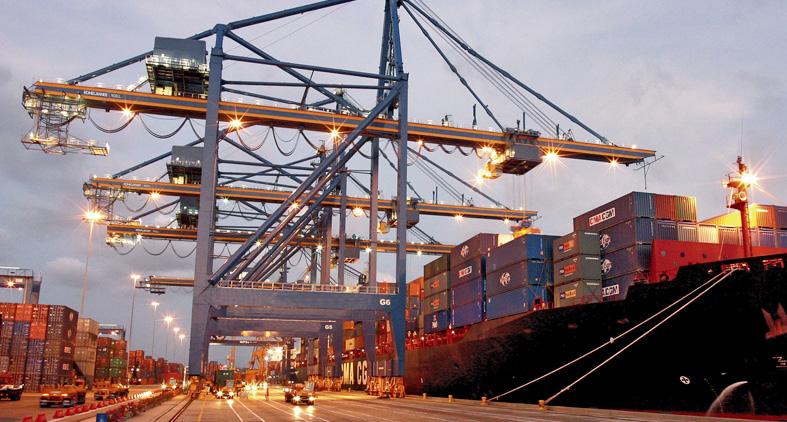
21 minute read
Tales from TOC
STS DESIGN: NEW FRONTIERS
New concepts in STS container crane design have been introduced recently but the main emphasis in design is on refining existing elements to promote efficiency and sustainability. Mike Mundy reviews the initiatives
Design priorities at the top end of the ship-to-shore container crane market have a strong focus on making improvements to the crane systems in service today.
There are entirely new ship-to-shore (STS) crane designs and concepts on the drawing board – for example the Balance Crane design developed by Liftech Consultants of California in conjunction with ZPMC, the Shanghai headquartered crane manufacturer (see box story), and Kone’s multi-trolley crane concept which facilitates vessel working from both sides of a ship in an indented berth. In the main, however, design innovation is proceeding within the framework of established STS crane design parameters. Trevor O’ Donoghue, Marketing Manager, Liebherr Container Cranes, puts the spotlight on these when he identifies key design drivers today as “… automation, digitalisation, sustainability, safety, matching vessel size, improving productivity and responding to client specific requirements.”
The crane size issue is an interesting one, with the perennial question hanging over it of how much further can you go? As O’ Donoghue notes: “To-date many of the Liebherr STS produced have outreaches well in excess of 70m and feature a lift height of 54m or more.”
Current top-of-the-range STS container crane configurations are proven to be able to efficiently serve vessels with a capacity of up to 24,000TEU – Evergreen’s recently commissioned Ever Alot has a capacity of 24,004TEU. There has been talk of even larger vessels, 25,000TEU to 30,000TEU but while acknowledging that such designs are technically feasible the general feedback from the shipping sector is that they offer little merit economically, not much gain in terms of reduced slot cost, pose challenges in terms of achieving a high level of slot utilisation and most significantly would likely generate a prohibitive level of investment requirement on the landside.
It is thus within the existing top-end parameters of STS container crane design that innovation looks set to proceed, with the current weighty container vessel order book confirming this.
AUTOMATION INTEREST
Interest in harnessing the powers of automation continues to build in high income economies, where labour costs are high, and to an increasing extent in upper middle-income economies. According to Simo Mustalammi, Director, STS Cranes, Konecranes, as regards the specific aspect of automating for remote operation there is building interest but as yet selective take-up.
One example, however, of the steadily widening interest in remote operation and automation in the operating cycle is the specification of four high-capacity STS container cranes in a package order, which includes, 12 rubber tyred gantries (RTGs) recently placed by the Port of Duqm, Oman with Liebherr Container Cranes.
Each of the Duqm STS Cranes will possess an outreach of 71m, a back-reach of 18m, a lift height over the rail of 50m and have a safe working load of 65 tonnes under a twin-lift spreader. They will be supplied without a cabin and operated utilising a combination of remote control and automation. Automation will take care of the majority of the cycle with operator intervention only required when operating below a predefined safe height. Each Liebherr STS will be connected to its own dedicated Remote Operator Station (ROS).
The centrally located remote operation facility will also host the ROS for control of the automated RTGs. The cabinless RTGs feature automation over the stack with remote control only required for container pick or place from the truck trailers, or for exceptional handling circumstances. Four ROS operators will operate the twelve RTGs.
8 There is steadily
building interest in ship-to-shore container cranes specified with a remote operation capability
Paceco Corp, another well-known manufacturer, further confirms the steadily growing interest in automation for handling functions with US-based Troy Collard, General Sales Manager, Paceco, noting that the company is building upon its existing semi-automated capability with full automation now under development.
Where there is plainly great interest in capitalising on the powers of automation is in conjunction with what can broadly be called support or safety functions. Typically, for instance, Liebherr points out that its STS crane design incorporates a remote crane management system allowing for remote assistance, service and diagnostics. Plus, the design, “…features a traffic light system for controlled traffic flow, laser and mechanical crane to crane anti-collision systems, ultrasonic anti-collision systems for gantry travel as well as laser boom to vessel anti-collision and sill beam protection systems.”
Konecranes also underlines the importance of such features highlighting the importance of its predictive maintenance system coupled with its TRUECONNECT remote monitoring service, as well as diverse features which serve to promote operator efficiency. In the same vein, O’ Donoghue points out that while Liebherr’s STS cranes have benefited from a mechanical anti-sway system, “that is a favourite among crane operators for many years, electronic anti-sway is also now available and is supplied as a component of many of our automation sub systems.”
SUSTAINABILITY SEARCH
In crane design and in their manufacturing and business activities considerable emphasis is now being placed by key crane manufacturers on sustainable arrangements. On the design side electric power is a key factor including the feedback of generated electricity to the grid. LED lighting is a factor as is the better overall control of the handling process and crane movement through systems such as anti-sway and anti-skew.
At the individual company level, there is also great attention to achieving sustainability in-house. O’ Donoghue notes that Liebherr has recently been awarded a gold medal for sustainability from sustainability ratings supplier EcoVadis. Konecranes points out that in December 2020 it signed the Science Based Targets Initiative and earlier this year it published its new climate targets which it says, “have been validated as being in line with the ambition to limit global warming to 1.5degC.”
STRUCTURAL INNOVATION
Innovation in the area of STS crane structural design has been quite notable in a macro context recently – ZPMC is centre stage with this, originating in conjunction with Liftech, the new generation Balance crane design (see box story) and also a new light-weight STS crane that employs ‘spiral pipe’ in its construction. Reportedly, this pipe is originated by rolling strip at a helical angle and then welding.
At a more micro level, there is also evidence of crane structural component innovation with Liebherr reporting a recent crane design for Alicante which can be used on both an older and new quay. The design was accomplished, notes the company, without any compromises. Generally, it also points out that the lattice type crane structure employed in its STS container crane design, together with the use of high tensile steel, ensures a low centre of gravity and consequently lower wheel loads. Both Konecranes and Paceco also report the proven ability to lower wheel loads with Paceco further pointing out that its monobox boom and the use of a selfpropelled trolley are a lighter arrangement than a twin girder crane thereby inherently reducing wheel loadings.
CONTINUOUS PROCESS
Design refinement in the STS container crane sector is a continuous process with this closely allied to meeting new user requirements, many dictated by container system upgrades. It is interesting that ZPMC has recently originated two new crane designs – it begs the question does the competitive cost basis of Chinese production facilitate such innovation?
In this context and generally it will be interesting to see what follows Kalmar’s withdrawal from the heavy crane sector and its parent Cargotec’s transfer of related intellectual properties and assets to RIC in China – see Equipment News. One thing is for sure, the sector is very market responsive, a positive achievement in a business climate where the Cargotec relinquishment of its heavy cranes portfolio, including STS units, signals tough competition and squeezed margins.
Enter the Articulated Balance Crane
US-based Liftech, a well-known name in the field of crane design, has developed a new crane concept working in collaboration with Shanghai-headquartered crane manufacturer ZPMC – the Articulated Balance Crane.
The Balance Crane has reduced wheel and tie down loads compared to a standard ship-to-shore (STS) container crane. The design originated by Liftech is in the order of eight per cent lower than a standard crane in terms of total weight and the wheel loads, in both operating and stowed modes, are around 15 per cent lower. The boom is continuous from the landside legs to the boom tip. The landside girder is connected to the boom with a parallel linkage.
To clear the vessel bridge, the boom and upper works rotate as a unit about waterside. The machinery house and shortened trolley girder landside of the landside leg remain horizontal while translating in a downward arc. The net result, Liftech underlines, is a “stowed crane with a lower centre of gravity and reduced overturning moment due to stowed wind loads. In the operating position,” the company further points out, “there will be reduced trolley rail hinge maintenance due to fewer trolley cycles crossing the hinge relocated to the landside. The Liftech Web Site features a video showing the key design features and ability of the Balance Crane’s boom to be raised in line with operational requirements as well as other key actions.

8 US-based
Liftech, working in conjunction with ZPMC, has originated the new concept Articulated Balance Crane
THE REEL DEAL
Crane reel system suppliers are responding to modern day design requirements and building healthy order books. John Bensalhia reviews the sector
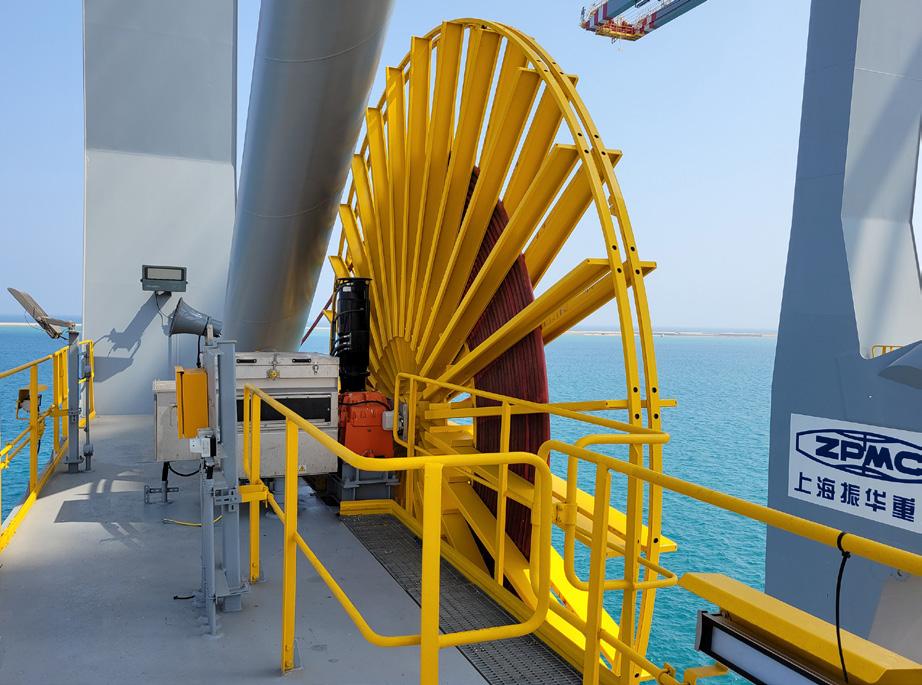
For Conductix-Wampfler GmbH, continued high demand for cable reel systems is fuelled by three overlapping trends. In the short-term, by congestion in container terminals and high margins in this sector; medium-term, conversion of diesel applications to electric drive; and long-term, generalisation of container transport by land.
Damian Russell, VP Product Management, Reels Technologies, Ports and Maritime Cavotec, comments in a similar vein: “We have been fortunate to secure several orders in recent months, notably from long-term Cavotec equipment owners. We have open orders for 15 cable reel systems for Georgia Ports Savannah. We also have a couple of orders with challenging conditions, especially for spreader cable reels, with restricted space availability on the crane trolley for installation of the spreader reel.”
Conductix-Wampfler has also received multiple repeat orders, as Olivier Ruelle, Global Product Manager Reeling Systems explains: “Our customers trust our reels because they will support the application during its lifetime, and we will be there to support anywhere in the world if a problem arises.”
A major advantage claimed for the cable reel is its flexibility for STS container crane power supply. Stemmann-Technik argues “Conductor bars are constantly in the way, while a hybrid system would not bring enough power for a constant operation, considering the emission efficiency.”
Generally, the company also notes: “Electrical cranes reduce energy consumption compared to diesel systems, reduce maintenance cost and wear and tear. It helps also to automatise the operations of the cranes, making this capable for future remote systems.”
REEL ADVANTAGES
Cable reels are claimed to have the advantage over other STS container crane power supplies due to their long-term proven reliability and easy maintenance concentrated in one spot. “Cable reels are the only practical means to feed MW power and Gigabits/s of data 24/7 to container cranes,” says Michael Kusch, Head of Global Marketing & Communications, Conductix-Wampfler. “Diesel power,” he does acknowledge, “is being retrofitted due to maintenance costs and CO2 emissions and high voltage conductor bars are used in a few terminals.”
“A key advantage of our cable reels,” he elaborates, is their reliability constructed and continuously developed based on decades of experience and on customers’ feedback, both electrical and mechanical, HV sliprings and Transmitter Fiber Optics (TFO). Our TFO adds its very high reliability to the secure and practically unlimited bandwidth data transmission through optical fibres.”
Russell concurs that cable reels are long established as the most reliable power supply solution to STS cranes. “Existing brownfield terminals may continue with older technologies like bus bar systems installed in trenches for
8 Conductix-
Wampfler says that cable reels are the only practical means to feed MW power and Gigabits/s of data 24/7 to container cranes
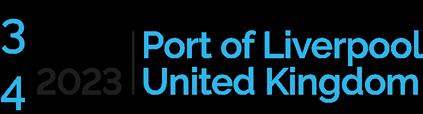

Hosted by:
Book your place now
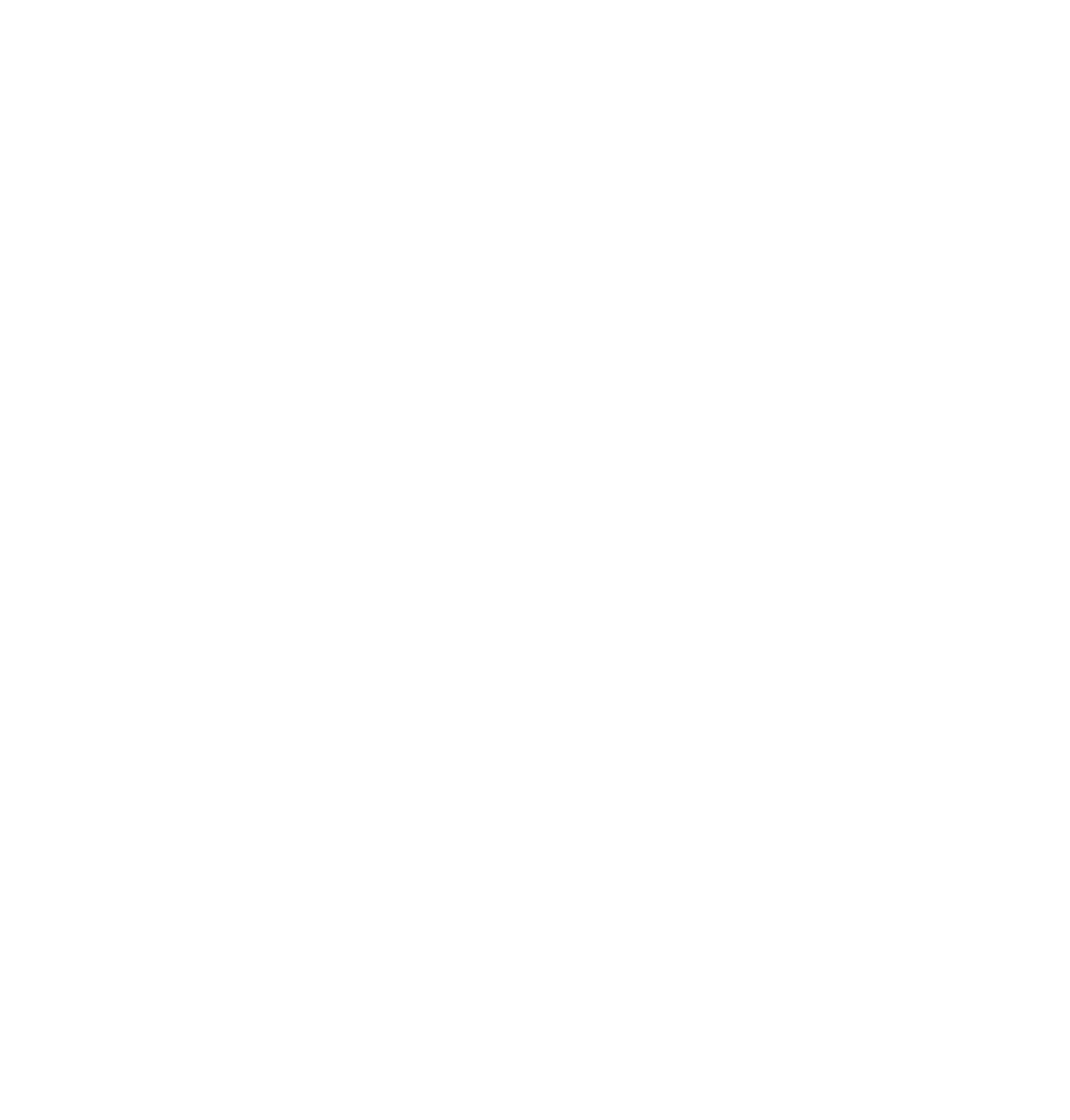
Coastlink is a neutral pan-European network dedicated to the promotion of short sea feeder shipping and the intermodal transport networks that support the sector
Premium delegate place includes:
use code CLKEARLYPREM
• One and a half day conference attendance • Full documentation in electronic format • Lunch and refreshments throughout • Place at the Conference Dinner • Place on the Technical Visit
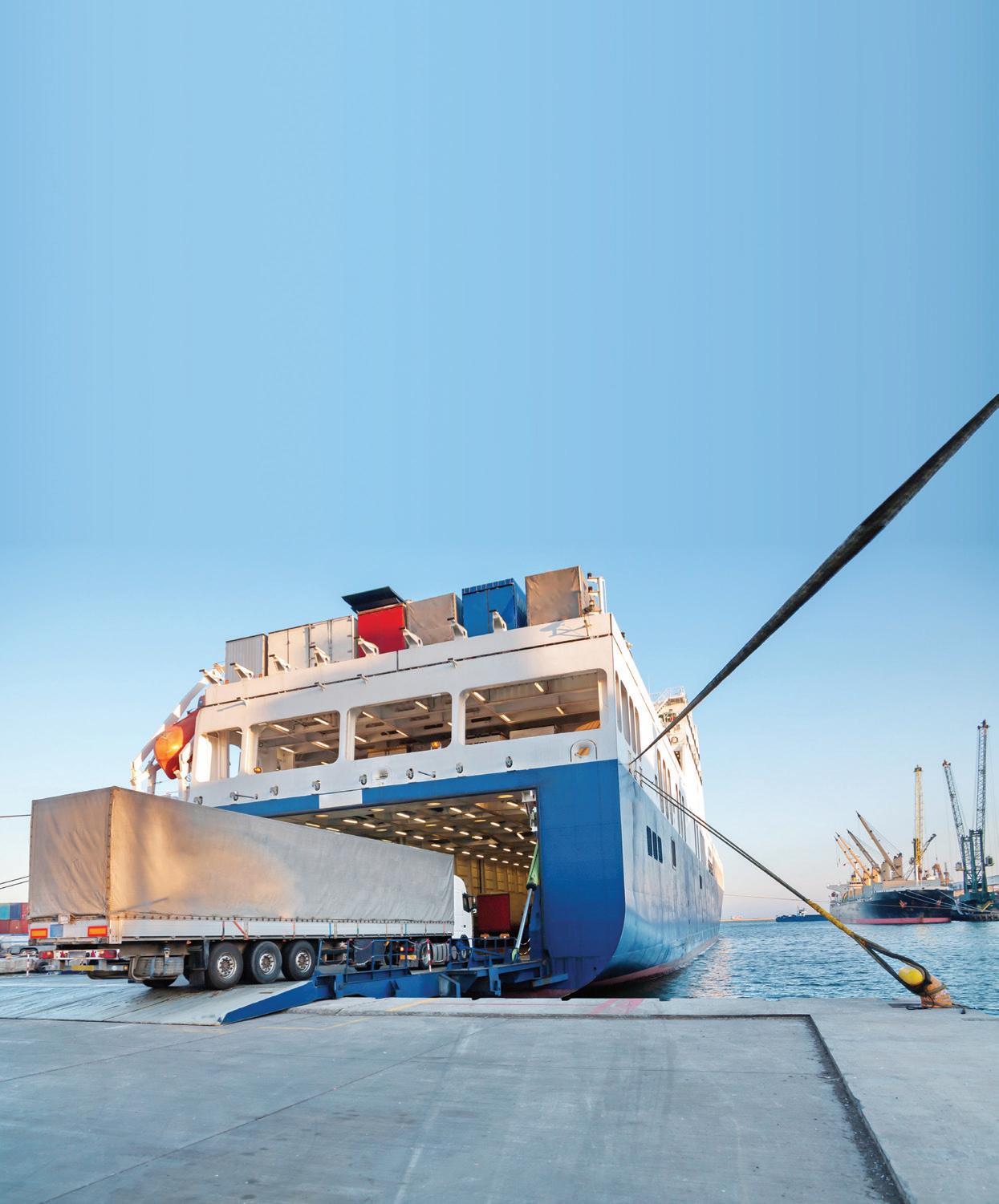
Standard delegate place includes:
use code CLKEARLY
Conference Handbook only • Lunch and refreshments throughout • Place on the technical visit
Meet and network with international attendees representing shipping lines, ports, logistics companies, terminal operators and freight organisations For more information on attending, sponsoring or speaking contact the events team: visit: coastlink.co.uk contact: +44 1329 825335 or email: info@coastlink.co.uk
Media partners:
MOTORSHIPTHE
MARINE TECHNOLOGY
GREENPORT
Supporter:
new cranes, but these types of systems require more maintenance and are more susceptible to wet or dusty environmental conditions,” he says.
TODAY’S DESIGN REQUIREMENTS
Modern cable reel design criteria include a light weight and design to endure harsh environments with material robustness, higher data transmission, remote access facility, higher accelerations/speeds, and predictive maintenance with associated cost reduction. “We have also noticed a very good response from the customers regarding our commissioning time,” says Konstantin Schultheis, Key Account Manager, Stemmann-Technik. “We have a very easy, ready to plug and start powering system, allowing savings up to five days on commissioning, comparing to the next best alternative.”
Reliability takes precedence in today’s design requirements. For Conductix-Wampfler, this applies to power supply and data transmission.
“Reliable, real-time data transfer equals the importance of reliable power in automated and remote-controlled applications: if something might go wrong in the automated operation, the operator must be able to take control, get a complete understanding of the situation in a split-second from multiple real-time on-board cameras and sensors, and get his commands executed the next split-second, without latency, contention or hacking,” emphasises Conductix-Wampfler.
More Cavotec customers are placing a premium on reliability of the cable reel systems, to maintain crane uptime. “We also see requests for redundant drive motors and controls so that the cable reel can continue to operate, either at full or some reduced capacity in case of component failure,” says Russell.
“A sound, simple and solid mechanical and electrical design is the mandatory basis to construct reliable cable reeling systems,” explains Kusch. “For example, we systematically use cast iron cases for gearboxes for STS to better guide the shafts and gears and better support the bearings, and we systematically protect our mechanical and electrical components against moisture.”
Conductix-Wampfler avoids engineering-to-order, focusing on defining modular ranges of products that use standardised, industrialised components. “This allowed us to invest a lot in the reliability engineering of our reels’ components and test them equivalent to 20 years operation on a set of long-term test benches,” the company says.
A recent addition for Conductix-Wampfler is the Condition Monitoring/Predictive Maintenance options on its KHD series to enable early detection and fast repair of mechanical wear on unmanned cranes.
Stemmann-Technik developed its specific Active Acceleration Control (AAC), helping to predict ‘stop & go’ movements with high (de)/accelerations. “This is all about the control and the deep know-how about the crane’s behaviour, which we have gathered over the last decades. Our AAC system is constantly analysing the data, allowing for stepless torque adjustments. It protects the cable from oscillation and slacking. A system can be 100 per cent redundant without cutting the crane’s operational efficiency.”
Cavotec’s cloud based IoT platform, ‘Cavotec Connect’, can offer enhanced monitoring of its equipment for predictive/preventative maintenance or remote monitoring and troubleshooting. “We have a suite of sensors that can be used, for example, in conjunction with shock/vibration, temperature, humidity, and arc-flash.”
Specified cable reel design upgrades or changes are possible. Stemmann-Technik says that it is keeping the widest range of cable portfolio to meet specification requirements. “If the crane upgrade or refurbishment is made, it requires changing the design of the cable reel. Drawing on long experience, we do it almost automatically/simultaneously, having enough solutions for all requirements and cable types. If the number of cores (copper or fibre optics) is to be increased, we also have to update the slipring assembly,” says Schultheis. “In some cases of crane upgrades, replacing the complete reel is the most economical solution. On the other hand, in case of refurbishments, control program adjustments of our systems will already fulfil the requirements.”
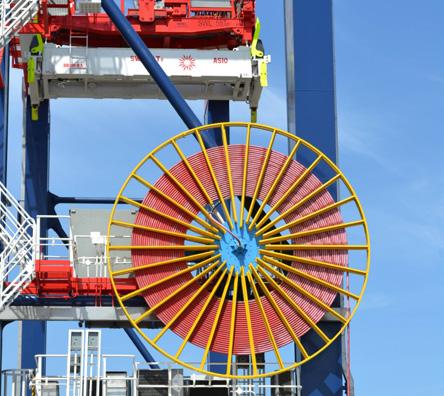
IRONING OUT SNAGS
A potential problem encountered with cable reels is cable snagging. Stemmann-Technik reports it uses robust, specially designed profile spokes to avoid any deflections of the cable reel body. “We implemented the AAC, fine-tuned cable control system in order to keep the cable tension as constant as possible. Besides this, we work with compliance of the cable bending radius and avoidance of any cable’s torsion/ twists. With our solution, the problem of cable snagging is widely reduced.”
In the same context, Russell notes: “To prevent the cable getting stuck or pinched, the spacing between cable drum spokes must be set correctly, with a small clearance around the cable. The same goes for the cable trench dimensions, or a product like our Panzerbelt cable protection system, where we dimension according to cable diameter and an allowance for lateral clearance between the crane rail and wheel flanges,” says Russell. “Cable guides and rollers need to be maintained to minimise friction during reeling of the cable.”
He continues: “If the cable path is clear, then the torque generated by the cable reel drive system must be well regulated to maintain correct cable tension. “Most cable reels are VFD (variable speed drive) controlled, which gives the best torque control and lowest operating cable tensions. Cable life can be maximised by keeping cable tensions low as possible.”
If a customer requires a larger cable reel, StemmannTechnik says that while there is no physical border for the cable reel itself: cable deformation is the challenge. “For European projects, we are facing cable reel bodies with an average of 7m. Depending on the cable dimensions, we can cover around a 1200m quay length considering power feeding at the centre of the track.”
The reducing factor, Stemmann-Technik elaborates is “the physical property of the cable which is not stable enough to keep its shape in the inner layers of the cable reel. Those layers have to carry the weight of 1.4 tons and are deformed.”
8 Stemmann-
Technik has developed its specific Active Acceleration Control (AAC), helping to predict ‘stop & go’ movements with high (de)/ accelerations
TWO TALES FROM TOC
Steve Cameron, well known Moderator at the Terminal Operations Conference (TOC) and roving correspondent for Port Strategy, highlights two ‘tales’ from the June TOC in his own inimitable style
STREAMLINING INLAND BARGING
Last year at TOC Rotterdam the consistent feedback from speakers, was concern about the lack of connectivity, shared data, and visibility in the hinterland supply chain. Since then, Maersk has developed a supply chain Resilience Model (SCRM) to help customers reduce supply chain risks and mitigate disruptive impacts. This year Matthijs van Doorn, Vice President Commercial the keynote speaker from the Port of Rotterdam, focused on these issues.
For some time, the handling of inland container vessels at Rotterdam’s deep-sea terminals has been under pressure. Barge delays at terminals peaked last year when congestion resulted in waits of over 180 hours. In part, the congestion has been due to barge operators arriving at already congested terminals, taking up space to unload small volumes of containers when the berth space could have been used more effectively. As the Operations Manager of one barge operator pointedly underlines: “This is not good for inland supply chains, when all of your barge fleet is stuck at the deep-sea terminal.”
Another issue identified is where the major inland barge destinations share the same artery/routing. The duplication of vessels for that sector of the route contributed to congesting the waterway and overall inefficient use of resources. The solution for these and other issues, requires a more transparent and efficient structuring of the container inland shipping chain with all players working together.
During an interview with Port Strategy, after his presentation, Matthijs van Doorn, flagged that: “Inland shipping plays an indispensable role in the transport of containers to the hinterland. Last year container throughput at the port of Rotterdam was 15.3 million TEU. At present, 38 per cent of the containers that move between the Maasvlakte (outer port area), and the hinterland are transported by inland vessels. The Port Authority, says van Doorn, aims to increase this share to 45 per cent by 2030 by fully optimising the inland container shipping chain, noting that with no fewer than five deep-sea terminals at the Maasvlakte, the planning of inland container shipping in Rotterdam has become more complex than ever.”
Until recently, the inland terminals have relied on their own vessels to transport cargo to the terminals in Rotterdam. As a result, the deep-sea terminals receive a lot of calls with smaller sized vessels. Accordingly, planning terminal calls in the port complex is a complicated affair, and there are risks of accumulated delays when vessels call at more than one terminal during their visit.
INITIATIVES IMPLEMENTED
Initiatives have already been implemented to limit waiting times for container vessels at Rotterdam’s deep-sea terminals. One of these initiatives is the bundling of cargo destined for Rotterdam in the West-Brabant. This new collaboration between Oosterhout Container Terminal, Barge Terminal Tilburg, Combined Cargo Terminals, Moerdijk Container Terminals, and the deep-sea terminals in Rotterdam’s port area within the West-Brabant Corridor has been the first concrete initiative to yield positive results. Merging cargo streams within the Corridor has improved the
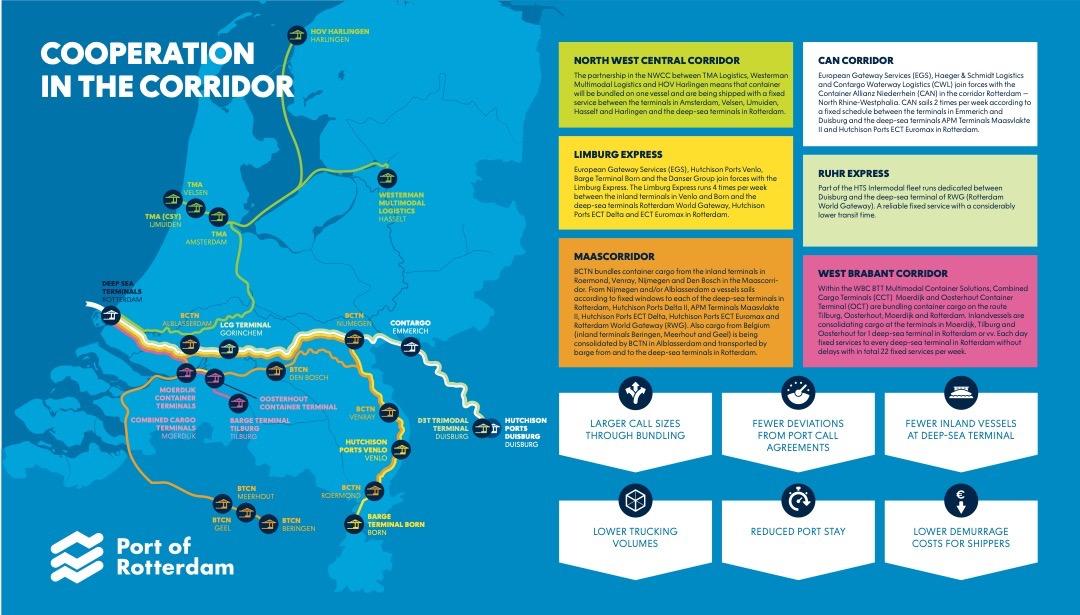

capacity utilisation of inland shipping on this route, which, in turn, has shortened waiting times at the terminals.
The UK MD of a global liner container operator responsible for European logistics, explains that route optimisation enables carriers to share barge, road and rail containers, and its use for inland logistics enables, in a few seconds, the planning of 10,000 loads. He notes that, while it has been around for 30 years and used by individual carriers, it only recently started to be shared and used more strategically to look at vessel scheduling and transit times. “The ethos in Rotterdam,” he said “appears to be to get everything to Moerdijk to decongest quay & roads. This may work well on imports, but perhaps on exports it may be less effective, we will have to see what happens”.
In the meantime, the Port of Rotterdam has introduced a weekly report on its barge monitoring service, which shows the percentage of delays and schedule performance for the lower, middle, and upper Rhine as well as time spent in port
OUTCOME INTERESTING
It will be interesting to see how this collaboration between the Port of Rotterdam and the barge operators develops. As efficiency gains from co-ordination of sailings, and sharing of barges take effect. The barge operators appear to be mirroring the liner shipping consortia. If they achieve the same level of sophistication as the liner shipping industry, in controlling the balance between supply and demand, it will be revealing to see the long-term effect this has on freight rates.
THE SPREADER THAT ASSESSES CONTAINER STRUCTURAL INTEGRITY… …while in lifting mode
ConnexBird has developed an innovative solution for assessing container structural integrity during core handling processes.
Many years ago as Operations Director of a shipping line that successfully developed and ran a ro-ro / container liner shipping service to West Africa, I was faced with the challenge of the high repair costs to our container fleet due to a combination of the damage caused by the handling of containers with a forklift on ro-ro ships; a lack of container handling equipment in most of the ports and the time spent by staff and managing the administration of heavy repair processes.
Over 10 years we developed various cost reduction initiatives, from repairing containers in lower labour cost countries (Nigeria & Cote D’Ivoire) to automating the checking of the repair estimate cost and billing process which enabled us to divert the attention of our shareholders towards other issues. So it is with great interest, a few decades later, to find a new approach from a company called ConnexBird, which has developed a container spreader mounted system that pings the container with vibrations, and before it reaches the repair depot, identifies the condition and structural integrity of the container. This takes place during the lift between ship and the quay, or into the stack.
Motivated by these possibilities, my research depressingly revealed that at present, many container damage assessments are still done manually. This incurs delays to the containers - whilst they await inspection, additional container handing costs, and increased fuel consumption for the handing equipment moving them in & out of the stack.
The vibration analysis hardware developed by ConexBird delivers actionable data to the end user enabling decision making on usability and the identification of the long-term repair costs needed to maintain the container.
This innovation potentially opens the door to a big step change in monitoring the condition and therefore safety and repair costs of a container. However, getting people in the industry to change, has always been something of a challenge.
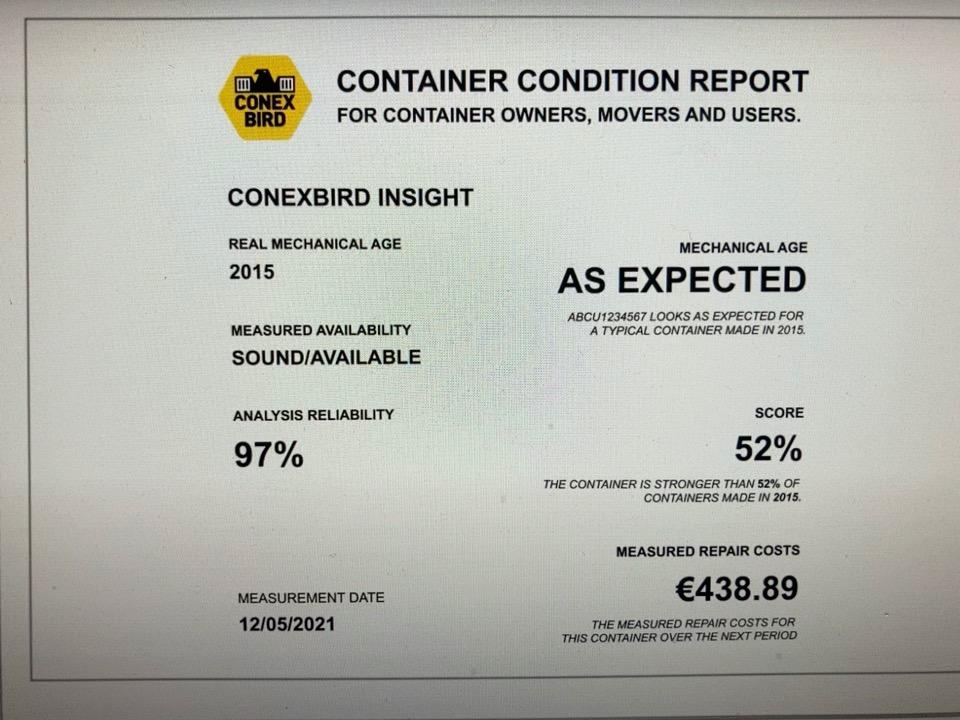
8 The Port of
Rotterdam’s weekly report generated from its barge monitoring service
8 Conex Bird