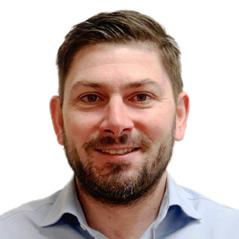
16 minute read
Session 3 The Motorship Awards
SESSION 3
The Motorship Awards
MICHAEL NORTH
Sales & Marketing Manager for Norway & Iceland, Lloyd’s Register
BIOGRAPHY
Michael North is Lloyd’s Register’s Sales and Marketing Manager for Norway and Iceland. He leads LR’s commercial activities in the area and has many years of experience in the Marine industry having started his career as an Electro-Technical Officer sailing on cruise vessels before moving into shore-based sales and project roles. Originally from the United Kingdom, he started working regularly in Norway in 2007 and then moved permanently to Oslo in 2009 and now is also a Norwegian citizen.
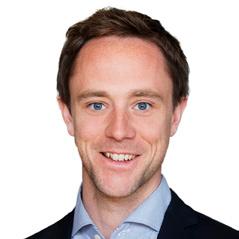
HENRIK ANDERSSON
Head of Sustainability, Hoegh
BIOGRAPHY
Head of Sustainability, Henrik Andersson. Henrik has had numerous positions within Höegh Autoliners, having worked for the Norwegian based company for since 2014. He was responsible for fuel efficiency, risk management and worked with technical fleet management and environment before assuming the position as Head of Technical Development two and a half years ago.
In 2022 Henrik became Head of Technical Development and he is overall responsible for the green transition and technical development of the fleet.
The Aurora Class - the future of deep sea shipping
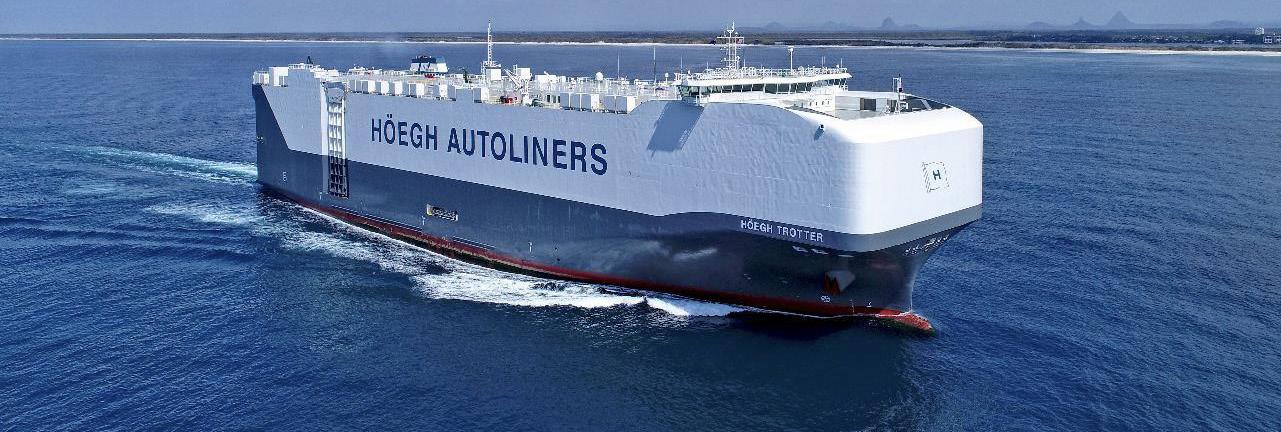
The steps on our path to zero…
CO2
CO2
neutral CO2
2008-2020
Reduced carbon intensity by 38% (EEOI 2008-2020):
The New Horizon series delivered On offer to a2015-2016,ll cu arestomthe ers largest and greenest PCTC vessels in the world (emit only half of the CO2 per car transported compared to a standard car carrier). Modifications to existing vessels (new bulbous bows, optimised propellers, hull cleaning for improved energy efficiency. 2021-2022
Carbon neutral voyages available to all customers:
Simple commercial proposition, including certification processing Use of biofuel where supply and costs permit Supplemented with ‘real’ carbon capture projects within
Höegh’s own business system through RVC 2023-2025
Reduction in customer emission footprint from newbuilds:
Delivery of first, zero carbon ready, vessels in new-building program with Multi-
Fuel engine Partnerships with sustainability focused OEMs Continued development of commercially attractive green proposition
Net Zero carbon
2025-2030
Availability of net zero carbon shipping:
Delivery of first zero carbon vessels from 2025 Conversion to new technologies Replacement of 80% of existing owned fleet by 2030 2040
Achieving net zero :
Own and operated fleet approaching zero carbon emissions
Bulb optimization improved overall efficiency by 5%
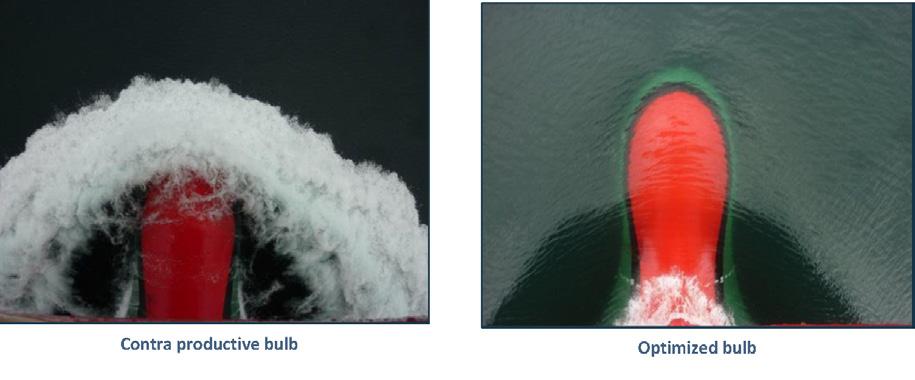
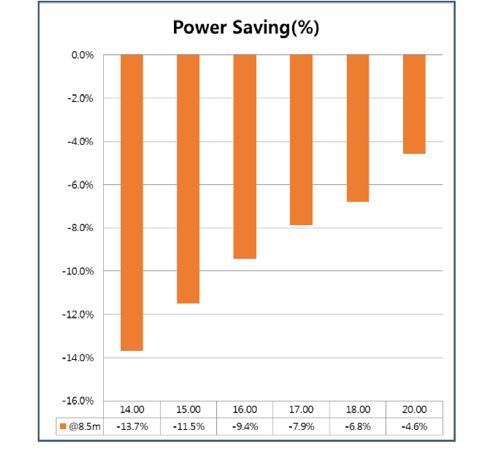
Continuous focus on fuel efficiency has resulted in major emission reductions
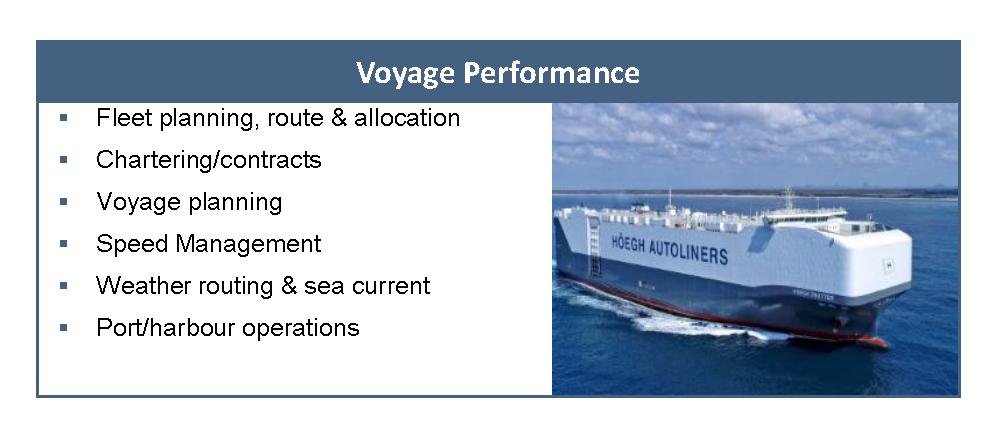

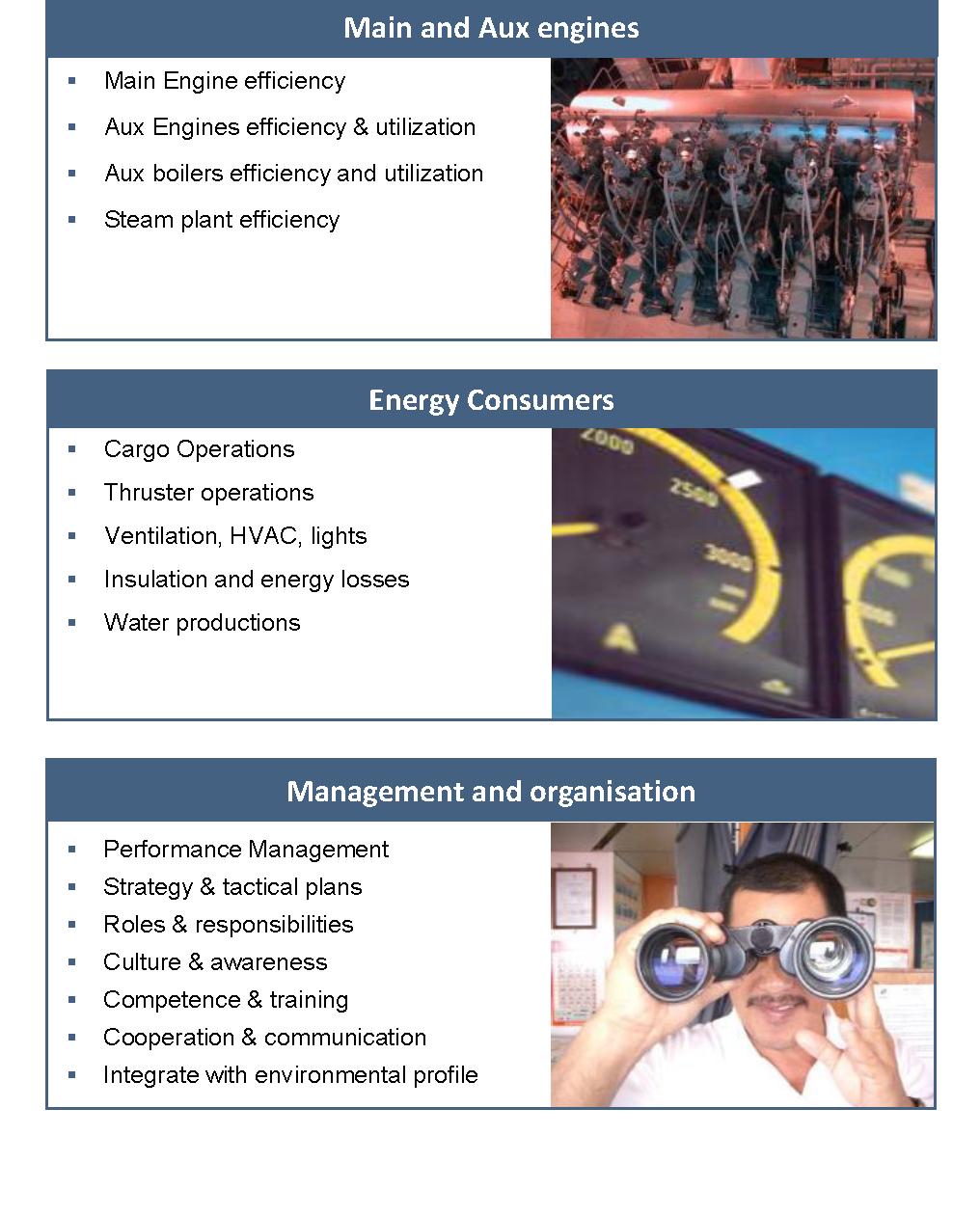
Since 2008 Höegh Autoliners has improved CO2 emissions per Nm and car by 38%
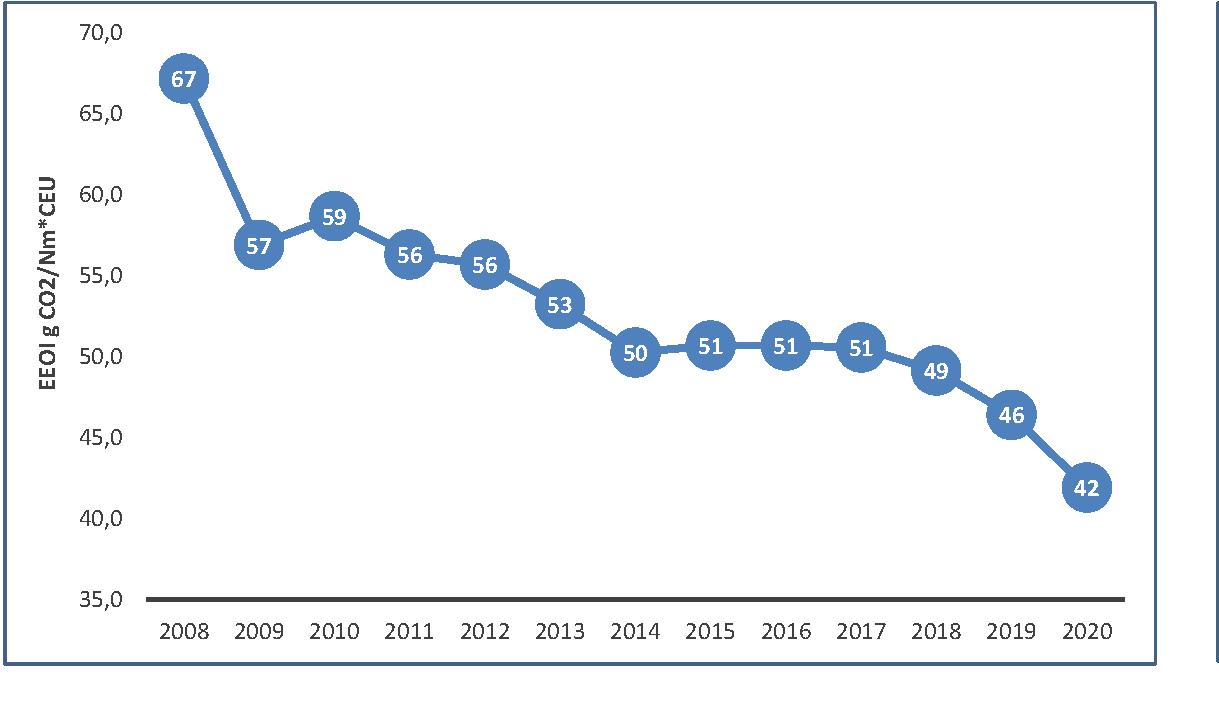
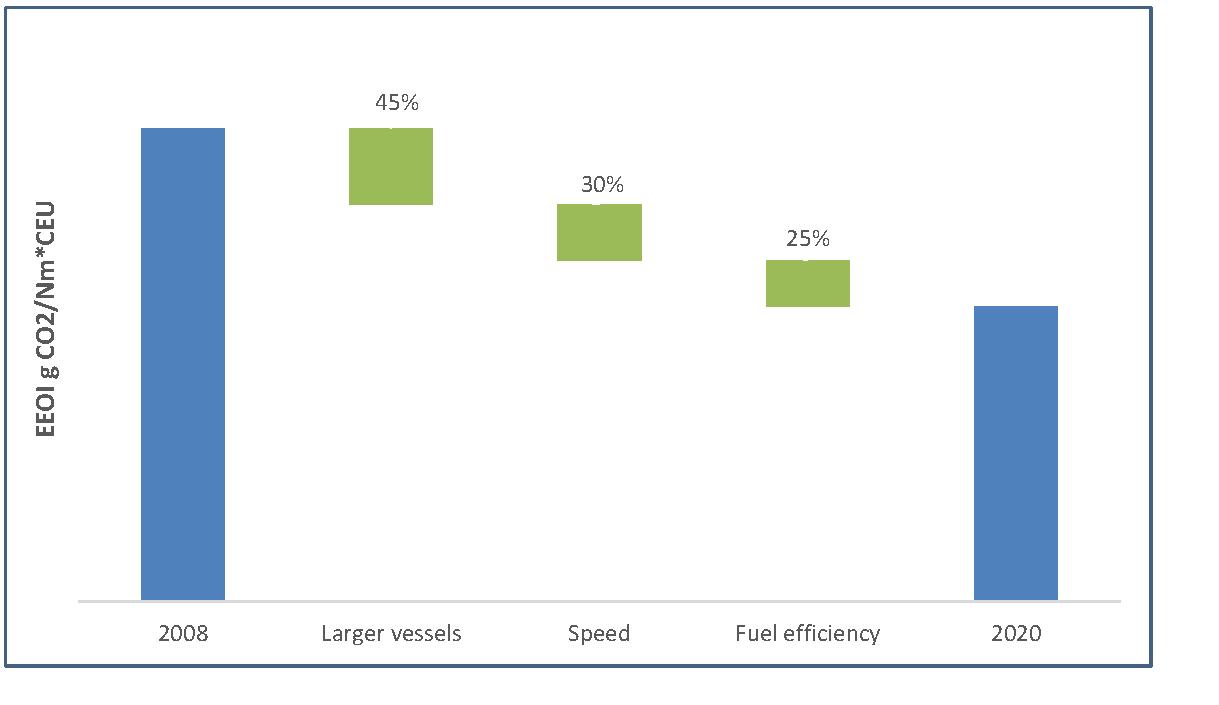
Improved efficiency goes hand in hand with cost saving
The fleet performance is ahead of IMO’s fleet target, however continued improvement will be necessary
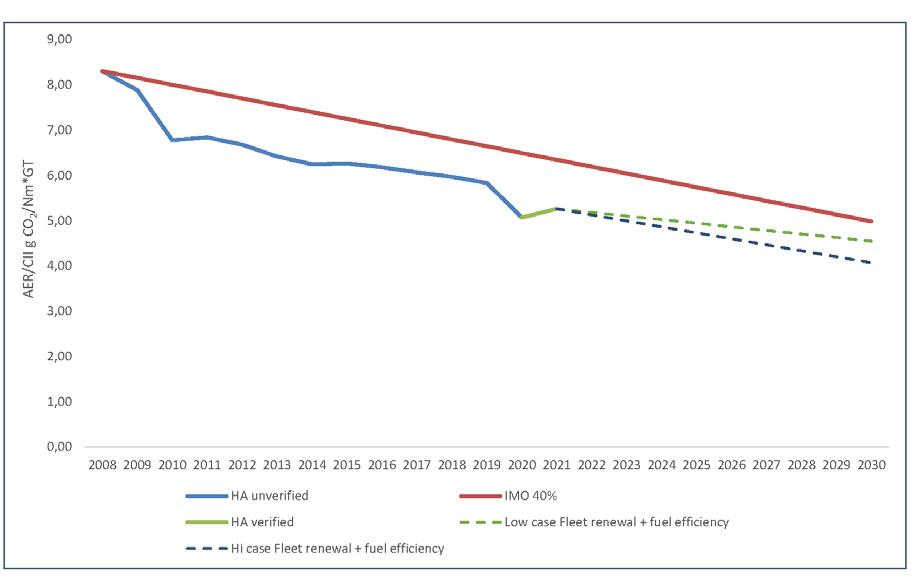
Note: Effect of shorepower connection is not accounted for
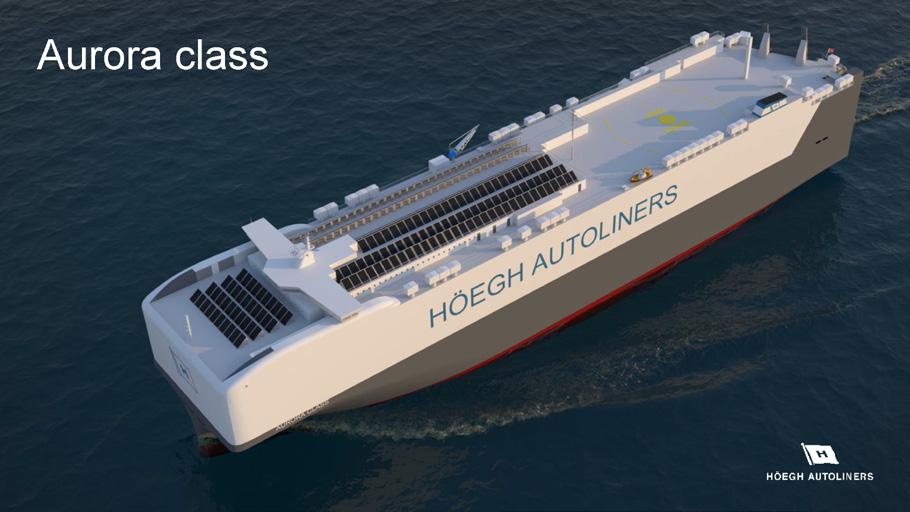
The Aurora class: GREENER – BETTER – SMARTER
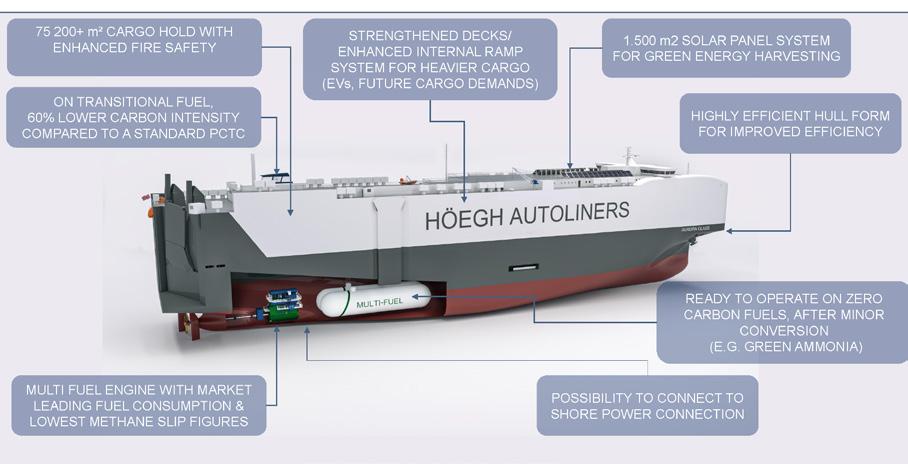
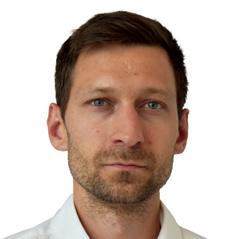
KRISTAIN MOGENSEN
Principal Specialist and Promotion Manager, MAN Energy Solutions
BIOGRAPHY
Kristian Mogensen is working as a promotion manager for MAN-ES in Copenhagen, where he assist and support various of stakeholder in the Marine Sector. He started his career as a seagoing Marine engineer, later went ashore to work with energy efficiency in a shipping company. In 2015 he started in MAN-ES 2-Stroke operation department. During his five years in the operation department Kristian was the author of serval service letters and operational guidelines, as well as responsible for the lubrication oil strategy for the LNG burning engines.
Technologies from MAN Energy Solutions for carbon capture and transport
How to deal with unavoidable emissions has been a central question in the race to achieve climate goals. Certain industries such as concrete and cement simply have very limited alternatives to their methods. In fact, cement production alone, which emits large amounts of carbon dioxide (CO2) into the atmosphere from the chemical reaction that turns limestone into cement, is responsible for 8 percent of all CO2 emissions – four times the amount of Germany. This means innovative new approaches are urgently needed – chief among them: carbon capture, transport and storage. At MAN Energy Solutions, we believe that developing technologies that support this approach is a key part of the journey that will achieve deep decarbonization of the sectors that matter most.
The Norwegian Government’s Longship project aims to demonstrate that carbon-capture technology can be applied to larger industrial plants and set a new standard for future industrial projects. From the summer of 2024, the HeidelbergCement Norcem plant near Oslo, Norway will be the first to use the Carbon Capture Heat Recovery technology (CCWHR®) developed by MAN Energy Solutions and Aker Carbon Capture to capture 400,000 tons of CO2 annually, corresponding to 50% of its overall emissions. The gas will be compressed, liquefied and subsequently transported by Northern Lights by use of the new carriers powered by MAN B&W ME-GI engines, before it is safely and permanently stored 2,600 meters under the seabed on the Norwegian continental shelf.
In the following, we will touch upon the technologies from MAN Energy Solutions that support this groundbreaking project.
Capturing, compressing and liquefying CO2
HeidelbergCement Norcem will be the first to use the ‘Carbon Capture Heat Recovery’ technology (CCWHR®) developed by MAN Energy Solutions and Aker Carbon Capture. A new process allows the heat emerging from the compressor system to be recovered and used as steam to meet approximately one third of the total heat demand from the Aker Carbon Capture plant. Consequently, the system solution demands significantly less energy compared with conventional carbon-capture technologies. The scope of work by MAN Energy Solutions includes the supply of an electrically-powered compressor train – type RG 63-7 with integrated CCWHR® technology – which allows the compression heat of the recovery compressor to be exploited. The steam generators cool the CO2 mixture between the compressor stages and generate steam that is in turn used for capture. Thanks to the use of innovative digital tools, the compression system for the CCS application has been significantly simplified.
Keeping emissions low while transporting liquefied CO2
As part of the first phase of the CO2 transport and storage infrastructure development, Northern Lights is building two dedicated CO2 carriers. Naturally, the green credentials of these two vessels have been carefully examined, and the primary fuel will be liquefied natural gas (LNG) to keep emissions low. Therefore, the two 7,500 m3 carriers will be equipped with MAN B&W 7S35 ME-GI dual-fuel engines. Each engine will feature MAN Energy Solutions’ proprietary exhaust gas recirculation (EcoEGR) system, which – in combination with the high pressure diesel cycle engine technology – allows for high efficiency and only negligible methane slip.
The MAN B&W ME-GI (Gas Injection) engine has set new industrial standards for two-stroke propulsion engines aboard vessels such as LNG carriers, container vessels, car carriers and bulk carriers – and now also for LCO2 Carriers. The ME-GI engine provides ship-owners and operators with a peerless solution within environmentally friendly and high-efficiency twostroke technology, with close to zero greenhouse gas emissions – also when it comes to methane slip. Consequently, the ME-GI engine has quantified and guaranteed methane slip levels in a range from 0.20 – 0.28 g/kWh over the engines’ load range. In order to optimize the performance of the engines even further, our EcoEGR technology is applied. It is based on more than ten years of service experience with our EGR design, which has enabled both refinements and optimizations of the technology. The latest design is a perfect example of such optimization, where the latest generation EGR is employed on the our dualfuel ME-GI engine. EGR has become an integral tuning tool for all our low-speed engines and its maturity will allow further exploration of the potential for optimizing engine performance well into the future.
While LNG will be the primary fuel for the two vessels, other technologies, such as a windassisted propulsion system and air lubrication, will be installed as well to reduce carbon intensity further.
Moving big things to zero - together
While the carbon capture technologies are developing, the shipping industry has an obligation to push forward to ensure that the necessary infrastructure offers solutions that support deep decarbonization. The dedicated CO2 carriers will potentially set new standards for CO2 shipping on coastal trading routes and lead the way for a new, interesting ship segment – a segment which is expected to grow significantly in the coming years, as carbon capture, transport and storage from shore based emitters rises. At MAN Energy Solutions, we are proud to contribute to this development, by engineering solutions for the sectors that matter most.
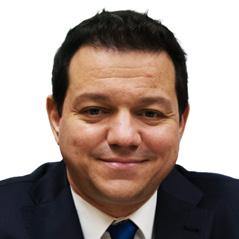
STAM ACHILLAS
BIOGRAPHY
Stam Achillas is the Head of Business Development & Sales, 2-Stroke Fuel Conversions at Wärtsilä, where he’s spearheading the commercialisation and business growth of 2-stroke decarbonisation solutions globally.
Growing up in a seafaring family and having graduated from the Merchant Marine Academy in Greece, Stam started his career on board vessels as a marine engineer officer. Following further education in Mechanical & Marine Engineering, he entered the field of diesel engine development with Cummins and later led production and service departments in the defence industry with Kraus-Maffei Wegmann. As a senior project manager with WinGD (formerly Wärtsilä Switzerland) and subsequently with AVL in Austria he led the development and productization of 2-stroke and 4-stroke diesel and dual fuel engines for marine, power generation and rail applications. Stam transitioned into more commercial roles with ABB Turbo Systems (currently Accelleron) as the global Head of Product Management, Low-Speed Turbocharging before re-joining Wärtsilä.
Patrick Rebecchi
Program Manager for Two-Stroke Future Fuel Technology, Wärtsilä
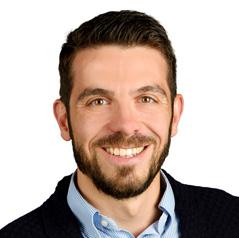
As a Program Manager, Patrick leads several technology projects to develop retrofit solutions for the safe and reliable implementation of future fuels in existing two-stroke marine engines. Patrick’s career in the marine sector began at Wärtsilä in 2012 as an Engine Performance Expert, playing a key role in the development of the first 2-stroke dual-fuel engine. He later led projects in marine engineering at WinGD and energy infrastructure before moving to the Wärtsilä Services organization in early 2022. Patrick holds a PhD in Combustion Control Theory from the University of Stuttgart, a master’s degree in mechanical engineering from the ETH Zurich and a Certificate of Advanced Studies in General Management from the University of Applied Sciences in Business Administration Zurich.
A better way to convert two-stroke engines for LNG and future fuels
ABSTRACT
Fuel conversions can be an effective way of reducing emissions and ensuring regulatory compliance long into the future. But the cost and complexity of converting vessels can be a significant barrier. A new two-stroke future fuels conversion platform deploys innovative fuel injection technology to significantly reduce integration complexity, capital cost and onboard footprint, bringing the environmental advantages of LNG and future fuels within reach of an even wider range of vessels.
1. INTRODUCTION
The ability to convert vessels for new fuels once they are in operation is an important part of future-proofing the global fleet in line with increasingly strict emission regulations. Fuel flexible solutions ensure that, while the availability of future fuels matures, vessels can take advantage of the fuels that become viable to their particular business and operating case.
Wärtsilä’s new Two-Stroke Future Fuels Conversion Platform is based on newly developed injection technology that enables the fuel supply system to be dramatically reconsidered. The pilot conversion is planned for 2023, closely followed by the first commercial conversion project.
The conversion platform offers two fuel pathways. For operators in need of an immediate impact on air pollution and greenhouse gas emissions, an initial conversion to LNG is one option. The environmental impact of LNG can be further improved by replacing fossil-based LNG with carbon neutral bio- or synthetic LNG as it becomes available, either as a blend or in full substitution. An LNG conversion can also be prepared in advance to minimise retrofitting requirements for a future onward conversion to other net-zero fuels.
The second route is to convert directly from diesel to methanol or ammonia when these fuels are available affordably and at sufficient scale. This approach offers an instant step to using carbon-neutral or zero-carbon fuel and meeting long-term decarbonisation targets.
2. THE SOLUTION
The Wärtsilä Two-Stroke Future Fuels Conversion Platform is a new fuel injection technology and combustion concept for retrofitting vessels. The solution combines the benefits of Diesel (high pressure) and Otto (low pressure) combustion cycles – low-pressure supply with high power density and low methane slip.
Because fuel preparation processes are incorporated in the on-engine systems, allowing the supply of low-pressure cryogenic LNG directly to the engine, less onboard space is needed for the fuel gas supply system. Furthermore, additional power demand is minimised by powering the fuel preparation processes with excess energy from the engine’s servo oil and jacket cooling water systems. Because of the proprietary hybrid combustion process, the converted engine will also benefit from negligible methane slip (≤0.3 g/kWh). The result is a concept that cuts the capital investment and complexity associated with an LNG retrofit, while delivering a system that minimises maintenance requirement and operational cost. Compare the diagram below (Figure 2) to the configuration above (Figure 1) as a graphic illustration of the simpler installation.
Wärtsilä’s technology platform features a cryogenic fuel supply system and flexible combustion process. Cryogenic LNG is supplied from the tank to the engine at -150°C and at low pressure, around 10 bar. On-engine amplification raises the pressure of the gas fuel to more than 100 bar before injection into the cylinders.
No major changes to the engine are required beyond new cylinder covers and add-on components. And because the fuel is supplied at low pressure and at tank temperature, no large compressors, pumps and heat exchangers are required as part of the fuel gas supply system. The system also offers redundancy and operational flexibility, with the capability of switching to use conventional liquid fuels like HFO, MDO or VLSFO.
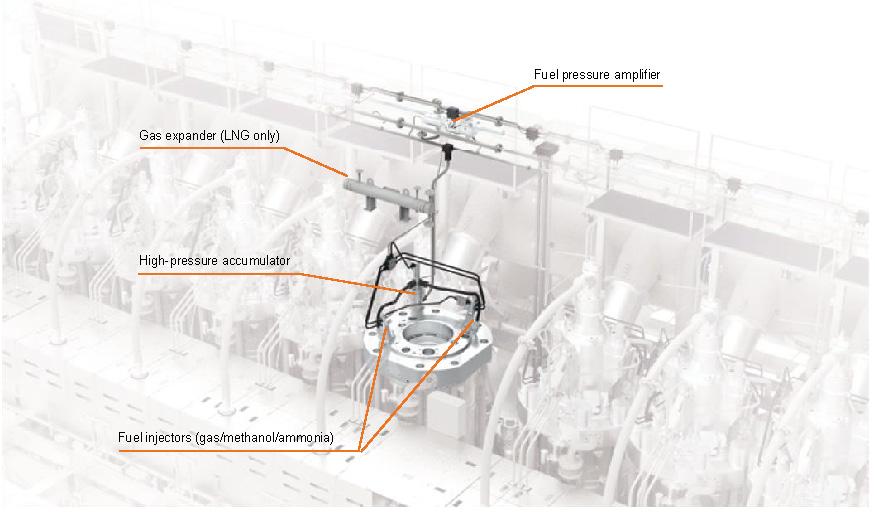
Methanol
The conversion of a two-stroke propulsion engine’s fuel storage and supply system to methanol is less complex. Methanol is a liquid fuel, stored at ambient temperature and pressure and as such, easier to handle than LNG. In fact, existing fuel (HFO or MGO) storage tanks can be converted to hold methanol as long as a ventilated cofferdam is put in place to comply with class rules for storing low-flashpoint fuels. Additional methanol can be stored in tanks placed on deck.
Because Wärtsilä’s Two-Stroke Future Fuels Conversion technology incorporates on-engine fuel pressure amplification and control, it requires only a simple low-pressure fuel supply system with low energy demand. The use of a three-layer flexible stainless-steel pipe - combining methanol supply, return and vacuum insulation - maximises retrofit flexibility, making the fuel conversion possible even for installations with limited space. The platform’s hybrid combustion technology ensures negligible fuel slip and in turn a minimal risk of formaldehyde formation as a by-product of the combustion.
Minimising off-hire time
As off-hire time is often a barrier to fuel conversion projects, the platform is designed to ensure rapid retrofitting. Equipment is skid mounted as much as possible using prefabricated, preassembled modules to speed up installation. Off-hire time is minimised with the engine conversion taking approximately three weeks, and a target to complete the vessel fuel
conversion within five weeks at a repair yard. This time saving should not detract from the fact that any conversion project needs to be carefully prepared. A typical project can take up to a year and a half from initial planning to completion (Figure 1). However, the time savings in the project phase make a significant difference to costs
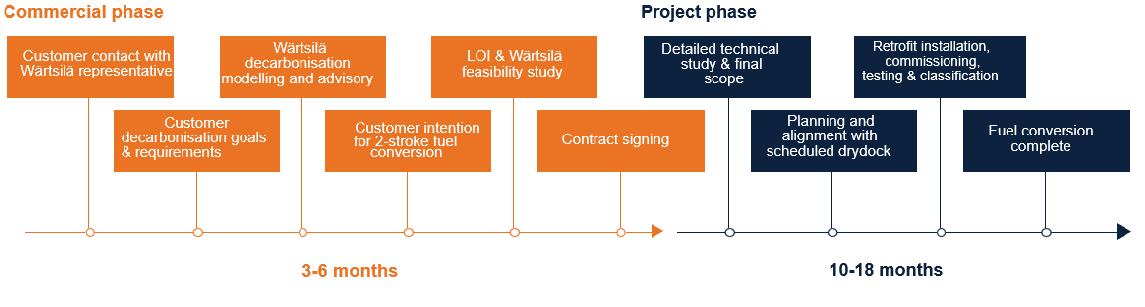
Figure 1: Illustrative planning period for a typical fuel conversion project
3. THE OUTCOME
Converting two-stroke engines for future fuels brings substantial economic benefits for a range of applications. Table 1 indicates the competitive 2-stroke engine conversion costs for three vessel types.
Conversions can also bring a great deal of flexibility as operators plan their compliance. Vessels can remain compliant with IMO’s Carbon Intensity Indicator longer by converting to use LNG or future fuels. As well as extending the vessel’s operational lifetime - and its future earning potential – conversions can also offer greater flexibility for ship operators. The charts below reveal how.
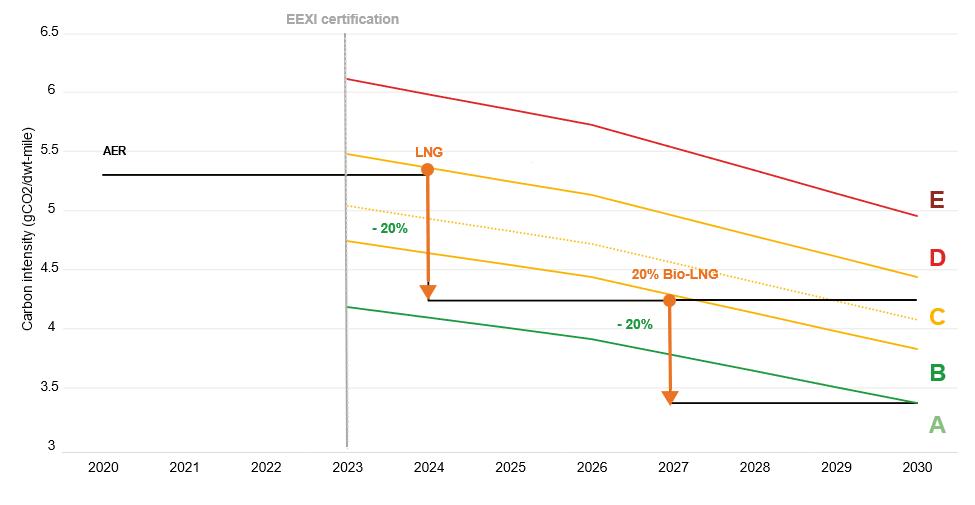
Figure 2: Future proofing a 15,000 TEU containership (LNG pathway) Looking at the case of a 15,000 TEU containership, a conversion to enable the use of LNG can offer around a 20% improvement in Annual Efficiency Ratio. This can be improved further at a later date by adding synthetic or bio-LNG as a drop-in fuel. Figure 3 shows how a vessel that would fall into CII’s D rating in 2023 can keep within the C rating until at least 2030 by using LNG. Adding a blend of 20% bio-LNG will keep the vessel compliant in an even higher category for even longer – the vessel stays within category A until around 2030.
These significant improvements in AER can be useful in two ways. First, the owner and/or operator can choose to keep in the highest available CII rating – complying to the maximum extent and opening up the benefits that this brings in terms of access to green finance and work from charterers demanding high levels of compliance. Alternatively, the vessel owner can choose to make use of the gap between maximum compliance and required compliance to operate with greater flexibility. If the vessel only needs to stay within CII’s C rating, the operator can choose between several options. For example, they can increase vessel speed, which would increase emissions but still within the required limit. This could allow operators to increase utilisation of the vessel and to access charters that require a higher speed. Or the operator could choose to take advantage of the difference in fuel prices, for example by adjusting the proportion of bio-LNG used, or even running on conventional fuel for some voyages – while still staying within compliance.
The flexibility to either increase speed or take advantage of fuel price differences could be a crucial benefit compared to operators who choose to walk the compliance line without a future fuel conversion. These operators could maintain compliance by slowing down – and potentially losing valuable business – or by using drop-in fuels compatible with conventional fuels, in which case they would be dependent on the limited supply of these fuels, whatever the cost.
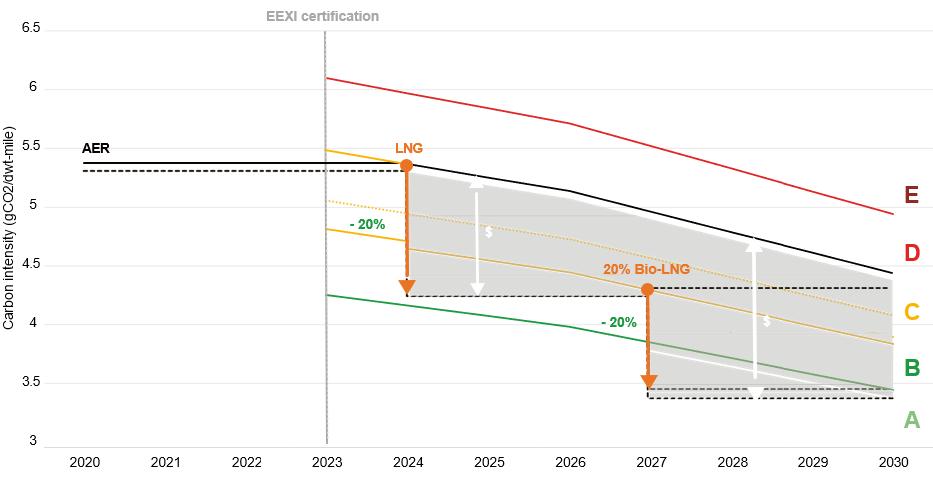
Figure 3: Operational flexibility within compliance limits for a 15,000 TEU containership with LNG conversion

STEFAN GORANOV
General Manager, Sustainability Solutions, WinGD
BIOGRAPHY
In his current role, Stefan is responsible for sustainability advisory and creating value-based solutions that improve the environmental and financial performance of ships operations through electrification and digitalisation. His career in the maritime industry has spanned over 20 years, where he has held various technical and managerial positions.
Today, Stefan’s team advises ship owners, operators, charterers, and financers in the field of sustainability in the maritime industry – from technical and economic assessments, to defining system features and user experience. They also develop and deliver turn-key energy efficiency solutions for new and existing ships, tailored to concrete requirements.