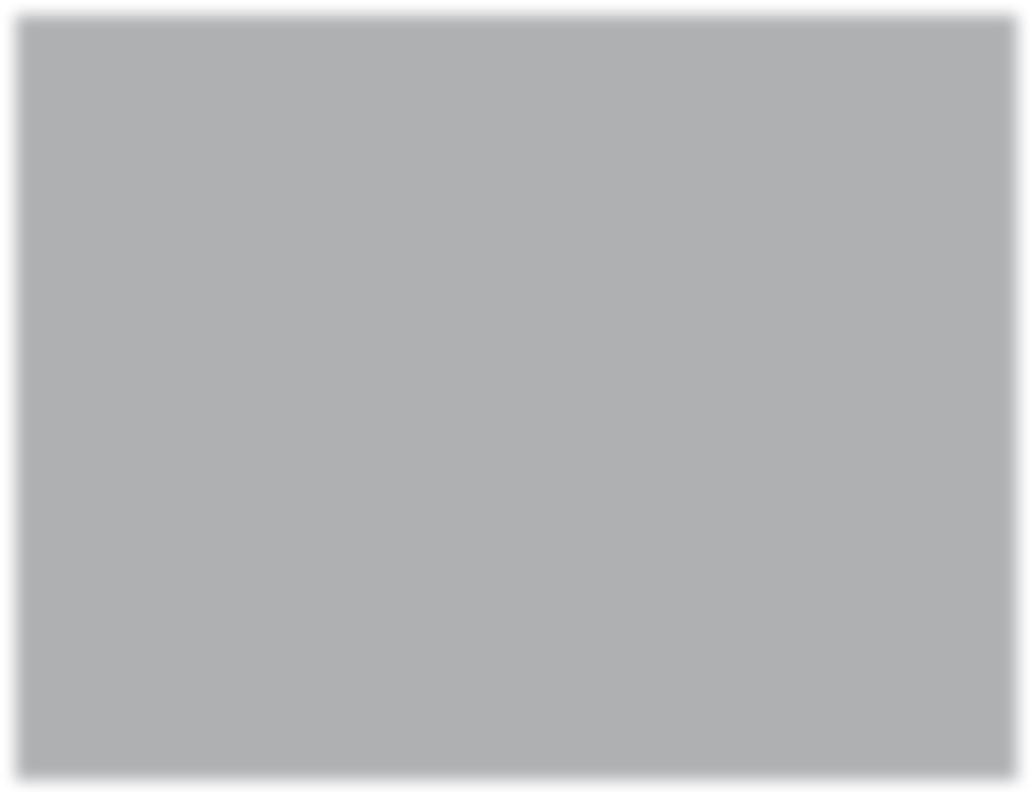
5 minute read
Multivariable control as a core competency
Allan G. Kern, P.E., APC Performance LLC.
Advertisement
Acore-competency is a skill set, mastery of which is essential to success in your business. For example, it is accepted establishing and sustaining a healthy base-layer process control (BPC) system is a core-competency of the process industries.
A healthy multivariable advanced process control (APC) layer is also a core-competency of the process industries – or should be. That may sound like a tall order due to the historic struggle the process industry has already waged trying to master conventional model-based multivariable control technology. However, by taking stock of the lessons learned, and taking a fresh look at the conventional APC paradigm, seeing how and why multivariable control must evolve into a core-competency is a lot clearer.
Working concept of multivariable control
Chiefamongthelessons learned is the need for of a more accessible working concept of multivariable control and its existential role in process operation. A shared working concept of multivariable control is essential in order to make multivariable control, as a tool that can automate and optimize many aspects of process operation, more accessible to on-site operation stakeholders, such as process engineers, operating staff, and managers. In the past, multivariable control has usually remained in the hands of APC specialists and was mostly a black box to the on-site operating team. A more accessible working concept means the local operating team can more efficiently identify, deploy, operate, maintain and participate in multivariable control applications – with local ownership skills and a shared working knowledge of the technology being key aspects of a core-competency.
Just as a single-loop controller automates the job of making frequent valve output adjustments that are otherwise left to operators to make manually, a multivariable controller automates the job of making frequent single-loop controller setpoint adjustments.
This is how any multivariable controller, regardless of the technology employed (model-based or model-less), touches the process. It is the easiest way to understand the actual role of multivariable control in process operation – it automates the job of making
Table: Revise your thinking about multivariable control from lessons learned in advanced process control applications. Courtesy: APC Performance
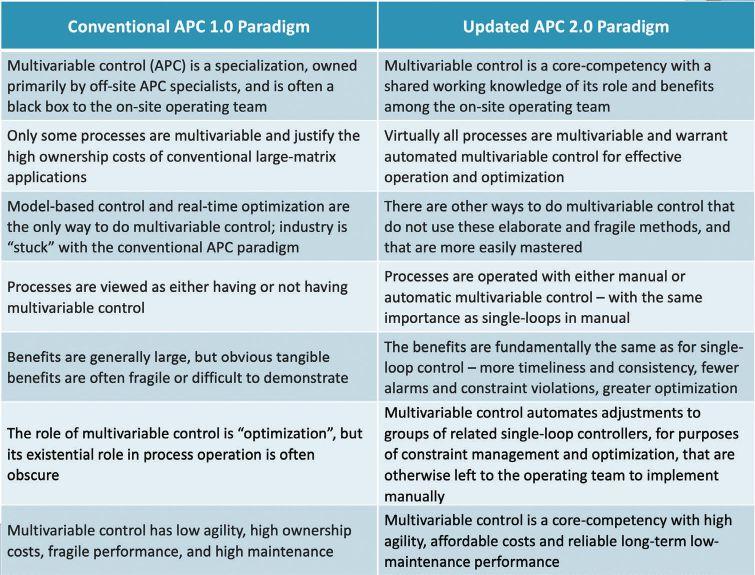
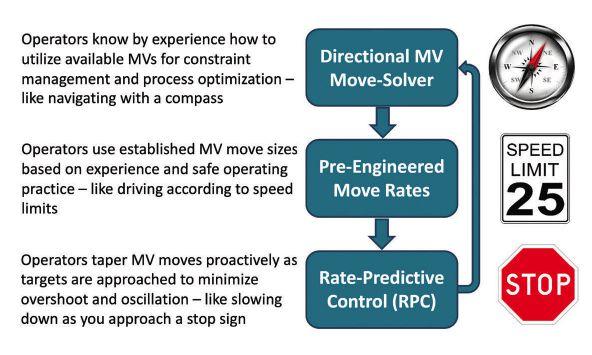
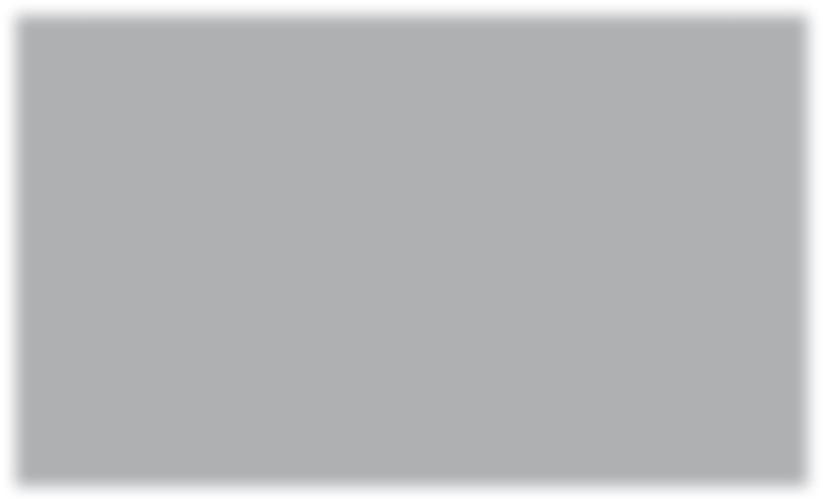
Figure: The basic method operating teams have always used for Figure: The basic method operating teams have always used for manual multivariable control, which notably does not require process models or real-time optimizers. This method can be automated to provide a less fragile and more readily mastered multivariable control tool. Courtesy: APC Performance
M
More
setpoint adjustments to groups of inter-related controllers, for purposes of closed-loop constraint control and optimization.
The qualitative benefits of automatic multivariable control can also be understood as fundamentally the same as single-loop control – more timeliness and consistency, fewer alarms and constraint violations, and greater optimization. These benefits range from the inherent performance benefits of closed-loop control over open-loop, to significant operational and economic improvements, to large-scale benefits associated with conventional large-matrix multivariable controller applications.
Manual versus automatic multivariable control
When operators make setpoint and output adjustments to groups of related controllers, that’s manual multivariable control. When a multivariable controller is applied to automate these adjustments, that’s automatic (or closed-loop) multivariable control. Making frequent adjustments to sets of related controllers is an inherent aspect of almost every process operation. A more informative way of looking at processes is not whether they have multivariable control or not, but whether it is manual or automatic. This is the same way the process industry views base-layer control health – how many controllers are in automatic versus manual mode. The lack of a healthy multivariable APC layer is the equivalent to having excessive baselayer loops in manual mode highlights the need to address the lack of manual multivariable control because the battle of gaining widespread shared operating team agreement on the fundamental importance of closed-loop control over open-loop control was won long ago. For example, many operating sites today uses some form of the controllers-in-manual key performance indicator (KPI) to measure and manage BPC health. The process industry lacks a similar metric to measure and manage APC health, but alternatives are available for adoption, such as loop intervention or bad actor loop metric (see industry’s missing metric). Wherever operators are frequently observed to be busy making controller adjustments, or where operating conditions are often observed in a sub-optimal state is an opportunity for automatic multivariable control. Process operation engineers, who are often the main “boots on the ground” when it comes to overall responsibility for process optimization, in particular tend to observe these conditions on a regular basis and would often “trade their kingdom” for a more effective solution than frequent follow-up (or “badgering”) of operations. Multivariable control as a core-competency offers a solution.
Path to core-competency: Multivariable control
Another key lesson is model-based control and
ANSWERS real-time optimization are not strictly required KEYWORDS: Advanced process control, multivariable control Get a working concept of multivariable control. components of multivariable control. They are part of the way conventional APC technology solves the multivariable control problem. However, there are other ways to do automated closed-loop multivariUnderstand the difference able control that are less complex and more readbetween manual versus ily mastered. automatic multivariable control. For example, users can see operating teams are Find the path to core- routinely engaged in manual multivariable con-competency with multivariable control. trol – and do so without detailed models or realtime optimizers. This reveals an alternative path CONSIDER THIS to multivariable control by automating the methAre you taking advantage of ods traditionally employed by operating teams to multivariable control for critical processes? Coming in September, “APC for the rest of us,” a 3-part series effect constraint management and optimization manually (Figure 1). This takes a time-proven approach to multidesigned to impart a practical variable process operation and adds the benefits of working knowledge of APC for automation – real-time closed loop performance, the on-site operating team -- not just APC specialists -- for more effective collaboration on process operation, constraint built-in expertise and consistency and corresponding process performance improvements (see What is XMC?) ce management, and optimization achievement. ONLINE www.controleng.com/ control-systems/pid-apc Allan G. Kern, P.E., is owner and consultant at APC Performance LLC. Edited by Mark T. Hoske, content manager, Control Engineering, CFE Media and Technology, mhoske@cfemedia.com.