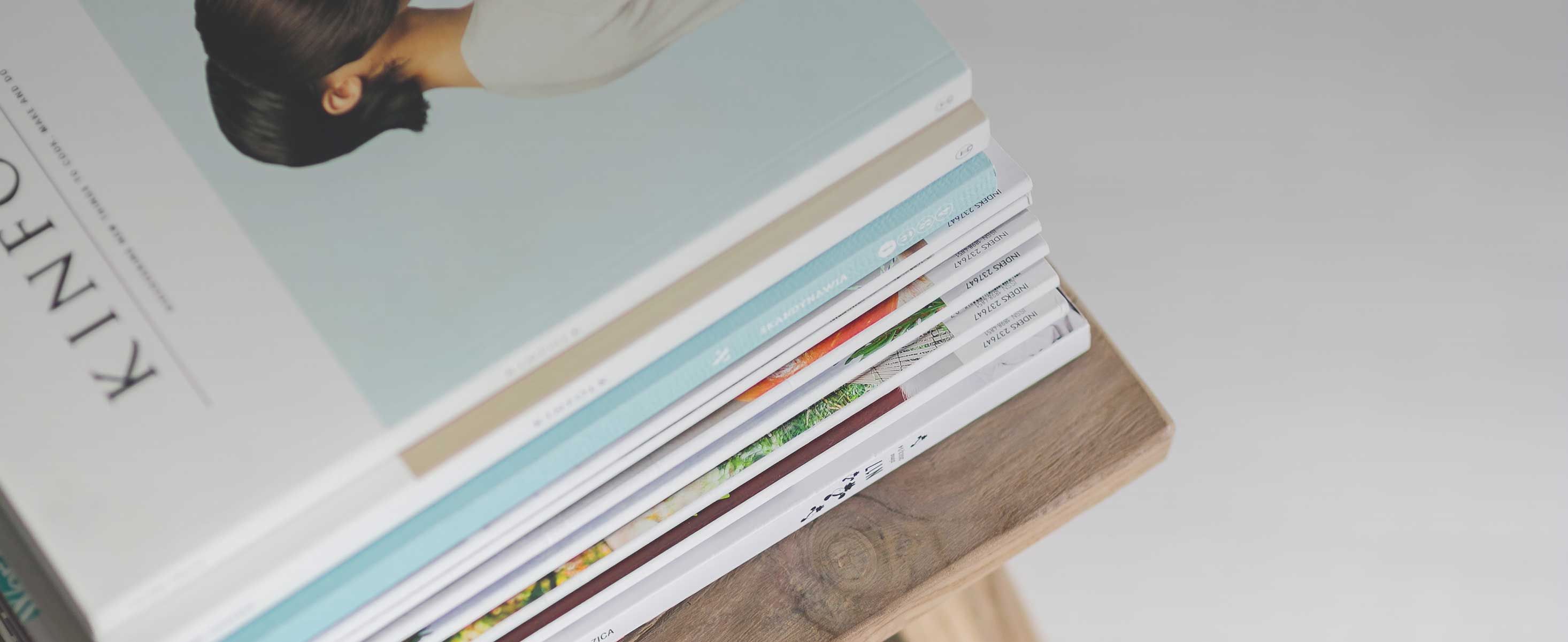
1 minute read
UNDERSTANDING KAIZEN AND ITS RELATION TO WASTE ELIMINATION
Kaizen, a cornerstone of Lean manufacturing, embodies the philosophy of continuous improvement and is pivotal in the elimination of waste within industrial processes. Originating from Japan, Kaizen translates to "change for the better" and involves every employee in the pursuit of making the workplace more efficient and less wasteful. This methodology is not only a set of guidelines but a mindset that permeates through all levels of an organization, encouraging a culture of constant, incremental improvements. The practice of Kaizen involves various activities including Kaizen events, which are focused initiatives aimed at addressing specific issues within a process or area in the production line. These events typically last from one day to a full week and are structured to foster team collaboration across different functions and levels within the company to brainstorm solutions, analyze data, and implement the most effective improvements.
The integration of Kaizen in Lean practices focuses heavily on the elimination of the eight wastes, known as 'Muda', which include defects, overproduction, waiting, non-utilized talent, transportation, inventory, motion, and extra-processing. By continuously identifying and eliminating these wastes, organizations can significantly enhance their operational efficiency and productivity. For instance, Kaizen encourages employees to spot inefficiencies in their immediate work environment and suggest practical solutions. This proactive involvement helps in fine-tuning processes and removing unnecessary steps or resources that do not add value to the product or service.
Moreover, the application of Kaizen principles extends beyond manufacturing processes. It is equally effective in project management and other business operations where efficiency is crucial. By applying Kaizen strategies, businesses can define clear value objectives, streamline workflows, optimize resource allocation, and foster an environment where continuous learning and improvement are part of the organizational culture. This holistic approach not only supports waste reduction but also drives sustainable growth and competitiveness in the market.