MANUFACTURING TIDBITS: ROOFTOP SOLAR PANELS: EMPOWERING ONE-THIRD OF THE US MANUFACTURING SECTOR
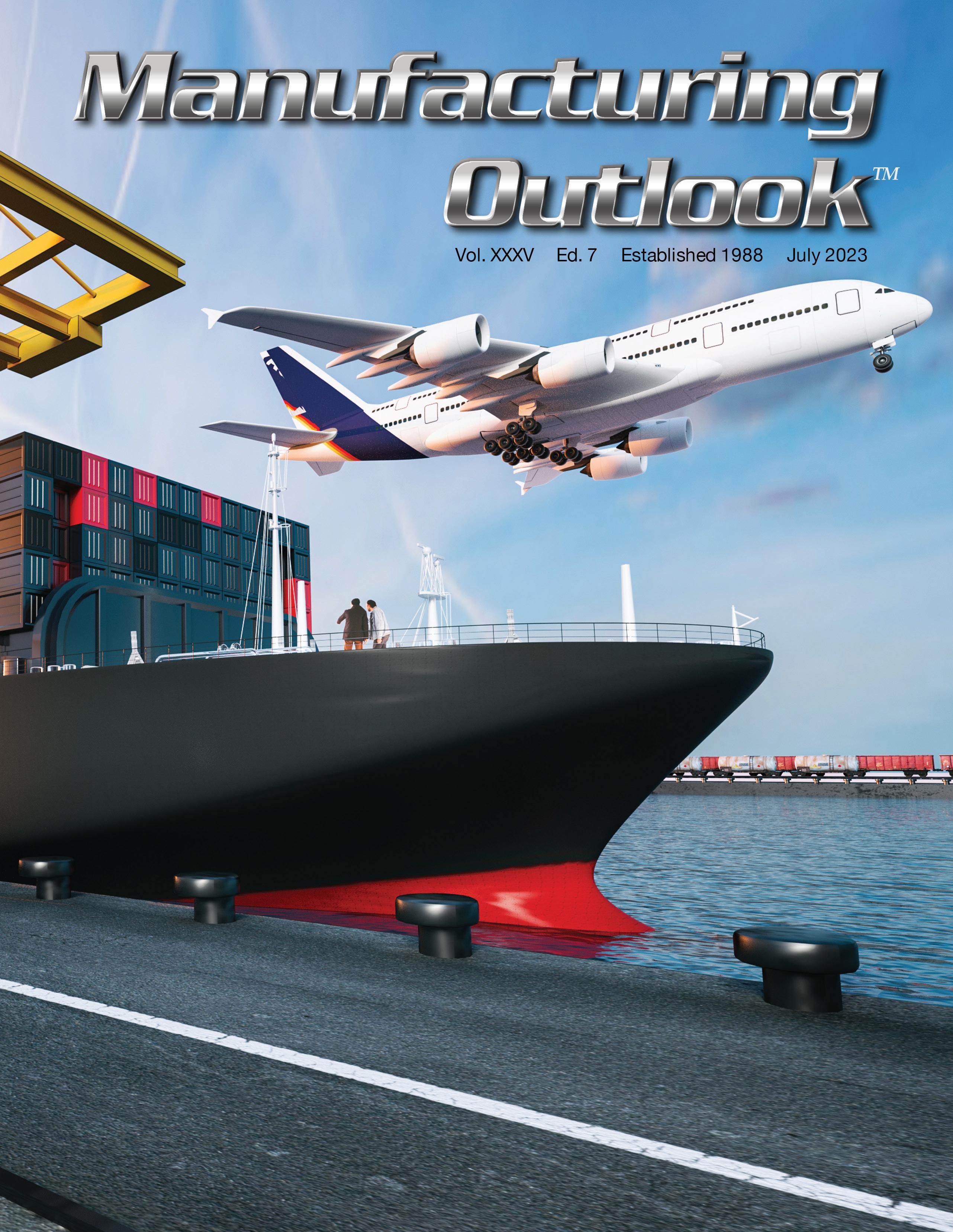
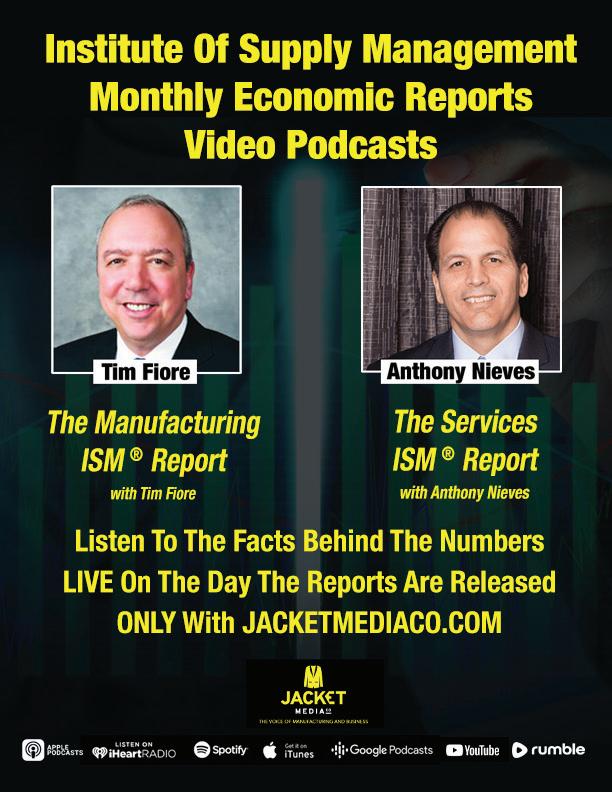
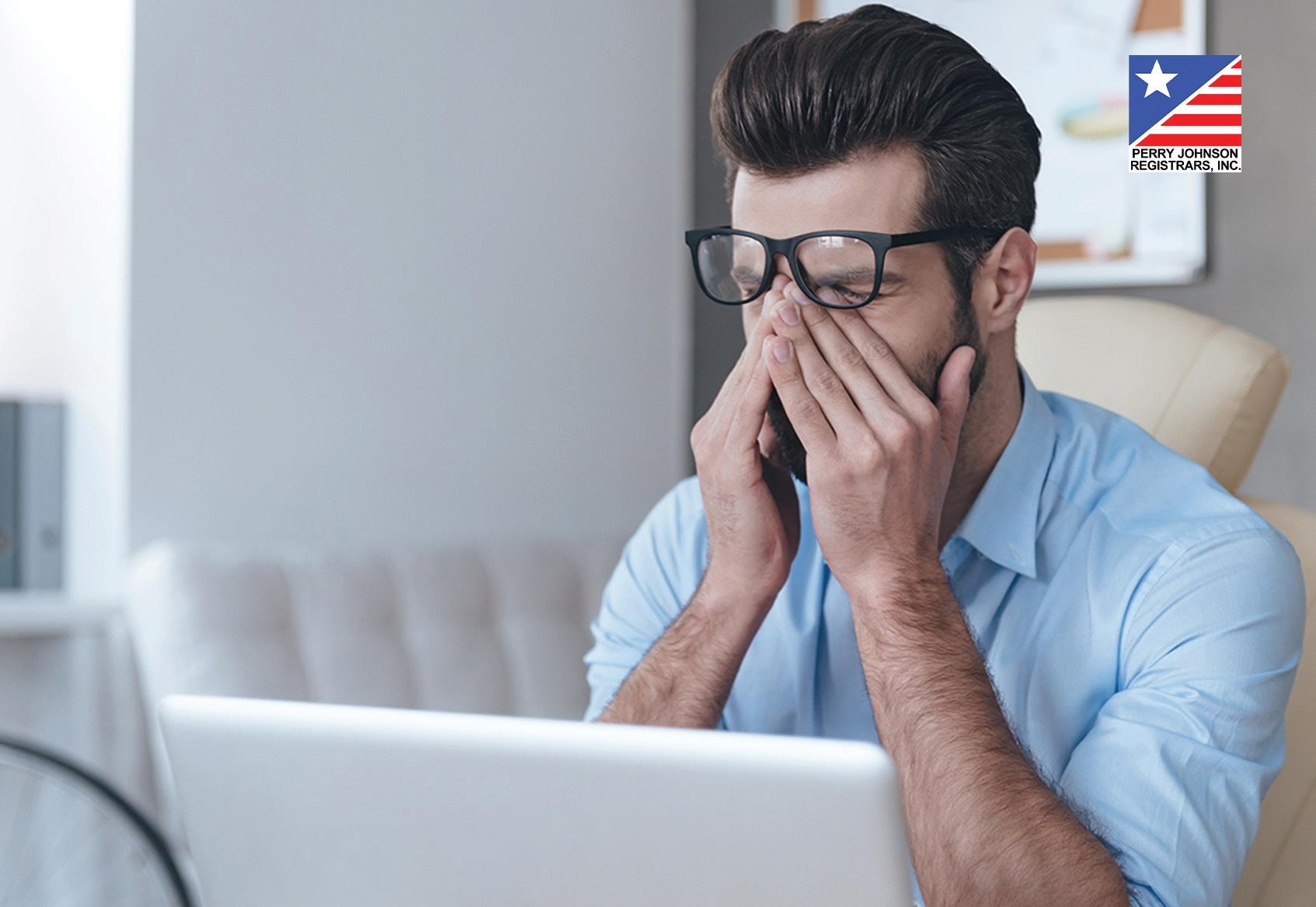


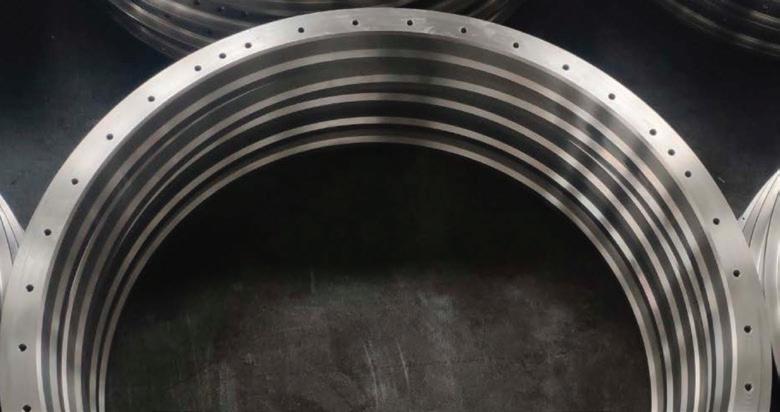
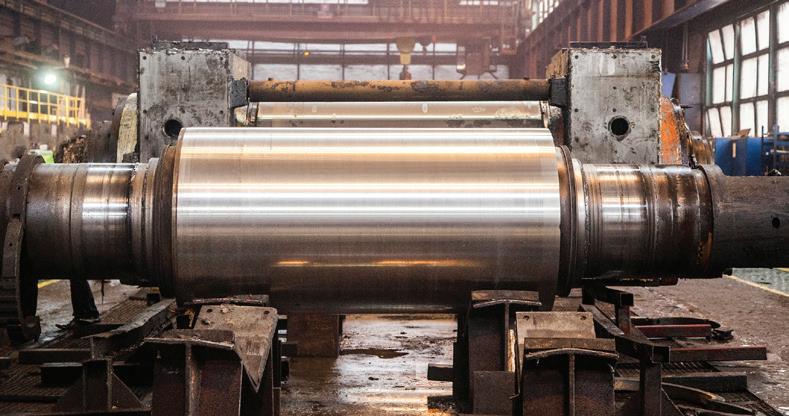
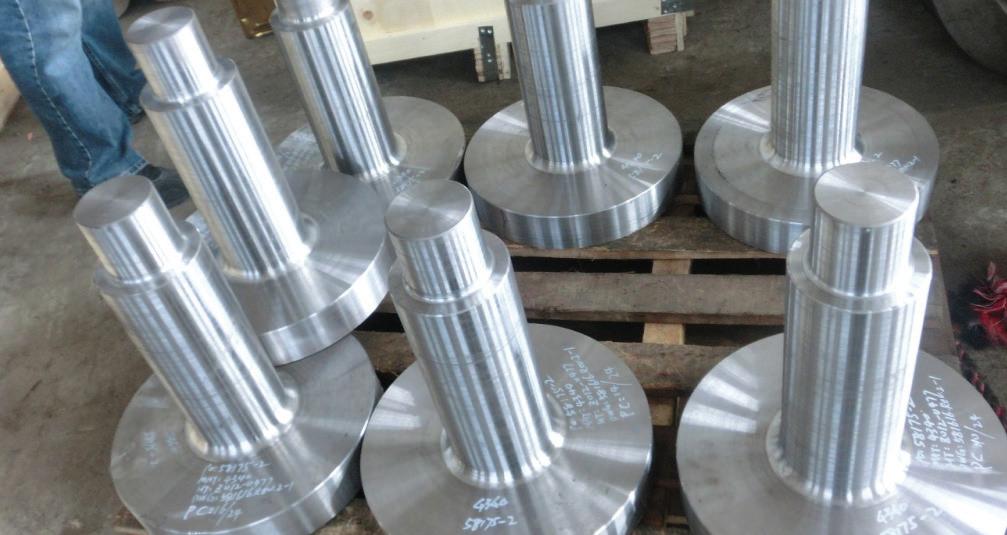
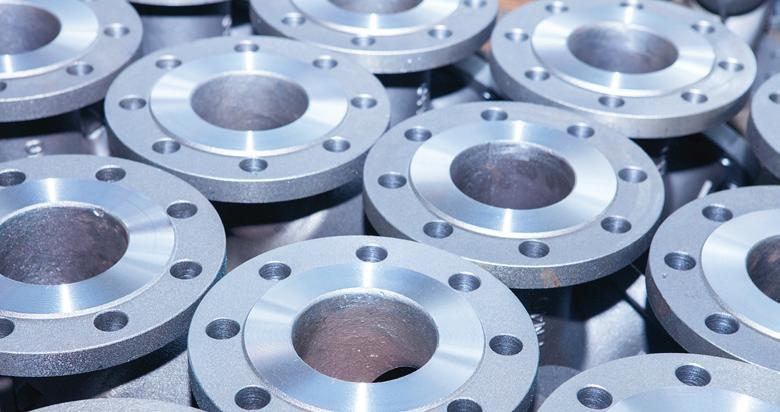
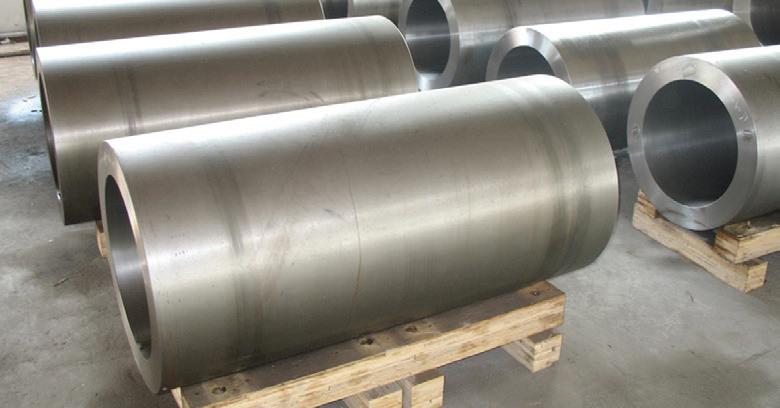
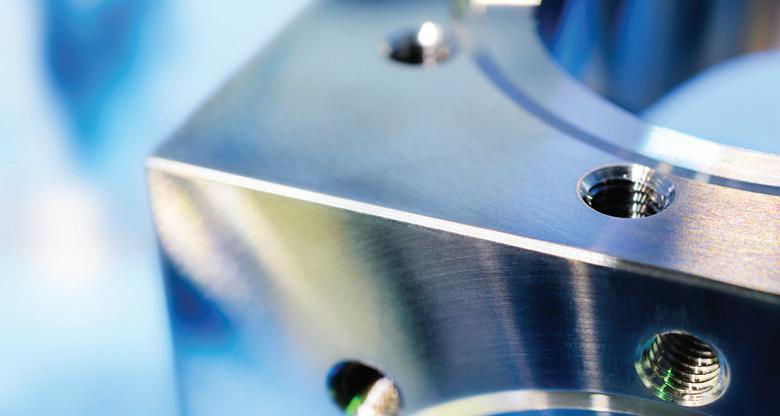
MANUFACTURING TIDBITS: ROOFTOP SOLAR PANELS: EMPOWERING ONE-THIRD OF THE US MANUFACTURING SECTOR
If things are slowing down, you may have some spare time on your hands. When things are slow, it will be more productive to review and plan than to worry.
We have all heard about Industry 4.0, Big Data, and disruptions in manufacturing. Many manufacturers are adopting new approaches to production through changes in their software systems, which has added to the burden of getting the goods out the door over the last three years or more. Now, with many indicators pointing to slower growth, manufacturers have time to assess how new technology is performing, identify where improvements lie, and how operations can be tweaked for peak performance.
Implementing an ERP system when business is booming is often a pressure cooker that adds more stress than productivity. Implementing software or making production changes when things are slower allows people to think through the problems they are trying to solve rather than trying to solve problems when capacity utilization is running in the high 80s. Now is the time to identify and address what could work better and where improvements can be made in preparation for the next economic expansion.
There is another critical area of manufacturing we hear less about but is of great importance: marketing. If a recession is looming, the best way to adapt is to find new customers, gain new business from existing customers, and look into new product development to sell to new and existing customers or entirely new markets when the next expansion begins.
Marketing and manufacturing are often distant cousins instead of close relatives. Manufacturers are great at making things but often don’t take the time to tell their stories. There are so many ways to get the word out beyond the traditional printed brochure or catalog, and many manufacturers have adopted some but may not be leveraging all. Most manufacturers have converted their print catalogs or brochures to digital versions. The beauty of a digital catalog is that the pdf file can be changed and uploaded to replace a previous version within minutes after the change. And fixing a typo or any other mistake is quick and simple, instead of throwing away thousands of printed catalogs containing errors.
The digital world of the Internet includes opportunities for manufacturers to market their goods and services for free. Most manufacturers have websites, which is the first place prospective customers go to check out a new supplier or their product. Then there is a free business page on Facebook where manufacturers can post fresh updates, show pictures, and convey success stories. Facebook adds the element of showing people in the workplace, not just products or services. Next would be LinkedIn and Twitter. However, the second most searched engine on the Internet is YouTube, which is a video platform. Be sure to post videos on both YouTube and Rumble; Rumble is an up-and-comer video platform. Before dismissing video as too complex, time-consuming, or costly, ask the staff if one of them can help create and post videos on YouTube. The person sweeping the floor may be highly skilled with YouTube. If they are younger than 25, they are likely very familiar with online video.
To reiterate, Facebook is free. Twitter is free. LinkedIn has a free version. YouTube is free. Rumble is free. All of these are for lead generation, for interested people to make direct contact, or to attract people to the website. Posting a digital catalog is free after the investment in creating it. In addition, a page or two from that pdf file can be used as standalone flyers or email attachments sent to remind customers or prospects of a product line or service area of the business.
A digital catalog can become the compendium of all the manufacturer’s marketing materials rather than having documents, pictures, graphics, brochures, and catalogs developed separately by different departments and wondering what documents are current, what needs to be updated, and where the source files are located. A little review and planning can bring the marketing efforts for manufacturers into focus and yield better messaging and improved control. This also translates into better cost control of marketing.
The economy will always have ups and downs. If activity is slowing at your shop, consider the above for review and planning. n
Based on what we’ve seen over the past few months, coupled with ongoing data from ASIS, the coming global scenario for manufacturing industrial production is tending toward a slight improvement starting in early fall to the beginning of 2024, then a slow drop in the summer-fall of 2024.
Here there will be a positive couple of months before another drop over the next month or so. One example is the movement in both Primary Metals and Fabricated Metal Products. Keep an eye on Chemical Products, a key input for many manufacturers that is presently in contraction.
“The Economist” is looking for the U.S. economy to experience a mild technical recession in 2023, with two consecutive quarters of contraction, with a larger decline in the third quarter. Although downside risks persist, they still expect this to feel more like a business-cycle slowdown than a
typical recession, with a modest recovery in 2024. Consumer sentiment is above the levels experienced at the end of 2022. If consumer sentiment, driven by their security about their employment, takes a downturn, then the overall economy will slide negatively.
The recent trend for users of steel, copper, and aluminum is expected to continue for a while, wherein the recent overall production is slightly up. This is due effectively to an improvement in Asia, with continuing declines in the U.S. and Europe, where demand is down. There is very little movement in the prices of non-ferrous metals.
There is ongoing improvement in the aerospace and automotive sectors in the U.S., Europe, and China. The electrical and construction areas are also doing well.
Global steel users report a marginal improvement in operating conditions in April, with renewed rises in production, new orders, and employment. There were returns to growth in the U.S. and Asia, whereas in Europe, the rate of decline quickened to the fastest for four months.
J.P. Morgan’s global economist, Bennett Parrish, comments on the May situation, which, although speaking on things as they were a couple of months ago, looks to describe what may well come to pass: “The May
PMI surveys suggest continued positive momentum in the global manufacturing sector. The global output index, boosted by a sizeable gain in China, strengthened 0.7 points and is consistent with a 1.6% gain in global factory output. However, the internals of the May PMIs temper the positive signal from the output index and suggest lackluster growth in goods demand. The new orders PMI ticked down again last month to remain below the 50 mark. Also concerning is that the ratio of orders to finished goods inventories held stable at 0.99, a level consistent with output declines. A move back down in the employment index reversed the April improvement.”
It should also be noted that were it not for India and Thailand, global results would have looked much different. So far, the economy is slowing globally and about equally across all countries.
The Outlook remains tepid, as economies are just entering a recessionary phase. A soft landing could mean a protracted but shallow recession. A hard landing might mean a deep recession with a recovery sooner.
There are many ways that supply chains can get disrupted: ships sink, get stuck, or face port logjams; cargo planes have to take longer routes because of restricted airspace; trucks face so much city congestion that millions of dollars are lost; freight trains get looted; and bicycle delivery workers deal with people stealing their bikes. Of course, there’s also COVID-19, the Great Resignation, tariffs, and all the other usual suspects.
It’s stressful, and that’s why today’s supply chain professionals — from the procurement officers negotiating prices to the warehouse workers who manage inventory and beyond — are heroes. You’re managing the challenges so that we can get the goods.
Here are 12 actionable steps to take to ensure your supply chain is bulletproof.
When raw materials are skyrocketing and delays are stretching, it’s tempting to put the burden on the vendor. Not only does that not change the reality of the situation, but making unrealistic demands, unleashing your frustration on someone who is likely already stressed, and taking retaliatory actions for issues that are not the vendor’s fault can sour your relationship with the vendor. They may even decide to drop your business in favor of another.
Instead, work with your vendor toward common goals, a strategy that saved the Kellogg Company from experiencing further pain points during the pandemic. It’s also a tactic the startup Filti used, saying, “We have great relationships with our media supplier, our corrugate supplier, and every other supplier that we really depend on. We all mutually benefit by working hard to achieve the same common goal.”
Building a symbiotic relationship with a vendor doesn’t mean not doing your due diligence. As ProPurchaser explained, suppliers will inform procurement officers when raw material costs go up, but they’re silent when these costs fall. It’s up to procurement professionals therefore to track the fluctuations and negotiate accordingly. ProPurchaser told us, “Sales reps actually like Silent Slopes because they get paid for closing. If price is an obstacle, they’ll be anxious to remove it. Arming sales reps with Silent Slopes allows them to champion your joint cause to their management team.”
3. Over-communicate
Communicate early and often. It’s easy to assume that everyone on your team and all of your vendors are fully aware of changes or know to continue with standard operating procedures during times of supply chain disruptions. While you shouldn’t inundate staff and vendors with messages, sending short, regular communications can build trust, help maintain morale and productivity, and refresh your team on basic policies and resources they may have forgotten about or don’t know exist.
When it comes to communication, documentation is key. Handbooks, online resources, and emails serve as valuable information that can be referred back to. However, depending on whom you want to reach and the context, instant messaging platforms, the telephone, and in-person meetings each have their place.
A shockingly low number of companies — 6% — indicate that they have complete visibility on their supply
chains. Visibility has long been a challenge in supply chains because there are so many moving parts and gatekeepers working across different time zones. Cloud-based supply chain visibility software can provide real-time data that helps businesses improve efficiency, reduce cost, decrease the impact of disruptions, and increase transparency and trust.
Enterprise resource planning (ERP) is the main hub for operations, logistics, inventory, and operations. ERP systems have been around for a long time, so even if you already have one, it may be time for a new one that can integrate with the latest technology. [This checklist can help you determine if your ERP is performing to its fullest potential.]
A transportation management system (TMS) is a logistics tool that offers visibility over transportation. It can determine the best carriers, optimize routes, track shipments, perform audits, ensure deliveries are trade compliant, and provide KPIs. It can be used for both raw materials coming to the factory as well as finished products headed to the warehouse.
A warehouse management system (WMS) manages on-site products. The software provides an overview of inventory, organizes the warehouse and optimizes the space available, and helps manage order fulfillment.
5. Consider Additive Manufacturing
“When you talk about large supply chain disruptions such as a pandemic, 3D printing became very popular because the minimum requirement was a 3D model,” Greg Paulsen, director of application engineering at Xometry, told us. “If that 3D model is able to be generated — whether it’s for emergency personal protective equipment or a stopgap solution for a
component that was sourced internationally — they could get near-immediate results.” [Xometry offers pricing, lead time, and DFM feedback through the Xometry Instant Quoting Engine.]
It’s no wonder the 3D printing market is expected to quadruple, reaching more than $50 billion by 2030. Even if you plan to continue with traditional manufacturing, it’s forward-thinking to research your additive manufacturing options now so you have a game plan in place should you need to pivot.
While gigantic warehouses like the Boeing Everett Factory are the ones that make the headlines, having numerous small warehouses strategically situated at locations relevant to your production facility and to your clients could actually be more beneficial to running smooth operations. Micro warehouses also provide the opportunity to open customer fulfillment centers in cities, which translates to speedier delivery times.
By 2030, it’s predicted that the global commercial warehouse robotics market will reach $51 billion. If you’re not taking advantage of robotics, you will likely not be able to keep up with your competitors.
Automation is not just a “nice to have” anymore; it’s a “must have,” Hanna Yanovsky, general manager of Caja Robotic, told Inbound Logistics.
“By bringing automation to the U.S. and increasing the amount of automation in American factories, we’re creating a much more defensible supply chain,” Saman Farid, CEO of Formic Technologies, told Thomas Insights.
8.
Digital tools like the ones mentioned above can gather and track data. Machine learning and predictive analytics take the guesswork out of forecasting consumer demand. According to a recent McKinsey survey, most companies today are using artificial intelligence (AI) to increase their revenue: “In supply-chain management,
respondents often cite sales and demand forecasting and spend analytics as use cases that generate revenue.”
Fashion retailer H&M hired more than 200 data scientists so they could predict what they’ll need to restock and what the next big trend will be. Its competitor Zara, meanwhile, uses AI to not only predict style but also what colors and sizes will be most popular.
Part of bulletproofing your supply chain is retaining and growing your customer base, and that’s why, particularly amid product gaffes and supply chain hurdles, it’s important to have a high level of customer service.
Facing a shortage of delivery drivers, Domino’s got creative with a marketing gimmick to improve customer service by incentivizing pizza lovers to pick up their own pizza. Usually, customers tip pizza delivery drivers. Domino’s turned the tables and is now tipping online carryout customers.
“We’ve been very upfront with customers,” Michael Shaughnessy, Senior Vice President of Operations at Balsam Brands, told Inbound Logistics, speaking of holiday logistics hurdles. “We want to make sure expectations are set and met.” The company provided product availability information on its website and, when inventory was depleted, suggestions for similar products.
When it comes to quality check failures and product recalls, it’s especially important to get in front of the situation. In our article “How to Survive a Product Recall,” suggestions include reaching out to customers, communicating openly, apologizing, and investigating the problem.
Keep your ear out about anything that may impact supply chains. Subscribe to publications like the Thomas Industry Update newsletter and Inbound Logistics to get industry updates and thought leadership. It’s important to also stay up-to-date
on current events and politics, since weather forecasts, inflation, tariffs, and other news can impact supply chains. Additionally, part of communicating with your staff, vendors, and customers is listening to any intel they may have.
Automate dates in your calendar to take time out on a regular basis to systematically review your supply chain. You will want to take this opportunity to conduct training to ensure everyone on your staff is following procedures correctly, is informed of any policy and compliance changes, and has a thorough knowledge of your product and service offerings. You’ll also want to perform an audit with your vendors to confirm they are following your company instructions as well as legal requirements.
You can use your software to analyze data to ensure every aspect of your supply chain is functioning at its optimal level. Take time to audit any machinery and technology you
use to ensure it is in shape and that it is still competitive. Perform a deep dive into your company’s financials to see where your money can go further and if your budget may provide you with tools that can accelerate your business — keeping in mind that employees are your biggest asset and that investing in their education and salaries can benefit your company in the long run. And of course, look for common bottlenecks and find ways to clear them.
This checklist can help better manage disruptions, but supply chains can be unpredictable. Because of the global nature of supply chains — even if you manufacture in the United States, raw materials and shipping products may come from overseas — it may sometimes feel all-consuming. But even heroes need rest.
It’s important to keep your work-life balance in check. 83% of U.S. workers face work-related stress, and this stress leads to missing work, which can cost businesses up to $300 billion a year. One study found that transportation workers are among the most likely to not sleep the recommended hours, which can lead to mistakes on the job. You cannot be your best at work when you are running on empty. Spend time with your family and friends. Practice self-care by making meals with fresh, whole ingredients and by exercising regularly. Do the hobbies you love, and partake in new ones that will enrich your life and provide you with new skills. Travel — even if it’s just reading books that transport you. All of these things can inspire and motivate you in and out of work.n
In early 2022, Bruce Crumley reported for DRONEDJ that the company Natilus, founded in San Diego in 2016, was feeling upbeat after securing $6 billion worth of purchase commitments for hundreds of aircraft from various aviation business clients. This is about a company involved in the business of commercial freight drones, orders for 460 units, and the development of the concept by size and load capacity.
Orders have come from both major airlines and integrator customers. The company further announced a letter of intent from Flexport, a supply chain tech specialist, to buy two 100T Natilus aircraft, and secure an option
for a third, thus completing a $900 million investment in Natilus. Natilus is out to revolutionize air freight transportation through innovation and advanced technologies, to make air freight costs competitive to cargo shipping, and to improve delivery times dramatically.
Natilus has designed and developed a blended-wing, autonomous global air freight system that can offer services at a fraction of the cost of today’s air transport while improving the environment.
The Kona, the model presently receiving the most attention, has a built-in “diamond” cargo bay, which
gives the aircraft 60% more volume and reduces flight costs by 60%. This model is expected to rank as the biggest commercial freight drone when airborne in 2024, but the short-haul Kona, at 3.8 tons, is only the beginning for Natilus. Other cargo planes are coming through at 60 tons, 100 tons, and 130 tons.
It may still be some time before Natilus gets its full-scale prototypes off the ground, but the aerospace industry is already showing sufficient interest in the drones, and together with the $6.8 billion in total commitments and the 460 aircraft scheduled for delivery, the future looks positive. Natilus has been working with
Janicki, Pratt & Whitney Canada, Collins Aerospace, and Siemens to develop composite designs, engines, and loading systems for its aircraft. The company also said it has secured purchase agreements from customers, including Astral Aviation, Ameriflight, Aurora, Volatus Aviation, Dymond, and Flexport.
The logic behind the concept might best be explained by Natilus’ CEO Aleksey Matyushev, who says, “Today, there are only two ways to move cargo internationally: by air and by sea. The difference between the cost and time of these two modes of transportation is dramatic. Sea freight is currently 13 times less expensive than air freight; but 50 times slower in delivery. Natilus intends to revolutionize the transport industry by providing the timeliness of air freight at an affordable cost reduction of 60%, making air cargo transportation substantially more competitive.”
Natilus has designed and developed a blended-wing, autonomous global air freight system that can offer services at a fraction of the cost of today’s transport while reducing negative impacts on our environment. The aircraft is actually designed around cargo, and can hold a large
configuration of standard pallets, outsized cargo, without a contouring requirement. All is watched over by a remote pilot.
Natilus recently completed multiple flight tests for the subscale prototype of its Kona regional aircraft. The tests were carried out in California, and the prototype reached airspeeds of up to 70 miles per hour. The work also showed that the company’s blendedwing-body aircraft is stable enough to fly without an advanced autopilot platform.
Natilus is now shifting its focus to completing the full-scale, 85-footlong Kona prototype. The company said its full-sized drone will be able to carry up to 90,000 pounds of freight. The design will be such that the Kona will take off and land on unpaved runways that are as short as 800 meters, which Natilus hopes will open up new air cargo markets. Natilus is developing its cargo drones tailored to several vehicle categories. Those include eight-ton payload short-haul feeder, 60-ton payload medium/long range, 100-ton payload long-range, and 130-ton payload long-range UAVs (Unmanned Aerial Vehicles.) The company says that in addition to the 60% reduction in operating costs, its
craft will permit users to increase volume-per-aircraft loads by an equal amount, while cutting carbon emissions by 50% .
Volatus said recently that it would buy Natilus’ N3.8T twin-engine turboprop cargo drones to expand its freight hauling activities. The aircraft, which is expected to go into operation in 2025, will have a maximum takeoff weight of 19,000 lbs., 1,035-mile range, and carry up to 8,500 lbs. of payloads in standardized LD3 containers.
Natilus says software in its ground control system minimizes pilot training and workload, permitting a single operator to fly three of the cargo drones at once. Its cloud-based navigation system interfaces with satellites to communicate with and control the craft, and is backed up by an onboard autopilot.
The company says industry analyses currently estimate the market for autonomous cargo drones at $280 billion, which would more than double the air freight market to $470 billion.
Freight movement efficiency with cost and carbon emission reductions will continue to expand into the transit system, especially as freight companies encounter the 3-fold increase in cost to acquire each new electric semi truck and the absence of charging stations and distance capabilities of the current truck models. One way or another, the freight will move with innovations like cargo drones.
Author profile: Royce Lowe, Manufacturing Talk Radio, UK and EU International Correspondent, Contributing Writer, Manufacturing Outlook. n
As the world transitions toward a greener future, renewable energy sources are gaining traction across various industries. Among them, rooftop solar panels have emerged as a sustainable solution for generating electricity while reducing carbon emissions. Not only are solar panels becoming increasingly affordable and efficient, but they also have the
potential to power a significant portion of the U.S. manufacturing sector. The expansive, generally flat roofs of manufacturing facilities, not to mention other facilities like warehouses and even big box store, make rooftop solar panels attractive in driving sustainability and powering up to one-third of the country’s manufacturing sector.
Over the past decade, solar power has witnessed remarkable growth as a viable alternative to traditional energy sources. Falling costs, technological advancements, and government incentives have played a crucial role in driving the adoption of solar panels. Today, solar energy is being
harnessed not only at utility-scale solar farms but also at individual homes and commercial buildings through rooftop solar installations. One conflict is who makes them. Currently, U.S. government regulations do not favor U.S. manufacturers, and allow China to circumvent tariffs by completing and shipping Chinese panels from other S.E. Asia countries.
Cost Savings: By installing rooftop solar panels, manufacturers can significantly reduce their energy bills, thereby improving their bottom line. With access to abundant rooftop sunlight, solar power allows manufacturers to generate electricity on-site, minimizing reliance on ever-increasing power grid costs. In addition, excess energy can be sold to the grid, helping balance the ROI equation.
Environmental Sustainability: One of the most significant advantages of rooftop solar panels is their positive impact on the environment. By producing clean energy, manufacturers can lower their carbon footprint and contribute to mitigating climate change. The manufacturing sector, which traditionally consumes vast amounts of energy, has a unique opportunity to transition to sustainable practices and lead the way toward a greener future.
Energy Resilience: Rooftop solar panels provide manufacturers with energy independence and resilience. By generating electricity on-site, manufacturers can reduce their vulnerability to power outages, grid failures, and price fluctuations in the energy market. This reliability ensures uninterrupted operations, allowing manufacturers to stay competitive even during challenging times. Manufacturers in countries with
unreliable power can help themselves by installing solar panels on their plant rooftops.
According to a recent study by the National Renewable Energy Laboratory (NREL), the U.S. manufacturing sector holds immense potential for solar energy adoption. The study found that roughly one-third of the manufacturing sector’s electricity demand could be met by rooftop solar installations.
To put this into perspective, the NREL study estimated that installing solar panels on the available rooftop space of manufacturing facilities alone could generate approximately 227 terawatt-hours (TWh) of electricity annually. This is equivalent to powering around 21 million homes or reducing carbon dioxide emissions by nearly 150 million metric tons each year.
While the potential is enormous, there are several challenges to widespread adoption of rooftop solar panels in the manufacturing sector. These include initial investment costs, limited rooftop space, and the need for favorable policies and regulations. However, technological advancements, declining costs, and government incentives can help overcome these hurdles.
To unlock the full potential of solar power in manufacturing, policymakers can introduce targeted financial incentives, such as tax credits and grants, to encourage manufacturers to invest in solar installations. Additionally, implementing favorable net metering policies and simplifying the permitting process can accelerate adoption.
Rooftop solar panels have the capacity to revolutionize the U.S. manufacturing sector by providing sustainable, cost-effective, and resilient energy solutions. With the potential to power one-third of the U.S. manufacturing sector’s electricity demand, solar energy offers a significant opportunity for manufacturers to reduce costs, lower their environmental impact, and enhance energy resilience. By embracing rooftop solar installations and implementing supportive policies, the manufacturing sector can take a giant leap toward a cleaner, more sustainable future. Amplify this globally to all companies who have available rooftop space, and the result would be a siesmic shift from fossils fuels to a renewable energy resource
Tim Grady is Editor-in-Chief of Manufacturing Outlook and a host on Manufacturing Talk Radio. He can be reached at timgrady@mfgtalkradio. com. n
Economic activity in the manufacturing sector contracted in June for the eighth consecutive month following a 28-month period of growth, say the nation’s supply executives in the latest Manufacturing ISM® Report On Business®
The June Manufacturing PMI® registered 46 percent. The New Orders Index remained in contraction territory at 45.6 percent, 3 percentage points higher than the figure of 42.6 percent recorded in May. The Production Index reading of 46.7 percent is a 4.4-percentage point decrease compared to May’s figure of 51.1 percent. The Prices Index registered 41.8 percent, down 2.4 percentage points compared to the May figure of 44.2 percent. The Backlog of Orders Index registered 38.7 percent, 1.2 percentage points higher than the May reading of 37.5 percent. The Employment Index dropped into contraction, registering 48.1 percent, down 3.3 percentage points from May’s reading of 51.4 percent. The Supplier Deliveries Index figure of 45.7 percent is 2.2 percentage points higher than the 43.5 percent recorded in May. For context on the current seven-month run of faster supplier delivery performance: The Supplier Deliveries Index’s lowest reading in the last 14 years was in March 2009 (43.2 percent).
The four manufacturing industries that reported growth in June are: Printing & Related Support Activities; Nonmetallic Mineral Products; Primary Metals; and Transportation Equipment. ISM
Analysis by Timothy R.
Fiore, CPSM, C.P.M.Chair of the Institute for Supply Management® Manufacturing Business Survey Committee
The U.S. manufacturing sector contracted in June, as the Manufacturing PMI® registered 46 percent, 0.9 percentage point lower than the reading of 46.9 percent recorded in May. This is the eighth month of contraction and continuation of a downward trend that began in June 2022. That trend is reflected in the Manufacturing PMI®’s 12-month average falling to 48.8 percent. Of the five subindexes that directly factor into the Manufacturing PMI®, none are in growth territory. Of the six biggest manufacturing industries, only one (Transportation Equipment) registered growth in June.
Commodities Up in Price: Electrical Components (8); Electronic Components (5); and Steel — Carbon.
Commodities Down in Price: Aluminum; Aluminum Products; Corrugate (7); Crude Oil; Diesel (2); Freight (8); Ocean Freight; Pallets (2); Paper (2); Plastic Resins (13); Polypropylene (2); Steel (3); Steel - Hot Rolled (2); Steel Products; and Synthetic Rubber.
Commodities in Short Supply: Electrical Components (33); Electrical Controls and Equipment; Electronic Assemblies; Electronic Components (31); Hydraulic Components; Semiconductors (31); and Titanium.
ISM’s New Orders Index contracted for the 10th consecutive month in June, registering 45.6 percent. The five manufacturing industries that reported growth in new orders in June are: Printing & Related Support Activities; Nonmetallic Mineral Products; Furniture & Related Products; Transportation Equipment; and Paper Products.
The Production Index registered 46.7 percent. The eight industries reporting growth in production during the month of June are, in order: Nonmetallic Mineral Products; Paper Products; Furniture & Related Products; Primary Metals; Fabricated Metal Products; Transportation Equipment; Machinery; and Computer & Electronic Products.
ISM’s Employment Index registered 48.1 percent. Of 18 manufacturing industries, six reported employment growth in June, in the following order: Printing & Related Support Activities; Furniture & Related Products; Machinery; Fabricated Metal Products; Transportation Equipment; and Food, Beverage & Tobacco Products.
The delivery performance of suppliers to manufacturing organizations was faster for the ninth straight month in June, as the Supplier Deliveries Index registered 45.7 percent. Six of 18 manufacturing industries reported slower supplier deliveries in June, in the following order: Textile Mills; Wood Products; Petroleum & Coal Products; Primary Metals; Miscellaneous Manufacturing‡; and Paper Products.
The Inventories Index registered 44 percent. Of 18 manufacturing industries, the three reporting higher inventories in June are: Textile Mills; Primary Metals; and Computer & Electronic Products.
ISM’s Customers’ Inventories Index registered 46.2 percent. The six industries reporting customers’ inventories as too high in June are, in order: Paper Products; Plastics & Rubber Products; Electrical Equipment, Appliances & Components; Fabricated Metal Products; Chemical Products; and Computer & Electronic Products.
The ISM Prices Index registered 41.8 percent. In June, three industries reported paying increased prices for raw materials: Textile Mills; Nonmetallic Mineral Products; and Computer & Electronic Products.
ISM’s Backlog of Orders Index registered 38.7 percent. No industries reported growth in order backlogs in June. The 13 industries reporting lower backlogs in June — in the following order — are: Textile Mills; Plastics & Rubber Products; Wood Products; Paper Products; Food, Beverage & Tobacco Products; Fabricated Metal Products; Electrical Equipment, Appliances & Components; Computer & Electronic Products; Miscellaneous Manufacturing‡; Chemical Products; Transportation Equipment; Primary Metals; and Machinery.
ISM’s New Export Orders Index registered 47.3 percent. Two industries reported growth in new export orders in June: Printing & Related Support Activities; and Miscellaneous Manufacturing‡
ISM’s Imports Index registered 49.3 percent. The four industries reporting an increase in import volumes in June are: Petroleum & Coal Products; Nonmetallic Mineral Products; Primary Metals; and Food, Beverage & Tobacco Products.
The shipments component of the Cass Freight Index® fell 1.6% m/m in June and fell 1.9% m/m in seasonally adjusted (SA) terms.
On a y/y basis, the index was 4.7% lower in June, after a 5.6% decline in May.
Freight markets continue to work through a downcycle which featured its first y/y decline 18 months ago. The past three downcycles have ranged from 21 to 28 months. Declining real retail sales trends and ongoing destocking remain the primary headwinds to freight volumes, but dynamics are shifting as real incomes improve and the worst of the destock is in the rearview.
In seasonally adjusted terms, the index is now 12% below the December 2021 cycle peak, slightly greater than the peak-totrough declines in two of the three downcycles in the past dozen years.
With normal seasonality, this index would fall slightly m/m in July and decline about 6% y/y.
The expenditures component of the Cass Freight Index, which measures the total amount spent on freight, fell 2.6% m/m and 24.5% y/y in June.
With shipments down 1.6% m/m in June (compared to a decline in total spending of 2.6%), we infer
rates were down 1.0% m/m (see our inferred rates data series below).
On an SA basis, this index declined 2.8% m/m, with shipments down 1.9% and rates down 0.9%. This index includes changes in fuel, modal mix, intramodal mix, and accessorial charges, so is a bit more volatile than the cleaner Cass Truckload Linehaul Index®.
The expenditures component of the Cass Freight Index rose 23% in 2022, after a record 38% increase in 2021, but is set to decline about 17% in 2023, assuming normal seasonal patterns from here. With both freight volume and rates under pressure at this point in the cycle, that continued
assumption is likely optimistic, so we may be looking at a ~20% decline in freight spending this year.
The rates embedded in the two components of the Cass Freight Index declined 21% y/y in June, after falling 11% in May.
Cass Inferred Freight Rates decreased 0.9% m/m SA after a 7.1% decline in May, as contract rates reset lower and, in part, due to lower fuel prices. Based on the normal seasonal pattern, this index would rise slightly m/m in July and the y/y decline would tighten to about 17% on noisy comparisons.
We estimate lower fuel prices are knocking about 5% off freight rates y/y starting in mid-Q2.
While fuel is a big factor, there’s clearly also still market pressure on rates. Cass Inferred Freight Rates are a simple calculation of the Cass Freight Index data—expenditures divided by shipments—producing a data set that explains the overall movement in cost per shipment. The data set is diversified among all modes, with truckload (TL) representing more than half of the dollars, followed by lessthan-truckload (LTL), rail, parcel, and so on.
The Cass Truckload Linehaul Index, which measures the per-mile change in linehaul rates, fell 0.4% m/m in June to 142.3, after a 2.6% m/m decline in May.
Although the June decline was smaller, the 1.5% average decline of the past two months is still nearly twice the 0.8% average of the prior six months.
On a y/y basis, the Cass Truckload Linehaul Index fell 14.1% y/y in June after a 15.3% y/y decline in May. As a broad truckload market indicator, this index includes both spot and contract freight. With spot rates already down significantly, the larger contract market is likely to continue adjusting down.
The volume downturn appears to be in the later innings, and after a long soft patch, we see the U.S. freight transportation industry on the cusp of a new cycle. We characterize this phase of the cycle as the bottoming phase.
One key ingredient of the bottoming phase, which is absent so far this cycle, is lower equipment production. As Class 8 build rates remain elevated, pressure remains on fleets to seat these tractors.
Our fleet friends suggest that some of the recent strength in Bureau of Labor Statistics (BLS) employment data is owner-operators moving back to forhire jobs.
Thus, the BLS trucking jobs data likely overstates industry employment trends but has been resilient nonetheless, leading to fewer hours worked. In the months to come, rebalancing will continue, but this dynamic threatens to prolong the bottoming process. n
Of course, the answer is to believe the intrepid Manufacturing Talk Radio economist. On the other hand, we need to remember the quote from John Kenneth Galbraith – “The sole function of economic forecasting is to make astrology look respectable.” The bottom line is that there is never a point when the economic data is stable, as we are dealing with human behavior, and people are anything but stable. It has been pointed out that the U.S. is a country so large and diverse that it can easily host both recession and growth – it all depends on what industry one is in and even what part of the country.
Then there is the issue of Canada and Mexico, two nations that are deeply connected to the U.S. and are forced to react to what happens south and north of their border. Now that all those disclaimers are out of the way – what
is the prognosis? Are we headed for a recession? Are we already in one? How deep and how long?
Let’s get the depressing stuff out of the way first. We can finish with the optimistic assessments. There are several sets of indicators that have been routinely referenced as recessionary. The latest set of Leading Economic Indicators produced by the Conference Board is sitting at the lowest level in 23 years. If one looks back over the last couple of decades, there have been periods when the LEI has been in this position – 2000-2001, 2007-2009, and 2020. Thus far, the data is not showing a decline as deep as in those years, but the slump is significant.
Given the importance of the consumer in the U.S. economy, their performance is critical. At the moment, fully 65%
of consumers are living paycheck to paycheck due to the surge of inflation over the last couple of years. Of those making under $50,000, fully 75% are spending everything they make and have been sliding into debt. There has been a significant level of caution and angst showing up in the banking sector as credit standards keep tightening. There has been a reduction of over $100 billion in lending activity, accelerated by the banking crisis in March. Lately, banks have been trying to sell off their commercial property loans (even at a loss) as they anticipate the market dropping further. They want to sell while there is still some demand for these investments.
The U.S. did manage to dodge the selfinflicted wound of default by approving the increase in the debt ceiling, but now Treasury will be issuing and
selling over a trillion dollars in bonds, and that will have an impact on bond yields as well as other parts of the bond market. All this drama in the bond market has created another of those recessionary signs – an inverted bond market. This is when the relationship between the two-year bond and the ten-year bond flip. The short-term bonds react to interest rate changes, and the long-term bonds react more to prospects for economic growth. Investors think that inflation threats will keep the Fed pushing rates higher, and that slows the economy. The yields have been inverted for months, and an inversion often signals a recession or some kind of downturn eventually. By now, you have all elected to take to your bed with a strong drink in hand. Is it as bad as all this would suggest? Maybe not. There are other currents that seem to be telling a different story or at least a more complex one.
We can start with the behavior of the labor market. In any other recessionary period over the last several decades, there have been big layoffs and a sharp spike in the rate of unemployment. Every month there have been grim forecasts asserting that the jobless rate is due to spike and that hiring would fall off. Last month the economy added another 339,000 jobs. The unemployment rate moved up slightly, but all of that gain was from people in the U-6 category shifting to U-3. This means those discouraged workers counted in U-6 started to reenter the formal search for work and got counted in U-3. Business is still reluctant to lay people off as they have had such a difficult time finding these employees in the first place.
Another contradictory piece of data comes from corporate investment. Spending on capex is still setting records as companies need to expand to accommodate some of the big changes in the economy. Two major drivers for this investment have been an expansion
of robotics and technology as well as the surge in reshoring, as companies have lost faith in the supply chain and the whole concept of JIT. If one can’t find the needed workers, there are few other options other than investing in robotics. The breakdown of the supply chain and suspicion regarding the future of China trade has convinced many to return production to the US (a trillion dollars’ worth last year alone). There are certainly sectors that have not been performing very well, but there are other sectors that are doing very well. Automotive continues its very strong run, and the data on both durable goods and factory orders has remained robust. In fact, much of the data we look at shows solid performance, and even the declines are relatively minor.
A lot of the data regarding Canada has been trending more in a positive direction. Among the other G-7 nations, Canada has been outperforming. This group includes the U.S., UK, Japan, France, Germany, and Italy. The jobless rate has been very low as 830,000 more Canadians are employed than prior to the pandemic. As with every other nation, Canada has been hit hard by inflation. The rate of inflation has fallen for the last eight months in a row, but it is still roughly twice what the Bank of Canada would prefer. The rates have been pushed up by the BoC in response. The peak for inflation was in June of 2022, when it hit 8.1%. Since then, the rate has come down to about 5.0%. That takes it lower than almost any of the other G-7 states; only Japan sports a lower rate at around 4.0%.
The Canadian economy remains very sensitive to the U.S. manufacturing sector as fully 65% of Canadian operations are either owned by U.S. entities or are nearly entirely dependent on the U.S. partner. The other pillars of the Canadian economy are oil/
gas operations and agriculture. The volatility of the oil market has affected Canadian commodity markets, and the weather has been impacting the farm sector. The wildfires have already had a major impact on the economy due to the resources that have been brought to fight the outbreaks. There have been over 400 of them thus far, and an area the size of the Netherlands has been destroyed – over 120,000 people have been displaced. There is an economic impact to that, but difficult to measure.
The Mexican economy grew by 3.7% in the first quarter, and that is the sixth straight quarter of growth. There was an expectation of 3.9% growth, so the actual performance was a bit less than expected. The data on Q2 is still preliminary, but it appears to be on track for a seventh straight growth quarter. The concern is based on some decline in business activity just recently. The service sector remains strong with 1.5% growth, but there has been a 2.8% decline in primary sectors such as farming, forestry, fishing, and mining (which includes the oil and gas sector). Inflation remains a major concern, and the central bank is still suggesting rate hikes, although the recent data has many discussing a more dovish approach. If there is a jump in jobless data or these economic sectors continue to sag, the possibility of a rate reduction improves. The informal rate of unemployment is still well over 30%.
Author profile: Dr. Christopher Kuehl (Ph.D.) is a Managing Director of Armada Corporate Intelligence and one of the co-founders of the company in 1999. He has been Armada’s economic analyst and has worked with a wide variety of private clients and professional associations in the last ten years. He is the Chief Economist for the National Association for Credit Management and is on the Board of Advisors for their global division – Finance, Credit and International Business. n
The Economist magazine recently did a survey on the state, or lack of, manufacturing in South America. This is a continent that is overflowing with natural resources the way Argentina once was with beef. All these resources need to be taken from the ground, and they all need workers, but it seems that the workers they have are not very productive. And the mining industries detract from the manufacturing industries. So South America doesn’t produce the quantity of goods it should. An awful lot of the mining industry is foreign-owned, and that’s not good, particularly since the owners are just taking the resources someplace else for refining and use.
In 1962, Latin America’s income per person was three times that of East Asia, and by 2012 both regions had the same level. East Asia’s was some 40% higher by 2022, whereas Latin America stalled. When the differences in purchasing power are taken into
account, the GDP per person in Latin America has been stuck at little more than a quarter of that of their neighbors in the U.S. for the last three decades. The World Bank says that between 2010 and 2020, Latin America was the world’s slowest-growing regional economy. And it looks to be getting worse. Growth is slowing. The pandemic hit Latin America hard, with the highest number of excess deaths of any region between March 2020 and October 2021.
The workers are not very productive. The World Bank, in its efforts to measure productivity, places Latin American workers as the second-least productive in the world, behind the Middle East. Maybe there’s insufficient investment in new technology, infrastructure, and education. Schools in the region, for example, remained fully closed for 158 days from March 2020 to February 2021, compared with the global average of 95 days.
There’s a huge informal sector. Workers in this sector tend to be less productive, and by one estimate Latin America has the world’s fastest-growing shadow economy. Corruption in both formal and informal sectors is an additional problem.
Latin America has the natural resources, and its governments want to persuade multinational companies to switch their interest from the minerals alone to refining them in the region and then building batteries and EVs there. Companies that might be interested in manufacturing in Latin America would need to be convinced that the region is tackling the productivity problem. This would involve ongoing improvements in education and training, a serious reduction in the informal economy, and the mañana mentality of the workforce.
Author profile: Royce Lowe, Manufacturing Talk Radio, UK and EU International Correspondent, Contributing Writer, Manufacturing Outlook. n
The Economist and The Guardian recently went to press on the beauty that can emanate from metals and the greed and violence that might ensue. This story concerns the “fate” of millions of brass manilla braceletsthe grim currency of the transatlantic slave trade between the 16th and 19th centuries. The Edo people in the Kingdom of Benin, modern Nigeria, created their extraordinary sculptures by melting down these bracelets. While rarely found in archaeological excavations on land, they have been retrieved in substantial numbers from the wrecks of vessels that had been transporting them. A German research project determined that the Benin bronzes were made from metal mined around Cologne. “This is a big deal within the high-profile Benin bronzes art and history world.”
In 1897 a heavily armed expeditionary force sacked Benin City in what was said to be an act of revenge in a bitter trade dispute between Britain and the Kingdom of Benin, east of Lagos. The city was burned to the ground, and its royal ruler, the Oba, was imprisoned, and the quite magnificent collection of plaques and statues made from brass, wood, and ivory was torn from his palace’s walls and sold to museums and
private collectors in Britain, Europe, and America. These were some of the finest artworks ever made in Africa, but views about their acquisition have changed. The destruction of Benin City has come to be seen as one of the low points of British imperialism, and the looting of its sculptures as indefensible.
The case for the return of the sculptures would seem to be morally clear. It has been taken up by those arguing for the return of artworks seized during colonialism. A joint effort by artists, activists, and curators has begun to yield results, and pledges have recently been signed by museums in America, Britain, France, and Germany, plus some universities, to return their Benin bronzes to Nigeria’s National Commission for Museums and Monuments (NCMM.)
These efforts may not bear fruit. Nigeria’s president Muhammadu Buhari, shortly to leave office, recently announced that returned bronzes will not be returned to the NCMM but to the current Oba, Ewuare II, “as the original owner and custodian of the culture, heritage, and tradition of the people of Benin Kingdom.” Ewuare II is the great-great-grandson of Oba Ovonramwen Nogbaisi, from whom the bronzes were first seized. So the
NCMM and many of its museum partners in Britain and Europe were caught completely by surprise and fear that the returned pieces will find their way to private collection rather than public display, as promised.
Last year saw the German government sign an agreement with the NCMM to return 1,100 artifacts from museums in Germany. So the nation loses out to a single royal family. Those in the “museum business” see Buhari’s decision favor the Oba over Nigeria’s own federal museum authorities as the latest move in a power play between the Oba and Godwin Obaseki, the governor of Edo State, of which Benin City is the capital. Obaseki is planning a new museum and wants all the bronzes he’s getting back to be put on display there.
The Oba, the Edo people’s traditional ruler, and keeper of the Edo culture, wants to house all the bronzes in his palace. Mr. Obaseki, who leaves office in 2024, has little time to assert his authority. He will need to run fast to reach his rather sneaky goal.
Author profile: Royce Lowe, Manufacturing Talk Radio, UK and EU International Correspondent, Contributing Writer, Manufacturing Outlook. n
The Flagship Reports with Dr. Chris Kuehl is both an “Officer of the Watch” briefing of economic conditions and an Executive Briefing on specific situations impacting those conditions. Written and presented by the officers of Armada Corporate Intelligence, Dr. Kuehl lightens up the mood of sometimes distressful geoeconomic news with a bit of humor. This monthly podcast includes information from the Flagship Reports issued 3 times and week, and AISI, the Armada Strategic Intelligence System, a tool for durable goods manufacturers that dives deep into the sector each month to provide more than 95% accurate near-term forecasts.
The 2nd quarter of 2023 continues as it started as the year started with continuing falling demand prompting reductions in production. Greece, again, continues to be the only country of the main eight to show expansion, but even here, a slowdown is underway.
The fall in new orders from most places around the globe signals that the weakness in production is most likely here to last for several more months. Capital goods are the one bright spot in production, being more resilient than the intermediate and consumer goods segments.
The majority of companies surveyed expect to produce more goods in the next 12 months than is currently the case. As such, the downturn has not
adversely affected the labor market, where employers are loathe to let people go lest they have problems replacing them when the next upturn comes.
The Eurozone is experiencing the same ebb of activity as the U.S. and China. Demand in the Eurozone for goods from China has tapered off, based on exports from China. It appears that the Eurozone, like the U.S., is just entering a recessionary cycle. Again, as is discussed in other articles of Manufacturing Outlook this month, no one knows if it will be a long, soft landing in the Eurozone, or a hard, short downturn. n
JULY 2023
Key Southeast Asian developing economies are doing their very best not to align themselves with either “The West” or “The Rest.” They are navigating complex, independent, and mutually beneficial trading and manufacturing relationships with the U.S., its Allies, China, and Russia, as
well as their Pacific Rim neighbors, to survive and thrive, regardless of geopolitics.
CPTPP
Vietnam, Malaysia, and Brunei have signed the free trade agreement known as CPTPP (Comprehensive and Progressive Agreement for Trans-Pacific Partnership), which includes major U.S. trading partners, including other Pacific Rim countries (Australia, New Zealand, Japan, Sin-
gapore), as well as a few Global South economies in the Americas (Mexico, Chile, Peru) and Canada. It reduces or eliminates tariff and non-tariff barriers and has established enforceable trade rules. China, Taiwan, The UK, and Ecuador have applied and await admission. The U.S. is not currently a signatory but has 61% of its goods trade with CPTPP members and current applicants. Originally, the U.S. was a party to its massive predecessor trade agreement, the continued
TPP, which reflected U.S. Congressional mandates, but it withdrew in 2017 during the Trump Administration. The goals had been (and largely remain) to enhance regional integration and to address issues that the WTO did not address, such as digital trade, state-owned enterprises, labor, and the environment.
In May of 2022, the Biden Administration launched the Indo-Pacific Economic Framework for Prosperity (IPEF) with a dozen initial Partners based on four pillars: trade, supply chains, clean economy, and fair economic growth, with the ultimate goals being resilience and sustainability. These platforms are vague and being scoped out in discussions with participants, which include CPTPP members (without China) plus other nations who are not signatories to CPTPP: India, Fiji, Indonesia, Thailand, Philippines, and South Korea. This U.S.-led economic framework is viewed as an initiative in progress to counter China’s growing influence in the region.
China is beset with ongoing reduced overseas export demand, crippling local government debts (sovereign debt is much lower), massive overseas Belt and Road unpaid loans, and slowing tech and property sectors. There is a resulting weakened investor interest. Also, long-term investors/producers like Apple and its suppliers like Taiwan’s Foxconn are expanding elsewhere in the Global South. China is hugely exposed to global market forces slowing down its growth, in addition to its own shrinking working-age population and 20% youth unemployment. (Overall unemployment is roughly 6%.) China’s growth might reach 5% in 2023 if the government takes measures to support expansion and consumption but is predicted to slow to 2-4% annually from 2024-2030. With
uncertainty comes consumers stashing away most of their cash and paying off mortgages rather than buying new.
Facing these headwinds, China’s enterprises are doing what long-established multinationals have been doing: combining domestic stimulus policies with moving lower-end manufacturing offshore to less expensive production sites in the Global South. This is not new. For years China has developed operations in Vietnam, Malaysia, Thailand, and Cambodia to produce solar energy parts, electronics, and automotive components, among others. As these nations develop transport and digital infrastructure, they will be able to produce products higher up the value chain with lower-cost skilled labor.
The bright spots for China are its dominance of the global battery industry (CATL) and the emergence of a major competitive auto industry, becoming a leader in global EV sales (BYD, NIO, Shanghai Tesla). Manufacturing in these industries depends on critical sources of lithium minerals, which ties China inextricably to the Global South. Australia is the world’s largest producer of lithium, and China imports as much as it can get in this competitive demand market. Chile is the world’s second-largest producer and has recently announced a plan to nationalize its lithium industry. This is worrisome to some Chinese companies with investments there.
China’s Tianqi Lithium Corp. has taken a 22.16 % stake in the Chilean Miner SQM. It has mining concessions in partnership with US-based Albemarle Corp, which expire in 2030 and 2043. Tianqi does not export lithium but earns investment income from its stake. China’s Ganfeng Lithium imports most of its lithium minerals from Australia, only a small amount from Chile. On the other hand, China’s NEV maker, BYD, has been granted per-
mission to build factory facilities and produce lithium iron phosphate (LFP) cathode material in Chile. With $290 million in investment, it is on track to produce 50,000 tons of annually, beginning in 2025. (GT)
China is holding up pretty well in spite of the Covid Pandemic, the war in Ukraine, and efforts by governments such as the U.S. to curtail trade and limit its rise in advanced manufacturing. Brad Setser, Senior Fellow at the Council on Foreign Relations and formerly a senior trade advisor to the Biden Administration, has spoken at length on Bloomberg’s Odd Lots podcast (6/9/23) about the massive shifts underway in world trade after three years. His conclusion is that tariffs and the trade war initiated during the Trump administration to make trade less attractive to China “did not have the effect of making China less dependent on trade.” China is exporting $1 trillion more than it was before the pandemic. But the effects of the Inflation Reduction Act and the Chips+ Act have radically changed the nature of manufacturing development in China. Tune in for more on the US-China trade imbalance, the future of the dollar, and the impact of sanctions on the world economy, including China’s electric vehicle and plane production.
Next month: Manufacturing in The Global South Part 3: India, Vietnam, and BRICS; also, the critical interdependence of the U.S., China, and Taiwan.
Author profile: Christine is co-founder and President of China Human Resources Group, Inc, a management consulting firm based in Princeton NJ. She has provided U.S. companies with strategic development and project implementation services for projects in China since 1986. n
A recent interesting opinion column in the NY Times focuses on the energy revolution that has been going on for some years, particularly from the point of view of what has been happening in Texas.
works quickly enough and spreads through other countries, it will play a significant part in helping us avert climate catastrophe.
But quite a while before the I.R.A. started to take effect, America was experiencing a renewable energy boom. And the boom has been led by, surprise, surprise, a surprising place. The crown for electricity generation, except hydro, goes to Texas. California has more solar power and a lot of geothermal electricity, too. But Texas takes the cake in wind power.
it is also a place where things can get built and done, and this has included a lot of wind turbines. So wouldn’t this be a reason for Texas politicians to celebrate the renewables boom, which is good for the state’s economy, and highlights the state’s laissez-faire policies?
Texas has many flaws, so they say, but
Wrong! Seems that Texas Republicans don’t like renewable energy, the sort that’s cheap and clean. Their answer to all this is a pile of proposed measures that would subsidize fossil fuels, impose restrictions that might block many renewable energy projects, and perhaps even shut down some existing
Over the past fifteen years or so, ongoing and huge technological progress has made it cheaper to generate electricity from solar and wind power than by burning fossil fuels. The Inflation Reduction Act, effectively a climate bill, aims to speed up the transition to renewables and also to electrify as much of the economy as possible. If this continued
facilities. So this legislation, again to our surprise, puts fossil fuels over an industry that could reflect Texas’s energy future. How many other states, let alone countries, would grab the chance to produce what Texas can produce? So why?
If we put sheer greed aside, although we probably shouldn’t, what are we left with that would prompt such actions? It’s suggested in the NYT article that most Americans have become relatively liberal on social matters and that corporations have been adjusting to their customer base. The word “woke” enters here, and this may be equated with wind power, as renewable energy is something environmentalists favor. And it’s being promoted by the Biden administration. So in the minds of Texas right-wingers, the wind has become woke, and wind power has become something to be fought even if it hurts business and costs the state both money and jobs. Thus the opinion columnist: “If all this sounds crazy, that’s because it is. But that’s Texas - and, I fear, much of America - in 2023.”
Stay tuned for occasional updates on the windy state. Maybe Texas will, one day, inherit the wind.
General Electric has pledged $50 million for a new assembly line at its plant in Schenectady, New York, for its
on-shore wind business, GE Vernova. The plant currently manufactures steam turbines and generators but will be converted for the assembly of three components for GE Vernova’s 6.1-MW turbine.
The plant will assemble the machine heads, hubs, and drive trains for its 6.1-158 onshore wind turbine, which includes a two-piece, carbonfiber blade design, thus simplifying manufacturing and installation in “hard-to-reach sites.” GE has logged orders for nearly 10 GW of generating capacity for this turbine model. There will be some 200 new jobs involved.
GE credited the 2022 federal Inflation Reduction Act for strengthening the demand for renewable energy. New York State is offering up to $2.5 million in employment subsidies.
GE Vernova is the business unit established to include General Electric’s Power, Renewable Energy, Digital, and Energy Financial Services businesses and is scheduled to be spun off in 2024. The GE Renewable Energy business is responsible for developing and manufacturing onshore and offshore wind turbines.
A recent article from IOP Publishing describes research carried out at Northeastern University, concluding that solar panels installed on the
roofs of industrial buildings have the potential to satisfy the entire electricity needs of up to 35% of American manufacturers. The study explores the feasibility of meeting these power requirements by installation of panels across various regions and manufacturing sectors in the United States.
The findings reveal that, depending on the season, rooftop solar installations could fully meet the electricity needs of 5-35% of American manufacturing industries, with the furniture, textile, and apparel sectors standing to gain the most.
The personnel from Northeastern involved in the study state that currently, less than 0.1% of the electricity required by the manufacturing sector in the U.S. is generated through renewable, on-site sources. They further state that, in many cases, rooftop solar panels are now a feasible option for supplying low-carbon energy. And that seasonally, manufacturing companies across nearly 40% of U.S. locations could fulfill their electricity needs in the spring and summertime with rooftop solar arrays. The research provides an indication of the locations and manufacturing sectors for which rooftop solar panels could significantly help manufacturing firms to reach their goals.
It should be mentioned here that the use of rooftop solar panels does not, to date, have a good history. Elon Musk’s efforts with his solar rooftop tiles, which effectively turned out to be too expensive. The road from the research laboratory to the rooftop may be long and arduous.
Author profile: Royce Lowe, Manufacturing Talk Radio, UK and EU International Correspondent, Contributing Writer, Manufacturing Outlook n
JULY 2023
Montreal is the home of a company called NanoXplore, a graphene company. We’ve already spoken briefly about this wonder material, one atom thick, two hundred times stronger than steel, and a superconductor of both heat and electricity. NanoXplore is headquartered in Montreal and has manufacturing facilities in the United States and Europe.
Graphene itself is a paradox. It is the thinnest material known to science, yet also one of the strongest. Researchers at the University of Toronto’s Faculty of Applied Science & Engineering have shown that graphene is also highly resistant to fatigue and is able to withstand more than a billion cycles of high stress before it breaks. Graphene resembles a sheet of interlocking
hexagonal rings, similar to the pattern seen in bathroom flooring tiles. At each corner is a single carbon atom bonded to its three nearest neighbors. While the sheet could extend laterally over any area, it is only one atom thick. The intrinsic strength of graphene has been measured at more than 100 gigapascals, among the highest values recorded for any material. But materials don’t always fail because the load exceeds their maximum strength. Small repetitive stresses can weaken materials by causing microscopic dislocations and fractures that slowly accumulate over time, a process known as fatigue. To understand fatigue, we might imagine bending a metal spoon, The first time the spoon is bent, it just deforms. But if it’s worked back and
forth, back and forth, eventually, it’s going to break in two.
NanoXplore manufactures and supplies graphene powder for use in industrial markets and provides both standard and custom graphene-enhanced plastic and composite products to the transportation, packaging, pipe, film, electronics, and other industrial sectors. Its graphene manufacturing technology, innovative, proprietary, and patent-protected, provides a significant cost-effective solution to its customers in high-volume applications. According to the Research Company IDTechEx, NanoXplore is the largest graphene powder producer in the world, with its fully automated 4,000 metric tons per year facility in Montreal.
The company provides its branded GrapheneBlack(TM) powder with a thickness of 6-10 atomic layers and a purity of 96-98%.
Years of R&D and development have gone into the addition of graphene to current Li-ion battery chemistries, with a focus on silicon-enabled Li-ion anodes that improve energy capacity and charging speeds for EVs, energy storage, and electric truck and bus sectors. There is in place a $10M project with Sustainable Development Technology Canada (SDTC), a Government of Canada organization, for the replacement of metals by graphene-enhanced plastics in the electric transportation market. Its shareholder base includes Martinrea International Inc., a tier-one automotive parts manufacturer; the Business Development Bank of Canada (BDC), Investissement Québec, and the Caisse
de depot et placement du Québec (CDPQ).
The company is doing well and is in good hands. Production of 4,000 metric tons by the world’s biggest player does not seem earth-shattering, but 4,000 MT represents an unbelievable area of material. Although NanoXplore is the world’s biggest company, China is the world’s biggest producer, supposedly making one-third of global output. They say they’ve made graphene from corn???
We seem to be awaiting a big breakthrough, both in terms of production and application. There is no doubt that significant progress has been made and that the possibilities relating to strength, conductivity, and energy would seem, on the surface, to be endless. On the other hand, we hear, from some quarters, that the presence
of silicon as an impurity may detract from graphene’s major qualities. We further hear that current production is expensive as well as being energy and resource intensive and that too little product emanates from it.
We will follow the progress of NanoXplore, along with any major global advances in graphene production and end uses by manufacturers and the many universities involved in its R&D. The number of people and companies working on the material makes it pretty sure that the industry will thrive and big breakthroughs will occur.
Author profile: Royce Lowe, Manufacturing Talk Radio, UK and EU International Correspondent, Contributing Writer, Manufacturing Outlook. n
JULY 2023
That’s the name of China’s star turn in the EV business, otherwise known as BYD. Bloomberg recently did a number on the company, outlining the long and winding roads the company’s sales have been taking across the globe. People normally think of Tesla, and rightly so. They’re good and, of late, quite accessible.
But the best-selling car in what we might call emerging clean-car markets, for example, Brazil, Israel, and Thailand, isn’t a Tesla; it’s a BYD. EV and plug-in hybrid maker whose product can be seen on the streets from Sydney to Delhi, even Montevideo, Uruguay. The brand even toppled VW as China’s biggest-selling brand during
Q1 of 2023, when it accounted for 39% of new-energy vehicle sales (electric or hybrid) or 12% of all passenger-car sales in the country.
And BYD, backed by Warren Buffett’s Berkshire Hathaway, is rapidly spreading its wings, recently going to Mexico, Spain, and the UK. Italy continued
is next. Its first target for new-energy vehicles was Norway in 2021, the country that went mad for Tesla. BYD came out of nowhere, and now it’s going everywhere. Except to the U.S., where the rules keep it out. But it does sell electric buses to the U.S.
BYD has a wide range of good-looking, (reputedly) well-functioning cars, with the Seagull starting at $10,400, a range of 190 miles, and a top speed of 80 mph. Hardly autobahn fodder. But then we move to the Han, starting at around $33,000, and at the top, top we have the Yangwang U8 SUV, which goes for around $154,000. Sales of that model might take some time to take off outside China. The company has a vertical integration strategy, whereby many components are made in-house, including batteries (it’s the world’s no.2 cell maker) and semiconductors. BYD sold 1.86 million new-energy vehicles in 2022, more than in the previous four years combined. Its global workforce doubled to 570,060. It aims to sell 3.7 million NEVs in 2023. It seems France wants it to build a plant there.
We could continue to state where and when BYD will expand around the world, how many cars they’ll build in the next five years, and how much money they’ll make. But the company is definitely one of the world’s major auto industry players and will continue to thrive.
Ford and Stellantis and Batteries
Ford Motor Co. and Stellantis NV recently announced agreements to strengthen their EV battery supply chains, increasing the demand for critical materials.
Ford will look to two agreements for lithium hydroxide, one of the main ingredients in EV batteries. The first is with Albemarle Corp., which will provide Ford with 100,000 metric tons of battery-grade lithium hydroxide, enough for some 3 million EV batteries.
This agreement will run from 2026 through 2030, and the possibility of developing a closed-loop solution for lithium-ion battery recycling is being explored.
Ford’s other deal is with Nemaska Lithium for a supply of lithium products over an 11-year period that includes up to 13,000 tons of lithium hydroxide per year. Spodumene will come from Nemaska’s mine in Whabouchi, Québec, and processing will be done in the new facility in Bécancour, Québec. Stellantis, meanwhile, said it has invested in California-based materials firm Lyten Inc., which is developing lithium-sulfur battery technology, among other things. Lyten is headquartered in Silicon Valley and working on a range of applications centered on its patented 3D graphene material that is engineered from natural gas.
For Stellantis, the company’s LytCell lithium-sulfur battery promises a carbon footprint 60% smaller than other batteries because it doesn’t use nickel, cobalt, or manganese and can be regionally sourced and produced.
Carlos Tavares, Stellantis’ CEO, was impressed by Lyten’s lithiumsulfur battery. He felt their material technology is well positioned to reduce vehicle weight. Tavares and his EV team have ambitious plans, including a fully-electric Chrysler range by 2028 and one of every two jeeps electric by 2030. The company has further invested in Australia’s Element 25 Ltd as part of a deal to source manganese for battery packs.
One has to wonder when the Earth will start to run out of the minerals that seem to be necessary to make all the batteries for all the EVs that will hopefully be bought.
Charge it,
And from minerals and batteries and EVs, we move along to chargers, and
a recent statement from Ford’s head honcho, Jim Farley, as to why the American public has been so slow to take to electric vehicles. It isn’t the cars but the plugs that power them, he said, in reference to the numerous surveys that refer to shoddy chargers.
So here again comes our knight in shining armor, with a deal starting early in 2024 that will see Ford owners get access to more than 12,000 Tesla Superchargers. Ford will begin equipping its EVs with built-in ports for connecting to Tesla’s proprietary North American Charging Standard, or NACS, from 2025 onward. This will eliminate the need for adapters that Ford vehicles will have to use to tap Tesla’s chargers initially since Ford and the rest of the industry have used a different kind of connector called Combined Charging System, or CCS. Tesla recently boasted that there were 60% more NACS posts in North America than all CCS-equipped networks combined.
Farley recently told CNBC that “GM and the others are going to have a big choice to make. Do they want to have fast charging for customers, or do they want to stick to their standard and have less charging?”
And, lo and behold, on the heels of Farley’s statement, General Motors Corp. announced a partnership with Tesla, and will begin using Tesla’s North American Charging Standard ports in its electric vehicles by 2025.
The collaboration will allow GM drivers to access 12,000 Tesla superchargers in 2024 with the use of an adapter. After 2025, GM will begin making an adapter that will allow its NACS vehicles to charge on CCS ports.n
Lawrence Makagon, Staff WriterCybersecurity traditionally protects data and users by focusing on the best and most efficient technology fixes. While this obviously has merit, one very key detail is left out of the equation: the people operating the technology.
A more holistic approach is Humanizing Security, where humans are the focus of security measures. I believe that the Humanizing Security approach is the better and ultimately more effective method when it comes
to cybersecurity for your business. Humanity should be considered in each step of security, which includes preparation for an attack, response during an attack, and recovery after an attack. The last step, the recovery, is where security professionals most often drop the ball concerning the human element of security. The financial cost of an attack is considered, but not the emotional cost of recovery. We must question: did the attack result in an employee being too afraid to take action, cause emo -
tional damage, or result in corporate paralysis due to fear of another attack?
Humanizing Security considers more than the material or financial impact of cyberattacks. Beyond the monetary cost of a breach, there is also often emotional damage to employees that affect performance, quality of life, and outcomes. Not addressing these issues as part of the security process can leave users hurt and alone.
When designing security, in addition to how secure it makes us, there needs to be consideration for how much it harms us in its implementation. Overly complex, non-humanized security is like a classic Corvette encased in cement: it is secure, and no damage can be easily done to it, but ultimately it has no value – you cannot drive it, see it, or enjoy it. Security that is too hard to use or too disruptive to its users is therefore not as valuable because its complexity has a negative impact on the user that prevents its full effectiveness.
We need to create and implement security by starting with the people. If we make items “secure” but unusable for those who use them, they will resist it, which results in less protection than expected (and required).
For security to be functional from a Humanizing Security standpoint, it
needs to be seen as Valuable, Manageable, and Relevant from the user’s perspective:
• Valuable - Do I fear the threat? Do I think someone may try and attack me? Do I feel safe enough right now?
• Manageable - Can I implement the security and still feel like I can do my work in a reasonable way?
• Relevant - Do I value the security? How does it affect my life? Do I understand how security keeps me working and safe?
Without these three items, security will be resisted by its users, and the impacts of emotional stress incurred by attacks will remain unaddressed. We as an industry need to see beyond the technical issues to the human issues. Security is about the human experience first and is supported by technology second.
Author profile:
Ken Fanger, MBA has 30 years of industry experience in the fields of technology and cyber security, and is a sought-after CMMC Registered Professional, helping manufacturers and contractors to meet DoD requirements for CMMC compliance. He is passionate about technology deployment, and his MBA in Operations & Logistics has helped him to be an asset in the designing and deployment of networks to enhance the manufacturing experience. Over the past 5 years, he has focused on compliance and security, including working on the SCADA control system for the Cleveland Power Grid. Mr. Fanger works with each client to identify their unique needs, and develops a customized approach to meeting those needs in the most efficient and cost-effective ways, ensuring client success. n
JULY 2023
The Employment Scene and the Returning Citizen
Although the PMI figures for U.S. manufacturing have been below 50 for the past few months - even worse in Europe - there is still much concern about the availability of skilled workers. Industry Week has written on this problem of late and come up with background and suggestions on what is actually, and potentially, a serious manufacturing
problem. No matter the demand for manufactured products, the wheels of production will not turn at their most efficient unless guided along by workers who not only understand the importance of what they are doing but are, in fact, ready, willing, and able to do it.
Carl Livesay, general manager at Baltimore’s Mercury Plastics company, has over 30 years of experience working with formerly
incarcerated citizens, whom he refers to as returning citizens. He says that given the time and understanding, such citizens are more often worth the time investment than would be choosing from the general population.
He has hired over 200 returning citizens in his career and says that 80% of the time, they proved the worth of time investment. He compares this with a success rate of 60% or less from hiring “walk-ins.”
His first-hand experience points to the most successful candidates having served eight years or more.
He further finds that those who have served less time weren’t necessarily interested in changing their previous way of life; such people come across as being very easily distracted and showing disinterest in a good job or career opportunity.
Livesay notes that those who served eight to 15 years are adversely affected by a lack of visits from family and friends and people stopping writing. They were forced into all the survivalist and cultural aspects of the prison system. Many learned a trade while incarcerated, and in learning a trade, they learned how to learn. There are programs of which Livesay speaks highly, one of which involves inmates being trained to care for retired thoroughbred horses. This is a day-long program, and it instills a positive work ethic. Similar programs, little known among manufacturers, are available.
Returning citizens will leave incarceration with a minimum of social skills. They will find
themselves for an indeterminate period in poor living conditions, with no vehicle and possibly no driving license, although this may be no great hardship and is, in any event, not limited to returning citizens. In many cases, there may be minimum support from family, and friends may no longer be around.
Effectively the returning citizen is starting over, and in most cases, a new job and new colleagues represent the basis of their life. They may run into companies that are either reluctant or fearful of hiring returning citizens, and there may be people in the companies that hired them who just don’t want to work alongside them.
Thus returning citizens who opt to start a new life and a new career have many obstacles to overcome, and it is here that the leadership of those training them must come to the fore. It takes patience, but most of all, it takes trust on both sides. A person coming out of several years of incarceration will most likely be loathe to trust, and the leader may feel likewise at the beginning. It has to be a two-way street but imagine
the mutual feeling of accomplishment when it works out and the company has a productive, satisfied employee brimming with skill and self-esteem. It should be noted here that there are programs in prisons where inmates actually engage in manufacturing for a stipend. The Guardian newspaper reported, just under a year ago, that some $11 billion worth of goods and services are produced annually by incarcerated persons - and for a pittance - and this is according to a report from the American Civil Liberties Union (ACLU).
Not to compare the two aspects of the fate of incarcerated persons but to stress the positive outcome of the programs described by Mr. Livesay and his personal involvement in them, but it seems that the training and placement of returning citizens is a more than just way through this human dilemma.
Author profile: Royce Lowe, Manufacturing Talk Radio, UK and EU International Correspondent, Contributing Writer, Manufacturing Outlook. n
For companies of 200 or less employees
With your NOW!membership you receive:
l Applicant Advantage Annual Membership (student video resume portal)
l Annual membership certificate
l Finding America's Greatest Champion Book (signed by Terry Iverson)
l CNC Rocks Virtual Manufacturing Camp (annual subscription)
l Access to networking community/mentoring focused on MFG workforce development
l A promotional video produced by your company posted to the
Channel