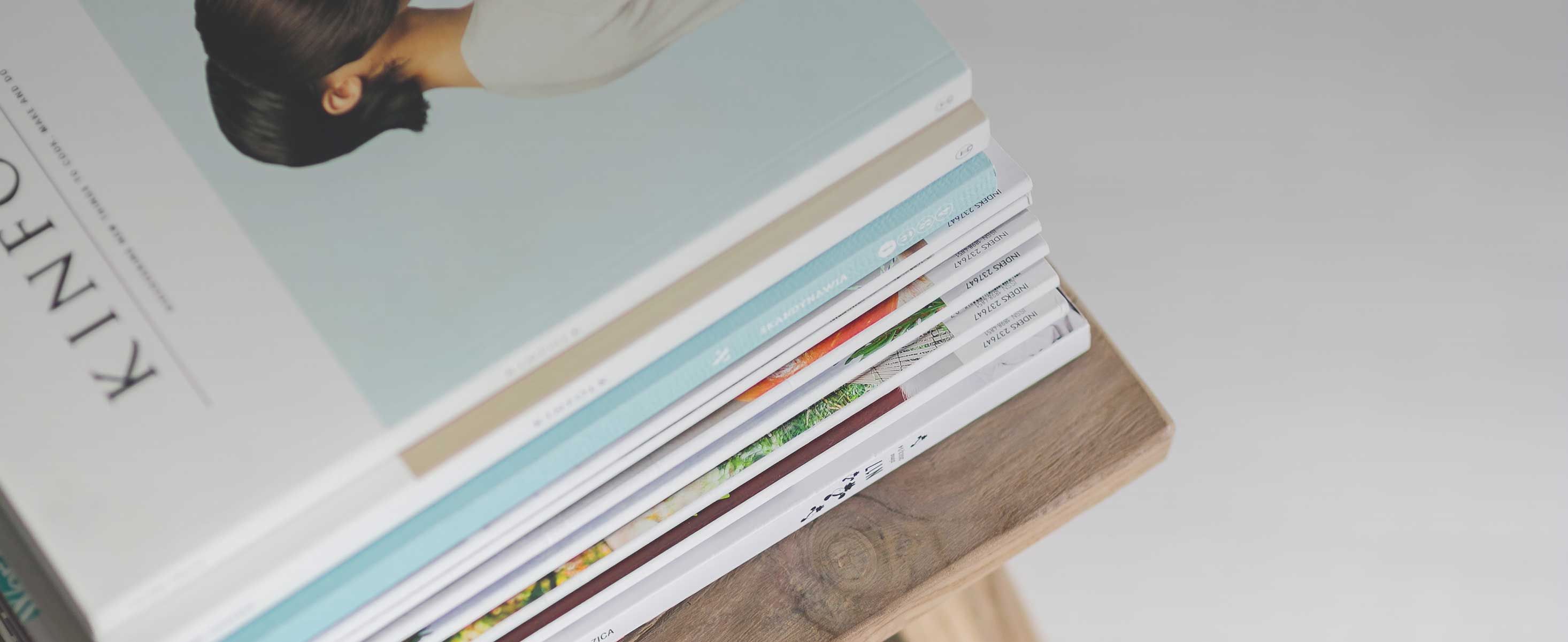
7 minute read
Control system best practices wearable exoskeleton; Stretchable sensor gives robots, VR a human touch; Headlines online include Top 5
Researchers designing wearable
The Occupational Safety and Health Administration (OSHA) said one in 10 construction site workers is injured every year, and 21% of worker fatalities are in construction. Aiming to improve worker safety and efficiency, LSU and Rutgers University researchers hope to develop an integrated, multidisciplinary approach to bring emerging robotic technologies, such as a wearable exoskeleton, to the construction industry to save lives and time.
Advertisement
The researchers received a $150,000 planning grant from the National Science Foundation to develop an exoskeleton. The award gives LSU and Rutgers one year to create a team of researchers to compete for a $3 million research grant in March. So far, their project is ahead of the game since there are few, if any, construction companies that have actually adopted exoskeleton technology.
Exoskeleton project goals: This FWHTF project has three goals – to develop lightweight, flexible, high-performance, personalized wearable exoskeletons for construction workers; develop machine learning-based human skill modeling and training in construction; and initiate new cross-disciplinary collaboration and foster engagement with industry partners and stakeholders.
“Construction workers get hurt for three reasons,” said Fereydoun Aghazadeh, an LSU professor of engineering. “Number one, they are tired. Number two, the task is beyond their capacity. Number three, they are not properly trained. If they don’t have the capacity to do the physical work, how can we enhance their physical capability? We can give them more power. This project is all about that.”
Wang, who serves as the project’s principal investigator, says there are a few exoskeleton products currently available on the market, but they mainly target the industrial/manufacturing setting. The exoskeleton is still a new concept in construction because the construction site is more dynamic and complicated.
“We’re seeing how we can explore personalized exoskeleton or robotics technology,” said Chao Wang, an assistant professor at LSU. “In a manufacturing facility, a worker probably does the same thing 1,000 times a day. It’s repetitive, which is perfect for an exoskeleton because they design it just for that one task. A construction site is a lot different. You must be able to climb stairs, walk, squat, and reach out to different levels depending on what trade you are in.
“That makes it difficult to design an exoskeleton because you need something that can help with all of these tasks. We are investigating how to make the exoskeleton smart enough to recognize what
Stretchable sensor gives robots, VR a human touch
RESEARCHERS at Cornell University have created a fiber-optic sensor that combines low-cost LEDs and dyes, resulting in a stretchable “skin” that detects deformations such as pressure, bending and strain. This sensor could give soft robotic systems – and anyone using augmented reality technology – the ability to feel the same rich, tactile sensations that mammals depend on to navigate the natural world.
The researchers are working to commercialize the technology for physical therapy and sports medicine. A 2016 stretchable sensor sent light through an optical waveguide, and a photodiode detected changes in the beam’s intensity to determine when the material was deformed. The lab also made sensors using optical lace and foams.
Doctoral student Hedan Bai drew inspiration from silicabased distributed fiber-optic sensors, which detect minor wavelength shifts as a way to identify multiple properties, such as changes in humidity, temperature and strain. Silica fibers aren’t compatible with soft and stretchable electronics. Intelligent soft systems present structural challenges.
“We know that soft matters can be deformed in a very
complicated, combinational way, and there are a lot of deformations happening at the same time,” Bai said. “We wanted a sensor that could decouple these.” Bai’s solution was to make a stretchable lightguide for multimodal sensing (SLIMS). This long tube contains a pair of polyurethane elastomeric cores. One core is transparent; the other is filled with absorb‘The sensor can detect ing dyes at multiple locations and connects to an LED. Each core is coupled with a red-green-blue pressure, bending or elongation sensor chip to register geometric by lighting up the dyes, which changes in the light’s path. The dual-core design increases act as spatial encoders.’ the number of outputs by which the sensor can detect deformations (pressure, bending or elongation) by lighting up the dyes, which act as spatial encoders. Bai paired that technology with a mathematical model that can decouple different deformations and pinpoint locations and magnitudes. Sensors are wearable and may boost virtual and augmented reality experiences. ce David Nutt, Cornell University. Edited by Chris Vavra, associate editor, Control Engineering, CFE Media and Technology, cvavra@cfemedia.com.
exoskeleton
task the construction worker is doing and adjust its power level and control strategy to more effectively assist with the work.”
The researchers will study what tasks each construction crew member performs in order to develop and train an exoskeleton that fits different construction tasks. They will consider if the robotic exoskeleton should support the upper or lower body and how much power should be given.
The team says its motivation for this project comes from the workforce shortage in the United States. There are plenty of construction jobs along the Gulf Coast but not enough workers. Wang said what caused the workforce shortage is construction workers aging or retiring due to an injury and a decrease in young people doing construction work.
With an exoskeleton to alleviate risk of injury, more construction workers could perform for more years and do so safely and efficiently. The team said it would also open the door to more women being able to do jobs that were once solely for men.
There are some issues the team is trying to work out, such as the cost of the exoskeleton and how it could work safely in different weather conditions since it would be powered by battery. The team is collaborating with industry companies and trade schools who are not yet aware of this technology but will help them develop a better product.
“It takes industry and society working together to make this happen,” Aghazadeh said. ce
Libby Haydel, communications specialist, LSU College of Engineering. Edited by Chris Vavra, associate editor, Control Engineering, CFE Media and Technology, cvavra@cfemedia.com.
Headlines online
Top 5 Control Engineering articles Nov. 9-15
The most read articles covered SCADA, HMI and MES projects, the 2021 Engineers’ choice finalists [vote by end of December], top 5 VFD parameter changes, advanced process control changes and matching motors and drives.
Lithium-metal batteries offer alternative for users
Lithium metal solid-state batteries can provide a safer, more powerful alternative to the current standard.
Squeeze-twist coupling material strengthens actuators
University of Wisconsin-Madison engineers have made an asymmetric material that twists, which could help advance actuator technology.
Boeing updates 737 Max control system and its policies and procedures designed to strengthen training, safety, quality
On Nov. 18, the FAA approved Boeing’s request to resume Boeing 737 Max (737-8 and 737-9) operations. That news, summarized below, is posted at www.controleng.com as an update to a Nov. 13, 2019, “Think Again” Control Engineering commentary that noted: “Best practices matter when designing control systems.”
Addressing design changes, Boeing said in an Oct. 25, 2019, statement: “Boeing has redesigned the way Angle of Attack (AoA) sensors work with a feature of the flight control software known as Maneuvering Characteristics Augmentation System (MCAS). Going forward, MCAS will compare information from both AoA sensors before activating, adding a new layer of protection. In addition, MCAS will now only turn on if both AoA sensors agree, will only activate once in response to erroneous AOA, and will always be subject to a maximum limit that can be overridden with the control column. These software changes will prevent the flight control conditions that occurred in this accident from ever happening again. In addition, Boeing is updating crew manuals and pilot training, designed to ensure every pilot has all of the information they need to fly the 737 MAX safely.”
Addressing changes to Boeing company policies, a Nov. 18, 2020, Boeing statement said: “In addition to changes made to the airplane and pilot training, Boeing has taken three important steps to strengthen its focus on safety and quality. 1. Organizational alignment: More than 50,000 engineers have been brought together in a single organization that includes a new Product & Services
Safety unit, unifying safety responsibilities across the company. 2. Cultural focus: Engineers have been further empowered to improve safety and quality. The company is identifying, diagnosing and resolving issues with a higher level of transparency and immediacy. 3. Process enhancements: By adopting next-generation design processes, the company is enabling greater levels of first-time quality. For more information, visit www.Boeing.com/737-max-updates.” ce Mark T. Hoske is content manager, Control Engineering, CFE Media and Technology, mhoske@cfemedia.com.