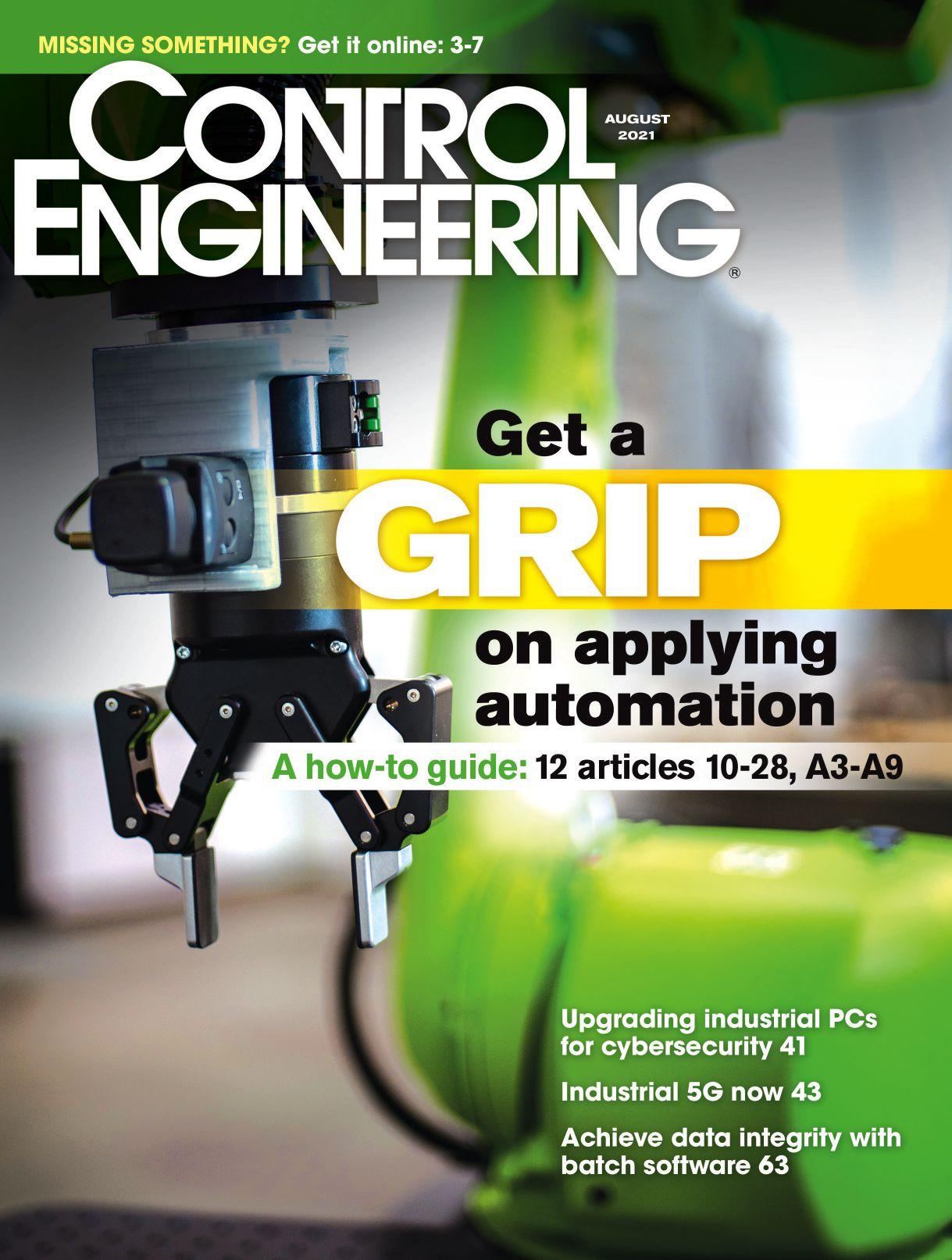





























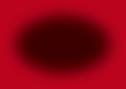

Are you getting the best possible price from your supplier on every purchase, or do you have to buy in bulk to get the lowest price?
Are you getting the best price from your on every or do you have to in bulk to get the lowest
The buy more, pay less game works great for those with big budgets and big projects, but if you only need a handful of components doesn’t work at all. At AutomationDirect, we never play games with our prices, you get the lowest price possible no matter if you buy one or a thousand.
The more, pay less game works great for those with big budgets and big projects, but if you need a handful of components it doesn’t work at all. At AutomationDirect, we never games with our prices, you get the lowest price no matter if you one or a thousand.
in PHOENIX,
in SUWANEE,
Cleigh in HEBRON,
61 | Power converters with conformal coating, Service ball valves, Micro variable frequency drive, Screening vibration sensor system, Flowmeter sensor series, UWB sensor for IIoT applications, Customized SCADA systems, Water detection monitoring sensors
63
More New Products for Engineers: www.controleng.com/NPE.
Electronic batch records (EBRs) can improve record-keeping by making it more automated and removing the human element from the equation.
• Structuring with IEC 61131-7: 7 steps to success
• Robotic finger uses tactile sensing to find buried items
• Control Engineering hot topics, June 2021
• Collaborative robots’ role in high-mix, low-volume production
• Keeping robot programming simple Keep up with emerging trends: subscribe. www.controleng.com/newsletters.
Did you miss the last Virtual Training Week?
You can still attend CFE Media and Technology’s Virtual Training Week ondemand to receive training on a variety of the latest industry trends. Register and receive full access to exclusive content offered by industry experts with live Q&A sessions!
https://cfeedu.cfemedia.com/learning-paths/ cfe-media-technology-virtual-training-week
Robotics are one of the fastestgrowing industries and their impact can be felt on many manufacturing floors. There’s more to the robot, however, than what you see on the plant floor. This helpful eBook includes articles about disinfection robots, collaborative robot use cases and reducing COVID-19 worker risks with robots
Learn more and register to download at www.controleng.com/ebooks/.
How system integrators make remote automation work, Migrating legacy PLCs to modern PLCs, Replacing seven SCADA systems with one and More advice in a Supplement to Control Engineering and Plant Engineering www.controleng.com/GSIR
The tablet and digital editions provide links to additional article images and text online and links to other related, useful resources.
® controleng.com provides new, relevant automation, controls, and instrumentation content daily, access to databases for new products and system integrators, and online training.
www.controleng.com/magazine
Lithium battery developments step forward for electric vehicles, more, https://www.controleng.com/articles/lithium-battery-developments-step-forward-for-electric-vehicles-more/ Cybersecurity management tips for an organization, https://www.controleng.com/articles/cybersecurity-management-tips-for-an-organization/
Improving operator performance from field to control room, https://www.controleng.com/articles/improving-operator-performance-from-field-to-control-room/ Machine vision technologies for automation, https://www.controleng.com/articles/machine-vision-technologies-are-more-important-than-ever-for-automation/ Funding for COVID-19 wastewater monitoring, https://www.controleng.com/articles/researchers-receive-expanded-funding-for-covid-19-wastewater-monitoring/ Essence of digital enterprise: Three types of digital twins, https://www.controleng.com/articles/essence-of-digital-enterprise-three-types-of-digital-twins/ Perovskite superfluoresces could benefit quantum computing https://www.controleng.com/articles/perovskite-superfluoresces-could-benefit-quantum-computing/ Four tips for designing scalable IIoT networks, https://www.controleng.com/articles/four-tips-for-designing-scalable-iiot-networks/ Using AI to better understand alloys, metals, https://www.controleng.com/articles/using-ai-to-better-understand-alloys-metals/
Understanding the difference between Profinet RT and Profinet IRT, https://www.controleng.com/articles/understanding-the-difference-between-profinet-rt-and-profinet-irt/ Structuring with IEC 61131-3: 7 steps to success, https://www.controleng.com/articles/structuring-with-iec-61131-3-7-steps-to-success/
Programming standardization unifies, improves https://www.controleng.com/articles/programming-standardization-unifies-improves-operator-experience/ Nissan accelerates assembly, lowers costs with 3D printing, https://www.controleng.com/articles/nissan-accelerates-assembly-lowers-costs-with-3d-printing/ New president at machine-builder automation and motion-control company, https://www.controleng.com/articles/new-president-at-machine-builder-automation-and-motion-control-company/
Reducing industrial automation risk and downtime with high availability components, https://www.controleng.com/articles/reducing-industrial-automation-risk-and-downtime-with-high-availability-components/ Advice: Exploring best practices for industrial wireless, https://www.controleng.com/articles/advice-exploring-best-practices-for-industrial-wireless/ Cummins integrates metal 3D printed production, https://www.controleng.com/articles/cummins-integrates-metal-3d-printed-production/
Better gripping with intelligent picking robots, https://www.controleng.com/articles/better-gripping-with-intelligent-picking-robots/ Additive manufacturing without a 3D printer: Impossible parts, https://www.controleng.com/articles/additive-manufacturing-without-a-3d-printer-impossible-parts/ Increasing speed, reliability of wireless communications, https://www.controleng.com/articles/increasing-speed-reliability-of-wireless-communications/ Automated 3D printing: Additive manufacturing, https://www.controleng.com/articles/automated-3d-printing-additive-manufacturing/
Ultralight material withstands supersonic microparticles, https://www.controleng.com/articles/ultralight-material-withstands-supersonic-microparticle-impacts/
Impact of Zebra’s acquisition of robotics company, https://www.controleng.com/articles/impact-of-zebras-acquisition-of-robotics-company/ How AI can predict electronics failure, https://www.controleng.com/articles/how-ai-can-predict-electronics-failure/ Understanding HART status information, https://www.controleng.com/articles/understanding-hart-status-information/ Regional interest agreement signed for technology group, https://www.controleng.com/articles/regional-interest-agreement-signed-for-technology-group/ Simulation and analysis market grows in 2020, https://www.controleng.com/articles/simulation-and-analysis-market-grows-in-2020/ Making computers more secure, https://www.controleng.com/articles/making-computers-more-secure/ Drive suppliers facing supply chain issues, semiconductor shortage, https://www.controleng.com/articles/drive-suppliers-facing-supply-chain-issues/ Four ways to build a digital knowledge infrastructure, https://www.controleng.com/articles/four-ways-to-build-a-digital-knowledge-infrastructure/ Technique to manufacture flexible electronics developed, https://www.controleng.com/articles/technique-to-manufacture-flexible-electronics-developed/ Microprocessor manufacturer joins TSN group, https://www.controleng.com/articles/microprocessor-manufacturer-joins-tsn-group/ Nanotech OLED could cut power consumption, https://www.controleng.com/articles/nanotech-oled-could-cut-power-consumption/ Top 5 Control Engineering articles July 5-11, 2021 https://www.controleng.com/articles/top-5-control-engineering-articles-july-5-11-2021/ Bird-like wings could help drones keep stable in gusts, https://www.controleng.com/articles/bird-like-wings-could-help-drones-keep-stable-in-gusts
ABB acquired ASTI Mobile Robotics Group (ASTI), a mobile robot (AMR) manufacturer. Courtesy: ABB and ASTI https://www.controleng.com/articles/ mobile-robotics-group-acquired
New combination of materials provides progress toward quantum computing, https://www.controleng.com/articles/new-combination-of-materials-provides-progress-toward-quantum-computing/ Organic-based, solid-state lithium EV battery developed with altered microstructure, https://www.controleng.com/articles/organic-based-solid-state-lithium-ev-battery-developed-with-altered-microstructure/
On pages 6 and 7 are articles posted in July 2021, in case you missed something. Links are live in the digital edtion at www.controleng.com/magazine.
Top 5 Control Engineering articles July 12-18, 2021, https://www.controleng.com/articles/top-5-control-engineering-articles-july-12-18-2021/
Streaming precise positioning data from valve positioners, https://www.controleng.com/articles/streaming-precise-positioning-data-from-valve-positioners/ Manufacturers adjusting to a changing risk landscape, https://www.controleng.com/articles/manufacturers-adjusting-to-a-changing-risk-landscape/ How process calibration has evolved with digitalization, https://www.controleng.com/articles/how-process-calibration-has-evolved-with-digitalization/ Robot algorithm improves safe motion around humans, https://www.controleng.com/articles/robot-algorithm-improves-safe-motion-around-humans/
Three ways omlox helps Industry 4.0 as an open standard, https://www.controleng.com/articles/three-ways-omlox-helps-industry-4-0-as-an-open-standard/ Cybersecurity education and research institute established, https://www.controleng.com/articles/cybersecurity-education-and-research-institute-established/ Autonomous UV robot developed to sanitize classrooms, https://www.controleng.com/articles/autonomous-uv-robot-developed-to-sanitize-classrooms/
Three types of Profibus device types explained, https://www.controleng.com/articles/ three-types-of-profibus-device-types-explained/
Combating cognitive fatigue with collaborative robots, https://www.controleng.com/articles/combating-cognitive-fatigue-with-collaborative-robots/ Structural alloys strengthened with precipitates, https://www.controleng.com/articles/structural-alloys-strengthened-with-precipitates/ Mobile robotics group acquired, https://www.controleng.com/articles/mobile-robotics-group-acquired/ Ethernet group discusses safety, conformance testing, https://www.controleng.com/articles/ethernet-group-discusses-safety-conformance-testing/
Bridging the cybersecurity leadership gap, ttps://www.controleng.com/articles/bridging-the-cybersecurity-leadership-gap/ AI being used in real-world robotics applications, https://www.controleng.com/articles/ai-being-used-in-real-world-robotics-applications/
Top 5 Control Engineering articles July 19-25, 2021, https://www.controleng.com/articles/top-5-control-engineering-articles-july-19-25-2021/
RTU and SCADA systems help with telemetry monitoring, control, https://www.controleng.com/articles/rtu-and-scada-systems-help-with-telemetry-monitoring-control/ Changing a 2D material’s symmetry can help improve optoelectronic devices, https://www.controleng.com/articles/changing-a-2d-materials-symmetry-can-help-improve-optoelectronic-devices/ Airport logistic automation market stays strong in spite of COVID-19, https://www.controleng.com/articles/airport-logistic-automation-market-stays-strong-in-spite-of-covid-19/ Going green with obsolete equipment for manufacturers, https://www.controleng.com/articles/going-green-with-obsolete-equipment-for-manufacturers/ Accelerating digital transformation focus of online forum https://www.controleng.com/articles/accelerating-digital-transformation-focus-of-online-forum/ Manufacturer, university on additive mfg, https://www.controleng.com/articles/manufacturer-university-partner-up-to-advance-additive-manufacturing-technology/ Five steps to select predictive analytics software, https://www.controleng.com/articles/five-steps-to-select-predictive-analytics-software/ Global semiconductor sales to pass $100 billion by 2022, https://www.controleng.com/articles/global-semiconductor-sales-to-reach-100-billion-by-2022/ Technique for recycling nanowires developed https://www.controleng.com/articles/technique-for-recycling-nanowires-developed/ Data integrity with electronic batch records, https://www.controleng.com/articles/data-integrity-with-electronic-batch-records/ Optimizing manufacturing processing and quality management with digital twins, IIoT, https://www.controleng.com/articles/optimizing-manufacturing-processing-and-quality-management-with-digital-twins-iiot/ Engineering company installs automated production, material handling solutions, https://www.controleng.com/articles/engineering-company-installs-automated-production-material-handling-solutions/ Companies need to reassess cyber-physical security risk, https://www.controleng.com/articles/companies-need-to-reassess-their-cyber-physical-security-risk/ Changing a network security approach, https://www.controleng.com/articles/changing-a-network-security-approach/ Robotic 3D manufacturing providing greater flexibility , https://www.controleng.com/articles/robotic-3d-manufacturing-providing-greater-flexibility/ Multivariable control as a core competency, https://www.controleng.com/articles/multivariable-control-as-a-core-competency/ Six steps to improve computer hardening, https://www.controleng.com/articles/six-steps-to-improve-computer-hardening/ Device type manager changes for IIoT applications, https://www.controleng.com/articles/device-type-manager-changes/
A technique for retrieving nanowires from electronic devices that have reached the end of their utility and then using those nanowires in new devices has been developed by North Carolina State University researchers. Courtesy: North Carolina State University www.controleng.com/articles/technique-for-recycling-nanowires-developed/
Global sales of semiconductor manufacturing equipment by original equipment manufacturers (OEMs) are forecast to surpass $100 billion next year, a new high, after jumping 34% to $95.3 billion in 2021 compared to $71.1 billion in 2020, SEMI announced in its Mid-Year Total Semiconductor Equipment Forecast – OEM Perspective at the Innovation for a Transforming World virtual conference. Continuing investments by device makers in secular growth areas are fueling the expansion of the front-end and back-end semiconductor equipment segments.
The foundry and logic segments, accounting for more than a half of total wafer fab equipment sales, will grow 39% year-over-year to reach $45.7 billion in 2021 on strong demand for leading-edge technologies powered by the digitization of industries worldwide. The growth momentum is expected to continue in 2022 with the foundry and logic equipment investments rising another 8%. The wafer fab equipment segment, which includes wafer processing, fab facilities, and mask/reticle equipment, is projected to surge 34% to a new industry record of $81.7 billion in
Automation and motion control company Lenze Americas welcomed Steve Markham as its new president, in a July 7 announcement. The company, based in Uxbridge, Mass., supplies automation technologies and services to the machine-building industry, and specializes in motion-centric automation. Christian Wendler, chairman of the Lenze executive board, said, “We are thrilled to welcome Steve Markham to our organization. Under his leadership, Lenze Americas will build on our North American sales, production, and engineering footprint to better serve our customers and drive company growth.” Wendler added, “Lenze’s industrial solutions expertise and motion centric applications can make a real difference for machine builders looking for higher productivity, better energy efficiency, lower system cost, and global service support.”
Having lead U.S. and international firms in rapid growth, Markham brings extensive experience providing management and business consulting services, continuous improvement, and business transformations. With multi-industry expertise in supply-chain, operations, production, and international business, Markham will make expansion of the Lenze brand in North America a top priority. Markham said, “By leveraging Lenze’s impressive worldwide capabilities, investing in logistics and supply chain, and expanding our comprehensive solutions portfolio and engineering support, I look forward to accelerating Lenze Americas’ position as a top motion control supplier.”
“It is an exciting time to be joining Lenze as we work to make a dramatic expansion in the Americas with our consistent and scalable solutions portfolio – which includes high-quality mechatronic products, powerful hardware and software for machine automation, and services for digitalization in areas such as big data management, cloud or mobile solutions, and software in the context of Internet of Things (IoT).” ce
Edited by Mark T. Hoske, content manager, Control Engineering.
2021, followed by a 6% increase in 2022 to more than $86 billion.
Robust demand for memory and storage are driving spending on NAND and DRAM manufacturing equipment. The DRAM equipment segment is expected to lead the expansion in 2021, surging 46% to surpass $14 billion. The NAND flash equipment market is projected to increase 13% in 2021 to $17.4 billion and 9% in 2022 to $18.9 billion, respectively.
The assembly and packaging equipment segment is forecast to grow 56% to $6 billion in 2021, followed by a 6% increase in 2022, driven by advanced packaging applications. The semiconductor test equipment market is expected to grow 26% in 2021 to $7.6 billion and expand another 6% in 2022 on demand for 5G and high-performance computing (HPC) applications.
Regionally, Korea, Taiwan and China are projected to remain the top three destinations for equipment spending in 2021, with Korea at the top on the strength of a robust memory recovery and strong investments in leadingedge logic and foundry. Equipment spending for all regions tracked are expected to grow in 2021. ce
– Edited from a SEMI press release by CFE Media. SEMI is a CFE Media content partner.
www.controleng.com/webcast/past
Fueling advanced analytics with industrial data management
How to improve PLC system resiliency to reduce risk and downtime
Current issues in industrial analytics
Are you data rich and information poor?
Exploring industrial wireless best practices
Navigating hiring amid a changing workforce
Accelerate machine designs, speed to market, collaboration, digital twin
3010 Highland Parkway, Suite 325, Downers Grove, IL 60515. 630-571-4070, Fax 630-214-4504
Mark T. Hoske, Content Manager 630-571-4070, x2227, MHoske@CFEMedia.com
Jack Smith, Content Manager 630-571-4070, x2230, JSmith@CFEMedia.com
Kevin Parker, Senior Contributing Editor, IIoT, OGE 630-571-4070, x2228, KParker@CFEMedia.com
Emily Guenther, Director of Interactive Media 630-571-4070, x2229, eguenther@CFEMedia.com
Amanda Pelliccione, Director of Research 978-302-3463, APelliccione@CFEMedia.com
Gary Cohen, Senior Editor GCohen@CFEMedia.com
Control Engineering has been the go-to source for understanding and applying automation since 1954, and, the August topic, “Applying automation: A how-to guide for the best results,” drew more than a dozen applicable articles. Advice from each and links (online and in the digital edition) follow below and starting on page 13. Think again about finding what you need at www.controleng.com; we added more than 70 articles in July (pages 6, 7) alone.
Greateroperationalefficiencyis required in manufacturing today and it requires a comprehensive look at everything, starting with how things are purchased. See four clarifications on consolidated industrial purchasing advantages - Jason Hoover, Sr., Yaskawa America Inc.
I think it is in everyone’s best interests to move to full automation, particularly for publicly owned facilities. Experiences running large spinning equipment in a dangerous and unhealthy environment led to exploring ways to reduce, if not eliminate, human involvement in the process - Daniel E. Capano, Gannett Fleming.
Digital transformation leverages technology to close the loop so visibility to the products and devices and the processes are
continuously expanded and internal mind set. Machine learning and data analytics help - Andy Wang, Prescient Devices.
Actuators explained: Types of actuators, application choice, maintenance: Actuators used in industrial and other applications require careful analysis of the requirements before choosing the right actuator for the application - Gilbert Welsford Jr., ValveMan.
Electronic motion control systems require reliable communications interfaces to exchange information between the controllers, actuators and sensorsChristian Fell, Fraba Inc.
Each manufactured product has some impact on the environment and produces carbon emissions. Manufacturers are using obsolete equipment can reduce that impact - Claudia Jarrett, EU Automation.
While more expensive initially, turnkey manufacturing offers more longterm advantages over using independent contractors. System integrators can help - Tom Catlin, RedViking. ce
Onthefollowingpagessee:13, 17-Two articles on applying collaborative robots; 21-Multivariable control as a core competency; 25-What to consider before applying new automation; 28-How automation will transform the workforce; A3-Process safety; A9 - System integrator in digital transformation.
Chris Vavra, Web Content Manager CVavra@CFEMedia.com
Suzanne Gill, Control Engineering Europe suzanne.gill@imlgroup.co.uk
Ekaterina Kosareva, Control Engineering Russia ekaterina.kosareva@fsmedia.ru
Agata Abramczyk, Control Engineering Poland agata.abramczyk@trademedia.pl
Lukáš Smelík, Control Engineering Czech Republic lukas.smelik@trademedia.cz
Aileen Jin, Control Engineering China aileenjin@cechina.cn
www.controleng.com/EAB
Doug Bell, president, InterConnecting Automation, www.interconnectingautomation.com
David Bishop, chairman and a founder
Matrix Technologies, www.matrixti.com
Daniel E. Capano, senior project manager, Gannett Fleming Engineers and Architects, www.gannettfleming.com
Frank Lamb, founder and owner
Automation Consulting LLC, www.automationllc.com
Joe Martin, president and founder Martin Control Systems, www.martincsi.com
Rick Pierro, president and co-founder
Superior Controls, www.superiorcontrols.com
Mark Voigtmann, partner, automation practice lead Faegre Baker Daniels, www.FaegreBD.com
Content For Engineers. That’s what CFE Media stands for, and what CFE Media is all about –engineers sharing with their peers. We welcome content submissions for all interested parties in engineering. We will use those materials online, on our website, in print and in newsletters to keep engineers informed about the products, solutions and industry trends.
www.controleng.com/contribute explains how to submit press releases, products, images, feature articles, case studies, white papers, and other media.
* Content should focus on helping engineers solve problems. Articles that are commercial or are critical of other products or organizations will be rejected. (Technology discussions and comparative tables may be accepted if non-promotional and if contributor corroborates information with sources cited.)
* If the content meets criteria noted in guidelines, expect to see it first on our Websites. Content for our e-newsletters comes from content already available on our Websites. All content for print also will be online. All content that appears in our print magazines will appear as space permits, and we will indicate in print if more content from that article is available online.
* Deadlines for feature articles for the print magazines are at least two months in advance of the publication date. It is best to discuss all feature articles with the appropriate content manager prior to submission.
Learn more at: www.controleng.com/contribute
Collaborative robots, often referred to as cobots, are robotic devices designed to physically interact with humans in a workspace. Consider three phases in the successful application of collaborative robots: Education, assessment and design.
The first phase with any new type of technology is education. How does this device work? What are its capabilities and limitations? How does this impact our understanding of safety?
The unique position of cobots in the robotic field is due to internal designs with force-sensing technology. The robot is designed to stop when external forces beyond thresholds are detected to prevent injury. The speed and torque allowed during robot motion are restricted to eliminate unsafe contact with human operators. Many cobot models allow programmable control for these settings so that the level of restriction can be tuned to the needs of the system. Those implementing cobots must be educated on proper safety requirements for automated systems and cobots.
A great deal of safety strategy for conventional robots is centered on separation between the robotic automation and human, such as safeguards like fences to restrict human access to robotic operating areas. In robot and human shared workspaces, it is typical to employ monitoring devices like light screens and floor scanners. Standards set operating distances between automation and humans in different scenarios.
Among important implementation steps is designating a safety authority. It requires a shift in how safety is approached when the intent is for humans and robots to work together. Guidelines continue to develop and it is critical to have a designated champion who is up to date on industry standards and best practices. These regulations include ANSI/RIA R15.06-2012 for general robotic system safety and RIA R15.806-2016, which more specifically addresses collaborative robot technology. Technical report RIA TR15.806-2018 provides additional guidance on testing that may be required when designing a collaborative workspace.
A common misconceptions of collaborative robots is that the system is safe for humans. The power and force limiting features only apply to the robot itself.
They do not account for other potential hazards including other components mounted to the primary robot body like end-of-arm-tooling (EOAT).
The second phase of implementing collaborative technology is to assess the system safety. A safety risk assessment is a task-based review of potential hazards in the system. Hazards are rated by characteristics such as severity and frequency and then reviewed for the ability to mitigate the risk through design. This ongoing processt should begin in system pre-design and continue through build. This type of iterative procedure will ensure safety considerations are met during design and not as an afterthought.
Consider what tasks automation will do. Let humans do what humans do best, such as critical decision-making, high dexterity/perception, technical know-how, and non-routine operations. Robots are best suited for work that is repetitive and routine. Programming can be taught to include decision-making processes, but it is an efficient tradeoff when the decision outputs are limited. With collaborative robots, this task assignment decision is expanded to consider how it will impact the risk assessment.
The assessment phase will rely upon knowledge of collaborative devices and standards. Task assign-
Figure 1: The unique position of cobots in the robotic field is due to their internal design that includes force-sensing technology. Images courtesy: Applied Manufacturing Technologies
COVER, Figure 2: The assessment phase will rely upon knowledge of collaborative devices and standards. Task assignment will be impacted by the capabilities of the robot itself.
Collaborative robots offer manufacturers potential, but companies must be diligent in education, assessment and overall design.
Chalmers, Applied Manufacturing Technologies
Figure 3: Most cobot devices have adopted rounded contours to increase surface areas and decrease forces in contact situations.
ment will be impacted by the capabilities of the robot. Power and force limiting devices work with restrictions on payload and speed to control force. Cobot devices from one robotic manufacturer vary in maximum payload capacity from 4 to 35 kg. This is a relatively light range in comparison with industrial robots, which can have payload capacities of more than 2000 kg. Arm speed is limited significantly compared with conventional robot models, which can affect cycle time targets. Each cobot task will need to be evaluated against these parameters for feasibility.
Collaborativerobotimplementationdesign includes human contact analysis, not just the cobot. Tooling and devices need to be considered in a risk assessment. Tasks must be reviewed for potential crush and impact contact hazards because humans can be in proximity to equipment. Safety standards clarify what forces are acceptable for hazards to areas of the human body. Considerations for contact differ for a leg than a human eye. Flexibility of cobot programming and setup makes it necessary to understand
how specifications can be tested to ensure proper limits for operator safety. Simulation helps identify hazards and design parameters.
Most cobot devices have adopted rounded contours to increase surface areas and decrease forces in contact situations. Similar types of deliberate design choices need to be reflected in other tooling and devices that will be part of the workspace. This may involve the use of special covers to prevent unnecessary access to components that could pose a hazard for a nearby worker. When maintenance tasks are required, the cover can be removed for access.
Some tasks can pose a hazard that cannot be resolved due to the process. A force that is required to fasten a part to an assembly may be beyond the specification limitation. Another option is to use auxiliary equipment to control human access to a controlled space during that operation. This could involve components like light screens to monitor for human access to the area around the device. The design of the system should provide safety control during the hazard of the insert task and allow for a cooperative process between the human and robot.
Treating cobots like standard robots will limit their value. Ignoring safety from the start will create unnecessary design challenges. Design the collaborative workspace from the beginning. ce
Kelly Chalmers is senior project manager at Applied Manufacturing Technologies, a CFE Media content partner. Edited by Chris Vavra, web content manager, Control Engineering, CFE Media and Technology, cvavra@cfemedia.com.
KEYWORDS: collaborative robots, cobots
Choosing a collaborative robot starts with asking what the robot should and can do.
Knowing collaborative robot safety standards and general robot safety standards is crucial.
Collaborative robot implementation design starts with the robot and includes human interactions.
See more about robots in the “robotics” section at www.controleng.com/discrete-manufacturing/robotics
How have you applied collaborative robots in your facility and what have the results been like?
‘Ensure safety considerations are met during design and not as an afterthought.’
Class
and Class of
Emergence of collaborative robots has created new paradigms for industrial automation. Industrial robot deployments traditionally required massive capital investment, teams of engineering and programming specialists and many months of lead time. Some large-scale industrial robot deployments can take years and tens of millions of dollars to complete. That’s before factoring in ongoing maintenance, programming and support costs.
Cobots changed that by providing manufacturers with a viable alternative to traditional automation’s complex, costly, and time-consuming “all-or-nothing” approach in the form of a modernized, humanfriendly automation paradigm. They can be used in many industries, such as electronics manufacturing, metal fabrication and others. Collaborative robots, less expensive and easier to deploy than traditional robotics (even by those without robot experience), have expanded use of automation to thousands of smalland medium-sized businesses.
Unlike traditional robots, cobots can be safely deployed in the same workspace as humans without the need for extensive safety fencing and guarding, following a risk assessment. With floorspace at a premium in most industrial and manufacturing settings, cobots’ small footprint, safety features and cage-free deployment possibilities add to the fast-growing global appeal of cobot technology. Cobots can be deployed close to humans without special fencing (following a risk assessment) and are easy to program. They also can deliver massive improvements in ergonomics for existing workers by taking over the repetitive, heavy-duty tasks that lead to strain and injury. This frees human workers to focus on higher-value tasks. Cobots also provide 24/7 availability and consistent performance which leads to improved quality outcomes compared to tasks performed manually.
The shortage of available labor is a long-term challenge for the manufacturing sector and a challenge that has been exacerbated by the COVID-19 pandemic; 62.4% of respondents to a National Association of Manufacturers (NAM) survey in December 2020 identified attracting and retaining a quality workforce as their primary business challenge. Cobots are an effective way for manufacturers to address these labor gaps, enabling increased production and throughput and improved quality, even with labor market shortfalls. As it becomes more difficult to find labor for
material handling, welding, small parts assembly, and computer numerical control (CNC) machine tending, and welding tasks, cobots have picked up the slack.
The International Federation of Robotics (IFR) reveal cobots are the fastest-growing segment of the industrial robot market. Early adopters of cobot technology in the late 2000s were adopting new ideas: automation could be safely deployed around humans; automation could be programmed and deployed by manufacturing personnel rather than industrial robot experts; and automation can be introduced and in a way that doesn’t require large-scale changes to existing floorplans, especially valuable for smaller companies.
So far, early cobot adopters have been proven right. Cobots have demonstrated usefulness in tens of thousands of successful deployments in the automotive, manufacturing, pharma and electronics sectors and on diverse applications such as as machine tending, assembly, finishing, inspection, packaging and palletizing. Cobots are now 5% of the global industrial robot market; Interact Analysis predicts that will increase to around 30% by 2027. To drive successful cobot deployment, consider seven areas.
Due to their ease-of-use and small footprint, cobots are ideally suited to do-it-yourself implementations. If your application is a simple one – such as a pick-and-place operation – then companies should feel confident in their ability to handle the deployment in-house. DIY deployments are considerably cheaper than those that require integration specialists, which is a major attraction for
Figure 1: “Cobots gave us the opportunity to grow, expand, create more jobs, and move our most valuable resources, our human resources, into new projects, where the know-how was most needed,” said Aldo Albieri, operations manager at thyssenkrupp Bilstein’s plant in Hamilton, Ohio, where UR10 cobots from Universal Robots handle machine tending, assembly, and product inspection.
“If we relied only on hiring new people, we would never be able to expand three times the size.” Images courtesy: Universal Robots
Select a collaborative robot: Consider risks and if a system integrator is needed.Joe Campbell, Universal Robots
Figure 2: To learn more on UR robot setup and programming, the engineering team at DCL Logistics in Fremont, Calif., did the free online training modules at the Universal Robots Academy and free application simulator on the UR website.
Walter Perchinumio, senior software engineer at DCL Logistics, said, “In the simulator, we saw the actual interface ... the first month that we worked with the robot was exclusively with the simulation... that ended up being the deciding factor for me.”
small companies with limited automation budgets.
Quantity and quality of the educational resources provided by different cobot makers vary. Particularly for those with little or no previous robotics experience, it’s essential to identify cobot brands that provide the online training, education and support required to implement a cobot in-house.
For more complex applications, or for any reason, the in-house capabilities don’t extend to a full deployment. Companies need to choose among three types of integration. a. A value-add distributor is the least expensive and will provide technical assistance to help facilitate a sale and will recommend configurations and peripherals. b. A Lean integrator often focuses on a specific application (welding, for example, or surface finishing) and measures integration time in weeks. c. A traditional system integrator builds a cobot-based cell from scratch, integrating all the peripherals and hardware required in a turnkey cell. Traditional integrators measure lead times in months, making for a more expensive and complete integration process.
Every application is different and presents its own challenges. Some risks are inherent to the process, such as arc welding. Other risks arise from the addition of extra complexity, such as when a vision system is added to a cobot cell. The environment also can present risks, particularly in relation to moisture and temperature levels. Factors such as how close to maximum payload you operate your cobot can impact on the lifespan of the equipment. Ask your cobot manufacturer for an application risk scorecard that can help in an informed assessment of these factors.
ROI values also incorporate overall equipment effectiveness (OEE), a measure of how well equipment is utilized versus its maximum potential when it is scheduled to run, and overall labor effectiveness (OLE), which determines how well the company uses its highest-performing personnel, adjusted for variables such as availability, throughput and quality.
This first step to ensuring painless upskilling of existing staff to become cobot operators is choosing a cobot that is high on usability. If the cobot is easy to program via teach pendant, smartphone or tablet computer, one of the main obstacles to successful upskilling has been eliminated right away.
After that, select a cobot ambassador to champion the technology. Due to the “wow” factor associated with cobots, the challenge here will likely not be finding a cobot champion, but sorting through several enthusiastic applications for the role.
Look for cobot brands that provide education and training resources. This will help streamline the training process and reduce implementation times. Quality matters, so look for well-established cobot training curriculums, especially those that result in industry-recognized certification.
Risk assessments are an obligatory part of the cobot deployment process. For guidance on completing a risk assessment, visit the A3 Robotics website (part of the Association for Advancing Automation), which provides excellent robot safety resources and training. Elsewhere, the European Unionfunded COVR project recently released a free, digital toolkit that provides a central repository of information and guidance regarding risk assessments, case studies, safety directives, international standards, and best practice in cobot safety.
Collaborative robots (cobots) can help manufacturers improve efficiency and safety. A company needs to determine early if a system integrator should help. Proper research on cobots and what they can do.
See more advice, photos at www.controleng.com/robotics.
Are your competitors accelerating with collaborative robotic implementations?
The business case for cobots is compelling, but detailed return on investment (ROI) information is required by many executives when making an automation investment. Ask the cobot supplier for an ROI worksheet and instructions on how to calculate total benefits from a cobot installation.
Cobots are platforms that enable an incredible variety of applications from precise inspection tasks to heavy duty palletizing operations, but to complete a system, select some type of end-of-arm-tooling. Not all cobots are created equal. Perform due diligence and ensure to invest in cobots that are certified plugand-play compatible with the widest range of end-ofarm-tooling, hardware and software peripherals. Seek cobot brands that understand how cobots are used in varied application-specific scenarios with complete application kits with all the software and hardware required to get started on a specific task.
Navigatigating through considerable online information on collaborative robots is the biggest challenge. Real-world case stories are a good place to find practical information about cobot deployments and outcomes. White papers cover a particular application, topic or industry. With many new entrants to the cobot manufacturing market in recent years, focus research on information from companies with a proven track record. Independent sources of cobot information worth exploring include TÜV Rheinland, A3 and the European Union-funded COVR project. ce
Joe Campbell, senior manager of applications development, Universal Robots. Edited by Chris Vavra, web content manager, Control Engineering, CFE Media and Technology, cvavra@cfemedia.com.
Teleportation has not been invented yet. But modern IT technology does make it possible to have a virtual presence almost anywhere in the world, an ability ANDRITZ has leveraged for its new Metris Performance Center.
“This is a step beyond a simple hotline or service line as we can now digitally connect our experts all over the world with the operators working at plant,” says Gerhard Schiefer, Vice President of Global Automation at ANDRITZ. “With remote support we can see in real time what an operator sees on the distributed control system screen. By collaborating via this fast connection, we can troubleshoot, answer urgent questions on processes or equipment, or even make process adjustments on the fly.”
And there is more. Combining remote
support with augmented reality and decision wall tools enables Metris Performance Center experts to be virtually inside the plant; close communication and interaction can take place as if the different parties were in the same room. The Metris Performance Center uses secure remote access to connect directly to a plant’s distributed control system (DCS) at one end and a Metris server at the other.
The Metris UX Platform is ANDRITZ’s solution for optimization and decision support. It collects data in a secure way from the mill, analyzes it and converts it into useful information.
The new Metris Performance Center now offers its remote support service to any industry, giving plant operators virtual access to ANDRITZ experts whenever they need it.
Acore-competency is a skill set, mastery of which is essential to success in your business. For example, it is accepted establishing and sustaining a healthy base-layer process control (BPC) system is a core-competency of the process industries.
A healthy multivariable advanced process control (APC) layer is also a core-competency of the process industries – or should be. That may sound like a tall order due to the historic struggle the process industry has already waged trying to master conventional model-based multivariable control technology. However, by taking stock of the lessons learned, and taking a fresh look at the conventional APC paradigm, seeing how and why multivariable control must evolve into a core-competency is a lot clearer.
Working concept of multivariable control
Chiefamongthelessons learned is the need for of a more accessible working concept of multivariable control and its existential role in process operation. A shared working concept of multivariable control is essential in order to make multivariable control, as a tool that can automate and optimize many aspects of process operation, more accessible to on-site operation stakeholders, such as process engineers, operating staff, and managers. In the past, multivariable control has usually
Table: Revise your thinking about multivariable control from lessons learned in advanced process control applications. Courtesy: APC Performance
remained in the hands of APC specialists and was mostly a black box to the on-site operating team. A more accessible working concept means the local operating team can more efficiently identify, deploy, operate, maintain and participate in multivariable control applications – with local ownership skills and a shared working knowledge of the technology being key aspects of a core-competency.
Just as a single-loop controller automates the job of making frequent valve output adjustments that are otherwise left to operators to make manually, a multivariable controller automates the job of making frequent single-loop controller setpoint adjustments.
This is how any multivariable controller, regardless of the technology employed (model-based or model-less), touches the process. It is the easiest way to understand the actual role of multivariable control in process operation – it automates the job of making
A healthy multivariable advanced process control (APC) layer should be a core-competency of the process industries.
APC layer is the equivalent to having excessive baselayer loops in manual mode highlights the need to address the lack of manual multivariable control because the battle of gaining widespread shared operating team agreement on the fundamental importance of closed-loop control over open-loop control was won long ago.
For example, many operating sites today uses some form of the controllers-in-manual key performance indicator (KPI) to measure and manage BPC health. The process industry lacks a similar metric to measure and manage APC health, but alternatives are available for adoption, such as loop intervention or bad actor loop metric (see industry’s missing metric).
Figure: The basic method operating teams have used for
Figure: The basic method operating teams have always used for manual multivariable control, which notably does not require process models or real-time optimizers. This method can be automated to provide a less fragile and more readily mastered multivariable control tool. Courtesy: APC Performance
setpoint adjustments to groups of inter-related controllers, for purposes of closed-loop constraint control and optimization.
Wherever operators are frequently observed to be busy making controller adjustments, or where operating conditions are often observed in a sub-optimal state is an opportunity for automatic multivariable control.
KEYWORDS: Advanced process control, multivariable control
Get a working concept of multivariable control.
The qualitative benefits of automatic multivariable control can also be understood as fundamentally the same as single-loop control – more timeliness and consistency, fewer alarms and constraint violations, and greater optimization. These benefits range from the inherent performance benefits of closed-loop control over open-loop, to significant operational and economic improvements, to large-scale benefits associated with conventional large-matrix multivariable controller applications.
Understand the difference between manual versus automatic multivariable control. Find the path to corecompetency with multivariable control.
CONSIDER THIS
Are you taking advantage of multivariable control for critical processes?
Coming in September, “APC for the rest of us,” a 3-part series designed to impart a practical working knowledge of APC for the on-site operating team -not just APC specialists -- for more effective collaboration on process operation, constraint management, and optimization achievement.
ONLINE www.controleng.com/ control-systems/pid-apc
When operators make setpoint and output adjustments to groups of related controllers, that’s manual multivariable control. When a multivariable controller is applied to automate these adjustments, that’s automatic (or closed-loop) multivariable control. Making frequent adjustments to sets of related controllers is an inherent aspect of almost every process operation. A more informative way of looking at processes is not whether they have multivariable control or not, but whether it is manual or automatic. This is the same way the process industry views base-layer control health – how many controllers are in automatic versus manual mode.
The lack of a healthy multivariable
Process operation engineers, who are often the main “boots on the ground” when it comes to overall responsibility for process optimization, in particular tend to observe these conditions on a regular basis and would often “trade their kingdom” for a more effective solution than frequent follow-up (or “badgering”) of operations. Multivariable control as a core-competency offers a solution.
Another key lesson is model-based control and real-time optimization are not strictly required components of multivariable control. They are part of the way conventional APC technology solves the multivariable control problem. However, there are other ways to do automated closed-loop multivariable control that are less complex and more readily mastered.
For example, users can see operating teams are routinely engaged in manual multivariable control – and do so without detailed models or realtime optimizers. This reveals an alternative path to multivariable control by automating the methods traditionally employed by operating teams to effect constraint management and optimization manually (Figure 1).
This takes a time-proven approach to multivariable process operation and adds the benefits of automation – real-time closed loop performance, built-in expertise and consistency and corresponding process performance improvements (see What is XMC?) ce
Allan G. Kern, P.E., is owner and consultant at APC Performance LLC. Edited by Mark T. Hoske, content manager, Control Engineering, CFE Media and Technology, mhoske@cfemedia.com.
Automationtechnologycontinuesto grow more diverse and available. This is good news for the planet to meet the needs of a growing population sustainably and the engineers who implement automation. More applications and processes are becoming candidates for modernization. The question to automate, or not to automate can be tricky. Consider four variables for greater automation success.
This question is a little deeper than it seems. Automation platforms technology providers supply have caught up to the universities and integrated circuit (IC) builders. It is common for modern machines to connect to the web for operational inputs like global position, temperatures and energy prices to know when they should operate to maximize efficiency in production. When automating uncommon processes, be sure to question everything about the application and available automation. Consider the assembly of a consumer good, such as an electric shaver. Perhaps doing so is unremarkable, unless the goal is to double throughput, create endless variants and reduce machine footprints; then there’s a need to know the latest technologies. Conveyors might get us there, linear motion closer, but planar motion will do the trick.
To explain this example, planar motion is a system with two parts – a “table” made of planar tiles and movers. The movers, travelling like a hovercraft, can be commanded freely around the table with a good payload. Path setups allow serial or parallel assembly, depending on the tact time and product features. These planar motion systems allow moving the workpiece to the operation instead of moving the operation to the workpiece.
In a fully-integrated architecture, the flying motion system can achieve more. Machine learning (ML) and artificial intelligence (AI) often lead to better performance, machine stability and energy savings. These results can be achieved even faster and to a greater degree when ML is implemented in a standard machine controls environment.
Select an automation technology partner with packages ready to integrate ML into a machine. Knowing what the market provides helps in evaluating an application capabilities against application goals.
If planar technology, for example, was selected as the best way to move an assembly application forward, will the technology integrated into the machine operate with minimal downtime and receive 24-hour support? While application engineers may say, “Yes,” end users often insist on ladder logic programming code. Often the time and energy an applications team put into writing code for the machine and planar motion system cannot be understood by machine users or operators.
The remedy is not to program planar motion in Ladder code or put comments in the code, though both could help. The remedy is an operator interface or human-machine interface (HMI) designed for a person assumed to have zero experience with the machine, like the boss (sorry, bosses). When the office printer jams, the boss does not crack open ladder code to troubleshoot what’s wrong. Those involved use the printer’s display, follow instructions and fix the problem.
Figure 1: For maximum flexibility and fewer handoffs, the XPlanar system from Beckhoff supports a variety of layouts for different processing and transport functions, such as rectangular floor areas (right) or in application-specific configurations (left). Images courtesy: Beckhoff Automation
Implement leading-edge automation technology, achieve a fast return on investment (ROI), make it simple for end users to support automation investments.Tom Jensen, Beckhoff
KEYWORDS: Motion control, mechatronics, control design
Examine if current automation technologies can support the target application’s goals.
This approach to troubleshooting is even more important for complex mechatronic systems. As industry moves toward the future and faces greater skilled labor shortages, it is clear companies are willing to pay more to partner with original equipment manufacturers (OEMs) that can provide intuitive ways to keep production running. Plant floor operators like keeping operations running without calling someone to open laptops and dig into code.
Consider if the end-user community can support this technology.
Calculate the automation return on investment (ROI).
CONSIDER THIS
What new levels of efficiency could automation designs achieve with new motion control technologies?
ONLINE www.controleng.com/ discrete-manufacturing/ cnc-motion-control/ www.controleng.com/ discrete-manufacturing/ mechatronics/
Aftersettinggoalsandfinding how to support a new automation concept, does the price justify the effort spent? This is a time-honored question. Looking at the planar system example, each tile that makes up the table of a planar system is essentially a drive, so the costs of building a table can get expensive, making the design cost intimidating. The same model applies to linear transport systems and robotics motion control. Because planar movers have 6 degrees of freedom (DoF)
and can be the size of the piece being assembled, the cost is offset in a big way. Planar systems use the mover to do the work of the robot, meaning you can replace the large working envelopes that robots require for assembly with simple, space-saving, single-axis devices. This increases capacity (or peripheral density) and adds options for new features in a very small footprint machine. It provides reduces changeover times adding value for most end users.
Consider replacing walking beam machines with linear motor systems. New advantages include flexible parallel operations, collation and control of tact time in a smaller-frame machine. There are cost tradeoffs. More than enough value justifies any cost differences.
Limiting handoffs between processes or machine modules with machine design make lives easier. Many production problems originate with jammed conveyors, worn or loose belts, or incorrect operation because a product is out of position. Imprecise or halted motion affects quality with reworks or scrap and takes a lot of personnel to troubleshoot, identify and remedy such breakdowns. Robotics can improve the handoffs between machine modules and adds cost, footprint and complexity.
By designing around linear motor and planar concepts, the goal is to accomplish all assembly operations while the workpiece remains on the system’s mover. This non-linear manufacturing technology doesn’t have to pass off the workpiece between modules. Instead, the movers carry the workpiece through multiple processes, eliminating handoffs that used to be necessary. This improves overall ROI and machine uptime since operators avoid tweaking conveyors, timers and working changeovers.
By using examples in linear and planar motion, understand how to better move the workpiece to the operation rather than move the operation to the workpiece. By embracing new automation technologies, OEMs and manufacturers can rethink what is possible, shatter conventional limitations in machine design and create a new class of machines designed to solve many new challenges.
ce
Tom Jensen is assembly industry manager, Beckhoff Automation LLC. Edited by Mark T. Hoske, content manager, Control Engineering, CFE Media and Technology, mhoske@cfemedia.com.
‘Imprecise or halted motion affects quality with reworks or scrap.’Figure 2: Using the XPlanar system from Beckhoff, the original equipment manufacturer (OEM) Plasmatreat effectively moves workpieces for treatment processes on planar movers and keeps the mechanically and electrically complex plasma jets in a fixed position.
Smart control technologies are fulfilling a cross-industry need for more adaptable, future-proof industrial solutions by enabling more efficient, sustainable, and safer manufacturing. To combat the loss of employees to retirement – ultimately creating a severe industrial knowledge gap – automated technologies are helping to recruit and train the next generation of industrial workers. Explore how new automation technologies enhance workforce safety and performance through more adaptable and accessible system assets. Learn how industrial facilities can use new technology to automate workflows, gain greater awareness of operational risks, and have a more comprehensive view of process inefficiencies. Gain insight on long-term benefits of remote operations solutions such as streamlining communications through a dedicated server, allowing employees to connect to systems via a virtual private network, regardless of location.
For several decades, industrial organizations have been required to be agile and innovative, designing systems and processes to be flexible and efficient to meet fast-changing demands. A growing number of companies use automated systems to collect and dis-
tribute data. This helps internal and external stakeholders monitor and optimize productivity and safety. The automation revolution is raising interesting questions about how it is transforming the industrial workforce and about what it might look like in the future.
Most of the industrial sector understands its workforce is changing due to demographic shifts, technological advancement and recent challenges. Smart control technologies bring new ways of working with more efficient and sustainable manufacturing.
Find effective advanced automation Industrial operations of all sizes are embracing various forms of new technology as they strive to lower costs, help to increase production and reduce response times. In this environment, plant owners seek practical advice for applying advanced automation solutions in a way that’s beneficial to their operations and workers.
The management of a workforce consisting of employees, contractors and visitors is important for manufacturers. Dealing with the growing scale of operations; increasing safety, security and regulatory requirements; and optimizing safety and compliance while maintaining operational efficiency are all crucial challenges. Global health concerns are forcing plant operating companies to consider new strategies for maintaining safe, reliable business continuity with reduced on-site staff. Many plant owners and operators have been reluctant to apply remote enablement technologies, primarily because operations were performed in a fixed control center at the industrial site. The current business climate has transformed plants and processes with deployment of remote operations strategies. Despite automation advantages, industrial organizations need a more efficient approach to control system engineering and implementation, one that can be adopted incrementally and used interchangeably with existing systems and infrastructure.
The fourth industrial revolution is altering the way modern industrial plants are run. New technology, such as the Industrial Internet of Things (IIoT) and machine learning, aims to make manufacturing safer, more efficient and faster. Real-time data collection and autonomous operations that can be remotely managed have led to workforce reconsiderations.
The automation revolution is changing how technology is implemented and how workers are trained. Companies need to rethink everything to thrive.
The industrial sector is losing millions of employees to retirement. Seasoned workers are taking decades worth of expertise with them, and companies must find ways to use automation to help bridge the resulting knowledge gaps. To stay competitive, they need to leverage automation as a recruiting tool and target millennials, a tech-savvy generation who will be attracted to smart factories’ capabilities. For every industrial firm, it is extremely important as workforce transitions, to retain the knowledge of production processes from experienced personnel and use the knowhow to build expertise in newer workers.
Smart manufacturing is realized when industrial workers use innovative automation software solutions that enable data gathering and analysis. Software tools such as digital twins allow users to simulate equipment and processes without having to invest in hardware to validate a proof of concept. Not requiring experts to be physically on-site to manage operations enhances flexibility and further safeguards worker health and safety.
Modern industrial facilities are highly dependent on the workforce. They need to implement new technologies to enhance operational efficiency and security through seamless communication of data, automated workflows, smooth transfer of domain knowledge and digitalization of operational processes.
Plant owners have a keen awareness of the need to comply with changing economic and regulatory requirements and confirm all employees are safe, well trained and are up-to-date with certifications.
Industrial sites embracing the latest digitization initiatives can do more with limited resources. They can create an environment that enables employees and contractors to perform tasks using proactive, supportive processes. They can leverage technology investments to help improve the productivity and efficiency of workers through accessible, intelligent data that fuels real-time decision-making.
An end-to-end workforce management solution can help bolster safety and productivity by automating policies, establishing proactive compliance processes and integrating training into the workflow.
The current breed of digitized workforce management solutions uses powerful embedded analytics to advance the context, awareness and analysis of key decisions at the time they must be made. They employ machine-learning algorithms to detect meaningful trends within vast quantities of data and make highly relevant recommendations. Industrial sites can use e-permitting solutions to gain instant visibility of permit to work status for permit controllers, emergency response teams and facility management. They provide a paperless means to raise, submit, review, approve, reject, print and close out permits through an electronic workflow. It becomes much easier to visualize where all work in the facility is being performed to gain a full picture of the cumulative operational risk, improving workplace communication and safety.
Automation technology suppliers have developed augmented remote operations solutions, which provide rapid, flexible and secure deployment of remote operations strategies for critical industrial facilities. Prepackaged remote solutions streamlines the implementation, testing and certification of remote access points for monitoring and controlling process industry sites. These solutions can be tailored to meet specific operational needs and unique topology and information technology requirements.
With remote operations solutions, users can employ the same human-machine interface displays, configurations and menus as a normal console station. Pre-built virtual machines can be downloaded and deployed in virtual infrastructure and configured on-site to meet a facility’s needs. A dedicated server is used to augment the plant distributed control system and provide remote operations capabilities to authorized stakeholders. One server can host multiple concurrent users of control room stations, enabling operations other on-site areas, from another operations center, or by employees working from home who connect to the system via a virtual private network connection to the corporate IT network.
Augmented remote operations can be used by plant engineers and process experts to monitor production processes, provide operational support and rapidly troubleshoot problems as needed, wherever they are. A remote operating station, replicating the control room console HMI, allows temporary control of the plant during emergencies. The remote workstation also can be used for incident investigations and process hazard analysis. ce
Joe Bastone, director, product marketing for Experion at Honeywell Process Solutions. Edited by Chris Vavra, web content manager, Control Engineering, CFE Media and Technology, cvavra@cfemedia.com.
Experion ARO can quickly provide remote operating locations with very similar capabilities to how the operator works normally using Honeywell Orion Console to maintain operations in case of an emergency.
KEYWORDS: automation, skills gap, workforce development
Automated technologies are helping to recruit and train the next generation of industrial workers. Many companies face a knowledge gap deficit that automation can help address and help younger workers grow.
Many organizations want a more efficient approach to control system engineering integrated with existing systems and infrastructure.
See more on simplifying technology with this article online at www.controleng.com.
How is your company preparing for the automation revolution?
Manufacturing automation is embracing digital transformation and the system integration plays a key role in facilitating it and integrating information technology (IT) and operational technology (OT)
ture, using secure access to the customer’s virtual private network (VPN) or even being issued customer-supplied engineering tools (computers) for remote access.
Manufacturing automation is seeing a shift from controls type projects to informa tion solution, or digital transformationtype projects. The Industrial Internet of Things (IIoT) supports this digital trans formation and falls under its umbrella. John Cunningham, director of business and industrial IT, RoviSys discusses the role of the system integrator in the digital transformation, safe remote access, better band width and resiliency in manu facturing. RoviSys is among CFE Media and Technology’s 2021 System Integrator Giants.
CFE Media: How has COVID19 and remote monitoring and/or remote automation applied to the way you engage with customers? How has the pandemic changed the way you approach remote access/remote monitoring?
John Cunningham: We are finding that the pandemic is accelerating a move toward more remote access that was already in movement before the pandemic began. Customers are being forced into more remote access as corporate policies are limiting the number of outsiders into plants, and even how close employees can physically be to each other within the plant. They are also evaluating — in some cases moving more quickly to digitalize — systems that had limited or no remote access previously.
Customers with a strong information technology-oper ational technology (IT-OT) internal connection are more methodical about this process than smaller companies or those who have not previously connected their IT and OT groups. With those companies more mature with this approach, we are often integrated into existing infrastruc
For customers who are new to working remotely, we are helping them see the need for secure remote access and helping to define how that access can be used and what can be done remotely. This includes not only the technology, but also the policies and governance model for scalability.
We are also working closely with our customers to have them assign plant personnel to serve as “boots on the ground” for the work that must be done onsite. We engage in training and frequent meetings with the site person nel to get them comfortable with the new roll and to assure that they understand what needs to be done and how to do it. This process is working best when customer leadership commits to this model.
We are anticipating the new normal after the pandemic will continue to include more remote access than previ ously. Reduced travel time and expenses, as well as greater engagement of site personnel are seen as benefits that customers want to maintain.
CFE Media: How do you provide asset visibility, real-time health monitoring while ensuring access and cybersecurity?
Cunningham: The need for remote access, along with the ongoing flood of security breaches, have made OT security a top priority for many of our customers. We stress the need for OT security for all customers, but especially those who are expanding their remote horizon. We often find customers who had ad-hoc, insecure remote access previously. The current focus has raised the need
The need for remote access, along with the ongoing flood of security breaches, have made OT security a top priority for many of customers.
for security, and customers are more frequently paying attention to limiting and securing access.
We generally try to work with the customer’s IT team to see if they have already addressed remote access and mon itoring on the enterprise side of the business. If so, we will work to integrate with the tools currently in place and where practical, extend their use into the OT space. We partner with several companies that offer excellent tools that extend visibility and health monitoring. Many of our customers have legacy systems that do not lend themselves to remote moni toring and accessibility. In these cases, we work closely with the customer to determine their comfort level and budget to extend visibility. Many of these customers choose not to make the necessary changes and look to return to business as usual as soon as they can.
We are finding that the key to successful, secure remote access is tight coordination between the IT, OT and infor mation security groups. Without the buy-in and support of all three of these groups, solutions are prone to haphazard implementation and limited supportability and scalability. We work closely with all three groups for the strategy, design, implementation and support of the security-conscious infra structure. In these cases, we are finding that the infrastruc ture and security elements are becoming integrated into the manufacturing site and are valued as highly as the controls and information systems they are protecting.
CFE Media: How can system integrators support asset visibility, real-time health monitoring and cybersecurity?
Cunningham: SIs should serve as the experts for these solutions and often need to act as the liaison between the customer’s IT, OT and information security teams. SIs should remain independent of any particular product or technology, working with what the customer may already have in place if it is an appropriate solution.
SIs should focus on the “insurance” nature of these solutions and on the return on investment (ROI) associ ated with them. SIs should be able to support the needs of all three groups (IT, OT and InfoSec). They should be able to develop the strategy for the solutions, design them, implement them and support them. SIs should ide ally be able to help the customer develop and maintain policies and governance models for the ever-changing environment into which the solutions are to be deployed.
SIs also should be a primary resource for adoption of the new solutions in the manufacturing environment. The operations team will often have limited or no experi ence with the new solutions and may initially resist the changes. Adoption includes early engagement of site stakeholders, keeping them informed along the journey, training in new systems and technologies and help ing them see how their involvement is essential to the acceptance and value of the solutions.
CFE Media: In your opinion, what is the role of the system integrator in digital transformation?
Cunningham: This question was partly answered in the question above about how SIs can support the new solu tions. A few other thoughts about the role of the SI in digi tal transformation include:
• Engage as early as possible with the customer to understand the thought process and purpose of a digital transformation initiative
• Understand what the customer needs are; what is the customer strategy? Who is driving digital transforma tion on the customer end? What is the end goal of the digital transformation initiative?
• Help facilitate discussions that span the customer’s organization to develop a functional strategy for digital transformation implementation
• Help the customer understand and be driven by ROI
• Be the expert; provide support at all phases of the digital transformation journey
• Be independent of any particular product or technol ogy; focus on the issues the customer is trying to address and let the technologies follow from there
• Avoid digital transformation for its own sake; customers can become enamored with digital transformation with out thinking through what it means for them, what the cost will be and what cultural changes will need to take place for success
• Act first as trusted partner, then as a vendor.
Jack Smith is a CFE Media and Technology content man ager, jsmith@cfemedia.com.
KEYWORDS: Applying automation, system integrators, IT/OT integration
Understand how system integrators support asset visibility, real-time health monitoring and cybersecurity.
Examine how COVID-19 and remote monitoring and/or remote automation has changed system integrator interac tions with customers.
Determine the role of a system integrator in digital transformation.
ONLINE
www.controleng.com/system-integration
CONSIDER THIS How are you building on the remote monitoring, automation, and cybersecurity gains made during the COVID-19 pandemic?
As cybersecurity attacks on industrial processes become more common, the number of companies taking active steps to protect their critical con trol systems is growing. Advisors and consultants — internal and external — often pro vide key personnel with a list of requirements and recommendations on how to improve overall secu rity. This list almost always includes a requirement to “harden” industrial computers.
Hardening is a process where a computer is made more resistant to cyber intrusion from mali cious attack and from accidental infection. Hard ening acts by remediating known vulnerabilities, by positioning the system to reject certain class es of attack, and by documenting system activities.
An industrial computer is never going to be completely impervious to intrusion, but the hard ening process gives industrial systems addition al layers of cybersecurity protection. It is worth exploring six different areas of hardening, each of which deserves an in-depth study. However, as a starting point, consider the following overview:
Every attempt to protect a system from a cyber attack is imperfect. Every element of hardware and software has the potential to contain vulnerabilities. Manufacturers release updates and patches to reme diate potential and known vulnerabilities. Apply ing these patches and updates in a timely manner is one of the best ways to keep a computer resistant to attack. A machine continually grows more vulnerable when existing exploits remain unpatched, and when the time since they were identified has increased.
In the industrial world, it is often impractical to halt production to apply patches on a weekly basis, but having a planned schedule for patch application, perhaps quarterly, is recommended. It is also impor tant to recognize not every patch should be immedi ately applied. When original equipment manufacturer (OEM) control software is involved, the risk of an untested patch causing a failure in industrial soft
ware can be high. Most OEMs have their own testing program that validates operating system (OS) patch es against their own equipment, and sometimes OS patches drive corresponding updates to OEM systems.
Like any computer, industrial PCs are vulner able to individuals attaching devices that contain infected data. Even without malicious intent, an operator who wants to show a coworker pictures of their kids might plug in a thumb drive. A wellintentioned engineer who needs to move a data file might use a portable hard drive rather than following the proper secure file transfer methods. Systems that evaluate files for danger are frequent ly out of date, so it can be more straightforward to prevent access to new file systems completely. It doesn’t matter whether the device is infected or not if the OS refuses to recognize the files.
It is not uncommon to find evidence of connections from industrial comput ers to untrusted networks. Whether this is Wi-Fi being connected to a hotspot to watch YouTube, or an iPhone being plugged in with the intention of charg ing it, any network connection other than an authorized industrial control network is a high risk. Once the designed network connections are established, all extra net work connections should be prevented.
The actions of a computer are based on the programs that run on it. Only the programs that are planned for normal use should be allowed. Authorized users should be the only ones allowed to exe cute the required programs. Unauthorized users must be prevented from executing
Hardening is a process whereby a computer is made more resistant to cyber intrusion from malicious attack and from accidental infection. Companies should update and patch their systems as often as they can.
Recording activities, hosting firewalls and preventing untrusted use are also key steps to hardening an industrial computer.
See more stories about industrial cybersecurity and network security at www.controleng.com.
What is your company doing and not doing when it comes to computer hardening?
Computer hardening helps make systems resistant to cybersecurity attacks. Six tips are highlighted to help engineers respond.
untrusted or even trusted programs. Modifying files on disk also should be limited to authorized processes and users.
5. Host firewalls to prevent untrusted network traffic to industrial PCs
Host firewalls are programs that run on the com puter locally that prevent unauthorized network com munication. They can limit the types of data that can be exchanged, the protocols used for the exchange, and the endpoints of the conversation. Network fire walls should prevent unwanted traffic across the loca tions where the firewalls are physically installed, but it is generally not feasible to install them adjacent to every individual computer. Host firewalls on every computer will prevent unwanted traffic between com puters that are in the same physical network zone.
6. Log to record activities, for realtime detection, post-event auditing System activity logging does not necessarily harden an individual computer by itself, but it can help with the overall hardening of the systems that include them. All activities of note, such as network events, user authentication failures and successes, file system updates and many others should be logged to a location other than on the local computer. A cen
tralized event management system can evaluate the logged events as they happen to detect potentially negative activities and prompt protective action. A historical record of events can assist in the evaluation of an attack after the fact so that specific vulnerabili ties can be identified and remediated.
Hardening in all six areas can be implemented to some degree with tools and features that are built-in for most OSs. This task requires specific knowledge of the OS, the security requirements and how both interact with the industrial software running on each machine.
Security software can be purchased or licensed to perform the tasks in a more user-friendly manner. Some industrial facilities have engineering staff with the required skillsets to implement and maintain an asset hardening program, but many do not. Where resources are limited, a third-party partner can assist with both the up-front effort required to bring the system to the desired state and with the long-term maintenance effort.
When using a third-party partner for implemen tation and maintenance and when using commercial security software, recognize that local engineering staff still need to be involved with operating and mon itoring the system. Hardening industrial computers is not a one-time activity; it is a continual process that must be constantly reviewed and updated.
Robert Henderson is a principal engineer with Maverick Technologies, a CFE Media content part ner. Edited by Chris Vavra, web content manager, Control Engineering, CFE Media and Technology, cvavra@cfemedia.com.
‘All activities of note should be logged to a location other than on the local computer.’
Hardening acts by remediating known vulnerabilities, by positioning the system to reject certain classes of attack, and by documenting system activities.
Courtesy: Maverick Technologies
5G is a broad term describing a range of different technologies and implementa tions and can mean many different things to many different people. Even among the major consumer cellular providers, the 5G that each provides can be different from the next.
Generally these offerings span either: lowband, mid-band, or high-band. There are benefits and trade-offs for each. Low-band 5G yields better penetration and distances, but at lower speeds and bandwidths. High-band 5G provides more perfor mance but at the expense of longer distances.
For these reasons, high-band 5G is appealing to industrial automation where distance concerns can be overcome with many cells while surpassing tra ditional Wi-Fi performance.
There are three main categories of use-cases for 5G. Of course there will be applications which span more than one category; hence the broad appeal of 5G.
1. Extreme mobile broadband (eMMB). Use-cases here include those requiring very high bandwidth and data rates. Applications include high-definition video streaming.
2. Massive mobile machine type communica tions (mMTC). Use-cases here include those requir ing a large amount of devices, typically in dense proximity to one another. Applications include the Internet of Things (IoT) or smart cities.
3. Ultra-reliable low-latency communication (URLLC). Use-cases here include those requiring high determinism and mission criticality. Applica tions include self-driving cars and industrial auto mation. It is here where 5G becomes applicable to industrial networks like Profinet.
The focus on 5G in Industry at the moment is on the ability to create private networks. A private 5G network does not rely upon the infrastruc ture of traditional telecommunication companies. Instead, it is installed and configured by the user locally.
In early 2020, a collaboration between Audi and Ericsson achieved 3ms cycle times with 1ms latency running Profinet and PROFIsafe over 5G. Such timescales also are a requirement for factory automation and enable use cases like automated guided vehicles (AGVs) or autonomous mobile robots (AMRs).
There are three main categories of use-cases for 5G: extreme mobile broadband, massive mobile machine type communications and ultra-reliable lowlatency communications. Cour
KEYWORDS:
5G
There
Because PROFIsafe uses the black channel principle, no special configu ration is required to enable function ally safe communication between PROFIsafe devices and control lers over 5G. ce
This article originally appeared on PI North America’s web site. PI North America is a CFE Media content part ner. Edited by Chris Vavra, web content man ager, Control Engi neering, CFE Media, cvavra@cfemedia.com.
tesy: PI North America
industrial automation where distance concerns
can surpass
Customersaremakingincreasing demands from machinery suppliers, which leads to greater customization, ease of use and integration to the customer plant and ecosystem. Machine reliability and lower total cost of ownership are among other needs. Software tools seamlessly integrate the machine development silos of mechanical, electrical, software, and simulation into one platform.
Scott Felber, NX product engineering software marketing manager, Siemens Digital Industries Software, in a June 30 Control Engineering webcast, “Accelerate machine designs, speed to market, collaboration, digital twin,” is expected to explain insights from customers and share recent research results to help industrial machinery companies with digital twin adoption.
KEYWORDS: Machine builders, industrial digital twins
Digital twins address transformation industrial trends.
Hyperautomation, machine feedback from sensors; lowcode cost reductions can help machine builders and their customers.
Overcoming obstacles to digital twins can accelerate time to market.
How are you using digital twins to address industry demands and increase competitiveness?
ONLINE www.controleng.com/webcasts/ accelerate-machine-designsspeed-to-market-collaborationdigital-twin/ www.controleng.com/ iiot-industrie-4-0/
Felber outlined several transformational trends that mark a significant turning point in machinery evolution, helping to reshape the engineering, manufacturing and service operations for most machinery manufacturers.
A shift toward personalized products and customized services is challenging machinery companies to design and build machines that support expanding product mixes and more rapid and frequent changeovers, Felber said. Because consumer preference changes are more immediate, there is added pressure to innovate quickly and compress delivery schedules.
For example, a potato chip package has the potential for multiple variants, which help lead to an explosion of complexity, in size, shape, packages per box, recyclability considerations (output of machine) and regional flexibility including (flavors, size weight).
Industrial component suppliers are quickly embracing Internet of Things
(IoT) enabled technologies in products, and machinery manufacturers are on a steep learning curve to take advantage of petabytes of data that can be generated from today’s machinery. This has changed the landscape for electrical and controls automation engineers, from huge increases in input/output (I/O) channels, new communication protocols like 5G, to building intelligent programming that provide interactive and granular device control.
The trend of hyperautomation requires vast amounts of data and cloud-based analytics to accelerate learning about machine behavior and performance to automate machine functions. Adding sensors may not be enough. Capabilities are needed to analyze the explosion of complex data being monitored.
For example, Felber said, even a simple fabric weaving machines are precision machines that can increase throughput by taking advantage of automation and incorporating feedback from speed, vibration, noise and temperature.
Hyperautomation also is enabled by low-code tools that can mine data analytics for many business processes – manufacturing optimization, as well as engineering reliability and cost reductions.
Leaders in the machinery space, the disrupters, are expected to embrace three key concepts to turn complexity into a competitive advantage.
These are the most comprehensive digital modern, adaptable, personalized solutions, and a flexible open ecosystem.
Research conducted with Control Engineering sought to understand the biggest roadblock to adoption of the digital twin/digitalization. Largest three replies were corporate culture, initial cost and complexity of the solution at 18, 17, and 15%, respectively. Responses in the next tier were: “tools currently in use” and “adoption is underway” at 7%, and training at 6%.
By using an integrated digital twin software based
A survey of industrial machinery companies explores issues with digital twin adoption. Machine builders use digital twins to increase efficiency of machine design processes to get machines running in less time at lower cost.
on one model eliminates the need to re-enter data into other systems, Felber said, for an efficient, accurate business process. The digital twin lower costs to manage intellectual content across assemblies, part manufacturing, and commissioning. This helps maximize revenue with proactive service, replacement part response, and upgrades to the machines.
A design software platform has tools for modeling, electro-mechanical design, including design input from simulation and manufacturing teams, managing the process and data across multiple
domains and disciplines, using computing power based on a set of key inputs and outputs, and embracing additive manufacturing for more than prototyping.
A multidisciplinary platform serves the enterprise. The webcast provides more information and trends on digital twins. ce
Edited by Mark T. Hoske, content manager, Control Engineering, CFE Media and Technology, mhoske@cfemedia.com.
A holistic digital enterprise can help design products and the production process, realize product manufacturing and manufacturing operations, and optimize product utilization, plant performance maintenance in a continuous product and production improvement cycle. These are among trends discussed in the June 30 webcast: Accelerate machine designs, speed to market, collaboration, digital twin. Siemens Digital Industries Software NX design platform can help throughout the product lifecycle and production. Courtesy: Siemens Digital Industries Software
In a world that is constantly changing, we understand the need to have information for your business at your fingertips. ABB is offering a webinar series that will address today’s industry challenges and opportunities along with solutions and tips on how to overcome them.
The ABCs of VFDs
Learn the basics of variable frequency drives from ABB’s Larry Stanley. Register: https://campaign.abb.com/ABCofVFD
ON DEMAND
Selecting the right motor to be driven by a VFD When running motors with VFDs, motor selection is critical to reliability and motor life. This workshop will provide tips on proper motor selection to ensure proper performance when powered by a VFD.
Register: https://campaign.abb.com/extend-motor-life-driven-by-VFD
Which motor do you need for variable speed applications?
In this workshop, Rick Kirkpatrick discusses tips and guidelines for choosing the right motor for your variable speed application beyond speed, torque, power and voltage. Register: https://campaign.abb.com/choosing-motors-for-variable-speed-applications
baldor.abb.com • 479.646.4711
The Beckhoff team works hard to design and deliver the most advanced automation and controls technologies available. Of course, that is only half the battle as offering best-in-class education and training is also crucially important. A wide range of online resources are available 24/7/365 from Beckhoff for engineers:
Free E-Learning Portal
Beckhoff USA offers an extensive e-learning portal with a range of presentations on topics related to industrial automation – and you’re invited to join! These useful educational resources are free and open to the readers of Control Engineering magazine. Multiple classes are available, including topics from all Beckhoff product families: automation software, industrial PCs, I/O, drive technology and advanced mechatronics.
Each presentation is followed by a quiz to reinforce the topics covered and gauge what you’ve
learned. No Beckhoff hardware is required to participate, but there are modules that permit students to use their own Beckhoff equipment during the training.
Register for an account at learn.beckhoffus.com and start learning today!
Educational Webinars Pressed for time? Beckhoff offers many webinars throughout the year on a wide range of interesting topics, particularly automation and controls programming, industrial Ethernet applications, tips for designing world-class motion control architectures and much more.
Visit www.beckhoff.com/webinar to learn more. Don’t forget to visit the webinar archive to view the complete history of Beckhoff webinars anytime.
TwinCAT Engineering Environment Programmers and engineers can download the base engineering module of TwinCAT 3, the leading PC-based automation software at no charge from Beckhoff (TE1000).
Visit www.beckhoff.com/twincat3 to quickly download and install TwinCAT 3 on your programming and development PC today!
For more information: www.beckhoff.com
Technical resources you need from an automation vendor you can depend on
Whether you are a beginner or an advanced user, CODESYS North America has the right training to take your knowledge to the next level. First hand tips and tricks, online or face to face.
Our courses are instructor-led and alternate between lectures and hand-on exercises. CODESYS trainers draw on decades of experiences.
This training is targeted for individuals who are new to CODESYS and need to get started with a good foundation. Through a mix of lectures and hands-on exercises, this class teaches the basic features and concepts of CODESYS and the IEC 61131-3 programming languages. codesys.us/training-detail/t/codesys-v3essentials-training-north-america.html
This training is targeted for experienced control engineers transitioning to CODESYS, or for
engineers wishing to take their knowledge of CODESYS to the next level. It combines basic and advanced training modules to give participants a comprehensive understanding of the capabilities of CODESYS, alternating between lectures and hands-on labs.
codesys.us/training-detail/t/codesys-v3intensive-training-north-america.html
Transitioning from Rockwell to CODESYS
This class is targeted for ControlLogix® PLC programmers who are transitioning to CODESYS V3. Through a mix of lectures and hands-on exercises, learn how your existing knowledge can be applied in CODESYS.
codesys.us/training-detail/t/transitioning-fromrockwell-to-codesys-north-america.html
CODESYS is the global market leader of manufacturer-independent IEC 61131-3-automation software with over 5 million device licenses sold worldwide. More than 500 control system manufacturers and tens of thousands of companies worldwide use CODESYS’ products.
The CODESYS
is the basis of a comprehensive suite that covers the entire software side of automation including Industrial Internet of Things (IIoT), communication, Soft PLC, motion, drives, CNC, robotics, redundancy and visualization.
Accessing machines at remote sites over the Internet can be a challenge since firewalls block messages that originate from the Internet. Although it is possible to open up ports in the firewall by using Port Forwarding, IT professionals are reluctant to compromise the security of their network and usually decline this type of request.
Without permission from the IT department, the systems integrator is left with few options. One solution to this problem is to incorporate a Virtual Private Network (VPN) service, such as Contemporary Controls’ RemoteVPN subscription service.
Setting up an OpenVPN server on your own is not trivial. It typically involves setting up a root certificate
authority and generating certificates and keys for the OpenVPN server and for each client device that intends to connect to this server. However, the EIGR-V router has a built-in webpage interface to generate certificates and keys for VPN client devices, without requiring users to download software or having to learn the complexities of setting up a VPN.
One EIGR VPN router set to OpenVPN server mode and assigned a fixed public IP address resides at the client site or any other convenient site and uses
Example of Remote Monitoring with Self-HostedVPN
the Internet for communicating to OpenVPN clients without any cloud service involved.
The Self-HostedVPN solution provides secure, remote access to any IP device by just using the VPN IP address for a device. There is no additional requirement to setup Network Address Translation (NAT) or Port Forwarding on the client routers, as they initiate outbound connections to the OpenVPN server. Furthermore, the OpenVPN client devices only require internet access – there is no requirement for a static or public IP address.
Digi-Key Electronics offers a wide selection of automation products from the brands you depend on, including KUKA Robotics, Omron Automation and Safety, Banner Engineering, Festo, Phoenix Contact, and more. Easily navigate Digi-Key’s automation and control landing page with a visual search tool that features the ability to dive into specific product families. From end of arm tooling to PLCs or even a light curtain, the enhanced search functionality allows you to quickly navigate to the product category of your choosing.
The new Design and Integration Services page at www.digikey.com provides an expansive list of integration partners who can support you from conceptualization and planning through testing and deployment. Access automation integration experts and start collaborating on your next project today!
Digi-Key’s Marketplace gives customers access to millions of new products and services, including bare PCB boards and industrial robotics. This added solution from the same website serves customers in applications such as industrial automation, test and measurement, IoT solutions, and virtually all things related to technology innovation.
Boost your drive for innovation with Digi-Key’s vast selection of products and solutions:
• Automation and Control Product Selector –Quickly find the automation products you need
• Design and Integration Services – Access a network of experienced system integrators to develop automation solutions from concept to commissioning, testing, and beyond
• STARTUP Site and Resources – Leverage Digi-Key’s industry experience and network to advance your idea from prototype to production
• Articles and Blogs – Discover industry insights in new products and applications
• White Papers and App Notes – View the latest technology news, product information, and supplier updates
• Calculators and Conversion Tables – Get the answers you need with Digi-Key’s wide array of online conversion calculators
The first step to implementing digitization, IIoT, Industry 4.0 and other modern technologies is proper use of smart instrumentation – and that starts with proper training.
Smart instruments can provide a wealth of information via HART, EtherNet/IP and other digital interfaces, but most plants are not using these communication protocols. Surprisingly, a vast majority of units purchased and installed still communicate via 4-20 mA analog output of the process variable, disregarding the digital interface capabilities.
In many cases, plant technicians and engineers do not have the proper training for these smart instruments. A skills gap often exists that can only be filled with specific trainings. That could include internal onboarding and mentoring, informal institutional
knowledge absorbed organically, online eLearning, classroom instructor-led events or some combination of them all.
IIoT and digitization can be challenging to understand. However, there are modern training classes readily available from most instrument manufacturers where they teach about advanced instrumentation, such as self-calibrating RTD temperature transmitters and flowmeters and self-verifying measuring electronics.
Endress+Hauser has a training group dedicated to offering training solutions that are tailored
to each customer’s needs. Some solutions include on-demand technical courses, on-site training where experts come to your location, or hands-on training at Endress+Hauser’s full-scale PTUs (Process Training Units).
In the PTU, students can see how data is generated, transmitted and processed in real time.
A long-term strategy for IIoT adoption will be difficult to implement if plant personnel aren’t properly trained– these learning experiences are designed to empower and equip end users to step into digitization with confidence.
Learn more about Endress+Hauser’s training opportunities!
www.us.endress.com/training
Most suppliers of HMIs and PLCs claim that their software is easy to learn and easy to use. The real test comes in when you actually get to do it.
We introduced EZTouch in 2001 with a simple aim for a new user to learn the software from scratch in less than an hour and create a fairly complex screen in 10 minutes or less. No going to a school like Rockwell requires, nor spending endless hours reading manuals. We created a simple design interface to add pre-built objects to a screen.
You have a quick selection on which EZTouch panel, what PLC protocol among hundreds including DH+/RIO, and you start placing the objects on the screen. There is an extensive symbol library to pick objects from. You can also simulate your HMI screens on the computer itself!
A recent study of plant users of HMIs found that a typical user makes changes to the HMI screens at least 6 times during the first three months. EZTouch patented on-line edit allows screen modification
without shutting the machine down. Changes are made on the fly. This feature is enhanced by our new miniWIFI, allowing you to program up to 50 feet away and with no cables.
EZPLC offers a similar free-flowing drag-n-drop programming software. No restrictions, just draw the ladder. Try inserting an e-stop contact in an existing rung in any other PLC programming software and you will quickly find out that not every programming software is the same. In addition, our integrated software with no annual fees with free life time upgrades, is common to all our HMIs, PLCs and EZTouchPLCs.
Order your FREE KTD (Knowledge Treasure Drive) to see live examples. www.ezautomation.com.
every HMI/PLC Programming Software is the same!
Read below: 10 minute screen design, on-line edit, drag-n-drop PLC software.
When specifying enclosures, a key consideration is the material to be used. Stainless steel enclosures offer several key benefits – corrosion and chemical resistance being primary.
Due to the nature of the manufacturing environments, there are a number of industries particularly suited to using stainless steel boxes. These include Oil & Gas, Water Treatment, Wastewater, Food & Beverage, Pharmaceutical, Mining, Marine applications, Roadside (salt exposed) and many more. When working in any of these industries, it is critical to research the corrosion resistance requirements in advance.
Hammond stainless steel enclosures generally carry UL/CSA Type 4X and IP66 ratings – while similar, these 2 ratings have differences. The North American Type “4X” rating indicates two separate things – the “4” indicates
ingress protection of Type 4 testing (65 gallons/min hose-down for minimum 5 minutes) and the “X” indicates additional salt spray resistance for corrosion purposes. The European “IP66” rating is similar for water ingress testing, but has no guarantee of corrosion resistance.
There are generally 2 types of stainless steel used for electrical enclosures, 304 and 316L. Type 304 stainless steel is most common for enclosures. Type 316L has the addition of molybdenum up to a maximum of 3%. Molybdenum increases the corrosion resistance against many harsh industrial
chemicals and solvents and inhibits pitting caused by chlorides. The 316L grade can withstand corrosive attack by potash, sodium and calcium brines, hypochlorite solutions, phosphoric acid, sulfite liquors and sulfurous acids. Type 316L is commonly specified in paper, textiles, bleaches and rubber industries. It is also common for marine applications.
For CAD files and detailed specifications on Hammond’s Stainless products visit: www.hammfg.com/stainless
Hammond Manufacturing offers thousands of enclosures to suit your needsLenze offers a comprehensive, future-proof portfolio that covers the control level, the field level, and the electromechanics, and ensures standardized data communication right up to the cloud level. Our solutions enable you to meet all your machine development requirements easily and efficiently, with the greatest possible flexibility. You can rely on:
• Scalable hardware in a comprehensive and open automation platform
• Modular software for efficient software engineering
• Open networking thanks to the use of market standards
• Solutions that meet the requirements of digitalization
• A thorough understanding of your machine from experienced experts in your sector
Our newest portfolio additions:
The i950 Servo Inverter is a match for any operational scenario thanks to three different modes of operation. It can be freely programmed or serve as an actuating drive under a CiA402 motion control, but the most common mode of operation is via parameterization using preconfigured technology applications.
Lenze’s X4 Remote, offers an integrated and readyto-use solution for cloud-based remote services. Easily
set up and configured, machine manufacturers can confidently offer reduced downtime and increased productivity, making their machine fit for the future.
Our new i550 protec Frequency Inverter, well-protected with IP66 (NEMA 4X), conquers a wide range of decentralized drive tasks. It is an exceptionally compact device with a design that ensures maximum protection against adverse environmental conditions such as high temperatures, dust, dirt or water jets during cleaning operations.
The Lenze Smart Motor works without contactor or starter, fixed speeds can be set at will, and there are many integrated functions for material handling applications. It meets the strictest energy efficiency requirements and can be operated very conveniently using a smartphone.
info.us@lenze.com 800-217-9100, 508-278-9100 www.Lenze.com
The best machines and production facilities around the world use Lenze
The PI North America team is here to support you by answering questions, offering training, and connecting you with the right industry experts.
Since last year, we have increased our production of free online materials, including webinars, white papers, documentation, books, courses, and much more. You can access all of these resources at us.profinet.com
Find out more about our latest offerings:
Live and On-demand Webinars Register for upcoming sessions or browse through our wide selection of on-demand webinars at us.profinet.com/training/webinars/.
Live webinars include a Q&A block and demos. The recordings of all live webinars are archived for your convenience. These are some of our latest sessions:
• How PROFINET Works?
Beginner’s Guide
7 Steps to Develop a PROFINET Device
PROFIBUS Online Training Course
“A complete PROFIBUS introduction in one structured course”
The PROFIBUS Online Training Course is a self-paced training specifically designed for remote learning. It includes technical details of the technology and a complete overview of network design, configuration, installation, commissioning, and maintenance for PROFIBUS DP and PROFIBUS PA.
(Professional Development Hours)
us.profinet.com/profibusonline
such as
Here are some of our
about PROFINET,
and Industry 4.0.
•
Introduction to IO-Link
PI North America info@pinorthamerica.com • 480-483-2456 us.profinet.com
Radwell International’s Asset Recovery program is an exceptional resource for your company. We offer cash for parts and products you don’t need. In many cases, selling your excess inventory to Radwell gives you the opportunity of adding dollars to your bottom line.
With extensive knowledge, Radwell stocks and sells new and certified preowned industrial automation, MRO, pneumatic, motion, electronic, hydraulic, HVAC, and electrical control equipment for plant floor and facilities maintenance machinery.
The process is easy. Gather all your inventory, box it, and then call Radwell for free pick-up.
Need more information?
Radwell has highly trained and
experienced asset recovery and surplus team members ready to help.
It is important to note that any equipment being sold to or sourced by Radwell International must meet the highest standards of functionality and use. However, not all equipment sold to Radwell via the Asset Recovery program has to be brand-new.
Radwell has a team of in-house engineers and technicians who can refurbish equipment to a like-new state, granting it the Radwell Certified PreOwned stamp of approval, which comes with Radwell’s Two-year warranty.
Radwell has highly trained and experienced asset recovery and surplus team members ready to help you make your business thrive.
The types of equipment Radwell most often purchases and upcycles include industrial automation equipment, PLCs, drives, motors, electronic parts, circuit boards, meters, ensors, and all types of industrial controls.
However, if your company has other types of surplus inventory that you’re looking to offload, please feel free to contact us at 800-884-5500 ext. 824.
Tired of looking up multiple sources for answers to common engineering questions about gear units or gearmotors? We have the solution.
SEW-EURODRIVE’s online Technical Notes can be a real life-saver when you need answers. Technical Notes provide quick access to many engineering topics such as how to properly mount a torque arm, how to determine and design for inertia, or how to properly design your machine to use a hollow shaft gear unit.
Need answers on how the speed, mounting position, environment, and duty cycle can affect the thermal rating of a gear unit and how to protect against too much heat? That’s one of many in-depth documents you can find by visiting www.seweurodrive.com and clicking Technical Notes.
Our technical white paper, Maximizing Gearmotor Speed Range shows you how to operate VFDs above 60Hz to widen speed range, improve stability and reduce cost.
In this white paper, you’ll learn why it can be a good idea to operate gearmotors above 60Hz. Through a common example, we will show you how to select the proper gearmotor that will significantly enhance performance in the following ways:
•
•
•
•
•
stability
reducing inertia mismatch
speed range
a costly ventilator fan at low speed
smaller motor
Visit www.sewwhitepapers.com/vfd to download the PDF. mktg@seweurodrive.com 864-439-7537 www.seweurodrive.com
Want to learn about engineering topics pertaining to gearmotors? We have the information at your fingertips!
Understanding your attack surface is the first step toward protecting your operational technology (OT) and your organization. Without critical insights, you’re in the dark in relation to where you’re vulnerable. The question organizations need to ask themselves is, “Are we applying the same cybersecurity best practices and due diligence to our industrial control systems (ICS) as we are for our IT enterprise systems?” If not, why not?
Real-time visibility into the assets in your industrial environment, including behavior anomalies, security threats and vulnerabilities; is crucial to the protection of your organization. Our proprietary visibility study sheds light on what you can’t see. It gives you everything you need to create your vision, strategy, and digital safety implementation plan and is more than simply a moment-in-time Risk Assessment.
Velta Technology’s visibility study helps you translate plant floor insights and vulnerabilities into metrics that IT, OT and the C-suite can understand and do something about. You also receive your unique Connected Devices Vulnerability (CDV) Index score as part of your visibility study.
The CDV Index is a method of quantifying and evaluating an industrial facility’s preparedness, resiliency, risks, and progress around addressing digital incidents, threats and compromises that can negatively impact production, operations, environment, and lives. In addition to giving you a metric and insights into your operational risks and vulnerabilities, the CDV Index score may also help you with your cybersecurity insurance rates.
With over 100 years of combined experience, think of us as an extension of your internal team.
With over 1,000 points of entry, they only need one. Velta Technology - Get Safer Sooner
The CDV Index quantifies and evaluates an industrial facility’s preparedness. www.veltatech.com asktheexperts@veltatech.com 314-463-3600
Global Headquarters 119 South Main Street St. Charles, MO 63301
Inductive Automation offers many flexible options for learning the Ignition industrial application platform:
• Inductive University has hundreds of free videos to get you trained or help you find quick answers.
• Our comprehensive Online User Manual is closely tied with Inductive University so you can get a conceptual understanding and a visual walk-through of the features by using them together.
• Our Training Courses offer in-person, on-site, or virtual instruction taught by one of our Ignition experts.
• Our collection of Webinars provide insights about best practices and industry trends.
• Gather with the world’s most innovative group of industrial professionals at the annual Ignition Community Conference (free & virtual in 2021).
Find out more at: inductiveautomation.com
input #31 at www.controleng.com/information
As an established industry leader for critical communications, Sealevel knows a thing or two about control systems and digital I/O. Available resources on our website include the five-part series “Control System Basics,” written by technical author Jon Titus. Titus explores relays, sink versus source control, NPN versus PNP logic, open collectors and isolation. Of particular interest are the differences between NPN and PNP logic, as well as how these connections apply to control and logic level applications.
For more insights from Titus, and the makers of data acquisition and control modules, read The Digital I/O Handbook. With experience-driven insights, the handbook explains real-world digital I/O implementation from both hardware and software perspectives. Contact us to receive your free copy.
at www.controleng.com/information
See more New Products for Engineers. www.controleng.com/NPE
The Quint dc/dc converters from Phoenix Contact feature conformal coating for protection in harsh environments. The conformal coating protects against dust and conductive debris, corrosive gases, and humidity, and it prevents failures due to creepage currents and electromechanical corrosion. It also reduces the risk of failure due to vibration and thermal shock. The dc/dc converters can amplify, iso late, and convert voltage, and they also allow for the creation of an independent supply system. Their output side enables easy expansion and a reliable heavy load startup. The dc/dc converters are available in both 5- and 10-A versions. The selected components in these converters are not only high in quality, but have an operating temperature ranging from -40 to 70°C.
Phoenix Contact, www.phoenixcontact.com
Input #200 at www.controleng.com/information
Eaton’s PowerXL DM1 micro variable frequency drive (VFD) is designed for commercial, industrial and original equipment manufacturer (OEM) customers, the Eaton engineered drive is designed to simplify design, integration and opera tion. The DM1 includes onboard Ethernet-based communications, IoT, webserv er, Bluetooth, safe torque off, SIL2 and more. Eaton’s PowerXL DM1 micro drives are engineered to help customers reduce system costs and meet the challenges of today’s more demanding commercial and indus trial applications. The PowerXL DM1 is a micro drive that incorporates a patented energy control algorithm, extensive onboard industrial communication protocols and built-in webserver capabilities to help customers reduce the cost of using a VFD.
Eaton Corp., www.eaton.com Input #201 at www.controleng.com/information
The Flow-Tek Series M4 Severe Service ball valves are engi neered for isolation in vent and drain valve applications in the power industry. Series M4 valves are rigorously tested for dependable zero leakage on/off applications in high pressure, high temperature steam and superheated steam. Series M4 Vent & Drain Valves ensure maintenance free operation in the most extreme conditions. Featuring a standard 4-year performance warranty, series M4 severe service ball valves are engineered using advanced technology, featuring a 1-piece unibody body construction, with heavyduty drivetrain, mate-lapped ball and seat with high velocity oxygen fuel (HVOF) and spray & fuse hard coating options along and live-load packing with Belleville springs. Bray Flow-Tek, www.bray.com Input #202 at www.controleng.com/information
The Proline 10 provides time and money savings over the product life cycle without limits on mea surement performance. Every device is tested on accredited and traceable calibration rigs per ISO/ IEC 17025. Proline 10 flowmeters cover a wide range of basic applications in all kinds of indus tries. Proline Promag electromagnetic flowme ters are ideally suited for measuring the flows of conductive liquids, as well as for volume measurement of water and corrosive liquids (Promag W/H/D 10). Com missioning and operation can be done quickly, in the field as well as in the control room. A commissioning wizard enables on-site configuration with either the autorotatable and high-contrast LCD touch screen or the SmartBlue app via Bluetooth. The latter approach is particularly useful when devices are installed in difficult-toaccess locations.
Endress+Hauser, www.us.endress.com Input #203 at www.controleng.com/information
The Fluke 3562 Screening Vibration Sensor system features batteryless tech nology, long-range sensor-to-gateway communication and can connect up to 1,000 sensors to one gateway. The Fluke 3562 can operate continuously, even in hard-to-reach places. The vibration screening system enables maintenance teams to spot machine faults before catastrophic failures happen, avoiding costly downtime. The vibration sen sor draws power from a machine’s heat or the light in the room using inno vative thermoelectric or photovoltaic energy harvesters. The technologically advanced sensor screens overall vibra tion levels, temperature, and humidity, as well as trends of the nine highest FFT peaks by magnitude.
Fluke Corp., www. uke.com
Input #204 at www.controleng.com/information
The X-Tag is a UWB-sensor designed for Industrial Internet of Things (IIoT) applications. Companies can deploy the X-Tag for previously unfeasible IoT-applications and increase their productivity in production and logistics –from search and find and track and trace to automated material flow or assembly tool control. The X-Tag delivers ultra-precise data in the most cost-efficient way so companies can significantly reduce their amortization times and achieve an up to 50% higher ROI. It’s software-based approach reduces the complexity on the hardware side to a minimum and enables the company to offer the X-Tag for other UWB solutions. Leading companies in the automotive and aerospace industries are already implementing the X-Tag within their smart factory initiatives. Kinexon, www.kinexon.com Input #205 at www.controleng.com/information
The Sensaphone Zone Water Detection Sen sor detects the widespread presence of water in areas like floors or drop ceilings. Users receive an alert when the sensor contacts water. The sensor includes 10 ft of water rope to cover a large area. Operators can connect up to 10 water ropes to one sensor for up to 100 ft of coverage. This sensor operates on two AA lithium batteries. When the batteries run low, the sensor sends an alert, so users can replace the batteries when no water is present. The sensor reveals the presence of water on a hori zontal surface.
Sensaphone, www.sensaphone.com
Input #206 at www.controleng.com/information
Russelectric’s customized supervisory control and data acquisition (SCADA) systems enable users to monitor system operation, acknowledge alarms, and review programmable logic controller (PLC) setpoints and alarm history. All screens are custom-designed for each power control system, providing the most realistic, accurate display possible. The basic system has a dynamic one-line display with changing color codes to indicate real-time power switching device status and power source con nection to loads. Russelectric, www.russelectric.com Input #207 at www.controleng.com/information
Record-keeping in the life sciences industry is just as crucial as manufac turing high quality products. The reg ulations, such as FDA 21 CFR Parts 210 and 211, dictate the required records a life sciences manufacturer must produce and maintain, as well as the requirements around data and record integrity. The old adage “say what you do, do what you say, and prove it” rings true.
Among the myriad records created in the industry, the master production and control record and the associated batch production and control records are particularly important. The master production and control record (often abbreviated as MPR) is the blueprint for the man ufacture of a drug product and is unique to each formulation, batch size, and packaging method of the product. The batch production and control records (often abbreviated as BPR) describes how a batch of drug product was manufactured.
With the advent of computerized systems in manufacturing, the FDA and other regulators allowed manufacturers to use electronic record keeping methods, if they followed certain rules. The FDA encapsulated these rules in the regu lations as 21 CFR Part 11. If Part 11 is followed, electronic records and electronic signatures are considered equivalent to paper records and hand written signatures.
This regulatory acceptance of e-records and e-sig natures created a pathway for drug companies to implement electronic batch recording (EBR) systems.
Systems across the entire Purdue Enterprise Reference Architecture were connected, enabling master data to be converted into instructions for the manufacturing equipment to execute and allowing production data to be captured electroni cally, which digitized the BPRs.
EBR systems remove the (error-prone) humans from the record-keeping equation, enhancing data integrity and speeding up the batch release pro
cess. Quality assurance (QA) personnel are no lon ger needed to parse binders full of paper prior to signing off on a batch of drug product. As the sys tems matured and confidence was gained, batch es could be released by exception: only deviations from standard procedures needed to be reviewed prior to batch release.
Other industries can reap the benefits of elec tronic batch records. For example, traceability is important in the food and beverage industry. It is imperative for manufacturers produce goods that contain allergens alongside an allergen-free version of the product in the same facility. Rigorous trace ability controls are required to ensure no potentially deadly allergens make it into the allergen-free product. An EBR sys tem integrated to the production equip ment will enforce that the correct raw ingredients and packaging materials are used for a specific batch of product.
This is just one example of how an EBR system can be leveraged in nonregulated industries. Any situation in which human error or paper recordkeeping is at play is a potential use case for EBRs. While the upfront cap ital costs are high, there are enough potential efficiencies to ensure a healthy ROI for any industry. ce
Bryon Hayes, director of life sciences, Grantek. Edited by Chris Vavra, web content manager, Control Engineering, CFE Media and Technology, cvavra@cfemedia.com.
KEYWORDS: process manufacturing, electronic batch recording
Record-keeping in life sciences and manufacturing are critical. Electronic batch recording (EBR) systems enhance data integrity and speeding up the batch release process.
EBR can improve traceability and safety in the food and beverage industry.
See additional stories at www.controleng.com/ process-manufacturing
What other ways could EBR help a manufacturing plant?
Electronic batch records (EBRs) can improve record-keeping by making it more automated and removing the human element from the equation.Bryon Hayes, Grantek
‘Non-regulated industries also can use electronic batch records to their bene t.’
ContentStream
Lynch, Director of
630-571-4070 x2210
PLynch@CFEMedia.com
AR, IL, IN, IA, KS, KY, LA, MN, MO, MS, NE, ND, OK, OH, SD, TX, WI, Central Canada
Robert Levinger 630-571-4070 x2218
RLevinger@cfetechnology.com
AK, AZ, CA, CO, HI, ID, MT, NV, NM, OR, UT, WA, WY, Western Canada
Aaron Maassen 816-797-9969
AMaassen@CFEMedia.com
CT, DE, MD, ME, MA, NC, NH, NY, NJ, PA, RI, SC, VA, VT, WV, DC, Eastern Canada
Julie Timbol (978) 929-9495
JTimbol@CFEMedia.com
Jim Langhenry, Co-Founder/Publisher, CFE Media JLanghenry@CFEMedia.com
Steve Rourke, Co-Founder, CFE Media SRourke@CFEMedia.com
Courtney Murphy, Marketing Services Manager 630-229-3057 CMurphy@cfemedia.com
McKenzie Burns, Marketing and Events Manager mburns@cfemedia.com
Brian Gross, Marketing Consultant, Global SI Database 630-571-4070, x2217, BGross@CFEMedia.com
Michael Smith, Creative Director 630-779-8910, MSmith@CFEMedia.com
Paul Brouch, Director of Operations PBrouch@CFEMedia.com
Michael Rotz, Print Production Manager 717-766-0211 x4207, Fax: 717-506-7238 mike.rotz@frycomm.com
Maria Bartell, Account Director, Infogroup Targeting Solutions 847-378-2275, maria.bartell@infogroup.com
Rick Ellis, Audience Management Director 303-246-1250, REllis@CFEMedia.com
Letters to
to MHoske@CFEMedia.com
630-214-4504.
name,
Information: For a
go to www.controleng.com/mediainfo.
Marketing consultants: See
Custom reprints, electronic: Shelby Pelon, Wright’s Media, 281-419-5725 x138, cfemedia@wrightsmedia.com