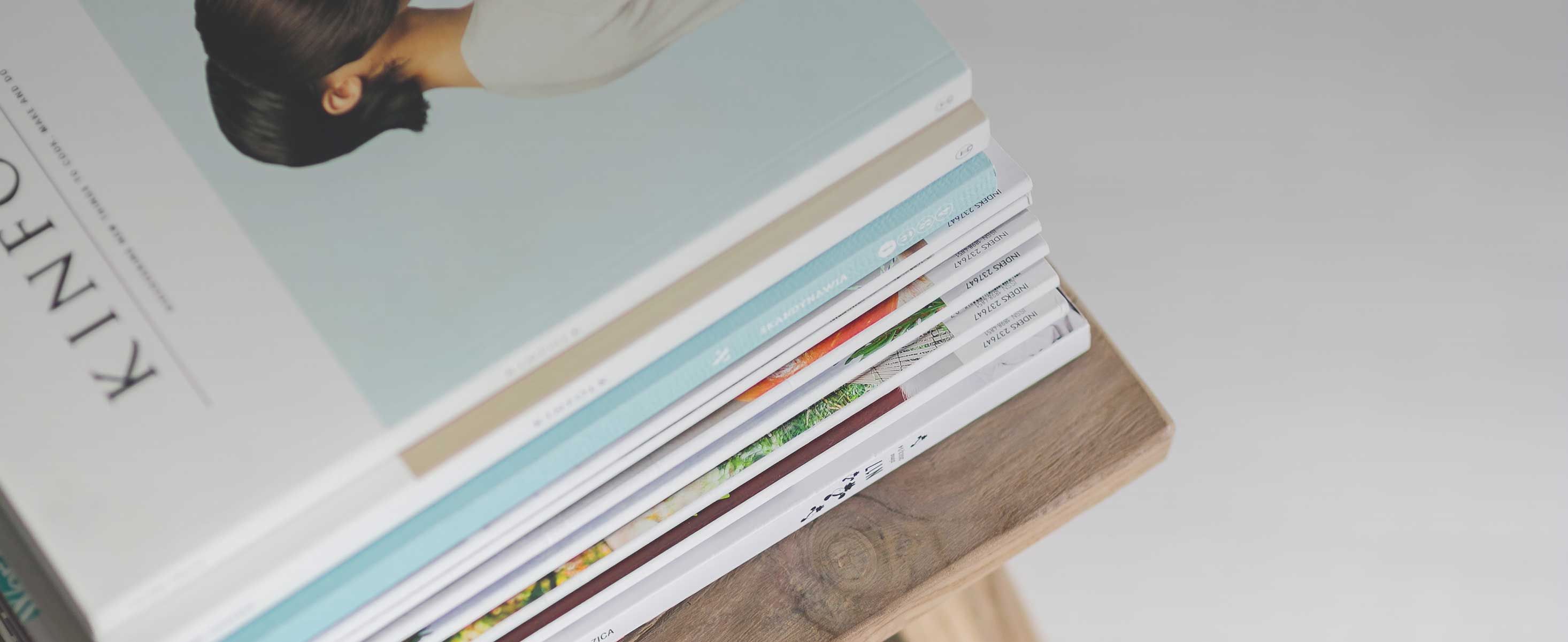
4 minute read
Gamma activation analysis Gamma activation analysis of gold-bearing ores
1 600 000 ore samples per year.
The GAA laboratory in Uzbekistan, equipped with two GAA units, has been in operation for 45 years. It is located in a 3-storey building: on the third floor, containers with samples are loaded into a vertical channel, on the second floor samples are irradiated with a linear electron accelerator, and on the first floor, the induced activity is read with a two-channel spectrometer.
Advertisement
This design stems from the need to reduce the level of background radiation (that appears due to scattered radiation in transport channels where containers with samples are transferred) to permissible values, safe for the personnel.
removal from the accelerator.
Fig. 1 shows the facility with a safety fence; the loading and unloading conveyors are visible. At any point in the safety fence, a dose rate of less than 1 mSv/h is provided. The facility operates in fully automatic mode.
Gamma-ray activation analysis (GAA) has great potential to replace the traditional assay analysis in gold mining, in the future. The essence of the method is the irradiation of ore samples with high-energy gamma quanta generated by a linear accelerator (LINAC), and recording the induced activity of excited gold nuclei by a gamma spectrometer. Main advantages of the GAA method in determining the gold content in ores are as follows:
• The high penetrating power of the accelerator’s gamma radiation with a maximum energy of about 8 MeV allows the analysis of samples of large volume, which eliminates the need for fine grinding of the sample material and significantly increases the representativeness of the analysis.
• Sample analysis time is less than 1 minute.
• Residual induced activity is practically absent, since the half-life of excited gold nuclei is approximately 7.5 seconds.
• The sample material is not destroyed during the analysis, the samples can be analyzed repeatedly and stored to confirm the measurement results.
• The GAA system can be configured to measure elements other than gold, such as silver.
Actually, the GAA method itself was proposed more than 60 years ago, but the first three industrial GAA laboratories first appeared in the Soviet Union in the 70’s of the last century. The experience of operation of these three industrial laboratories showed the uniqueness of the GAA method for analyzing ore samples in the extraction of gold, as well as other precious metals and related elements. To date, of these three laboratories, only the Uzbekistan GAA laboratory (at Muruntau gold deposit) is operating, providing measurement of more than
The “Au-isomer” GAA facility for gold analysis [1] is a continuation and development of those technical solutions that have proven their effectiveness and reliability over many years of applying the GAA method in industrial conditions of gold mines. It has a portable design, owing to the use of a collapsible radiation shield, made of iron. The radiation shield consists of iron blocks weighing no more than 2.4 tons. To assemble the shield, the crane that is part of the facility, is used. For the maintenance of the accelerator, 5 rear shield blocks are removed and the accelerator is wheeled out of the radiation shield. This procedure takes no more than 20 minutes. The facility is mobile: it can be disassembled, if necessary, and moved to another location in several 20’ and 40’ footers. The required time for disassembly and assembly of the facility is 2 and 3 weeks, respectively.
“Au-Isomer” uses the same scheme for moving containers with samples and the same irradiation scheme as in the installations at the Muruntau mine (Uzbekistan). The movement of containers with samples under the force of gravity ensures reliable uninterrupted operation due to the simplicity of the design. Sample containers are round, 45 mm thick, and have a diameter of 110 mm. They are irradiated from the side while rotating, which ensures the uniformity of the absorbed dose of hard gamma radiation by the container’s volume. However, in the “Au-isomer” facility, all equipment is located in a single-storey premises. Owing to the curvature of transport channels and the installation of two fast lead shatters in them, we were able to place the entire structure within a 230 cm high iron radiation shield. The facility has dimensions of 7.1 x 4.5 m and a height of 4.1 m together with a crane designed for the assembly and disassembly of radiation shield (fig. 1). Outside the facility, in separate rooms, there are power supplies of the accelerator and a cooler for heat
A diagram of the facility is shown in fig. 2. Containers with ore samples (300 ml volume) are weighed and marked with a bar code, and then placed on the loading conveyor 2 of the Sample Transportation System 1. At the end of the conveyor 3, the containers stop for reading of their barcode, and then roll down channel 4 to the electron accelerator’s target 5. During irradiation, the containers are rotated by drive 6 to ensure uniformity of dose distribution in the container volume. Channels 4 and 7, like the electron accelerator, are surrounded by radiation shielding. After irradiation, the containers roll down channel 7 to the spectrometers 8 of the Registration System to measure the spectrum of induced activity. After measurement, the containers are lifted by a lifting mechanism 9 for unloading onto the container return conveyor 10, or loading into channel 4 for re-irradiation. The decision to re-irradiate is carried out by the Transportation System control program, which contacts with the signal processing program of the Measuring System if there are not enough statistics (i.e., when the level of signal in the energy irradiation zone of the “Au-isomer” is low). Containers measured a second time will alternate in channels 4 and 7 with containers measured the first time, and the container barcode reading system at the entrance to channel 4 will inform the computer control system about which container went to irradiation.
The time limit regulations of the GAA facility operations for gold are as follows: reading the barcode – 3 sec, moving the container to the irradiation zone after reading the barcode – 2 sec; irradiation – 10 sec; moving the container to the detectors of the Registration System after irradiation – 2 sec; measurement – 15 sec;