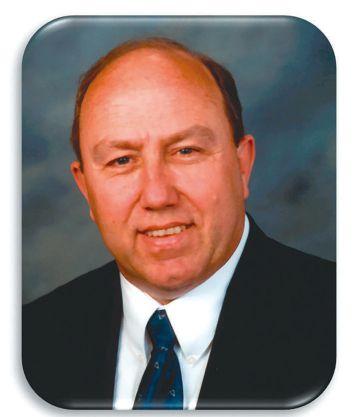
6 minute read
Motor repair answers at Virtual Training Day; More online training; Control and automation program- ming languages: View from the field; Headlines online
Motor repair answers: Virtual Training
Trends on motors and drives were covered in the CFE Media & Technology Virtual Training Day on Aug. 19, providing online training; the instructor for one of the courses answered additional questions about motor repairs. Four courses offer potential for four approved learning units:
Advertisement
• What to know when repairing electric motors • How to specify motors for more efficient HVAC systems • Introduction to motors and drives • How to design hospital, health care facility HVAC systems.
Motor repair application, motor designs, motor detective stories
Thomas Bishop, PE, senior technical support specialist, EASA, gave 45 minutes of instruction on motor repairs followed by more than 15 minutes of questions and answers. The information will be available at www.controleng.com/online-courses until Nov. 30, 2020. Answers to unanswered questions follow.
Are there certain applications that have particular motor repair concerns?
Applications with higher than normal mechanical stress or in harsh environments may require additional repair steps. For applications with higher stress, such as a rock crusher, mechanical components such as the shaft need closer inspection to check for bending or cracks. Harsh environments such as outdoors near the ocean with its salt water can lead to extensive corrosion damage. Applying overcoating with epoxy materials would probably be called for to reduce the effects of corrosion.
Thomas Bishop, PE, is senior technical support specialist, EASA. He offered information about motor repairs in a Aug. 19 one-hour course available for viewing until end of November 2020. Courtesy: CFE Media and Technology and EASA
a popular misconception is that motor design life has also increased. However, the factors that affect motor thermal life, such as winding temperature, for the most part haven’t changed; and the bearings and mechanical systems are still the same.
Can you share a useful “detective story” about motor repairs?
An end user had a motor in a centrifugal pump application and when it required service center repairs, it was found the shaft had a crack in it. The pump application would not have caused a mechanical shock that could explain the cracked shaft, and the next suspicion was the shaft material had an inherent flaw in it. A root cause analysis (RCA) was performed and what was found was the motor had been used in a severe mechanical shock application, a shredder subject to overload, and that the crack occurred in that prior application. ce
IIoT platform built on battery-free sensors
Do more recent motor designs extend motor life over earlier generations? How?
The short answer is “no.” As energy efficiency of motors has increased,
Many analysts have predicted an explosion in the number of Industrial Internet of Things (IIoT) devices that will come online over the next decade. Sensors play a big role in those forecasts. Unfortunately, sensors come with their own drawbacks, many of which are due to the limited energy supply and finite lifetime of their batteries. Everactive, a startup company founded by MIT graduates, has developed indus‘A sensor to monitor rotating machinery, like trial sensors that run around the clock, motors and pumps, runs require minimal maintenance, and can last over 20 years. The company created the on second-generation sensors not by redesigning its batteries, but by eliminating them altogether. Everactive builds finished products on top of its chips that customers battery-free chips.’ can quickly deploy in large numbers. Its first product monitors steam traps, which release condensate out of steam systems. Such systems are used in a variety of industries, and Everactive’s customers include companies in sectors like oil and gas, paper, and food production. Everactive has also developed a sensor to monitor rotating machinery, like motors and pumps, that runs on the second generation of its battery-free chips. - Zach Winn, Massachusetts Institute of Technology (MIT).
Control and automation programming languages: A view from the field
I read the article on “Which programming language is best.” Control Engineering, July 2020 had Which IEC 61131-3 programming language is best? Part 1, and August 2020 has Which IEC 61131-3 programming language is best? Part 2.
I would like to give you some info I realized working as an electrician and control engineer. During program design, the engineer only sees it once. In the field, the electrician or controls engineer sees it thousands of times.
Company standards for programming
Each company I worked for (U.S. Steel and Ford Motor Co.) have standard forms of programming which should be followed so the those in the trades are familiar with the scheme. Also, it’s easier to program control loops in ladder logic, but very hard to troubleshoot this program.
Not all control engineers or those in the trades are created equal so some pickup on things differently. I like sequential function charts (SFCs) and
Online training for continuing education credits: Virtual Training Week
Five days of online training are planned for Oct. 5 to 9 for 30 continuing education credits from CFE Meda and Technology, owner of Control Engineering, Plant Engineering, Consulting-Specifying Engineer and other recognized industry educational resources.
Five consecutive days of training include industry experts, videos, research and panel discussions and question and answer opportunities. Topics are digital transformation, motors and drives, predictive maintenance, critical power, and innovative automation. A best practices session will start at 10 a.m., research or roundtable panel will be at noon, and an application will be at 2 p.m., central time. Daily details follow. Oct. 5, Monday: Disruptive Digital Transformation: Why and How Attendees will hear from industry experts, leading manufacturers and research analysts to learn how to scale a digital transformation strategy. Oct. 6, Tuesday: Motors and Drives Training Hear from experts in the industry to learn about best practices for motors, drives, and applications related to energy management. Oct. 7, Wednesday: Preventive and Predictive Maintenance Thought leaders in manufacturing and construction will discuss how software can reduce mistakes and increase productivity. Oct. 8, Thursday: Critical Power: Electrical Safety and Standby Power Experts in the electrical engineering field cover best practices for designing electrical rooms and standby power requirements. Oct. 9, Friday: Innovative Automation: Control Systems, Drives and Motors Leading manufacturers, distributors, and those involved in applying innovative motors, drives and control systems cover advancements in product design and features.
Learn more and register at www.controleng.com/online-courses.
function block diagram (FBD) programming but it was not used in some facilities because those in the trades didn’t understand it. When you see it for the first time when the equipment is down you are confused, and on-the-job training (OJT) is very expensive.
Programmer should communicate with operations
The programmer should contact the control engineers and those in the trades at the facility where the equipment is going to see what they are comfortable with. I know that isn’t always possible. Writing logic and troubleshooting it are very different. In the field you have to get into the programmer’s head to understand the programming technique used, which can be difficult at times. Just a few thoughts on the article. Thanks. ce
John Damasiewicz is a retired controls engineer with Ford Motor Co. Edited by Mark T. Hoske, content manager, Control Engineering, CFE Media and Technology, mhoske@cfemedia.com.
Headlines online
Top 5 Control Engineering articles August 10-16, 2020
Featured articles included edge computing and IIoT, automation helping the COVID19 pandemic response, system integration, and message queuing telemetry transport (MQTT).
How a COVID-19 testing trailer was built for a university
MIT engineers and medical staff built a 60-foot trailer for COVID-19 testing that can test up to 1,500 people a day and is now operating as the main test site for asymptomatic members of the MIT community.
Global AI market projected to have strong growth
The AI is expected to show strong growth in all world regions in spite of the COVID-19 pandemic according to ARC Advisory Group research.