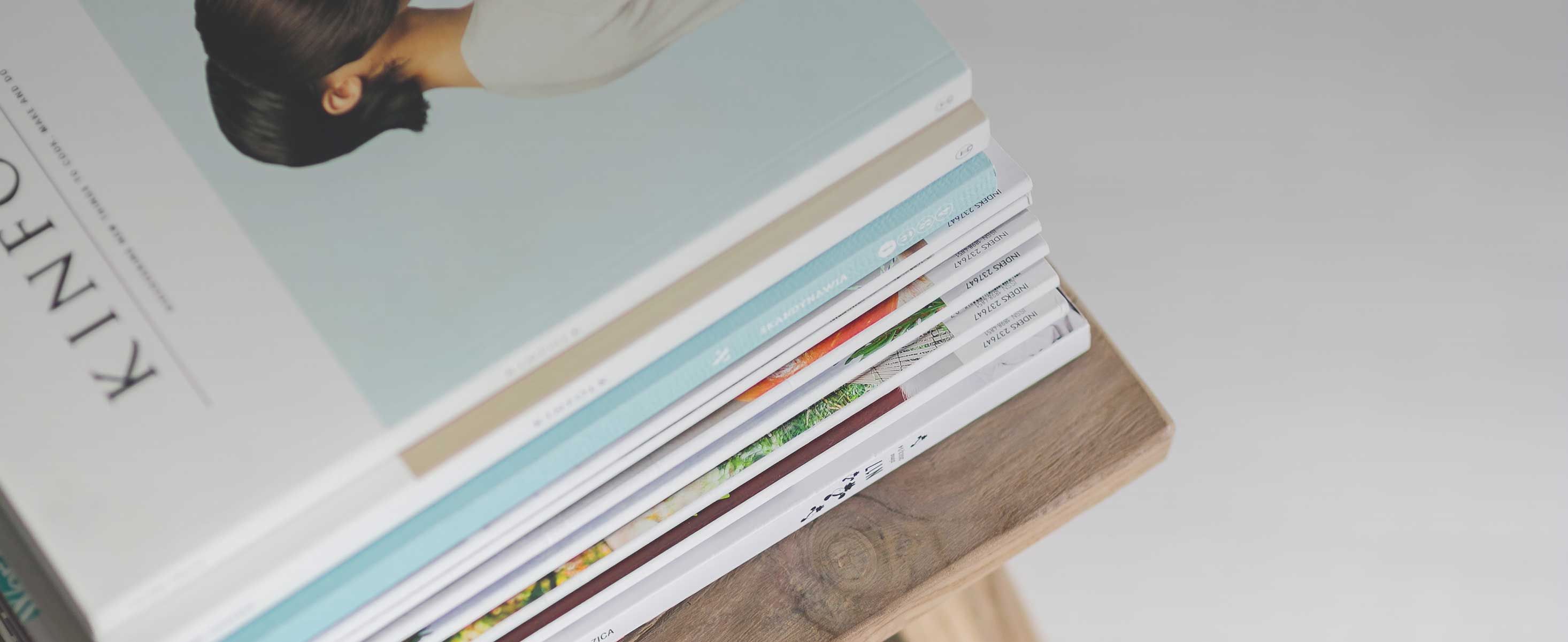
1 minute read
LEAN
Manufacturing
In the context of Lean manufacturing, waste represents any activity that consumes resources without adding value to the customer. This concept is crucial in identifying inefficiencies that could be streamlined to enhance productivity and reduce costs. Here, we explore the 8 wastes of Lean, often summarized by the acronym 'DOWNTIME'.
Here are the 8 types of wastes. These are all different types of waste. Lets dig into the 8 wastes:
1. DEFECTS
Defects in products or processes lead to rework or scrap, which incurs additional costs and effort. Common causes include inadequate quality control, poor process design, and insufficient worker training. Mighty Line floor tape and signs can help delineate specific zones for quality inspection, reducing the risk of defects escaping to the next stage of production.
2. OVERPRODUCTION
Producing more than is needed or before it is required creates excess inventory and ties up capital. This often results from poor demand forecasting or overestimating the efficiencies of batch production. Implementing floor markings to designate specific production areas can help control the pace and volume of production, aligning it more closely with actual demand.
3. WAITING
Waiting for materials, information, or equipment leads to significant downtime, affecting overall throughput. This waste is often due to poor workflow design or imbalanced workloads. Strategic placement of Mighty Line floor markings can streamline operations, clearly indicating where materials and tools should be placed for optimal access and flow.