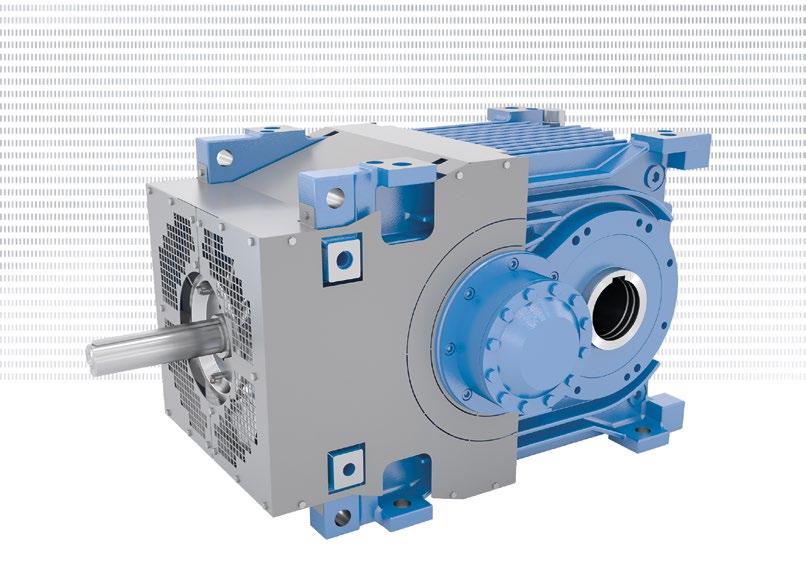
4 minute read
NORD
Durable drives for belt conveyor systems
With high thermal limit powers, MAXXDRIVE® XT industrial gear units have been optimised for bulk logistics applications such as belt conveyor systems.
MAXXDRIVE® XT industrial gear units are tailored to applications where high powers with low speed ratios are required Image: NORD DRIVESYSTEMS
High thermal and mechanical load capacities and long service life: With regard to the requirements for conveyor technology drives in the bulk goods and mineral industries, NORD DRIVESYSTEMS specially developed the MAXXDRIVE. XT industrial gear unit. It provides output torques of 15 to 75 kNm with speed ratios from 6.3 to 22.4 and is offered in seven sizes for powers from 22 to 2,100 kW.
LOW SPEED RATIOS, HIGH POWERS
The power and speed ranges of the two-stage right-angle gear unit have been specially designed for industries in which low speed ranges are required in combination with high powers – such as the bulk goods and mineral industries. Its robust design makes the MAXXDRIVE. XT resistant to dirt and reliable in rough operating conditions. A special sealing concept reduces maintenance. Large roller bearings and centre distances increase the load capacity and service life of the components.
As standard, the industrial gear unit is equipped with a heavily ribbed UNICASE housing and an integrated axial fan. Due to the increased surface and the airflow covers, the cooling airflow is optimised and a very high thermal limiting power is achieved. In many cases, additional cooling is not required.
CUSTOMISED PLANNING configured for customers according to the modular principle”, emphasises Jörg Niermann, Head of Marketing at NORD DRIVESYSTEMS. This is based on a comprehensive range of frequency inverters, motors and gear units, as well as coupling and brake systems, each with a wide variety of options. Features such as hydraulic couplings tailored to the particular process or Taconite seals, which effectively protect radial shaft seals against abrasive dust and corrosion, ensure smooth operation.
NORD also offers innovative predictive maintenance concepts for heavy industrial gear units. NORD drives networked via the frequency inverter communicate their status data via the control system or directly into a secure Cloud. With optional vibration monitoring, condition changes can be detected at an early stage and predictive maintenance can be scheduled in good time. Performance data recording also ensures optimal system dimensioning as well as continuous condition monitoring (Condition monitoring) of the drives.
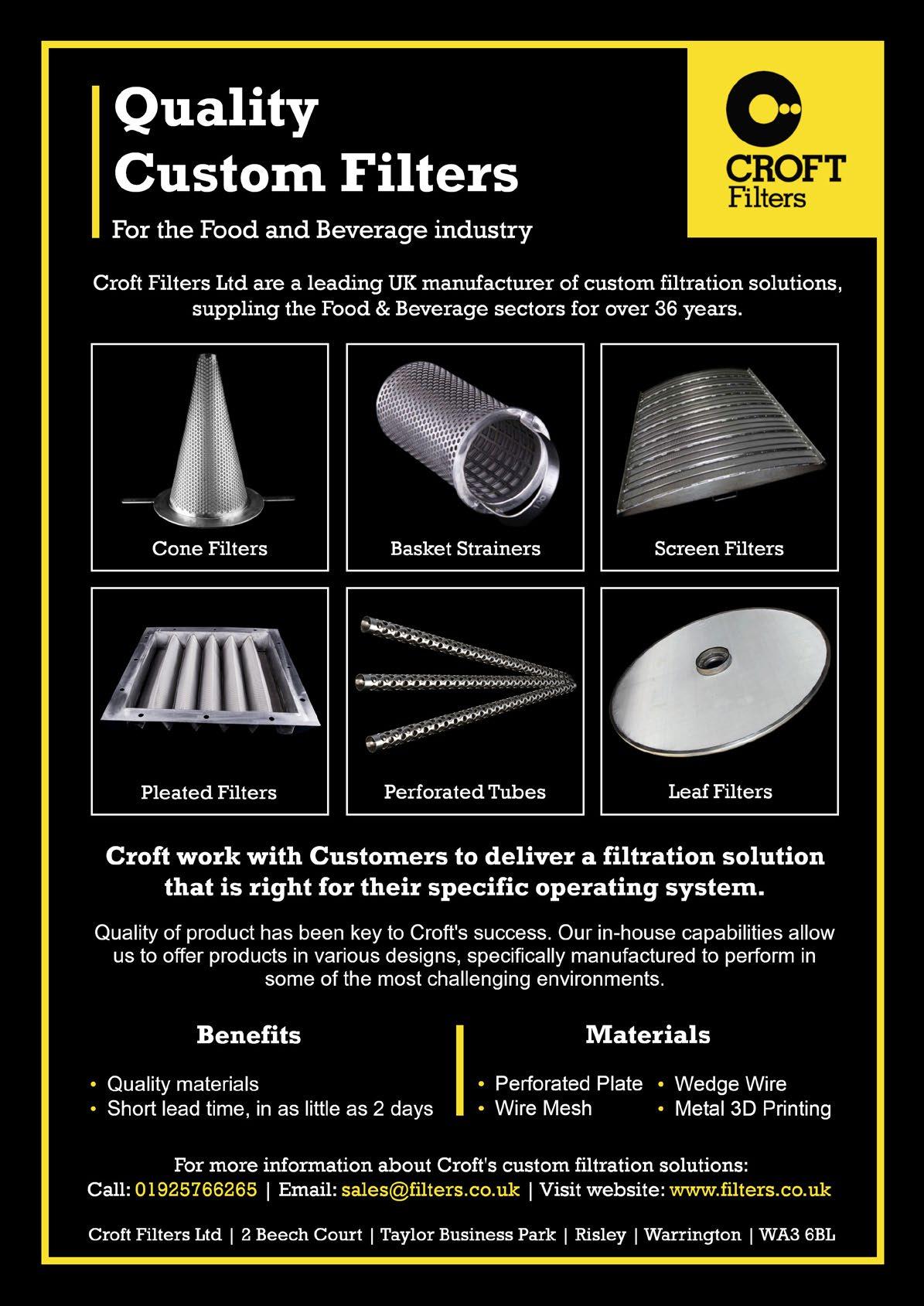
HPC: Supplying the food packaging & processing industry with air for the past 40 years
HPC is a core supplier in the oil-free (dry screw) compressor market, and has served the food processing and packaging industry for over 40 years with the most reliable and energy-efficient compressed air equipment.
Meeting the strictest air quality standards, HPC offers the full range of independently certified Class 0 oil-free compressors to meet all the critical demands of the food and beverage industries. HPC’s compressed air systems help drive primary processing equipment, mechanical conveyors, packaging equipment, printing and labelling, palletizers and de-palletizers, and air-driven hand tools, to name a few applications. The compressed air generated can safely be used in processes where the air is in ‘Direct Contact’ with the food product ensuring both product quality and safety.
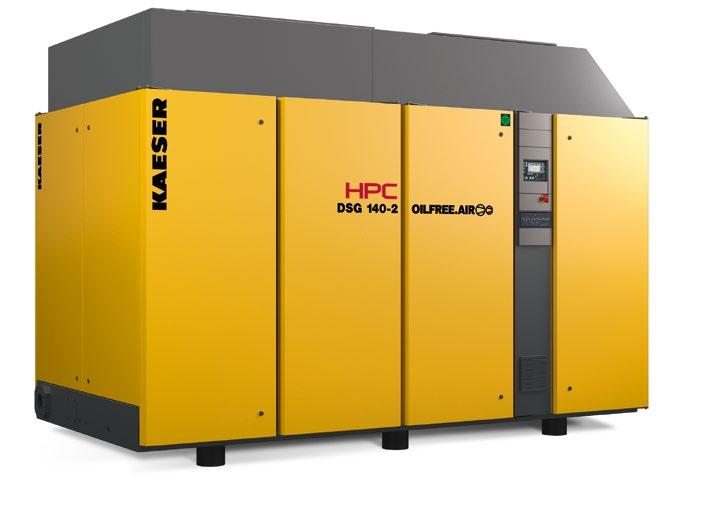
With their “built for a lifetime engineering”, HPC’s 2-stage oil-free rotary screw compressors deliver the best combination of efficiency and reliability. Too often, oversizing and lack of suitable system control wastes electrical power. Unreliable compressed air, inconsistent pressure and flow rate increase the risk of production downtime and product spoilage. With the additional issue of air leaks, improper uses, and artificial demand, up to 50% of the air produced can be wasted. HPC has performed tens of thousands of air system analyses and has the expertise to help you improve the reliability of your compressed air station whilst aiming to reduce your electrical power costs.
Designed for lower service costs, with tailored customer maintenance packages, HPC offers a range of energy-efficient fixed or variable speed models in an array of power sizes (2.2kW up to 355kW) and pressure options. With either integrated refrigerated or heat-ofcompression dryer options and advanced control and monitoring, HPC oil-free compressors comprise tried and tested components that deliver the durability and compressed air availability to meet even the toughest demands.
Supported by over 100 highly qualified engineers from HPC centres and its nationwide Authorised Distributor Network, HPC’s range of reliable, energyefficient, and independently certified ISO8573-1 Class 0 oil-free compressors also offer a unique heat recovery system, making it the first choice for reducing energy costs and your carbon footprint.
HPC is also planning to launch a new range of HPC KAESER CSG oil-free compressors in the new year. Delivery of the units is expected to start from March 2023.
HPC’s oil-free compressors backed up by HPC’s 5-year No Quibble Warranty. This warranty is supported by KAESER in its entirety for the first year. Thereafter, KAESER supports parts requirements for its duration, extending its support on major components including airends, motors and coolers. .
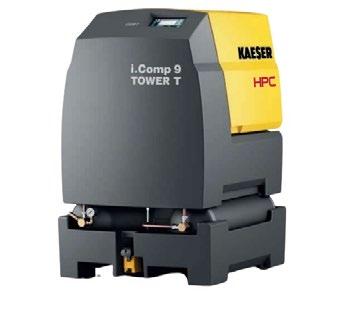
Supplying reliable food-grade air for over 40 years


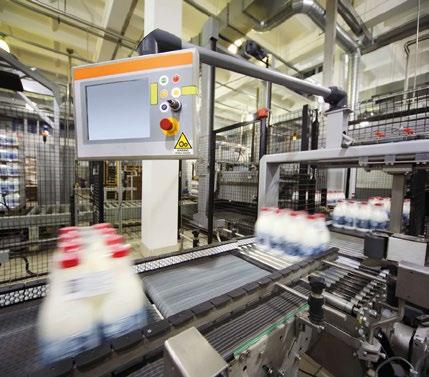
hpccompressors.co.uk +44 (0) 845 4300 472 web.enquiry@hpcplc.co.uk @HPCcompressor HPC plc
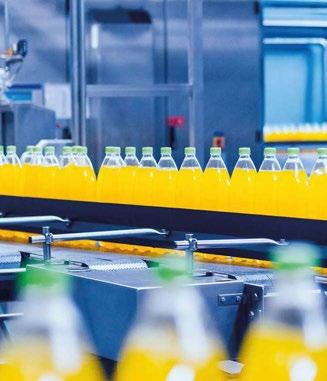
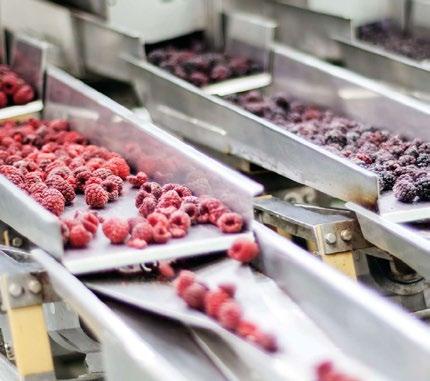
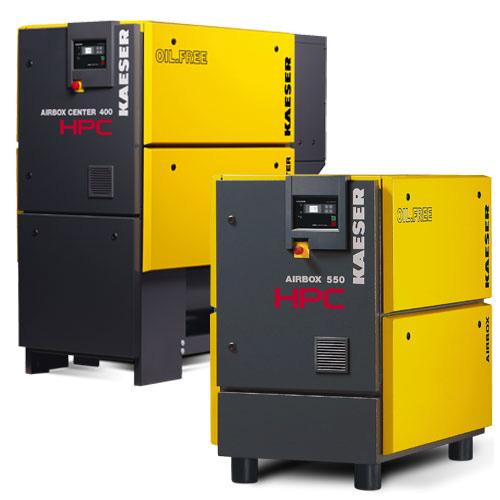