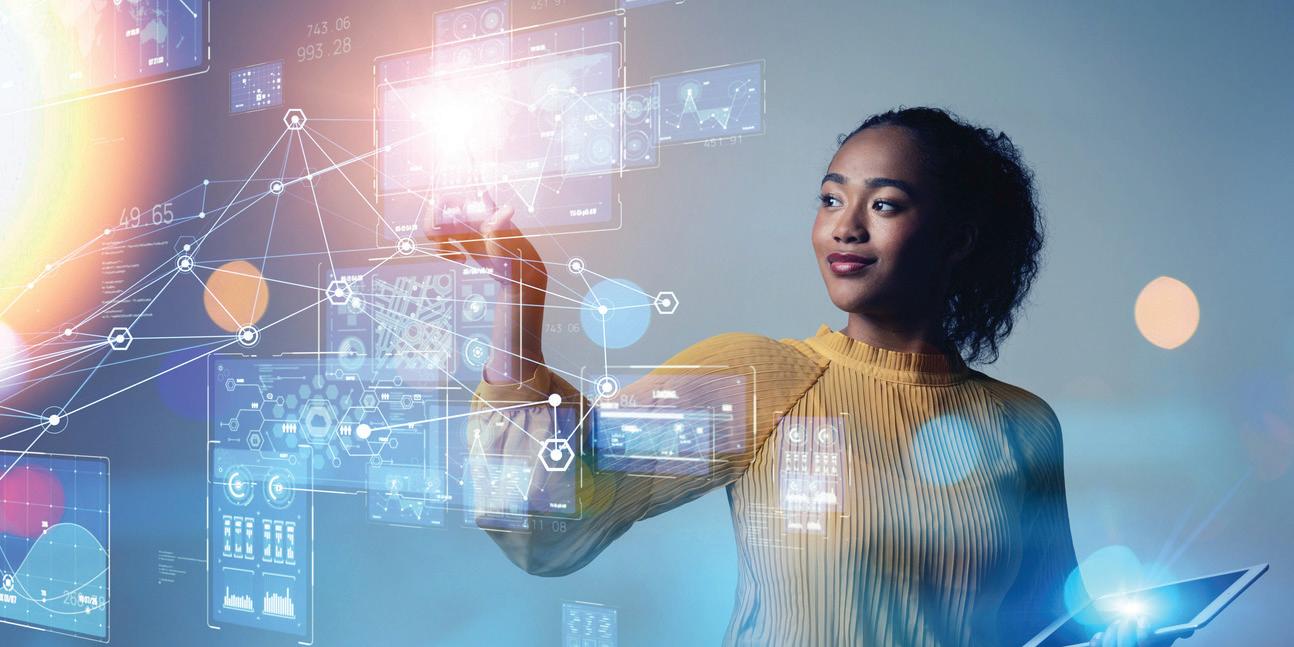
3 minute read
The Key to the Future for Manufacturers is in the Past
By Vince Sassano
Merriam-Webster defines the future as “a time that is to come” and in most cases, “an expectation of advancement or progressive development.” Automated data collection, artificial intelligence (AI), and other advanced process controls and equipment are all contributing to the promise of a better future. The question is: where is the future for manufacturers headed?
Data: As the pace of business quickens, and good labor is increasingly hard to attract and retain, it becomes more important than ever to be in the know. In the know about why things are not performing as expected. In the know about what expectations to have in the first place. But more importantly, being more aware of the fact that you don’t know what you don’t know.
While this may sound cliché, it is the reality for most manufacturers, and it often results in a proliferation of the status quo. Evidence of complacency is often heard in statements like, “Everything is chugging along just fine.” Data can provide objective evidence that improvements are possible. Insights from the data enable better understanding of downtime causes, performance bottlenecks, quality issues, and workforce impediments.
As data becomes more freely available to all levels of the organization, transparency replaces siloes, thereby enlightening and empowering the operation. And that improves culture.
Culture: Change to a manufacturing culture is like a trip to the doctor or dentist. It usually only happens when something is REALLY wrong. But it doesn’t have to be that way if the future path is ‘easy’, because nothing beats ‘easy’. Being able to push a button and have the production process run, without injury, without error, and with high quality and efficiency is the holy grail for manufacturing. But that requires people, procedures, paperwork, meetings, and all the other glue that runs the operation. Whenever change is introduced into this chain, panic often ensues. Clear objectives, training, progress measurement, and defining WIIFM (What’s In It For Me) will make acceptance and commitment much more likely. It also requires new leadership skills.
Leadership: Good leadership will become even more important as organizations strive to increase employee engagement and foster a positive and productive work environment. New skills will need to be added, however, including data analysis and the development of a common language. In the movie “Patton”, General George
Patton quoted George Bernard Shaw saying, “The English and Americans are two people separated by a common language.” Communication in the future will become easier for management and operations to not only get on the same page, but also agree on what needs to be done. Why? Because data, especially trusted data, is objective. This allows the discussion to proactively focus on solutions where everyone in the organization can demonstrate leadership. Profits follow.
ROI and the Bottom Line: Competition, consolidation, increasing customer expectations, and rising costs will dictate a tighter run operation and rigorous measurement of return on investment. Capital expenditures, special projects, and digital transformation efforts will need to be justified and measured by the impact they have on the bottom line. Consequently, manufacturers will move towards a more agile approach that emphasizes smaller, more modular investments that will generate quick wins to build upon, rather than large, expensive implementations with long payback periods. Expertise, both internal and external, is vital to staying on target now and in the future.
One of the most powerful forces that exists in manufacturing today is the desire to maintain the status quo. To move forward, manufacturers only need to look to the past to understand how things are and how they got that way. Once an initial assessment is made, focus in these areas will increase the probability of future success:
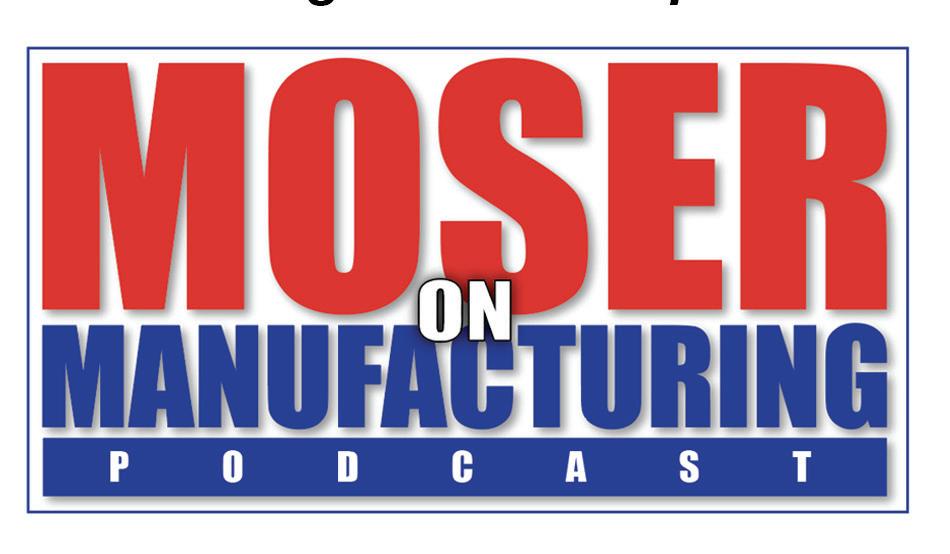
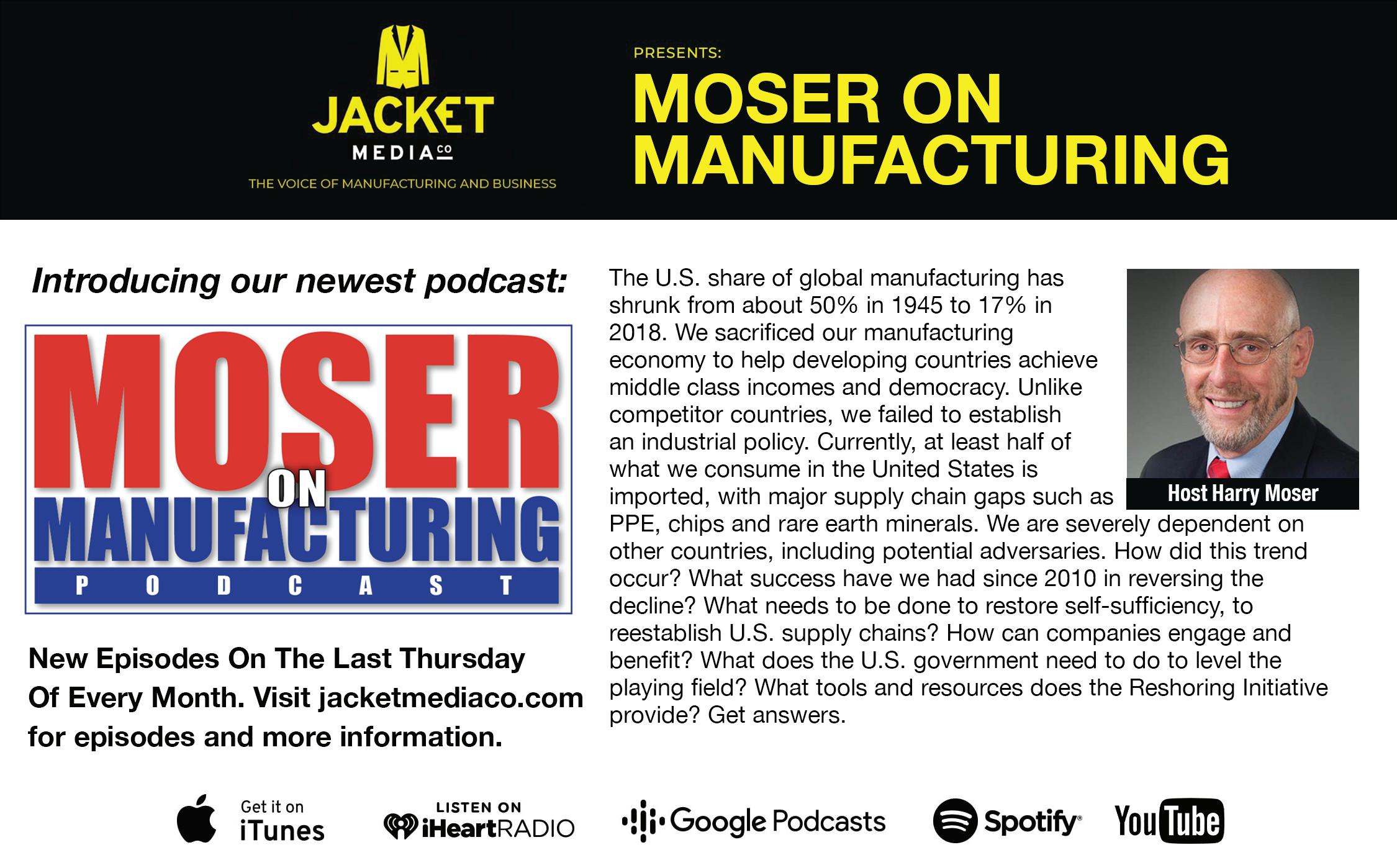
Data. This is the foundation for generating insights and action plans. It will objectively inform the organization on the best path forward and focus the team on solutions rather than debate.
Culture. Change is tough. There is widespread agreement on the behav- ioral patterns of change, including the path from disillusionment to acceptance. Clear communication of the ‘why’ behind change and the benefits to the organization and employees is critical for success.
Leadership. The right mindset, coupled with trusted data and an open culture will empower the workforce at all levels to have a voice in the future of the company.
ROI. The days of managing by gut feel are over. Data-driven decision-making is critically important for manufacturers to compete in today’s environment. It takes two points to draw a line. The future is the end point while the past holds the key to showing you where to begin.
Author profile: Vince Sassano is the owner of the Strategic Performance Company. n
by CASS INFORMATION SYSTEMS, INC.