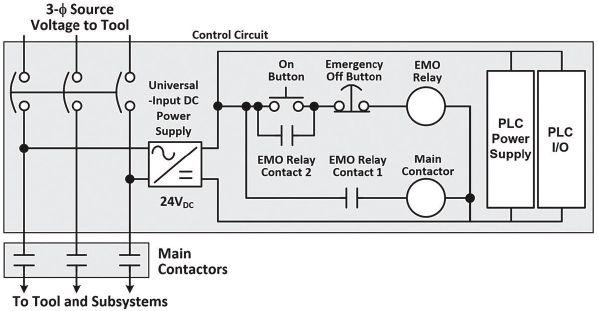
4 minute read
Understanding power quality and improving manufacturing system reliability
Mark Stephens and Alden Wright, EPRI
Improving power quality
Advertisement
Design options for industrial controls can provide built-in robustness to voltage sags. The controls already have capabilities installed and don’t require after-the-fact voltage sag mitigation for defense against the effects of voltage sags.
Parts 1 and 2 of this article series explained and described the origins of industrial process sensitivity to power quality (PQ) events, or variations in the electrical power supply – specifically, voltage sags – as well as retrofit methods of mitigating those variations and help sensitive processes remain operating despite those events.
Main shutdown cause: Sags
Voltage sags are the main culprit involved with industrial process shut down incidents – the 120-volt control circuit being most sensitive to voltage sags. Most voltage sags have sag magnitudes (voltage remaining) at or above 50% of nominal with durations at 0.5 seconds or less. Within the control circuit, several individual components common to most controls could be causing the controls, and thus the process, to shut down. These components are often the PLC, its I/O, dc power supplies, ac “ice cube” relays and contactors, and adjustable speed drives. Allowing the control circuit and the process to ride through voltage sags involves mitigating one or more component’s sensitivities to voltage sags or propping up the voltage of the control circuit for the duration of the voltage sag. While the latter may be accomplished using a battery-based uninterruptible power supply (UPS), these require regular maintenance checks and full battery replacement after three to four years for lead-acid batteries. Newer technologies such as lithium-ion-based UPS units tout battery lifespans in the seven to eight-year range. “Battery-less” mitigation options need little or no maintenance, operate better in elevated temperatures, and do not require battery replacement. These may operate for 10 to 15 years.
Control circuits may be designed to be more robust by requiring the incorporation of voltage sag standard-compliant components – SEMI F47 or IEEE Std 1668, or by requiring through the purchase order the entire process be compliant to those standards without requiring a battery-based UPS to maintain. The controls may be most robust by using only dc components supplied by a three-phase, universal-input dc power supply operated at the highest input voltages in its range, and at less-than full load.
By keeping the control voltage up, the RUN signal to an ASD may be maintained, yet the drive may shut down for dc bus undervoltage. Most modern drives have adjustable parameters that may allow the drive to ignore the voltage sag for a period of time until full input voltage returns if enabled. These parameters may not be enabled by the manufacturer.
Several methods of improving the voltage sag sensitivity of industrial controls can make industrial process more robust to voltage-sag effects. ce
M
More
ANSWERS KEYWORDS: power supplies,
voltage sags
Design options for industrial controls can provide built-in robustness to voltage sags. ONLINE This article online has links to parts 1 and 2 of this series, 3 other figures and more on: -Effective use of existing PQ standards -Use of robust dc power supplies, ac components -Adjusting ride-through parameters on motor-drive systems CONSIDER THIS How much could more reliable automation power quality save?
Figure: Example of a universal input dc control circuit design. Courtesy: EPRI
Mark Stephens isprincipal project manager; Alden Wright is technical leader, Electric Power Research Institute (EPRI). Edited by Chris Vavra, associate editor, Control Engineering, cvavra@cfemedia.com.
PQ issues and uptime
• Understand your PQ Environment –
Prescribe solutions that fit your situation • Don’t assume battery-based UPS systems are needed; there are other technologies • Avoid use of sensitive ac components in controls • Embed robustness using ac- or dc-based controls that are compliant with IEEE 1668 or
SEMI F47. • Utilize voltage sag ride-through settings in your motor drive systems. http://mypq.epri.com has tips to mitigate voltage sags in industrial automation systems.
Calling all system integrators...
System Integrator of the Year Awards

Entries are due September 4, 2020
Who should enter?
If you’re a system integrator with demonstrable industry success, Control Engineering and Plant Engineering urge you to enter the 2021 System Integrator of the Year competition. Past System Integrator of the Year winners—Class of 2020, Class of 2019, and Class of 2018—are not eligible to enter the 2021 System Integrator of the Year program.
What’s in it for the winners?
The chosen System Integrator of the Year winners will receive worldwide recognition from Control Engineering and Plant Engineering. The winners also will be featured as the cover story of the Global System Integrator Report, distributed in December 2020.
How will the competition be judged?
Control Engineering and Plant Engineering’s panel of judges will conscientiously evaluate all entries. Three general criteria will be considered for the selection of the System Integrator of the Year: • Business skills • Technical competence • Customer satisfaction
Questions?
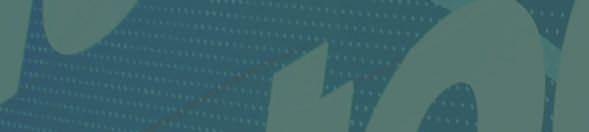

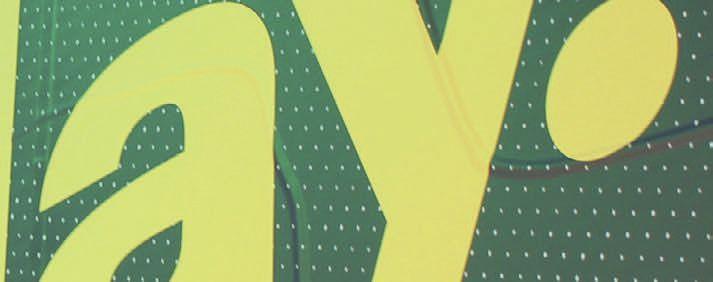
Contact Tom Magna System Integrator Marketing Consultant CFE Media tmagna@cfemedia.com
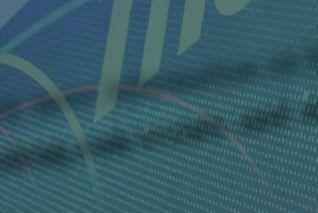
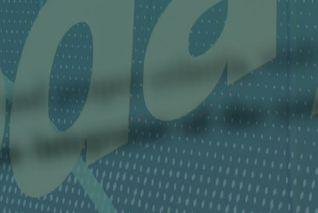
