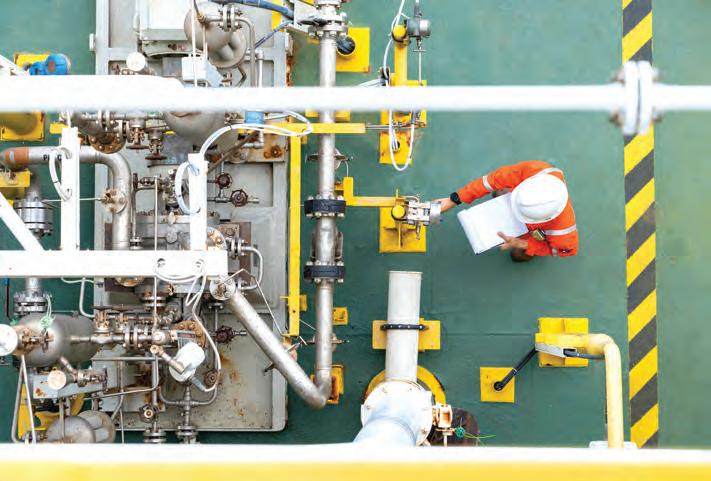
6 minute read
BEARING DOWN: HOW THE INTERNET OF THINGS IS REDUCING FACTORY DOWNTIME
BEARING DOWN
How The Internet of Things is Reducing Factory Downtime
Advertisement
All manufacturers have been there: A ball bearing in a gearbox suddenly fails and production comes to a standstill, with products sitting on the line, workers left with nothing to do, and thousands of dollars wasted until a replacement is made.
“Downtime is the bane of every manufacturing plant in the world,” said Ben Shine, sales account manager at the Grand Rapids branch of Motion, a subsidiary of Genuine Parts Co. “Businesses have historically accepted that as a part of making product.”
The average manufacturer deals with 800 hours of downtime a year, with costs ranging anywhere from $500 per hour into the thousands, depending on the products on the line. According to a study conducted by MIT, an estimated $240 billion is lost annually in industries across the United States because of downtime for repairs on failed manufacturing equipment. Half of those failures are due to improper bearing maintenance.
Now, thanks to Smart Sensors, downtime may be a thing of the past.
Dodge Industrial, a leading manufacturer of mounted bearings, enclosed gearing, and power transmission products, worked with ABB Group to develop the Dodge Smart Sensor five years ago. The sensors are small, about 3-inches tall, and fit on a variety of gearboxes and mounted bearings. They monitor assets for temperature and vibration, aggregating real-time data that is pushed through a gateway via Bluetooth into the cloud and into an app, which alerts users to anomalies that indicate a need for maintenance before a failure is imminent. One gateway can collect data from 50 sensors on a shop floor.
This interconnectivity is called the Industrial Internet of Things, and it’s revolutionizing the shop floor by giving machines a means to “talk” to workers by letting them know when a critical component is on the verge of failing. Jack Gilmer, West Michigan territory manager for Dodge Industrial, refers to the Smart Sensors as “like a FitBit” and emphasizes the power of the data collection.
“As you are collecting trending data, each bearing creates its own signature,” Gilmer said. “Every bearing doesn’t operate at the same temperature and vibration, depending on where it is installed. Over time, it creates a baseline.”
Each company that uses Smart Sensors owns its data outright, and data are encrypted as recommended by the National Institute of Standards and Technology. Personnel can view the data on a smartphone, tablet or computer.
Mock-up dashboards from Dodge show what looks like an EKG reading as the sensors track the temperature and vibration data. The interface is intuitive and designed for ease of use. It communicates the health of a part with the classic traffic light system: Green for tip-top shape, yellow to alert something may be amiss, and red to alert an impending failure. Systems also can use advanced algorithms to direct maintenance endeavors and establish protocols.
Motion distributes replacement components for machines as well as the Dodge Smart Sensors. As such, Shine is familiar with the pain a sudden bearing failure can cause a company.
“A lot of manufacturing plants, when they have a failure, it is a critical failure,” he said. “Everything stops, the line shuts down. You may have product on the line that isn’t salvageable. You may have a product that has a dwell or set time. It’s extremely expensive.”
Manufacturers typically perform maintenance on a schedule, but when a bearing
MANUFACTURING DOWNTIME BY THE NUMBERS 800
is the average number of hours a manufacturer deals with each year. $500
is the hourly cost of downtime for manufacturers $240B
lost annually across the U.S. because of manufacturing downtime 50%
of manufacturing failures due to improper bearing maintenance
fails, it fails suddenly and needs immediate attention, or reactionary maintenance.
With minimal installation time, Smart Sensors provide unprecedented opportunities for monitoring machine health while increasing effectiveness and improving safety and productivity on the shop floor.
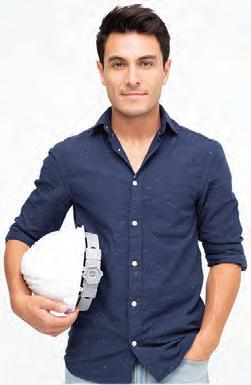
“You can do a planned outage to replace or repair that part, which doesn’t disrupt production,” Gilmer said. “Safety-wise, many of these bearings are in the bowels of the process and are not easily reachable, so it is collecting data from these hard-to-reach areas. Also, when something fails critically, it may take out other pieces of equipment.”
Additionally, as preventive maintenance is currently performed, workers use their best-informed guess as to when a part needs to be replaced, potentially replacing parts that don’t need it.
“With predictive maintenance driven by the sensors, you can run a bearing for the entire life of the product, which adds up to huge savings,” Shine said.
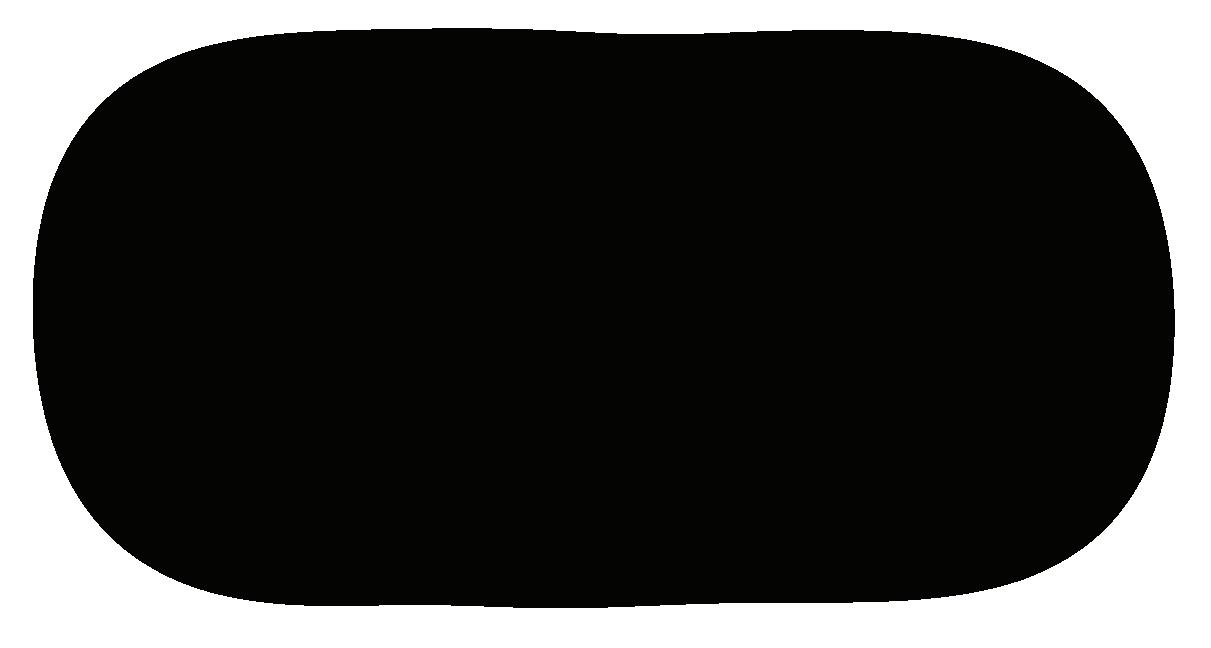
While the Smart Sensors need to prevent just one incident of factory downtime for customers to recoup their investment, many manufacturers consider the initial cost as prohibitive, Shine added.
“(Smart Sensors) are now much more consumer-friendly, and now we are in a world where sensors are far less than $1,000 a sensor,” Shine said. “They just need to prevent one downtime and it pays for itself. Like anything else, the more people use it, the more they buy, and the price drops.”
For Shine, the capability of Smart Sensors signals a data-driven glimpse into the shop floor of the future, where sensors alert workers to bins being low on raw materials or signal when shipping areas need to be clear before production continues.
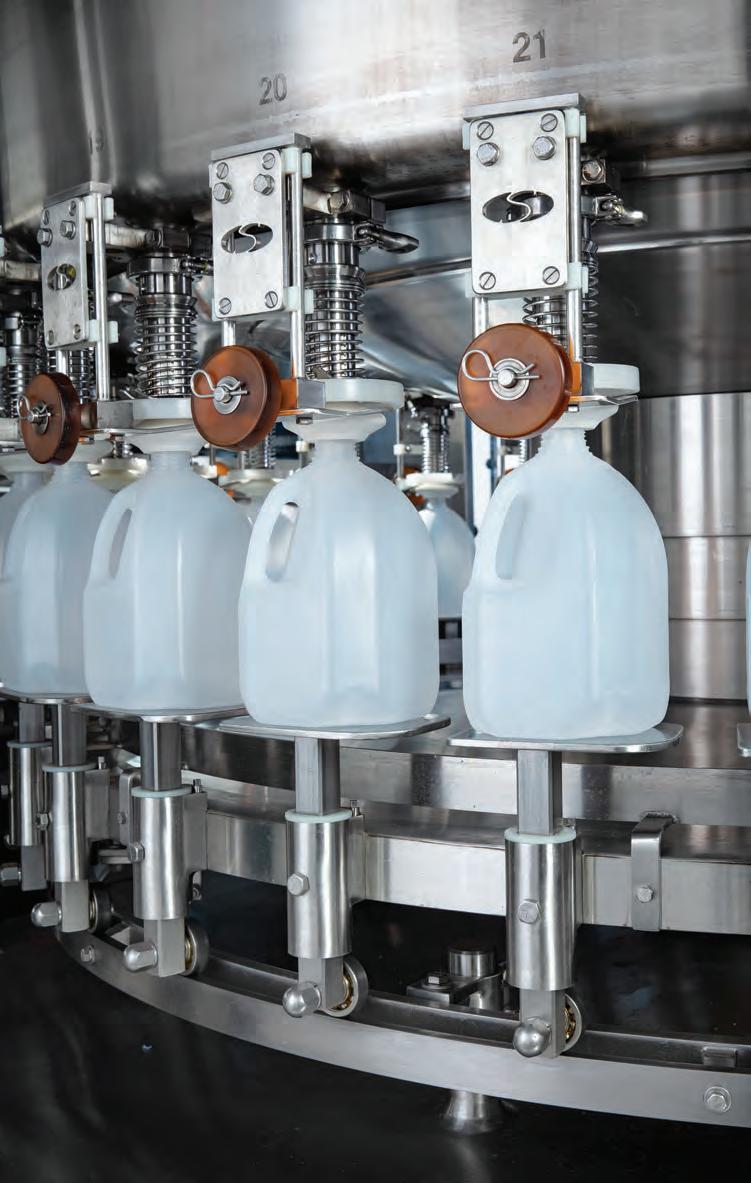
“All of these mundane tasks can be automated and monitored by technology,” Shine said.
Today, Motion is adapting quickly to provide customers with other smart products, such as pneumatic air cylinders that are powered by electronic actuators, allowing for precise control.
“Say you are gluing a box. With an electric actuator, you can finitely control it to deposit just the right amount of glue,” Shine said. “You’re saving money and getting a much better product.”
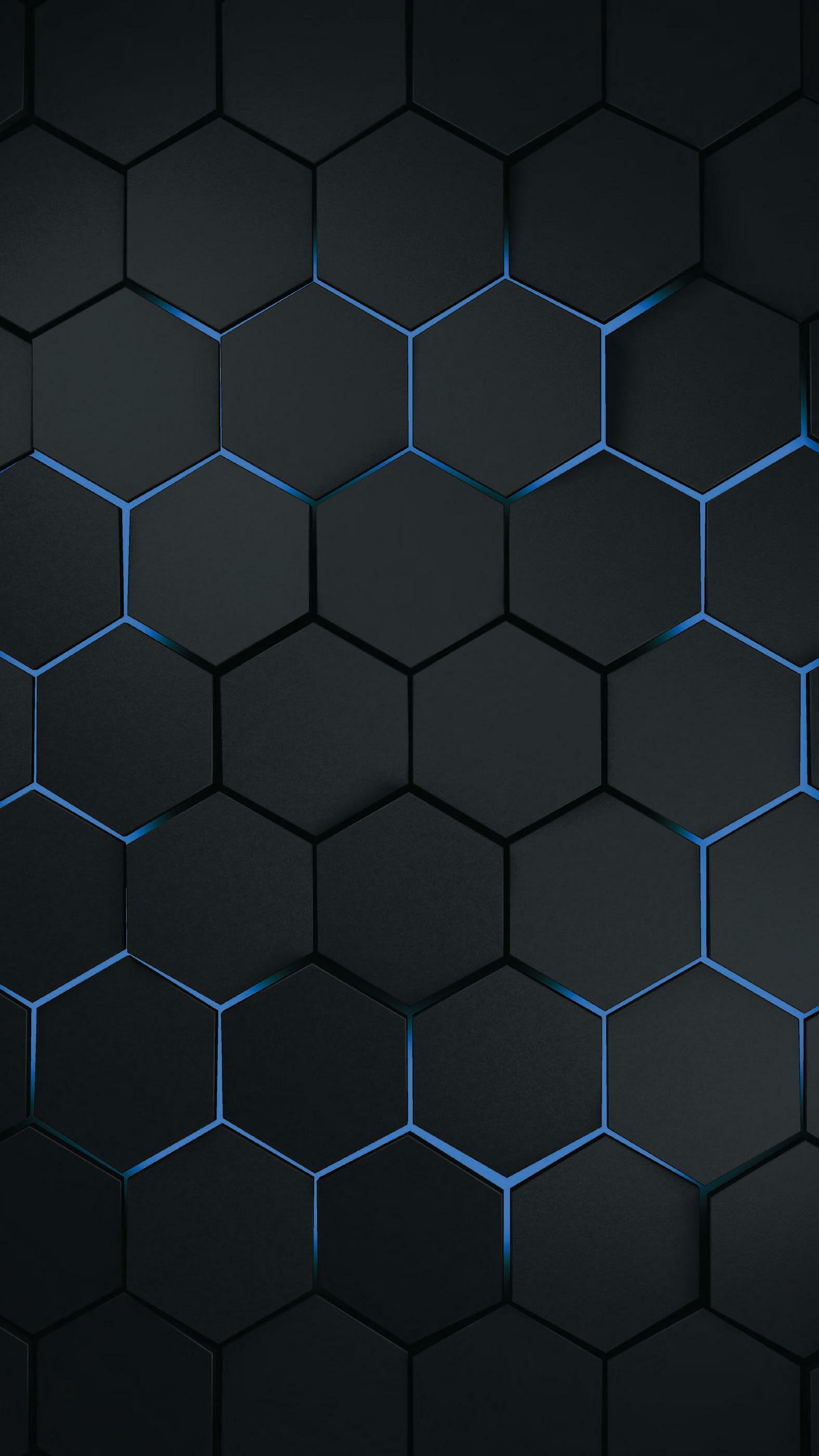
Gilmer notes that as the Industrial Internet of Things moves further and further into the shop floor, the need for laborers will diminish in place of a growing need for technicians.
“They have to be able to trend data and set up technology,” he said. “It is all going to be on computers, and we train people ourselves once they come on board.”
Shine says that adaptation to new technology on the shop floor will pick up as manufacturers realize a future free of downtime.
“We are creatures of habit, and it requires a shift in thinking,” Shine said, “but the cost savings are really a no-brainer.” n
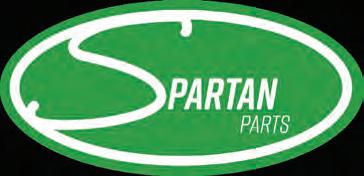
To be your voice, we must hear your voice.
For 120 years, the Michigan Manufacturers Association (MMA) has been a unifying champion of an industry in constant evolution and growth. Our mission to the industry is clear: to hear your voice, to unify your voice, to amplify your voice and to be your voice.
Your company can’t afford to not be a member. Join the only association dedicated solely to manufacturers.
Learn more at mimfg.org.
Special Offer Join MMA at mimfg.org with code EXPO2022 to receive 20% off your first year’s dues investment.
