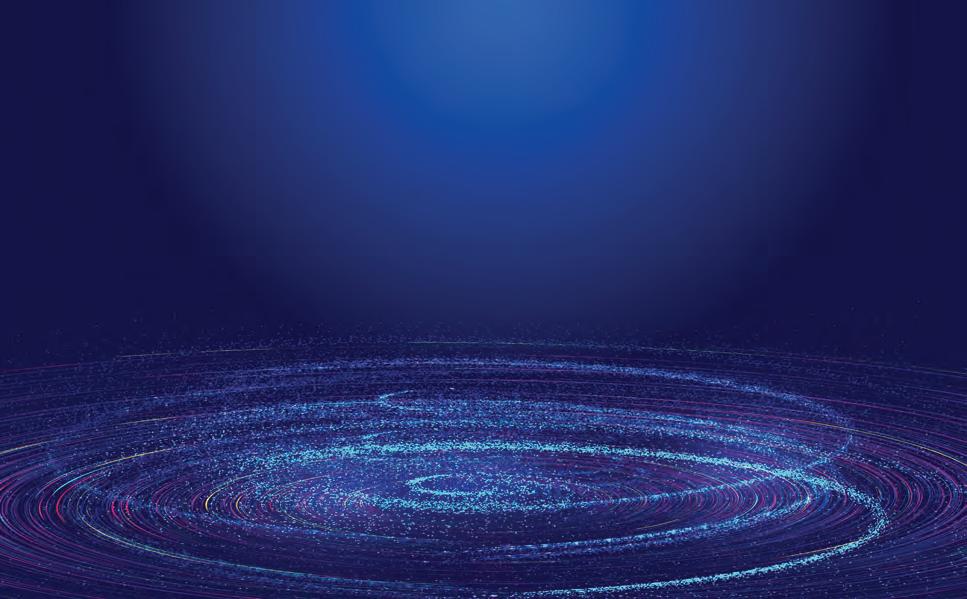
5 minute read
ESCAPING DATA ISLAND
How manufacturers are going beyond data collection to drive operational improvements
The proliferation of sensors, programmable logic controllers (PLCs) and countless other advancements in Internet of Things technologies has created a massive trove of data for manufacturers to access.
Advertisement
However, without the proper tools, systems and training in place, this wealth of information can largely go untapped, creating a drag on an organization rather than improving efficiencies, increasing quality and driving value.
“You can collect all the data in the world, but unless you’re using that data, it’s overprocessing, as they would say in manufacturing,” said Michael McGray, a senior sales engineer with Zeeland-based Industrial Control. “I’m doing something that’s adding no value to my organization and adding no value to the customer. If I’m just collecting data and not using it to impact my business, then I’m wasting my time and resources.
“You don’t realize the impact or ROI on these investments until you use the data to make changes in your organization.”
Data collection is nothing new. Supervisory Control and Data Acquisition (SCADA) systems have been around for decades. However, in today’s technically driven manufacturing environment, it’s no longer enough to simply collect data. SCADA has since evolved into a larger umbrella including data storage, visualization and analysis in which myriad tools, information systems and software are used to drive process improvements on the shop floor.
Yet many manufacturers are “deadheading” the data they already collect, leaving it on their various machines or stuck in “shadow” databases they don’t readily access, McGray said.
In his work, McGray points to numerous examples where an operator manually records the number of pieces a machine is producing. A supervisor then comes around, evaluates the production rate and determines if the operator and machine are on task. This amounts to a manual intervention, ultimately decreasing efficiency, according to McGray.
The machine’s sensors are already conducting a piece count along with other key parameters such as the RPM of the tool. This data should then be exported to a database where it can be viewed immediately by the operator and analyzed and benchmarked later by production managers and other executives.
“Unless people are looking at the data, it’s still not helping at all and you’re still going to have the same old problems,” McGray said. “That’s what this has really been about: getting this data off these islands and into an environment that brings transparency to it.”
IMPLEMENTATION REALITIES
In practice, expanding beyond data collection into storage, visualization and analysis can prove challenging for manufacturers, particularly smaller and mid-size companies that may lack the resources and expertise to properly implement the systems.
One of the primary challenges comes from making all the different technologies — sensors, PLCs, robotics, machines and other tech — interface in a cohesive manner.
These technologies may all operate under different industrial protocols or “languages” and require third-party tools and software to translate them through a company’s ERP or MES system, according to Gray.
Once all the different pieces of technology around the shop floor are communicating in the same language, manufacturers need to store that data in a database such as SQL or Oracle. From there, they should deploy a data visualization tool, like PowerBi, to properly analyze and act on the data.
The issue is that these are often complex and expensive systems, outside the budgets for many small and mid-size manufacturers. When helping manufacturers implement these systems, McGray likes to begin
TWO WAYS TO LEARN MORE ABOUT “OPEN CONTROLS”
n Senior Engineers from Wago, Inc. will be speaking about how to capture, display, and move data on Thursday, 9 AM in the speaker Automation Room #1 (see page 16)
n Michigan Manufacturing Technology Center (MMTC) has its Smart Technology Zone cul-de-sac of exhibitors and speakers about Industry 4.0
by addressing prominent pain points, in many cases starting with on-time delivery. McGray analyzes the operation at the cell level to determine which specific operation kicks off the delay. Then he helps facilitate data collection and analysis on those operations so management has a clear picture of what is happening at any moment. “No one wants to be late,” McGray said. “If data collection can help you accomplish being on time, most people aren’t going to fight you. The problem comes in the implementation of these systems and having the capital to go and find the right integrator to connect your equipment, implement the correct information systems and train your personnel on how to become database decision makers instead of being reactive.”
ACCELERATING ADOPTION
As data collection, storage and analysis becomes a larger part of the manufacturing ecosystem, emerging technologies are making implementing the comprehensive systems easier.
McGray specifically points to MachineMetrics and Freepoint, as examples of new tools that are agnostic of hardware. These platforms allow companies to log into and configure devices remotely and use third-party connector tools to communicate with all of the equipment on the plant floor. The data are then automatically uploaded to the cloud, where the tool provides robust data analytics capabilities and the ability to contextualize the data in one platform, McGray said.
Advancements in technology will likely continue to drive down the costs and barriers of entry associated with data collection, storage and analysis systems. Ultimately, all of the base technology and concepts already exist; it’s a matter of companies finding the technology that fits their budget and use case.
“Data collection, storage, analytics and visualization are the core components and that’s what it’s really about,” McGray said. “Everything else is about innovation.” n
PRODUCTIVITY, DELIVERED.
The People | The Products The Service | The Solution!
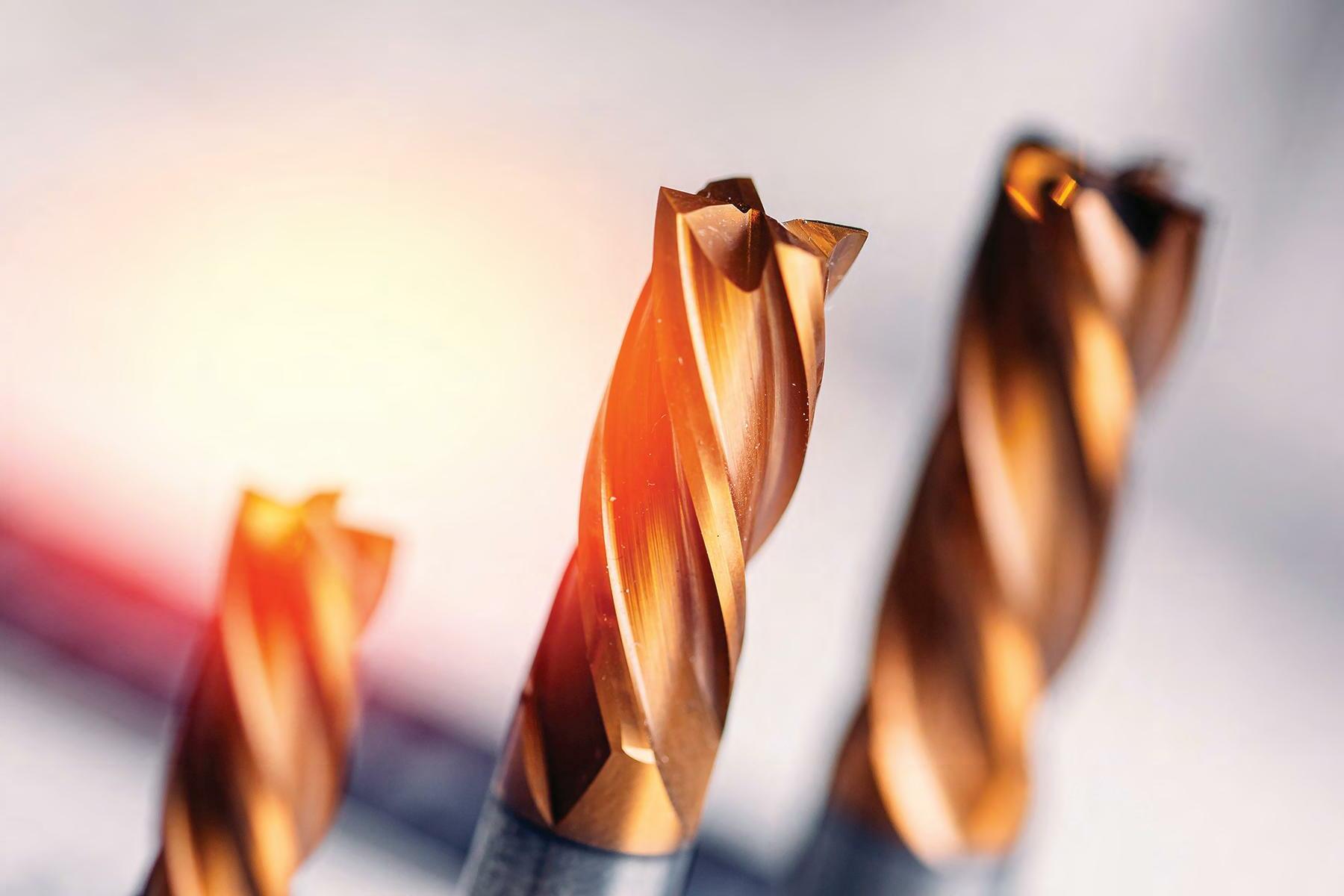
VISIT US AT BOOTH #1108
Exclusive Metalworking Hall Sponsor
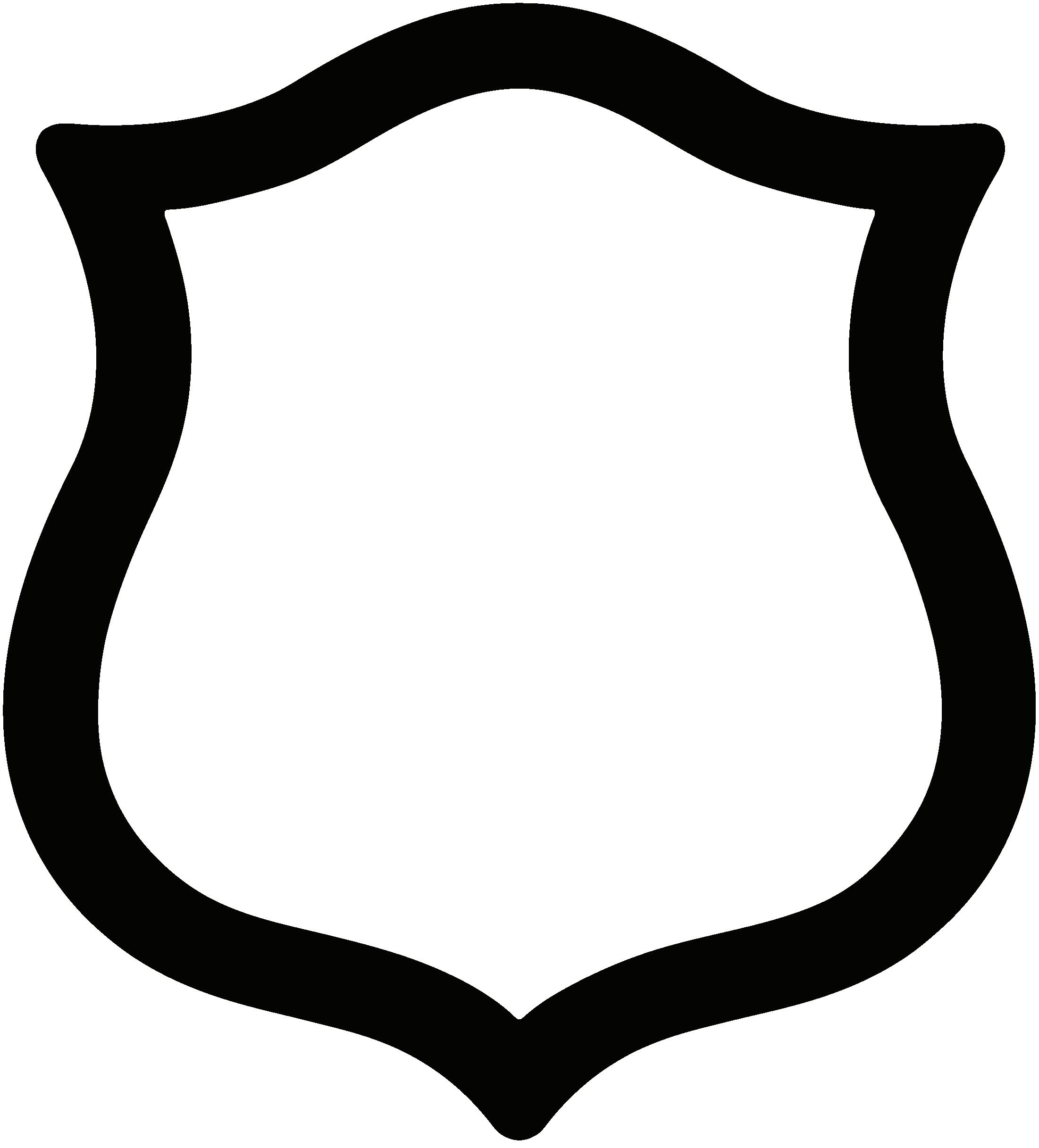
CrestonIndustrial.com | 800.999.9180
Home of Friction Free Commerce.
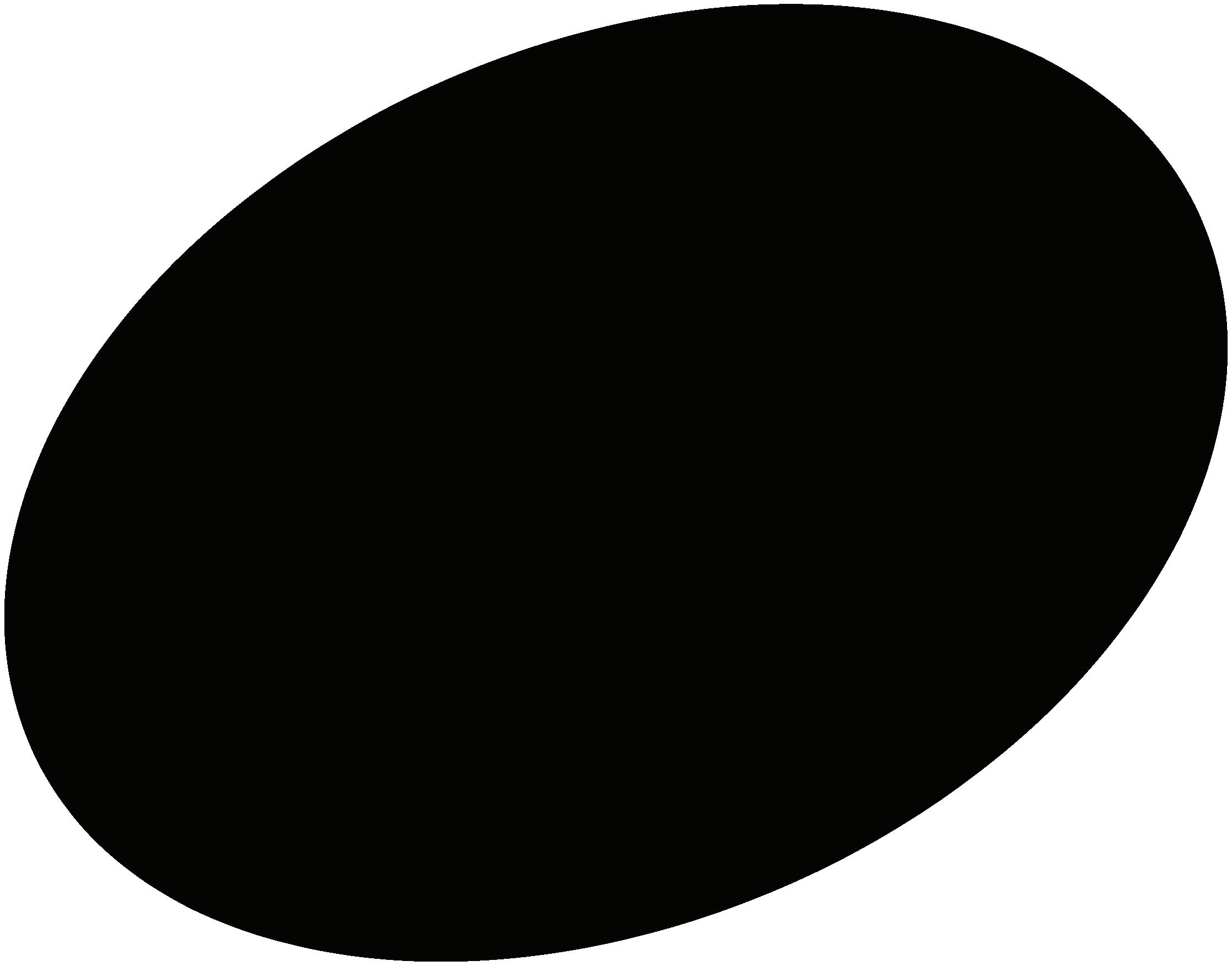