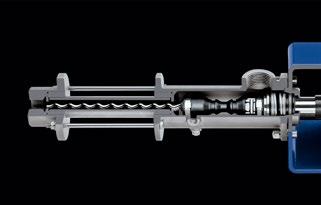
6 minute read
SEEPEX
Accurate dispensing of ab mauri bakery ingredients: Concept Controls Ltd and Seepex UK Ltd provide a perfect solution
A significant factor in baked goods manufacturing is the need to reduce the cost of raw material delivery into dough mixes. Modern research and process techniques have been used by AB Mauri, a major manufacturer and supplier of bakery ingredients, to produce a range of Enzymes, Bread Improvers and Enhancers in a highly concentrated form. These ingredients are highly effective, requiring very small amounts to be added to each batch.
To maximise the benefit of these concentrated products accurate dispensing of the ingredients is critical, both to ensure optimal ingredient performance, and to minimise overdosing (which can add to material usage and cost). Traditional weighing and Diaphragm Pump dispensing, even with the best of metering control, can lead to significant variations in the actual additive level to each batch of dough.
SOLUTION Although A.B. Mauri has considerable in house experience at developing the products, the related processes, and even the engineering of equipment, they wished to use an external engineering company with experience in Bakery and other process equipment to develop a solution that met demands for accurate dispensing.
Concept Controls Ltd (Waltham on the Wolds) were approached, and shown some of the original systems, a number of which had performance limitations with the latest developments in ingredients. After technical analysis of 44 FDPP - www.fdpp.co.uk
peristaltic, lobe and double diaphragm pumps a higher performance pump was sought to ensure accurate repeatable dispensing of concentrated ingredients from bulk containers.
During the research process the SEEPEX Progressive Cavity (PC) Pump, became a clear leader. The main benefit of the PC pump is that there is a sooth pulsation free delivery of material delivering repeatable accuracy of +/-1%. The flow rate is linear, proportional to motor speed and regulated by a simple speed controller over a very wide range. This was specifically useful as there is a limited time (Less than 25 Secs) for dosing of the A.B. Mauri products when operating on a standard Bread Mixer, hence a high rate of delivery is needed for rapid dispense, but a low rate of delivery for accuracy of dispense.
The pressure capability of these pumps is also very wide, and the Concept Controls Ltd system uses this to deliver a high pressure and high accuracy phase at the end of the dosing cycle. The pumps can also accurately dispense products with a wide range of viscosities.
By coupling this high performance PC pump, orifice plates, and a very high accuracy Endress and Hauser Coriolis Flow meter, Concept Controls Ltd, in conjunction with their partner company PVSL Ltd. (Brierley Hill), are able to meet the challenging specification requirements for A.B. Mauri. The detailed design phase started with 3D Models of the proposed equipment generated by PVSL Ltd.
The result is an easy to apply Dosing System, that includes bulk frame storage for IBC containers (normally in Stores area), with buffer tanks to allow a practical regime for maintaining product stock. The Seepex PC pumps are more than capable of delivering the various products to a dosing frame mounted close to the Mixers, and hence through the associated mixer lids and into each batch of Dough.
The Dosing Frame is a small matrix of fast acting Ball Valves which allow the product to be fed either directly to the Mixer, or via the flow limiting orifice plate.
The net result is a system that can deliver as low as 50g into a batch of product, and also extend to several kilogrammes, all within the 25 second window, and every batch can be metered to the nearest gram.
The overall benefit to the end customer, is that they can rely on a very consistent product, with the advantages of the most modern process innovations, without the potential of overdosing (i.e. wasted product), overall enhanced quality and reduced overall scrap.

Innovation at high-speed: container filling machines
Newtec’s High-Speed Container Filler (HSCF) has been designed for speed and versatility, in response to client requests for a solution capable of achieving higher capacity across a variety of products and packaging materials.
The HSCF can be easily adjusted to pack a diverse range of products, from harder items such as nuts and candies to softer and more fragile foods such as cherry tomatoes and blueberries. The solution is capable of filling containers in various dimensions with or without lids.
Newtec has designed a tool for each container type and while covering complex functions each tool is very easy to change from running e.g. clamshell trays to buckets. It has achieved this by using the following three units: the denester, the filling chute and the closing unit, which are all exchangeable. 46 FDPP - www.fdpp.co.uk
The cost-effective system is operated by an intuitive interface, which is an important factor, as well as the easy access for cleaning and servicing if you are changing your production many times a day.
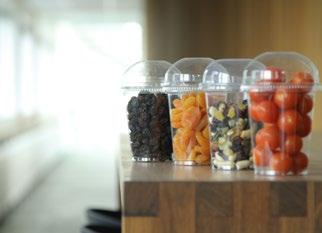
DESIGNED WITH SPEED IN MIND
Newtec mechanical engineer, Mathias Theil Eilertsen, worked on the solution’s development. The solution represents a fully automatic system from start to finish and is just one example of how Newtec can streamline your applications and increase your bottom line.
“It’s highly flexible and it offers highcapacity and high-speed,” he says. “That’s the main advantage of this machine. The high flexibility comes from the concept of having a basic machine where you add a set of unique tools depending on your preferred container types”.
“This means that you don’t need to buy a completely new machine if you get a new packaging material. That’s a big advantage.”
However, the machine has been designed specifically to deliver higher levels of speed. “Speed was quite a big thing for this machine,” adds Mr Eilertsen. “That was the main goal. With other machines, we are doing about 70 or 80 packs a minute. We can do up to 100 packs a minute with this one”.

“Customers will experience a higher speed and they will notice a lot more production than normal.”
KEEPING UP WITH NEW ORDERS
“We always develop new machines based on request and interest from customers,” Mr Eilertsen says. “Of course, they have an interest in getting the machines as quickly as possible when they get in touch with us. Often, our customers are taking a big automation step forward and can’t wait to start optimising their production”.
“So there’s a bit of pressure when we are in the innovation phase aiming for the best quality on the market and working hard to exceed the expectations of our customers. For me, it is so rewarding to

visit the customer after the installation for the final fine-tuning and see how their vision has been realised.”
Despite being able to operate at higher speeds, the HSCF’s energy consumption isn’t any higher than current machines on the market. Mr Eilertsen says the feedback has been highly positive and there are more orders to follow. This adds to Newtec’s total of installing more than 20,000 machines during the last 40 years.
Newtec is a leading manufacturer of weighing, packing and sorting machinery primarily for the fruit and vegetable industry. With more than 20,000 successful installations over the last 40 years, they have maintained their position as a reputable worldwide company. Newtec is represented in more than 50 countries with subsidiaries in Copenhagen and the UK and a joint venture in China. Newtec has formed many strong partnerships throughout the industry, ensuring the right solutions are delivered. They deliver cutting-edge machinery, integrated into one solution and supported by local, qualified representatives to ensure each solution continues to meet the needs of their customers.
NEWTEC Odense (UK) Ltd. 22 Fleet Road Industrial Estate, Fleet Road, PE12 8LY Holbeach, Spalding United Kingdom Ph: 01406 426 526 Mobile: 07827 973 238 Mail: dean@newtecuk.com www.newtec.com

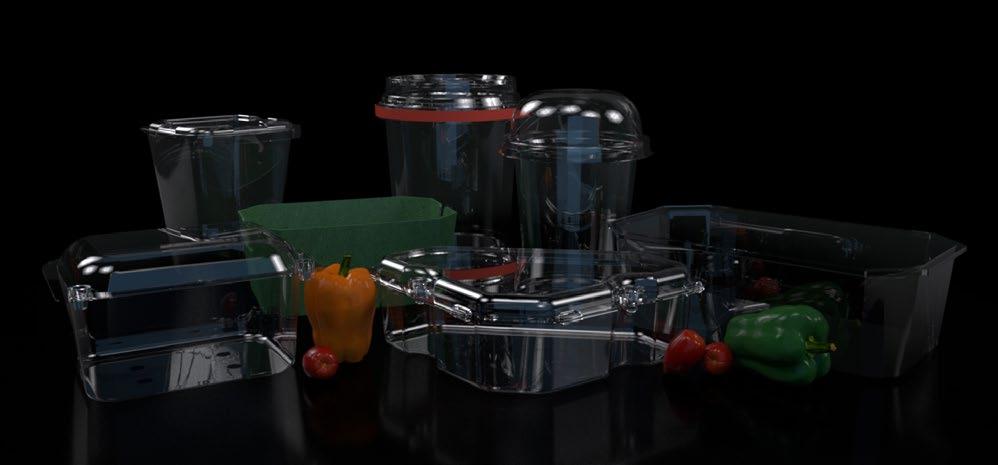