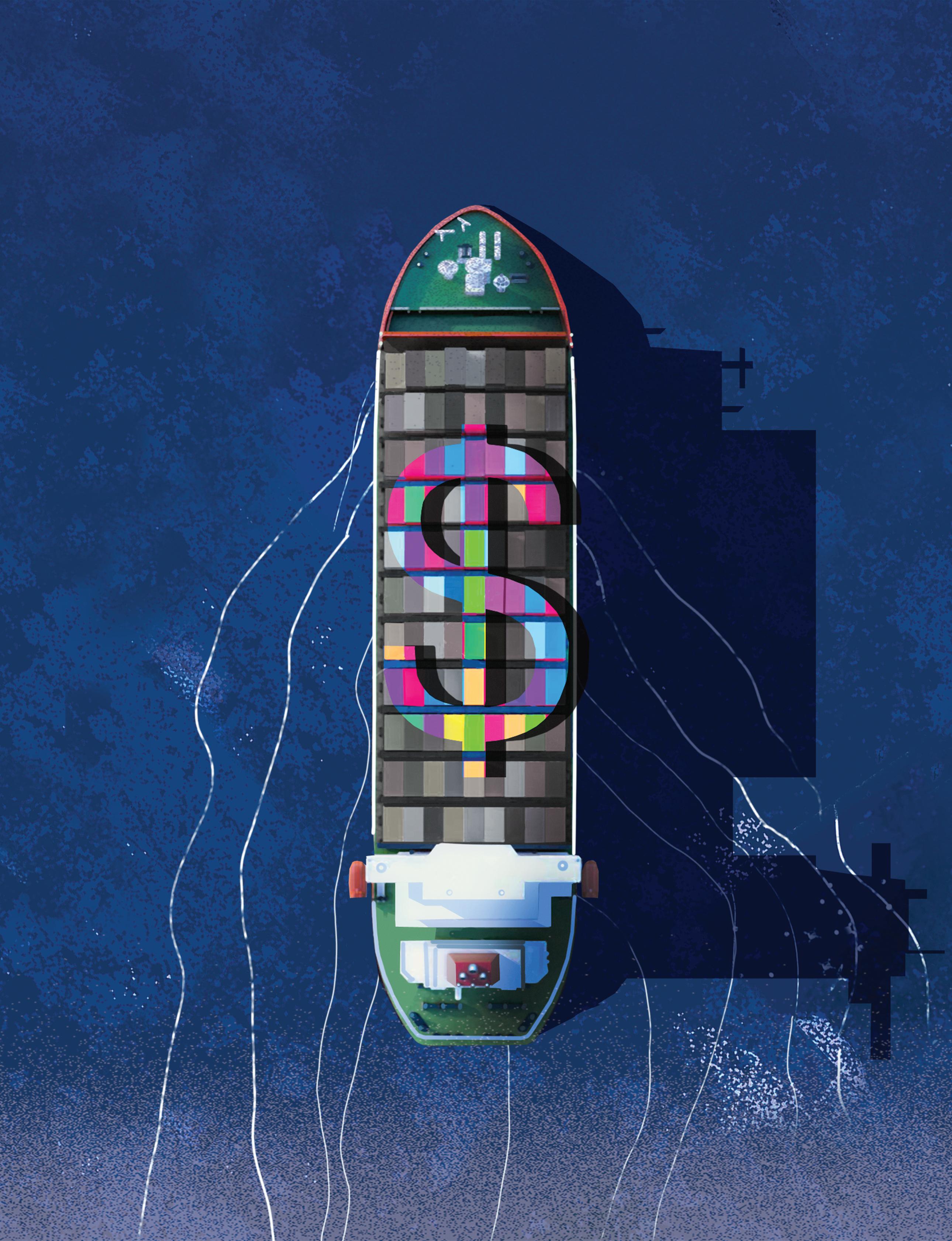
9 minute read
Supply Chain Strain Hits the Middle Market
XX XXSupply Chain
Strain Hits the Middle Market
Advertisement
WRITTEN BY MEGHAN DANIELS | ILLUSTRATED BY EVA VÁZQUEZ
Companies grapple with unprecedented logistics issues while looking for solutions, including diversifying vendor sources and upgrading technology.
For almost two years, the
COVID-19 pandemic—and the unprecedented demand for goods that came with it—has wrought havoc on the global supply chain. Middle-market companies have faced obstacles in sourcing, manufacturing and delivery, and many have had to fundamentally rethink their supply chain and logistics strategies.
The situation is unprecedented to say the least. After a brief dip in the early pandemic, spending on goods has risen almost every month since April 2020, according to the Bureau of Economic Analysis. U.S.-bound imports have continued to rise each month this year, with an average of 95,341 TEU (Twenty-Foot Equivalent Units) imports in Q3 of 2021, according to Panjiva. The fourth quarter was on pace to exceed last year’s record-breaking holiday season. Though suppliers have increased production dramatically since the beginning of 2021, they are still working to match the continuing demand.
“There has been a massive shift in e-commerce over the course of the pandemic where people, for health and other reasons, have moved most of their buying decisions online. This is true even as it relates to some of the most expensive and valuable assets people own, like houses and cars,” says Shane Kaiser, a director at Houlihan Lokey.
A confluence of factors in addition to the surge in demand for goods has contributed to the strain. Factory and port shutdowns were commonplace in early 2020 thanks to coronavirus outbreaks, but troubles have continued into this year as well. For example, in August, China suspended operations in the Meishan terminal, a crucial terminal in its third-busiest port, after detecting a single COVID case. The infamous Suez canal blockage in March had ripple effects that lasted far longer than the six days the ship was stuck, increasing port congestion and putting further pressure on already-taxed supply chains.
With the increased demand for goods also came soaring container prices. While prices have dropped as of October 2021, the prices for ocean freight remain several times their pre-pandemic cost, according
Jim Pratt
Managing Partner, Forsyth Advisors
to Bloomberg. And price isn’t the only concern: Availability has also been severely limited. “While people are concerned about cost, availability can be an even more immediate concern. If businesses can’t get a component at all, they can’t make a sale. For major retailers, there are penalties for not having shipments available on time,” says Jim Pratt, a managing partner at Forsyth Advisors.
Other factors contributing to the supply chain crisis include outdated freight and rail systems, truck driver and other labor shortages, lack of container movement, full warehouses and more. Record-high inflation rates and freight prices further complicate the issues.
A whopping 80% of middle-market companies are currently experiencing supply chain challenges, according to a recent ACG survey. For 60% of respondents, delayed or canceled shipments of inventory or raw materials posed the biggest problem.1 High transportation costs were also a big concern, with 23% of respondents citing these costs as their greatest supply chain challenge.
COVID didn’t create these problems, but it did bring about a perfect storm in which nearly every business seems to be experiencing all of them at the same time. “The issues in the supply chain that companies are facing right now have been around for decades, but they’re really being highlighted now in an atmosphere of heightened demand,” says Pratt.
The impact on middle-market companies has been significant. Elkay Interior Systems (EIS), which designs, manufactures and installs commercial interior solutions, has struggled with the availability and cost of key raw materials, increased lead times for intercompany supply between Asia and the U.S., increased costs for air and sea freight, unexpected shifts in construction schedules due to labor shortages, decreased availability of shipping containers, clogged ports and more. “There have been instances when shortages in shipping containers and backlogs in Chinese and U.S. ports have resulted in air freighting products to meet U.S. customer product schedules,” says Prem William, head of global supply chain at EIS.
For air freshener company Drift, increased lead times and uncertain availability of key materials have made it necessary for the team to scale back on marketing efforts multiple times. “The most significant impact for us has been on the acquisition side. We’ve had big media hits that would have been huge acquisition opportunities for us that we weren’t able to capitalize on because we couldn’t guarantee getting our product to new customers in a timely manner,” says CEO Ryan Baylis.
Companies are used to dealing with supply chain problems but not all at once. “The greatest challenge has been the compounding nature of the current environment,” says William. “For the past 18 months we have had to deal with multiple disruptions simultaneously, absorbing the
Over the past year, have you added a dedicated supply chain professional, or hired another professional with supply chain experience to your team?
Yes
26%
No
66%
Not yet, but we plan to
8%
10 0 20 30 40 50 60 70
Source: Survey of ACG members
Are you experiencing supply chain disruption?
t
Yes 80%
No 20%
Prem William
Head of Global Supply Chain, EIS
cumulative cost increases associated with both raw material and logistics, extreme variability in demand and scarcity of human resources needed to manage the supply chain.” Juggling these crises in real time while working to minimize delays to customers is a full-time job.
In addition to COVID-related concerns, there are also unrelated supply chain disruptions to contend with, including climate-related natural disasters like fire and flooding, bad weather, regulatory restrictions and geopolitical affairs.
With these obstacles looming, middle-market companies are eager to find ways to make their supply chains more resilient—adopting new tools, restructuring teams, adjusting product lines, adapting timelines and rethinking suppliers. Nearly 60% of respondents to ACG’s survey said that supply chain challenges have led their companies to change the way that they do business.
RESTRUCTURING TEAMS
With more frequent and more pressing supply chain issues than ever before, middle-market companies are having to adjust operations accordingly. According to the ACG survey, 34% of companies have either hired a dedicated supply chain professional, added an additional professional to their team, or plan to do so soon.
Other middle-market companies are shifting responsibilities for supply chain management to top executives. “We’re seeing CEOs and other senior management take a much more active role in solving supply chain crises,” says Forsyth Advisors’ Pratt. “The people that normally would handle supplier relationships are good at being the squeaky wheel but in this scenario a greater relationship focus is needed. More and more CEOs are negotiating lead times and deliveries with suppliers.”
RESHORING AND DIVERSIFYING THE SUPPLY BASE
For today’s businesses, evaluating and identifying risks at every point in the supply chain is key to addressing issues and making processes more resilient for the future. Depending only on one geographic region (or factory or supplier) for raw materials or inventory can be disastrous in the case of a crisis or shutdown in that area, as countless companies have learned over the past year or two. As a result, many middle-market companies are looking to move suppliers closer to home and also increase the number of suppliers so there is a backup if needed.
EIS, for example, is diversifying its Asia supply base across both China and Vietnam, “to allow for orders to be placed strategically depending on market conditions,” says William. The company is also expanding its supply chain in Mexico and reshoring
production into regional business models to minimize exposure to logistics delays (and the associated cost increases).
For many companies, diversifying may mean finding alternatives to China. While this is important to avoid overreliance on any one source, it can come with its own challenges. Shifting production to Southeast Asian countries like Vietnam, Indonesia or Thailand, for example, “will necessitate different logistics strategies as well,” notes the Harvard Business Review. Ports in these countries don’t always have the capacity to handle the largest container ships, and shipping from there may not allow for direct service to major markets. Ultimately, diversifying suppliers and/or reshoring won’t happen overnight, but the pandemic has illustrated how important it is for businesses to be prepared to encounter supplier issues before they strike.
ADOPTING TECH SOLUTIONS
Only 22% of middle-market companies have full insight into their supply chain providers, according to the survey. This lack of transparency can cause countless issues, especially in such a volatile environment. Adopting new technology can help middle-market companies gain more insight into their providers and streamline their overall supply chain. For many businesses, their current technology may be outdated and may not provide the real-time insights they need to address issues as they arise. According to the survey, 34% of respondents have adopted new technology solutions for supply chain management.
Technology’s ability to forecast and predict supply chain issues down the line can be a game-changer for businesses. EIS recently launched a digital supply chain initiative to help “better predict what may happen as well as create visibility into supply chain disruptions in real time, allowing us to make decisions before they are a problem,” says William. “We just implemented a machine learning forecasting process that looks at over 40 external macroeconomic factors to develop a more realistic view of what may happen in the future.” This has significantly reduced the company’s overall projection error since its implementation, ultimately helping lower costs and increase customer satisfaction.
Technology is key to more resilient supply chains. But for many compa-
nies, especially those that may not have changed supply chain management practices for some time, getting started can be intimidating. Taking an adaptive approach to technology adoption is crucial, notes a recent Bain & Company brief.
Rather than thinking about technology transformation as a multi-year process—as once was standard—successful companies “deploy rapidly evolving technologies, including cloud-based software-as-a-service applications, that continually enhance the supply chain backbone,” the Bain report says. While ERP systems remain at the core of their operations, they minimize their reliance on the software and delegate tasks that the ERP was once responsible for to smaller SaaS products and other emerging technologies. This kind of tech architecture can more easily adapt to change, which is inevitable given the rapid pace of technological innovation.
There is a huge range of technology solutions that have the potential to transform the way businesses manage their supply chain, notes Bain, including artificial intelligence and
machine learning tools to improve forecasting, robotic solutions to transform warehousing, drones for last-mile delivery and location monitoring, blockchain for traceability and smart contracts, 5G for inventory management and remote services, and 3-D printing for decentralized production.
Many of these technologies have been in development or available for some time, but greater demand
Robotics is transforming warehousing as more and more businesses adopt, innovate and embrace the concept of using autonomous robots to fulfill orders.
Shane Kaiser
Director, Houlihan Lokey