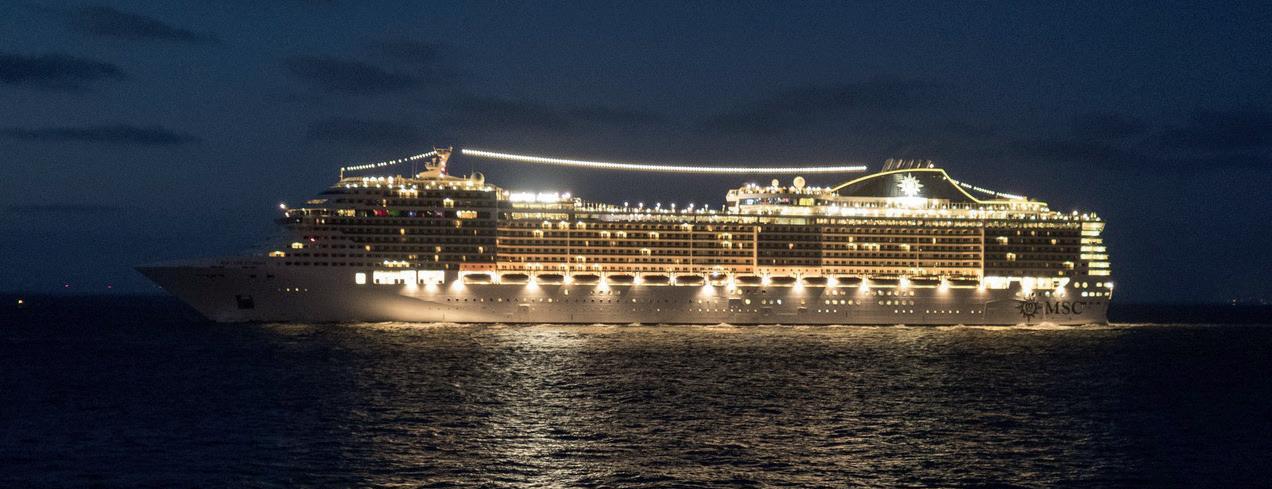
3 minute read
Fuel flexible injection
TUNING THE ENGINE THROUGH THE AIR INTAKE
Combustion optimisation usually involves tricky remodelling of fuel injection parameters... but there is another approach - through the air flow
“Currently all engines are static on the air intake side, you are limited to the ambient air available and the size of your turbocharger,” explains Marc Sima of FuelSave. “This technology gives you a whole new dimension to play with, as it adds new variables.”
It is also safe and resilient: a failure won’t interrupt engine operation.
The development has come about from another look at two slightly problematic chemistries. “People have individually played around with mixing hydrogen and methanol with the fuel supply - and both have drawbacks: hydrogen leads to slightly earlier ignition which means you can be in danger of engine knock, while methanol tends to delay it, potentially creating combustion issues,” says Sima.
But “there is a way to make the most of the synergy”, he says.
“First of all, water and methanol together in fluid form extends the premix phase,” says Sima, “while an introduction of small amounts of hydrogen and oxygen gives you a more complete burn”. However, taken alone this raises NOx emissions, created when oxygen and nitrogen fuse: “So, injecting the liquid again can mitigate this effect, by lowering the combustion temperature,” he explains.
Therefore, the FS+ system works by timed injection of hydrogen, oxygen or methanol mix at three different locations along the air intake - something that varies slightly from engine to engine - with enough pressure to reach the combustion chamber effectively. The necessary control is achieved by feedback from engine load and charge air pressure. As a result, the overall effect is “to enhance both volumetric and thermal efficiency”, Sima explains.
Further, he adds that it also raises the efficiency of the turbocharger, “which is suddenly able to push more air into the engine for the same amount of energy consumed as it’s cooler, and therefore denser”.
Importantly, the system is, at its heart, adaptable: “We aim to optimise the stoichiometric mix at every load phase,” he underlines: “In general we can configure the system for even higher fuel economies and cost savings or higher emission
Photo:pxhere
reduction as there is a trade-off; by default, we choose the best combination that performs within the emission tiers for which the engine is certified.”
Looking at it in more detail, the FS technology is fine-tuned for each application to yield the greatest payback in the load range for which the engine’s been optimised.
What it doesn’t need is a huge hydrogen tank. Instead, the FS+ system creates it on the spot by electrolysis, which safely splits water into H2 and oxygen. “This syngas generator has a price penalty, but it has several other advantages: as we produce and consume the hydrogen only on demand, there’s not so much worry about storage and handling, plus the related safety concerns ,” says Sima. That avoids some of the physical bunkering restrictions and regulatory issues. However, it’s worth noting that these gases won’t be premixed. “We separate the hydrogen and oxygen for safety reasons, injecting them independently,” he explains.
The methanol, however, has to be bunkered, so one element of the onboard kit is a storage tank, sized according to bunker intervals. Still, it’s only about 3% to 5% of the total fuel throughput, so - for the sake of round numbers - a ship with an annual bunker demand of 10,000 tonnes per year will use 300 tonnes of CH3OH: given a monthly bunkering call pattern, an installation would only need to find room for a 25 tonne capacity methanol tank onboard - something that shouldn’t prove too onerous.
Overall, the footprint is rather neat: the brains of the system, the control cabinet and PLC, is connected with double-walled, barrier monitored piping. It is ideally located close to the engine to minimize the installation costs and cut down response lag: the last part of the package is a modest, 1m3 service tank.
Interestingly, the system can be fairly small-scale: in fact it was first tried and proven onboard trucks before being applied to stationary power generators. This showcases another interesting point: it can be designed for each specific use case and sized according to the engine being supported.
Following these initial applications, it was installed on an
8 Cruise ships