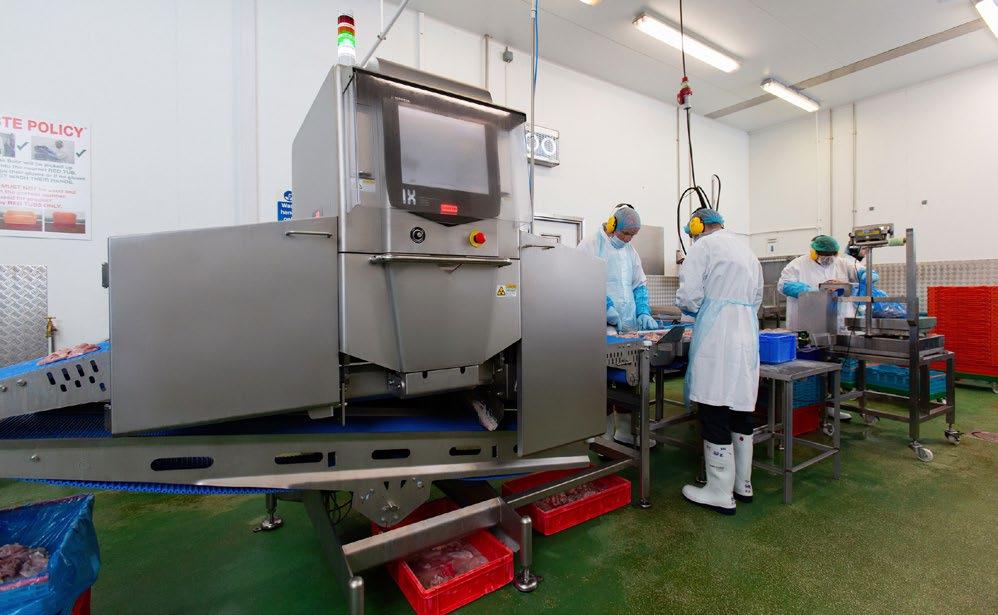
20 minute read
ISHIDA
Ishida x-ray machines are part of the family at Smithfield Murray
With a commitment to maintaining the highest standards of food quality, poultry processing specialist Smithfield Murray has installed two IX-G2 X-ray poultry solutions from Ishida Europe to detect and remove bone and cartilage from its products.
As one of Europe’s leading suppliers of prepared fresh and frozen poultry, Smithfield Murray handles around 250 tonnes of meat each week, which is ultimately supplied to major retailers and food service companies including the UK’s leading supermarkets.
The dedicated Ishida X-ray inspection systems for poultry were installed in 2021 at Smithfield Murray’s BRC Grade AA purpose-built plant in King’s Park, Manchester. The investment in X-ray inspection technology supports the company’s drive to be, as Managing Director Damien Murray explained, “the best in the world at what we do.” The two Ishida IX-G2 models use advanced dual energy technology which incorporates two-line sensors, one which takes images at high energy and one at low energy. These are then compared, which provides a better overall image of the product with a clearer contrast between the product and any lowdensity foreign bodies, such as bone fragments. Should any foreign body be identified, it is rejected and returned for re-trimming. of the poultry industry where the density of the product and the potential contamination can be very similar, for example the bone and meat of a chicken which have almost the same density. Removal of low-density foreign bodies, such as bone and cartilage, is essential as the majority of poultry products need to be supplied boneless for use in recipes such as ready meals, children’s meals, deli products, pies and pastries.
“Consumer expectation is that meat is boneless, but due to the relatively young age of many chickens at slaughter, their bone development isn’t at full density. This can leave cartilage or soft bone fragments in the meat, which we need to remove before supplying product to our customers,” explained Smithfield Murray’s Operational Production Manager, Pawel Charazmusiewicz.
check’. Previously, Smithfield Murray’s foreign body inspection process was manual, with an initial check during trimming and a more thorough search further down the line. This was not only time-consuming but exposed the meat to several stages of manual handling.
Smithfield Murray knew there was a better way of doing things but they needed a solution that would fit the compact footprint at its Manchester site. “While the overriding decision was based on machine capabilities and performance, space was a big issue,” said David Hrubos, Operational Technical Manager.
The answer came via one of the company’s industry peers, which was already using the Ishida IX-G2. Following a site visit, it was clear that Ishida offered the right combination of quality and design to suit Smithfield Murray’s set-up.
“Our view is there’s no downside to sharing best practice in the industry. If it makes better product and improves standards for everybody, there’s a responsibility to look out for each other,” confirmed David Hrubos.
This honest, friendly attitude to business is matched by Smithfield Murray’s commitment as a whole towards its employees. “We’re a work family – and often, a literal one, too,” said Damien Murray. “We have plenty of husbands and wives, or fathers and sons, working together in the factory.
“This has been particularly true since COVID-19, when we stopped using agency staff and realised that morale, dedication, and quality improved because our permanent staff really take pride in what they do.
“This has a bearing on the Ishida machines, because it’s important that anything we invest in is well maintained and cared for. David and Pawel led a very close-knit team running them, who take real ownership and responsibility for the X-ray machines. You might say the Ishida machines have become part of the family!” The IX-G2 offers a cost effective, compact solution for poultry producers, who need high accuracy in detecting low-density bone, bone fragments and cartilage. To match the high speeds of poultry processing, the IX-G2 models used at Smithfield Murray are the dual lane variant, giving throughputs well in excess of 100 fillets per lane.

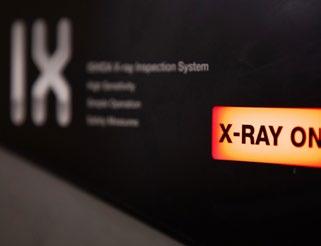
The first Ishida X-ray poultry solution was installed in March 2021 in the primary preparation area, where (for example) chicken is trimmed in readiness for use in children’s meals. This environment was ideal for training and calibration, with Ishida supporting Smithfield Murray to achieve the perfect balance for each application.
Once calibration was complete, the second IX-G2 formed part of a new “Opti“ line, which was configured with the anticipation of an X-ray machine being included. Therefore, installation had to be plug-and-play, a swift and efficient process that took place in June 2021. practice for positioning chicken products as they enter the IX-G2. Smithfield Murray’s engineering team created a unique and practical solution by adding prominent markers onto the conveyor so that employees know exactly where to place the poultry.
Since installation, both X-ray inspection systems have been running daily and their advantages continue to reveal themselves.
“Most importantly, it’s about quality of product and a key part is improving food safety. By adding the IX-G2s to our operation, we can deliver 300% inspection – trim, machine check, visual recheck – and our customers are delighted,” confirmed Pawel Charazmusiewicz.
“X-ray inspection means less manual handling, quicker feed and improved productivity. The team has quickly adapted to using the machines and we’re added training in X-ray technology as part of our standard induction,” added David Hrubos.
For Damien Murray, the investment has been money well spent. “I wouldn’t hesitate to recommend Ishida to other companies in our sector. The value their X-ray machines are adding to our operation has been significant, and they’ve been a joy to work with.”

The Humble Cam Follower
Cam Followers are often overlooked as an essential part of many modern machinery designs. With a vast array of different designs, construction methods, and materials available, this simple product can have a lasting impact on the overall efficiency and durability of whatever Food and Beverage application it’s used in.
IKO UK and Ireland’s team of Technical Sales Engineers are regularly presented with a variety of application requirements, and are often called upon to assess existing or potential issues, using their knowledge and past experiences to suggest alternative solutions.
The Food and Beverage industry is the UK’s largest manufacturing sector, contributing more to the economy than all other manufacturing sectors combined, including automotive and aerospace. With such a vast array of food and drink manufacturing businesses all striving for the highest possible standards, it’s not surprising that IKO’s products are already specified and used widely throughout the sector. IKO UK and Ireland have helped many manufacturers overcome issues whether it be to increase their production, reduce their downtime, or reduce their maintenance costs.
One relatively recent example of this was when the company had been contacted by a UK Can Manufacturing facility that had been experiencing regular failures on the line with the previous guide bearings used. In an added complication, the facility had grown over time and had been using several machines manufactured by various companies across the globe prompting a requirement for both metric and imperial sizes to suit different applications. This, however, proved not to be a problem.

The maintenance team at the Can Manufacturing facility needed to close the line monthly due to the current bearing arrangements regularly collapsing without warning. The maintenance schedule (although predicted and planned to reduce overall impact) continued to have an impact on loss of production and the situation got to a point where it needed to be addressed.
IKO collected some of the failed bearings for inspection and issued a free detailed report to the customer
giving their professional opinion on the root cause of the failure. Following subsequent inspection it became apparent that the washdown procedure used to clean the lines was itself washing away the bearing lubrication, causing excessive corrosion to the rolling elements. This inevitably led to the collapse of the cage and ultimately resulted in seizure and bearing collapse.
To resolve these issues IKO suggested the customer use a combination of their maintenance-free integrated C-Lube technology, their centrally lubricated Cam Followers, and in some areas, their external C-Lube unit to which is used to lubricate the rolling surface itself. The IKO C-Lube maintenance-free lubrication system incorporates the use of NSF H1 certified lubrication oil and an FDA compliant resin, whereby the resin deposits a small amount of lubricant onto any dry contact surfaces via a capillary action. This ensures the bearing is never over lubricated, and the requirement for a regular or ad-hoc regreasing regime is removed.
The centrally lubricated units allowed the use of automated lubrication feed systems to apply sufficient food safe grease to the internal rolling elements.
With these changes implemented, planned maintenance was reduced and was subsequently incorporated into the annual facility shutdown regime. Thus, not only did IKO drastically reduce the maintenance costs but increased production rates and improved production volumes soon followed.
As you can see, ‘The Humble Cam Follower’ is not something to be overlooked, and like all IKO products they are designed and manufactured to the highest possible standards. These seemingly inconspicuous products can have a huge effect on improving reliability, durability, and profitability, and it pays to get the experts in to help.
IKO UK and Ireland have the knowledge and expertise to help and advise on the best possible solution for your application, and alongside their wide range of Cam Followers, they also produce an extensive range of other high precision needle, linear motion, and mechatronic products.
Whether you need a site visit, a Teams or Zoom meeting, or a consultation over the phone or via email, the company is happy to help whenever they can.
Tel: 01908 566144 or email: enquiries@iko.co.uk www.ikont.eu/en
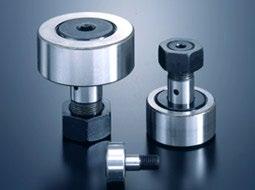
IKO Sales Points! #1 10 Product Features
Sales Points !
Please see Interchange Table (Attached)
for comparing to competitors’ products.
We have a Variety of Products with over 1,000 identification numbers for standard products!
High carbon Steel Stainless steel With cage Full compliment Shield sealed Cylindrical Crowned
General Purpose Inch Series
Saving Space
Point! #1
Eccentric Type Easy Mounting
IKO Original Products
Cam followers suitable for the intended use can be selected by specifying the identification number only.
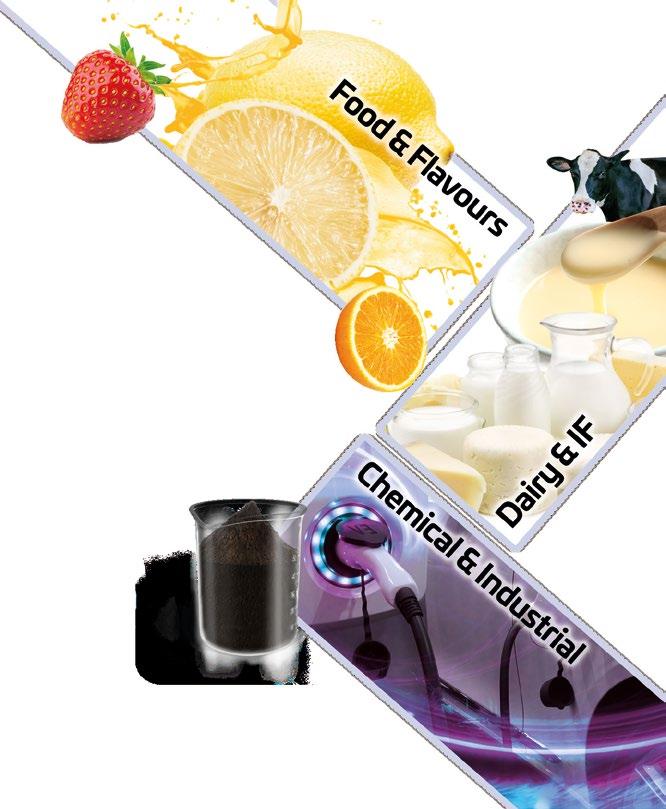

EUROPEAN SPRAYDRY EUROPEAN SPRAYDRY TECHNOLOGIES TECHNOLOGIES
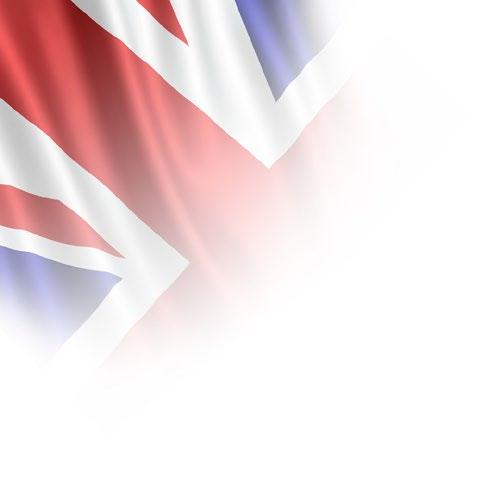
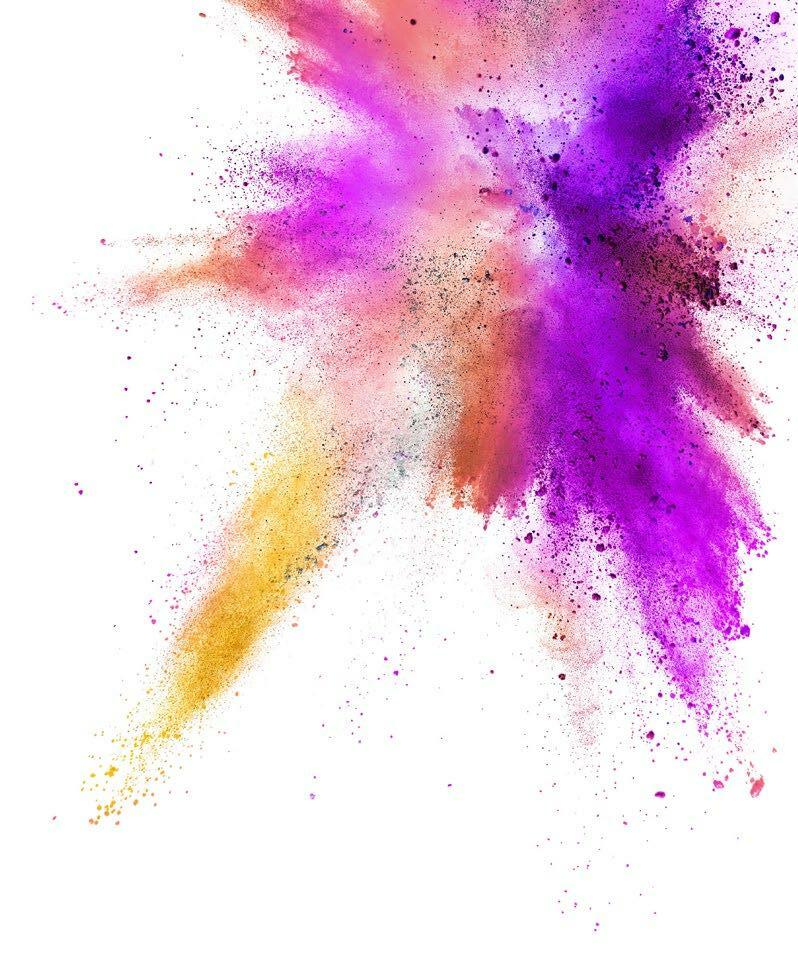
ESDT are the UK’s premier suppliers of ESDT are the UK’s premier suppliers of spray drying systems with an extensive spray drying systems with an extensive range of process plant and equipment for range of process plant and equipment for powder production. powder production.
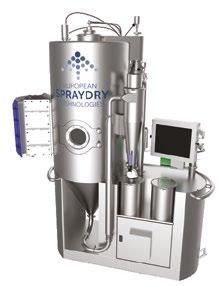
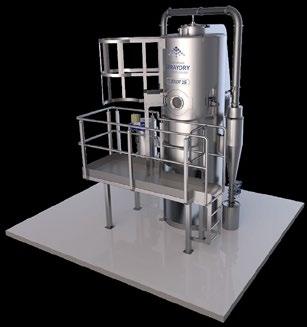
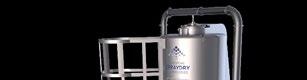
Our dedicated team of process engineers and chemists can turn our customer’s ideas into the reality of fully functioning process plants, which deliver the highest quality custom engineered powders. We are committed to the design and supply of high performance, safe and simple to operate systems and equipment which are subject to continuous review and development. ESDT process solutions are designed, where possible, to allow future upgrading to enable our customers to take advantage of new technology as it becomes available. Main product lines include both wet and dry process solutions incorporating liquid feed preparation, evaporation, spray drying, fluid bed drying, cooling, agglomeration, powder separation, powder conveying and powder storage solutions. With a legacy spanning over four decades, ESDT supply equipment which is technologically advanced, aesthetically pleasing and of the highest industry quality standards.
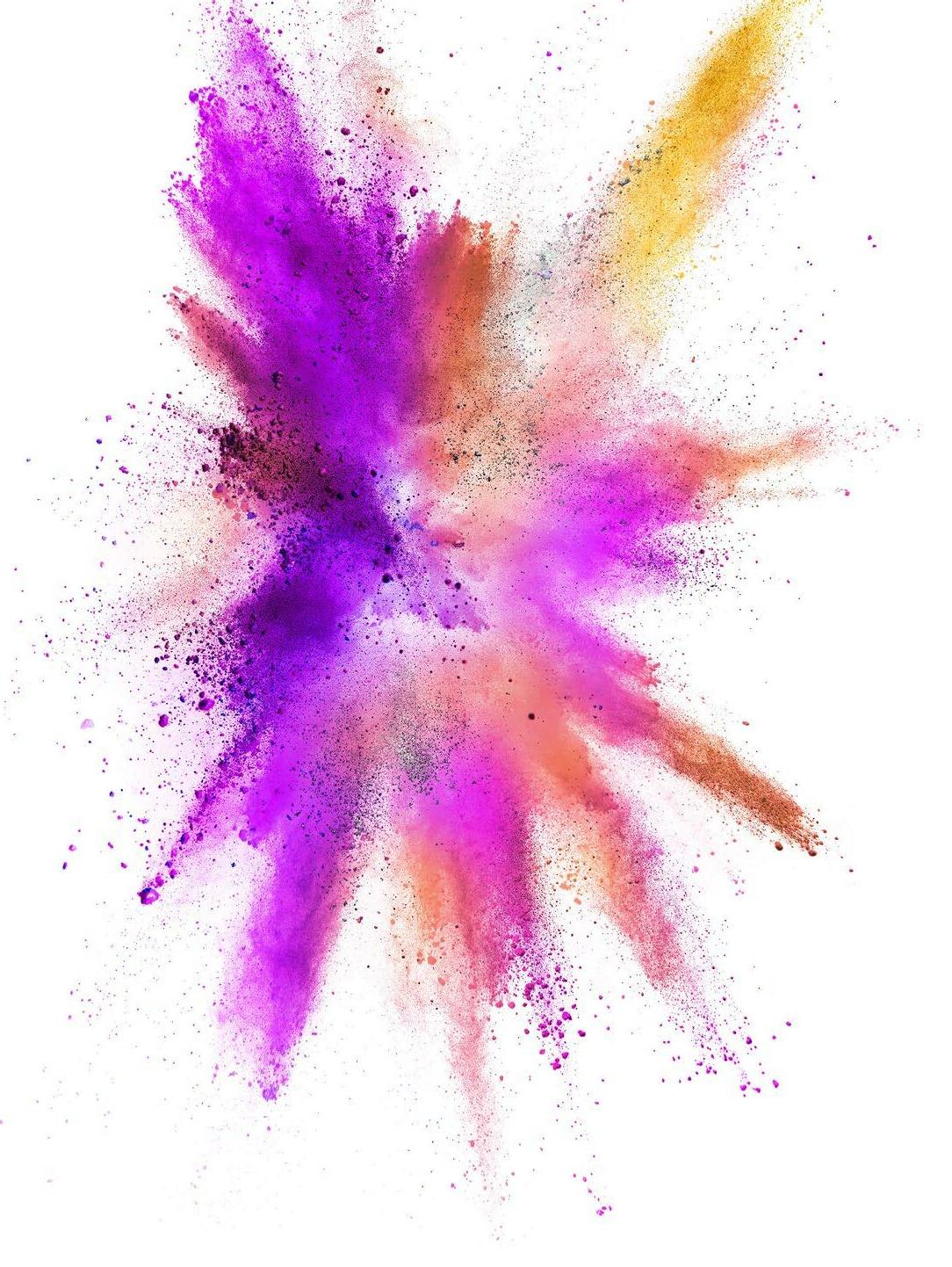
Our dedicated team of process engineers and chemists Our experienced can turn our customer’s ideas into the reality of fully project delivery team functioning process plants, which deliver the highest provide a professional service quality custom engineered powders. to our customers which includes We are committed to the design and supply of high performance, safe and simple to operate systems and equipment which are subject to continuous review and sales, design, project management, installation supervision, operator training and commissioning. development. ESDT’s highly skilled production and fabrication ESDT process solutions are designed, where possible, to allow future upgrading to enable our customers to take advantage of new technology as it becomes available. department oversees the manufacture of all ESDT equipment from stainless steel and other specialist materials. Main product lines include both wet and dry process solutions incorporating liquid feed preparation, evaporation, spray drying, fluid bed drying, cooling, agglomeration, powder separation, powder conveying Having approved fabrication facilities in the UK, Mainland Europe, USA, Middle East and Oceania, ESDT are well positioned to service our customers requirements throughout the world. and powder storage solutions. With a global clientele, our plant and machinery is With a legacy spanning over four decades, ESDT supply equipment which is technologically advanced, aesthetically pleasing and of the highest industry quality standards. designed to be fully compliant with both regional and industry specific standards in order to satisfy production requirements in all market sectors including chemical, food, dairy and pharmaceutical applications.
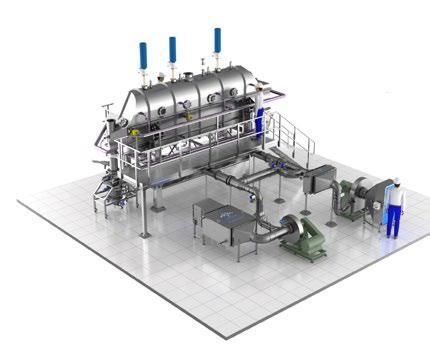
Our experienced project delivery team provide a professional service to our customers which includes sales, design, project management, installation supervision, operator training and commissioning. ESDT’s highly skilled production and fabrication department oversees the manufacture of all ESDT equipment from stainless steel and other specialist materials. Having approved fabrication facilities in the UK, Mainland Europe, USA, Middle East and Oceania, ESDT are well positioned to service our customers requirements throughout the world. With a global clientele, our plant and machinery is designed to be fully compliant with both regional and industry specific standards in order to satisfy production requirements in all market sectors including chemical, food, dairy and pharmaceutical applications.
Today’s material development for Today’s material development for tomorrow’s products. tomorrow’s products.
For more information on ESDT systems and For more information on ESDT systems and equipment, please visit: www.spray-dryer.comequipment, please visit: www.spray-dryer.com or contact: sales@spray-dryer.comor contact: sales@spray-dryer.com
Products From Stainless Steel Products From Stainless Steel Manufacturing & Equipment Ltd. Manufacturing & Equipment Ltd.
MANUAL BOOT WASHER MANUAL BOOT WASHER
Manual boot wash stations, like the ones we supply at Stainless Steel Manufacturing & Equipment, are great for small to mediumsized processing areas and plants. Our manual boot washer can be used for all types of footwear worn in production areas and is often used on entry and exit to prevent employees from walking debris into changing rooms and corridors. Available in 1-4 stations, the manual boot washer comes with a high-density nylon base brush for scrubbing the soles of shoes and includes a convenient, water-fed, handheld boot brush that enables you to clean the top and sides of your boots and shoes.
Manual boot wash stations, like the ones we How to use the Manual Boot Washer: supply at Stainless Steel Manufacturing & To activate the manual boot washer, you Equipment, are great for small to medium- simply place your foot on the base brushes sized processing areas and plants. within the trough, which actuates a valve mounted on the underside of the boot Our manual boot washer can be used for all washer. Water the flows through the hose types of footwear worn in production areas brush and enables you to effectively clean and is often used on entry and exit to prevent the boot from all angles– ensuring all dirt is employees from walking debris into changing removed. rooms and corridors. Investing in a manual boot wash station Available in 1-4 stations, the manual boot will ensure your employees perform the washer comes with a high-density nylon base necessary washing and disinfecting steps brush for scrubbing the soles of shoes and required for hygiene regulations. includes a convenient, water-fed, handheld boot brush that enables you to clean the top and sides of your boots and shoes.
How to use the Manual Boot Washer:
To activate the manual boot washer, you simply place your foot on the base brushes within the trough, which actuates a valve mounted on the underside of the boot washer. Water the flows through the hose brush and enables you to effectively clean the boot from all angles– ensuring all dirt is removed. Investing in a manual boot wash station will ensure your employees perform the necessary washing and disinfecting steps required for hygiene regulations.
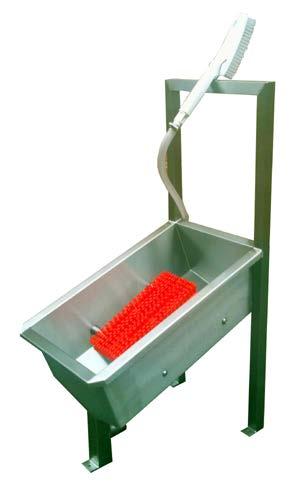
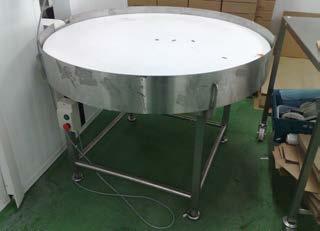
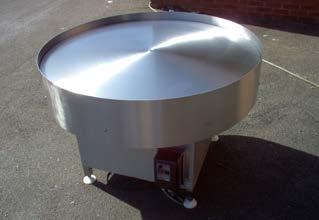
STAINLESS STEEL LAZY SUZY ROTARY TURNTABLE STAINLESS STEEL LAZY SUZY ROTARY TURNTABLE
We supply the Lazy Susan Turntable, We supply the Lazy Susan Turntable, which is a Stainless Steel Turntable, to which is a Stainless Steel Turntable, to meet and exceed the requirements of all meet and exceed the requirements of all industries. We aim to satisfy even the industries. We aim to satisfy even the most diverse demands, including those most diverse demands, including those based in the food, drink, pharmaceuticals, based in the food, drink, pharmaceuticals, packaging and production industry, packaging and production industry, ensuring that all equipment is ensuring that all equipment is manufactured to the highest quality and manufactured to the highest quality and made to last. made to last.
The Stainless Steel Turntable is just one The Stainless Steel Turntable is just one of the products that we are proud to of the products that we are proud to supply at SSME and is available in various supply at SSME and is available in various sizes. sizes. A turntable that’s made from stainless A turntable that’s made from stainless steel is a cost-efficient investment to steel is a cost-efficient investment to make, especially if you’re looking to make, especially if you’re looking to maximise the efficiency of production. maximise the efficiency of production.
We supply the Stainless Steel Turntable We supply the Stainless Steel Turntable in a range of sizes to make it easier for in a range of sizes to make it easier for you to find products that will fit perfectly you to find products that will fit perfectly within your industrial setting. When it within your industrial setting. When it comes to accumulating products evenly, comes to accumulating products evenly, you cannot go wrong with the Stainless you cannot go wrong with the Stainless Steel Turntable- it’s specifically designed Steel Turntable- it’s specifically designed to bring work closer to the user. to bring work closer to the user.
MODULAR BELT CONVEYORS MODULAR BELT CONVEYORS
The modular belt conveyor offers a The modular belt conveyor offers a reliable versatile solution to many reliable versatile solution to many conveying applications. conveying applications.
The modular belt conveyor introduces a The modular belt conveyor introduces a flexible conveying solution that can, due flexible conveying solution that can, due to the nature of the belt itself, convey to the nature of the belt itself, convey products through inclined as well as products through inclined as well as horizontal and helical paths. horizontal and helical paths.
Space and loads permitting, 90 and Space and loads permitting, 90 and 180 degree turns enable products to 180 degree turns enable products to be conveyed on winding routes through be conveyed on winding routes through production areas. production areas.


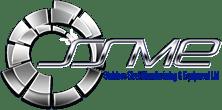
SANITISING CONVEYORS SANITISING CONVEYORS
Description:
Our Atomiser Sanitising Conveyors have been designed for the sanitization of the outer surfaces of various products being transferred between low and high care areas. A huge variety of products can be transported through the Sanitising Conveyor, such as boxed or bagged food ingredients like vegetables, sauces, coatings, blocks of cheese, the list is endless
Operation:
The solution tank is automatically filled with a pre-dosed mixture of water and sanitiser using a Dosatron water powered dosing pump. When a product is placed on the in-feed roller conveyor a sensor gives a signal to the control panel and the conveyor belt will start. Then using compressed air the mixture is then supplied to five atomiser nozzles which are positioned above and below the conveyor belt. These produce a mist within the tunnel giving total coverage of all surfaces of the products that are
Description: conveyed through the tunnel. The control Our Atomiser Sanitising Conveyors have panel has a built in inverter which allows been designed for the sanitization of the you to control the speed of the belt and outer surfaces of various products being ensures that a wide range of products transferred between low and high care can be safely passed through the system areas. ensuring that hygiene routines can be carried out quickly and reliably. Atomising A huge variety of products can be sanitization is very efficient as each nozzle only uses .8 litres of solution transported through the Sanitising per hour and with the integral gravity Conveyor, such as boxed or bagged food recirculation system the use of solution ingredients like vegetables, sauces, is kept to a minimum and your products coatings, blocks of cheese, the list is will not come out of the tunnel dripping endless with water.
Operation:
The solution tank is automatically filled with a pre-dosed mixture of water and sanitiser using a Dosatron water powered dosing pump. When a product is placed on the in-feed roller conveyor a sensor gives a signal to the control panel and the conveyor belt will start. Then using compressed air the mixture is then supplied to five atomiser nozzles which are positioned above and below the conveyor belt. These produce a mist within the tunnel giving total coverage of all surfaces of the products that are conveyed through the tunnel. The control panel has a built in inverter which allows you to control the speed of the belt and ensures that a wide range of products can be safely passed through the system ensuring that hygiene routines can be carried out quickly and reliably. Atomising sanitization is very efficient as each nozzle only uses .8 litres of solution per hour and with the integral gravity recirculation system the use of solution is kept to a minimum and your products will not come out of the tunnel dripping with water.
About Us About Us
At stainless steel Manufacturing & Equipment ltd, design and manufacture a wide range of stainless steel equipment for At stainless steel Manufacturing & Equipment ltd, design and manufacture a wide range of stainless steel equipment for the food and pharmaceutical industries. Our design team have over 25 years of experience and have worked on projects the food and pharmaceutical industries. Our design team have over 25 years of experience and have worked on projects for many of the major food and pharmaceutical manufacturers. We are based in the West Midlands, just 3 minutes form for many of the major food and pharmaceutical manufacturers. We are based in the West Midlands, just 3 minutes form Junction 10 of the M6. All our products are manufactured in house and we are the UK agent for the SCM boot washer and Junction 10 of the M6. All our products are manufactured in house and we are the UK agent for the SCM boot washer and hygiene station range. We pride ourselves in manufacturing good quality products at competitive prices and as well as our hygiene station range. We pride ourselves in manufacturing good quality products at competitive prices and as well as our standard range standard range We will manufacture items to meet customer specific requirements. We will manufacture items to meet customer specific requirements.