DESIGN THE FUTURE
Winter 2024
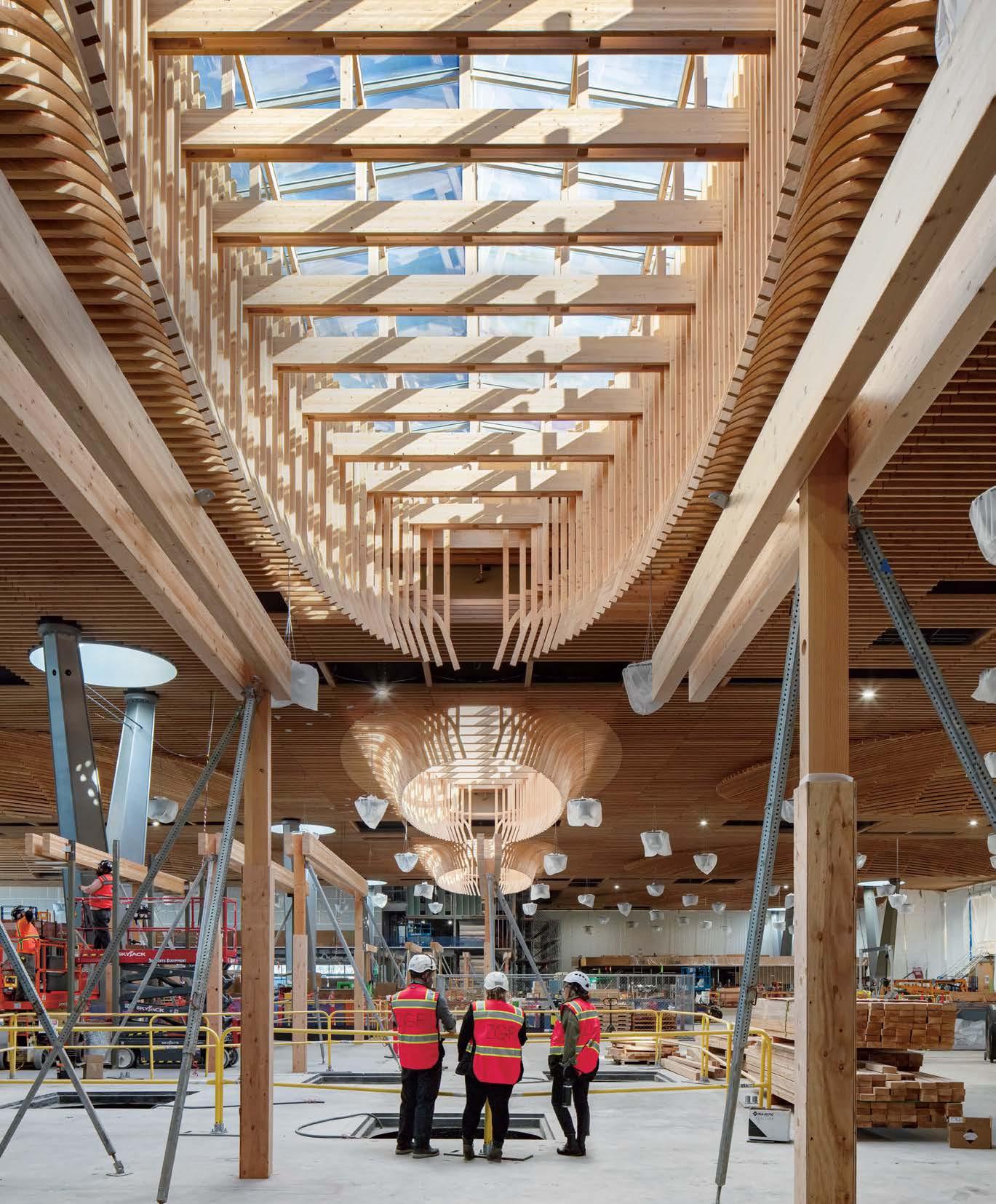
DESIGN THE FUTURE
Winter 2024
Breakout pairs modern ombré detailing with a timeless grid pattern, resulting in an on-trend design in your favorite colorways. Offered at an attainable price point, the hardworking carpet tile style checks every box when it comes to design, performance, innovation, and sustainability.
Discover more.
Breakout pairs modern ombré detailing with a timeless grid pattern, resulting in an on-trend design in your favorite colorways. Offered at an attainable price point, the hardworking carpet tile style checks every box when it comes to design, performance, innovation, and sustainability. Discover more.
interface.com/madeformore
interface.com/madeformore
For 25 years, WaveWorks has been a foundation for creating inspiring spaces where connections happen. As workstyles have evolved, the WaveWorks portfolio has expanded and flexed to meet a spectrum of needs from individual workspaces to collaborative areas.
In early 2025, new enhancements to the series include wall panels and shelves to add storage and functionality, smaller storage options to fit shrinking footprints, new trestle legs designed to add aesthetic appeal to conference and private office environments, additional height adjust options for added ergonomic and well-being, and planters that make it easy to add biophilia anywhere.
EcoWorx™ Resilient has a GWP (Global Warming Potential) of 5.2 Kg co2/m2.
Through our re[TURN]® Reclamation Program, we take back EcoWorx™ Resilient products to create more EcoWorx® products. We’re committed to a circular economy.
We have been entrusted in both this company and our planet,
Crafted to Sustain. View our Supplier Code of Conduct.
and must pass them along better than we received them.
- Tom Pendley President and CEO
The best time to plant a tree was 20 years ago. The next best time is today.
Trees heal the earth. Since 2020, we have partnered with One Tree Planted to reforest areas throughout the world as a commitment to carbon reduction and natural habitat restoration.
Find a tree planting near you.
285,233
WHEN EVERY DETAIL MATTERS, A TRUSTED PARTNER MATTERS MORE.
For 120+ years, USG has been a trusted industry expert in innovative designs and solutions. From concept to specification all the way through installation, USG delivers the products and the expertise to protect your vision from start to finish.
Learn more at usg.com/ design-with-usg
METROPOLIS’s Planet Positive Award winners represent excellence in sustainable, healthy, and just design at every scale in the built environment.
Indigenous Urbanism, this year’s METROPOLIS Planet Positive Award winner in the Student Work category, is UCLA students Charley Andrews and Jane Wu's master-plan proposal for Cathedral City in the Coachella Valley aimed at reconnecting previously divided land.
Design your next project on Material Bank.
Get personalized recommendations based on your project type.
Save and share inspiration and materials in a single, collaborative board.
Download spec sheets and sample materials overnight for free.
106
The tree-lined terminal designed by ZGF Architects sets a higher bar for materials sourcing, carbon accounting, and biophilic design.
118
The world’s most popular green building certification is getting ready for an update. Here’s what you need to know about it.
Deciphering the labels on natural and natureinspired materials is not easy. But clarity is coming.
Funded by architectural nonprofit re:arc institute, Latin and Central American practices are designing with water to create urban spaces for planetary well-being.
142
Discover the people, manufacturers, and suppliers behind the projects featured in the Winter 2024 issue of METROPOLIS.
144
Learn more about the topics you’re interested in as you explore the Winter 2024 issue of METROPOLIS.
remade to matter. to matter.
Circular by design. Material reimagined. For 25 years, EcoWorx
Circular ® has been the backing system has for making our high-performance carpet tile. Now we are bringing that innovation to our resilient flooring with ReMATERIAL PVC-free EcoWorx™ Resilient Backed by a 25 year warranty, it is fully . recyclable at the end of its useful life. Rethinking performance, sustainability and design, ReMaterial is the next generation of resilient flooring.
EDITOR IN CHIEF Avinash Rajagopal
DESIGN DIRECTOR Tr avis M. Ward
SENIOR EDITOR AND PROJECT MANAGER Laur en Volker
SENIOR EDITOR AND ENGAGEMENT MANAGER Fr ancisco Brown
ASSOCIATE EDITOR AND RESEARCHER J axson Stone
DESIGNER Rober t Pracek
COPY EDITOR Benjamin Spier
FACT CHECKER Anna Zappia
EDITORS AT LARGE Ver da Alexander, Sam Lubell
ADVERTISING DIRECTOR
Tamara Stout tstout@sando wdesign.com 917.449 .2845
ACCOUNT MANAGERS
Julie Arkin jarkin@sandow design.com 917.837.1344
Meredith Barberich meredith.barberich@sando wdesign.com
Ellen Cook ecook@sando wdesign.com 423.580.8827
Gr egory Kammerer gkammer er@sandowdesign.com 646.824.4609
Laury Kissane lkissane@sando wdesign.com 770.791.1976
Julie McCarthy jmccarth y@sandowdesign.com 847-567-7545
Colin Villone colin.villone@sando wdesign.com 917.216 .3690
PRINT OPERATIONS MANAGER Olivia Padilla
DIRECTOR, PROGRAMS & PARTNERSHIPS
Kelly Allen kkriwko@sando wdesign.com
GRAPHIC DESIGNER, CREATIVE SERVICES Paige Miller
METROPOLISMAG.COM @metr opolismag
A MORE SUSTAINABLE METROPOLIS
As part of the SANDOW carbon impact initiative, all publications, including METROPOLIS, are now printed using soy-based inks, which are biobased and derived from renewable sources. This continues SANDOW’s ongoing efforts to address the environmental impact of its operations and media platforms. In addition, through a partnership with Keilhauer, all estimated carbon emissions for the printing and distribution of every print copy of METROPOLIS are offset with verified carbon credits.
CHIEF EXECUTIVE OFFICER Erica Holborn
CHIEF MARKETING & REVENUE OFFICER Bobby Bonett
CHIEF OPERATING OFFICER Michael Shavalier
CHIEF DESIGN OFFICER Cindy Allen
EXECUTIVE VICE PRESIDENT AND DESIGN FUTURIST AJ Paron
VICE PRESIDENT, DIGITAL Caroline Davis
VICE PRESIDENT, HUMAN RESOURCES Lisa Silver Faber
VICE PRESIDENT, BUSINESS DEVELOPMENT Laura Steele
DIRECTOR, VIDEO Steven Wilsey
CHAIRMAN Adam I. Sandow
CONTROLLER Emily Kaitz
VICE PRESIDENT, FINANCE Jake Galvin
DIRECTOR, INFORMATION TECHNOLOGY Joshua Grunstra
METROPOLIS is a publication of SANDOW 3651 FAU Blvd. Boca Raton, FL 33431
info@metropolismag.com 917.934.2800
FOR SUBSCRIPTIONS OR SERVICE
800.344.3046 customerservice@metropolismagazine.net
SANDOW was founded by visionary entrepreneur Adam I. Sandow in 2003, with the goal of reinventing the traditional publishing model. Today, SANDOW powers the design, materials, and luxury industries through innovative content, tools, and integrated solutions. Its diverse portfolio of assets includes LUXE INTERIORS + DESIGN, INTERIOR DESIGN, METROPOLIS, and DESIGNTV by SANDOW; ThinkLab, a research and strategy firm; and content services brands, including The Agency by SANDOW, a full-scale digital marketing agency, The Studio by SANDOW, a video production studio, and SURROUND, a podcast network and production studio. SANDOW is a key supporter and strategic partner to NYCxDESIGN, a not-for-profit organization committed to empowering and promoting the city’s diverse creative community. In 2019, Adam Sandow launched Material Bank, the world’s largest marketplace for searching, sampling, and specifying architecture, design, and construction materials.
THIS MAGAZINE IS RECYCLABLE.
Please recycle when you’re done with it. We’re all in this together.
KATE DEHLER
Kate Dehler is an illustrator living in Austin, Texas, with her wife and their daughter. Her nostalgic work is often inspired by nature and draws from the graphic art of the 1970s. Recent projects include collaborating with the musicians Khruangbin and MonoNeon, creating a visual universe for Moog Sound Studio, and illustrating five book covers for Penguin’s Weird Fiction series. She has worked with a range of brands including Google, Dell, Chobani, and Warner Media, and contributes editorial illustrations regularly to publications like The New York Times and Bloomberg. Dehler’s illustrations are featured in “Will the New Version of LEED Be Better?” (p. 118).
At Atelier Ten, Prateek Jain works with real estate developers and their design and construction teams to ensure their projects tread more lightly on the planet. His deeper expertise lies in decarbonization of buildings, but he routinely manages projects looking to set bespoke and holistic sustainability goals and/or pursue green building certifications. His work experience encompasses LEED, WELL, ILFI Zero Carbon, life cycle analysis, energy analysis, facade optimization studies, sustainability master planning, and tying asset-level initiatives to corporate sustainability frameworks. Jain dives deep into LEED v5 in “Will the New Version of LEED Be Better?” (p. 118).
Will Speros is a freelance writer and journalist passionate about both the nuances and grandeur in architecture and design. His topics of interest also include sustainability, urbanism, hospitality, and human rights. Speros spends his free time at concerts, galleries, cinemas, bookstores, and urban architectural gems, and odds are you’ve seen him zip by you on a Citi Bike as well. He is based in Brooklyn, New York, and is currently writing a book about the Frank Ocean album Channel Orange. For this issue, Speros spotlights Swedish start-up PaperShell (p. 54), which is transforming plant-based materials into durable solutions for a circular economy.
ADELE WEDER
Adele Weder is an architectural writer, critic, and curator, and the founder of the Vancouverbased West Coast Modern League design advocacy group. She completed her master’s degree in architectural studies at the University of British Columbia. Weder has authored and co-authored several books on architecture, most recently Ron Thom, Architect: The Life of a Creative Modernist (Greystone Books, 2022).
A Fellow of the Royal Architectural Institute of Canada (RAIC), she is also a past recipient of the RAIC President’s Award in Architectural Journalism. In “The təməseẃtxw Aquatic and Community Centre Reflects Local Values” (p. 78), Weder covers Canada’s first Zero Carbon–certified aquatic center.
It’s All in How You Frame It.
Bring the natural textures of the outdoors into the interior with Feeney®’s DesignRail® resin infill options with organic embedded materials.
Welcome to the World of Feeney, where our designer custom options make it easy for you to create your own masterpiece, all while keeping it perfectly within frame.
Reach out to a Feeney Design Specialist to learn more: design@feeneyinc.com
“WHAT IF OUR homes and workplaces were like trees, living organisms participating productively in their surroundings?” asked William McDonough and Michael Braungart in their 2002 essay “Buildings like Trees, Cities like Forests” (The Catalog of the Future, Pearson Press). “In short, a life-support system in harmony with energy flows, human souls, and other living things. Hardly a machine at all.”
It’s a powerful idea—that the things we human beings make should work as similarly as possible to the things nature has evolved. Emulating nature is a big part of how we think about sustainability today, since it motivates us to the ideals of creating no waste, relying on the energy of the sun, and nurturing diversity. Inventors and innovators call this approach “biomimicry,” a term popularized by Janine Benyus’s eponymous 1997 book, and it is the progenitor of our current obsession with bio-everything (see “Help! We’re Drowning in Bio-Lingo,” p. 124).
Some of us continue to believe that if something comes from nature and does what nature does, then it can’t possibly be bad. The catch, of course, is that “you don’t want to copy nature and harm it at the same time,” warns writer Audrey Gray.
Now, ZGF’s addition to Portland International Airport is not a “building like a tree” in the sense that McDonough and Braungart imagined, even though it is made of lots of trees and has lots of trees inside it (“PDX Is More than a Mass Timber Marvel,” p. 106) . What makes it special, as writer Brian Libby and senior editor Francisco Brown lay out, are the efforts of an extraordinary group of professionals with deep respect for all
forms of life—the design team at ZGF, the biophilic design consultants at Terrapin Bright Green, the host of foresters and mill owners who supplied the timber, and many, many others. It takes gargantuan care and dedication on the part of a huge number of people to embody in a building even the smallest piece of nature’s magnificence.
The professionals you will meet in the following pages are engaged in a similar effort at the vanguard of sustainable design, whether they be Latin and Central American architects finding new ways of “Listening to Water” (p. 134) or the
winners of the 2024 METROPOLIS Planet Positive Awards (p. 88).
As our planet completes another revolution around the sun, it’s a good time to thank them, and all of you, for continuing to push for a better built environment. It is grueling work, and there are so many details to hyperfocus on and get lost in. The only way to keep going is to remember why we strive—we want peaceful and harmonious life on earth. So, if you will indulge me with a last arboreal reference, we can’t afford to miss the forest for the trees.
Happy New Year!
—Avinash Rajagopal, editor in chief
This past summer, sustainability advocates in the design and construction industries came together to envision progress on circularity in the built environment.
By METROPOLIS Editors
IN JULY AND AUGUST METROPOLIS brought together visionaries from across the building industry for its Circular Future Hackathon, aimed at reimagining how we design and construct in a way that aligns with circular design principles. Building off the Ellen MacArthur Foundation’s framework for design and the circular economy, the event encouraged participants to push the boundaries of sustainable thinking by considering waste and pollution, material life cycles, and regenerative design.
Representatives and sustainability experts across global firms, manufacturers, and industry organizations joined forces to tackle the building sector’s greatest circularity obstacles.
Participants included 3form, Andreu World, Arcadis, Buro Happold, CannonDesign, CO Adaptive, Dattner Architects, Doors Unhinged, DPR Construction, the Ellen MacArthur Foundation, FXCollaborative, the Good Future Design Alliance, Goody Clancy, HDR, HMC Architects, Houser Walker Architecture, HKS, HLW, IA Interior Architects, Interface, Legrand, Lifecycle Building Center, LMN Architects, Miller Hull, Momentum, MSR Design,
Los Angeles–based nonprofit ANEW works with corporations to responsibly steward surplus items into the community and away from landfills.
OPN Architects, Perkins&Will, Re:Vision, RIOS, Ross Barney Architects, Snøhetta, Studio Blitz, Valerio Dewalt Train, WRNS Studio, and ZGF.
During two rounds of virtual workshops, these participants joined one of seven groups, each focused on a particular challenge to a circular built environment: Eliminating Waste, Fighting the Culture of New, Questioning Ownership, Rethinking Lifecycles, Recovering Resources, Rallying Support, and Engendering Collaboration Across Industries. Teams brainstormed, refined, and fleshed out transformative ideas for new product ecosystems, commercial building leasing strategies, professional skills to support a circular design economy, and more.
In the months that followed, METROPOLIS shaped these concepts into comprehensive scenarios to be shared in a webinar in December, culminating in the online publication of seven forwardthinking solutions. Visit metropolismag.com for the unveiling of these groundbreaking ideas for a more sustainable and circular future in the built environment. M
“Alignment” is the word of the hour in every sector of the building industry, as different stakeholders come together to tackle climate impacts.
By Avinash Rajagopal
EPA announces its material label program
THE FEDERAL GOVERNMENT is one of the biggest buyers of building materials in the United States—federally funded purchases account for more than half of all concrete poured in the country per year, for example. So the EPA has made an even deeper foray into the development and promotion of sustainable building materials by announcing this past August that it will develop a new label program to help “federal purchasers and other buyers find and buy cleaner, more climate-friendly construction materials and products.”
2 to 4 Years
“Clean” requirements for construction materials will be periodically updated by the EPA
The program will define what constitutes “clean” construction materials, then keep those requirements updated every two to four years in order to drive the market toward preferring low-carbon materials. The EPA will focus on steel, glass, asphalt, and concrete as its first priorities, and has already issued supporting documents for the label program, including Product Category Rule criteria—which are the rules by which manufacturers will assess and report their impact using Environmental Product Declarations.
Pair up dramatic CastWorks™ walls with the calming texture of Tectum® ceilings and you’ll quickly discover why opposites attract. CastWorks is pure eye candy with perforated visuals; field finish in the color of your choice. Tectum features UL® Certified acoustics and aligns with industry-wide best practices. Spice up your acoustics at armstrongceilings.com/acoustics m/acoustics
The ECHO Project gets everyone on the same page
WHEN THE FIRST GENERATION of Life Cycle Assessment (LCA) tools for buildings were developed—the Athena Environmental Impact Estimator in 2002 and Tally in 2013 among them—we had but a nascent understanding of embodied carbon. So as the field of carbon accounting in buildings has grown and deepened over the past decade, we’ve ended up with different projects around the United States reporting different stages of their life cycle, using different methodologies for calculations, and even using different terminology in their assessment. The result? It’s been very hard to compare buildings, benchmark embodied carbon emissions, or set targets for reducing those emissions.
In 2023, five nonprofits— Architecture 2030, Building Transparency, the Carbon Leadership Forum, the International Living Future Institute, and the U.S. Green Building Council—came together to align on how we collect and report
embodied carbon data. Known as the ECHO project, which stands for Embodied Carbon Harmonization and Optimization, the group now includes representatives from a host of other associations and organizations in the built environment.
This fall, ECHO published its first industry recommendations.
The ECHO Reporting Schema, released this past September, provides a common format for reporting project-level LCA results—harmonizing different methods of reporting data and filling in gaps in current methodologies. The second publication in October, “Project Life Cycle Assessment Requirements: ECHO Recommendations for Alignment,” assesses 29 different commitments, certification programs, standards, policies, and benchmarking initiatives relevant to North American project LCA requirements, to finally provide a single, aligned set of LCA requirements.
Landscape Architecture; Climate-Friendly Construction
01 New Guides for Landscape Architects:
The American Society of Landscape Architects (ASLA) has released a new set of free guides to help architects, specifiers, and industry partners work toward ASLA’s Climate Action Plan goal of zero-emission landscape architecture by 2040. The resources include guides to decarbonizing specifications and the design process, as well as help navigating environmental product data. asla.org/climateactionplan.aspx
02 Climate Change Playbook for Construction: Architects complaining about risk-averse contractors who cannot get on board with a project’s decarbonization goals now have an insider tool to help get the job done. Written by contractors for contractors, the AGC Playbook on Decarbonization and Carbon Reporting in the Construction Industry is the first resource to help construction firms “play a leading role in crafting carbon-reduction measures for the industry.” agc.org/climate-change-playbook
At Mohawk Group, our goal is to use design to nurture a culture of care. Inspired by pollinators, the Pathmakers Collection connects people to the ways of nature, while working to protect and nurture our natural world.
Part of Bentley’s Prima Vista collection of 100 percent wool area rugs, the Sweater Collection consists of four minimalist textures with names that capture the familiar comfort of favorite wools: crew neck, hoodie, pullover, and quarter zip. The rugs are hand tufted, hand knotted, and hand-loomed. A variety of area rug sizes are available, as well as a 12-foot broadloom. bentleymills.com
By Nigel F. Maynard
THE FLOOR —whether it’s in a home, a hotel, or an office building—is possibly the first thing visitors see when they enter a space, so its appearance must be on point. But unlike other surfaces in a building, flooring also needs to be able to withstand the daily assault of foot traffic, wet boots, heavy objects, spills, and a dropped glass or two. These selections combine beauty and brawn.
MEND COLLECTION
The Mend Collection of modular carpet tiles celebrates the beauty of imperfection and the craftsmanship required to breathe new life into cherished fabrics, the brand says. The collection uses layers of texture and color to transform flaws into a design. The rugs are made from recycled-content nylon and come in three styles, each offered in a range of rich colorways. manningtoncommercial.com
Made from EcoSolution Q100, a high-performance 100 percent recycled-content nylon fiber from pre-consumer sources, Local Landscapes carpet tiles are optimized for low embodied carbon. Inspired by the world outside and human beings’ collective desire to bring the outdoors inside, the tiles come in six nature-inspired color palettes: Grassland, Forest, Mountain, Arctic, Desert, and Coastal. Each tile measures 18 inches by 36 inches. shawcontract.com
Drawing inspiration from the spirit of Idyllwild, California, the Idyllwild Collection features abstract interpretations of tranquil landscapes, evergreen trees, and vibrant flora. The collection is made from extruded nylon, which the company says is engineered to maximize appearance retention and lifetime stain removal. It’s offered in broadloom or 18-inch-by-36inch tiles, and in three designs: Sojourn, Bliss, and Harmony. jjflooringgroup.com
REMATERIAL RESILIENT FLOORING PATCRAFT
ReMaterial is a PVC-free resilient flooring that can be recycled after the end of its useful life. The manufacturer uses polyolefin material that contains up to 25 percent recycled plastic from yogurt cups, laundry containers, and more. When it’s time for a renovation, the flooring can be reclaimed through the company’s re[TURN] program. It comes in 21 colors. patcraft.com
HIGH-PERFORMANCE TILE GRES ARAGÓN-FAVEKER
The manufacturer that specializes in porcelain tile has introduced two new nonslip-grip collections for outdoor use. Available in rectified floor tiles and step tiles, Selene is a cement-effect collection in shades of white, cream, and mocha, while Materia reproduces natural stone streaked with subtle gray and ivory veins. gresaragon.com
Terra is a collection of ceramic tiles that offers the soft look and color palette of Mediterranean cement. The floor and wall tiles feature white scales, and a matte finish that the company says is a creative simulacrum for the real thing. Available in two finishes—Bone and Topo—the products come in two sizes for the floor and one size for the wall. productfinder.porcelanosagrupo.com
Riva Max is an engineered hardwood flooring that features a sustainably sourced European white oak top layer and a marine-grade Baltic birch plywood core that ensures stability. Planks measure ten inches wide, six or eight feet long, and five-eighths of an inch thick. The line offers ten colors and features a Bona UV matte lacquer. rivaspainbyfloors.com
The company that made its name in modular carpet tiles now offers recycled-content luxury vinyl. Earthen Forms LVT is a nature-inspired line with a wood-grain or travertine-stone look. Each tile includes 39 percent recycled content and high-performance features like a 22-millimeter wear layer and fiberglass for dimensional stability. It comes in planks and tiles. interface.com
Quality light, striking design, acoustic control.
By Nigel F. Maynard
FEW PRODUCT CATEGORIES are as dynamic or exciting as lighting. Just as important as daylight, artificial light comes in a wide variety of shapes, materials, designs, and configurations. And the now-dominant LED remains a technology that people take for granted. Is there a better product story than a bulb that can last for 50,000 hours?
It’s hard to look at the Knit Collection and not think about the Mediterranean sea urchin. The resemblance is uncanny. But Cologne, Germany–based Meike Harde, who designed the collection for Vibia, had something else in mind: textiles.
The pendants are covered in stretchy 3D Lycra, manufactured using a technique called “technical knitting.” Found mostly in sportswear, technical knitting is the ability to create non–garment related structures using advanced knitting equipment, programming, materials, and processes.
Playing with tone and texture, Knit’s darker ribs are opaque, while the space between the ribs is thinly knitted to transmit diffused light. “The beige yarn interacts with the light to create an intimate ambience enhanced by varying levels of density as the ribbed fabric stretches out over the diffuser,” the company explains.
Knit comes in three sizes and offers four installation options for creative freedom. vibia.com
Part of the Axis Collection, Axis X is designed with extruded bronze angles holding four perpendicular arrays of light that radiate outward from its central channel. The manufacturer says the LED fixture draws inspiration from industrial angles and channels that were common in the 19th century. Available in 36- or 48-inch lengths, the light comes in six finishes. juniperdesign.com
Designed by architect (and Artemide president and CEO) Carlotta de Bevilacqua, Somnĭum is a new linear pendant series that consists of an aluminum body and a series of light cells with a technopolymer diffuser. It comes in a brushed aluminum finish and can be specified in six sizes and linear, circular, or curved options. artemide.com
The Cape sconce is a modern interpretation and homage to old maritime fixtures. A collaboration with Little Wing Lee of Studio & Projects, the light features blown solid glass, steel, and aluminum. It comes in two sizes and four colors, but custom hues can be ordered. rbw.com
TURNKEY FUSION LIGHT WALL SYSTEM BENDHEIM
Offering illumination in two inches, the TurnKey Fusion Light Wall combines art and lighting. The quick-install product is an expansion of the company’s TurnKey Glass Wall System. Fusion provides integrated LED panels using LE’Diffusion Safety Glass, engineered for even light dispersion. The panels measure eight feet tall. bendheim.com
H SERIES DMF
The H Series is a modular whole-home downlighting system that consumes 5, 9, or 12 watts, and is designed to last 50,000 hours. Energy Star–rated, the LED line features a single light engine module with a field-selectable lumen switch, allowing three brightness levels (350, 750, or 950). It’s offered in a three- or four-inch model with round, square, flush, or adjustable trim options. dmflighting.com
The minimalist Talis fixture is as simple as it gets: a U-shaped bar with a frosted silicone diffuser housing LED illumination. Highly versatile, the fixture can be specified in single or multiple bars that can be adjusted to the height and space of the room. It’s available in a single- or multi-bar configuration and in 36, 48, 70, or 90 inches. Three finishes are available. kuzcolighting.com
Gridiron is one part architectural lighting and one part noise-reducing surface. Part of the STFU Acoustic Series, the fixture features rectilinear patterns of illuminated four-inch-by-two-inch linear profiles that are fitted with recycled PET felt acoustic panels. It has a recycled extruded housing and an LED that provides direct or indirect/direct light distribution, and it can be specified in 20 felt colors. coronetled.com
NY Showroom
907 Broadway, 2nd, New York, NY 10010
T + 1 646 701 7058
usa@nanimarquina.com nanimarquina.com
The two innovative platforms are designed to help architects and industrial designers streamline project management and boost collaboration.
By Francisco Brown
EFFICIENCY AND COLLABORATION are critical in the fast-paced architecture and design industry. Monograph and Naya are responding by reshaping workflows with platforms tailored to industry needs.
“I worked as an architectural designer in firms of various sizes,” says Monograph cofounder and CEO Robert Yuen. “I noticed a recurring issue: The industry often mismanages time and lacks visibility into budgets and performance.” Monograph addresses this gap with tools that let users track project phases, assign tasks, and monitor progress. The platform’s intuitive dashboard consolidates timelines, costs, and tasks, offering real-time insights into the project’s health.
In addition, Monograph has addressed a significant industry gap: the absence of reliable factual data for architecture firms to benchmark their performance. “Historically, industry reports have relied on self-reported surveys, which can be inconsistent due to
varying interpretations of key metrics,” says Yuen. By leveraging first-party data directly from thousands of users, Monograph offers what Yuen believes is “the most accurate and comprehensive report of business metrics ever shared in the architecture industry.”
While Monograph focuses on architects, Naya targets industrial designers, offering a platform to manage and streamline product design. Cofounded by Vivek Haligeri Veerana, Naya aims to “help designers who are currently in this highly fragmented and frustrating product design process to accelerate their workflow and go from an idea to product all in one integrated platform.”
His team identified inefficiencies in the design process, especially for multidisciplinary teams working on large projects with multiple stakeholders. “One of the main issues we found was that data is living in different places and, most of the time, they’re not talking to each other,” he explains.
Naya solves these issues with three core features. First, it centralizes all work in one place, integrating assets like images, 3D models, documents, and spreadsheets. Second, it allows for seamless collaboration, enabling real-time interaction with all stakeholders. Finally, AI capabilities accelerate the workflow, analyzing information across various project elements to expedite the design process.
By integrating AI and cloud computing, these platforms have made it easier for designers to collaborate, manage projects, and make data-driven decisions, creating more efficient and insightful workflows. M
Made from post-consumer waste products (plastic bottles), PET Felt has a very low-energy manufacturing process. The seat will not degrade, and at the end of its long life, it can be fully recycled once again. the end
Sweden-based PaperShell is transforming plant-based materials into durable solutions for a circular, biobased economy.
By Will Speros
WHEN ARPER REINTRODUCED the iconic Catifa Carta 53 chair at this year’s Salone del Mobile, the furniture titan also heralded its collaboration with Scandinavian biogenic material company PaperShell. With its signature thin silhouette intact, Catifa Carta became the first commercial product to don PaperShell’s dynamic technology, which reinstates paper as a durable, artificial wood.
“[As a] tree grows up, it takes the carbon from the atmosphere, and we reduce that tree to paper with a single life,” says PaperShell cofounder and CEO Anders Breitholtz. “We should be able to do something much more advanced around this.”
CRAFTED FOR LUXURY & TIMELESS DESIGN
A tailored product portfolio offering a rich variety of textures and finishes inspired by natural materials.
ECONYL® ReLana
Timeless wool-inspired elegance without shedding
ECONYL® ReSeta
Silky softness and luxurious feel, and easy to clean
ECONYL® Terra
Natural, rugged beauty reimagined for modern durability and sustainability
Design your next collection with ECONYL® Bespoke.
MEET PERFORMANCE DEMANDS & ENVIRONMENTAL GOALS
Infinitely regenerable nylon
Long-lasting texture and appearance Superior stain resistance
A designer and former technology scout, Breitholtz sought to unlock solutions for steering the design industry toward a circular economy. “Whether it's fashion, automotive, sports, whatever, there's always a hunt for new materials,” he says. “But the reality is that there aren't many materials that are actually viable in an industrial context.” Following some exploration with advisory service Material ConneXion, Breitholtz teamed up with fellow PaperShell cofounder Mathieu Gustafsson in 2018 to begin tests on a new paper alternative. PaperShell’s material possesses a superior strength to wood through intensive
compression molding that merges and cross-links paper fibers and bio-resin. The process reintegrates hemicellulose into the substrate to create a dry prepreg that is then cut into blanks and stacked under a large steel press for shaping and trimming. Production waste is turned into biochar as well, setting the basis for a circular economy. “You get a component which is 100 percent biogenic. There's no fossil carbon inside. It's just natural materials,” Breitholtz says. “By pressing it really, really hard, that's when you have the paper sheets sort of merge together and become a homogeneous material.”
PaperShell uses craft paper and a bio-binder from waste streams. The paper is impregnated with the binder, then stacked and subjected to heat and pressure in hydraulic presses, forming a uniform material molded to shape.
PaperShell’s lightweight, durable, and moldable qualities make it ideal for facades, offering sustainable cladding that withstands weather, supports intricate designs, and reduces environmental impact with carbonsequestering and biodegradable properties.
PaperShell continues to explore the material’s versatility. Testing is currently under way alongside collaborators in the architecture, construction, and recycling communities to develop circular facade panels and cladding. Nearly 50 automotive OEMs including Polestar have also expressed interest in using the material for interior and exterior applications. PaperShell has even entered the sporting goods market with its bindless snowboard known as Papersurf, and Breitholtz and content designer Johan Höög have pressed their material into a vinyl record to divine its sound as well. “The interest in our materials comes from all over,” Breitholtz says. “What we have learned now is that there's such a diverse use for this.”
Arper CEO Roberto Monti is perhaps PaperShell’s most enthusiastic collaborator, lauding the tech innovator’s mirroring of the manufacturer’s own pillars that aim to enhance human well-being, transition to a circular economy, and reduce environmental impact. The new and improved Catifa Carta 53 marks the beginning of a beautiful—and sustainable—friendship. “The design kind of captures an even better way of thinking of Carta,” Monti says. “It also allowed us to not go for the high-selling object immediately, but actually to start to dedicate to this form, which allows us to do much more.” M
For generations, AHF Products’ brands have been in tune with your needs, providing a firm foundation under the feet of workers, travelers, and even aspiring musicians. While you strive to be pitch perfect, our robust collection of durable and dependable hard-surface options ensures you won’t miss a beat.
The curator invites participants to reduce waste and integrate natural systems through a new circularity manifesto.
By Francisco Brown
, architect, engineer, and professor Carlo Ratti wants to demonstrate architecture’s relationship with natural systems. Ratti and his team have published a Circular Economy Manifesto, developed with guidance from Arup and the Ellen MacArthur Foundation, which calls on the exhibition’s participants to rethink their spaces and pavilions through circular design principles such as using a Whole-Life Carbon approach, maximizing recycled and reuse materials, designing for modularity for easy deconstruction, and integrating natural principles. METROPOLIS sat down with him to discuss his vision and initiatives for the next Biennale.
MIT’s Senseable City Lab study uses laser-scanning data to analyze the architectural logic of Brazilian favelas.
Above, Hot Heart is a series of islands in Helsinki with the dual function of storing thermal energy and serving as a hub for recreational activities. The project was recognized as a Responsible Disruptor by METROPOLIS in 2022. Below, Smart Curbs is an MIT and Hong Kong University of Science and Technology research project on technology using computer vision to measure street activities in real time.
Francisco Brown: What is your central vision for the 2025 Biennale?
Carlo Ratti: I think the biggest challenge of architecture today, which we are trying to address both with our practice at CRA (Carlo Ratti Associati) and our research at MIT, is to create a better alliance between natural and artificial systems. There are two ways: One way is with the artificial world, the world of sensors, AI, and so on. Systems that can help us transform a building, or even a city, into almost a living organism. The other way is to use the logic of nature itself. We, as architects, all know that these principles and circular practices are key ones. Those logics have informed much of our design work
regarding the use of renewables in buildings and new types of sustainable and circular architecture.
FB: Global events, including the Olympics, have slowly adopted circular design strategies. Tell us about your decision to publish the Circular Economy Manifesto.
CR: We've been looking at circularity in different ways for years at the studio. For instance, we did a Circular Garden at the Milan Design Week and later at the Italian Pavilion at the Dubai Expo. The idea is that everything you do in architecture can be reused or recycled at the end of its life. This new Circular Economy Manifesto followed a set of
guidelines we put together in New York during Climate Week with the Ellen MacArthur Foundation. We know that we won't be perfect next year. Still, we think this survey is the direction we want to push, especially for temporary events like the Olympic Games, when countries build very complex structures and then, after a short amount of time, it all goes to a landfill. The exhibition will later turn into an architectural manual for circular design.
FB: The manifesto asks the participants to showcase “bold examples of circular design that offer lasting sustainability legacy.” How are you guiding participants through this?
Nest baffles dampen sound from above with contoured panels that come together to create limitless configurations. Create your own unique layout from two rounded and one customizable linear baffle, available in over ninety colors of 100% Wool Design Felt. filzfelt.com/nest
Wanderlust is a research video by the MIT Senseable City Lab that analyzed more than eight billion human mobility traces collected in five cities on four continents to prove the universal visitation law of human mobility.
CR: We are not forcing people to follow [the Manifesto] because we see this as the beginning of a process and the first step of a “circular future.” Some countries started designing the pavilion even before we announced the theme, whereas some countries still needed to pick the design, so it changed a lot between participants. We couldn’t impose it because it would be like changing the rules of the game while it is being played. So next year, the thought is to start developing some knowledge. It’s not about imposing but about proposing new ways to design. So we can later create a guide and apply it to other events, such as the Milan Design Week, which has shown [more] interest in becoming circular.
FB: With the Biennale College Architettura, you invited students and young professionals to submit proposals that utilize natural, artificial, and collective intelligence to combat the climate crisis for an opportunity to build their projects. Tell me more about this.
CR: We were flooded with thousands of proposals from all over the world. So, on one hand, it was tough, but it was a hundred percent worth it for different reasons. One was about getting a taste of ideas, issues, and concerns from a different generation and parts of the world. And the second thing is that we’ve always believed in open-source architecture since we published Open Source Architecture (Thames & Hudson, 2015) [almost] ten years ago. We wanted a space where everybody could contribute to new ideas, and those ideas would replicate like a natural system. However, we know top-down happens much more in our field. This notion of the Promethean architect that ignores diversity, and the full complexity of the people, the environment, and the organic growth of
Jian Mu Tower in Shenzhen, China, incorporates a large-scale farm into its 51-story structure. It is set to produce crops that can feed 40,000 people a year while also housing offices, a supermarket, and a food court.
cities. This open call and workshop invited participants to do the opposite and collaborate. This open process is what we need to bring back to architecture. We have seen many projects based on the idea that design is a collaborative effort, and networks today can help us build on the traditional way of doing things, for example.
FB: How are you programming the Biennale to meet this collaborative process objective?
CR: We want to have primarily two types of “openings” in the Biennale. The
first one is opening between different disciplines. In many teams, you will see fantastic architects, designers, and planners working with top Nobel Prize–level scientists, sociologists, artists, or other disciplines. So there’ll be this very intellectually promiscuous point of view. The second type of “opening” is from the point of view of age. Thanks to the open call, we found out about the fantastic work that was coming out of some people who were just at the university and were being invited to be alongside some of the most well-known architects. M
The prefabricated houses are circular, modular, and fully demountable and reusable.
Moos’s building system promotes diverse neighborhoods through efficient, environmentally responsible, and socially inclusive construction.
By Petra Loho
FOCUSED ON RESHAPING the future of affordable housing, a Dutch start-up is spearheading a modular, circular building system with sustainability at its core. Moos unites experts who share a vision for positive change through forward-thinking design, construction, and development. In collaboration with the multidisciplinary architecture studio Concrete, they’ve introduced a groundbreaking, fully demountable construction model aimed at tackling the housing crisis in the Netherlands.
This crisis has reached a concerning peak, with Deloitte’s Living in Europe: Housing Trends and Prices 2024 report indicating that new-build homes now cost 16 times the average Dutch salary, and the waiting list for social housing can extend to almost 20 years in major cities like Amsterdam.
These figures highlight the significance of Moos’s debut project, Moos Euterpe, a social housing development near Rotterdam spanning over 21,500 square feet. With 30 housing units of varying sizes, the complex is designed to accommodate both small and large families. Two buildings with twin rows of stacked two-story modules face each other, fostering a community connection centered on a communal garden. The step-back facade transforms galleries into verandas,
providing flexible spaces for personal touches like planters or seating. One prefabricated module in each home includes essential functions like sleeping, cooking, and washing, while the second is a flexible space that residents can configure to suit their unique lifestyles.
“The plot was long and narrow, which made finding the ideal housing layout a challenge. By designing double-sided apartments that open onto an intimate garden through spacious, functional verandas, we created a small community where social interactions happen naturally,” says Iwan Hameleers, Concrete’s project architect.
“It was thrilling to see how years of design, engineering, and testing in model homes came to life successfully in this first project of the sustainable, modular Moos housing system.”
The thoughtful design is complemented by Moos’s commitment to sustainability, blending upcycled materials from demolition partners with biobased options. Recycled concrete supplied by Holcim forms the floors, while cross-laminated timber walls provide structural integrity. Wood-framed windows with triple glazing ensure energy efficiency. With approximately 500 additional homes on the way, Moos’s take-back guarantee allows for easy relocation, reinforcing the circular model and minimizing environmental impact. M
We believe in design for the long run, where durability and aesthetics are equally important, effortless cleanability and maintenance come naturally, and honest sustainability stands and above it all.
In Wyoming, CLB Architects transforms a former big box into a high-tech hub with a distinctive weathered-steel scrim.
By Brian Libby
Originally a concrete Kmart superstore, the 120,000-square-foot adaptive reuse campus serves as a commercial and industrial center for the Sheridan, Wyoming, community while positioning EMIT as a technology hub.
beside an interstate highway on the outskirts of Sheridan, Wyoming, might not have seemed an obvious place to transform a manufacturing company’s identity and attract a new generation of tech-savvy employees. But EMIT Technologies CEO Casey Osborn knew this former Kmart could become a striking company headquarters.
“I didn’t want to be in a position where it was like, ‘EMIT, they’re up in the Kmart building.’ But there were some bones here that we could leverage,” Osborn says. “We just need it to have some identity, something representative of the work we do.”
Designed by Jackson, Wyoming’s CLB Architects, with the client also serving as the project’s general contractor, the EMIT Technologies he adquarters consolidates
Marmoleum connects with modern nature through climate positive flooring and contributes to everyone’s well-being. An endless source of inspiration, from the natural materials we use, to the colors and designs we offer.
We invite you to create sustainable spaces that have a positive impact on everyone and everything.
View our new Marmoleum Solid collection at www.forboflooringna.com/stepintomodernnature creating better environments 1-800-842-7839 | www.forboflooringNA.com | email: info.na@forbo.com
four separate manufacturing facilities on different sites (where the company produced custom-fabricated structural steel as well as a suite of emission-control equipment) in one place, taking advantage of the over-80,000-square-foot former retail building. A new three-story office structure built adjacent to the Kmart is full of natural light thanks to its glass facade and an oval-shaped inner courtyard; additional windows, on the office side, look directly onto the manufacturing area. Wrapping the new and old architecture, as well as a second courtyard, with a perforated weathered-steel scrim that was engineered and manufactured by EMIT gives the conjoined buildings a unified presence while also shading the glass offices from direct sunlight.
A series of courtyards introduce daylighting into the structure and create a new type of programming for meeting and working.
MOBILE SURVEILLANCE
Security Design is currently based on restricting access and protecting perimeters. Invisible security in contrast foresees free access.
Invisible security uses data, technology and design to secure places. Everywhere and at any point in time.
While putting security at its core, it respects public acceptance, privacy and convenience, in order to make physical spaces not only safe, but also frictionless, trustworthy, and liveable.
CONTINUOUS AUTHENTICATION
VIRTUAL PERIMETER
BEHAVIORAL ANALYTICS
CONSENT-BASED IDENTITY MANAGEMENT
“It tells a story about what goes on in the building—this high level of craft, displayed very proudly on the outside of the building,” says CLB Architects partner Eric Logan. Osborn gave CLB wide latitude to design the headquarters and manufacturing facility, with a single condition. “His one edict was that all of the employees needed to enter and exit through one door,” Logan recalls, part of what EMIT calls its no-collar workforce. The project includes numerous common areas where industrial and administrative workers can mingle—a coffee shop, an auditorium, a
basketball court, a library, and a barbershop— many of which are also made available to the community. “We wanted to create a place that wasn’t just for the employees, that the whole town and county could come and use,” the architect adds.
The interior includes many custom features fabricated by EMIT, including wood ceiling panels in an intricate pattern, and a perforated steel reception desk. “It was a learning experience for us,” says CLB Architects interior design director Sarah Kennedy. “We would often have a typical
product specified, and they would say, ‘We can make our own.’ It gave us the opportunity to really rethink the way that we were executing some of these details.”
Outside the company headquarters in an adjacent new city park is a Stonehengelike circular steel sculpture called FILTER that CLB and EMIT codesigned and fabricated for the NYCxDESIGN festival in 2022. CLB had been working solo on a wood sculpture for the festival, but it proved prohibitively expensive, so Kennedy suggested to Logan that they invite EMIT,
WE BELIEVE IN
CERTIFIED
At J+J Flooring we’re giving new life to old plastic by turning it into the most durable soft-surface flooring on the market. Kinetex contains no less than 45% post-consumer recycled content. One box of Kinetex contains the equivalent of 492 plastic water bottles, with one 24”x 24” tile equaling 27 plastic bottles. And with its lower mass, Kinetex has a 50% lower environmental impact compared to other commercial floorings. STYLE SHOWN: SYNERGY // SPACE
AND HPD’S AVAILABLE JJFLOORING.COM
1 Library, Cafe, Offices
2 Auditorium, Offices
3 Entry, Amenities
4 Automated Steel Stockpile
5 Fabrication
6 Paint, Powder Coat
7 Architectural Screen
8 FILTER Pavilion EMIT Campus Components New Construction
with which they were already building the headquarters, to collaborate. For the sculpture’s new iteration, displayed in Times Square before returning to Wyoming, “we took a basic sheet of steel that shows up at their facility every day, and folded it in half so it actually has a spine and can self-support,” Logan recalls. “This material often plays a hidden role in construction, so the sculpture became a way to honor their craft.”
The EMIT headquarters is already attracting interest, and not from would-be Kmart shoppers. Osborn recalls a recent job applicant who arrived without an appointment: “She said, ‘I really have no idea what you do, but the building is so interesting, I had to apply because I was curious what’s going on inside.’” M
existing Kmart was an 80,000-square-foot concrete core building before expanding to the current commercial and industrial campus.
0$'(,17+(86$
Canada’s first Zero Carbon–certified aquatic center cuts back on its carbon emissions while building community engagement.
By Adele Weder
COMPLETED THIS PAST SPRING in the heart of New Westminster, British Columbia, the təməseẃtxw Aquatic and Community Centre serves as a vital hub, not only for the surrounding neighborhood of single-family houses but also for the entire city of 87,000. Its name—roughly pronounced tamma-sout— means “sea otter house” in the Indigenous henqeminem language. It’s the city’s largest recreation center and its only indoor pool. As such, its purpose extends far beyond merely offering a place to swim or pump iron: It functions as the city’s main communitybuilder—the cathedral of this time and place. Designed by Vancouver-based HCMA Architecture + Design, təməseẃtxw replaces an aging indoor pool that had been built for the 1970 Canada Games. Three times as big as its now-demolished predecessor, with a state-of-the-art pool-water filtration system, the new facility is Canada’s first Zero Carbon–certified aquatic center, according to the architects. The project includes a comprehensive program of pools, saunas, workout rooms, a childcare center, gymnasiums, offices, a café, and a wealth of hangout spaces—elements that were defined through a three-year-long community engagement process that prioritized the voices of Indigenous community members.
The new təməseẃtxw Aquatic and Community Centre, located in New Westminster, British Columbia, is Canada’s first aquatic facility to meet the Zero Carbon Building Design Standard. Designed by HCMA Architecture + Design, this all-electric facility serves people of all ages and abilities, and offers spaces for wellness, recreation, and community connection.
The lobby, with its expansive skylight and sculptural spiral staircase, serves as a central hub, connecting visitors to pools, fitness areas, and outdoor plazas. With wellness-focused design elements, including indirect natural light for reduced glare, the facility promotes a sense of calm and inclusivity.
With over 13,000 residents per square mile, New Westminster is the second most densely populated municipality in Canada and is proud of its identity, history, and land. Millennia of Indigenous inhabitation were followed by the city’s 1859 establishment as the original capital of British Columbia. That honor lasted only seven years but transformed it into a major industrial site and transportation hub. Subsequent population growth ultimately cost the city much of its lush natural landscape.
The Glenbrook Ravine was one such treasure—and is now the site of the new aquatic center. Once a deep valley bisected by a freshwater stream, the ravine has long
since been backfilled. A large underground stormwater pipe replaced the stream, restricting the buildable land to a jagged, narrow footprint, which the design team used to their creative advantage. “Rather than follow the colonial grid, we torqued the whole thing,” says architect Paul Fast of HCMA.
Each main section of the building is defined inside and out by a roofline that cants and jogs in alignment with its respective position and function. In the main 50-meter lap pool, for example, the ceiling peaks at the diving-platform end and slants down toward the shallow end, a functional approach that also avoids the common but rigid shoebox form of most aquatic centers.
The wading pool is spatially distinguished from the main pool by a lower ceiling and a glazed dividing wall, which offers a more intimate atmosphere for its purpose and contributes to energy savings.
Entry plazas on each side are edged with naturalistic landscaping by Vancouverbased PFS Studio to partially restore the ambience and stormwater retention qualities of the historical ravine. The landscape architects sourced plants that once thrived on its slopes: salmonberry, huckleberry, cattail, and other native flora.
Inside, a spacious and comfortably furnished entrance area evokes a public living room more than a foyer. At the other
THIS YEAR’S AWARDS ARE PRESENTED IN PARTNERSHIP WITH:
The WELL Accredited Professional (WELL AP) is the leading credential for creating healthier buildings and organizations. It's never been a better time to turn your passion into purpose and join the community of 21,000 registered and accredited WELL APs who are on a mission to improve the health and well-being of people everywhere.
The right light preserves the night. Outline by Landscape Forms reimagines the familiar light column with refined aesthetics, elevated performance, and enhanced sustainability. The International Dark-Sky approved luminaires provide precise illumination and eliminate high angle glare, enhancing the visual experience while helping combat light pollution.
The təməseẃtxw Aquatic and Community Centre's design was shaped by a robust community engagement process, involving over 3,000 participants. Urban Indigenous community members, Host Nations, multicultural groups, and an accessibility committee all contributed valuable insights, guiding the facility's inclusive features such as zero-entry pools, high-contrast signage, and gender-neutral washrooms. This collaborative effort led to the center’s name, t
meaning “sea
house,” reflecting playfulness,
and family.
Hiring the right interior designer and sourcing the best products for your project can be a difficult task. Let Design Finder by ASID simplify your search with listings of:
+ Interior Designers + Design Firms + Manufacturers + Suppliers
Use this platform to search through project image portfolios, product examples, and resources to make your space come to life!
At American Society of Interior Designers, we believe that Design Impacts Lives and finding the right partners is a key piece of the design process. Put your trust in Design Finder by ASID as you search and source your interior design partners.
DESIGNERS AND SUPPLIERS, DON’T MISS OUT ON YOUR FREE LISTING!
YOUR NEXT PARTNER
The center’s eight-lane, 50-meter lap pool, complemented by two diving platforms, sits under a sawtooth roof that maximizes natural daylight. The multi-use leisure pool combines 25-meter lap lanes with spray elements and a lazy river for play and rehabilitation. With bifolding doors opening onto an outdoor sun patio, the pools seamlessly blend indoor and outdoor spaces, offering both recreational fun and wellness-focused features.
end of the foyer, the dramatic circular stairway offers the semiotics of a home, rather than an institution. Beyond the paid-admission wickets, the design team has devoted much attention to the way people use athletic spaces. Instead of a wide-open plan, the upper-floor fitness area is broken up into smaller zones from “leftover spaces,” as Fast calls them: the practical reconfiguration of irregularly shaped areas adjacent to elevators, mechanical rooms, and the pool-viewing gallery. The approach has the extra benefit of providing a greater sense of privacy for anyone navigating the fitness area.
The pool itself is distinctive for its suspended CLT beams that support the ceiling with the help of embedded steel
girders. “They’re fantastic; CLT doesn’t corrode,” says Fast. It’s also noteworthy for its adjacent and very open locker-room area: 70 percent of the lockers are all-gender, with just 30 percent specifically earmarked for males or females. And the main locker area features floor-to-ceiling glazing between the change area and the pool. Private stalls are available, but the overall configuration reflects a larger cultural acceptance of transparency and gender neutrality. “These places are ground zero for a lot of changes that are happening in society,” notes Fast, “and it all comes down to the details.”
The aquatic center now serves as a contemporary town square. “The notion of free is really important to us, to have a no-barrier condition,” says New Westminster
chief administrative officer Lisa Spitale. That means it is both universally accessible (the project has a Rick Hansen Foundation Accessibility Certification) and has large public spaces inside and out. The pool and workout rooms require an entrance fee, but the foyer “living room” is completely open and free to enter.
At sunset, the glazed facade turns the building into an illuminated beacon within the low-rise neighborhood. At a time when city dwellers find it ever more challenging to connect in person, the Aquatic Centre provides a welcoming venue. “People can stay as long as they want and connect with their neighbors,” notes Spitale. “You have every right to be there, and it doesn’t cost you anything. That’s the epitome of civic life.” M
March 25-27, 2025
Oregon Convention Center Portland, Oregon | USA
A Full Conference Pass includes: FREE print copy of the 2025 International Mass Timber Report, FREE breakfast & lunch, FREE coffee & tea, and access to over 190 exhibitors and five educational tracks to enhance your competitive edge.
NEW for 2025:
• More interactive networking areas on the show floor
• New track added for expanded education
• Five mass timber building tours
• Three days of education, now starting on Tuesday
30%onmostregistration passes,through January8
METROPOLIS’s Planet Positive Award winners represent excellence in sustainable, healthy, just design at every scale in the built environment.
The Children’s Museum of Eau Claire
• Holz man Moss Bottino, Steinberg Hart, WholeTrees Structures
• Eau Claire, Wisconsin
The Children’s Museum of Eau Claire (CMEC) is a first-of-its-kind two-story structural round timber (SRT) building designed by Holzman Moss Bottino and Steinberg Hart, with WholeTrees Structures coordinating foresters, engineers, and fabricators to make the structure possible.
WholeTrees brought together the Port Blakely Companies, which donated the Douglas-fir truss material; Seven Islands Land Company (ME), which donated the stunning 30-foot maple branched atrium columns; and the Township of Sheboygan, Wisconsin, for the ash columns. The production of SRT systems leaves the trees in their original form with minimal processing, releasing far less carbon than alternative structural systems. The resulting structure is the primary support system for the museum, consisting of round timber columns and joist-andgirder trusses in place of conventional steel.
In addition, CMEC is a 100 percent renewableenergy building. “The building project has been truly amazing for our entire region,” says CMEC CEO Mike Lee. “We have already served over 100,000 people this year, an increase of 135 percent from the peak at our previous location: something we certainly attribute to the natural feel of the new space.”
Seattle Convention Center Summit Building
• LMN Architects
• In assoc iation with Graham Baba Architects, Scharrer AD, Rolluda Architects, Tiscareno Associates
• Seattle, Washington
A 1.5-million-square-foot, $2 billion, LEED Platinum addition to the Seattle Convention Center, the Summit building occupies four city blocks in the heart of the city’s urban core. Featuring a vertically stacked program, it is the world’s first high-rise convention center.
Utility-cost and carbon savings were integral to the overall sustainability strategies at this scale. Relying first on an abovecode, efficient envelope, Summit achieves further energy savings with radiant floors (requiring 99 miles of tubing), heat recovery, a 75-kilowatt solar array, and advanced building control features. Stormwater runoff is collected from the massive roof and site, filtered, and stored within cisterns holding up to 400,000 gallons, reused in flush fixtures and for irrigation. Reusing stormwater and installing high-performance fixtures results in a more than 50 percent indoor potable water use reduction.
Total energy use reduction is 57 percent better than baseline building performance as reported to the AIA 2030 Commitment.
The Summit’s interior incorporates plant-based acoustic ceiling tiles with 71 percent recycled content, biobased fabric panels, a ballroom ceiling made of reclaimed worm wood from old log booms, and benches constructed from large salvaged timbers.
Nearly $150 million in various scopes of work was awarded to women- and minority-owned business enterprises (WMBEs), almost doubling the goal of $80 million. Close to 120 different MBE, WMBE, and WBE contractors performed services for the project. The project also achieved a 92 percent construction mat erial diversion rate, meaning only 8 percent of the material went to the landfill and the rest was recycled or reused.
Walker Hall Graduate Student Center
• Leddy Maytum Stacy Architects
• Davis, California
Walker Hall is an adaptive reuse of a modest building that was constructed in 1927 at the University of California, Davis to house its agricultural engineering program.
The life of the structure has been extended for another 100 years, reducing operational energy use by 84 percent below baseline, embodied carbon emissions by 57 percent in comparison with a new structure, and potable water use by 64 percent. The university’s original project goal was LEED Gold certification on a budget 20 percent below benchmark for similar projects. Through careful design, Walker Hall ultimately achieved LEED Platinum certification at no additional cost to the client.
Existing single-pane glazing was replaced with highperformance, thermally broken windows and extensive sha ding. The existing concrete walls were insulated at the interior, and the existing wood roof framing received both
rigid and batt insulation. Daylight modeling supported the introduction of new skylights to reduce lighting loads. An efficient, easily maintained VAV system provides heating and cooling using existing chilled and hot water from the central campus plant. An on-campus PV 16.3-megawatt solar farm meets all of Walker Hall’s electrical needs.
The design minimized interior partitions, simplified finishes, and prioritized the use of new low-carbon or carbon-sequestering materials, including 50 percent fly ash concrete, 75 percent recycled content structural steel, 50 percent recycled content gypsum drywall, FSC-certified wood products, and Cradle to Cradle Certified carpet.
Walker Hall illustrates the multiple economic and environmental benefits derived from harvesting the embodied carbon in existing structures.
Nueva School Science and Environmental Center
• Leddy Maytum Stacy Architects
• Hillsborough, California
The Nueva School Science and Environmental Center provides eight flexible science labs and support spaces for prekindergarten through eighth-grade students to explore the interconnectedness of humans and the natural world.
The project incorporates all-electric building systems and is designed to be net-zero energy. The narrow, linear form of the building combined with exterior circulation provides classrooms with ample daylight and natural ventilation, reducing energy loads associated with lighting and mechanical cooling. A highperformance envelope with a low 35 percent window/wall ratio further reduces energy loads.
Energy recovery ventilators provide 100 percent outside air when the classrooms are occupied. LED lighting reduces overall lighting power density by nearly half, while a roof-mounted
70-kilowatt photovoltaic array provides all the energy required for the building on an annual basis.
In addition, the design prioritized embodied carbon reduction through the use of new low-carbon or carbon-sequestering materials, including fly ash concrete, structural steel, gypsum drywall with recycled content, and Cradle to Cradle Certified carpet. Ultralow-flow fixtures and stormwater harvesting help reduce measured potable water use by 89 percent from baseline.
The building was designed to welcome all students and community members. The accessible Canopy Walk connects the new building directly with the Student Center and the heart of the campus across the steeply sloping site, inviting everyone to share the experience of gliding above the restored native oak woodland below.
Blue Oak Landing
• David Baker Architects
• Vallejo, California
Blue Oak Landing demonstrates that permanent supportive housing—long-term homes paired with social services—can be built quickly, affordably, and sustainably. On track to be a zero-energy building, this all-electric project was built with modular construction, reducing the construction time by three months and the cost by $1 million.
Furnished homes sit atop a ground floor filled with services, office space for a behavioral health organization, and an expansive creekside yard with vegetable gardens tended by residents. The “dogtrot” massing encourages natural ventilation, and upper floors are linked with open-air bridge circulation. The broad yard features a series of outdoor rooms characterized by landscaping that enhances permeability, stormwater treatment, and native habitat. The project is set within a generous, permeable na tive landscape that recharges the creek and surrounding urban wetland ecosystem.
A rooftop bifacial PV array is predicted to fulfill 70 percent of the building’s energy needs. Solar carports, not yet constructed, will provide the rest, making this one of the first zero-energy permanent supportive housing projects in California.
The modules for this building were fabricated at a factory three miles from the site, where more than 70 percent of the factory’s 400-person workforce are local residents, who took pride in building homes in their community. The factory supports union and “fair chance employment” practices, which involved hiring and training formerly unhoused and incarcerated workers.
Humanscale Showroom Chicago
• Reddymade
• Chicago
The new 4,000-square-foot Humanscale showroom in Chicago is designated Living Building Challenge 4.0 Ready by ILFI, and designed to comply with the standards for Design for Freedom by Grace Farms, which mandates ethical material selection and procurement practices.
“Our top priority when working on this space was to uphold the highest environmental standards, even if it had never been done before,” says the company’s chief sustainability officer, Jane Abernethy. “We hope this encourages other manufacturers to be more considered regarding their physical footprint.”
More than 90 percent of installed building materials and finishes are Red List compliant, including poured concrete flooring, electrical wiring, a dedicated outdoor air system (DOAS), gypsum wallboard, tile, and paint. The space features 42 Declare-labeled products and 19 Living Products. New wood is FSC certified, and wood doors were salvaged from another construction site. Nearly half the materials by cost were sourced within approximately 300 miles of Chicago.
For the Design for Freedom research initiative, the design team worked with 20 leading manufacturers to collect provenance documentation, such as raw material extraction locations, supplier lists, receipts, and written statements and/or certifications indicating responsible labor practices. These manufacturers shared statements confirming no forced or child labor within the organization, their business ethics policies, and their supplier codes of conduct that require their vendors to adhere to responsible labor practices.
Brucewood Homes
• RODE Architects
• West Roxbury, Massachusetts
Perched on a rocky outcropping in a quiet residential neighborhood, the Brucewood Homes are Boston’s first internationally certified single-family Passive Homes.
The homes use less energy for heating and cooling compared with conventional houses. The exceptional airtightness and controlled ventilation result in greater thermal comfort and excellent indoor air quality for very little energy. With solar arrays on the roofs, all three homes run net zero or net positive despite all three homeowners driving and charging electric vehicles. One home has reported using 23 kBtu/sf/yr while producing 34 kBtu/sf/yr—that’s 148 percent of its energy needs met with on-site renewables.
The buildings’ lower level is clad in a product made from recycled poly-ash, an industrial by-product; the upper level is
clear-finished white cedar sourced locally from Maine. Below the surface, the strapping is reclaimed wood from a local demolished barn.
The homes were carefully sited to minimize the amount of ledge removed from the site, reducing the impact of construction on the site and neighbors. The site plan preserved a number of mature trees, reducing runoff and erosion, and maintaining the urban tree canopy.
The project’s financial success proved to the developer and to the greater community that the market is ready for Passive House on spec. The developer and design team are now working on an 18-home Passive House neighborhood on a 28-acre site in the suburbs south of Boston, anticipating construction to start in early 2025.
Stanley Center for Peace and Security
• Neumann Monson Architects Muscatine, Iowa
The Stanley Center for Peace and Security drives global policy change in three policy areas: nuclear disarmament, mass atrocity prevention, and climate change mitigation. Its new headquarters is set to be the second renovation in the world to achieve full Living Building Challenge (LBC) Certification. The building produces 110 percent of its energy, collects all potable and nonpotable water through rainfall, and uses Red List–compliant materials.
Most of the existing building mass was reused, and nearly half of new materials were sourced within 310 miles of the site. A portion of the existing building was removed to create a courtyard where fresh produce is grown for the neighboring food bank. The co urtyard also delivers daylighting and views to 95 percent of occupied spaces. The ground floor houses mainly public spaces, while the second floor contains private offices.
The LBC’s Responsible Materials Imperative requires that at least 90 percent of new materials avoid Red List chemicals. The project’s systems-based furniture and private office fronts—Aspect and Beyond walls by Allsteel—have been vetted through the Materials Petal for low VOC levels and have Red List Approved Declare labels. These products were manufactured locally and supported the local economy.
This project turned a liability into an economic asset for the city and the community. The building’s history as a center of learning continues through programming that attracts schoolchildren, local visitors, and global policy makers—to date over 5,000 people have visited from six continents.
In addition, the Stanley Center’s partnership with a neighboring nonprofit provides a domestic violence shelter, mental health counseling, pediatric dental care, a food pantry, and other essential services.
Austin Community College Highland Campus Phase II
• BGK Architects, Perkins&Will
• Austin, Texas
The House at 436 Indiana Street
• Studio 804
• Lawrence, Kansas
Lake|Flato San Antonio Office Transformation
• Lake|Flato Architects
• San Antonio, Texas
Kawneer, Low–Embodied Carbon Aluminum Product Portfolio
Kawneer is reducing the embodied carbon of its aluminum products by using a minimum of 50 percent recycled content and cleanenergy smelting. This change lowers the embodied carbon of Kawneer’s aluminum billets by more than 60 percent from the current North American average, aligning with its goal to cut emissions intensity 40 percent by 2030. kawneer.us
Shaw Commercial Brands, EcoWorx Resilient
EcoWorx Resilient is Patcraft and Shaw Contract’s first PVC-free resilient flooring solution that is fully recyclable at the end of its useful life. Made from polyolefin materials, including up to 25 percent postconsumer recycled plastic, the flooring is carbon neutral, free of harmful chemicals, and offers durability with a 20-mil wear layer and high PSI tolerance. shawinc.com
Mohawk Group, Pathmakers
Mohawk Group’s Pathmakers Collection is a modular carpet tile inspired by bees’ journeys, promoting both biophilic design and sustainability. Made with Duracolor Tricor fiber and EcoFlex ONE backing, the collection is carbon neutral, diverts plastic from landfills, and uses 69 percent less water in its manufacturing. mohawkgroup.com
Teknion, Aarea
Designed by Pearson Lloyd for Teknion, the Aarea conference chair boasts a radically modular design that facilitates easy repair and recycling. Its five parts include a tubular steel frame, an upholstered seat cushion, recycled plastic arm pads, a recycled aluminum star base, and a bespoke mélange knit back made from retrieved marine plastic. teknion.com
Andreu World, Bolete Collection
Dedon, Seashell Nuo
The Bolete Collection features sculptural seating and tables made from Andreu World’s Pure ECO® thermopolymer—100 percent recycled, recyclable, and reusable. The collection combines organic forms, bold geometry, and customizable options in materials like oak, marble, and technical stone, enhancing both public and private spaces. andreuworld.com
Inspired by a seashell’s gentle embrace, the Seashell Nuo Collection by Dedon includes arm, side, barstool, and lounge chair options. The chairs feature lightweight aluminum and the brand’s new EcoCycle Fiber, which is 90 percent derived from renewable plant-based resources. dedon.de
Division Twelve, Crux Collection
The Crux Collection was inspired by design studio Afteroom’s Swedish design roots. Constructed from FSC-certified oak and tubular bent steel, the carbon-neutral collection includes chairs, stools, and tables with organic curves and seamless wood–steel connections. Certified for indoor air quality, Crux is crafted in zero-waste facilities using renewable energy. division12.com
Duravit, DuraStyle 1g Two-Piece Toilet
The DuraStyle 1.0 gpf two-piece toilet, designed by Matteo Thun and Antonio Rodriguez, features Duravit’s Rimless Technology for optimized flushing with minimal water. DuraStyle 1g is CALGreen, WaterSense, and cUPC certified. Customizable with right or left lever options, it also meets ADA height requirements. duravit.us
Lightly, Butterfly
The body of the Lightly Butterfly luminaire features 95 percent biodegradable components and offers easy disassembly. Available as a pendant or wall-mounted, the lightweight fixture delivers high-efficiency lighting (140 lumens/watt). Utilizing internal surface reflections, it also reduces glare while maintaining optical performance. lightly.com
Landscape Forms, Outline
Outline is a versatile, sculptural light column family, available in multiple heights, that enhances public spaces while minimizing light pollution. All products in the collection are International DarkSky Approved. landscapeforms.com
Cosentino, Earthic by Silestone XM
Earthic by Silestone XM, designed in collaboration with Formafantasma, is made with up to 30 percent recycled materials like glass, PET, bio-resin, and Dekton fragments. Featuring six graytoned colors across two series, the surfacing contains 10 percent or less crystalline silica and is made using 100 percent renewable energy and 99 percent recycled water. cosentino.com
Turf, Stone Textures
Turf’s new Stone Textures collection offers natureinspired patterns digitally printed on 60 percent recycled PET felt for wall and ceiling solutions. Mimicking stone’s organic veining, the collection enhances acoustics without the environmental impact of natural stone. Available in 31 colorways across three patterns: Marble, Travertine, and Granite. turf.design
RESEAT, RENEW
RESEAT is a SaaS platform that offers real-time tracking and access to a circular marketplace, helping customers manage, donate, sell, or renew furniture, reducing landfill waste. The system’s new RENEW feature streamlines reupholstery and refinishing requests, gives instant quotes, and provides accurate details. reseat.com
Armstrong, Ultima Low Embodied Carbon Ceiling Panels
Armstrong’s Ultima Low Embodied Carbon (LEC) ceiling panels offer a 43 percent reduction in embodied carbon compared with standard options. Made from mineral fiber and biochar, they enhance indoor environmental quality with excellent sound absorption (0.75 NRC) and blocking (35 CAC), while containing 55 percent recycled content and being fully recyclable through the company’s own recycling program. armstrongceilings.com
Designtex, Pepper
Pepper by Designtex features the innovative Loop to Loop yarn, which, developed in collaboration with Steelcase, Unifi, and Duvaltex, is the first closed-loop upholstery yarn made from recycling alreadyrecycled textile waste. Pepper can be used for upholstery and panels, and is available in 16 piece-dyed colorways. designtex.com
Forbo Flooring Systems, Marmoleum Solid
Marmoleum Solid linoleum offers 72 colors in a timeless minimalist design, utilizing natural materials for a climate-positive, durable, and healthy flooring solution. forbo.com
The Good Plastic Company, Polygood Translucent Collection
The Good Plastic Company’s latest range of Polygood panels made entirely from recycled plastic includes near-transparent patterns that react beautifully with light. thegoodplasticcompany.com
CEILINGS
Urban Evolutions, Veneer Plywood
Urban Evolutions’ Select Heart Ash wall paneling features live-sawn veneers from 65 to 85 percent reclaimed city trees, minimizing waste. urbanevolutions.com
Park for Floral Farms
• Dallas
• HKS Inc.
Situated on the site of a former illegal dumping ground known locally as “Shingle Mountain” in southern Dallas, Floral Farms Park was conceived through robust community engagement led by HKS. Bilingual sessions invited neighbors to shape a vision for reclaiming their neighborhood, historically centered upon agriculture and homes for families of color. After years of environmental injustice, including health issues caused by toxic waste, the Park for Floral Farms symbolizes renewal.
The design’s centerpiece, a “ribbon of play,” reflects the community’s desire for spaces that foster relaxation and discovery. This meandering path includes shaded seating, vibrant plantings, and play areas for children, promoting
both decompression and exploration. A bright yellow arch, inspired by the marigold—representative of the neighborhood’s resilience— marks the entrance. The iterative process included multiple design options, with feedback from neighbors shaping the final vision. Floral Farms Park is not just a response to environmental injustice; it is a testament to the power of collaboration, providing a restorative space that honors the community’s history and culture.
Trent Lands and Nature Areas Plan
• Peterborough, Canada
• SvN, Trent University
Natural Hazards Engineering Research Infrastructure (NHERI) Tall Wood Project
• LEVER Architecture
In 2017, LEVER joined the NHERI Tall Wood Project, an interdisciplinary research initiative funded by the National Science Foundation to study the seismic resilience of wood structures. As part of its continued research with NHERI, LEVER conducted seismic testing of a ten-story mass timber structure in May 2023.
The 112-foot-tall building features a rocking wall system designed to shift seismic loads back and forth during an earthquake, dissipating energy and reducing the overall impact. Tested on a three-axis shake table, the structure is the tallest wood structure ever subjected to full-scale seismic testing, generating groundbreaking data. The NHERI Tall Wood Project’s findings lay the groundwork for new engineering design guidelines, particularly for incorporating rocking wall systems into tall wood buildings. By sharing this data, the team aims to support code review processes in various jurisdictions and potentially inform future building code updates.
United Airlines Headquarters
• Chicago
• IA Interior Architects
The renovation of 13 floors at United Airlines’ headquarters in Willis Tower was focused on reducing carbon emissions while creating a dynamic branded workspace. The reuse and revitalization of the existing space was a top priority to align with United’s sustainability goals. The team reduced embodied carbon across six key categories: low-carbon carpet, acoustical ceiling tile and grid, reuse of existing metal stud and interior partitions, new demountable wall partitions, reuse of existing furniture, and landfill diversion of any furniture and fixtures that were not reused.
The new space reuses over 500,000 pounds of systems furniture and 793,000 pounds of other furnishings, diverting them from landfills. Acoustical ceiling tiles and grids were reused, saving 380,000 square feet from disposal. Any new materials used in the project were selected by prioritizing recycled content and circular design. Low-flow water fixtures contribute to a 30 percent reduction in water use, and energy-efficient lighting cuts energy use by 23 percent.
843 North Spring Street
• Los Angeles
• LEVER Architecture
A windowless 1980s-era retail warehouse, 842 North Spring Street is now one of the first and largest hybrid CLT buildings in L.A. The office blends the city’s high-rise and warehouse cultures—with a material palette of mass timber, steel, and concrete, and a floor plan that integrates outdoor workspace and biophilic design.
LEVER worked with landscape architect Field Operations to leverage the climate and landscape the city is known for. Outdoor space is maximized in and around the building with a tiered vertical garden courtyard between the office wings, open-air circulation spaces, pr ivate balconies, and a shared rooftop amenity
deck—all contributing to the well-being of anyone in the building.
In addition to natural ventilation, the project hits sustainability and wellness targets via a rooftop solar PV array, EV charging stations, more than 200 bike stalls, recycling rainwater for reuse on-site as landscape irrigation, and a facade designed to reduce solar heat gain.
Victory Wellness Center
• Los Angeles
• Patterns
Catifa Carta
• Arper
Designed in collaboration with Swedish start-up PaperShell, Catifa Carta is a sustainable reinterpretation of Arper’s original iconic design, the Catifa 53. Its seat is crafted from PaperShell’s revolutionary namesake material, which transforms discarded offcuts of deceased trees into durable craft paper. To create the seat shell, 29 sheets of the ecofriendly paper are meticulously pressed into a mold with steam and bio-resin. Catifa Carta maintains the characteristics of Catifa 53—elegance, reliability, and durability—and is UNI-EN 16139 certified while being compliant with BS cigarette and match requirements. Steel and black aluminum base options are available in dark brown and graphite finishes, and the shells are mounted to the base with four hex screws. Catifa Carta is manufactured in the south of Sweden, with production being overseen by PaperShell.
Partnership Toward Zero Waste
• Tarkett
Globally, Tarkett has set a goal that its products will consist of 30 percent recycled content by 2030, and its ReStart® take-back program is its core strategy for achieving this goal. Since the program’s inception, ReStart has diverted flooring waste equivalent t o 12 Eiffel Towers from landfills. In 2023 alone, 1.5 million pounds of post-use flooring were recycled in North America. Now, through an exclusive partnership with Mycocycle—a biotech start-up leveraging the power of mycelia to break down waste—Tarkett is pioneering a unique recycling approach. While Tarkett’s goal remains to recycle old flooring into new flooring whenever possible, the Mycocycle technology will provide a diversion option for materials that are traditionally hard to recycle. Tarkett will also explore the resulting by-product as a central ingredient in new flooring products.
Rwanda Institute for Conservation Agriculture
• Gashora, Rwanda
• MASS Design Group
Rwanda’s population in 2050 will be ten times greater than it was in 1950. During this period, the land has transformed from predominantly forest and savanna to subsistence farming. Sustainably nourishing this growing population requires the production of more nutritious food within a shrinking land area while addressing challenges such as climate change, biodiversity loss, soil degradation, and pollution.
The Rwanda Institute for Conservation Agriculture (RICA) serves as an alternative model for agriculture training and regenerative construction in East Africa and around the world. The 1,400-hectare, 69-building campus plan balances human, ecological, and animal health. Approximately 90 percent of RICA’s 1,200 workers were local and the campus was built with predominantly natural and local materials, leading to 60 percent less embodied carbon than baseline. The net-zero campus operates off-grid with a 1.5-megawatt solar array and on-site water treatment. With optimized land use, RICA will be climatepositive by 2040, conserving local ecosystems and contributing to Rwanda’s regenerative future.
River People Health Center
• Scottsdale, Arizona
• SmithGroup
The River People Health Center (RPHC) is a beacon of hope for the Salt River–Pima Maricopa Indian Community (SRPMIC), whose members have experienced severe health disparities and have an average life expectancy of just 52 years. The RPHC is a direct response to the community’s “five in five” goal: to increase members’ average life span by five years within five years of opening.
Funded by the Indian Health Service, an agency of the Department of Health and Human Services, the RPHC transformed a poorly maintained golf course into a vibrant health and wellness hub. Its design is a tribute to the community’s resilience and tradition, inspired by the ne arby sacred mountains and the lore of a healer who journeyed from peak to peak to learn their craft. Since opening, the RPHC has unified, expanded, and introduced new services, eliminating the need for community members to travel more than 45 miles from their homes to receive comprehensive care.
The Theodore Roosevelt Presidential Library
• Medora, North Dakota
• Snøhetta
The Theodore Roosevelt Presidential Library will invite visitors through a preserved North Dakota landscape, supporting conservation research with its educational walks and recreation while serving as a biological repository for Badlands flora.
Inspired by Roosevelt’s environmental legacy and periods of introspection, the library loop will connect adventurous paths to the Maah Daah Hey Trail and pavilions. Ranging from contemplative nooks to expansive vistas, these pavilions will invite visitors to experience Roosevelt’s trials and triumphs in dialogue with the landscapes that shaped him. Visitors can also ascend an accessible rooftop to take in views of the
national park and Roosevelt’s Elkhorn Ranch, or to stargaze at night.
The library’s construction will use locally sourced and renewable materials, including mass timber, while its sophisticated energy systems will set a new standard for sustainable design in the region. The design also mitigates the impact of wind and other climatic factors so that the library will be accessible in all seasons.
The Phoenix
• West Oakland, California
• MBH Architects, Factory OS, and Autodesk
Melissa Kelly
• Sust ainability Director
• G ensler
As a sustainability director in Gensler’s Climate Action and Sustainability Studio, Kelly advises clients like Google, Daniels, and JPMorgan Chase. But “beyond her project work, Melissa has made a significant impact on the industry,” says David Briefel, a principal and global resilience leader at Gensler. “She has spearheaded the develop-
ment of our analytics services across the firm, mentoring dozens of professionals along the way, including a dedicated group of women focused on analytics.” Kelly has also been closely tied with the creation of the Gensler Product Sustainability standards—sustainability performance criteria for the top 12 commonly used, high-impact products selected
for Gensler’s architecture and interiors projects. In particular, Kelly was instrumental in setting the standards aimed at reducing embodied carbon impacts, creating a methodology for benchmarking embodied carbon that carefully considers market availability, reduction opportunities, and the reliability of the underlying data.
In June 2024, the University of Florida’s Student Health Care Center, designed by CannonDesign, became the first higher education building in the United States to attain WELL Platinum certification. It joins CannonDesign’s always-growing roster of sustainable, healthy buildings created through an advisory and consultative relationship with clients—the WELLand LEED Platinum–certified Toronto headquarters for LinkedIn, SUNY Albany’s LEED Platinum ETEC Building, and the beautifully engineered mass timber Resnick Sustainability Center at Caltech that’s pursuing LEED Platinum. At the time of writing, 74 projects by the firm are aiming for LEED certification, and one is targeting the Living Building Challenge.
“We’re actively cultivating new partnerships, directing resources toward research and embracing ne w technologies, all geared toward amplifying our positive impact,” writes the firm’s director of sustainability Eric Corey Freed in its 2023 Sustainability Impact Report. Recent developments include tracking embodied carbon on every project with Tally and EC3 for envelope, structure, and major interior elements; developing a firmwide Building Material Database of products with ingredient certificates and EPDs; and updating the firm’s energy reporting process for a higher degree of tracking and accountability on energy use intensity (EUI) reduction. As it is, in 2022 the firm’s whole building projects did 54 percent better on average than the AIA 2030 EUI reduction benchmark.
As the firm’s 14 full-time sustainability team members continue to improve both internal process and project outcomes, they share actionable advice that is aimed at clients but accessible to their professional peers through CannonDesign’s Planet 2100 initiative.
Evan Shieh
• Assi stant Professor of Architecture
• New York Institute of Technology
Shieh’s teaching, research, and professional practice are at the intersection of architecture with urbanism, landscape, and infrastructure. In spring 2024, he taught a final-semester MArch thesis studio in which students investigated how architecture could contribute to the resilience of ecological, sociocultural, and infrastructural systems in the São Cristóvão neighborhood of Rio de Janeiro, Brazil. For his teaching, Shieh was awarded the 2023 Presidential Excellence in Teaching Award by New York Tech, and the national 2023 New Faculty Teaching Award by ACSA/AIAS. He is the author of Autonomous Urbanism: Towards a New Transitopia (ORO Editions/AR+D Publishing, 2024), a two-volume book monograph on the impact of autonomous vehicles on the future of cities. Shieh is also the director of Emergent Studio, a design and research office, and previously worked at Henning Larsen, UNStudio, and New York City’s Department of City Planning.
Michelle Jacobson
• Facult y Member
• New York School of Interior Design
Jacobson is the founder, president, and CEO of the interior design firm MLJacobson Design, which focuses on healthy and sustainable environments. Her teaching at NYSID enables students to make interior design decisions that enhance the health and well-being of both people and the planet. In the design studio “Sustainable Residential Design for Graduate Students,” the class undertakes the interior renovation of an existing multilevel
historical residence, applying sustainability principles to residential space planning, lighting, mechanical systems, finishes, fixtures, and furnishings. Jacobson has served as a special researcher for the ASID Committee on Climate, Health, and Equity. She is a member of the ICC Code Interpretation Committee and the ICC Sustainability Membership Council, and is a reviewer for the Fitwel certification at the Center for Active Design.
Indigenous Urbanism
Charley Andrews, Jane Wu
• UCLA, Master of Architecture
• Instruc tor: Jeffrey Inaba
Andrews and Wu’s master-plan proposal for Cathedral City in the Coachella Valley seeks to reconnect previously divided land, consolidating the land and sovereignty of the Agua Caliente Band of Cahuilla Indians. Through careful historical and regional analysis, as well as conversations with the Agua Caliente Band, the students decided that Cathedral City would be the best site to explore a new framework of indigenous urbanism. They imagine a phased series of changes in land status that would gradually consolidate tribal land; an acknowledgment of different relationships to that land, whether it be wild or managed; a network of pathways and courtyards; and, finally, a layer of new programming that includes housing, commercial use, and new amenities like a welcome center.
West Farms Community Land Trust+
Kendal Eastwood, Elise Park
• New York Institute of Technology, Bachelor of Architecture
• Instruc tor: Evan Shieh
Eastwood and Park propose a community land trust (CLT) model to address the problems with affordable housing in the West Farms neighborhood in the Bronx, New York City. Careful analysis of other housing developments and CLTs and input from residents build up to a proposal for layered missing middle housing, public space, industry zones, and more—all planned through community participation. Comic artist Matthew Wong helped Eastwood and Park visualize the implications for families and individuals in West Farms.
By Brian Libby
On a recent morning at Portland International Airport, passengers weren’t just hurriedly wheeling suitcases through the new terminal. They were stopping to marvel and snapping photos of an undulating nine-acre mass timber roof, a grove of mature trees beneath dozens of skylights, and an auditorium-style seating area where friends and family could meet them upon return. If moving through many American airports can be a claustrophobic march, this evokes walking through the wideopen railway palaces of yesteryear like Grand Central Terminal.
“It was the idea of creating a transit center that acts as a civic room,” says Eugene Sandoval, a partner with ZGF, the new terminal’s designer.
PDX, as the airport is familiarly known, was already beloved before its multiyear expansion and renovation, the first phase of
which opened on August 14. The airport has repeatedly ranked as America’s most popular in national polls. Even PDX’s carpet has gone viral: Thousands post Instagram pics looking down at their shoes on the teal flooring.
Yet the airport had to grow and change. The Port of Portland, its operator, needed to accommodate an estimated 35 million annual passengers by 2045. But within metropolitan Portland’s urban growth boundary, there wasn’t land f or an entirely new facility—which wasn’t the sustainable choice anyway. Simply building onto the existing terminal, a hodgepodge of conjoined buildings, wasn’t viable either. PDX needed seismic resilience to survive an unprecedentedly powerful Cascadia Subduction Zone earthquake predicted. Oh, and the existing terminal had to remain operational during construction.
The new main terminal brings the Pacific Northwest indoors with mass timber and greenery, and integrates previous design elements like the original PDX carpet. Two new video walls feature a 24-hour art installation called “Extraordinary Windows” by Half Sister Studio and Dot Dot Dash.
The answer was what would become America’s largest mass timber airport: to prefabricate at the edge of PDX’s grounds. The structure is a nine-acre wood roof, doubling the existing terminal’s square footage. After slowly sliding the roof into place on hydraulic jacks over several nights in 2022, the just-completed rst phase, built underneath it, includes new check-in counters, a market hall lined with local businesses, enlarged security checkpoints, and a so-called “walk in the forest,” which includes 5,000 plants and 72 mature black walnut, cus, and olive trees, courtesy of Portland landscape architecture studio PLACE. Phase 2, with passenger exit lanes, additional shopping/dining areas, and north-south views through walls of glass, will open in late 2025.
“By choosing to add-on over a new airport, the project reduced its carbon footprint by 70 percent, but this required complicated choreography. Not a lot of airports have tried to do what we’re doing,” says George Seaman, the Port of Portland’s engineering project manager. “Our biggest challenge was how to keep operations ongoing while building close to two billion dollars’ worth of work around it. And that was one of the impetuses for the remote fabrication of the roof structure.”
The roof, made with 3.5 million board feet of Douglas fir, comprises 14 rectangular pieces, or cassettes, that sandwich mechanical, electrical, and plumbing between a mass-plywood roof diaphragm and a latticed timber ceiling, all connected with glulam beams. Some 49 skylights provide about 60 percent of the terminal’s illumination. The 18-million-pound roof sits 55 feet above the ground on 34 steel Y-columns.
The old terminal’s popularity was due partly to its intimate scale, as well as its focus on local shops and restaurants, most
PDX WOOD ROOF AXON
The new nine-acre mass timber roof was built through a modular and prefabricated system manufactured remotely and transported to the site while keeping PDX fully operational.
notably the iconic Powell’s Books. In its vastness, “people were afraid the new airport wouldn’t feel like Portland’s,” says ZGF managing partner Sharron van der Meulen. “So we approached it very strategically and tried to break it down into a series of ‘rooms.’ We looked for inspiration from some of our beloved streets of Portland, and we used the same dimensions for the [central] walkway.” The local focus is also back, including what’s called “street pricing”—instead of inflated airport prices, a burger or beer here costs roughly the same as outside.
Inspired by farm-to-table cuisine, ZGF and its consultant Sustainable Northwest Wood created a “forest to frame” approach. Wood was sourced from landowners and mills within a 300-mile radius of the airport and is either Forest Stewardship Council–certi ed or traceable to forests or landowners meeting equally forestfriendly practices. The team also prioritized sourcing wood from smaller mills, family forests, nonpro ts, and tribal nations.
“To me it’s a beautiful love story of what happens when people and the land come together,” Anne Niblett of the Coquille Indian Tribe, whose forest in southwestern Oregon provided wood for the roof’s glulam beams, said at the terminal’s opening dedication.
This is not how the timber market normally works. When ZGF began the project, “you couldn’t answer how much wood came from, say, fire-resilience harvesting, or from small familyrun forests doing good forestry,” recalls ZGF associate principal Jacob Dunn. Instead, “forests get logged. The logs go into piles, go through a mill, and they get turned into products. They’re not segregated by forest origin or landowner type. So there’s no way to say that this deck of wood came from this forest. It gets completely blended up.”
Because the PDX terminal was such a big project, ZGF and the Port of Portland were able to “define our own set of criteria,” Dunn adds. “Just by asking, ‘Where did this come from?’ we can start to answer some questions. We could engage mills and ask them, ‘Can we make a custom purchase?’ Now we have a way to actually have a positive impact on where our wood’s coming from.”
For some small providers, PDX has proved transformative. The terminal includes oak tile flooring from Zena Forest Products, harvested from Oregon’s last remaining commercial oak forest. The company had earned its revenue from wide-plank oak flooring, but there was no market for the forest’s thinner
oak trees. The airport commission enabled Zena to invest in new machines to make tile from strips of these thinner logs. PDX also utilized wood salvaged from wildfires east of the Cascade mountains, on Nature Conservancy–owned land.
For Peter Hayes, a sixth-generation owner of the Forest Stewardship Council–certified Hyla Woods in the northern Oregon Coast Range, which supplied lattice for PDX’s ceiling, the airport brings hope for systemic change. “Until very recently the dominant message from the market has been ‘We don’t care where the wood comes from.’ It’s a slice of the value proposition that gets thrown away,” he says. “What’s really different about the airport is they’re saying, ‘We insist on knowing where.’ And they’ve had to thread a political slalom course, because the timber industry is powerful in the Northwest.”
For that reason, Hayes adds, PDX is not just a project but a process. “We’re building an experience of cooperation in a time where cooperation isn’t very fashionable. I see it as one point in a continuum. Where will this go in the future? And how do we make sure it’s not just a one-time deal that only a public entity can pull off?”
In the meantime, passengers may still be gazing downward to snap photos of their feet on the airport’s carpet, but even more often, they’re looking upward. M
ZGF and the Port of Portland pursued radical transparency in the wood supply chain for the new terminal, keeping close track of every source of wood (left) and leveraging a network of landowners and mills (opposite). “We can tell you exactly where each three-by-six board came from,” says Kevin Kaster of Kasters Kustom Cutting, one of the mills who supplied the project.
ZGF's Portland Airport expansion served as a test bed for the tool developed with the University of Washington's Applied Research Consortium.
By Francisco Brown
ZGF, in collaboration with the University of Washington’s Applied Research Consortium, has developed a wood life cycle calculator called UpStream. This spreadsheet tool helps designers assess biogenic carbon storage, forest carbon sequestration, and end-of-life scenarios for wood products. Portland Airport’s wood roof served as a perfect test bed for this tool.
“We were trying to understand upstream carbon dynamics of mass timber—going back to the forest and connecting everything,” says Jacob Dunn, ZGF’s principal. UpStream aims to integrate carbon impacts from forest management into life cycle analyses (LCA) and allows for custom end-of-life scenarios for wood products.
The challenge, Dunn explains, was how to quantify carbon in forests properly and attribute it to wood products. ZGF identified two key issues: Many end-of-life scenarios aren’t modeled at all, and when they are, there’s an assumption of biogenic carbon neutrality. This assumes that as long as the forest regrows, carbon emissions from wood in landfills or incinerators will be offset by tree regrowth. However, the team wanted more flexibility and accuracy. For example, local conditions in Portland meant a default 50 percent of wood goes to landfills and 50 percent to incineration, rather than relying on accurate figures. That’s why the airport’s design, sourcing, and construction were crucial for developing this new tool.
“We needed to rethink biogenic carbon,” Dunn says, explaining that the forest and built environments are interconnected. The wood in a building isn’t isolated but part of a larger carbon cycle that must be optimized for climatesmart forestry. The goal is to increase the amount of carbon stored in wood, reduce emissions by substituting wood for steel or concrete, and promote the reuse of durable wood products.
The tool’s basic approach involves calculating the carbon sequestration in a forest over time and dividing that by the amount of wood harvested. Using both observed satellite data and NASA resources, the team measured how much biomass grew on specific lands over the past 30 years. Satellite tools like lidar could analyze forest growth on a per-pixel basis, tracking changes in carbon stocks across small or large tracts of land.
At Portland Airport, the team connected this data with their wood sourcing, applying carbon factors to the wood based on its origin. “This was the ‘aha’
moment,” Dunn says, as they began quantifying how much carbon each forest saved or emitted. The variation was significant depending on the data set and forest in question. These discrepancies also opened the conversations about forest stabilization and rotational patterns as regeneration practices.
According to the ZGF team, the case study cemented three principles for climate-smart sourcing in the region: first, understanding how harvest practices in the Northwest can influence carbon storage; second, evaluating whether the forest is increasing its carbon stocks over time; and third, working with definitions and frameworks to ensure that forests are managed sustainably, stabilizing carbon where needed.
By integrating these data sets, UpStream has provided the tools to analyze and optimize wood’s role in the carbon cycle. Portland Airport is proof of the concept’s potential to guide climateconscious building practices for the region and the entire nation. M
Beneath its vast nine-acre roof, the terminal is designed for a human-scaled, stress-reducing experience.
By Brian Libby
The airport embraced biophilic design both to reflect the natural beauty of the region and to strategically enhance the experience of different people in the terminal (right and below). A forestlike central zone surrounds visitors with trees and diffused light, creating a serene oasis amid the brightness and bustle of the entry and ticketing areas.
The redesigned and extended ticket hall (opposite) was planned for clarity and a sense of ease. It’s built with the future of travel in mind, accommodating evolving traveler needs, technological advancements, and the opportunity to keep expanding.
Although PDX’s new terminal is defined by its vast mass timber roof, ZGF’s design also focused on human-scale experience, with an emphasis on biophilia.
“The Port [of Portland] was very clear that a key outcome was to reduce passenger stress,” recalls Bill Browning of Terrapin Bright Green, the project’s sustainability consultant.
The design team created several user profiles to map high-stress areas and target specific moments of intervention. Just after the ticketing area, for example, passengers encounter a grove of mature deciduous trees (under the largest among dozens of skylights) before moving on to restaurants and shops or ensuing security checkpoints.
Not only do the trees deliver a dose of nature, but their canopy provides a protective sense of enclosure.
The roof itself is part of the biophilia strategy, from the warm-feeling wood to its curvy biomorphic shape.
The skylights’ wood-lattice edges create dappled light patterns like a tree canopy. “That’s a type of fractal pattern that we know lowers stress,” Browning explains, citing studies by University of Oregon physicist Richard Taylor that influenced the design.
A nearby mezzanine, where a large pub is located, provides a perch supporting two aspects of biophilic design: prospect, or an ability to survey your environment; and refuge, a place of protection.
The lower-ceilinged security checkpoints, above which are Port of Portland conference rooms, were affixed with large video walls featuring soothing artist depictions of nature.
The terminal’s displacement ventilation can be fine-tuned in specific spaces, like a deliberately lower-temperature security area, where people tend to sweat the most.
Before the terminal opened, Sandoval took his 15-year-old son, whose responses were ideal. “He said, ‘One, wow: It smells like wood.’ Second, he said, ‘The light is really comfortable,’” Sandoval remembers. “Third, he goes, ‘It’s so peaceful.’ And fourth, he said, ‘I want to come here early before our next flight.’ That to me was the ultimate win.” M
The world’s most popular green building certification is getting ready for an update. Here’s what you need to know about it.
By Prateek Jain
Illustrations by Kate Dehler
two million square feet of real estate in 186 countries and territories around the world receives LEED certification from the U.S. Green Building Council (USGBC). So, as the latest version of the building certification, LEED v5, is being reviewed for official launch in early 2025, it faces an all too common challenge: pitching a big tent while trying to make a big dent. Specifically, the building industry has asked LEED to respond to two persistent critiques that aren’t mutually exclusive but present a formidable task to reconcile:
• Do more for climate action and move the market
• Reduce documentation burden and extra work for practitioners
And LEED is expected to achieve this while being a flexible system applicable across building types and geographies! Even skeptics would agree that this ask is gargantuan.
The first drafts of LEED v5 came out in April 2024. Since then, it has undergone two rounds of public comments, with the second round wrapping up in October at the time of writing this article. The drafts have received nearly 6,000 comments from designers, builders, developers, manufacturers, and nonprofits, signaling both strong engagement from the market and the high stakes for this endeavor. While we can expect further changes to the standard before the launch next year, let’s unpack some of the biggest moves in LEED v5.
The certification requirements span hundreds of pages, but even without diving into their substance, there are some clearly discernible takeaways from the way USGBC has packaged LEED v5 and communicated the big changes in it.
HERE’S WHAT STANDS OUT:
• Simpler messaging: LEED v5 has simplified its impact to three goals—de-
carbonization (climate action), ecology (restoration and preservation), and inclusivity (quality of life). Every credit and prerequisite maps to one or more of these goals, which makes it easier for clients to communicate the impact of LEED and for design teams to prioritize which credits to pursue.
• Investor alignment: While ESG reporting and investing have become increasingly mainstream (with public debates raging in the business community), its connection to building projects has been tenuous. As a third-party benchmark, LEED certification (as a whole) does feature in several companies’ ESG frameworks. But deeper synergies between building-scale reporting and company- or fund-scale KPIs are still nascent. LEED v5 takes a positive step in that direction with its carbon assessment requirements, which should plug neatly into developers’ portfolio-scale planning for greenhouse gas emission reporting. The new equity and resilience requirements should align more easily with ESG frameworks as well.
HERE’S WHAT’S STILL MISSING:
• Simpler documentation: Does LEED v5 help reduce paperwork and enable teams to spend more time on design impact? A new digital platform promises to streamline how project teams document their work, but it’s unclear whether going through the process will be any less cumbersome than it currently is.
• Performance verification: LEED has never required much on-site verification or post-occupancy monitoring for BD+C/ID+C rating systems, unlike schemes such as Living Future’s Zero Carbon or the IWBI’s WELL. LEED’s emphasis has been on rigorous documentation as a means of proof, and that appears unchanged.
Overall, LEED v5 has the same structure as previous versions, with several mandatory prerequisites and 110 points to choose from. Point thresholds for the
ratings—Certified (40), Silver (50), Gold (60), and Platinum (80)—remain unchanged, but the Platinum club is now more exclusive and requires unequivocal commitment to decarbonization. The requirements continue to be wide-ranging and detailed, adding both breadth with new topics and depth to existing themes.
The themes of equity and resilience have graduated to the main rating system after being on the fringes in v4’s innovation and pilot credit catalogs.
• Equity: New requirements include assessing demographics, local infrastructure, human health impacts, and occupant experience. If this doesn’t quite add up to “equity” in your opinion, that’s because the April draft’s “Social Equity Assessment” prerequisite attracted strong commentary on the added effort to meet its requirements for community engagement and concerns about the language’s political implications. So, the originally laudable effort has morphed into the broader and arguably easier “Human Use Assessment” prerequisite in the October draft. Nevertheless, optional requirements for the “Equitable Development” and “Accessible Outdoor Space” credits do cover more ground, addressing community benefit programs, affordable housing, public use of spaces, diversity in project teams, and designing for physical accessibility. The “Accessibility and Inclusion” credit takes it up a notch by addressing physical diversity, aging and safety, social health, and navigation.
• Resilience: In less politically charged territory, new requirements for resilience are fairly technical and make teams address at least two “priority hazards” from a long list of natural calamities. There is ample opportunity to align with jurisdictionally required studies, and for European projects to align with the EU
taxonomy. Optional measures push teams to leverage the assessments and incorporate tangible design strategies for the hazards they’ve identified.
Decarbonization-related credits account for nearly half the points in LEED v5, which is a remarkable commitment to climate action. A few key credits are analyzed below:
• Carbon assessment: Projects will be required to compile a holistic 25-year projection looking at operational, embodied, transportation, and refrigerant emissions using data collected in related credits, which in turn require detailed studies and decarbonization planning.
• Embodied carbon: All projects will now be required to quantify embodied carbon for construction materials, but the prerequisite does not require demonstrating a reduction. This is a good starting point, and the corresponding credit awards up to six points for demonstrating reductions in a variety of ways. A whole-building LCA using specialized software is not necessary but does provide the most points. This increased emphasis is laudable, but there are some missed opportunities:
Metrics: LEED v5 still doesn’t provide full clarity on LCA baselines, which is arguably hard to define for a variety of project types (and the April attempt drew dozens of comments), nor does it move toward absolute carbon intensity targets like Living Future’s Zero Carbon.
Procurement focus: Selecting cleaner materials and products lies at the center of the credit, but efficient design to reduce material quantities is not as well rewarded.
Limited scope: While hardscape materials must now be addressed, teams don’t get additional credit for capturing
interiors, MEP, and FF&E, which are also increasingly recognized as significant emission sources.
• Electrification and enhanced energy efficiency: With an eye on long-term emissions, LEED v5 prioritizes heating electrification while providing sufficient flexibility for projects in cold climates, having gas for cooking, etc. The v4 energy performance credit has now branched into two: Energy Efficiency— which provides multiple options to reduce energy modeling burdens but still suffers from methodological challenges in tying in to ASHRAE 90.1-2019—and Reduce Peak Thermal Loads, which is a laudable effort with extremely technical compliance paths that will likely see more changes.
• Refrigerant management: Fugitive emissions from refrigerant leakage get more attention in LEED v5. Aligning with the Kigali Amendment, the AIM Act, and more, this credit is now much more stringent and worth more points. Compliance may be challenging initially, but the market must move in line with incoming regulations, making it easier over time.
In aggregate, LEED v5 has barely removed any v4 requirements while adding what feels like another third of additional requirements. In those retained requirements, though, we see several nuanced updates. Among the most prominent in this category is probably the “Building Product Disclosure and Optimization” credit.
This credit has expanded in scope, now addressing themes of social health and circularity more explicitly while retaining emphasis on third-party ecolabels. The calculation methodology remains complex and will continue to draw the ire of project teams, and the exclusion of structural materials also raises eyebrows. But it might be best to withhold detailed commentary on this credit until associated calculators and final updates (which are highly likely) become available.
LEED v5 clearly attempts to do more for climate action and moving the market than previous versions. New additions of equity and resilience make the certification more holistic and help align it with investor frameworks.
However, with this increased depth and breadth, project teams will need more design thinking and analyses than they did with LEED v4. While this may result in higher soft costs, the resulting impact should be commensurate.
That’s because v5 is complex for a reason. LEED still wants to be accessible to projects with varying levels of ambition, different building typologies, and across geographies. And it still wants to be rigorous while not requiring on-site verification. This means providing more options for compliance and asking for more details, which results in a complex set of requirements. To tackle this increased complexity, projects will require specialists or sustainability champions. They will need to corral interdisciplinary teams to navigate all the options and determine which certification pathways will be most effective for each project’s unique circumstances.
USGBC takes pride in the consensusdriven development process of LEED and welcomes industry engagement. LEED v5, coming 12 years after its predecessor, is a huge step in the right direction, and we need the broader professional community to engage in the conversation so we can all get this right. M
Deciphering the labels on natural and nature-inspired materials is not easy. But clarity is coming.
By Audrey Gray
early in her career (this was the ’90s), architect Tracy Stone got a chance to work with Ray Kappe, the deeply rooted SoCal architect revered for his warm take on Modernism. Kappe liked his clients to feel super-connected to the natural elements already in play on a site. “To experience each tree to its fullest and to create an ambience sensitive to light and sounds are prime goals,” he once said, a biophilic ethos if there ever was one. Stone was fascinated by how Kappe pulled it off with the simplest palette of materials.
“The first house I worked on with him didn’t have one piece of drywall in it,” she remembers. “And that was the Keeler Residence!”
Stone’s respect for Kappe’s short list of “honest” building components endured. She branded her own practice “California modern architect with a focus on natural materials.” But three decades later, she’s found it increasingly difficult to discern what’s natural and what’s a petrochemical mash-up. Even sourcing a product as simple as rubber base molding, something that would logically come from a rubber tree, requires reconnaissance. Are the “rubber” trims on offer bendy and rubberlike? Yes, but what are they really made of, and in what percentages? What do labels like “biobased” or “biosourced” guarantee, if anything? And which manufacturers are willing to be fully transparent about any of this?
“I call ’em sometimes,” she says, ready to keep asking questions until she knows for sure.
Complicating the quest is the fact that professionals (even the eco-sensitive) at various points
along the supply chain are operating with different definitions of the same bio-labels. Legal standards and certifications haven’t quite caught up with the growing urgency industry-wide to specify lower embodied carbon, and less toxic materials. So, in the same way a well-drawn lime-green leaf on a package can mislead, the letters B-I-O worked into a product description can suggest a noble origin story that might be largely fictional.
“It’s a bit of a swamp out here,” says Alison Mears, cofounder of the Parsons Healthy Materials Lab in New York. “These terms are being used by any number of people to indicate a little sprinkling of something that maybe one time was a plant.”
Not only is this confusing to designers making product choices on deadline, but a word like “biobased” can still spook a facility manager or building inspector comfortable with the established solidity of conventional building products. In ultrapractical ways, words matter.
Clarity is coming. Scores of academics and practitioners are working hard right now to help each other define and discern which natural and nature-inspired materials meet specific goals. They are using tools and lists like the HPD (Health Product Declaration) Standard and mindful MATERIALS. The Parsons Healthy Materials Lab has developed a compendium of these sorts of tools, along with its own vetted lists of categorized building products, like 16 “Adhesives, Mortars, Grouts, and Sealants.” Meanwhile, here’s a stab at working definitions for six commonly used biowords, based on interviews with some of the people paying the closest attention.
/bīō jenik/
Think about living organisms and natural processes as executive producers of these materials. It’s the raw stuff—made before humans got their hands on it. Shells of marine animals are biogenic, as is the straw from our farms and the timber in our forests. But so is the crude oil pooling deep under the ocean floor before it is turned into plastics. “Perhaps look at it as a mono-material,” suggests Lola Ben-Alon, director of the Columbia GSAPP Natural Materials Lab, who cautions that not everything produced by nature is beneficial for humans or harmless to ecosystems when processed/burned, so “biogenic” is not a label of absolution. It’s more a signal that we’re at le ast starting with something that wasn’t made in a factory. “It feels truer to the 100 percent,” says Alison Mears at Parsons, because “it’s harder to use ‘biogenic’ as greenwashing.”
This primary school in Nykøbing Falster, Denmark, is laid out in an open ring—a nod to the ringlike fortresses of the Viking Age—creating a safe inner area for outdoor play and learning. However, the most striking aspect of this building designed by Henning Larsen has to be its thatched facade. Straw is a traditional building material in the area, explains the project’s lead design architect Per Ebbe Hansson. But the Sundby School is one of very few commercial buildings in the world to have a straw facade.
“Introducing this element in our design, we were able to reference local heritage and mirror the school’s surroundings, with the aim of uplifting both,” Hansson says. —Avinash Rajagopal
“When plant- or earthbased building materials are discussed in architectural discourse, there is often an inherent nostalgia for the traditional forms of building,” write the principals of New York–based firm LTL Architects in the introduction to Five Biogenic Houses (Princeton School of Architecture, 2023). The five houses they published, including the CLT A-Frame House (shown here), eschew such nostalgia, instead adding more proof of the enormous creative possibilities of biogenic materials that the authors first documented with 55 case studies in their previous publication Manual of Biogenic House Sections (ORO Editions, 2022). —A.R.
/bīō bāst/
One of the sexiest terms in architecture today, this word has launched federal grants, cool chemistry experiments, and a fascinating array of building materials composed—at least in part—of once-living things. Mycelium, bacteria, and any number of plants or proteins with a history of growing or respirating can anchor a biobased material. Examples include the “Bio-Blocks” engineered by Prometheus Materials that employ “microalgae along with other essential components” as an alternative to Portland cement, or Yale professor Mae-ling Lokko’s research into adhesives and acoustic paneling developed from the fiber of discarded coconut husks. Dissertation-worthy as they are, each of these material compositions raises more questions. If it works in a lab, what kinds of conditions will it require to work on a building site? How much energy is burned to make it? And what else is in it? In November 2023, a group called the Northeast Bio-Based Materials Collective held a summit in Boston to discuss such questions. Meanwhile, the U.S. Department of Agriculture is using its own definition of “biobased products” in its BioPreferred Program, which claims to “increase the use of renewable agricultural resources” with more than 3,000 companies as participants. The program allows different product types to call themselves “biobased” at different levels of natural components—carpets with seven percent biological content can get the label, while wallcoverings must attain at least 62 percent. Watch this space: The label is evolving fast.
Designed by Snøhetta, this luminaire has a body made of sugarcane-derived polylactic acid reinforced by hemp fibers. It has a global warming potential of 6.03 kgCO2e compared with 22.72 kgCO2e for the aluminum version. ateljelyktan.se
Two new lines of Biobased Xorel round out Carnegie’s Conscious Collection of sustainable fabrics. Both are not only USDA certified but also Cradle to Cradle Gold and Living Product Challenge certified. carnegiefabrics.com
The mind-boggling array of Wilsonart’s High Pressure Laminates—more than 300 in-stock designs with more available on demand—carries the USDA BioPreferred label because more than 70 percent of the laminates' content is biobased. wilsonart.com
Paul Crofts designed the Tejo sofa out of cork blocks—a by-product of the wine industry—topped by cushions of natural latex wrapped in wool wadding and then upholstered in flax or hemp fabric. isomi.com
PURLINE 1500 MATTER SURFACES
The bio-polyurethane flooring Purline is now available in 25 new roll colors. It is made predominantly from rapeseed or castor oil, and is Cradle to Cradle Silver certified while exceeding ASTM F925 standards. mattersurfaces.com
The Marmoleum Solid collection is made from 97 percent natural raw materials, including linseed oil, pine rosin, wood flour, calcium carbonate, recycled Marmoleum, jute, and titanium dioxide–and iron oxide–based pigments. forbo.com
/bīō
sōrst/
Here’s where we start confounding the word police: Many smart people are using “biobased” and “biosourced” interchangeably. One way into a more specific conversation is this trick: When you see the word “biosourced,” ask, “From where?” The answer will most likely be geographical and point you toward some sort of agricultural crop. “It has some overlap with ‘biobased,’ but we think of [‘biosourced’ as] something that’s derived from a renewable biological source,” says Parsons Healthy Materials Lab cofounder and design director Jonsara Ruth. “‘Renewable’ is the key term there.” Columbia’s Ben-Alon concurs. “‘Biosourced’ is a bit narrower, talking about materials chemically speaking in the polysaccharides group: starches and sugars, not proteins or fats.”
Translation: mostly plant-based. Pinpointing where a crop is cultivated opens the door to some other fertile areas of inquiry: fair labor practices and the carbon costs of transport.
These type II vinyl wallcoverings differ from others in their category in how the PVC itself is made. Rather than rely on fossil fuel–derived PVC resin and other plastics, 70 percent of Circon wallcoverings are biobased or bio-attributed. These source materials are wood-based feedstock (including wood chips and other timber by-products) from sustainable forestry, an “algaelike” base material, and a proprietary backing. The resultant wallcoverings meet the same performance standards as their conventional counterparts.
The idea, explains Momentum’s vice president of sustainability Julia Gillespie, is to provide a less fossil fuel–reliant option to specifiers who, owing to client preferences, project demands, or
simply their own comfort with familiar chemistries, continue to specify conventional PVC wallcoverings. For those who wish to go PVC free, the company has several lines of wallcoverings made of thermoplastic olefins (TPO) or cellulosepolyester blends.
The first Circon collection, launched this past June, consists of four patterns or textures—Zari, Miro, Miro Texture, and Loma (shown here). But Circon can also be specified for the hundreds of patterns in Momentum’s Versa and Digital Creations collections. All Circon products come with EPDs and HPDs and are Greenguard Gold certified. —A.R.
/bīōde grādeb(e)l/
Though this word may still be confusing for consumers, it’s one that most architects and designers have a decent handle on. We’re talking about how products break down at the end of their life cycles and what impact that decomposition has on ecosystems. There’s a time factor in play: For example, the EPA gives “biodegradable plastics” a one-year deadline for complete decomposition, and warns that just because a plastic is labeled biosourced and compostable does not mean it belongs in a backyard bin. Seemingly safe building products like bamboo, cork, or timber may have been covered in a chemical sealant or processed in a way that makes them more long-lasting and toxic wherever they land. And even if natural materials remain truly compostable, they won’t get to fulfill their regenerative potential and nourish soil unless there’s viable composting infrastructure in place. The University of Washington’s Kate Simonen, founding director of the Carbon Leadership Forum, has been focused recently on LCAs (life cycle assessments) and lowering the environmental impact of building materials. From an emissions perspective, Simonen would rather products stay out of the waste stream altogether. “Buildings are the closest thing we have to permanent storage,” she says.
BANBŪ
This leather alternative from Von Holzhausen is made mainly from bamboo, which, as one of the fastest-growing plants on earth, is considered rapidly renewable. But what makes Banbū truly noteworthy is that it biodegrades completely in landfills in less than 250 days.
The material consists of two parts—a backing that is fully made of bamboo yarn and a top coat that’s a mix of plant-based material and solvent-free polyurethane. It has a lambskinlike feel with
a low shine and is scratch-, stain-, and water-resistant, but is lighter than cow leather and, Von Holzhausen estimates, has a fifth of cow leather’s carbon emissions. Banbū comes in eight colors and is now available as an upholstery option for Herman Miller’s Eames Lounge Chair and Ottoman. A.R.
/bīō fi lik/
The most poetic word on the bio-list, this adjective describes an enduring, powerful, and instinctual love affair between humans and the natural world, our original habitat. It speaks to our innate, largely positive response to the sight of dappled sunlight or the surprising sensation of a breeze making its way to our desk through an operable window. Biophilic design attempts to maximize those encounters, and science has confirmed the health benefits, from faster healing rates in hospitals to better mental states in the workplace. But in the context of a natural materials discussion, there’s a twist. “Something can be biophilic and not healthy,” says Catie Ryan, an environmental design consultant at Terrapin Bright Green. “It might have a positive impact from looking at it, but if it’s doing other harm, that’s a whole other level. It doesn’t come up enough.” Imagine wall-towall carpeting in an open office with the elegant, abstract design of a kelp forest: lovely, but not if it’s off-gassing VOCs to everyone in the room. “There’s a lot of challenges, especially in interior design,” says Ryan. While the concept of biophilia has been well integrated (even in real estate ads) and standardized over the past quarter century, there’s a lot of work to be done in the development and sourcing of nontoxic, nonpolluting products in price ranges that designers and their clients will accept.
When the slick surface of our modern world starts showing cracks, another world—fecund, curvaceous, enchanting—bursts out into the open. At least that’s the message of Denver’s One River North, a newly completed mixed-use residential and retail project, built to inventive biophilic standards by MAD Architects, that has become an instant icon in the city.
The 16-story building’s meandering, whimsical standout is a “canyon” that breaks open the tower’s glassy exterior to reveal a living work of abstract art composed of landscaped terraces and water features. “To me, biophilic means a close relationship between humans and nature,” says Ma Yansong, MAD’s founder and principal partner. “We talk about this connection
because we live in a man-made world.” At every turn, the canyon, which provides a superb view of the surrounding Rocky Mountains, is meant to remind residents of nature—and how one moves through it. “On several floors, residents have access to public amenities like gyms, clubhouses, and swimming pools, all linked to these outdoor spaces,” Yansong says. —Drew Limsky
/bīō mimekrē/
Biomes shaped like bubbles. Pavilions shimmering like beetle wings. Earthen structures aiming for the thermal regulation of a termite mound. More a movement than simply an idea, biomimicry suggests observing nature’s patterns or processes and then adopting them, often quite literally, in design, engineering, and other problem-solving pursuits. It’s a broader concept than biophilia and was popularized with a 1997 book by Janine Benyus and resulting public television specials and TED Talks. The Biomimicry Institute, a nonprofit based in Montana, was founded in 2006. Its strategy today, according to CEO Amanda Sturgeon, is “bridging between ecological systems and species biology…with folks who don’t have any of that knowledge that are in the design space or social systems space.” Sturgeon says she’s seen more ecological literacy and “bio-inspired” designs in the building products space recently. The institute has an accelerator to fund ventures like ECOncrete, and its COASTALOCK product that mimics marine rocks and reefs. There’s no official standard for a biomimetic product, so let the designer beware: Even with “nature’s genius” as inspiration, it takes a human to ask critical questions about the material composition of these products. You don’t want to copy nature and harm it at the same time.
MOUNDS TERMITES
Little insects in Africa, Australia, and South America build complex structures with tunnels and vents atop their subterranean nests that architects and engineers have a lot to learn from. The mounds are self-cooling, circulate air more efficiently than most modern buildings, are engineered by thousands of termites working together, and are incredibly resilient—some of these earthen structures have been known to stand for up to a hundred years. —A.R.
Funded by architectural nonprofit re:arc institute, Latin and Central American practices are designing with water to create urban spaces for planetary well-being.
By Jaxson Stone
Earlier this year, architectural philanthropy platform and nonprofit re:arc institute hosted its annual symposium in Bogotá, Colombia. Titled arquitecturas de buen-vivir planetario, or Architecture of Planetary Well-being, the symposium was inspired by the Andean concept of “buen vivir,” which expresses a symbiotic existential relationship between nature and humanity. Pictured: Catalina Mejia Moreno, Gabriela Leandro Pereira, and Felipe Arturo present Pororoca: Abraz(ç) o de río e mar, a process-based curriculum funded by re:arc.
Región Austral is a multidisciplinary design firm working at the intersection of urban design, landscape architecture, and regional planning based in Córdoba, Argentina. It designs the city and the territory based on an interdisciplinary, multiscale dialogue, together with citizen participation processes and the strategic understanding of local communities, infrastructures, and ecosystems.
said Colombian environmentalist Josefina Klinger Zúñiga, during a day of dialogue at re:arc institute’s Architecture of Planetary Well-being symposium hosted in Bogotá, Colombia, at the beginning of this year. She continued: “If you want to learn about values, read the water. And if you want to learn about justice, go to the river.” Throughout the panel discussion aptly titled “From Poetry to Practice,” the ancient idea of listening to water submerged the audience—metaphorically and literally.
That day, I was invited to various moments of deep listening—through traditional dance and music, poetry, and thoughtful design presentations that highlighted the intersections of our social and ecological systems. Midway through the day, Catalina Mejia Moreno, senior lecturer in climate studies and spatial practices at Central Saint Martins, took the stage with her collaborators Felipe Arturo and Gabriela Leandro Pereira to lead the audience through an experiential interlude titled Pororoca: Abraz(ç)o de río e mar, or “I embrace the river and the sea.”
Their research began in Salvador de Bahia, where Moreno, Arturo, and Pereira learned about the resistance struggles of Brazil’s Baiana communities that are sustained in relation to their waters. Arturo continued, “We visited lagoons, ancestral fountains, and quilombos, sandbanks, dunes, seawalls, and coastal neighborhoods destroyed by modernization and urbanization processes but rebuilt by collective networks.”
Over the course of about 30 minutes, the researchers spoke practically and poetically while viscous projections of the Paraguay River covered the walls of the room. At one point, the trio took out a massive roll of black-and-white fabric, digitally printed with the texture of the ocean. Passing it over our heads, across rows and rows of seats, it eventually reached the back wall. The image of the sea washed over us, symbolically immersing us in its powerful waters. Arturo instructed us: “At some point scissors will appear. We hope you will cut some fragments and pieces of this fabric—
scarves, ponchos, handkerchiefs to wipe your tears, curtains, as you wish—but we invite you above all to listen.”
The Pororoca interlude perhaps left us with more questions than answers. Where does the river end? Where does the ocean begin? “What is the space that these waters share—is it a region? An edge? Two molecular bodies in collision?” Arturo asked.
When we design with water, we forgo clear borders, as we do the other constraints of land. In its 2019 report “Ocean Energy Landscapes: Energy Infrastructures Towards Greater Local Sovereignty in Patagonia, Argentina,” re:arc institute Practice Lab grantee Región Austral writes: “It is imperative to think of the sea as an opportunity, a site from which the nation can reimagine a future sustainable relationship with its coasts and territory, leaving behind the current continental and introspective view.” During its symposium presentation, Región Austral showed the audience how its work integrates research, practice, policy, and implementation.
Re:arc’s funding will help Región Austral to design and build public spaces and community infrastructure for Buenos Aires’s Playón de Chacarita community. As one of over 2,000 informal settlements within the metropolitan region of Buenos Aires, Chacarita “typifies the challenges faced by informal settlements in Latin America.” When the city government started an integration process for
ECOLOGICAL DESIGN: STRATEGIES FOR THE VULNERABLE CITY
In the 2022 report coauthored by Región Austral, the firm explores vulnerability in urban spaces. In it, they present urban and national policies, strategies, and case studies to enhance public space in the most vulnerable urban areas of Latin America and the Caribbean, through green infrastructure. The 30 projects presented in the report illustrate the diverse biogeographic regions of Latin America, as well as the distinct context and environmental conditions of each.
Funded by re:arc, Región Austral’s Playon Network project introduces public spaces and community infrastructure to Playón de Chacarita, an informal settlement near Buenos Aires. Through participatory workshops, the firm worked with residents to shape four programs: an open agora (top), a community center, the Guevara Garden (middle), and a sports court (bottom). Together, the initiatives create a network of green infrastructures essential for community safety and well-being.
Office of Urban Resilience, or Oficina de Resiliencia Urbana (ORU), is an urban and landscape design office with a mission to shape the future of people and ecosystems on earth. ORU was awarded a re:arc Practice Lab grant to develop their project, The San Felipe Water Intelligence Hub. This project will play a vital role in preserving the ecosystem and habitat of the upper Río San Felipe basin through monitoring and education programs.
the neighborhood in 2017, it left a lot in terms of vacant space and little in terms of green infrastructure.
To fill this gap, Región Austral conducted participatory workshops, interviews, and discussions around four topics—culture, environment, economy, and health—with more than 70 residents. Alongside various governmental agencies as well as local NGOs and cooperatives, community members were able to actively shape the design and construction of the project that includes an open agora, a sports court, a community center, and the Guevara Garden, which serves as both a pocket park and a rain garden. “The idea is to introduce vegetation that consumes very little water as well as fruit trees to mitigate flooding during the rainy season,” Región Austral cofounder Soledad Patiño explained. “We believe that although small, these interventions will contribute to reduce
the urban heat focus and improve environmental comfort.”
“Vulnerability” was a critical idea discussed throughout most of the day’s presentations. When it was time for the Office of Urban Resilience (ORU) to present, they began with a sobering quote from the World Meteorological Organization: “Latin America and the Caribbean is one of the world regions where climate change effects and impacts such as heat waves, decreases in crop yield, wildfires, coral reef depletion, and extreme sea level events are projected to be more intense.”
The following slides detailed how ORU approaches design within Latin America and what they call “a megadiverse environment.” While the 33 countries of Latin America and the Caribbean
ORU aims to address some of these concerns with its re:arc-funded San Felipe Water Intelligence Hub, located on the outskirts of Oaxaca in San Felipe del Agua. The space is intended to be a hub for innovation, conservation, and heritage and will help play a vital role in preserving the ecosystem and habitat of the upper Río San Felipe basin through monitoring and education programs. “Our vision involves an ecotourism model that offers hiking and ORU
may share borders and waterways, they each face their own unique challenges— socially, politically, and environmentally. Mexico, for example, faces significant water scarcity, especially in its northern regions, where the landscape is further affected by global warming and the over-extraction of groundwater. Aging and inefficient water infrastructure exacerbates the water loss, with estimates suggesting that up to 40 percent of treated water is lost through leaks.
Taller Capital is a Mexico City–based architecture and urban design studio founded in 2010 by José Pablo Ambrosi and Loreta Castro-Reguera. Their work focuses on “designing the city through densification and infrastructural public spaces.” With a particular attention to water, the studio has applied extensive research to the development of urban design projects that address water management in Mexico City and beyond. Their project Pooling Xolox will integrate community spaces with essential water management in the Valley of Mexico.
bird-watching activities, thus establishing a new destination and creating economic development opportunities for the community,” the studio explained.
At the heart of ORU’s work is a desire to change the current management of water “from a linear model of water extraction to a decentralized and circular model, treating urban water as a resource and not as a waste.”
José Pablo Ambrosi and Loreta CastroReguera of Mexico City–based Taller Capital are grappling with similar water management concerns.
Founded in 2010, Taller Capital focuses on urban interventions that prioritize densification and infrastructural public spaces. “We design infrastructural public spaces to fix the broken city,” Castro-Reguera explained in a video presentation on their Practice Lab project titled Pooling Xolox, which transforms the historic pre-Hispanic town of San Lucas Xolox.
ALBERTO KRITZLER
Alberto Kritzler is a Mexican developer interested in adaptive reuse, urban density, and living systems. He believes urban development should produce positive environmental, social, and local economic impact. In 2010 Kritzler cofounded Reurbano, a Mexico City–based adaptive reuse development platform, and last year he was the recipient of a Loeb Fellowship from the Harvard University Graduate School of Design for his research on water scarcity and regenerative design in Mexico.
The former village was once located near the former lake of Texcoco, in the Basin of Mexico. “Through re:arc’s practice-based funding initiative, we reconnected with the local community. Specifically, the group of Ejidatarios, which own the land and have jurisprudence over it,” Castro-Reguera noted. “Previously, water runoff from the mountain went into the lake, but the construction of the new airport desiccated the lake, causing floods.”
Taller Capital invited the local potable water system that manages drinking water, irrigation, and sanitation to collaborate on the project. Together, they worked to mitigate the flooding and address runoff management concerns caused by the new airport, reusing the water for agricultural irrigation while introducing a communal area for recreational and cultural purposes. Rather than piping rainwater that runs from the mountain, they contain and redistribute the runoff. Because water piping is “an expensive and unsustainable measurement,” they created soft infrastructure
and community space that serves as an “ecosocial catalyst” and “recovers water culture” in the town. Taller Capital believes Xolox can set an example on how to integrate public life and water management in the Valley of Mexico.
I left Bogotá feeling hopeful in the face of oftentimes-hopeless climate discourse and grateful that emerging nonprofits such as re:arc are dedicating themselves to supporting the designers and grassroots initiatives working at the intersection of architecture and climate. My experience proved to me that by designing with, not against, water systems, architects and urban planners can create equitable, sustainable public spaces that promote both personal and planetary well-being. As Zúñiga asked at the beginning of the day’s events, “What happens when people begin to speak the languages of the mangroves, the waves, the tides?” We may be learning the language, but let’s not forget to listen. M
What inspired your research as a 2023 Loeb Fellow?
Growing up in Mexico City, I experienced a city always on the edge of collapse where everyone experienced a common disaster: an aggressive urbanization process of mindless overdevelopment. My experience led me to believe that the way we currently live is unsustainable. From this perspective I sought to reframe business models that are usually based on exploiting land and people. My work aims to reverse the destructive power of mindless overdevelopment by creating business models built across scales in urban and rural Mexico. My research focused on the intersection of urbanization processes and sustainable design at a territorial scale from a systems approach. That is where water and its infrastructure come into play.
Why is water such an urgent concern, especially in Mexico?
Mexico’s constitution enshrines the right to water, yet Mexico is the No. 1 bottled-water per capita consumer in the world. Our capital city was built on a lake by draining it, yet we built a system to bring water from 138 miles away (losing around 40 percent along the way). In 2024, nearly 76 percent of the country was experiencing drought. In addition to this, the distribution of water is deeply inequitable. According to a 2024 study conducted by the Universidad Iberoamericana, a little over 77 percent of the population in Mexico City does not have access to enough potable water to maintain a healthy life in accordance with WHO standards. The urgent question is, how do we adapt our cities and infrastructure to sustain life under these extreme conditions?
Discover the people, manufacturers, and suppliers behind the projects featured in the Winter 2024 issue of METROPOLIS.
EMIT
(“EMIT’s HQ Turns a Kmart into a Landmark,” p. 70)
• Client: EMIT
• Design architect: CLB Architects
• Architect of record: CLB Architects
• Interiors: EMIT with CLB Architects
• AVI consultant (audiovisuals/data/ information): BG Building Works
• Engineering: Nelson Engineering, KL&A Inc., BG Building Works
• Landscaping: CLB Architects
• Lighting: Lux Populi
INTERIORS
• Bath fittings: Kohler, Blanco, Sloan, Toto
• Ceilings: exposed acoustical metal deck painted white, Armstrong Acoustic Panels
• Flooring: Cast in place concretes, integral color and polished finish Kitchen cabinets: Birch veneer millwork
• Kitchen surfaces: Custom concrete counters and sinks
EXTERIORS
• Cladding/facade systems: Custom hot rolled steel paneling
• Doors: Tubelite
Windows: Tubelite
• Other: Hot rolled custom perforated louver screen
BUILDING SYSTEMS
• HVAC: Carrier
• Structural (steel/mass timber/concrete/ etc.): Steel
PORTLAND INTERNATIONAL AIRPORT (PDX) MAIN TERMINAL EXPANSION (“PDX Is More Than a Mass Timber Marvel,” p. 106)
• Client: Port of Portland
• Architect of record: ZGF
• Interior designer: ZGF
• General contractor: Hoffman Skanska Joint Venture
• Pre-construction services: Turner Construction Company
AQUATIC AND COMMUNITY CENTRE
(“The təməseẃtxw Aquatic and Community Centre Reflects Local Values,” p. 78)
• Client: City of New Westminster
• Design architect, architect of record, interiors: hcma architecture + design
• AVI consultant (audiovisuals/data/ information): MC2
• Engineering: Fast + Epp, AME Group, AES, Aplin & Martin, RWDI
• Landscaping: PFS Studio
• Lighting: AES Engineering
• Public art: James Harry
• Project manager: Turnbull Construction Project Managers
• Construction manager: Heatherbrae Builders
INTERIORS
• Flooring: Forbo, Daltile, Cascadia, NorthWest Rubber, Shaw Contract, DL Watts
• Lighting: Lumenpulse, Meteor, Mark
• Lockers: Bradley
Sports equipment: Cascadia, Daktronics, Draper
• Ticketing/admission: Gunnebo Turnstiles
EXTERIORS
• Cladding/facade systems: APS
Precast, Parker Johnson, Schlebach Standing Seam
Doors: Access SMT, Tormax, Nana Wall, Diamond Doors
• Lighting: Lumenpulse, Meteor, Mark
BUILDING SYSTEMS
• Air ventilation systems: Trane, Klimor, Greenheck, E.H. Price, Reversomatic, Big Ass Fans
• Structural engineers: KPFF Consulting Engineers (primary), Arup
• Mechanical/electrical/plumbing: PAE Engineers (primary), Arup
• Geotechnical engineers: GRI
• Civil engineer and airside planning: HNTB
CONSULTANTS
• Mass timber trade partner: Swinerton Mass
• Steel trade partner: W&W AFCO Steel Mass timber fabricators/manufacturers: Zip-O-Laminators, Timberlab, Freres Engineered Wood, Calvert
• Mass timber manufacturers: Calvert, Freres Engineered Wood, Zip-O-Laminators
• Wood adviser: Sustainable Northwest and Sustainable Northwest Wood Lumber mills: Elk Creek Forest Products, Frank Lumber Co., Freres Lumber Co., Herbert Lumber Co., Kasters Kustom Cutting Inc., Manke Lumber Company, Zip-O-Log Mills
• Aviation planning: Arup USA
• Landscape: PLACE Landscape Architecture
Biophilic design consultant: Terrapin Bright Green
• Sustainability consultants: ZGF (lead consultant), Arup
• Building envelope: Professional Roof Consultants Inc., RDH Building Science Inc.
• Air and wind analysis: RWDI Consulting Engineers and Scientists
• Erector: Derr and Gruenewald Construction
• Heavy lift/transport: Mammoet
Glulam connections: Madlyn Metal Fab
• Y-column fabrication: Thompson Metal Fab
• Curtain wall: Benson
• Roofer: Snyder
• Lighting design: Fisher Marantz Stone
• Fire protection: Cosco Fire Protection Inc.
• Electrical: Oregon Electric Group
• Plumbing: Harder Mechanical Contractors
• Acoustics and public address: Arup
• Cost estimating: Rider Levett Bucknall (RLB)
HVAC: Arctic Sheet Metal
• Architectural metals: McKinstry Co., LLC
• Expansion joints: Performance Contracting Inc.
INTERIORS
• Acoustical ceilings: Armstrong World Industries
Dimming system or other lighting controls: ETC Inc.
• Downlights: Acuity Custom Architectural Lighting, Flos, Meteor
• Interior ambient lighting: Acuity Custom Architectural Lighting
• Paints and stains: Timber Pro
• Special interior finishes unique to this project: Interior sunshades by Levolux
• Wood flooring: Zena Forest Products
EXTERIORS
• Built-up roofing: Siplast
• Curtain wall: Benson l, Arcadia
• Glass: Carey Glass with Glas Trösch, Viracon
• Lighting: Musco Lighting
• Metal panels: Morin Corp.
• EIFS, ACM, or other: Custom Metal Cladding Ltd.
• Moisture barrier: Henry Co.
• Skylights: DeaMor
• Other cladding unique to this project: Expansion joints by MM Systems, Sunshades by McKinstry
• Other roofing: Seismic Isolators by Maurer SE
FORESTS OF ORIGIN/WOOD HARVEST SITES
Camp Adams Youth Camp, Camp Bishop Grays Harbor YMCA, Camp Namanu, Chimacum County Park, The Nature Conservancy Central Cascades Forest, Coquille Indian Tribe, Hanschu Family Forest, Hyla Woods, Joint Base Lewis-McChord, Roslyn Urban Forest, Skokomish Indian Tribe, Willamette
University Educational Forests, Yakama Nation
With hundreds of style and color combinations available, Tarkett’s ethos® modular carpet tile is a testament to good, responsible design. This Cradle to Cradle Certified® Silver backing contains up to 79% recycled content and can be turned into new tile backing at its end of life through Tarkett’s Restart® take-back and recycling program. commercial.tarkett.com
Learn more about the topics you’re interested in as you explore the Winter 2024 issue of METROPOLIS.
ADAPTIVE REUSE
32 METROPOLIS Hosts Circular Future Hackathon
70 EMIT’s HQ Turns a Kmart into a Landmark
AFFORDABILITY
68 Modular Construction Provides a Solution to the Netherlands’ Housing Crisis
BIODIVERSITY
134 Listening to Water
BIOPHILIA
46 Architectural Lighting Continues to Astonish
106 PDX Is More Than a Mass Timber Marvel
124 Help! We’re Drowning in Bio-Lingo
CIRCULARITY IN PRODUCTS
32 METROPOLIS Hosts Circular Future Hackathon
38 Flooring That Looks Good and Works Hard
54 This Company Turns Paper Back into Wood
60 Carlo Ratti Calls for a Circular Architecture Biennale
CLIMATE ADAPTATION
118 Will the New Version of LEED Be Better?
134 Listening to Water
EMBODIED CARBON
34 Sustainability News Updates for Q4 2024
78
HQ Turns a Kmart into a Landmark
78 The təməseẃtxw Aquatic and Community Centre Reflects Local Values
106 PDX Is More Than a Mass Timber Marvel
118 Will the New Version of LEED Be Better?
EQUITY AND ACCESS
118 Will the New Version of LEED Be Better?
ESG
118 Will the New Version of LEED Be Better?
HEALTHY MATERIALS
46 Architectural Lighting Continues to Astonish
106 PDX Is More Than a Mass Timber Marvel
NET ZERO AND NET POSITIVE
78 The təməseẃtxw Aquatic and Community Centre Reflects Local Values
REGENERATIVE DESIGN
32 METROPOLIS Hosts Circular Future Hackathon
60 Carlo Ratti Calls for a Circular Architecture Biennale
RESPONSIBLE RENOVATION
32 METROPOLIS Hosts Circular Future Hackathon
WATER
134 Listening to Water
ARTIFICIAL INTELLIGENCE
52 Monograph and Naya Are Transforming Architecture and Design Workflows
BIOBASED MATERIALS
54 This Company Turns Paper Back into Wood
124 Help! We’re Drowning in Bio-Lingo
CALCULATORS, SOFTWARE, AND PLUG-INS
52 Monograph and Naya Are Transforming Architecture and Design Workflows
CONSTRUCTION MATERIALS
34 Sustainability News Updates for Q4 2024
68 Modular Construction Provides a Solution to the Netherlands’ Housing Crisis
PLASTICS
124 Help! We’re Drowning in Bio-Lingo
PREFABRICATION AND AUTOMATION
68 Modular Construction Provides a Solution to the Netherlands’ Housing Crisis
SPACE works everywhere. And for every student. SPACE cuts clutter. Extends resources. Enhances student agency. Invites collaboration. And stores 40% more than casework. What you need. Where and when you need it. See it in motion at vsamerica.com/space