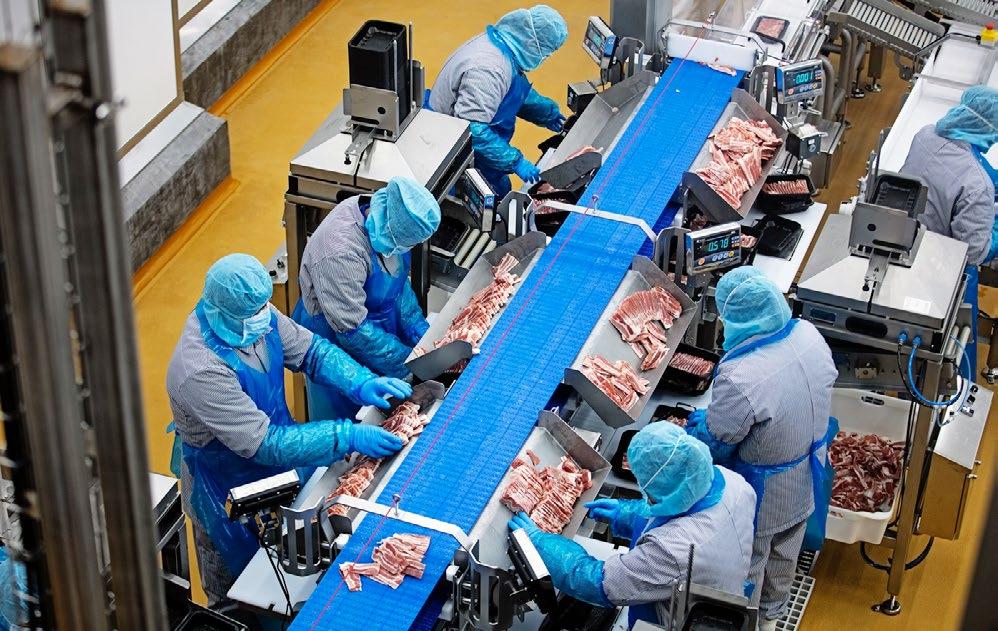
7 minute read
ISHIDA
Ishida Solutions support Danish Crown’s China expansion
Ishida Europe has designed and installed a series of bespoke packing lines for specialist meat producer Danish Crown’s new greenfield factory in China.
Working in close partnership with the customer, Ishida has supplied its own and ancillary equipment for the four lines, which are handling a variety of products including minced and diced pork, ribs and steaks, as well as quality control for thermoformed packs of pork. The factory is now in operation and will have a capacity for 14,000 tonnes of meat to be processed and packed each year when it is up to full speed.
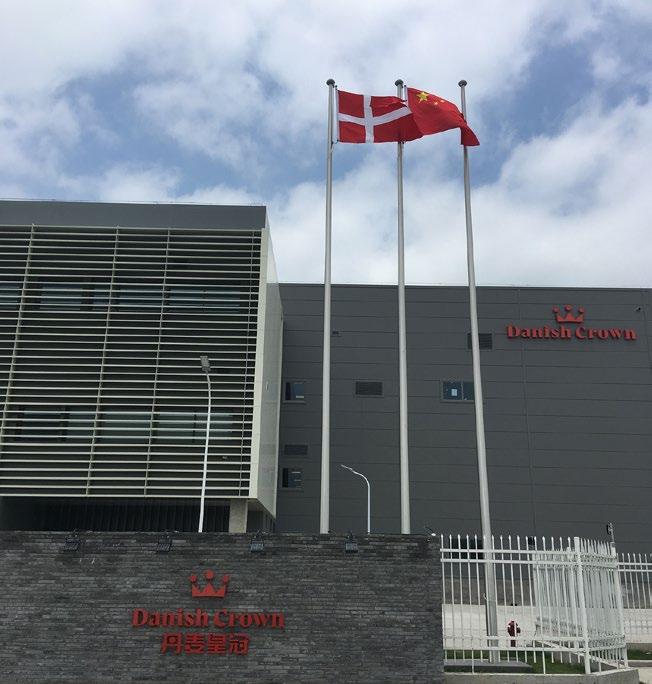
Ishida’s ability to devise complete solutions in line with customer requirements and efficiency and throughput targets, along with the excellent performance and reliability of its equipment, were key reasons for the company’s selection by Danish Crown. 32 FDPP - www.fdpp.co.uk
“We felt that Ishida offered the most relevant experience and the best solutions,” explains Nicolai Linde, Senior Manager Projects, Production and Supply Chain. “Having a single point of contact helped to speed up the process. In particular, the close working relationship established between our two teams and the continuing dialogue between them ensured that any issues or problems could be discussed and quickly dealt with to keep the project on time and budget and enable us to meet our performance targets.
“In addition, the company has an office in China which ensures a fast response in terms of service support and spare parts.”
The Ishida models installed at the factory include the company’s advanced RV-214 multihead weigher, QX-1100 Twin tray sealers, DACS-G checkweighers, IX-GN x-ray inspection systems and its weigh-price-labellers. Additional equipment integrated into the lines includes dicers, slicers, batching tables, labellers and cartoners. Ishida also gave factory personnel comprehensive training on all its machines and provided a technician onsite permanently during the first months of operation to ensure a trouble-free start up.
A key requirement of the overall design was to ensure maximum flexibility in the lines’ ability to handle a wide
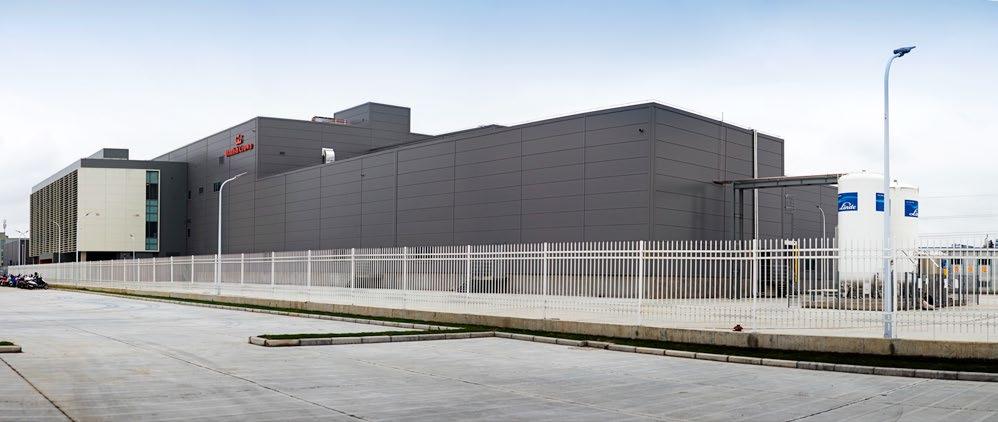
variety of products and pack types. For example, the multihead weigher is able to discharge diced meat directly into trays, or transfer ribs to a batching table for styling in the trays. Similarly, the QX-1100 tray sealers which currently seal MAP trays are also able to handle skin packs, which will enable Danish Crown to meet growing demand in the Chinese market for bone-in products.
“Although we were not previously familiar with Ishida’s tray sealers, they have proved to be very reliable and deliver consistently high-quality seals,” comments Nicolai Linde.
As another example of the excellent performance of the Ishida machines, the company’s IX-GN 4044 x-ray inspection systems and DACS-G-015 checkweighers are also providing quality control and weight checks on two separate thermoforming lines.
Danish Crown is one of the world’s largest exporters and one of Europe’s largest producers of pork. The new China factory in Shanghai was established to meet growing consumer demand in the Chinese market for high quality meat products, supplied via supermarkets and e-commerce.
“Our objective was to build the new factory to Danish standards,” explains Nicolai Linde. “For this reason, we focused on sourcing the very best European equipment throughout.”
www.ishidaeurope.com
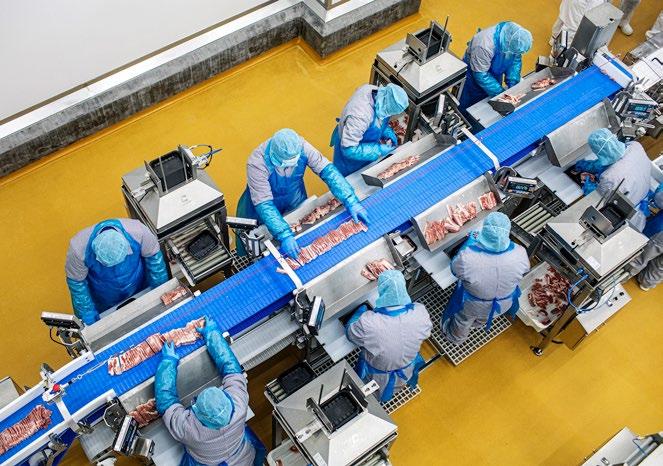
The Benefits of Automatic Metal Detector Testing
By Mike Bradley, Global Head of Sales (Metal Detection) Mettler-Toledo Product Inspection
Traditional methods of testing gravity fed metal detectors and those installed on Vertical Form Fill and Seal (VFFS) packing lines typically involve frequent and timeconsuming stoppages, potential risks to operator safety and often generate inconsistent results. In many cases, the test methods used do not confirm that the operational specification of the metal detector is being achieved. Automatic metal detector testing systems overcome these issues and can aid food manufacturing quality, efficiency and productivity.
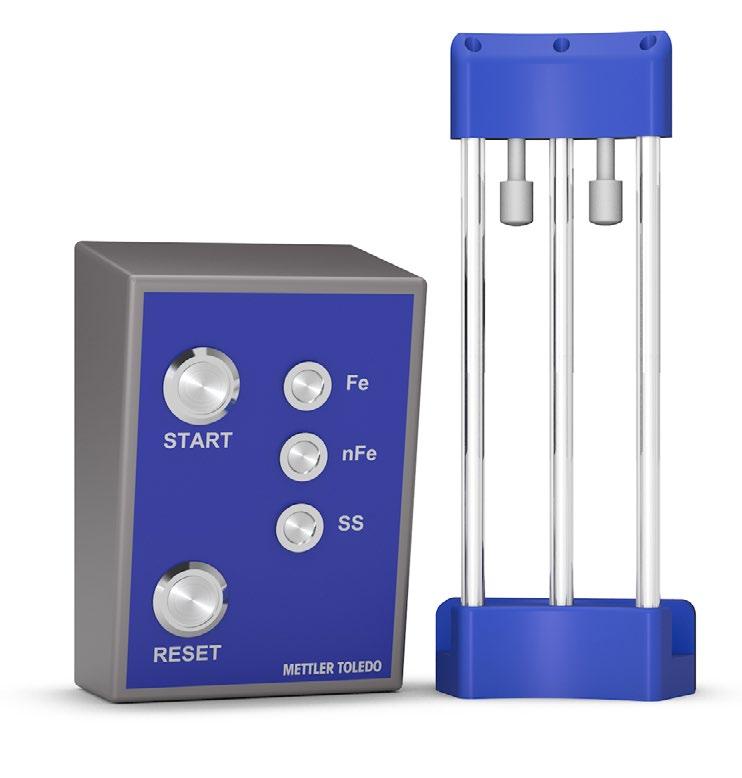
The “Drop-Through”, “Fishing Line” and “Test Rod” methods are all routine performance monitoring test processes for vertical metal detection inspection systems. Manual testing often requires teams of operators to put their safety at risk by climbing ladders and reaching over machinery so that they can drop or insert test samples into a throat or gravity-fall metal detector. These test processes are unable to accurately verify the operational specification of the metal detector. This is because they do not confirm centerline testing – the least sensitive part of the metal detector – as the placement of test samples passing through is generally random. In addition, manual testing processes can carry cross-contamination risks and can potentially compromise food product quality, as the test samples come into direct contact with the product.
Mettler-Toledo has delivered a solution to all these problems, while also helping to improve Overall Equipment Effectiveness (OEE) and productivity: its Automatic Test System (ATS) on Safeline metal detection systems, won the CFIA Innovation Award for Quality, Hygiene, Security and Environment in France in 2019 and has been recognised as accepted best practise by a major UK high street retailer. ATS is suitable for use in vertical food inspection applications such as snacks, crisps, confectionery, infant formula, bulk flour and nutraceutical powders, plus granulates such as sugar and food additives. Test samples are transported, by pneumatic control, up discreet nonmetallic tubes inside the metal detector’s aperture to a defined position within the sensing coils. The test samples are then released, simulating the presence of a contaminant in free-fall under gravity. A software algorithm correlates centerline sensitivity with edge of aperture sensitivity, eliminating the random nature of vertical metal detector testing.
Reduced Test (RT) Mode is an additional feature available on some throat and gravity-fall metal detection systems. When RT Mode is active, the metal detector monitors its online sensitivity performance and provides an alarm should the sensitivity drop below the specified level allowing companies to reduce the frequency of testing by up to 80%, without increasing their risk. This directly, and in some cases dramatically, improves productivity as production is now stopped less frequently for testing allowing productivity gains to be realised.
Major Italian savoury snack producer PATA S.p.A has 30 throat-style metal detectors on its production line, of which five have ATS installed. RT Mode is included as standard on the MettlerToledo Profile metal detectors that it uses. ATS and RT Mode have provided several benefits for PATA and for other food manufacturers that use them:
#1 ENSURE COMPLIANCE
ATS is the only method of testing that confirms centerline (worst-case) sensitivity performance. As such, it delivers test results of ongoing working performance that can be trusted.
When connected to centralised data collection and management systems, such as Mettler-Toledo’s ProdX software, ATS provides electronic records that are easily stored for future reference, for audit compliance or proof of due diligence. Having electronically stored data reduces the risk of errors or loss associated with paper records. This also supports rigorous quality control regimes, production optimisation and simplified production line operation.
#2 INCREASE PRODUCTIVITY
ATS tests are much faster than traditional testing methods. An end-toend 3-metal test (ferrous, non-ferrous and stainless steel) can be completed by
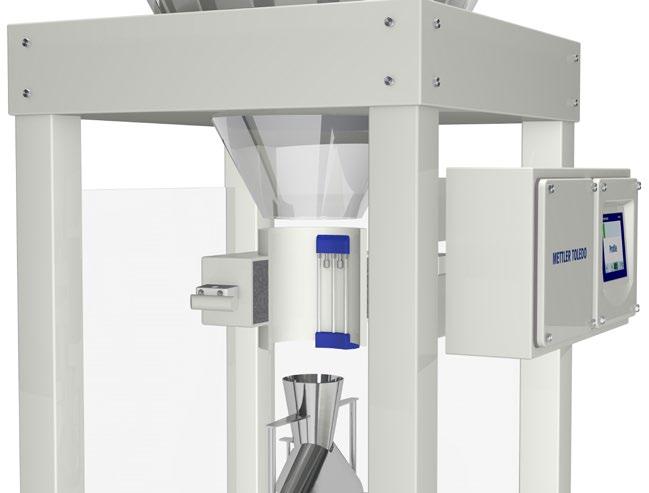
a single operator in under 40 seconds, compared to an average three to four minutes and two operators using traditional, manual methods.
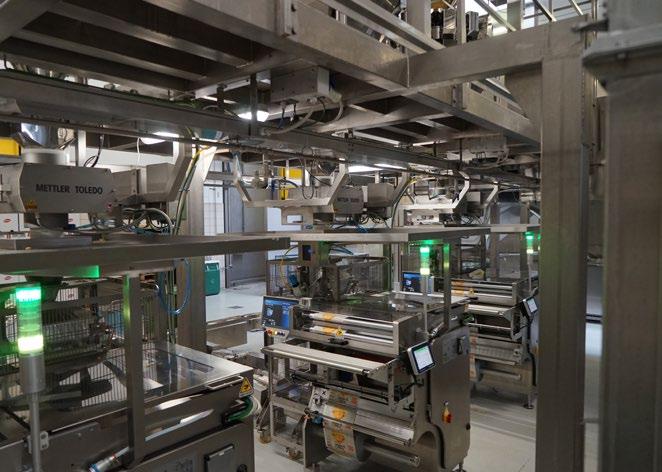
By using RT Mode to reduce testing frequency from every two hours to every 12 hours, a typical snack food manufacturer with 24 weigher-bagger lines running at an average of 100 bags per minute could save more than 4000 man-hours and produce 25 million more packs per year.
Mettler Toledo’s online calculators www.mt.com/md-roi-rt enable food manufacturers to work out how much they could benefit from using ATS and RT Mode. Not only will operators be safer with ATS, but fewer of them will be needed to conduct testing. For example, instead of one operator having to climb high to drop a sample through the aperture, and one to record the result and remove the sample from the production line, ATS testing can be completed by a single operator. It virtually eliminates the need to work at height to conduct routine testing and removes the need for operators to reach across installed equipment to insert a test sample.
#4 IMPROVE PRODUCT QUALITY AND FOOD SAFETY
ATS is a non-invasive method of testing, so test samples do not come into contact with food, removing the danger of cross-contamination. The higher sensitivity levels of RT Mode mean that smaller, irregularly shaped metal contaminants can be detected. RT Mode also continuously checks the performance of the metal detector to ensure it is always working to a level as good as, or better than, the food manufacturer’s specifications.
#5 ADDITIONAL FEATURE TO FACILITATE SOCIAL DISTANCING REQUIREMENTS
Additional to ATS and RT Mode is an ‘Emulation’ feature which allows operators to remotely control the metal detectors by mirroring their interfaces on remote networked devices. This is ideal for testing of systems installed in inaccessible locations plus also supports COIVD-19 social distancing requirements and enhances operator safety.
Food manufacturers can try out Mettler-Toledo’s ATS ROI Calculator here: www.mt.com/md-roi-rt
For more information, download MettlerToledo’s “Five Reasons to Invest in Automatic Test System”: www.mt.com/md-ats
FDPP - www.fdpp.co.uk 35