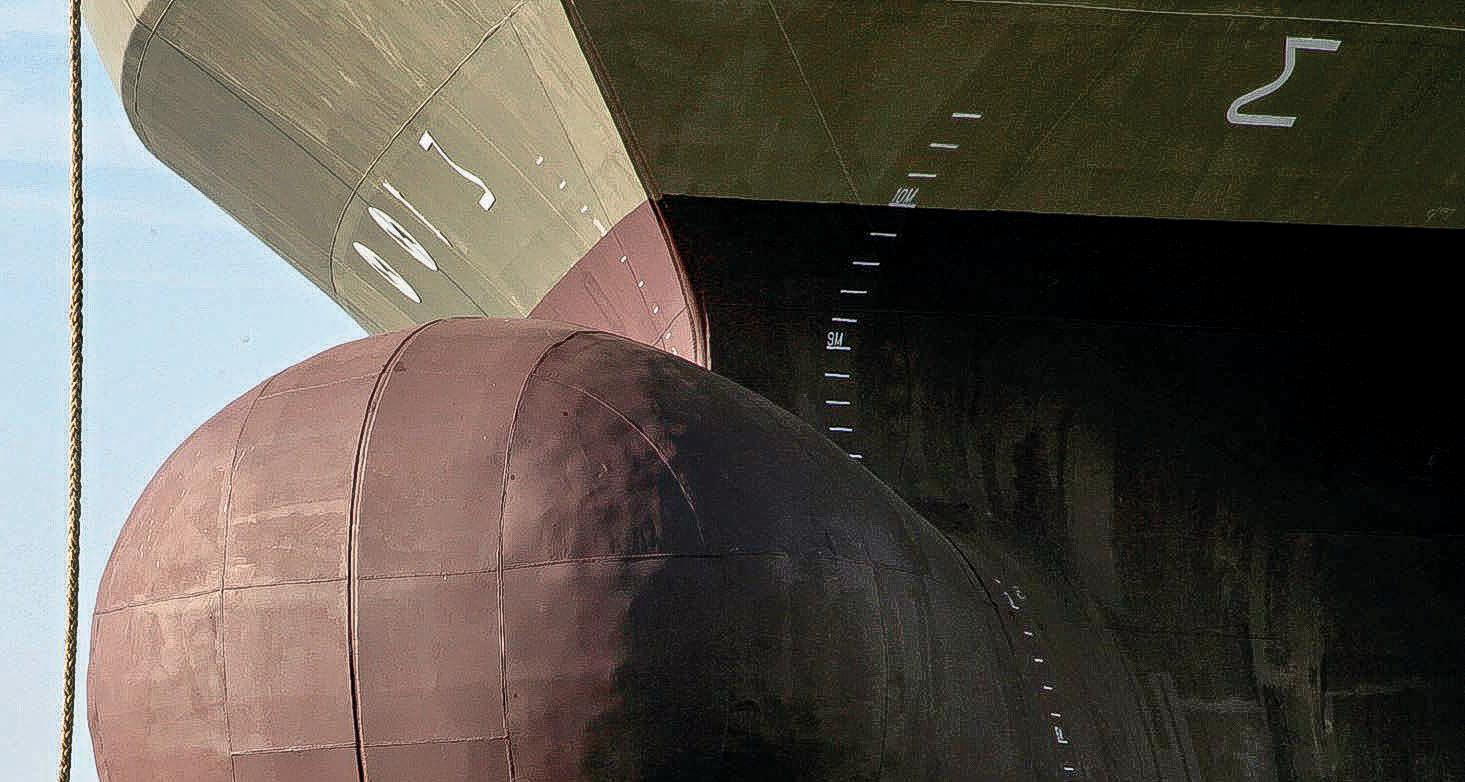
ANOTHER LANDMARK IN SHUTTLE TANKER OPERATIONS
An innovative breed of DPST, powered by LNG and liquefi ed cargo vapour, promises competitive advantages as Norwegian environmental controls tighten, writes David Tinsley
Transferring crude oil on a year-round, intensive basis from North Sea and Norwegian Sea off shore loading points to refi neries and terminals in dedicated, purpose-designed tankers is an especially demanding sphere of the business, requiring a very high level of capital intensity, technical and operational know-how.
To ensure the dependability, safety and efficiency of the cargo handling and transportation service sustained in often extremely arduous conditions, proven systems and technologies employed are of an order that render shuttle tankers among the world’s most sophisticated crude oil carriers.
A new generation is hoisting the benchmarks for economic performance and emission control. Following the recent introduction of the first of Teekay’s E-Shuttle Tanker series, two vessels built for a joint venture of South East Asian and Norwegian interests have made their debut under charter to Norwegian energy group Equinor (formerly Statoil). The 128,000dwt Eagle Blane and Eagle Balder integrate a raft of advances intended to provide the kind of long-term ‘sustainability’ and operational flexibility necessary to the logistics of ultimately ensuring the competitiveness of Norwegian-produced oil.
Each twin-skeg tanker is powered by low-speed engines using LNG as the primary fuel, and is additionally endowed with the capability to capture, liquefy and burn 100% of the volatile organic compound (VOC) emissions issuing from the cargo as supplementary fuel. The adoption of a more efficient system of dynamic positioning (DP) and a direct current (DC) shaft generator solution in combination with LNG dual-fuel main and auxiliary machinery and VOC recovery is expected to save up to 3,000t of fuel per annum compared with ‘conventional’ DP shuttle tankers of similar size.
Credit: AET

Eagle Blane and Eagle Balder have been constructed on the Korean peninsula by Samsung Heavy Industries to the account of AET Sea Shuttle, a joint undertaking of Singapore-based owner and commercial operator AET and the Norwegian shipping company Arendals Dampskibsselskab (ADS).
Immediate and sustained employment for the new tonnage has been secured by way of seven-year charters to state-owned Equinor. The assignment will entail crude oil liftings from fields on the Norwegian Continental Shelf, in the North Sea, Norwegian Sea and southern Barents Sea, as well as the UK Continental Shelf.
Technical management is in the lap of another Norwegian firm, OSM Maritime. Project oversight was afforded by EagleStar, the MISC Group’s integrated marine services arm, jointly owned by MISC Berhad of Malaysia and subsidiary AET and created from the in-house shipmanagement divisions of the respective companies.
Tankers designed for bringing shipments direct from the offshore fields have an operating profile typified by sailing patterns involving short voyages and frequent cargo handling, and need to deal with especially large amounts of VOC. Venting and flaring of VOC, vapours which naturally arise from the crude oil during loading and transportation, is not only environmentally harmful but also represents a loss of cargo volume over the course of a voyage.
The dual-fuel specification for the Eagle Blane and Eagle Balder embraced not only each ship’s two propulsion engines but also the two principal auxiliaries, applying arrangements that allow operation on a mix of LNG and VOC.
Consequently, the vessels are expected to emit 85% less SOx, 98% less particulate matter (PM) and 93% less black carbon particulates, as well as 98% less NOx than DP
8 New-generation
off shore crude oil loader Eagle Balder uses vaporised cargo in the fuel mix
equipped shuttle tankers burning heavy fuel oil. The design allies with IMO’s target to reduce carbon energy per work transport unit by 40% against 2008 baselines by 2030, and halving of CO2 emissions by 2050.
In gas mode, the low-pressure, dual-fuel two-stroke engines fulfil IMO Type III requirements as to NOx, obviating the need for exhaust gas aftertreatment, and comply with the global sulphur cap. Furthermore, the intended trading areas necessitate adherence to the Gothenburg Protocol. Implemented this year, the edict laid down by the UN Economic Commission for Europe (UNECE) has set a cap on VOC emissions.
According to AET’s president and CEO, Captain Rajalingam Subramaniam, who is also chairman of joint venture AET Sea Shuttle, “These vessels are proof that environmental sustainability and commercial viability can coexist, and are also testament to the fact that operational performance does not have to be sacrificed in the pursuit of reducing emissions. The goal was always to leverage the combined experience of AET, ADS and Samsung Heavy Industries to develop vessels that really push the boundaries in what is possible in North Sea DP operations, and to prove the value of LNG dual-fuel solutions in the energy shipping segment.”
Each tanker’s propulsion installation is based on two sevencylinder models of the X52DF engine designed by Winterthur Gas & Diesel (WinGD), driving two Kawasaki controllable pitch propellers. The rating diagram for the 7X52DF extends from a nominal maximum continuous output of 10,430kW/105rpm at the R1 rating point to 6,510kW/79rpm at R4.
The low-pressure gas admission principle adopted in the X-DF series is conducive to the blending of VOC with natural gas, since condensation of heavier hydrocarbons can be avoided.
Two years ago, a test campaign was carried out at the Trieste engine complex in north east Italy whereby an X-DF unit was run on an NG/VOC mix. This demonstrated the engine’s capabilities under various load scenarios with up to 20% VOC in the fuel ratio, and confirmed performance throughout transfers from pure natural gas to a combination with VOC, as well as when switching to diesel mode and back again. While efficiency criteria were maintained, it was shown that NOx emissions remained significantly below IMO Tier III levels when burning an NG/VOC mix.
The VOC recovery system, devised and supplied by Wartsila, involves a two-stage process. The heavier fractions are removed in the first stage, and medium fractions from propane to hexane are condensed to liquid state in the second stage, forming the liquefied VOC (LVOC). The fuel supply line for the LVOC comprises a deck-mounted, pressurised storage tank, the evaporator, and LNG/VOC mixing unit and control. The fuel mix can be ingested in the two main dual-fuel auxiliaries, nine-cylinder Wartsila 34DF engines, as well as the main engines.
ABB’s proprietary power and energy management system (PEMS) enables the generators to operate at variable speeds in optimal fashion. The arrangements are in stark contrast to traditional alternating current (AC) systems where the gensets run at fixed maximum speed irrespective of the pertaining, onboard power demand, leading to excessive engine wear over time and poor fuel efficiency at lower loads. Together with PEMS, ABB’s integrated control and monitoring system provides the crew with means to manage the vessel’s steaming and DP operations at the lowest possible specific fuel consumption.
The two-stroke engines act as the primary source for power using ABB’s Onboard DC Grid shaft generator solution for all operational modes. The combination of the Onboard DC Grid and the generators on the two-stroke shaftlines has facilitated a reduction in conventional gensets, cutting fuel consumption and emissions.
Augmenting the variable pitch main propellers and highlift rudders, the underwater wherewithal for the precise manoeuvring and station-keeping demanded of an offshore loader takes the form of a single Kawasaki tunnel thruster in the bow, and three retractable, azimuthing thrusters, two forward and one aft.
The ships feature the latest (5th) generation of bow loading systems, allowing greater connecting angles, so as to extend the offshore operational window in conditions where shuttle tankers would normally be hard-pressed to get the loading line connected. The arrangements are intended to enable the hose to be married up with the offshore platform or buoy in a significant wave height of 4.5m, at an entry angle of up to 110 degrees.
Eagle Blane received her DNV GL class assignment on February 7 this year, and Eagle Balder on March 13.
In what constituted one of the first endorsements of the dual-fuel concept by the crude carrier sector, AET commissioned two Aframax tankers equipped with WinGD two-stroke X-DF engines in 2019. Both vessels, Eagle Brasilia and Eagle Bintulu, were also products of the Samsung complex at Geoje Island.
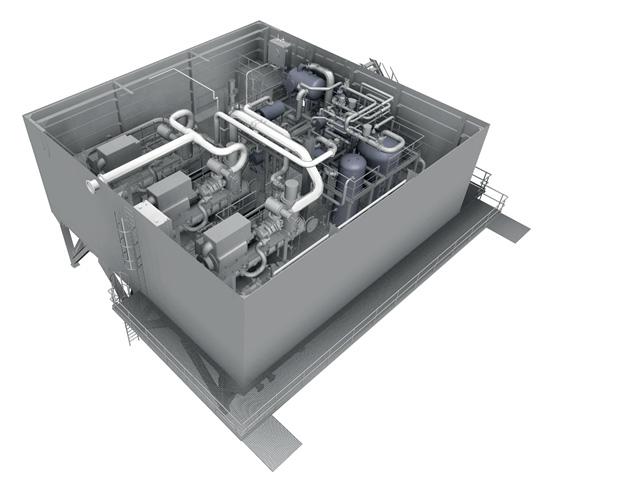
PRINCIPAL PARTICULARS - Eagle Blane
Length overall 276.66m Length bp 265.02m Breadth, moulded 46.00m Depth 23.40m Draught 15.30m Gross tonnage 85,745t Deadweight 128,427t Main engines 2 x WinGD 7X52DF Auxiliaries 2 x Wartsila 9L34DF Class DNV GL Class notations 1A1 Tanker for oil, BIS, Bow loading, BWM(T), CCO, Clean(Design), COAT-PSPC(B, C), COMF(C-3, V-3), CSA(FLS2), CSR, DAT(-10degC), DYNPOS(AUTR), E0, ECA(SOx-A), ESP F(A,M,C), Gas-fuelled, HELDK(S,H), LCS, NAUT(AW), Recyclable, RP(2,50%), TMON(oil-lubricated) Flag Norway
8 Using energy
recovered from Wärtsilä’s VOC Recovery unit (pictured), shuttle tankers can lower their CO2 emissions by around one-third
LARGE MEDIUM SPEED POWER
The June 1970 issue of The Motorship included two special supplements (of which more later) so there was rather less general news and feature material than was the norm 50 years ago.
The main editorial opinion piece concerned insurance - something which, from the technical side, still today tends to be regarded as a cargo and business issue. Our predecessors were bemoaning the fact that, despite the numerous technical advances that contributed to the overall safety of the vessel, premiums seemed to be based solely on ship size, with perhaps a small discount for a highlyassessed owner with a good record. One suggestion was that owners were being discouraged from investing too highly in safety features because the consequent extra cost would reduce profitability and attract higher insurance premiums because of the high capital cost of the ship. “Technical considerations are apparently irrelevant,” the editors wrote, quoting the safety benefits of multiple engines. “Underwriters are unwilling to negotiate even a derisory allowance for twin-screw propulsion.”
A leading article described successful engine performance results of the Finlandia, an 8168gt Baltic ferry, the largest and fastest of its type. Powered by four Wärtsilä-Sulzer 9ZH40/48 medium-speed engines, each of MCR 4,950bhp at 430 rpm, arranged in pairs, each pair driving a CP propeller through a reduction gearbox, the ship had performed reliably for over two years, running on HFO. The writers had been able to witness the cylinder covers and valve gear on one engine being opened up for inspection, and everything was in good clean condition with little evidence of wear. Operator Finland Line said that initially, these being the first of a new engine design, problems were expected, and a couple of early piston ring breakages were cured by a change to chromehardened upper rings; similarly three main bearings were replaced after water contamination from a defective heat exchanger. Because Finlandia could run happily on three, or even two, engines, maintenance could be carried out while the vessel was in service.
The same engine design had been chosen for a new order to be built at Wärtsilä, for three 36,000 hp icebreakers for export to the Soviet Union, the biggest single order ever placed in Finland. The ships were to use a diesel-electric propulsion system, each vessel
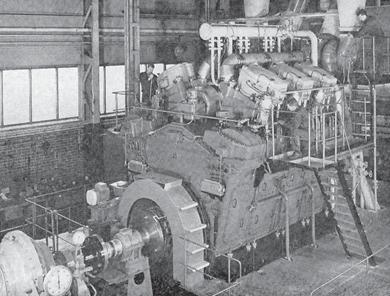
8 Prototype UDAB 6-cylinder engine on the Götaverken
test bed
8 British Rail’s new Irish Sea container ships could carry
184 standard 20ft boxes
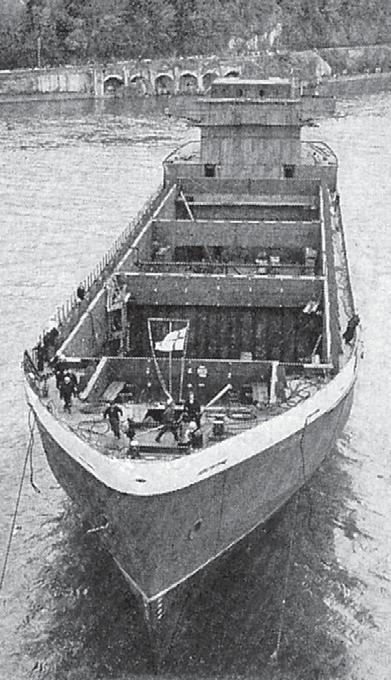
equipped with nine 12-cylinder ZH40/48 main engines and seven Wärtsilä 814TK auxiliaries.
The main ship description concerned the second of two container ships for Irish Sea service linking Holyhead with Dublin and Belfast. The ships were built at the Verolme Cork dockyard, and powered by twin Mirrlees 2,100 bhp medium speed engines. At a mere 184 TEU they seem minute compared with today’s leviathans. Restricted draught at Holyhead meant the vessels drew only about 4m, while they were fitted with bow rudders rather than bulbous bows as manoeuvrability was considered more important than speed.
The first of the supplements explored the ‘Clyde’ ship series in depth. This was a design proposed by Upper Clyde Shipbuilders, as a standard ship with wide appeal, along similar lines to the Liberty Ships and the various replacements. The Clyde class was intended to add efficiency and versatility to these basic designs, even if it was slightly more expensive. It could be built for containers, bulk cargo or general duties, and powered by a Sulzer 5RND68 two-stroke engine.
The other supplement devoted 44 pages to the Swedish UDAB engine, a medium speed unit for applications where high horsepower was required from compact dimensions. Its designers anticipated that the engine was the future of container and ro-ro ship propulsion. Power output of up to 20,700 bhp was expected from the largest, 18-cylinder version. MOTORSHIP THE
INSIGHT FOR MARINE TECHNOLOGY PROFESSIONALS
The international magazine for senior marine engineers
EDITORIAL & CONTENT
Editor: Nick Edstrom editor@mercatormedia.com
News Reporter: Rebecca Jeff rey rjeff rey@mercatormedia.com
Correspondents
Please contact our correspondents at editor@motorship.com Bill Thomson, David Tinsley, Tom Todd, Stevie Knight
Production
Ian Swain, David Blake, Gary Betteridge production@mercatormedia.com
SALES & MARKETING t +44 1329 825335 f +44 1329 550192
Brand manager: Toni-Rhiannon Sibley tsibley @mercatormedia.com
Marketing marketing@mercatormedia.com
EXECUTIVE
Chief Executive: Andrew Webster awebster@mercatormedia.com
TMS magazine is published monthly by Mercator Media Limited Spinnaker House, Waterside Gardens, Fareham, Hampshire PO16 8SD, UK
t +44 1329 825335 f +44 1329 550192
info@mercatormedia.com www.mercatormedia.com
Subscriptions
Subscriptions@motorship.com or subscribe online at www.motorship.com Also, sign up to the weekly TMS E-Newsletter 1 year’s magazine subscription £GBP178.50 UK & EURO Post area £GBP178.50 Rest of the World
© Mercator Media Limited 2020. ISSN 0027-2000 (print) ISSN 2633-4488 (online). Established 1920. The Motorship is a trade mark of Mercator Media Ltd. All rights reserved. No part of this magazine can be reproduced without the written consent of Mercator Media Ltd. Registered in England Company Number 2427909. Registered offi ce: Spinnaker House, Waterside Gardens, Fareham, Hampshire PO16 8SD, UK. Printed in the UK by Holbrooks Printers Ltd, Portsmouth, PO3 5HX. Distributed by Mail Options Ltd, Unit 41, Waterside Trading Centre, Trumpers Way, London W7 2QD, UK.

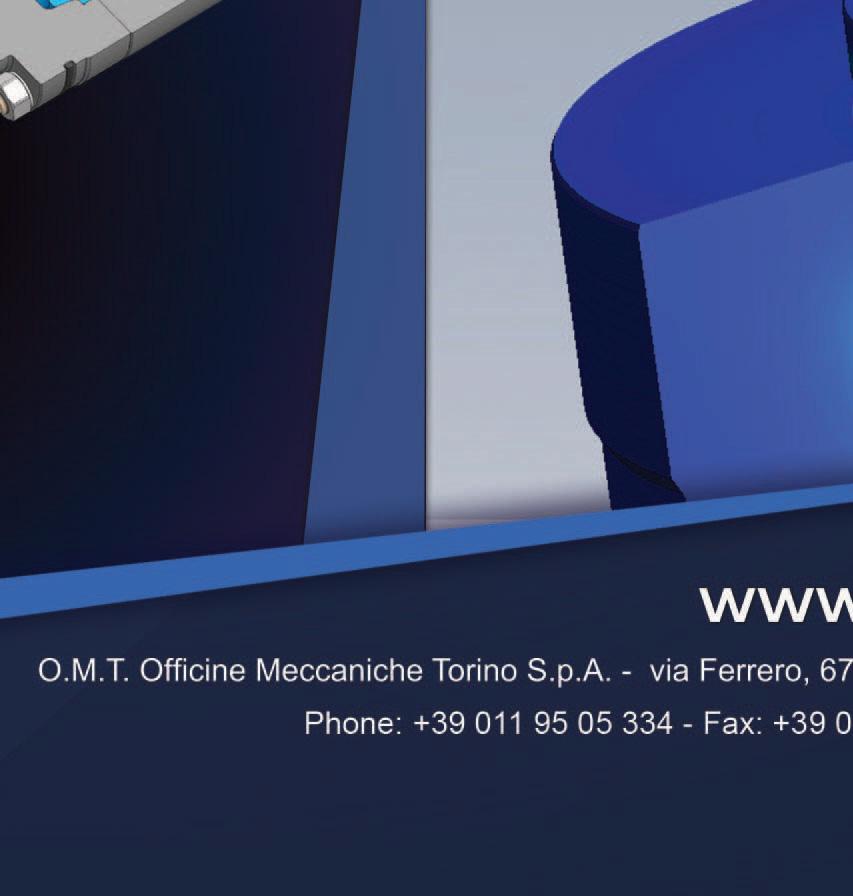

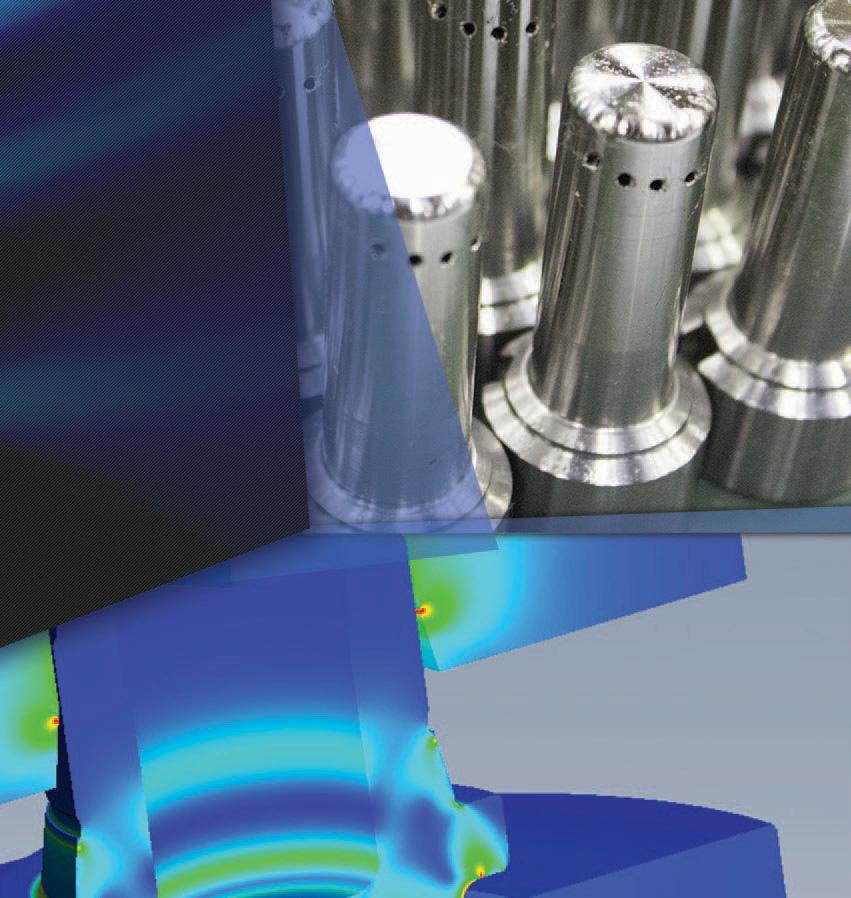
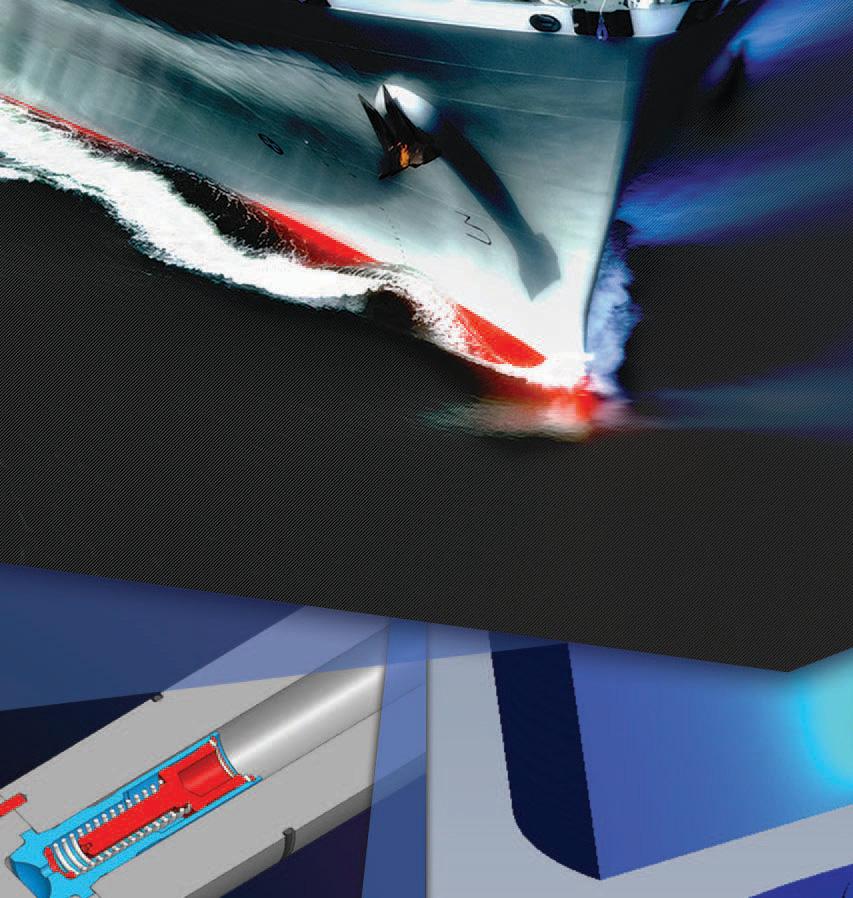
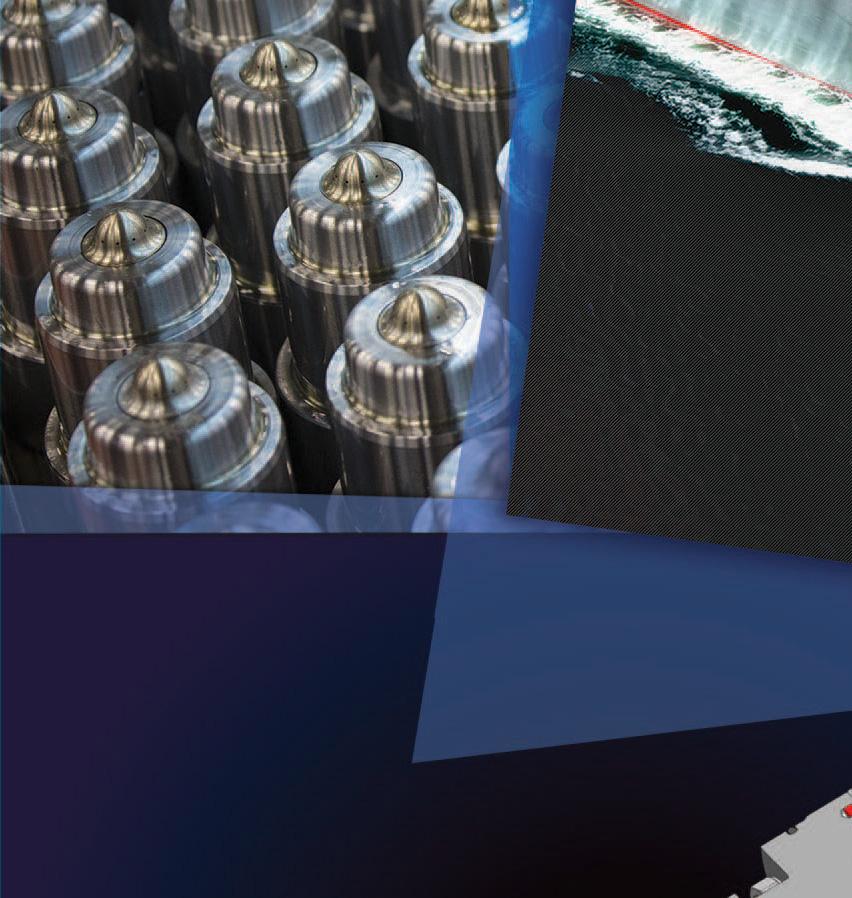
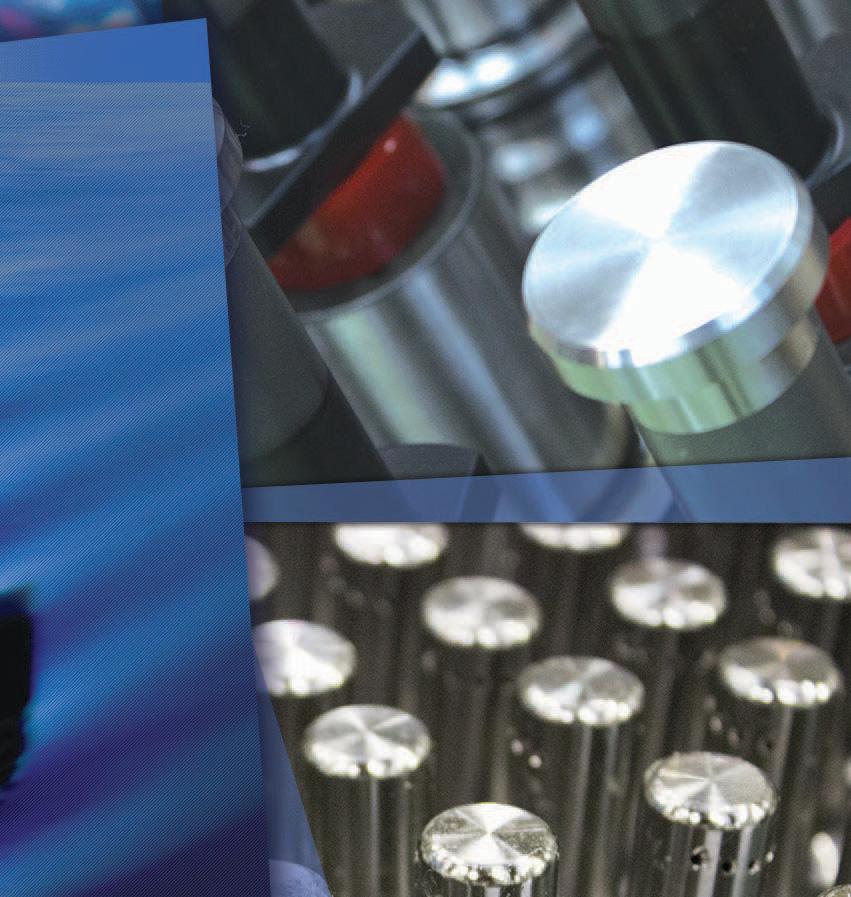

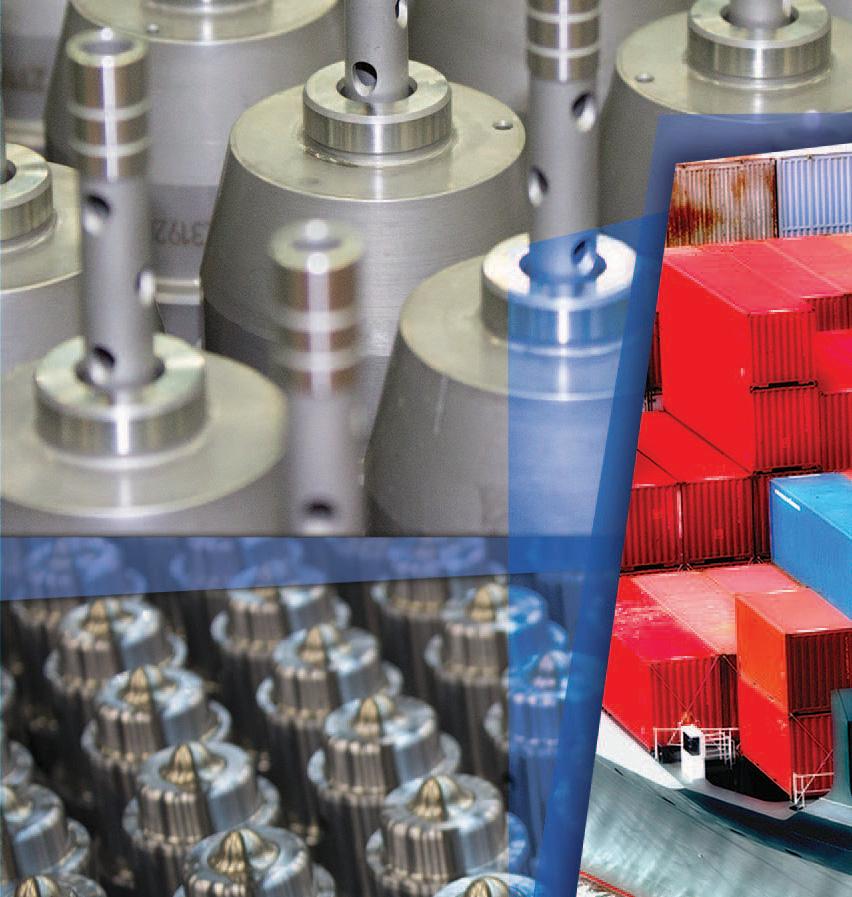


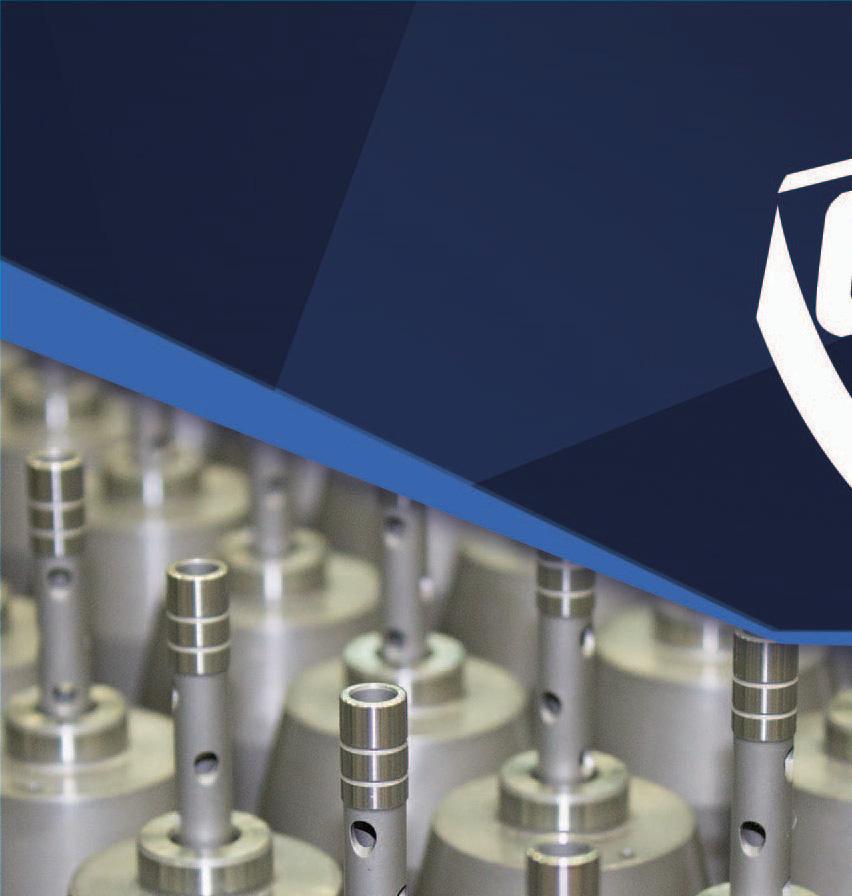