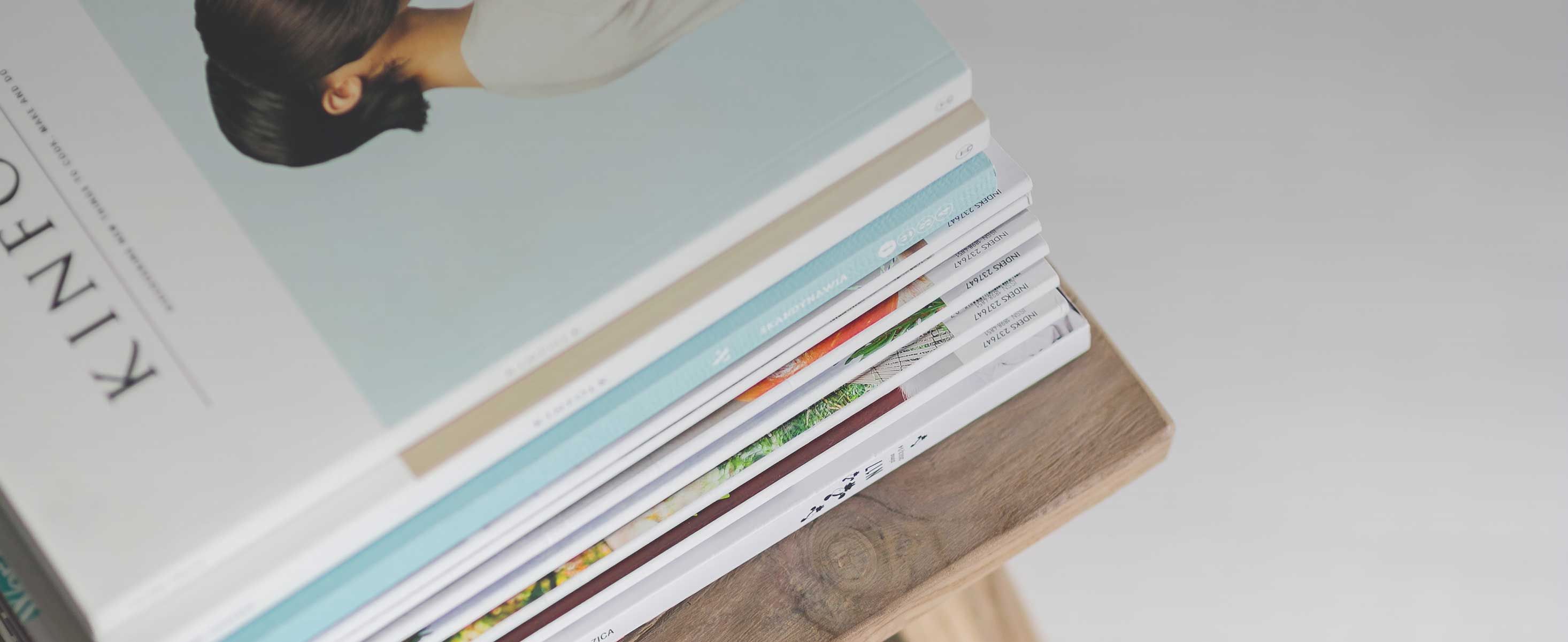
4 minute read
International: Flexible process control
Ralf Jeske, ABB AutomationRalf Jeske,
Flexible process control systems
Advertisement
An alternative modular automation approach to large-scale automation systems is emerging.
M
More
Modularization breaks down systems, plants, processes, and unit operations into standard, modular components, much like those popular children’s building bricks that can be mixed and matched freely to make any number of different creations. The concept centers around the pre-fabrication of specific and complete operational packages, which include the automation to control them. The ease of assembly this brings has led to major reductions in on-site work time, complexity and a reduction in the possibility of error. As a concept, modular automation has been around for some time, with construction and shipping industries among early adoptors. Until recently, use was confined to a small number of examples in process industries, with no large rollouts. With advances in the automation technology that controls mechanical industrial equipment, modular automation has become easier to integrate into existing systems, widening adoption for use in industrial production lines. This is a big change from the large-scale plant-wide automation systems that have been at the heart of production line control for decades and are designed to supervise and control entire production plants. The aim is to modularize common unit operations into packages to allow customizing of both the products made and the production quantities, giv-
INSIGHTS ing major competitive advantages in terms of KEYWORDS: process control, process equipment assembly flexibility and time to market. The concept also allows rapid changes in deployment of production assets, to make specific product Modular automation has types and volumes when and where needed. become easier to integrate into existing systems. NAMUR as a catalyst, MTP Module type packages Helping to move modular automation(MTP) for building modular automation capability into a process module can be forward is done by NAMUR, an international user association based in Germany that integrated. focuses on automation technology and digiAutomation will be talization in process industries. NAMUR has distributed where needed led the fundamental efforts to develop stanin the future rather than at a fixed location. dards which serve as a base for modular automation to be built upon in industrial plants. ONLINE It sees increasing flexibility of production More about scalability plants, using modularization, as a key tool to in greenfield and retrofit applications with this article at www.controleng.com. CONSIDER THIS What do you see as the future for process control and meet fast-changing market demands, especially for chemicals and pharmaceuticals. A few years ago, NAMUR introduced the module type packages (MTP) standard for building modular automation capability into process manufacturing? a process module (or PEA, process equipment assembly). The PEA includes the combined mechanical equipment and controller, and uses an MTP interface, which contains a vendor-neutral and functional description of the process module automation and can be generated by the engineering tool of the module.
Through a simple import of the MTP into the process control engineering of the production plant, the module can be integrated. This is described in the standard VDI-2658, developed in Germany and being adopted as IEC 63280 for automation engineering of modular systems in the process industry. Using PEAs takes less time and on-site work to deploy production lines and equipment. With automation already integrated into the mechanical production equipment, as MTPs within the PEA, deployment to get it running onsite is not difficult. Flexibility to meet rapid changes in market demand has been a major driver, especially for the pharma and biopharma sectors where it is becoming common to make very small batch quantities of highly specialized products and medications. For highly-targeted individual treatments, for cancer patients for example, the batch size can even be as small as one specific medication or formula.
Pilot trials at Bayer AG
Bayer AG, a life sciences company, successfully conducted a pilot study based on an MTP control sub systems and a modular configuration tool, running with a modular-enabled system for the orchestration. This is the world’s first commercial modular-enabled process automation solution, and Bayer has publicly stated that it sees it as a first step in moving from monolithic automation systems covering the complete production plant to a more flexible and market-oriented plug and produce solution.
The modular automation sector now is using the term “numbering up” capacity instead of “scaling up,” reflecting the number of PEAs put into service to meet demand. The modular, flexible approach allows both regional redeployment as well as product-specific redeployment. This clearly offers much greater flexibility than would ever be possible using the large, fixed-plant infrastructure that most industrial processes are built upon today. ce
Ralf Jeske is global product manager for ABB Automation, Germany. This article originally appeared on Control Engineering Europe’s website. Edited by Chris Vavra, associate editor, Control Engineering, CFE Media and Technology, cvavra@cfemedia.com.