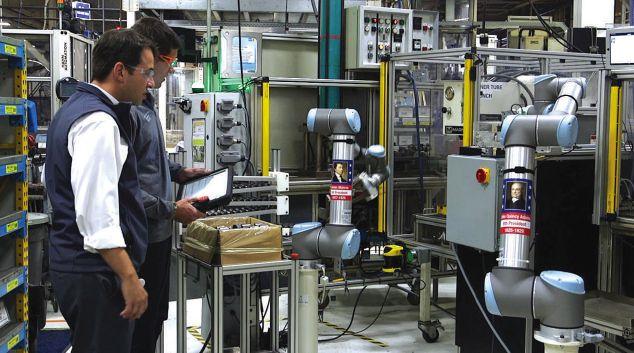
9 minute read
7 things needed to deploy cobots
Joe Campbell, Universal Robots
7 steps to cobot deployment
Advertisement
Select a collaborative robot: Consider risks and if a system integrator is needed.
Emergence of collaborative robots has created new paradigms for industrial automation. Industrial robot deployments traditionally required massive capital investment, teams of engineering and programming specialists and many months of lead time. Some large-scale industrial robot deployments can take years and tens of millions of dollars to complete. That’s before factoring in ongoing maintenance, programming and support costs.
More collaborative robotics, where?
Cobots changed that by providing manufacturers with a viable alternative to traditional automation’s complex, costly, and time-consuming “all-or-nothing” approach in the form of a modernized, humanfriendly automation paradigm. They can be used in many industries, such as electronics manufacturing, metal fabrication and others. Collaborative robots, less expensive and easier to deploy than traditional robotics (even by those without robot experience), have expanded use of automation to thousands of small- and medium-sized businesses.
Unlike traditional robots, cobots can be safely deployed in the same workspace as humans without the need for extensive safety fencing and guarding, following a risk assessment. With floorspace at a premium in most industrial and manufacturing settings, cobots’ small footprint, safety features and cage-free deployment possibilities add to the fast-growing global appeal of cobot technology. Cobots can be deployed close to humans without special fencing (following a risk assessment) and are easy to program. They also can deliver massive improvements in ergonomics for existing workers by taking over the repetitive, heavy-duty tasks that lead to strain and injury. This frees human workers to focus on higher-value tasks. Cobots also provide 24/7 availability and consistent performance which leads to improved quality outcomes compared to tasks performed manually.
The shortage of available labor is a long-term challenge for the manufacturing sector and a challenge that has been exacerbated by the COVID-19 pandemic; 62.4% of respondents to a National Association of Manufacturers (NAM) survey in December 2020 identified attracting and retaining a quality workforce as their primary business challenge. Cobots are an effective way for manufacturers to address these labor gaps, enabling increased production and throughput and improved quality, even with labor market shortfalls. As it becomes more difficult to find labor for material handling, welding, small parts assembly, and computer numerical control (CNC) machine tending, and welding tasks, cobots have picked up the slack.
The International Federation of Robotics (IFR) reveal cobots are the fastest-growing segment of the industrial robot market. Early adopters of cobot technology in the late 2000s were adopting new ideas: automation could be safely deployed around humans; automation could be programmed and deployed by manufacturing personnel rather than industrial robot experts; and automation can be introduced and in a way that doesn’t require large-scale changes to existing floorplans, especially valuable for smaller companies.
Successfully use collaborative robotics
So far, early cobot adopters have been proven right. Cobots have demonstrated usefulness in tens of thousands of successful deployments in the automotive, manufacturing, pharma and electronics sectors and on diverse applications such as as machine tending, assembly, finishing, inspection, packaging and palletizing. Cobots are now 5% of the global industrial robot market; Interact Analysis predicts that will increase to around 30% by 2027. To drive successful cobot deployment, consider seven areas.
1. Do it yourself or hire an integrator
Due to their ease-of-use and small footprint, cobots are ideally suited to do-it-yourself implementations. If your application is a simple one – such as a pick-and-place operation – then companies should feel confident in their ability to handle the deployment in-house. DIY deployments are considerably cheaper than those that require integration specialists, which is a major attraction for
Figure 1: “Cobots gave us the opportunity to grow, expand, create more jobs, and move our most valuable resources, our human resources, into new projects, where the know-how was most needed,” said Aldo Albieri, operations manager at thyssenkrupp Bilstein’s plant in Hamilton, Ohio, where UR10 cobots from Universal Robots handle machine tending, assembly, and product inspection. “If we relied only on hiring new people, we would never be able to expand three times the size.” Images courtesy: Universal Robots

Figure 2: To learn more on UR robot setup and programming, the engineering team at DCL Logistics in Fremont, Calif., did the free online training modules at the Universal Robots Academy and free application simulator on the UR website. Walter Perchinumio, senior software engineer at DCL Logistics, said, “In the simulator, we saw the actual interface ... the first month that we worked with the robot was exclusively with the simulation... that ended up being the deciding factor for me.”
small companies with limited automation budgets.
Quantity and quality of the educational resources provided by different cobot makers vary. Particularly for those with little or no previous robotics experience, it’s essential to identify cobot brands that provide the online training, education and support required to implement a cobot in-house.
For more complex applications, or for any reason, the in-house capabilities don’t extend to a full deployment. Companies need to choose among three types of integration. a. A value-add distributor is the least expensive and will provide technical assistance to help facilitate a sale and will recommend configurations and peripherals. b. A Lean integrator often focuses on a specific application (welding, for example, or surface finishing) and measures integration time in weeks. c. A traditional system integrator builds a cobot-based cell from scratch, integrating all the peripherals and hardware required in a turnkey cell. Traditional integrators measure lead times in months, making for a more expensive and complete integration process.
2. Identify risk factors
Every application is different and presents its own challenges. Some risks are inherent to the process, such as arc welding. Other risks arise from the addition of extra complexity, such as when a vision system is added to a cobot cell. The environment also can present risks, particularly in relation to moisture and temperature levels. Factors such as how close to maximum payload you operate your cobot can impact on the lifespan of the equipment. Ask your cobot manufacturer for an application risk scorecard that can help in an informed assessment of these factors.
3. Cobot risk assessment
Risk assessments are an obligatory part of the cobot deployment process. For guidance on completing a risk assessment, visit the A3 Robotics website (part of the Association for Advancing Automation), which provides excellent robot safety resources and training. Elsewhere, the European Unionfunded COVR project recently released a free, digital toolkit that provides a central repository of information and guidance regarding risk assessments, case studies, safety directives, international standards, and best practice in cobot safety.
4. The business case to invest
The business case for cobots is compelling, but detailed return on investment (ROI) information is required by many executives when making an automation investment. Ask the cobot supplier for an ROI worksheet and instructions on how to calculate total benefits from a cobot installation.
ROI values also incorporate overall equipment effectiveness (OEE), a measure of how well equipment is utilized versus its maximum potential when it is scheduled to run, and overall labor effectiveness (OLE), which determines how well the company uses its highest-performing personnel, adjusted for variables such as availability, throughput and quality.
5. Upskilling, cobot operators
This first step to ensuring painless upskilling of existing staff to become cobot operators is choosing a cobot that is high on usability. If the cobot is easy to program via teach pendant, smartphone or tablet computer, one of the main obstacles to successful upskilling has been eliminated right away.
After that, select a cobot ambassador to champion the technology. Due to the “wow” factor associated with cobots, the challenge here will likely not be finding a cobot champion, but sorting through several enthusiastic applications for the role.
Look for cobot brands that provide education and training resources. This will help streamline the training process and reduce implementation times. Quality matters, so look for well-established cobot training curriculums, especially those that result in industry-recognized certification.
6. Pick application accessories
Cobots are platforms that enable an incredible variety of applications from precise inspection tasks to heavy duty palletizing operations, but to complete a system, select some type of end-of-arm-tooling. Not all cobots are created equal. Perform due diligence and ensure to invest in cobots that are certified plugand-play compatible with the widest range of end-ofarm-tooling, hardware and software peripherals. Seek cobot brands that understand how cobots are used in varied application-specific scenarios with complete application kits with all the software and hardware required to get started on a specific task.
7. Perform cobot research
Navigatigating through considerable online information on collaborative robots is the biggest challenge. Real-world case stories are a good place to find practical information about cobot deployments and outcomes. White papers cover a particular application, topic or industry. With many new entrants to the cobot manufacturing market in recent years, focus research on information from companies with a proven track record. Independent sources of cobot information worth exploring include TÜV Rheinland, A3 and the European Union-funded COVR project. ce
M
More
ANSWERS KEYWORDS: collaborative KEYWORDS:
robots, risk assessment, cobots
Collaborative robots (cobots) can help manufacturers improve efficiency and safety. A company needs to determine early if a system integrator should help. Proper research on cobots and what they can do. ONLINE See more advice, photos at www.controleng.com/robotics. CONSIDER THIS
Are your competitors
accelerating with collaborative robotic implementations? Joe Campbell, senior manager of applications development, Universal Robots. Edited by Chris Vavra, web content manager, Control Engineering, CFE Media and Technology, cvavra@cfemedia.com.
Experts on demand
The new Metris Performance Center now offers its remote support service to any industry, giving plant operators virtual access to ANDRITZ experts whenever they need it.
Teleportation has not been invented yet. But modern IT technology does make it possible to have a virtual presence almost anywhere in the world, an ability ANDRITZ has leveraged for its new Metris Performance Center. “This is a step beyond a simple hotline or service line as we can now digitally connect our experts all over the world with the operators working at plant,” says Gerhard Schiefer, Vice President of Global Automation at ANDRITZ. “With remote support we can see in real time what an operator sees on the distributed control system screen. By collaborating via this fast connection, we can troubleshoot, answer urgent questions on processes or equipment, or even make process cesses or equipment, or even make process adjustments on the fly.” adjustments on the fly.”
And there is more. And there is more. Combining remote Combining remote support with augmented reality and decision wall tools enables Metris Performance Center experts to be virtually inside the plant; close communication and interaction can take place as if the different parties were in the same room. The Metris Performance Center uses secure remote access to connect directly to a plant’s distributed control system (DCS) at one end and a Metris server at the other.
The Metris UX Platform is ANDRITZ’s solution for optimization and decision support. It collects data in a secure way from the mill, analyzes it and converts it into useful information.
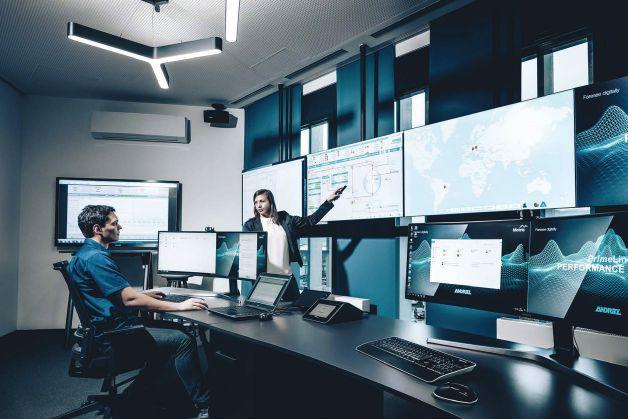
LEARN MORE
