CONNECT IONS
Spring 2023
USING DATA ON THE FARM
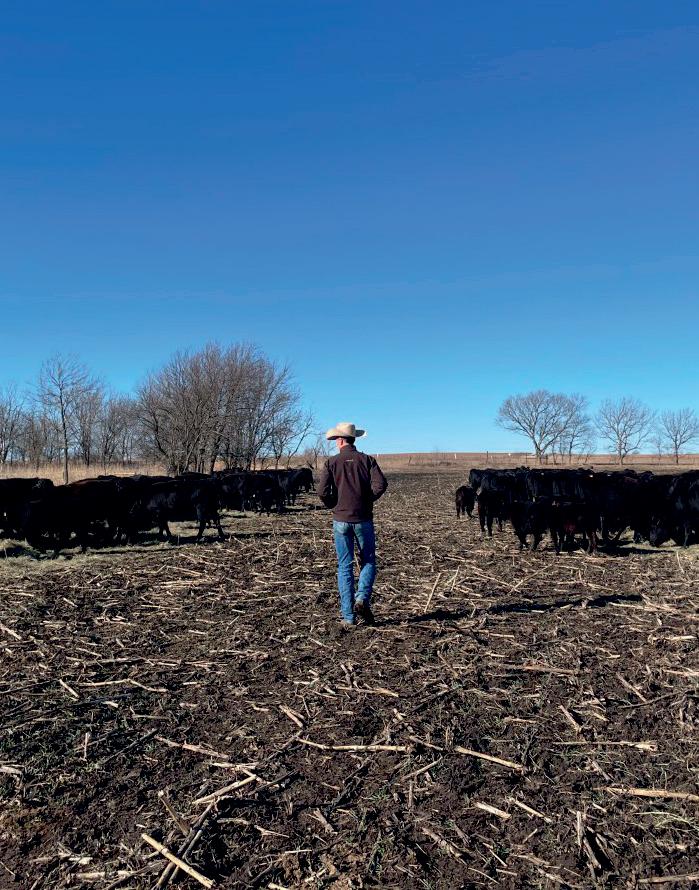
PG. 14
40,000 POUNDS OF MAC N CHEESE
PG. 20
Spring 2023
PG. 14
40,000 POUNDS OF MAC N CHEESE
PG. 20
We help equip farmers with the tools and resources to best protect our soil, water and air.
IN EVERY ISSUE
4 5
22
Straight from the President and CEO Brad Stedman's desk
NEWS BRIEFS
The latest from MKC and its employees
PHOTOS FROM THE FIELD
14 18 20 14 10
FOCUS ON TALENT
What MKC is doing to develop our best in class talent.
USING DATA ON THE FARM
MKC member-owner, Matt Perrier, shared how he partners with MKC on data insights for his farm.
COMING SOON: THIRD RAIL TERMINAL IN KANSAS
An update on the new grain shuttle loader being built in Rice County.
40,000 POUNDS OF MAC N CHEESE
MKC and Land O’Lakes donated 40,000 lbs. of mac n cheese and $10,000 to the Kansas Food Bank.
Mid
Connections
Kansas Cooperative
To create customer, employee and partner success to provide a safe and sustainable food supply.
MKC Vision
Partner with customers to successfully navigate the complexity of modern agriculture and industry.
MKC Values
The success of our business will be determined by our ability to focus on safety, courtesy, image and innovation.
Editorial Staff
Toni Jakes - Marketing and Communications Director
Abby Hartung - Creative Lead
Katlin Allton - Social Media Manager
Management
Brad Stedman - President and CEO
Danny Posch - Executive Vice President and CFO
Dave Spears - Executive Vice President and CMO
Erik Lange - Executive Vice President and COO
Anne Warren - Executive Vice President and CTO
Ted Schultz - Producer Ag COO
Allan Wegner - Chairman
J. Daniel Eakes - Vice Chairman
David Mills - Secretary
Duane Johnson
James Mosiman
Hal Mayer
Ben Schrag
Grant Klingenberg
Mark Davis
Ablackswan event is defined as an unpredictable event that is beyond what is normally expected of a situation and has potentially severe consequences. Black swan events are characterized by their extreme rarity, severe impact and widespread insistence they were obvious in hindsight. In the past, these types of events have certainly been disruptive, but also infrequent. In the past 3 years, we have seen these occurrences increase in frequency. Who could have imagined COVID, domestic political unrest, a container ship jackknifing in the Suez Canal, and a new war in Ukraine to all happen in such a short period of time? On their own, any of these would have caused uncertainty and disruption, but to have them all occurring during this window of time has created disruption many of us have not had to deal with in our adult lives. Volatility has become the new normal, impacting commodity markets, product availability, supply chains, monetary policy, and more.
Market relevance Market relevance is more important than ever in this type of environment. MKC needs to be relevant to our employees, strategic partners, and you, our member-owners and customers. MKC strives to make certain we have the products, resources, and tools available to our member-owners when you need them. If we don’t add value to farmers and ranchers to make them more efficient and profitable, our role as a cooperative is unfulfilled. We also aspire to be an employer of choice. Attracting the best talent possible, providing development and training, and ultimately creating career opportunities for those team members are core objectives for MKC. If we don’t have best-in-class talent, we cannot deliver best-in-class service and remain relevant to you. Finally, we also need to be viewed as a market mover to our strategic partners. They provide us access to products, resources, expertise, global markets, and technology. If MKC is not seen as a partner that can grow markets, we may not have the same access to all those services that help our customers be successful.
Asset renewal is critical as MKC strives to serve member-owners’ needs well into the future. Our board of directors and leadership team works hard to anticipate the needs of farmers and ranchers not only today, but also perhaps more importantly, well into the future. We continue to assess what assets need to be built, where improvements need to be made, and which assets have outlived their usefulness to our customers. These are all difficult decisions that are not made lightly as we consider how to position your cooperative for future generations. Recently, we broke ground on our 3rd rail loading asset in Rice County. This type of investment improves speed and space in the area locally, and gives your grain access to markets domestically and around the globe. To further this investment, we have recently announced our expansion of Producer Ag, our grain marketing JV with CHS Inc. This will allow us to maximize the value of an end-to-end cooperative supply chain in the Southern Plains. This development will expand market access and patronage-eligible options to maximize owner value by connecting area farmers and cooperatives with end-use markets and customers.
Investments in technology are essential to how we transform our business in the future. It’s easy for all of us to think about technology in terms of robotics, drones, and autonomous vehicles. MKC is investing in all of these to be ready for when they are commercially scalable. These are the investments that will help us serve our customers more efficiently in the future. Technology is also related to how we create a better, more consistent customer experience through the continuity of processes and how you access information about your operation and the business you do with MKC. We are utilizing robotic process automation (RPA) to create quicker, more consistent data collection and processing in backoffice functions. This not only reduces errors but also gets information back to you quicker and with more consistency. This technology helps us create more ways for you to do business with MKC and access your information. MKC Connect has over 1200 customers using this new technology in less than a year’s time from when we introduced the App. We are investing in these technologies so we can move at the same pace as you, our member-owners and customers.
We frequently talk about how we need to move faster as a cooperative. Our growth mindset is important to keeping pace with our fastest-moving customers and partners. The size of farm and ranch operations has consistently grown larger and fewer in the past decades. That trend is likely to continue. Supply partners that provide products, resources, and tools to agriculture have grown in size during that time and seek to find retailers with engaged employees that can impact markets. MKC is committed to moving at the pace necessary to be a relevant cooperative for generations to come. Investments in assets, talent, and technology will enable MKC to move quickly as the pace of change continues to accelerate. We appreciate your business and will continue to work hard to earn that business now and in the future. Thanks for the role you all play in agriculture; we’re proud to play a part in your operation.
Member-owners, employees and vendor partners attended our 17th annual Ag Symposium this past December in Newton, Kansas. Continuing with this year's theme of "Shaping the Future Together," attendees heard from industry experts on the topics of trade, policy, farmers of the future and agricultural technology.
Topics and Speakers included:
• After Elections: Impact on Policy - Jim Wiesemeyer, Washington Policy Analyst for Pro Farmer and Farm Journal
• Supply Chain Automation - Kevin Hall, CHS Inc, Vice President of Supply Chain and Continuous Improvement
• 2023 Global Ag & Trade Outlook - Gregg Doud, Aimpoint Research, Vice President of Global Situational Awareness & Chief Economics
For over 10 years, MKC and CHS have successfully partnered together to bring grain assets to the Kansas market to allow Kansas farmers’ grain access to global markets. In 2013, through a joint venture, MKC and CHS invested in building a grain shuttle loading terminal at Canton, KS. In 2017, a second terminal was constructed in Sumner County at Milan, KS and construction on a third terminal in Rice County, KS has begun. This project is anticipated to be complete in the summer of 2024.
In April, MKC and CHS announced the expansion of our current grain marketing joint venture, Producer Ag. This expansion will allow us to maximize the value of an end-to-end cooperative supply chain in the Southern Plains. This development will expand market access and patronage-eligible options to maximize owner value by connecting area farmers and cooperatives with enduse markets and customers. This will provide a link to domestic and international markets for cooperatives and their farmers, including leveraging the Houston TEMCO export facility. TEMCO is a joint venture between CHS and Cargill.
Farmers and local cooperatives will gain access to a wider global market while end-users domestically and internationally gain access to a stronger origination network to source high-quality grains to meet their customers' demands. This holds true to the Producer Ag mission of providing a grain marketing service that links the producer to the end-user giving the greatest value to both parties.
This expanded partnership will drive long-term growth through a responsive grain network and reinvestment to expand marketing opportunities and modernize rail infrastructure in this vital growing region.
“CHS has been successfully partnering with MKC through joint ventures for more than 10 years,” said John Griffith, Executive Vice President, Ag Business, CHS. “This initiative expands our collaborative presence and maximizes our complementary asset base in the region to create an efficient, integrated supply chain to connect cooperativeand farmer-owners in the Southern Plains with customers around the world while leveraging the TEMCO terminal in Houston, Texas.”
“Expanding our relationship with CHS will open up market access and create new opportunities for our farmers,” said Brad Stedman, president and CEO of MKC. “Our track record of successful partnership and shared vision to create value for cooperativeowners and customers makes MKC and CHS the right partners to link farmers with a more defined southern supply chain.”
MKC and CHS will continue to independently own and operate assets throughout the region. We expect operations for this expanded 50/50 joint venture to begin this summer.
WWW.MKCOOP.COM/NEWS/ARTICLES
MKC had the opportunity to attend the Legislative Action Day in Topeka again this January. The event is hosted by the Kansas Cooperative Council, Kansas Grain and Feed Association (KGFA), and Kansas Agribusiness Retailers Association (KARA). Legislative Action Day is a great way for co-op employees, members, and directors to learn more about the legislative process and help lawmakers understand how their actions influence daily operations on the farm and at the co-op.
Agriculture advocacy is an important way that MKC supports their member-owners, employees, and the industry. Chief Marketing Officer, Dave Spears and MKC Board Chair, Allan Wegner, set up meetings with key Committee Chairs and leadership. The team spent time talking with over 45 state legislators about current topics. This includes legislative issues, appraisals on taxes and water issues. At the end of the day, attendees join State Senate and House members at a dinner reception.
MKC is a member of the 3 host organizations of Legislative Action Day. In addition, at the national level, MKC is a member of Agricultural Retailers Association (ARA), National Council of Farmers Cooperative (NCFC), and National Grain and Feed Association (NGFA).
Dave Spears, Chief Marketing Officer, and Jeff Jones, Vice President of Operations, recently joined other ag retailers on the hill. During their visit, they met with Senators and Representatives to discuss current issues in ag, including labor, transportation and supply chain disruptions. Jeff Jones serves on the ARA membership committee and Dave Spears is on the ARA board of directors, the public policy committee chair and an executive committee member.
TEAM MEMBERS WHO ATTENDED LISTED BELOW
Thank you to team members who represented MKC and Producer Ag at this year’s event. Allan Wegner (MKC Board Chairman), Dave Spears (Chief Marketing Officer), Spencer Reames (Operations Director), Adam Butler (Operations Director), Scotty Yerges (Producer Ag Director of Sales), Todd Schultz (Producer Ag Grain Marketing Specialist), Lance Adams (Producer Ag Grain Merchandiser), Casey Jones (Director Operations), Devin Schierling (VP Sales), Kent Nichols (Director of Sales), Ted
HOT Training: MKC and Mid-West Fertilizer operations teams participated in our annual HandsOn-Training. This yearly training ensures employees are equipped with the proper knowledge of hazard monitoring, electrical repair and arc flash safety, grain grading, grain blending, proper grain storage, record keeping and more.
In February we hosted 2 days of grain training for MKC, Mid-West Fertilizer, and Producer Ag team members. Thank you to each of our presenters for sharing their knowledge and ensuring the best customer experience. In the pictures below you can see the team participating in a demo of a grain entrapment rescue and grain grading.
SCAN THE QR CODE TO WATCH THE GRAIN RESCUE DEMO
Over 90 managers for MKC, Mid-West Fertilizer and Producer Ag participated in a full day of Manager Training. All of our subject matter experts were internal presenters. Thank you to them for making this event such a success. We covered topics in safety, sales, DOT training, leadership training, marketing and finance.
At MKC we believe each employee plays an essential role in the success of our member-owners, customers, and your cooperative. Our team members drive the customer experience and add value to being a member-owner. With that, we know it is important to invest in our greatest asset, our people.
Over the past year, MKC has created several new learning and developmental opportunities. This included a redesign of our STEP program and a rollout of our New Manager Training and Leadership Development Associate Program. In May 2023, we launched our apprenticeship program. We have also created new ways to give back to our communities and tell MKC's story to a larger audience through a facility tour program for high school students.
The Strategic Thinking and Execution Program (STEP) is a development program proprietary to MKC that has been running for four years. STEP is for current managers who we recognize as potential senior leaders. This 6-week workshop builds off the existing knowledge of our experienced managers and shifts the focus from day-to-day operations to a more detailed dive into strategic thinking. This shift is all about continued learning and development and doing things with intention, the MKC Way.
Brad Duncan, Agronomy Operations Manager at Manhattan, who participated in our last STEP
program said, “During STEP, I learned how to better communicate the bigger picture to my team, how to get them involved in the process with their own buyin, and how to use that plan to make the best day-today decisions.”
STEP supports our strategic objective to grow talent using continuous employee development as a means to grow our experts and accrue bench strength for when leadership opportunities arise.
Lance Adams, Grain Merchandiser for Producer Ag, also participated in our last STEP program. “I enjoyed STEP; it provided an opportunity to connect with more MKC employees beyond the surface level. We were able to have transparent conversations about real-life opportunities and challenges that we as leaders are working through.” Adams said, “Those conversations helped to gain context, get ideas, and then we were held accountable to coming back the next meeting to discuss how some of those crucial conversations or decisions went.”
New manager training was developed to ensure that the employees that were promoted into management roles for the first time, as well as the managers that we've recently hired, would have the opportunity to gain knowledge and skills we feel are necessary to be a successful manager at MKC.
Over a four-week period, these managers gain a foundation of skills to improve their transition into management roles. The focus is on best practices and our processes, with additional time spent on the impact our managers have on employees' job satisfaction.
Kristina Zerger, Assistant Agronomy Manager at Haven, spoke about her experience going through the training and how she uses it in her day-to-day role.
“Working one on one with employees and the onboarding process has been an improved experience for both employees and managers since the training. One quote that I have taken from the training is ‘What we Permit, we Promote.’ This has been something that I have thought about while working with the team relating to MKC’s four keys and people management”
Caydren Cox, past LDA and current Walton Grain Operations Manager said this about his time in the program, “LDA allowed me to spend time with many different managers, so I experienced many different management styles. I was able to see things that I wanted to incorporate while in a management position. There were countless learning opportunities that took place in my LDA experience and much of that knowledge I use on a day-to-day basis.”
DO AS WELL AS MKC.” - Tyler Cloud, Past LDA
MKC’s Leadership Development Associate Program (LDA) was created to help guide employees who are evaluated to have potential in leadership but are uncertain about their best career paths with MKC.
While in the program, associates go to multiple locations to work under various managers and learn different operations roles. This allows participants to gain a broader understanding of how MKC works and build relationships across many departments.
Tyler Cloud, past LDA and current Plains Assistant Agronomy Operations Manager, said, “The LDA program has been a big help [in my career] by showing me all the different parts and keys of MKC. That's an opportunity I don't think many places can offer or do as well as MKC.”
This program lasts nine to twelve months and after completing all pieces of training, associates are able to apply for a management position, as placement in a
"THE LDA PROGRAM HAS BEEN A BIG HELP [IN MY CAREER] BY SHOWING ME ALL THE DIFFERENT PARTS AND KEYS OF MKC. THAT'S AN OPPORTUNITY I DON'T THINK MANY PLACES CAN OFFER ORPICTURED ABOVE: THE FIRST GROUP OF NEW MANAGER TRAINING ATTENDEES
role after the program is not guaranteed. So far, the LDA program has a 100% placement for those who have completed all aspects of the program.
MKC recently announced the launch of an apprenticeship program to hire agricultural equipment operators, CDL drivers and operations specialists through Kansas Farm Bureau’s (KFB) Rural Kansas Apprenticeship Program. This is the first agricultural apprenticeship program in the state of Kansas.
“This apprenticeship program formalizes the training and opportunities for career growth that have existed at MKC for years. We believe that clarifying our commitment through this opportunity provides people with or without agricultural
experience a clear path to a rewarding role in our organization.” – Anne
Anderton Warren, Executive Vice President & Chief Talent Officer, MKC.The program is designed to provide on-the-job training and technical instruction to employees hired into specific entry-level operations positions, regardless of an agricultural background.
In the fall of 2022, MKC created a multi-location tour focused on showing local high school students career options in agriculture. The tour visits three of our locations: the MKC Agronomy Hub in Groveland, the Shuttle Loader and Grain Terminal in Canton and the MKC Safety Center in Moundridge. While at Groveland, students learn about agronomy and technology, at Canton they
"THIS OPPORTUNITY PROVIDES PEOPLE WITH OR WITHOUT AGRICULTURAL EXPERIENCE A CLEAR PATH TO A REWARDING ROLE IN OUR ORGANIZATION.” –
Anne Anderton Warren, Chief Talent Officer
learn about food safety and storage and at the Safety Center agricultural safety is the focus.
Hilary Worcester, Manager of learning and development, said, “We want as many students as possible to have an ‘MKC experience’ to widen their view of agriculture careers and better understand what happens at our facilities they see from the road.”
We worked with FFA chapters, counselors, and teachers across the state to ensure our tour showcased MKC and has activities that relate to their FFA or scholastic focuses to have maximum impact on the future by being relevant for them now.
Currently, over 150 students have experienced this tour, and we look forward to the continuation of this program as it embodies our tagline “Shared growth, Shared success.”
TO SIGN UP FOR A FACILTIY TOUR SCAN THE QR CODE BELOW
TO READ THE FULL APPRENTICESHIP PRESS RELEASE SCAN BELOW
PICTURED LEFT: THE FIRST GROUP OF LDAS WITH THEIR MENTORS.
PICTURED RIGHT: A GROUP OF HIGH SCHOOL STUDENTS GOING THROUGH A TOUR IN OUR CANTON AND GROVELAND LOCATIONS.
This past February, Matt Perrier invited us to his ranch, Dalebanks Angus. We met on a beautiful sunny day after Matt finished his morning chores. After offering a cup of coffee and showing us the shop where they host their annual sale, we headed out to visit his herd. Matt shared the history of his farm and how he works with Kent Nichols, Director of Sales, and the MKC team.
Dalebanks Angus is a fifth-generation ranch in Eureka, KS. The name was not a family name but was the name of his ancestor’s farm in their home country, England. The farm and ranch has a long history in Kansas. Matt’s grandmother’s family originally settled on the farm in 1867. Initially, it was a sheep ranch, but in 1904 the first registered Angus cattle were brought to the farm. They’ve had registered Angus on their operation ever since.
Dalebanks Angus is now owned by the Perrier family. “The main focus of the farm is to raise good balanced trade bulls for the commercial cow producer that’s trying to find practical profitable genetics for their cow herd,” Matt explained. “We also sell some top-end genetics to other Angus breeders and AI companies.”
Matt, his wife, Amy, and both of Matt’s parents, Carolyn and Tom, are involved with the ranch. Matt oversees the cattle management and his dad, Tom, oversees most of the farm management. Matt and Amy’s children are beginning to show interest and help around the farm.
Dalebanks Angus has close to 500 head of registered Angus cows. In addition, they plant corn, wheat, soybeans, and a grazing mix. Most of the crop production is to feed his herd.
“We try to run our cows as close to a commercial cow-calf management system as possible and let them graze all the forage they can,” states Matt. “These cows are out on forage 12 months of the year, and they don’t ever go into a confined dry lot. In the spring, summer, and early fall, they will be grazing.”
Like nearly all farm and ranch families, the Perriers are working to make their operation sustainable for the next generation.
“The cattle primarily graze on native tallgrass prairie pasture, but that’s only good about 90 to 120 days of the year,” says Matt.That’s where we’ve used cover crops and perennial cool season grasses to extend that grazing season. Often, we put cattle on corn stock residue and fall planted cover crop cocktails with cereal grains and peas to offset the cost of delivered feed. Hopefully, it results in better soil health and will keep cows on pasture or grazing crop fields throughout the year.”
Matt works with MKC to service his needs for seed, crop nutrients, application and technical assistance. A few years ago, MKC conducted grid sampling on the ranch and put together a nutrient and application plan for the next several years.
“Technology and data are important to us so we have gravitated towards companies that can provide not only products but also answers and good unbiased information,” Perrier shared. “That is where MKC fits really well for us.”
On the cattle side of the operation, they collect 50 to 75 pieces of information on each animal by the time the animal is a year of age. That information is sent to the American Angus Association for analysis. It helps Dalebanks Angus make the right cattle selections and helps their customers select the right genetics for their operation. They have used data like that on cattle for more than 60 years.
On the farm side of the business, they have not invested in data the same way. The main income for the ranch is the registered Angus herds, not cash crops so that changes their investment and magagement plan.
“We’re not nearly as good at analyzing that data. We aren’t set up to use a lot of precision ag. We don’t have GPS on tractors, which I’m sure most people would find unbelievable, but that’s where we’ve been able to use some of the services that Kent and the MKC precision team have to offer. In having someone else do that grid sampling and using MKC’s technology to apply fertilizer and nutrients,we can get the most bang for our buck,” Perrier says.
Matt noted that with most of their planted acres used for grazing, they don’t usually harvest those crops. That is the reason their combine is not set up with any yield monitors or similar equipment.
“With so few acres that we have on the agronomy and farm side we just haven’t seen that it is efficient or economically viable for us to outfit a bunch of old equipment with the yield monitors and GPS,” says Matt.
The day of our visit Matt showed us his fall cow-calf pairs. We asked him to tell us a bit more about their feed plan.
“In September, we harvested hay on one of our fields but left the bottom leaf on the sudan and millet plants. We bailed that and allowed it to regrow through the late summer and early fall. Then post frost, we put the fall cow-calf pairs on dormant warm season cover to graze for about three weeks to a month.” Matt shared, “We try to strip graze to get the max grazing out of it. Now they’ve been grazing both that native dormant grass, corn stalks and the green fall planted cover.“
Now they are supplementing the feed with both native grass hay and 30% protein cube. The main goal on the soil health side is that they are adding nutrients back onto the field and the cows are doing their part by adding nutrients back on themselves.
“We as beef producers are going to have to continue to find ways that allow us to reduce our costs and a big part of that is going to be feed, labor and equipment. Using a pickup to haul the nutrients our cattle need or using any other equipment that burns diesel fuel or gasoline is an added cost.” Matt stated, “I think that’s where grazing as much forage as we can in the fall, winter and spring, at least in this region, pays bigger dividends than we realize because not only are
we hopefully saving some money by not having to purchase feed, but we’re also saving money by not delivering it.”
Matt talked about the topic of sustainability. “A certain amount of [sustainability] has a financial component and when we can save money on fuel and put the carbon back into the soil by letting that cow be a natural harvester, digester, and fertilizer spreader allowing her to follow the natural cycle that I think we as beef producers can tap into.”
Matt believes there are many opportunities for sustainability if farmers and ranchers can get past the thought that, “this is farm ground and this is pasture. And never the two shall intertwine or meet.”
“That’s what we’re trying to do is meld those together and find times that it makes more sense to have cows on farm ground = grazing and recycling some of those nutrients. There’s a lot of opportunities and I think it’s just a bit of a paradigm shift and you lose some control,” says Matt.
On the farm side growers can anticipate what a corn, soybean or wheat plant is going to do year after year to a certain extent.
“Cover crops especially when we’ve got four or five or 10 different seeds that we’ve put into the ground, it’s different,” Matt said. “Every year we plant these cover crops, some years we’ll get a bunch of turnips some years we’ll get a bunch of cereal grains and we don’t even think we planted turnips. You have to be ready for an audible whenever you start using cover crops especially for grazing because it’s not always going to be the same. You’re not always going to get the same production. But I think generally if you are patient, you’re going to be able to capitalize on some pretty cheap grazing and hopefully benefit the soil as well.”
In addition to the ranch, Matt has also been involved in leadership roles with several organizations, serving as President of the County Farm Bureau, County Cattlemen’s Association, Kansas Livestock Association, and Beef Improvement Federation. He has also served on a few other boards outside of agriculture.
Matt also has a podcast, Practically Ranching. Matt had grown frustrated with the amount of negativity that he sometimes saw at the local sale barn or coffee shop or social media. It seemed like farmers, ranchers and beef producers were mad about things like markets, regulations, producer associations and political stances. He was noticing they would express that anger without a solution. He was sensing a lack of point and counterpoint discussion, civil discourse amongst farmers and ranchers and he wanted to bring an opportunity where two people with possibly sometimes opposing views on a certain issue or set of issues, could talk through them and allow the world to listen in. He wanted the conversation to be like two people sitting at a lunch table talking about two or three issues every other week.
Matt says, “I’ve had fun with it. I’ve learned a ton. It takes some time to do them, but I’ve probably spent time in less productive ways.”
He chose to do a podcast to make it more accessible for listeners.
“Let’s face it, it’s tough when you’re running cows, or running a farm to leave that place and go to a meeting and hear about current trends and topics and issues that really need to be sorted out. And at some of these meetings, you just hear it from one person and then you go home, and you don’t have a chance to kind of talk with other people.” Perrier notes.
With a podcast listeners can join while feeding cows in the morning or sitting in the tractor drilling cover crop or planting or harvesting or taking a load of beans to the to the terminal. The episodes are 45 minutes to an hour with two or three people discussing a topic. Some of the topics are pretty deep, others are more lighthearted, some are informational or focused on tech topics.
To learn more about Dalebanks visit www.dalebanks.com by scanning below.
MKC, in partnership with CHS Inc., broke ground on a new grain shuttle loader near Sterling, Kansas in December of 2022. Located in Rice County, the facility will include a high-speed shuttle loader with access to rail on the K&O Railroad. Upon completion, on-site storage will be approximately 5.2 million bushels.
“This is MKC continuing to build out the infrastructure for the future of the Kansas Farmer. While some of our older assets are nearing their end-of-life stage, MKC continues to improve vital country elevators in the core of grain-producing areas. We're backing up those facilities with modern rail assets. Investments such as this rail terminal expand the cooperative system’s ability to deliver our farmer’s grain to various parts of the world, returning greater value to local farmers and local communities.” -
Erik Lange, Chief Operating Officer MKC.The new facility will have 3 additional truck pits with the capacity to receive 30,000 bushels of grain per hour each. With current and new capacity, we can receive grain at approximately 150,000 bushels of grain per hour. The facility can ship out grain at 90,000 bushels of grain per hour.
Jon Brown, Director of Facilities Management, said, “You can throw pretty much any scenario at this elevator – fall harvest, different commodities, and we're still moving grain at a very high speed.”
In addition to the truck pits and rail system, there will also be a bunker able to receive 30,000 bushels an hour. Meaning, this facility will be able to receive a total of 180,000 bushels per hour.
The project is expected to create new jobs during construction and operation. By the end of 2023, the elevator will look complete from the outside but will have internal work to be done. This project is slated to be completed by June 2024.
Hunger relief is one of the core pillars for donations, sponsorship and community outreach for MKC. We host an annual food drive to collect nonperishable food items for the food pantries in our communities. Over the last several years, we have collected over 100,000 lbs of food and provided over $100,000 in monetary donations. This year, as a member-owner, MKC had the opportunity to partner with Land O’Lakes through their first run mac and cheese program. This allowed MKC to secure a donation to the Kansas Food Bank of 40,000 pounds of first run mac and cheese. First run means that the product was produced fresh for this donation. Oftentimes, food donations are products that have been on shelves elsewhere before making it to the food bank.
“Last year, the Kansas Food Bank provided more than 13.6 million meals to Kansans struggling to put food on the table,” said Brian Walker, President and CEO of the Kansas Food Bank. “It is because of donations and partners such as Land O’Lakes that we are able to provide those missing meals for families, children and seniors who turn to us for help. We are truly thankful for this donation and opportunity to be a recipient of the First Run Program.”
“This is an opportunity for us to assist the Kansas Food Bank that provides hunger relief to many people within our footprint,” says Brad Stedman, President and CEO of MKC, a member-owner of Land O’Lakes. “We are committed to addressing food insecurity in the communities we operate and proud to support our local food banks.”
MKC also made a $10,000 monetary donation to the food bank. Having the opportunity to provide hunger relief to many within the MKC footprint was an honor.
The Kansas Food Bank is the primary source of food for over 700 hunger-relief agencies in the 85-county service area. These agencies include food pantries, soup kitchens, shelters, after-school programs and senior delivery programs. The Wichita Cargill Cares Complex is the central collection and distribution facility for this food. Working with Feeding America’s network of food distributors, the Kansas Food Bank receives millions of pounds of donated food product. This inventory is further supplemented by what is collected through local food drives, food recovery programs, and food purchased at steeply discounted rates. Drawing on these multiple sources, the Kansas Food Bank is able to offer hunger-relief agencies a nutritious variety of non-perishable and fresh food items. The agencies then use the food to supply pantries, food box distribution programs and on-site feeding programs. Kansas Food Bank pantries serve over 945,000 people annually.
The Kansas Food Bank invited the MKC team to the Cargill Cares Complex for a tour and to share more about what they do. A few team members visited the facility and saw the 40,000 pounds of frozen 5lb bags of mac n cheese. The warehouse had large temperature controlled rooms to house refrigerated and frozen food items.
In addition to storing these products, the team prepares them for distribution locally and for delivery.
While touring the impressive building, the team met a few volunteers, including a retired couple who volunteers weekly. Another group spent a few hours packing boxes to go home with school children as part of the Food 4 Kids program.
Interested in helping the Kansas Food Bank? They accept food donations, monetary donations or the gift of your time. To learn more visit, kansasfoodbank.org/howto-help
PICTURED ABOVE: CEO BRAD STEDMAN AND BRIAN WALKER, CEO OF KANSAS FOOD BANK.
LEFT: PALLETS OF MAC N CHEESE INSIDE THE CARGILL CARES COMPLEX.
BELOW: A KANSAS FOOD BANK EMPLOYEE TAKING A LOOK AT THE 5 LB BAGS OF MAC N CHEESE.
www.mkcoop.com
www.mkcoop.com